机械零件的强度和设计准则资料教程
机械零件的强度和设计准则
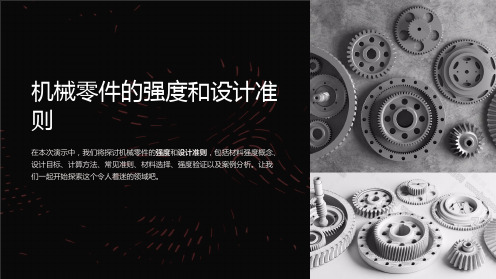
3
屈服强度
了解材料开始产生塑性变形的载荷水平。
4
韧性与脆性
了解材料在受力时的表现,以及其破坏模式。
机械零件设计的目标
1 实用性
确保机械零件能够正 常运行并完成预定任 务。
2 安全性
保证机械零件在工作 条件下不会出现失效 和危险。
3 经济性
优化材料使用和制造 成本,提高效率。
强度计算方法
解析法
根据材料的应力-应变关系曲线进行数学计算。
探讨飞机机翼连接件的设计 要求和强度分析。
工程机械齿轮
研究工程机械齿轮的寿命和 强度评估。
机械零件的强度和设计准 则
在本次演示中,我们将探讨机械零件的强度和设计准则,包括材料强度概念、 设计目标、计算方法、常见准则、材料选择、强度验证以及案例分析。让我 们一起开始探索这个令人着迷的领域吧。
材料强度的基本概念
1
应力与应变
了解材料的应力-应变关系是评估其强度的基础。
2
抗拉强度
了解材料在拉伸载荷下的最大承载能力。
2 可加工性
选择易于加工和制造的材料。
如何进行强度验证
1
理论计算
基于强度计算公式,评估机械零件的承载能力。
2
有限元分析
使用计算机模拟方法预测机械零件的强度性能。
3
实验测试
通过物理实验验证机械零件的强度可靠性。
案例分析及实例解析
汽车发动机曲轴
深入剖析汽车发动机曲轴的 强度设计与优化。
飞机机翼连接件
试验法
通过实验测试材料的强度性能。
常见的设计准则
安全系数
考虑提供足够的强度裕度来避免失效。
曲轴弯曲
选择满足承载能力和刚度要求的适当材料。
机械设计教学课件:机械零件的强度
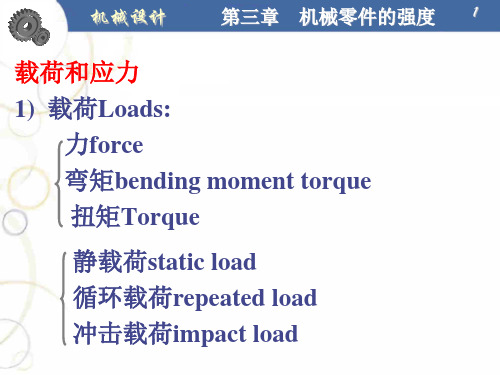
rN
m
N0 N
r
KN r
KN: 寿命系数 N0: 循环基数
机械设计
第三章 机械零件的强度 20
所有应力循环的疲劳极 限中,以对称循环的疲 劳极限为最低。
机械设计
第三章 机械零件的强度 21
(应力循环次数N一定)
机械设计
第三章 机械零件的强度 22
D G
C
材料的极限应力线图
机械设计
第三章 机械零件的强度 23
m 2
...
nz
m z
)
ni
m i
i 1
N
0
m 1
1
若材料在这些应力作用下,未达到破坏,则有:
z
ni
m i
N
0
m 1
i 1
令不稳定变应力的计算应力为:
ca
m
1 N0
z
ni
m i
i 1
则: σca< σ-1 ,其强度条件为:
Sca
1 ca
S
机械设计
第三章 机械零件的强度 30
(三)双向稳定变应力的疲劳强度计算
第三章 机械零件的强度 13
静应力下的强度设计
1) 塑性材料
lim s
2) 脆性材料
lim b
机械设计
第三章 机械零件的强度 14
变应力下的强度设计
疲劳破坏
表面光滑
特征:
表面粗糙
a) 疲劳断裂时:受到的 max 低于 b,甚至低于 s 。
b) 断口通常没有显著的塑性变形。不论是脆性材料,还是塑 性材料,均表现为脆性断裂。更具突然性,更危险。
疲劳极限的影响因素
尺寸系数: 有效应力集中系数: k 表面质量系数: 表面强化系数: q 综合影响系数: K
机械零件的强度教学课件PPT

s m ax s max
s -1
KsDs a y ss m
S
第2章 机械零件的疲劳强度设计
2.4 机械零件的疲劳强度计算
二、单向稳定变应力时的疲劳强度
1) 应力比为常数r =C
极限应力点N’1位于直线CG上,则
s 'max s 'ra s 'rm s s
有:
屈服失效,静强度计算:
Sca
sS s max
第2章 机械零件的疲劳强度设计
2.4 机械零件的疲劳强度计算
二、单向稳定变应力时的疲劳强度
1) 应力比为常数r =C
s 1 KsDs ra yss rm
比值:s a s max s min 1 r C ' s m s max s min 1 r
射线OM上任意点的应力循环r =C
M’1为极限应力点,极限应力σ’max 。
表面光滑 表面粗糙
疲劳断裂具有以下特征: 1)疲劳断裂的最大应力远比静应力材料的强度极限低,甚至比屈服极限低; 2)疲劳断口均表现为无明显塑性变形的脆性突然断裂; 不管脆性材料或塑性材料, 3)疲劳断裂是微观损伤积累到一定程度的结果。 4)断裂面累积损伤处表面光滑,而折断区表面粗糙。
第2章 机械零件的疲劳强度设计
σm,σa落在OA’G’C外, 一定会发生疲劳破坏。
正好落在A’G’C折线上, 表示应力状况达到疲劳破坏的极限值。
sm-sa极限应力图
第2章 机械零件的疲劳强度设计
2.2 材料的疲劳特性
例2-1 某合金钢σ-1=340MPa,σs=550MPa。
(1)绘制材料的简化sm-sa极限应力图。
(2)试求r=-0.3时的疲劳极限σ-0.3 。
机械零件设计的基本准则与步骤

机械零件设计的基本准则与步骤引言机械零件设计是机械工程中非常重要的一环。
它涉及到零件的功能、结构、材料、加工工艺等方面的考虑。
在设计过程中,遵循一定的准则和步骤可以提高设计的效率和质量。
本文将介绍机械零件设计的基本准则与步骤,以帮助工程师们更好地完成机械零件的设计工作。
一、机械零件设计准则在进行机械零件设计时,需要考虑以下准则:1. 功能性机械零件的设计首先要满足其预定的功能要求。
因此,在设计之初,需要明确该零件的功能需求,并结合整个机械系统的工作原理和要求,确定该零件所承担的功能角色。
在设计过程中,要时刻关注功能性需求,确保设计的零件能够准确、可靠地完成其预定的功能。
2. 结构合理性机械零件的结构设计要合理,即要考虑零件的外形、尺寸、连接方式、布置等因素。
要尽量使结构简单、紧凑,减少零件的数量和体积。
此外,还要注意结构之间的配合与协调,确保零件可以良好地配合使用。
3. 强度与刚度机械零件在运行过程中会承受一定的载荷,因此要保证设计的零件具有足够的强度和刚度,以防止因载荷引起的变形、断裂等失效问题。
在设计过程中,需要进行强度和刚度的计算与分析,以确定合适的材料选择和尺寸设计。
4. 可靠性与安全性机械零件设计要确保零件的可靠性与安全性。
可靠性是指零件在规定条件下连续正常工作的能力,而安全性则是指零件在工作过程中不会产生意外事故或造成人员伤害的能力。
因此,在设计过程中,需要充分考虑零件的耐久性、稳定性、故障率等因素,并遵循相关的安全标准和规范。
5. 经济性机械零件的设计还要考虑经济性。
设计师应该在保证零件功能和质量的前提下,力求减少材料、加工和使用成本,提高设计的经济效益。
在设计过程中,需要综合考虑成本与性能的平衡,选择合适的材料、工艺和加工方式。
二、机械零件设计步骤在进行机械零件设计时,可以按照以下步骤进行:1. 确定设计要求首先,明确机械零件的功能要求以及所处的工作环境和使用条件。
了解零件的工作原理和特点,分析其受力情况和运动要求。
机械零件的强度和设计准则
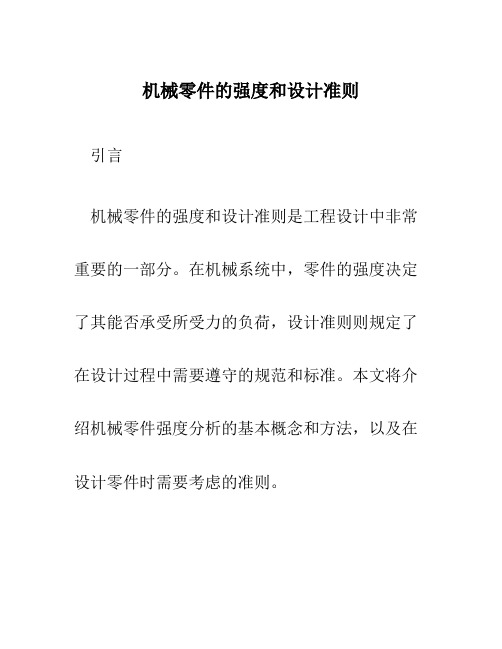
机械零件的强度和设计准则引言机械零件的强度和设计准则是工程设计中非常重要的一部分。
在机械系统中,零件的强度决定了其能否承受所受力的负荷,设计准则则规定了在设计过程中需要遵守的规范和标准。
本文将介绍机械零件强度分析的基本概念和方法,以及在设计零件时需要考虑的准则。
机械零件的加载形式机械零件在工作过程中通常会受到各种不同形式的加载,主要包括以下几种形式:1.静态加载:零件受到的外力是稳定不变的,不会引起零件形变和变形。
例如,支撑结构中的支撑杆。
2.动态加载:零件受到的外力是变化的,会引起零件的形变和变形。
例如,活塞在往复运动中的受力。
3.疲劳加载:零件在长期使用过程中,由于受到循环变化的载荷,会导致零件发生疲劳破坏。
例如,汽车悬挂系统的弹簧。
4.冲击加载:零件在瞬间承受巨大的载荷,往往会引起零件的破坏。
例如,锤子敲击物体的过程中,敲击面会受到很大的冲击力。
强度分析方法为了确保机械零件在工作过程中具有足够的强度,需要进行强度分析。
常用的强度分析方法包括以下几种:理论分析法理论分析法通过应力和应变理论分析零件受力情况,得出零件的强度指标。
常用的理论分析法包括静力学分析和材料力学分析。
静力学分析重点考虑静态平衡条件下的受力情况,而材料力学分析则考虑材料的物理性质和力学性能。
数值模拟方法数值模拟方法通过计算机辅助工程软件,对零件的受力情况进行模拟和分析。
常用的数值模拟方法包括有限元分析和计算流体力学分析。
有限元分析可以对零件的应力、变形等进行准确的数值计算,而计算流体力学分析可以对零件在液体或气体环境中的受力情况进行模拟和分析。
实验测试方法实验测试方法通过搭建实验平台,对零件进行实际加载测试,获取零件的应力、变形等参量。
常用的实验测试方法包括拉压试验、弯曲试验和冲击试验等。
实验测试方法具有直观、准确的优点,但成本较高且耗时较长。
设计准则在设计机械零件时,需要遵守一些相关的准则和规范,以确保零件具有足够的强度和可靠性。
机械零件设计的基本准则与步骤PPT(27张)
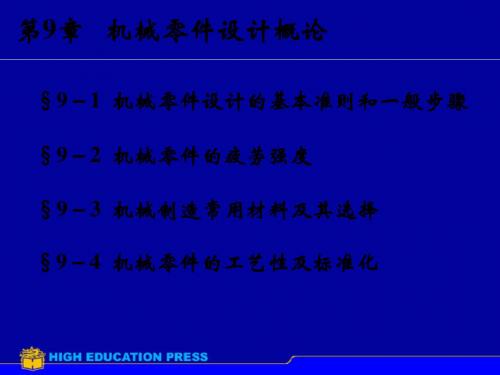
2)表面强度 分为表面挤压强度和表面接触强度
表面挤压强度是指面接触的两零件,受载后接触
面间产生挤压应力,应力分布在接触面不太深的表层,
挤压应力过大时,零件表面被压溃。
判定条件:
p [p]
[
p
]
p lim
Sp
表面接触强度是指两个零件
在受载前是点接触或线接触。受
载后,由于变形其接触处为一小
4) 疲劳断面明显分为两
个区域,即表面光滑的
疲劳发展区和表面粗糙
的脆性断裂区。
三、疲劳曲线
σrN
疲劳极限σrN与循环次数N 之σ
间的关系曲线称为:疲劳曲线
r
由图可知:应力越小,试件能经受的循环次数就越多。试
验表明,当 N>N0以后,曲线趋于水平,可认为在无限次循 环时试件将不会断裂。
1)无限寿命区
3)变应力下,
S =1.3~1.7
材料不均匀,或计算不准时取: S =1.7~2.5
§9-3 机械制造常用材料及其选择
机械制造中最常用的材料是钢和铸铁,其次是有色金属合金。非金属材料如塑料、橡胶等 。
一、金属材料
常用金 属材料
铸铁 ----含碳量>2% 钢 ----含碳量≤ 2% 铜合金
铁碳合金
1.铸铁:灰铸铁、球墨铸铁、可锻铸铁、合金铸铁等。
如轴、齿轮、轴瓦、轴颈、螺栓、带 传动等。机械零件虽然有多种可能的 失效形式,归纳起来最主要的为
零件的失效形式:
断裂或塑性变形; 过大的弹性变形; 工作表面的过度磨损或损伤; 发生强烈的振动;联接的松弛; 摩擦传动的打滑等。
失效原因: 强度、刚度、耐磨性、振动稳定性、温度 等原因。
对于各种不同的失效形式,相应地有各种工作 能力判定条件。这种为防止失效而制定的判定条件, 通常称为工作能力计算准则。
机械零件的强度培训课件(ppt 103页)

σa
A´
600
σ-1
500
σ-1e
300 A 260 200
O
1)r=0.2
D´
(σ0/2, σ0/2)
M ´D
M
ห้องสมุดไป่ตู้
(σ0/2, σ0e/2)
300 390 500
C
σS 800 σm
52
解:(3) 1)应力比r=0.2
Sca
m ax max
m m
a a
1 0 / 2 0 /2
σr
N0
N
15
已知45钢的疲劳极限-1=270MPa,疲劳曲线方程的幂指
数m=9,应力循环基数N0=5×106次。求当应力循环次数 N=104次时,其相应的有限寿命疲劳极限为 MPa。
16
已知45钢的疲劳极限-1=270MPa,疲劳曲线方程的幂指
数m=9,应力循环基数N0=5×106次。求当应力循环次数 N=104次时,其相应的有限寿命疲劳极限为 MPa。
11
例1 已知:max=200 MPa,r =-0.5,求:min、a、m。
解:
min r max 0.5 200 MPa 100 MPa
a
max min
2
200(- -100)MPa 2
150 MPa
m
max min
2
200 (100) MPa 2
50MPa
12
例2 已知:a= 80 MPa,m=40 MPa。求:max、min、
-1N
-1 m
N0 N
9
5106 104
270 MPa 539 MPa
17
σmax
σ0.4N σσ00N.4 σσ-10N σ-1
机械零件的强度和计算准则

• 可靠性计算准则,就是要保证零件在工作 过程中能够满足规定的可靠性要求。
2.3 提高强度的一般方法
2.3.2 提高机械零件强度的一般措施 1)合理布置零件,减少所受最大载荷
图2.6 改进零件布置提高弯曲强度
2)采用等强度结构
图2.7 阶梯轴的等强度原理
3)减少应力集中
之比为Ma:Mb:Mc为4:2:1,最大变形挠度之比ya:yb: yc为16:4:1,
3)通过预紧装配实现刚度的提高
2.6 机械零件的振动稳定性冲击强度
• 2.6.1 零件的振动和振动稳定性
振动---- 零件周期性的弹性变形现象
失稳----零件或机器的自振频率和周期性外力 的变化频率相等或相接近时,发生共振,振 幅将急剧增大,此种现象称为失稳。
零件工作
—→承受载荷
载荷欲使零件失效 —→
零件据自身结构、
材料反抗失效
—→反抗失效>失效 —→解决办法:合理设计
遵循设计准则
2.2.1 强度准则
强度:零件抵抗断裂、疲劳破坏的能力 1.判断危险截面的最大应力(,)是否小于或等
于许用应力([],[])
[ ],[ ] lim
[S ]
[ ],[ ] lim
2.2.2刚度准则
• 刚度----零件在载荷作用下抵抗变形的能 力 (力,力矩/弹性变形量)
• 柔度----在外力作用下产生变形的能力 (弹性变形量/力,力矩)
刚度指标: 伸长,压缩,挠度,扭角,转角 计算准则: 弹性变形量不大于许用值
y [y]
[ ] []
实际的弹性变形量可以根据不同的零件,依据不同的理 论或实验方法进行确定,而相应的许用值则需要根据不 同的场合,根据理论和经验确定合理的数值。
- 1、下载文档前请自行甄别文档内容的完整性,平台不提供额外的编辑、内容补充、找答案等附加服务。
- 2、"仅部分预览"的文档,不可在线预览部分如存在完整性等问题,可反馈申请退款(可完整预览的文档不适用该条件!)。
- 3、如文档侵犯您的权益,请联系客服反馈,我们会尽快为您处理(人工客服工作时间:9:00-18:30)。
• 表面接触强度:是指高副接触的表面抵抗接触破坏的能力
1
Hm
ax4
F 2ab
1 F
b
1E1 12
122
E2
1
2
Hm
ax23
F c2
13
6F
1E112
122
E2
在静载荷作用下,接触表面的失效形式为脆性材料 的表面压碎和塑性材料的表面塑性变形。
Hma x[ H]max
在实际问题中碰到的变应力很多处于一种不稳定变化状 态,甚至是随机变应力
静载荷也能产生变应力:
2.2 机械零件计算的准则
计算准则----针对某种失效形式、为满足某种工 作能力而建立的设计准则
强度准则
• 两种计算准则:一种是根据许用应力建立的计算准则, 另一种是根据安全系数建立的计算准则;
• 在实际使用中根据所掌握的数据情况确定选择使用哪 种强度准则。
强度准则
1.通过判断危险截面的最大许用应力(σ,τ)是否小于或 等于许用应力[σ],[τ]。
[ ]
[ ]
2.通过判断危险截面上实际的安全系数(Sσ,Sτ)是否大 于或等于许用安全系数([Sσ],[Sτ])
Sσ
lim
[Sσ ]
Sτ
lim [Sτ ]来自• 安全系数:零件所能承受的极限应力与实际应力的比值, 它反映的是零件的安全工作程度;
• 同一种零件发生失效的形式可能有很多种; • 最常发生的失效形式主要是由于强度、刚度、耐磨性、耐温度性、
振动稳定性、可靠性等方面的问题。
提高机械零件强度的一般措施
1.合理布置零件,减少零件所受到的最大载荷
2. 采用等强度结构 3.减小载荷和应力集中
4.选用合理截面 比如梁的截面采用工字型、T字型;轴的截面采用圆形、 空心圆形等。
5.对零件表面进行强化处理 比如,为提高零件表面疲劳强度,常采用的表面强化工艺 有:喷丸处理及碾压处理、渗碳、碳氮共渗、渗氮、表面 淬火。这些方法都可以在零件表面中形成残余压应力、提 高表面硬度,对提高零件的表面疲劳强度是有利的。
2.4 机械零件的三种表面强度
• 表面挤压强度:是指零件表面抵抗表面挤压破坏的能力
表面磨损强度 对于滑动速度低、载荷较大,可以通过限制工作表 面的压强进行计算,以限制过度磨损:
p [p]
滑动速度较高时,要限制摩擦功耗(限制pv值)
如果试验时间不断延长,则Nf将不断增加,可靠度逐渐 减少,这说明零件的可靠度是随时间发生改变的,是时 间的函数。
f(t)dFt dNf dt Ndt
累积失效概率
Ft dtF f(t)dt
Rt 1Ft
2.3 机械零件的失效方式及提高强度的一般方法
• 失效:机械零件在工作时出现丧失工作能力或达不到设计要求性能 的现象;
• 失效并不意味着破坏; • 常见的失效形式有:(1)整体断裂;(2)过大的弹性变形或残余
变形;(3)零件表面的破坏(过度磨损、过度腐蚀、接触疲劳破坏、 过热等);(4)不能满足工作条件所导致的失效(联接的松动、压 力容器和管道的泄漏、运动精度达不到要求、皮带传动出现打滑现 象、滑动轴承的油膜压力太小、转动速度与固有频率重合而发生共 振等)。
名义载荷:机器在平稳工作条件下作用在零件上的载荷; 计算载荷:考虑载荷的时间不均匀性、分布的不均匀性以及其它影响因 素对名义载荷进行修正得到的载荷
名义载荷的计算一般运用公式来进行 ,比如十分常用的一种已知转动速度 n和输入功率P计算旋转运动件所受到 的扭矩:
T9.55106 P(Nmm)
n
在进行载荷计算时往往要通过一些简 化处理,这是因为实际载荷的作用往 往都是作用在一定的范围面上。
• 安全系数如果选择过大,则造成材料浪费、机器笨重、 加工运输困难、成本提高等一系列问题。安全系数过小, 则可能导致不安全;
• 许用安全系数的确定要考虑:(1)载荷和应力的性质和计算
的准确程度;(2)运行条件的平稳程度(是否有冲击载荷);(3) 材料的性质和材质的均匀程度;(4)零件的重要程度;(5)工艺 和探伤水平;(6)环境是否具有腐蚀性。
2.2.4 可靠性准则
所谓可靠性,就是产品在规定的条件下、规定的时间内,完成规 定功能的可靠程度;
比如:有N个同样零件在规定的时间t内有Nf个零件发生失效,剩 下Nt个零件仍能继续工作,则可靠度为
失效概率
Rt N N t N N Nf 1N N f
Ft
Nf N
1Rt
Rt Ft 1
可靠性计算准则:保证零件在工作过程中能够满足规定的可靠性 要求。
• 安全系数的选择原则:在保证安全、可靠的前提下,尽 可能选用较小的安全系数。
2.2.2 刚度准则
零件在载荷作用下产生的弹性变形分为挠度y、转角θ 和扭角φ,刚度计算准则就是要求零件在实际工作中所
产生的弹性变形量小于或等于许用的弹性变形量
y [y] [ ] [ ]
2.2.3 寿命准则
•决定零件寿命的有腐蚀、疲劳和磨损三种最为主要的因素;
•变载荷:随时间作周期性变化或非周期性变化的载荷。如汽车 齿轮箱中的齿轮、轴、轴承等所受的载荷均为变载荷。
在进行载荷计算过程中也常将载荷分为名义载荷(F、T、M )和计算载荷(Fc、Tc、Mc),计算载荷等于名义载荷乘以 载荷系数K
F c KF T c KT M c KM
载荷系数K的数值主要取决于动力机和工作机的性质,动力 机和工作机的工作越平稳,则冲击载荷越小,载荷系数就越 小,反之则应该取大值。
第2章 机械零件的强度和设计准则
•载荷及其产生的应力,是导致机械零件发生损伤甚至失效的最 主要原因;
•对机械零件进行载荷和应力分析是进行机械设计过程中首先面 临和要解决的问题。
•机械零件的载荷:一般是指它所受到的力(F)、弯矩(M)、 扭矩(T)。
•静载荷:不随时间变化、变化缓慢或者变化幅度相对很小的载 荷。如零件所受到的重力、锅炉稳定工作时所受到的压力等。
•这三种因素的研究进程各不相同,关于磨损问题的研究目前还很 不完善,还无法建立一个能够为广泛接受的计算准则;腐蚀问题 的研究也存在同样的问题,至今还未出现能够具有通用性的计算 准则,因而也无法建立明确的计算准则;
•疲劳问题是目前发展比较成熟的一个研究方向,已经可以较为定 性地进行疲劳寿命计算,但是在一定可靠度的前提下进行的计算 。