Manufacturing Processes Report(发动机制造工艺)
发动机再制造零部件的生产工艺及检测
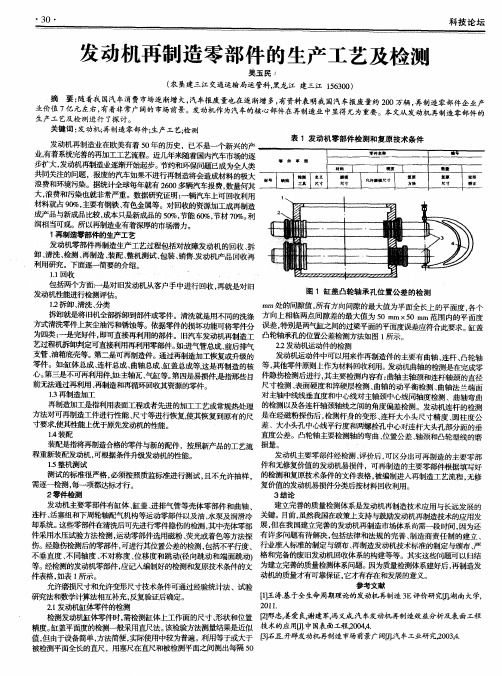
3 0・
科技 论坛
发动机再制造 零部件 的垦建三江交通运输局运 管科, 黑龙 江 建三江 1 5 6 3 0 0 )
值 : 摹 : 耋 着 烹 我 . 有 望 黄 专 非 ; 广 费 市 阔 场 的 警 市 渐 场 前 增 景 大 , 汽 车 报 废 量 也 在 逐 渐 增 多 , 有 资 料 表 明 我 国 汽 车 报 废 量 约 2 0 0 万 辆 , 再 制 造 零 部 件 企 业 产 生 产 发 动 机 作 为 汽 车 的 核 心 部 件 在 再 制 造 业 中 显 得 尤 为 重 要 。 本 文 从 菱 建 未
大, 浪费和污染也就非常严重。数据研究证明 : 一辆汽车上可 回收利用
、 l
材料 就占9 0 % , 主 要有 钢 铁、 有色 金属 等。 对回 收的 资 源加 工成再 制造
润 相当可 观。 所以 再制 造业 有着 深厚 的 市场 潜力。
斧=====}==== =
.
,
雪
… . 。
工 艺 及检 测进 行 了探 讨 。
‘ 。’ 。
…
堡 垫 造 业 在 欧 美 有 着 5 0 年 的 历 史 , 已 不 是 一 个 新 兴 的 产 — — 。 兰
竺竺 竺
步 扩 霎 大 , 发 动 机 葡 韫 隧 业 逐 渐 开 始 起 步 。 节 约 和 环 保 葛 问 麓 题 已 嚣 成 为 全 人 类 ~~ ’ 卜 _ 1 _ 一 三 — — 竿 T ; 1 一 浪 费 和 环 境 污 染 。 据 统 计 篡 全 球 鎏 每 行 年 萄 洧 2 6 0 0 多 辆 汽 车 报 费 , 数 量 何 其 : 二 l 二 二 j 匝盛王蕈 J I I : : : 二 I 二 : : l 竺
制造业发展报告 英文版
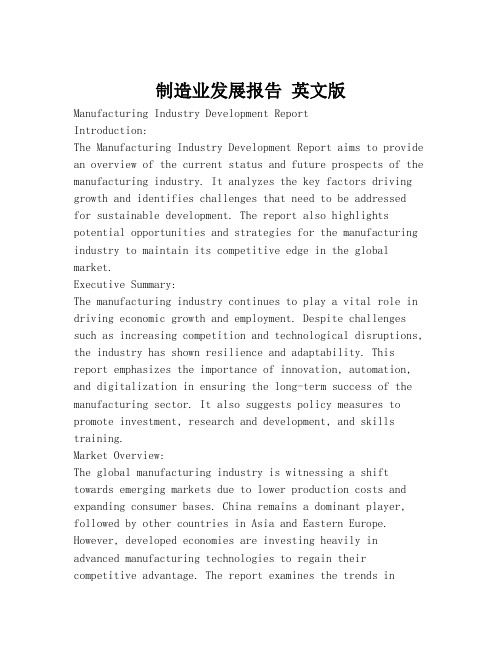
制造业发展报告英文版Manufacturing Industry Development ReportIntroduction:The Manufacturing Industry Development Report aims to provide an overview of the current status and future prospects of the manufacturing industry. It analyzes the key factors driving growth and identifies challenges that need to be addressedfor sustainable development. The report also highlights potential opportunities and strategies for the manufacturing industry to maintain its competitive edge in the global market.Executive Summary:The manufacturing industry continues to play a vital role in driving economic growth and employment. Despite challenges such as increasing competition and technological disruptions, the industry has shown resilience and adaptability. This report emphasizes the importance of innovation, automation, and digitalization in ensuring the long-term success of the manufacturing sector. It also suggests policy measures to promote investment, research and development, and skills training.Market Overview:The global manufacturing industry is witnessing a shift towards emerging markets due to lower production costs and expanding consumer bases. China remains a dominant player, followed by other countries in Asia and Eastern Europe. However, developed economies are investing heavily in advanced manufacturing technologies to regain their competitive advantage. The report examines the trends indifferent manufacturing sectors, including automotive, electronics, textiles, and pharmaceuticals.Key Drivers of Growth:Innovation and technological advancements are major drivers of growth in the manufacturing industry. The adoption of Industry 4.0 principles, such as the Internet of Things, artificial intelligence, and robotics, is revolutionizing production processes and improving efficiency. The report highlights the role of research and development in fostering innovation and the need for collaboration between industry and academia.Challenges and Strategies:The manufacturing industry faces various challenges,including skilled labor shortages, changing consumer preferences, and environmental regulations. The report proposes strategies such as upskilling the workforce, adopting sustainable manufacturing practices, anddiversifying product offerings to meet changing market demands. It also emphasizes the importance of government support in creating a favorable business environment and incentivizing investment in R&D.Opportunities for Growth:The report identifies several opportunities for the manufacturing industry to capitalize on emerging trends. This includes the growing demand for eco-friendly and sustainable products, the rise of e-commerce, and the potential of additive manufacturing. By embracing these opportunities and adapting to changing market dynamics, manufacturers can gain a competitive edge and expand their market share. Conclusion:The Manufacturing Industry Development Report providesinsights into the current challenges and opportunities in the manufacturing sector. It emphasizes the need for continuous innovation, digitalization, and sustainable practices to ensure long-term growth. By implementing the suggested strategies and leveraging emerging opportunities, the manufacturing industry can achieve sustainable development and contribute to overall economic growth.。
汽修产品制作流程作文英语
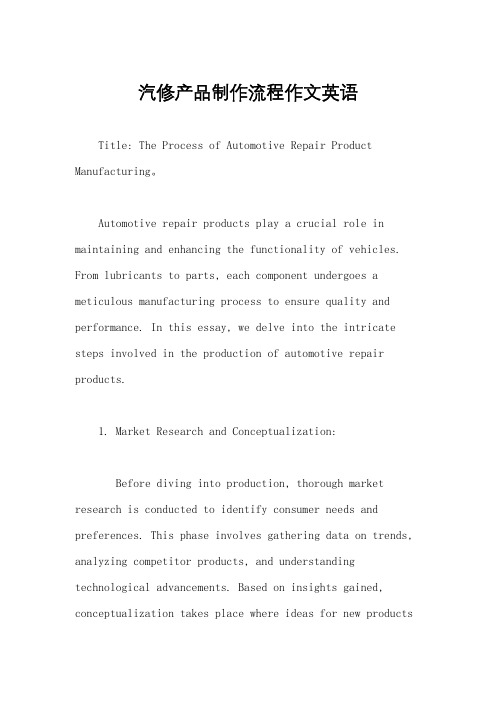
汽修产品制作流程作文英语Title: The Process of Automotive Repair Product Manufacturing。
Automotive repair products play a crucial role in maintaining and enhancing the functionality of vehicles. From lubricants to parts, each component undergoes a meticulous manufacturing process to ensure quality and performance. In this essay, we delve into the intricate steps involved in the production of automotive repair products.1. Market Research and Conceptualization:Before diving into production, thorough market research is conducted to identify consumer needs and preferences. This phase involves gathering data on trends, analyzing competitor products, and understanding technological advancements. Based on insights gained, conceptualization takes place where ideas for new productsor improvements to existing ones are brainstormed.2. Design and Development:Once a concept is finalized, the design phase begins. This step involves creating detailed specifications for the product, including dimensions, materials, and functionality. Engineers and designers collaborate to develop prototypes that undergo rigorous testing for durability, performance, and safety. Iterative improvements are made based on test results until the product meets quality standards.3. Sourcing Raw Materials:Raw materials are sourced from reputable suppliersto ensure consistency and quality. These materials vary depending on the type of automotive repair product being manufactured. Common materials include metals, plastics, rubber, lubricants, and electronic components. Manufacturers establish partnerships with suppliers to guarantee timely delivery and maintain a steady supply chain.4. Manufacturing Process:The manufacturing process varies depending on the complexity of the product. For simple components like oil filters or spark plugs, automated assembly lines are employed for efficiency and precision. More intricate products such as engine parts may require specialized machinery and skilled labor for manufacturing. Quality control measures are implemented at every stage to identify and rectify any defects.5. Packaging and Labeling:Packaging plays a vital role in protecting the product during transportation and storage. Manufacturers design packaging that is both durable and visually appealing, incorporating branding elements and product information. Labeling is done in accordance with regulatory standards, including safety warnings, usage instructions, and compliance certifications.6. Distribution and Marketing:Once manufactured and packaged, the products are ready for distribution. Manufacturers work withdistributors and retailers to ensure widespreadavailability in automotive stores and online marketplaces. Marketing efforts are employed to raise awareness and promote the product's features and benefits through advertising, endorsements, and digital campaigns.7. Customer Feedback and Continuous Improvement:Feedback from customers is invaluable foridentifying areas of improvement and addressing any issuesor concerns. Manufacturers actively solicit feedbackthrough surveys, reviews, and customer support channels. This feedback loop allows for continuous improvement, whether it's refining product design, enhancing performance, or optimizing manufacturing processes.In conclusion, the manufacturing process of automotive repair products is a multifaceted journey that requiresmeticulous planning, precise execution, and continuous innovation. From initial concept to final product, each step is crucial in delivering high-quality products that meet the needs of consumers and contribute to the efficiency and reliability of vehicles.。
国开形成性考核《管理英语(3)》单元自测(7)试题及答案
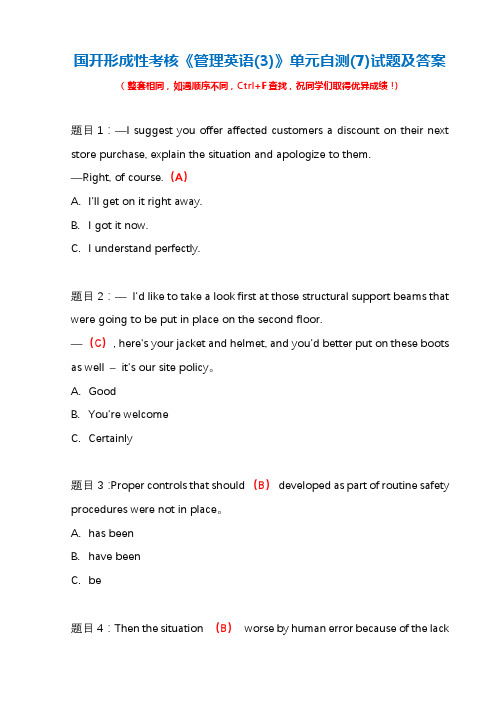
国开形成性考核《管理英语(3)》单元自测(7)试题及答案(整套相同,如遇顺序不同,Ctrl+F查找,祝同学们取得优异成绩!)题目1:—I suggest you offer affected customers a discount on their next store purchase, explain the situation and apologize to them.—Right, of course.(A)A.I'll get on it right away.B.I got it now.C.I understand perfectly.题目2:—I'd like to take a look first at those structural support beams that were going to be put in place on the second floor.—(C), here's your jacket and helmet, and you'd better put on these boots as well –it's our site policy。
A.GoodB.You're welcomeC.Certainly题目3:Proper controls that should (B)developed as part of routine safety procedures were not in place。
A.has beenB.have beenC.be题目4:Then the situation (B)worse by human error because of the lackof proper training。
A.wasB.was madeC.has became题目5:The products of this company are always (C)to standard, they have very strict quality control process。
发动机排气摇臂加加工工艺流程

发动机排气摇臂加加工工艺流程English VersionThe process of machining engine exhaust rocker arms plays a crucial role in the overall performance and efficiency of an engine. The exhaust rocker arm is responsible for opening and closing the exhaust valves at the correct timing, ensuring proper combustion and exhaust of gases.The machining process begins with the selection of high-quality materials for the rocker arm, such as alloy steel or aluminum. These materials are chosen for their strength, durability, and heat resistance, which are essential for withstanding the high temperatures and pressures within the engine.Next, the selected material is cut and shaped into the desired form using precision machining tools such as lathes, milling machines, and grinders. This step is crucial in ensuring that the rocker arm is accurately sized and shaped to fit within the engine assembly.After shaping, the rocker arm undergoes heat treatment to improve its hardness and strength. This process involves heating the rocker arm to a specific temperature and then cooling it rapidly to achieve the desired properties.Once heat-treated, the rocker arm is polished and finished to remove any imperfections and achieve a smooth surface finish. This step is essential for reducing friction and wear between the rocker arm and other engine components.Finally, the rocker arm is inspected for quality control to ensure that it meets the required specifications and tolerances. Any defects or deviations from the design are corrected, and the rocker arm is ready for assembly into the engine.In conclusion, the process of machining engine exhaust rocker arms is a critical step in ensuring the performance and reliability of an engine. By following a precise andcarefully executed process, manufacturers can produce high-quality rocker arms that contribute to the overall efficiency and longevity of the engine.中文翻译:发动机排气摇臂的加工工艺流程对发动机的整体性能和效率起着至关重要的作用。
APQP_for_Avalon_Suppliers-PPT文档资料

Source Release – Expectations for Beta 1 货源发放——对Beta 1的期望
• Send documentation to SQIE for approval. 提供文件给供应商质量改进工程师进行批准。
• PPAP: The proof a supplier is capable of making quality parts at production rates
• 生产件批准程序:供应商有能力按生产效率生产出优质零件的证明 – Pulls together key APQP information – 收集关键APQP信息 – Documents the production process – 用文件记录生产过程
• SQIE retains data 供应商质量改进工程师保留数据
• A copy of the signed Record of Conformance is kept with APQP evidence book 将一份签好字的合格记录和APQP证明文件信息保存在一起
Source Release – Package Content 货源发放——整套文件的内容
APQP - Key Strategies
前期产品质量策划-关键策略
• Get involved early 尽早参与
– Don’t wait for the PPAP request 不要等发出PPAP的要求后再开始
• Communicate issues to SQIEs 与供应商质量改进工程师就出现的问题进行沟通
• Full layout on three pieces 三件的全尺寸报告
发动机再制造的生产工艺过程

发动机再制造的生产工艺过程2发动机再制造的生产流程一、目的:为规范生产流程,提高生产各工序工作的效率,特制定本制度。
二、适用范围:适用于本公司生产管理。
三、内容:1、总则为加强生产工作的管理,提高生产工作的效率,制定本制度。
所有的生产人员及相关管理人员均应以本制度为依据开展工作。
2、发动机再制造的基本工艺流程领原机——拆解(检测)——清洗——表面处理——机加——二次表面处理——组装——测试——打标——入库领原机拆解清洗机加(镗缸、磨轴)表面处理二次表面处理外协加工组装测试打标入库检件报件采购检件抛光喷沙流程图说明一.领原机:满足销售要求,跟据销售订单,领取原机进行再制造生产。
二.拆解:发动机的拆解按生产要求应先拆解,后分类,再检件,最后再归类放好移交下工序。
零部件分类:区分有用金属、铝、塑料、其他与不可用的拆解步骤和检件的关健点:1. 用工具拆解发动机上的附件,拆掉放进附件放置车内。
用螺杆锁紧发动机两边进排气口螺丝孔,然后用吊机将发动机吊起来固定到翻转架上,把固定螺丝锁紧。
检查:发动机外观是否有损伤,2. 拆下气门室盖螺丝检查,检查:气门室盖外观。
3. 拆下时规盖螺丝检查缸体上有没有黑色胶垫,检查:胶垫是否完好。
4. 拆下正时链条和挡链板检查:是否磨损。
准备工具拆解检件报件归类放好移交下工序采购5.拆解缸盖凸轮轴螺丝,用工具一次把凸轮轴螺丝松开,用磁铁一次把液压顶杯吸出来放进蓝色零件放置车内。
用工具把缸盖螺丝拆掉,检查:凸轮轴是否有烧伤拉痕损坏,螺丝和螺丝孔是否滑牙。
6.拆下活塞和连杆瓦、连杆是否可以用,用铁丝按圈数绑在连杆上做标记。
检查:活塞和连杆瓦活塞7.拆下曲轴瓦检查曲轴瓦是否可用,检查:曲轴瓦检查曲轴瓦是否可用,曲轴有没有烧伤拉痕损坏。
按以上检查情况申报需购买的零件,生产跟单负责跟进进度。
三.清洗:零部件的清洗按工艺要求进行分类清洗。
清洗操作时必须佩戴规定的劳保用品(工作帽、戴口罩、系围裙、手套、鞋)。
汽车发动机制造工艺介绍精
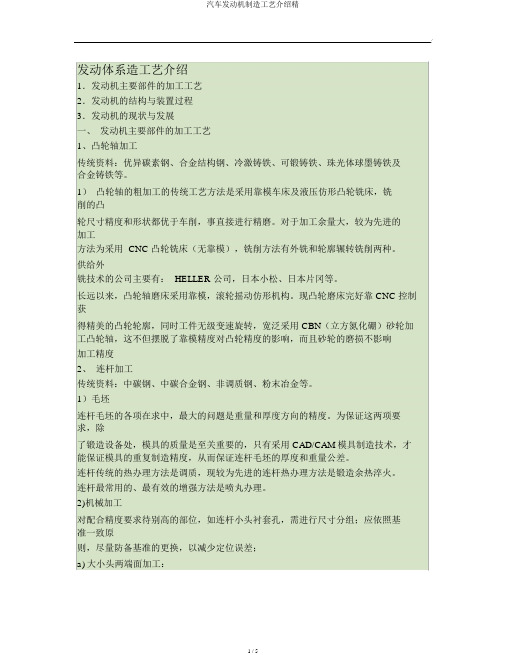
发动体系造工艺介绍1.发动机主要部件的加工工艺2.发动机的结构与装置过程3.发动机的现状与发展一、发动机主要部件的加工工艺1、凸轮轴加工传统资料:优异碳素钢、合金结构钢、冷激铸铁、可锻铸铁、珠光体球墨铸铁及合金铸铁等。
1)凸轮轴的粗加工的传统工艺方法是采用靠模车床及液压仿形凸轮铣床,铣削的凸轮尺寸精度和形状都优于车削,事直接进行精磨。
对于加工余量大,较为先进的加工方法为采用 CNC 凸轮铣床(无靠模),铣削方法有外铣和轮廓辗转铣削两种。
供给外铣技术的公司主要有: HELLER 公司,日本小松、日本片冈等。
长远以来,凸轮轴磨床采用靠模,滚轮摇动仿形机构。
现凸轮磨床完好靠 CNC 控制获得精美的凸轮轮廓,同时工件无级变速旋转,宽泛采用 CBN(立方氮化硼)砂轮加工凸轮轴,这不但摆脱了靠模精度对凸轮精度的影响,而且砂轮的磨损不影响加工精度2、连杆加工传统资料:中碳钢、中碳合金钢、非调质钢、粉末冶金等。
1)毛坯连杆毛坯的各项在求中,最大的问题是重量和厚度方向的精度。
为保证这两项要求,除了锻造设备处,模具的质量是至关重要的,只有采用 CAD/CAM 模具制造技术,才能保证模具的重复制造精度,从而保证连杆毛坯的厚度和重量公差。
连杆传统的热办理方法是调质,现较为先进的连杆热办理方法是锻造余热淬火。
连杆最常用的、最有效的增强方法是喷丸办理。
2)机械加工对配合精度要求待别高的部位,如连杆小头衬套孔,需进行尺寸分组;应依照基准一致原则,尽量防备基准的更换,以减少定位误差;a)大小头两端面加工:连杆大小头两端面是整个机加工过程中的定位基准面,关且对大、小头孔都有着地址精度要求。
所以第一道工序都是加工大小头两端面。
磨削加工:要求毛坯精度较高,磨削的生产率高、精度高。
磨削方式有:立式圆台磨床(双轴或多轴)、立式双端面磨床、卧式双端面磨床。
b)结合面的加工:连杆大头孔有直剖口,也有斜剖口;定位方式有螺栓定位、齿形定位、定位销定位等。
- 1、下载文档前请自行甄别文档内容的完整性,平台不提供额外的编辑、内容补充、找答案等附加服务。
- 2、"仅部分预览"的文档,不可在线预览部分如存在完整性等问题,可反馈申请退款(可完整预览的文档不适用该条件!)。
- 3、如文档侵犯您的权益,请联系客服反馈,我们会尽快为您处理(人工客服工作时间:9:00-18:30)。
Manufacturing ProcessesContents:Introduction 2 Engine block 2-4 Crank Shaft 5-9 Connecting rod 10-14 Conclusion 15 Appendices 16Introduction:There are thirteen parts in the engine as shown in above figure, I will discuss three parts of the engine. Engine block, Crankshaft and Connecting rod.In the following section, I will discuss the function, material used, mechanical properties of the part, the quality requirements and the process used of producing those parts.Engine block:1-1 Description:The Engine Block is a single unit that contains all the pieces for the engine. The block serves as the structural framework of the engine and carries the mounting pad by which the engine is supported in the chassis . The block is made of cast iron and sometimes aluminum for higher performance vehicles. The engine block is manufacturedto withstand large amounts of stress and high temperatures.1-2. Production requirements:The Internal design of the engine block must be extremely precise, because all parts must fit and be able to function properly once the entire engine is assembled. The outside design of the engine only has to fit fewer requirements like attaching to the car properly. Engines are made in all different shapes and sizes to fit inside the frame of the car, therefore a company must be able to manufacture many different engine block designs yet keep up with product demand. There are 6000-8000 engine blocks made a day at a highly qualified company, this may be for many different models.1-3. Process Requirements:The Engine block goes through two manufacturing processes before it is ready for assembly. The first process is die casting manufacturedusing cast iron. The strength of the piece depends on the type of iron used and if any other materials are added. The higher strength iron alloys can include Molybdenum, Chrome or Copper for increased strength.For the engine block the hot-chamber process is used. This process uses a die cut into three parts then combined using a large amount of pressure and temperature. Two parts of the die will contain extrusions to produce holes and cavities. This eliminates much machine process and saves time. Then all the die parts are forced together with the material inside to produce the engine block cast. Once the part has been casted then cooled (using a chill plat) the second process may be preformed. This processes is machining and is very important the overall performance of the engine.The first machining process is to bore out the cylinders for the pistons and then for the camshaft. Next the cylinders need to be sleeved; this provides the surface with a small gradient to trap an oil film. The next operation is to grind down and area for the bearing to set in, this does not have to be surface finished because bushings will be set down in first. The next operation is end milling. This will provide a smooth surface finish for the joining of the oil pan, the crankshaft cap and areas for mounting. The final operations include drilling, reaming and taping. These provide locations for the engine block to be mounted.Crankshaft:2-1. Descriptions:All the pistons in the engine are connected through individual connecting rods to a common crankshaft. The crankshaft is located below the cylinders on an in-line engine,at the base of the V on a V-type engine and between the cylinder banks on a flat engine. As the pistons move up and down, they turn the crankshaft just like our legs pump up and down to turn the crank that is connected to the pedals of a bicycle.The materials used in producing crankshaft including cast iron and steel. It depends on manufacturer and the strength needed. For racing car, steel will usually be used. It is used for transform the rotation of the cylinder due to the combustion process that take place in the engine.2-2. Product requirement:The quality requirement of crankshaft is high. It need high precisions because it used to transform the rotations, it should precisely produce such that that it can transmit that rotation correctly. The production amount of crankshaft depends on the manufacturer, however, since it is a replaceable part for engine, some producer actually producing more. The production rate depends on the process used and the crankshaft usually can be produce using two methods, such as expandable pattern casting (lost form) and forging. Here we will just discuss the forging process.2-3. Process used:The process use in the production of the crankshaft is bulk deformation process called the forging process. Crankshafts are a high cost replacement item.1. Forged and precision machined from premium, high strength steel.2. Heat treated by hardening process for high strength and outstanding wears characteristics.3. Journals are finish-ground and polished assuring ultimate smoothness for less internal friction and long bearing life.4. All crankshaft are precision balanced, both statically anddynamically to provide long life.The forging process is a process of processing work piece having a relatively small surface area-to-volume ratio. It is a process by which plastic deformation of the work piece is carried out by compressive forces. Forging is one of the oldest metalworking operations known. This process can be carrying out at room temperature or at an elevated temperature. Called the hot forging or the cold forging. This process is being chosen to produce the crankshaft is because it gives high precision and also harden the material either by hot work or cold work.The production of the crankshaft involves several different stages so to get the desired shape. These steps are describe in the following diagram:Figure 2. Intermediate stages in forging a crankshaftThese steps is needed because the proper design of the forging dies and selection of die materials required considerable experience and knowledge of the strength and ductility of the workpiece material, its sensitivity to strain rate and temperature, and its frictional characteristics. From Figure 2, we can see that there are five passes in the forging process of a crankshaft. These intermediate stages are important for distributing the material and filling the die cavities properly.The materials use in the production of crankshaft depends on its application. For best performance, the crankshaft is made by steel using the forging process. For some application, the crankshaft can be produce by casting process and the material used can be cast iron. For crankshaft produced using casting process, the following requirement must be made:1. Upgraded Nodular cast iron 80-60-06 to be selected for material which metal microstructure consists of pearlite iron 80 to 90%, graphite type over grade 2 and size over grade 3.2. All casting pieces are instruments checked for pearlite and graphite. The deflection of straightness of casting piece should not be over 5/1000". Ultrasonic inspection for internal defect is an essential process for every casting piece to eliminate any internal defective.3. All journals' radius is enlarged to eliminate stress spots and surface micro polished to 0.25 um. The roundness & size of every journal designed to be accurate to .0001". Magnaflux inspection on all journal surfaces upon completion of machining to ensure perfection.The material use in the crankshaft is AISI 5140 steel is a medium carbon with chromium. Chromium has a twin effect on steel, acting as a carbide former. This improves the harden ability, allowing deeper hardening with less quenching medium.Chromium also improves the corrosion resistance better than plain carbon steel. Currently, to produce a very good quality crankshaft, the manufacturing process of every crankshaft involves 9 basic operations: Magnafluxing, larger journal radius, main side grinding, flywheel flange grinding, oil holes chamfering, journal micro-finishing, and ultrasonic testing. Also, All journals are induction hardened to HRC 55 and above for high performance applications.Connecting rod and rod cap:3-1 Description:Connecting Rods are forged for high strength and toughness. They are hardened and machined to close tolerances to ensure straightness, correct weight and alignment.The connecting rod purpose is to link the piston and crank shaft together. Thus the work done by the piston is transferred to the crank shaft, minus the frictional forces acting on this subsystem. The rods are made of forged steel and have secondary machining operations on critical diameters. Due to the majority of work being doneby the piston, the connecting rod must have a strong compression strength. There are very minimal tensile forces acting on the rod, and they only last for a fraction of a second. The forged steel rods have been strain strengthen during their multiple step formation process.3-2. Production requirements:Rod compression strength is of the up most importance. Failure of a rod can puncture a hole in the engine block. The forging process then is ideal for production because of adding strain strengthening and allowing for high production quantities. The type of forging process most likely utilizes a hot closed die followed by secondary machining operations. There are the same amount of connecting rods in an engine as pistonsa. Forging process results in exceptionally high strength and durability.b. Hardening and machining to close tolerances ensure straightness, correct weight and alignment for smooth operation.c. Tight piston pin and crankshaft bore tolerances provide an exact fit with other components for top performance and long life.d. Endurance testing—up to four million cycles under normal loads—ensures durability.Power Engine Part's Chrome Nickel Moly Steel Racing Rods are manufactured from the highest aircraft quality Chrome Moly Steel using precision engineering techniques for Racing and High performance applications.Rods and Caps are separately forged from Aircraft Quality Chrome Moley Steel to obtain optimum grain flow. The AUTOCAD 14 blue print allows the super racing rods to fit into any stroke. All big and small ends are finished with SUNNEN cross grind. All cap screws are specially designed and manufactured for C.A.T. by ARP for stroker application.1. A18 aluminum bronze wrist pin bushings are made to withstand higher impact force. A third hole drilled at end of the bushing releases any air pockets from the bushing.2. Rods and caps are forged separately from the highest quality steel to obtain optimum grain flow.3. Surface hardness HRB 228-269 to ensure higher tensile strength.4. All rods have been treated with magnaflux inspection, stress relieve, and shot peening.5. Weight control for each rod within five(5) gram tolerance, and balanced for every set within eight(8) grams tolerance.6. ARP bolts with tensile strength over 190,000 PSI.7. Center to Center precision manufacturing with tolerances within 0.001" to obtain the best possible performance.3-3. Process Description:The process used in manufacturing the connecting rod and caps are forging as we have discussed before in the process of manufacturing the crankshaft. Starting with a heated rod blank an initial form is given to the rod. After two to three more dies the final shape of the rod is completed. However the flashing must be trimmed by yet another die which shears off the rough edge and produces two holes in either end of the rod. One large hole for connection to the crank shaft and a second smaller hole for connection to the piston pin. The process of this forging process are shown in Figure 3.Figure 3. Forging process for producing a connecting rod.The final operations are done using machining procedures. First the large and small holes are milled by a tool in a similar fashion to drilling but more precise. Then the two raised edges surrounding the holes are milled flat and are perpendicular to the length of the hole. Most likely a milling and drilling operation are happening at the same time for the connecting rod bolts which are used to hold the next operation pieces together. In order for assembly the larger of the two holes is cut in half. The cut is made perpendicular to the length of the rod and must have a good surface finish so as not having to need any more machining. Finally the small and large holes are ground leaving a very smooth surface finish. However grinding the ID of large hole is some what more complicated because there are two pieces. Using automation the two pieces are held together while grinding takes place.Not mentioned in description of the rod is that when forming the part, the larger hole must be elliptical. When the cutting of the large hole occurs some material is removed and this needs to be compensated for. The amount of the larger diameter minus the minor diameter is roughly the amount of material that can be allowed for cutting the larger hole in half.Conclusion:Many process are used to produce parts and shapes. There is usually more than one method of manufacturing a part from a given material. The manufacturing process to produce a particular part involves many considerations. Some of these considerations include cost, appearance, volume of production, application of the material, and many other issues. In this report, I try my best to find out the best method to produce the parts in a engine. Also, we need to know that manufacturing process of parts keep changing because new technology showing up. And a good method to produce one part today may not be a good method tomorrow since technology keeps improving.Manufacturing is a process of converting raw material into produce that is useful. A key task for manufacturing engineering is to select an optimal manufacturing method among multiple alternatives, given product design goals, process capabilities, and cost considerations. Beside this, the selection of materials for different parts is also important in determining a best manufacturing process.In writing this report, I have learned the various possible process to produce a part. It all depends on the manufacturer and also the material used.Appendices://Products.htm/facts/wwhy2.htm/harmonic_balancers.htm /case_studies/allen.htm /faq/introduction/whatis.htm /catalog1382.html/vprocess.htm/metalcastprocess.htm/forging.html。