湿法炼锌净化工艺的选择
湿法冶锌工艺流程

湿法冶锌工艺流程
1.浸出:将含锌矿石(多为氧化锌矿石)研磨成一定粒度的粉末,然后与硫酸等溶液混合,通过浸出反应将锌溶解出来。
浸出反应一般可以分为两个步骤:首先是矿石的颗粒与溶液之间的扩散过程,然后是锌离子在溶液中的化学反应。
2.过滤:将浸出溶液中的固体杂质物通过过滤器进行过滤,得到含锌的滤液。
过滤是一个重要的步骤,它可以有效地去除溶液中的固体杂质,防止后续工艺发生堵塞和设备磨损。
3.净化:通过净化工艺,将滤液中的铁、铜、镉等杂质去除,以获得纯度更高的锌溶液。
常用的净化方法有镉精萃取法、铜脱除法、硫酸铁脱除法等。
4.电积:将经过净化的锌溶液通过电解槽进行电积操作,使锌离子在阳极上还原成金属锌,在阴极上沉积。
电积是将溶液中的锌还原成金属锌的最主要方法,通常使用铅和钢板作为阴极,将锌电积出来。
5.脱水:将电积出来的锌板通过烘干设备进行脱水处理,去除残留的水分,使锌板干燥。
6.熔炼:将脱水后的锌板送入熔炼炉中进行熔炼操作,将锌板熔化成液态锌。
通常采用间歇式熔炼,将锌板在炉中加热至熔点以上,使锌融化成液态,然后通过出铅孔排出熔化后的锌液。
7.精炼:通过精炼设备,对锌液进行精炼操作,以提高锌的纯度。
精炼一般采用电解精炼法,通过电解槽将锌液中的杂质去除,得到高纯度的锌。
8.出锌:将精炼后的锌液通过真空蒸馏或其他方法,将铅和其他低沸点杂质从锌液中蒸馏除去,最终得到纯度达到要求的锌。
总的来说,湿法冶锌工艺流程是一个包括浸出、过滤、净化、电积、脱水、熔炼、精炼和出锌等多个步骤的过程。
通过这些步骤的处理,可以从含锌矿石中提取出纯度较高的锌,用于各种工业应用。
锌的湿法冶金方法概述

锌的湿法冶金
锌的湿法冶金是指使用水溶液作为冶炼锌的介质,其主要包括电解法、酸浸法和氨浸法等几种方法。
1.电解法:将锌精矿放入电解槽中,加入电解液(主要成分为硫酸和氯化铵),在外加
电流的作用下,锌离子被还原成金属锌沉积在阴极上。
这种方法具有效率高、能耗低等优点,是目前最主要的生产方式。
2.酸浸法:将锌精矿浸入硫酸水溶液中,利用硫酸的氧化作用将锌离子溶解出来。
这
种方法适用于高品位的锌矿石,但浸出过程中会产生大量的酸性废水,对环境造成污染。
3.氨浸法:将锌精矿浸入氨水溶液中,通过氨水的配位作用将锌离子溶解出来。
这种
方法对锌矿石的品位要求较低,同时产生的废水为碱性废水,对环境污染较小。
但该方法的操作成本较高。
以上三种方法各有优缺点,应根据不同情况选择合适的冶炼方式。
除了上述的电解法、酸浸法和氨浸法外,还有其他一些较为次要的湿法冶金方法。
4.氯化法:将锌精矿与氯气反应,生成氯化锌,再通过还原反应得到金属锌。
这种方
法主要应用于高品位的锌矿石,但因为氯气对环境的危害性较大,所以逐渐被淘汰。
5.氧化焙烧法:将锌精矿加入到反应炉中,通过高温氧化反应,将锌矿石中的锌转化
为氧化锌,再通过还原反应得到金属锌。
这种方法主要适用于低品位的锌矿石,但因为会产生大量的氧化废气,对环境造成了污染。
总的来说,湿法冶金方法相对于干法冶金方法来说,工艺流程更为复杂,但其适用范围更广,能够处理更多种不同品位的锌矿石,且可以生产出较为高纯度的金属锌。
但湿法冶金方法中会产生大量的废水和废气,需要进行处理和净化,以减少对环境的影响。
湿法炼锌硫酸锌溶液的深度净化

中氧化铋除氯法具有 工业简单 、成本低以及氯离 子脱除率高等 优
点 ,主 要 化 学 反 应 为 :BiOCl+NaOH+H2O=Bi(OH)3+NaC1和
有机 试剂 沉淀 法主要 包括 黄药净 化法 和亚 硝基 B一苯酚 净
工 序 。
化 法 ,通过相 关有机试剂 的添加 来对湿 法炼锌 过程 中产 生的 镉 、
(2)硫 酸锌 溶 液净 化 :此 步需 净化 除去 铜 、镉 、钴及 氟 氯. 镍 、钴 等杂质 进行置换 ,其 中主要 是进行钴 杂质 的去除 。但 在生
简要 概 述 湿 法 炼锌 硫 酸锌 溶 液 的概 念 ,并 结合 近年 来 国 内外硫 酸锌 溶 液 深度 净 化 的现 状 ,提 出具 有针 对 性 的 建议 ,一起 对我 国
未 来湿 法 炼锌 硫 酸锌 溶液 的深度 净 化 的发展 提 供 参考 依 据 。
关键 词 :湿法 炼锌 ;硫 酸 锌 溶液 ;深度 净 化
价钴 ,试 验采用先加 氧化剂再加 除钴剂的方 法去除溶 液中的钴 。 2.4 氧化铋除氯法
净 化过程 的富集作用 ,使 原料 中镉 、钴 、铊等有价 元素得到富集 ,
由于在 湿法炼锌的过程 中会 产生大量的氯离子 ,而硫酸锌溶
达 到从净化 渣中回收有价 金属成分 的 目的 。
液可 以通过与氯离子进行 反应来消除多余的氯离子 。除氯的方法
槽 、阴极 、阳极 、供电设 备 、载 流 母线 、冷 却 电解 液设 备 以及 剥 2.3 除钻 剂沉淀)去(新型的除钻 方法 )
锌机 等设备 …。
除钻剂 AnBm 中含 有黄原 酸基 团,能 与溶 液 中的钻 离子 生
1.2 硫酸锌溶液的初步净化
湿法炼锌净化渣处理新工艺
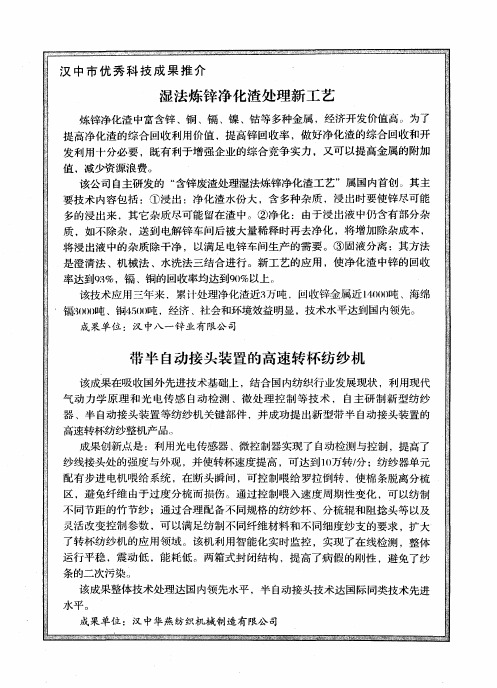
纱线接 头处 的强度 与外观 ,并使转杯速 度提高 ,可达 到 1万转/ ;纺纱器单元 ( ) 分
配有 步进 电机喂给 系统 ,在 断头 瞬间 ,可 控制喂 给 罗拉 倒转 ,使 棉 条脱离分梳 区 ,避 免纤 维 由于过 度分梳 而损伤 。通过控 制喂 入速 度周期 性 变化 ,可以纺制 不 同节距 的竹 节纱 ;通 过合理 配 备不 同规格 的纺纱 杯 、分梳 辊 和阻捻头 等 以及 灵活 改变控制 参数 ,可 以满 足纺制 不 同纤维 材料 和不 同细 度纱 支的要求 ,扩 大 了转杯 纺纱机 的应 用领 域 。该机 利用智能化 实时监 控 ,实现 了在 线检 测 ,整体
镉3) ) 、铜4 ) ,经济 、社 会和环境效益明显 ,技术水平达到 国内领先 。 I) (吨 1 吨
成果单位 :汉 中八一锌业有 限公 司
带 半 自动 接 头 装 置 的高 速 转 杯 纺 纱 机
该成果在 吸收 国外 先进技术基础 上 ,结合 国内纺 织行业 发展现状 ,利用现代
气 动 力学 原 理 和 光 电传 感 自动检 测 、微 处 理控 制 等 技 术 , 自主 研 制 新型 纺纱 器 、半 自动接头 装置 等纺纱 机关键 部件 ,并 成功 提 出新型 带半 自动接 头装置的
高速转杯纺纱整机产 品 。 成果创新 点是 :利用光 电传感器 、微控制器实现 了 自动检 测与控制 ,提高了
汉 中 市 优 秀 科 技 艺
炼锌净化 渣 中富 含锌 、铜 、镉 、镍 、 等 多种金 属 ,经 济开发价值高 。为 了 钴
提高净化渣的综合回收利用价值 ,提高锌回收率 ,做好净化渣的综合回收和开 发利用十分必要 ,既有利于增强企业的综合竞争实力 ,又可 以提高金属的附加
锌湿法冶炼渣处理工艺研究

锌湿法冶炼渣处理工艺研究摘要:有色金属冶炼的环境保护和资源高效利用已成为制约行业可持续发展的关键因素,湿法炼锌生产的浸出渣开路问题是企业面临的难题之一。
本文针对我国湿法炼锌采用的主流工艺,基于生产过程的产生的各种浸出渣、净化渣、烟尘、污泥等含锌物料的来源、组成和污染物进行分析,较系统地总结了目前各类锌冶炼渣的综合利用及无害化处理技术。
关键词:湿法炼锌;锌冶炼渣;处理工艺1冶炼渣的来源与组成1.1常规浸出冶炼渣常规浸出过程为中性浸出和酸性浸出两段。
中性浸出液的净化采用置换或化学沉淀,一般加入锌粉去除铜镉,然后将溶液升温加锌粉和活化剂锑盐或砷盐去除钴镍,最后加锌粉去除复溶镉,分别得到铜镉渣和镍钴渣,也可采用黄药除钴生成黄酸钴渣。
添加铜渣或石灰乳去除氟、氯,分别得到氯化亚铜和氟化钙沉淀。
通过控制酸性浸出液的pH值,Fe2+被氧化成Fe3+后水解去除,酸性浸出渣含锌约20%,Fe约25%,铅约5%,烟尘中含有少量的氧化锌尘和SO2。
常规浸出冶炼渣为有害渣,含有价金属多,回收利用技术相对成熟。
1.2热酸浸出冶炼渣热酸浸出与常规浸出不同的是中性浸出渣采用二段高温高酸浸出,使渣中难溶于稀硫酸的铁酸锌溶解进入酸性浸出液。
富集于热酸浸出渣中的铅、银等称为铅银渣,其中锌主要以ZnS和ZnFe2O4形式存在,铁主要以Fe2O3和FeO形式存在,铅主要以PbS和PbSO4形式存在,银主要以Ag2S和AgCl形式存在。
热酸浸出液除铁后返回中性浸出流程,除铁工艺主要有:黄钾铁矾法、针铁矿法、赤铁矿法,使浸出液中的Fe以黄钾铁矾、针铁矿、赤铁矿的形式与溶液分离。
1.3高压氧浸浸出渣氧压浸出是在高压釜内直接高温氧压浸出硫化锌精矿,可避免副产硫酸,浸出液的处理过程与常规流程一致。
此工艺反应速度快,提高了原料中镓、锗、铟等稀散金属的回收率和铜、镉的浸出率和回收率,利于铅、银等贵金属的富集。
氧压浸出废渣含20%~25%的水份和12%~15%的元素硫,根据精矿原料的不同及后续渣处理工艺的差异,氧压浸出渣分为高银渣和低银渣,高银渣又分成高铁渣和低铁渣。
从湿法炼锌锑盐净化钴渣中回收钴,锌,镉,铜

从湿法炼锌锑盐净化钴渣中回收钴,锌,镉,铜发布时间:2023-06-30T02:57:51.357Z 来源:《新型城镇化》2023年13期作者:安成斌[导读] 国内部分湿法炼锌企业净化采用新型试剂除钴工艺,除钴效果好,解决了传统三段逆锑锌粉除钴工艺产生有害气体、生产不稳定、成本高以及无法实现深度净化等问题。
新型试剂除钴过程产生的钴渣为有机渣,具有锌高、钴低的特点,回收难度大,长期堆存造成环境污染以及有价金属损失。
有必要研究探讨提升净化钴渣技术指标新工艺。
新疆紫金有色金属有限公司新疆克州 845350摘要:针对湿法炼锌净化钴渣钴品位低、渣含锌高的问题,开展了合金锌粉除残镉、三净渣再除钴以及钴渣净化贫镉液中钴镉的试验研究。
提出了金属锌粉预除镉、合金锌粉深度净化残镉以及钴渣多次反复除钴、钴渣与贫镉液反应、钴渣水洗工艺,钴渣含锌降至10%~12%,钴品位富集了(2~3)倍,达到了提升钴品位、降低渣含锌目的。
关键词:新型试剂;有机钴渣;多次利用;合金锌粉;贫镉液;国内部分湿法炼锌企业净化采用新型试剂除钴工艺,除钴效果好,解决了传统三段逆锑锌粉除钴工艺产生有害气体、生产不稳定、成本高以及无法实现深度净化等问题。
新型试剂除钴过程产生的钴渣为有机渣,具有锌高、钴低的特点,回收难度大,长期堆存造成环境污染以及有价金属损失。
有必要研究探讨提升净化钴渣技术指标新工艺。
1湿法炼锌净化钴渣处理的方法1.1选择性浸出—挥发窑工艺(1)工艺原理及工艺过程简述净化钴渣中的锌、镉等比氢电位负的金属元素以及渣中的氢氧化物在稀硫酸的作用下,生成易溶于水的硫酸锌、硫酸镉而进入溶液中。
在浸出的过程中,通过控制浸出过程的温度、pH值以及浸出终点的pH值,抑制净化钴渣中钴、铜进入溶液中,从而实现锌、镉与钴、铜的分离。
通过选择性浸出锌、镉进入溶液中,再返回到浸出工序;钴、铜得以在浸出渣中得到富集。
为了充分回收浸出渣中的有价金属,采用挥发窑处理工艺。
湿法炼锌的要求

湿法炼锌的要求1、锌精矿焙烧应采用流态化焙烧炉。
2、浸出工序应采用连续浸出的机械搅拌槽。
3、浓密工序宜采用高效浓密机。
4、浸出渣过滤宜采用箱式压滤机、箱式隔膜压滤机和立式压滤机。
5、净化工序采用连续净化时,除铜、镉应采用机械搅拌槽,过滤设备宜采用箱式压滤机。
6、电积工序宜采用树脂混凝土电解槽,废液冷却应采用空气冷却塔。
7、大型湿法炼锌剥锌作业宜采用机械剥锌。
8、锌熔铸应采用低频感应电炉。
9、各种冶金炉窑不应设置备用。
10、浸出搅拌槽不宜设置备用。
11、浓密机不宜设置备用。
12、湿法炼锌主要工艺设备选择的技术参数应符合下列规定:(1)流态化焙烧炉床能力应为6.0t/h~7.5t/h。
(2)焙砂浸出应符合下列规定:1)传统浸出工艺中性浸出时间应为1.5h~4h,酸性浸出时间应为3h~4h;2)热酸浸出工艺中的黄钾铁矾法,中性浸出时间应为1.5h~4h,Ⅰ段酸浸时间应为3h~4h,Ⅱ段酸浸时间应为4h~5h,沉矾时间应为5h~6h。
低污染黄钾铁矾法的中性浸出时间应为1.5h~4h,预中和时间应为2h~4h,低污染沉矾时间应为5h~6h,高酸浸出时间应为3h~5h,针铁矿法的酸性浸出时间应为2 h~3h,高酸浸出时间应为3h~4h,超酸浸出应为4h~5h,还原时间应为3h~4h,氧化沉铁时间应为3h~6h;3)氧化锌浸出及富集铟过程的酸性浸出时间应为2h~3h,高酸浸出时间应为5 h~6h,锌粉置换铟的时间应为3h~4h。
(3)浓密与过滤应符合下列规定:1)传统浸出浓密主要技术参数应符合表7.7.12-1的规定;表7.7.12-1 传统浸出浓密主要技术参数2)传统浸出过滤的过滤能力应符合表7.7.12-2的规定;表7.7.12-2 传统浸出过滤的过滤能力[kg/(m2·h)]3)热酸浸出过滤的过滤能力应符合表7.7.12-3的规定;表7.7.12-3 热酸浸出过滤的过滤能力[kg/(m2·h)](4)三段锑盐(或砒霜)锌粉净化应符合下列规定:1)第一段净化反应时间应为1h~2h;2)第二段净化反应时间应为2.5h~3.5h;3)第三段净化反应时间应为1.0h~1.5h。
小型炼锌厂采用湿法炼锌工艺流程的选择和优化
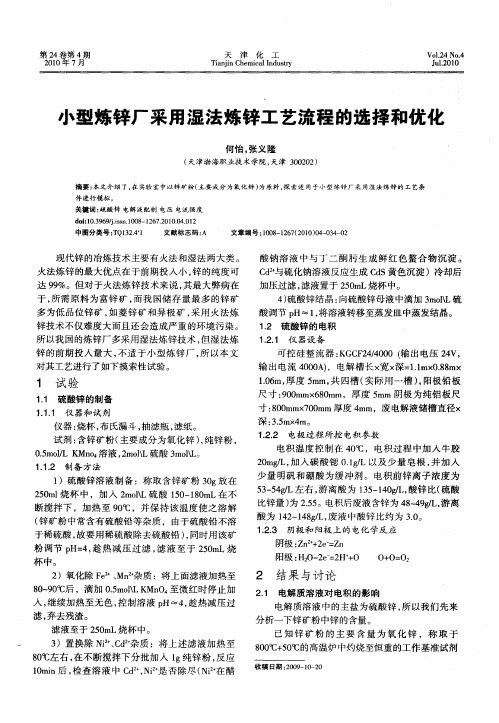
121 仪 器设 备 __
锌技术不仅难度大而且还会造成严重的环境污染。 所以我国的炼锌厂多采用湿法炼锌技术 , 但湿法炼 锌 的前 期 投入 量 大 , 不适 于小 型 炼 锌 厂 , 以本 文 所 对其工 艺进行 了如 下摸索 性试 验 。
1 试 验
122 电极过程 所控 电积 参数 ..
电积 温 度 控 制 在 4  ̄ 0C,电 积过 程 中加 入 牛胶
2 m / 加 人碳 酸锶 01/ 0 gL, . L以及 少 :称 取含 锌 矿 粉 3g放在 0
2 0 l 杯 中 ,加 入 2 o L硫 酸 1 0 10 5m 烧 ml \ 5 ~ 8 mL在不
于稀 硫酸 , 故要 用 稀硫 酸 除去 硫酸 铅 ) 同时用 该 矿 , 粉 调 节 p 4 趁 热 减 压 过 滤 , 液 至 于 2 0 L烧 H= , 滤 5m
杯中。
2 )氧 化除 F 、 n 杂 质 :将上 面滤 液加 热至 e M 8 ~ 0C ,滴加 0 m l Mn 0 9  ̄后 . o LK O 至微 红 时 停止 加 5 \ 入 , 续加 热 至无 色 , 制溶 液 p 4 趁 热减 压 过 继 控 H ,
深 :.m 4 3  ̄ m。 5
仪器 : 杯 , 氏漏 斗 , 滤瓶 , 烧 布 抽 滤纸 。
试剂 : 含锌 矿 粉 ( 主要 成分 为 氧化 锌 )纯 锌 粉 , , 0 mo L K o 溶液 ,mo L硫 酸 3 o\。 . l Mn4 5 / 2 l \ ml L
11 .. 制备 方法 2
11 硫酸锌 的 制备 .
11 1 仪 器 和 试 剂 ..
可控 硅 整 流 器 : G F44 0 输 出 电压 2 V, K C 2/00 f 4 输 出 电 流 4 0A ,电解 槽 长× × = .m 08mx 00 1 宽 深 1 x .8 1 1 6 厚度 5 . m, 0 mm, 四槽 ( 际用 一 槽 )阳极 铅 板 共 实 , 尺 寸 :0 m 60 m,厚 度 5 m 阴极 为纯 铝 板 尺 90 mx 8 m m 寸 :0 m x 0 m 80 m 70 m厚 度 4 m,废 电解液储 槽 直径X m
- 1、下载文档前请自行甄别文档内容的完整性,平台不提供额外的编辑、内容补充、找答案等附加服务。
- 2、"仅部分预览"的文档,不可在线预览部分如存在完整性等问题,可反馈申请退款(可完整预览的文档不适用该条件!)。
- 3、如文档侵犯您的权益,请联系客服反馈,我们会尽快为您处理(人工客服工作时间:9:00-18:30)。
湿法炼锌净化工艺的选择
广西来宾冶炼厂锌冶炼系统年产电锌3万t,为传统的湿法工艺流程,即:锌精矿-沸腾焙烧-焙砂硫酸浸出*浸出液净化—净化液电积—电锌。
2002 年3月开始技术改造扩建工程,使得电锌产量达到了年产6万t,在技术改造过程中,最关键的净化工艺拟采用三段连续净化取代改造前的两段间断净化。
因此,该工艺在生产中无论在设备上装置上还是在工艺操作中都引入了许多先进高效和适用的技术,有利于降低劳动强度、提高产率并实现生产过程的自动化控制。
1净化过程基本原理
1.1净化方法
净化过程是根据硫酸锌浸出液中不同的杂质及其含量,大多采用锌粉置换和加特殊试剂化学沉淀的方法将溶液中杂质除去。
工厂根据锌焙砂中性浸出上清液的特点,选择釆用加锌粉置换的逆歸净化方法。
1.2置换原理
置换是一种氧化还原反应,置换的热力学过程可用金属活泼性的大小或电子得失的难易等来定性描述,中性浸出上清液锌粉置换反应为:
MeSO4 + Zn = Z11SO4 + Me I
置换过程中金属的平衡电位如表1所示。
表1置换过程中金属的平衡电位(298 K) V
电极反应E°E平衡
Zn2* +2e=Zn■0.763-0.752(150 g/L)
Cd2* +2e=Cd-0.403-0.752(2xl0-7mg/L)
Cu2+ +2e= Cu+ 0.337-0.752(3.18x 10-35 mg/L)
Co2+ +2e=Co-0.227-0.752(5 x IQ-12 mg/L)
Ni2+ +2e=Ni-0.250-0.752( 1.5x 10-17 mg/L)
SbH3 = Sb+3H+ +3e+ 0.510+ 0.752(pH = 4, Pgb% = 202.65 Pa)
A S H3 = As+ 3H*
+3e+ 0.600+0.752(P H=4,P A1H3 = 202.65 Pa)
置换的动力学过程的反应机理:加入的锌粉作为微电池的阳极溶入液相,在那里发生水化作用,继而向溶液深处扩散并参与溶液的对流运动。
2三段连续净化工艺
2.1 一段锌粉置换除铜镉
一段净化过程为锌粉置换除铜和镉,操作温度在40 ~ 50Y,机械搅拌,反应原理为:
Zn + C11SO4 = Z11SO4 + Cu 寸
Zn + CdSOq = Z11SO4 + Cd 1
由表1可知,在理论上加锌粉置换除Cu、Cd是可行的。
但在实际生产中,一段除Cu、Cd 后,置换下来的Cd会有复溶现象产生,引起复溶的主要原因一般认为有两个:其一是化学溶
解,置换下来的金属与溶解在溶液中的空气接触,导致了镉的氧化溶解,且温度越高氧化溶解的速度越快,主要化学反应是:
2Cd + 02 = 2CdO
CdO + H2SO4 = CdSO4 + H20
其二是电化学溶解,溶液中具有比镉电极电位更正的金属离子(如Cu、Fe)导致镉的电化学溶解,其主要反应是:
Cd + Cu2+ = Cd2+ + Cu
Cd + 2Fe3+ =Cd2+ +2Fe2+
另外,在生产实践中,有的厂家在除Cu、Cd过程中,需加入适当的CuS04,这是为了强化锌粉对镉的置换作用,当溶液中[Cu2+]:[Cd2+] = l:3时,除镉的效果最佳,经过一段净化除Cu、Cd后,新液的铜镉含量基本可以达到电解的要求。
2.2二段铺盐高温除碑、锋、钻
除铜镉后的一段净化液含有碑、钟、钻等,需要进一步处理除杂,即将溶液温度升至80 - 90 加镣盐(锌粉活化剂Sb2()3),机械搅拌,反应原理为:
As + 3H+ +3e = AsH3 f Sb + 3H+ +3e=SbH3 f Zn + Co2+ = Zn2+ + Co I 由表1同样可知,在理论上加锌粉置换除As、Sb 是可行的,但在除Co时,有文献表明,因为Co属于过渡元素中的铁元素,它在溶液中析出时有超电压现象发生,而且温度越低,相应的析出超电压越大;同时,在pH = 5~5.4的中性溶液中,氢在钻上的析出电位约为-0.5-0.6 V,由于I碇I v I砖I,将使C°2,置换无法进行;当加入锌粉时,置换反应发生在锌和氢之间,即锌粉进行简单的溶解。
因而,要使置换除钻正常进行,就需要加入特殊的试剂SbzCh,当加入Sb2O3禅盐时,锌粉将更正的歸离子置换出来,此时歸与钻之间形成一系列金属化合物,如CoSb.CoSbz等。
由于氢在镑上的超电压较高,从而抑制了氢离子放电,这些金属化合物与锌粉颗粒组成微电池,钻将得到电子而析出。
温度和离子浓度对Ezn和Ec•的影响列于表2。
由表2可知,随着温度的升高,IE Zn l和IE S I 都减少,且IE/I减少的比例远大于lEz」减少的比例, 使lEznl与lEcJ的差值随温度的升高而增大,有利于锌粉除C。
,所以应该保持高温。
另外,随离子浓度的降低I Ezn I与I Eco I的值都增加,所以当中上清中的锌离子愈高,而要达到深度净化除钻,这个过程就会愈难进行。
因此,综合溶液的温度、离子浓度和形成微电池的阴极金属对析出电位的影响,除Co 必须在高温(80 Y以上)和添加锌粉活化剂的反应过程中,才能使溶液达到深度净化。
表2温度和离子浓度对Ezn和E&的影响
电极离子浓度
/g'L-1
E/N
25 r50 r75 Y
2.9-0.769-0.750-0.730
Zn /Zn 1.53-0.800-0.780-0.747
0.5-0.510-0.420-0.346
Co2*/Co 3.4 x-0.75—0.58 ~-0.45 -
IO4以上-0.52-0.40
2.3三段适温除残镉
经过一段和二段净化后,溶液中Cu、Cd、As、Sb、Co已经基本达到新液的要求,但为了进一步消除镉对新液质量的影响,第三段可以采取适温加锌粉除复溶镉,反应原理为:
Zn + CdS()4 = Z11SO4 + Cd I
3来宾冶炼厂工艺
3.1中上清含貴
来宾冶炼厂中上清含量情况列于表30
中上清液Zn紛
-- T .
%03、Zn粉一母液一净灣t=-^=r-co)
I 二段高^EI^CO、As、sT~|
1
(成收Co)
「三段I
I压混I
------------ 1
部.做三净渣
~~ (^ST®@iRCd)
I费冷血冷却I
送电解
图1工艺流程图
一段中已除去镉,减少了镉进入钻渣量,镉的回收率较其他净化方法高,可达60%以上;(2)铜、镉除去后,加歸除钻的效果更好,含钻量高达15-20 tng/L 时也能达到好的净化效果;(3)净化中产生的SbH3 容易分解,产生剧毒气体的危害性较小,劳动条件大为改善;(4)歸的活性大,添加剂消耗少,可以降低生产成本。
由于逆保盐净化方法具有上述优点,故该法在湿法炼锌厂得到广泛应用。
其工艺过程是:第一段在50 - 60 Y时加锌粉除Cu、Cd, —般锌粉的加入量是理论量的2倍,所产出的送综合回收。
一段净化后的过滤溶液通过加热升温到85 Y左右,加入锌粉和禅活化剂除钻、保等杂质,过滤后的净化渣用于回收金属钻。
第三段净化假如锌粉除残余的杂质,得到含锌较高的净化渣返回一段除铜、镉。
采用该净化方法净化后溶液中的Cu、Cd、Co的含量都可以降到1 mg/L以下,电锌质量明显提高,能耗降低。
3.目前成熟采用低-高-中的工艺流程的厂家有:西北白银铅锌冶炼厂、株州冶炼厂二系统、比利时巴比伦电锌厂等。
4.笔者偏向于采用低-高-中的逆歸净化工艺流程,首先该流程比较成熟,其次,低-高-中
的逆歸净化工艺有利于在第一阶段将杂质Cu、Cd基本置换下来,不会存在添加CuSO4除Cd 的问题;同时, Cu、Cd杂质一次置换下来,富集程度较高,有利于综合回收,并且有利于Co渣的富集回收。