湿法电解锌工艺流程选择概述
湿法冶锌工艺流程

湿法冶锌工艺流程
1.浸出:将含锌矿石(多为氧化锌矿石)研磨成一定粒度的粉末,然后与硫酸等溶液混合,通过浸出反应将锌溶解出来。
浸出反应一般可以分为两个步骤:首先是矿石的颗粒与溶液之间的扩散过程,然后是锌离子在溶液中的化学反应。
2.过滤:将浸出溶液中的固体杂质物通过过滤器进行过滤,得到含锌的滤液。
过滤是一个重要的步骤,它可以有效地去除溶液中的固体杂质,防止后续工艺发生堵塞和设备磨损。
3.净化:通过净化工艺,将滤液中的铁、铜、镉等杂质去除,以获得纯度更高的锌溶液。
常用的净化方法有镉精萃取法、铜脱除法、硫酸铁脱除法等。
4.电积:将经过净化的锌溶液通过电解槽进行电积操作,使锌离子在阳极上还原成金属锌,在阴极上沉积。
电积是将溶液中的锌还原成金属锌的最主要方法,通常使用铅和钢板作为阴极,将锌电积出来。
5.脱水:将电积出来的锌板通过烘干设备进行脱水处理,去除残留的水分,使锌板干燥。
6.熔炼:将脱水后的锌板送入熔炼炉中进行熔炼操作,将锌板熔化成液态锌。
通常采用间歇式熔炼,将锌板在炉中加热至熔点以上,使锌融化成液态,然后通过出铅孔排出熔化后的锌液。
7.精炼:通过精炼设备,对锌液进行精炼操作,以提高锌的纯度。
精炼一般采用电解精炼法,通过电解槽将锌液中的杂质去除,得到高纯度的锌。
8.出锌:将精炼后的锌液通过真空蒸馏或其他方法,将铅和其他低沸点杂质从锌液中蒸馏除去,最终得到纯度达到要求的锌。
总的来说,湿法冶锌工艺流程是一个包括浸出、过滤、净化、电积、脱水、熔炼、精炼和出锌等多个步骤的过程。
通过这些步骤的处理,可以从含锌矿石中提取出纯度较高的锌,用于各种工业应用。
锌的湿法冶金

锌的湿法冶金
锌的湿法冶金指的是通过化学反应将锌矿石转化为锌金属的一种冶金
方法。
这种方法利用锌矿石的可溶性,将其溶解在酸、碱或盐酸等溶解剂中,然后通过化学反应将其转化为锌盐。
随后,采用电化学或热还原等方
法将锌盐还原为锌金属。
锌的湿法冶金包括以下步骤:
1.矿石破碎和浸出:锌矿石首先经过破碎、粉碎和筛分,将其粉碎成
一定的颗粒度。
然后将矿石浸入溶剂中,以便将其中的锌元素溶解出来。
2.锌盐制备:浸出液中的锌元素经过一系列化学反应,形成锌盐。
不
同种类的溶剂和反应条件会产生不同的锌盐类型。
3.锌盐还原:对于某些类型的锌盐,可以通过电化学或热还原方法将
其还原为锌金属。
电化学还原需要使用电解池,经过一定的电流和电压作用,将锌离子还原为金属锌。
热还原是将锌盐加热至一定温度,使得其中
的锌离子还原为金属锌。
4.精炼和铸造:通过还原后的锌金属可制备成各种形式的工业用锌,
包括锌片、锌丝、锌棒、锌管等。
这些制品可进一步加工成各种锌合金制品。
锌的湿法冶金相比于传统的干法冶金具有很多优点,如能够溶解所有
类型的锌矿石、锌盐产生速度快、产品质量更稳定等。
在现代工业生产中,湿法冶金已成为主流的锌生产方式。
毕业设计 锌电解车间的工艺流程和生产方法

第一章绪论1.1 锌的历史世界上最早发现并使用锌的是中国,在10-11世纪中国是首先大规模生产锌的国家。
明朝末年宋应星所著的《天工开物》一书中有世界上最早的关于炼锌技术的记载。
1750~1850年人们已开始用氧化锌和硫化锌来治病。
1869年Raulin发现锌存在于生活机体中,并为生活机体所必需。
1963年报告了人体的锌缺乏病,于是锌开始列为1869年Raulin发现锌存在于生活机体中,并为生活机体所必需。
锌的生产过程非常简单,将炉甘石(即菱锌矿石)装满在陶罐内密封,堆成锥形,罐与罐之间的空隙用木炭填充,将罐打破,就可以得到提取出来的金属锌锭。
另外,我国化学史和分析化学研究的开拓者王链(1888—1966)在1956年分析了唐、宋、明、清等古钱后,发现宋朝的绍圣钱中含锌量高,提出中国用锌开始于明朝嘉庆年间的正确的科学结论。
锌的实际应用可能比《天工开物》成书年代还早。
1.2 性质及其用途1.锌的物理性质锌是白略带蓝灰色的金属,它的物理性质特点为熔点和沸点都较低,质软,有展性。
但加工后则变硬,熔化后的流动性良好。
锌的相对原子质量为65.37。
熔点为419.505℃。
沸点为906.97℃。
密度在20℃时为7.133g/cm3。
500℃时为6.58g/cm3。
800℃时为6.22g/cm3。
2O℃时比热为25.0236J/(mol.k)。
熔化热为7386J/mol。
气化热为114754J/mol。
莫氏硬度为2.5。
锌有三种结晶状态:α、β和γ锌,其同质异形变化温度为170℃和330℃。
在熔点附近的锌蒸气压很小,但液态锌蒸汽压随温度升高而急增,906.97℃时即达103125Pa,这是火法炼锌的基础。
2.锌的化学性质锌在常温下不被干燥的氧或空气所氧化,在潮湿空气中往往形成一层灰白色的致密碱式碳酸锌ZnCO3.3Zn(OH)2而防止了锌的继续被侵蚀。
熔融的锌能与铁形成化合物并保护了钢铁,此一特点被用在镀锌上。
锌的制造工艺
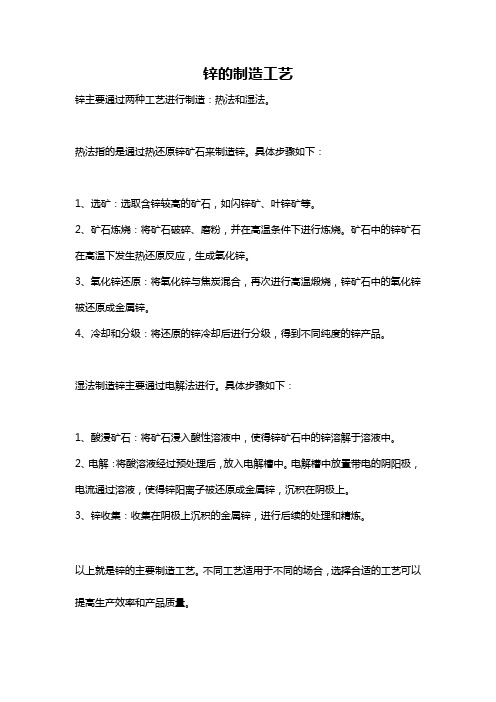
锌的制造工艺
锌主要通过两种工艺进行制造:热法和湿法。
热法指的是通过热还原锌矿石来制造锌。
具体步骤如下:
1、选矿:选取含锌较高的矿石,如闪锌矿、叶锌矿等。
2、矿石炼烧:将矿石破碎、磨粉,并在高温条件下进行炼烧。
矿石中的锌矿石在高温下发生热还原反应,生成氧化锌。
3、氧化锌还原:将氧化锌与焦炭混合,再次进行高温煅烧,锌矿石中的氧化锌被还原成金属锌。
4、冷却和分级:将还原的锌冷却后进行分级,得到不同纯度的锌产品。
湿法制造锌主要通过电解法进行。
具体步骤如下:
1、酸浸矿石:将矿石浸入酸性溶液中,使得锌矿石中的锌溶解于溶液中。
2、电解:将酸溶液经过预处理后,放入电解槽中。
电解槽中放置带电的阴阳极,电流通过溶液,使得锌阳离子被还原成金属锌,沉积在阴极上。
3、锌收集:收集在阴极上沉积的金属锌,进行后续的处理和精炼。
以上就是锌的主要制造工艺。
不同工艺适用于不同的场合,选择合适的工艺可以提高生产效率和产品质量。
湿法炼锌净化工艺的选择

湿法炼锌净化工艺的选择广西来宾冶炼厂锌冶炼系统年产电锌3万t,为传统的湿法工艺流程,即:锌精矿-沸腾焙烧-焙砂硫酸浸出*浸出液净化—净化液电积—电锌。
2002 年3月开始技术改造扩建工程,使得电锌产量达到了年产6万t,在技术改造过程中,最关键的净化工艺拟采用三段连续净化取代改造前的两段间断净化。
因此,该工艺在生产中无论在设备上装置上还是在工艺操作中都引入了许多先进高效和适用的技术,有利于降低劳动强度、提高产率并实现生产过程的自动化控制。
1净化过程基本原理1.1净化方法净化过程是根据硫酸锌浸出液中不同的杂质及其含量,大多采用锌粉置换和加特殊试剂化学沉淀的方法将溶液中杂质除去。
工厂根据锌焙砂中性浸出上清液的特点,选择釆用加锌粉置换的逆歸净化方法。
1.2置换原理置换是一种氧化还原反应,置换的热力学过程可用金属活泼性的大小或电子得失的难易等来定性描述,中性浸出上清液锌粉置换反应为:MeSO4 + Zn = Z11SO4 + Me I置换过程中金属的平衡电位如表1所示。
表1置换过程中金属的平衡电位(298 K) V电极反应E°E平衡Zn2* +2e=Zn■0.763-0.752(150 g/L)Cd2* +2e=Cd-0.403-0.752(2xl0-7mg/L)Cu2+ +2e= Cu+ 0.337-0.752(3.18x 10-35 mg/L)Co2+ +2e=Co-0.227-0.752(5 x IQ-12 mg/L)Ni2+ +2e=Ni-0.250-0.752( 1.5x 10-17 mg/L)SbH3 = Sb+3H+ +3e+ 0.510+ 0.752(pH = 4, Pgb% = 202.65 Pa)A S H3 = As+ 3H*+3e+ 0.600+0.752(P H=4,P A1H3 = 202.65 Pa)置换的动力学过程的反应机理:加入的锌粉作为微电池的阳极溶入液相,在那里发生水化作用,继而向溶液深处扩散并参与溶液的对流运动。
电解锌车间工艺流程
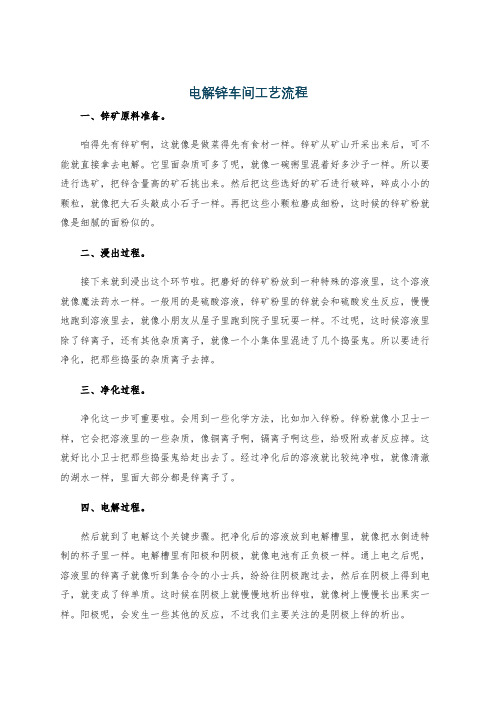
电解锌车间工艺流程一、锌矿原料准备。
咱得先有锌矿啊,这就像是做菜得先有食材一样。
锌矿从矿山开采出来后,可不能就直接拿去电解。
它里面杂质可多了呢,就像一碗粥里混着好多沙子一样。
所以要进行选矿,把锌含量高的矿石挑出来。
然后把这些选好的矿石进行破碎,碎成小小的颗粒,就像把大石头敲成小石子一样。
再把这些小颗粒磨成细粉,这时候的锌矿粉就像是细腻的面粉似的。
二、浸出过程。
接下来就到浸出这个环节啦。
把磨好的锌矿粉放到一种特殊的溶液里,这个溶液就像魔法药水一样。
一般用的是硫酸溶液,锌矿粉里的锌就会和硫酸发生反应,慢慢地跑到溶液里去,就像小朋友从屋子里跑到院子里玩耍一样。
不过呢,这时候溶液里除了锌离子,还有其他杂质离子,就像一个小集体里混进了几个捣蛋鬼。
所以要进行净化,把那些捣蛋的杂质离子去掉。
三、净化过程。
净化这一步可重要啦。
会用到一些化学方法,比如加入锌粉。
锌粉就像小卫士一样,它会把溶液里的一些杂质,像铜离子啊,镉离子啊这些,给吸附或者反应掉。
这就好比小卫士把那些捣蛋鬼给赶出去了。
经过净化后的溶液就比较纯净啦,就像清澈的湖水一样,里面大部分都是锌离子了。
四、电解过程。
然后就到了电解这个关键步骤。
把净化后的溶液放到电解槽里,就像把水倒进特制的杯子里一样。
电解槽里有阳极和阴极,就像电池有正负极一样。
通上电之后呢,溶液里的锌离子就像听到集合令的小士兵,纷纷往阴极跑过去,然后在阴极上得到电子,就变成了锌单质。
这时候在阴极上就慢慢地析出锌啦,就像树上慢慢长出果实一样。
阳极呢,会发生一些其他的反应,不过我们主要关注的是阴极上锌的析出。
五、锌的收集与后续处理。
等阴极上的锌积累到一定程度后,就可以把锌收集起来啦。
这时候的锌可能还不是特别规整,就像刚做好的小饼干形状有点奇怪。
所以可能还需要进行一些后续处理,比如熔炼啊,把收集到的锌再加热融化,然后铸造成我们想要的形状,就像把面团揉好再放进模具里做出漂亮的面包一样。
这样,从锌矿到最后的锌成品就完成了整个工艺流程啦。
湿法冶锌中性浸出电解沉积
湿法冶锌中性浸出电解沉积
引言:
一、原理:
二、工艺流程:
1.锌原料浸出:将锌原料浸入稀硫酸溶液中,通过加热和搅拌等方式将锌溶解成溶液中的锌离子。
2.电解沉积:用浸出溶液作为电解液,将阴极和阳极分别放入电解槽中,施加电流使锌离子在阴极上沉积成金属锌。
3.锌的回收:将电解沉积得到的金属锌进行收集和处理,以得到高纯度的锌产品。
三、设备:
1.浸出槽:用于将锌原料和浸出溶液进行反应和搅拌。
2.电解槽:用于进行电解沉积反应,其中放置有阴极和阳极。
3.电源:用于提供所需的电流,使锌离子在阴极上沉积成金属锌。
4.收集系统:用于收集和处理电解沉积得到的金属锌。
四、应用:
1.锌冶炼:通过湿法冶锌中性浸出电解沉积方法可以提取和生产金属锌,用于制备锌合金和锌制品。
2.锌回收:湿法冶锌中性浸出电解沉积可以将废弃物和废旧锌制品中的锌回收利用,减少资源浪费和环境污染。
结论:
湿法冶锌中性浸出电解沉积是一种有效的锌冶炼方法,通过该方法可以实现锌的提取和回收。
该方法的原理基于电解的原理,工艺流程包括锌原料浸出、电解沉积和锌的回收等步骤,并需要相应的设备支持。
该方法在锌冶炼和锌回收领域有广泛的应用。
电解锌工艺流程
电解锌工艺流程
《电解锌工艺流程》
电解锌是一种常见的金属表面处理技术,可以使锌以均匀的方式沉积在金属表面,以增强其耐腐蚀能力和美观度。
电解锌工艺流程通常包括以下几个步骤:
1. 准备工件
首先,需要对待处理的金属表面进行准备,包括去除油污、锈斑和其他杂质,以保证锌能够均匀地沉积在表面。
2. 酸洗处理
进行酸洗处理,以去除金属表面的氧化物和其他杂质,使表面变得干净、光滑,为后续的处理做好准备。
3. 电镀处理
将经过准备和酸洗处理的金属表面浸入含有锌离子的电解液中,通过电流引发化学反应,使锌离子沉积在金属表面上形成均匀的锌层。
4. 清洗处理
经过电镀处理后的工件需要进行清洗处理,以去除残留的电解液和其他杂质,保证表面的洁净度。
5. 烘干处理
最后,对清洗后的工件进行烘干处理,去除表面的水分,使锌层能够牢固地附着在金属表面上。
通过以上几个步骤,经过电解锌工艺处理的金属表面能够获得均匀、美观的锌层,不仅提高了金属的耐腐蚀能力,也提高了其外观质量。
因此,电解锌工艺流程在金属加工行业中得到了广泛的应用。
湿法锌工艺流程
湿法锌工艺流程
《湿法锌工艺流程》
湿法锌工艺是一种常用的提取锌的方法,它通常用于从含锌硫化物的矿石中提取锌。
下面将介绍一下湿法锌工艺的流程。
首先,矿石经过破碎和磨矿的过程,得到粉碎的矿石。
接着,将磨碎的矿石放入浸出槽中,加入硫酸和水,进行浸出反应。
在反应槽中,硫酸会与矿石中的锌化合物发生化学反应,生成硫酸锌溶液。
随后,将硫酸锌溶液送入电解槽,通过电解的方式提纯锌。
在电解槽中,将硫酸锌溶液进行电解,锌离子在电流的作用下会被还原成为金属锌,析出在阴极上。
同时,阳极上的氧化物会与水分解产生氧气。
最后,经过电解产生的金属锌会进行脱水和熔炼,得到最终的纯净金属锌产品。
同时,在整个工艺流程中,所产生的废水、废渣等也需要进行处理,以减少对环境的影响。
总的来说,湿法锌工艺流程是一个复杂但有效的提纯锌的方法。
通过破碎、浸出、电解和熔炼等步骤,可以从矿石中提取出高纯度的金属锌,为工业生产和其他领域的应用提供了可靠的原材料。
电解锌工艺流程
电解锌工艺流程电解锌是一种常用的金属表面处理工艺,可以为锌及其合金制品提供耐蚀性和装饰性的保护。
下面将详细介绍电解锌的工艺流程。
1. 清洗准备在进行电解锌之前,首先需要对待处理的锌制品进行清洗准备。
这是为了去除表面的油脂、灰尘和其他杂质,确保锌制品表面的清洁度和粗糙度符合要求。
常用的清洗方法有碱洗、酸洗和溶剂洗。
2. 酸洗酸洗是清洗准备的重要环节之一。
通过将锌制品浸泡在酸性溶液中,可以去除表面的氧化层和锈蚀物。
常用的酸洗溶液包括稀硫酸、稀盐酸和稀硝酸。
酸洗时间和温度需要根据锌制品的具体情况进行调整。
3. 预处理在酸洗之后,需要对锌制品进行预处理,以提高电解锌的效果。
预处理一般包括酸洗后再次清洗、酸中和和活化处理。
酸中和是为了中和酸洗残留在锌制品表面的酸性物质,活化处理则是为了提高锌制品表面的电导率,使电解过程更加顺利。
4. 电解锌电解锌是整个工艺流程的核心环节。
在电解槽中,将锌制品作为阳极,铅或铅合金作为阴极,通过外加电源的作用,使锌离子在阳极上溶解并沉积到阴极上。
锌制品经过电解锌处理后,表面会形成一层致密、均匀的锌层,提供了良好的耐蚀性和装饰性。
5. 清洗和后处理电解锌完成后,需要对锌制品进行清洗和后处理。
清洗是为了去除电解液和其他残留物,常用的清洗方法包括水洗和酸洗。
后处理一般包括中和、干燥和包装等步骤,以确保锌制品的质量和外观符合要求。
总结:电解锌工艺流程包括清洗准备、酸洗、预处理、电解锌和清洗后处理等步骤。
通过这些步骤,可以为锌制品提供耐蚀性和装饰性的保护。
电解锌工艺是一种常用的金属表面处理工艺,广泛应用于汽车零部件、建筑材料等领域。
- 1、下载文档前请自行甄别文档内容的完整性,平台不提供额外的编辑、内容补充、找答案等附加服务。
- 2、"仅部分预览"的文档,不可在线预览部分如存在完整性等问题,可反馈申请退款(可完整预览的文档不适用该条件!)。
- 3、如文档侵犯您的权益,请联系客服反馈,我们会尽快为您处理(人工客服工作时间:9:00-18:30)。
湿法电解锌工艺流程选择概述1.。
1 工艺流程选择根据原料成份采用常规的工艺流程,技术成熟可靠,劳动环境好,有较好的经济效益,同时综合回收铜、镉、钴等伴生有价金属。
工艺流程特点如下:(1)挥发窑产出的氧化锌烟尘一般含气氟、氯、砷、锑杂质,且含有较高的有机物,影响湿法炼锌工艺,所以通常氧化锌烟尘需先进多膛焙烧脱除以上杂质。
(2)氧化锌烟尘和焙砂需分别进行浸出,浸出渣采用回转窑挥发处理,所产氧化锌烟尘送多膛焙烧炉处理。
(3)氧化锌烟尘浸出液返焙砂系统,经中性浸出浓密后,上清液送净液车间处理,净液采用三段净化工艺流程。
(4)净化后液送往电解车间进行电解。
产出阴极锌片经熔铸后得锌锭成品。
(5)净液产出的铜镉渣和钴渣进行综合回收(或外卖)。
1.6.2 工艺流程简述焙砂经中浸、酸浸两段浸出、浓密、过滤,得到中浸上清液及酸浸渣。
酸浸渣视含银品位进行银的回收后送回转窑挥发处理得氧化锌,经脱氟、氯,然后进行单独浸出,浸液与焙砂系统的浸出液混合后送净液。
回转窑渣送渣场堆存。
产出的中浸上清液经三段净化,即第一段用锌粉除铜镉;第二段用锌粉和锑盐高温除钴;第三段再用锌粉除复溶的镉,以保证新液的质量,所得新液送电解。
电解采用传统的电解沉积工艺,用人工剥离锌片,剥下的锌片送熔铸,产出锌锭。
采用上述工艺流程的理由:主要是该工艺流程基建投资省,易于上马,建设周期短、见效快、效益高。
这在株冶后10万吨电锌扩建、广西、云南、贵州等多家企业的实践中,已得到充分证实和肯定。
对净液工艺的选择,目前国内外湿法炼锌净液流程的发展趋势,主要是溶液深度净化。
采用先冷后热的净液流程,为保证净液质量,设置三段净化,当第二段净化质量合格时,也可以不进行第三段净化,直接送电解。
该流程稳妥可靠,净化质量高,能满足生产0#锌和1#锌的新液质量要求。
作业制度,拟采用连续操作,国内西北冶、株冶等都有生产经验。
与间断操作相比,可大减少设备的容积,减少设备数量,相应可减少厂房建筑面积,故可大幅度降低基建投资。
1..3 综合利用及环境保护浸出渣可根据含银品位高低进行银的回收后再送回转窑处理,所得氧化锌经脱氟、氯后进入氧化锌浸出系统,进一步回收锌、铟等有价金属。
净液所得铜镉渣经低酸浸出后,所得铜渣可作为炼铜原料出售。
浸出液经锌粉置换,所得贫镉液含锌很高,返回锌浸出车间,所得海绵镉进一步处理后,获得最终产品镉锭出售。
净液所得钴渣,经酸洗脱锌后根据含钴品位再考虑是否回收钴,暂时先堆存(或外卖)。
熔铸所得浮渣,其粗粒可返回熔化或作生产锌粉用。
处理所得氧化锌可作为生产硫酸锌或氯化锌的原料,根据需求而定。
各湿法炼锌车间的污酸、污水,经中和沉处理后,可达到国家工业排放标准。
为合理使用电能,本设计根据国外电解工厂的经验,电流密度采用白天低(400A/ m2)夜间高(500A/ m2)的操作制度;根据比利时老山锌公司、日本的彦岛、饭岛、小鸣浜和安中等国外诸多10万吨/年以上电锌厂电解车间采用自然通风、局部强制通风和两班制剥锌的生产经验,本设计采用车间自然通风,所有可能产生酸雾的溜槽和贮槽均加盖并予以强制抽风,剥锌厂房局部强制通风,将酸雾对车间造成的污染降至最低水平。
综上所述,本设计不仅充分考虑了"三废"的有效治理,改善了环保条件,而且使之得到综合利用,提高了有价金属的回收率;2冶炼工艺设计采用成熟的工艺流程,技术落实可靠,劳动环境好,又有较好的经济效益,同时可综合回收铜、镉、钴等伴生有价金属。
焙砂送球磨后,分别经中浸、酸浸两段浸出、浓密、过滤,得到中浸上清夜及酸浸渣。
酸浸渣送回转窑挥发处理的氧化锌,经多膛焙烧炉脱氟、氯后进行单独浸出处理,中浸液返至浸出系统的中性浸出,氧化锌酸浸液用锌粉置换产出铟渣,留待进一步处理。
酸浸渣送渣场堆存,待回收Pb、Zn等有价金属。
浸出系统产出的中浸上清夜经三段净化,即第一段用锌粉除铜、镉,第二段用锌粉、锑盐除钴、镍,第三段用锌粉除残镉,所得净化后液即新液送往电解。
电解采用传统的电解沉积工艺,采用人工剥离锌片,剥下的锌片送熔铸,采用低频感应电炉熔锌,最终产出1#锌和部分0#锌的锌锭。
本设计金属回收率:锌93.5% 其中:浸出95%;净液99.3%;电解99.5%;熔铸99.7% 2.2 浸出2.2.1 工艺流程简述2.2.1.1 备料焙砂用刮板运输机送到浸出厂房内的料仓,由料仓锥底排出经星形给料器、称量给料机再进入中性浸出槽上的螺旋给料机,将焙砂送入浸出槽内。
从电解车间来的废电解液、阳极泥浆分别泵入废电解液贮槽和阳极泥搅拌槽。
净液工段来的各种含锌溶液和过滤干燥厂房来的过滤液及洗液均泵入混合液贮槽。
凝聚剂溶液的制备:在凝聚剂溶解槽中加入水并通蒸汽,控制温度40~60℃,逐渐加入凝聚剂,配制成1%的浓度,使用时用水稀释到0.1%浓度,存放在凝聚剂贮槽中,用泵送入各浓密机。
2.2.1.2 中性浸出中性浸出选用4台φ4500×5500机械搅拌槽,单槽反应间断作业。
将废电解液、阳极泥浆、混合液、MnO2矿粉分别给入中性浸出槽配液,控制始酸H2SO450~80g/l,Fe2+≤0.1g/l,然后加入焙砂,在加料时不断的用试纸测定槽内的酸度,保证中性浸出终点PH=5~5.2。
中性浸出矿浆由槽下部排出流入溜槽后进到中间槽,经泵打入1台φ18m中性浸出浓密机,其浓密溢流即为中浸上清夜,直接经溜槽流入中上清贮槽。
浓密机底流经泵送至酸性浸出槽。
2.2.1.3 酸性浸出酸性浸出槽与中性浸出槽规格相同,选用3台间断作业。
中浸底流泵入酸浸槽后,加入废电解液和浓硫酸,并通入蒸汽加热至75~85℃,控制浸出终点PH=2~3。
酸性浸出矿浆由槽下部排出经溜槽和泵槽打入1台φ15m酸性浸出浓密机,其浓密底流经中间槽泵送到渣过滤干燥工段,选用3台F=100m2带隔膜的压滤机压滤,所得滤渣经皮带运输机送到火法的给料系统,给入干燥窑。
其浓密溢流返回中性浸出。
2.2.1.4 氧化锌中性浸出氧化锌中性浸出选用1台φ4500×5500机械搅拌槽,间断作业。
浸出渣在火法车间经干燥、挥发产出氧化锌,经多膛焙烧炉脱硫、氯后,通过圆盘给料机送入1台湿式溢流球磨机,该球磨机规格为φ1200×2400,磨矿液来自渣滤干燥工段的压滤液和洗液,与氧化锌一同进入球磨机,磨矿的氧化锌矿浆经中间贮槽泵送到浸出车间的氧化锌中性浸出槽,同时加入废电解液,控制浸出终点酸度PH=4.8~5.2。
浸出后矿浆泵送至1台φ15m氧化锌中浸浓密机进行液固分离,浓密溢流经槽泵送至混合液贮槽,浓密机底流泵送入氧化锌酸性浸出槽。
2.2.1.5 氧化锌酸性浸出氧化锌酸性浸出选用1台φ4500×5500机械搅拌槽,间断作业。
氧化锌中浸底流、废电解液和浓硫酸同时加入槽中,浸出始酸H2SO4150~200g/l,控制浸出终酸20g/l左右,然后泵入1台φ15m氧化锌酸浸浓密机进行液固分离,浓密溢流经中间槽泵送至铟富(置换)槽用锌粉置换后再经压滤机压滤,所得滤渣即铟渣,待进一步处理得精铟。
滤液返回氧化锌中浸槽。
浓密机底流泵至1台F=100m2压滤机压滤,所得滤液返回氧化锌中性浸出槽,所得的滤渣经浆化用1台F=100m带隔膜的压滤机压滤洗涤后由气动排渣料斗卸入渣车,运送渣场。
2.2.2 主要技术操作条件2.2.2.1 中性浸出浸出液固比10:1浸出温度65~75℃浸出时间1~2h浸出终点酸度PH=5~5.22.2.2.2 酸性浸出浸出液固比10:1浸出温度75~85℃浸出时间2~4h浸出终点酸度PH=2~32.2.2.3 氧化锌中性浸出浸出液固比6~8.1浸出温度65~75℃浸出时间1~1.5h浸出终点酸度PH=4.8~5.22.2.2.4 氧化锌酸性浸出浸出液固比5~6.1浸出温度80~90℃浸出时间6~8h浸出始酸150~200g/lH2SO4浸出酸20g/lH2SO42.2.2.5 锌粉置换置换温度75~85℃置换时间3~4h始酸20g/lH2SO4终酸PH=4.8~5.02.2.3 主要技术经济指标2.2.3.1 焙砂锌浸出率85~90%2.2.3.2 浸出渣率~40%(以焙烧料计)2.2.3.3 上清夜产量33~34m3/h2.2.3.4 浸出渣量18240t/a(干量)2.2.3.5 氧化锌浸出渣量~2100t/a(干量)2.2.3.6 铟渣量112t/a(干量)主要成分In≥3%2.2.3.7 原材料单耗硫酸(98%H2SO4)120kg/t析出锌锰矿粉(MnO275%)15kg/t析出锌凝聚剂(3#)1kg/t析出锌蒸汽(0.2~0.3MPA)0.85t/t析出锌生产水 4.7m3/t析出锌2.3.1 工艺流程简述由浸出送来的中浸上涉清液泵入一段净化槽,一段净化槽共2台,规格为φ4500×5500,V=87m3/台,两台并联间断操作。
锌粉经振动给料机加入一段净化槽,反应完成后排料至中间槽,再用泵送至3台F=100m2 的厢式压滤机进行液固分离,所得滤渣即铜镉渣,经浆化后泵至镉工段回收镉。
所得滤液经2台F=30m2 的螺旋板加热器加温到85~90℃后经加热后液贮槽送往二段净化槽。
二段净化槽共4台,规格同一段净化槽,也是4台并联间断操作。
锌粉经振动给料机加入各净化槽,酒石酸锑钾溶液用人工加入槽内,反应完成后排料至中间槽,再用泵送至3台F=100m2的厢式压滤机压滤,所得滤渣即钴渣,再经酸洗、压滤后,所得滤渣即钴精矿,暂堆存待回收钴。
滤液用锌粉、酒石酸锑钾沉钴后,再经压滤,滤渣与钴精矿卸在同一堆场,滤液送浸出车间。
二段净化压滤后液送往三段净化槽。
三段净化槽共2台,规格也同一段净化槽,两台并联间断操作。
锌粉经振动料机加入槽内,以除去残余的镉。
反应完成后排料至中间槽,再用泵送至3台F=100m2的厢式压滤机压滤,所得滤渣含锌较高,用人工返回到一段净化槽再利用。
所得滤液即新液,用废电解液使新液含H2SO4l~3g/l ,减少新液在输送过程中的结晶,然后用泵送往电解车间。
净液工段产出的铜镉渣经浆化后,送往镉工段2台φ3000×3200,V=24m3机械搅拌槽进行铜镉渣的浸出,两台并联间断操作。
加入废电解液,控制始酸10g/l,终点PH=5.2~5.4。
矿浆经中间槽用泵送至1台F=40m2的厢式压滤机压滤,滤液送置换槽,产出滤渣即铜渣,可作为中间产品出售。
置换在1台φ3000×3200,V=24m3机械搅拌槽进行,置换前加入硫酸,控制溶液PH=2~3,以溶解锌粉表面的氧化锌膜,增加锌粉活性,加速置换速度。
置换后液用泵送至1台F=40m2的厢式压滤机压滤,产出滤液即贫镉液,用泵送回浸出车间。
所得滤渣即海绵镉,可作中间产品出售。