5特殊情况下理论板数的求法
8.4.510.4.5最少理论板数捷算法确定理论板数塔板效率和全塔效率

(2)最少理论板数 ----逐板计算法
若令 ത =
= 1 2 . . . . . .
芬斯克(Fenske)方程
1 2 . . . . . .
xA
N xA
xB D
xB W
N min
x A x B
(2)塔板结构参数
(3)操作参数
4. 填料层高度的计算
如果取一段填料作为一个单元,测得离开这个单元的气液两相组成满足相平衡
关系,则可将这个单元看作一块理论板。而这个单元内包含的填料层高度就称
为等板高度(Height Equivalent of a Theoretical Plate,可以HETP表示 )。
在实际精馏操作中,由于气液两相的接触时间有限,故离开塔板的气液两相
通常达不到平衡状态。因此,一般用板效率表示实际板与理论板的接近程度。
单板效率也称默弗里(Murphree)板效。
−1
− +1
汽相实际增加程度
= ∗
=
− +1
汽相理论增加程度
---汽相默弗里板效
−1 −
液相实际减少程度
=
=
−1 − ∗
液相理论减少程度
----液相默弗里板效
n
+1
3. 塔板效率和全塔效率
(2)全塔效率E0
理论板数 N
E0
实际板数 N e
其值一定小于1,多数在0.5~0.7之间。
思考:影响塔板效率的因素?
影响塔板效率的因素很多,可概括为以下三大类:
1.3理论塔板数的确定

1.3 理论塔板数的确定理论塔板数是通过平衡级逐板计算得到的。
所需的数据或方程有:气液平衡关系;精馏段操作线方程;提馏段操作线方程;q 线方程。
1.3.1 气液平衡关系气液平衡关系是分析蒸馏原理和进行蒸馏过程计算的基础。
平衡数据的来源主要由实验测定,已发表的气液平衡数据可见各种刊物和专著。
当气液平衡数据不全时,可通过热力学方法推算得到。
实验测得的气液平衡数据通常采用列表或坐标表示。
气液平衡关系也常用平衡常数和相对挥发度表示。
平衡常数K i 定义为i ii x y K =(1-1)相对挥发度αij 定义为 j ij j i i ij K K x y x y ==//α(1-2) 式中 x i 、x j ──分别为液相中i 、j 组分的摩尔分数;y i 、y j ──分别为气相中i 、j 组分的摩尔分数;K i 、K j ──i 、j 组分的平衡常数;αij ──组分i 对组分j 的相对挥发度。
对双组分物系 i j y y -=1,i j x x -=1代入式(1-2)可得i ij iij i x x y )1(1-+=αα (1-3)对于气相是理想气体、液相为理想溶液的情况,当处于平衡状态时,液相符合拉乌尔关系式i i i x p p 0=(1-4)式中 p i 、p 0i ──分别为i 组分的气相分压和饱和蒸气压,Pa 。
理想气体服从道尔顿分压定律 i i py p =(1-5)式中 p ──系统的压力,Pa 。
联立式(1-4)和式(1-5)可得到p p x y K ii i i 0==(1-6)当用相对挥发度αij 表示时,可得 00j ij i ij p p K K ==α(1-7)由式(1-6)可见,理想体系的平衡常数是温度和压力的函数。
对同一物系,p i 0/p j 0的值随温度的变化不很显著,因此在同一塔内,可取一平均αij 值进行计算。
若溶液为非理想溶液,气相仍可视为理想气体时,则 00j j i i ij p p γγα=(1-8)式中 γi 、γj ──分别i 、j 为组分的活度系数。
理论塔板数的计算课件
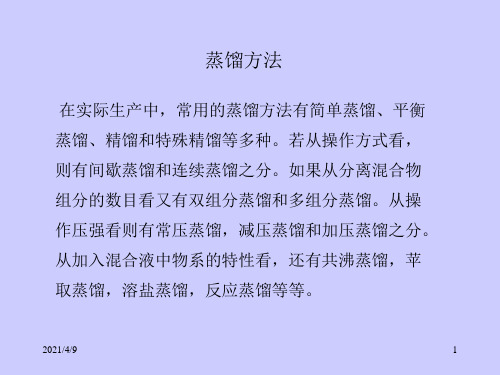
2021/4/9
3
(二元物系的)汽液相平衡
研究精馏过程必须掌握气液相平衡关系。汽液 相平衡关系是在一定温度和压力的条件下,气、液 两相达到平衡状态对其组成在气、液两相间的分配 关系,因为精馏过程是气、液两相间的传质过程, 常用组分在两相中偏离平衡的程度来衡量传质推动 力的大小,故气液相平衡关系是阐明精馏原理和进 行精馏计算
蒸馏方法
在实际生产中,常用的蒸馏方法有简单蒸馏、平衡 蒸馏、精馏和特殊精馏等多种。若从操作方式看, 则有间歇蒸馏和连续蒸馏之分。如果从分离混合物 组分的数目看又有双组分蒸馏和多组分蒸馏。从操 作压强看则有常压蒸馏,减压蒸馏和加压蒸馏之分。 从加入混合液中物系的特性看,还有共沸蒸馏,苹 取蒸馏,溶盐蒸馏,反应蒸馏等等。
2021/4/9
11
二、精馏装置
2021/4/9
12
三、精馏流程
2021/4/9
13
二元连续精馏的计算 基本假定: 一、理论塔板
2021/4/9
14
二、恒摩尔流
2021/4/9
15
• 例:用连续精馏法分离含苯0.44(摩尔分率,下同)的苯--二甲 苯混合液,要求塔顶馏出液含苯0.934,塔釜含苯0.0235,已知进 料为泡点进料,相对挥发度为2.46,精馏段操作线方程为:
一、具有正常偏差的系统 二、具有较大正偏差的系统 三、具有较大负偏差的系统
2021/4/9
9
简单蒸馏 一、流程
2021/4/9
10
精馏
一、精馏原理
可见液体混合物经过多次部分气化和部分冷 凝后从气相得到较纯的易挥发组分,而从液 相则得到较纯的难挥发组分。因此精馏过程 是多次部分气化和多次部分冷凝相结合的操 作。在实际生产中上述精馏操作是不能采用 的,因为每次部分气化和部分冷凝都需要用 相应的加热器和冷凝器来完成。必然产生许 多中间馏分,使得纯产品的收率很低。故工 业上的精馏过程都是采用精馏塔来完成的。
理论板层数( NT )的计算
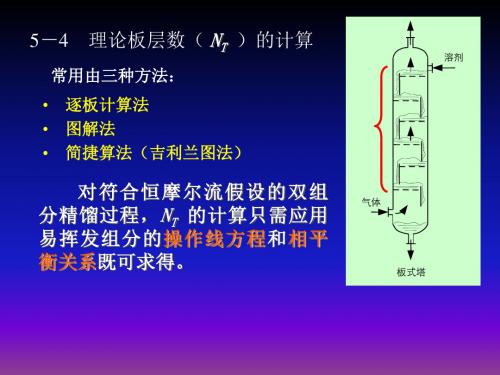
• 绘梯级; NT=阶梯数-1
不包括 再沸器
NT=5-1=4
(不包括再沸器)
e
b
c
0 xW
xx F
xD 1.0
不同加料热状态下的 q 线
• 图解法求理论板层数时,操作线的更换以某梯级跨过两 操作线交点来判断。
• 将跨过交点的梯级定为进料板。
注意:
每块塔板上平衡 关系及与相邻塔 板上的操作关系 清晰可见。
m
W, xW
泡点进料
xn≤xF
精馏段理论板层数=n-1
xn=x’1'
提馏段第一块板 n 板为进料板!
y2'
L' V'
x1'
W V'
xW
操作关系
x2'
y2'
y2'
(1
y2' )
平衡关系
y3'
L' V'
x2'
W V'
xW
操作关系
优点:结果准确, 同时可以得到每块 板上汽液组成。
缺点:当板层数较 多时计算繁琐。
x1
y1
y1
(1
y1)
平衡关系
y1
y1
1
y2 2
x1
x2
F, xF n
ym-2
D, xD
… …
.... ....
y2
R R 1 x1
xD R 1
y2
1
x2 ( 1)x2
x2
y2
y2
(1
化工原理王志魁第五版习题解答:第六章 蒸馏
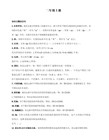
第六章 蒸 馏相平衡【6-1】苯(A)和甲苯(B)的饱和蒸气压数据如下。
A B A B 根据上表数据绘制总压为101.33kPa 时苯一甲苯溶液的-t y x -图及y x -图。
此溶液服从拉乌尔定律。
解 计算式为,000B A A Bp p p x y x p p p -==- 计算结果见下表苯-甲苯溶液的t x y --计算数据苯-甲苯溶液的t y x --图及y x -图,如习题6-1附图1与习题6-1附图2所示。
习题6-1附图1 苯-甲苯t-y-x 图习题6-1附图2 苯-甲苯y-x 图【6-2】在总压.101325kPa 下,正庚烷-正辛烷的汽液平衡数据如下。
试求:(1)在总压.101325kPa 下,溶液中正庚烷为0.35(摩尔分数)时的泡点及平衡汽相的瞬间组成;(2)在总压.101325kPa 下,组成.035x =的溶液,加热到117℃,处于什么状态?溶液加热到什么温度,全部汽化为饱和蒸气?解 用汽液相平衡数据绘制t y x --图。
(1)从t y x --图上可知,.035x =时的泡点为113.8℃,平衡汽相的瞬间组成.053y =。
(2).035x =的溶液,加热到117℃时为气液混合物,液相组成.024x =,汽相组成.040y =。
.035x =的溶液加热到118℃时,全部汽化为饱和蒸气。
习题6-2附图 正庚烷-正辛烷t-y-x 图【6-3】 甲醇(A)-丙醇(B)物系的汽液平衡服从拉乌尔定律。
试求:(1)温度80℃t =、液相组成.05x =(摩尔分数)时的汽相平衡组成与总压;(2)试求总压为.10133kPa 、液相组成.04x =(摩尔分数)时的汽液相平衡温度与汽相组成;(3)液相组成.06x =、汽相组成.084y =时的平衡温度与总压。
组成均为摩尔分数。
用Antoine 方程计算饱和蒸气压(kPa) 甲醇 .lg ..15749971973623886A p t =-+丙醇 .lg .137514674414193B p t =-+式中t 为温度,℃。
化工原理理论塔板计算

精馏过程的物料衡算和塔板数的计算一、理论塔板连续精馏计算的主要对象是精馏塔的理论塔板数。
所谓的理论塔板是指气液在塔板上充分接触,有足够长的时间进行传热传质,当气体离开塔板上升时与离开塔板下降的液体已达平衡,这样的塔板称为理论塔板。
实际上,由于塔板上气液接触的时间及面积均有限,因而任何形式的塔板上气液两相都难以达到平衡状态,也就是说理论塔板是不存在的,它仅是一种理想的板,是用来衡量实际分离效率的依据和标准。
通常在设计中先求出按生产要求所需的理论塔板数N T然后用塔板效率η予以校正,即可求得精馏设备中的实际塔板数N P二、计算的前提由于精馏过程是涉及传热、传质的复杂过程,影响因素众多。
为处理问题的方便作如下假设,这些就是计算的前提条件。
(1)塔身对外界是绝热的,即没有热损失。
(2)回流液由塔顶全凝器供给,其组成与塔顶产品相同。
(3)塔内上升蒸气由再沸器加热馏残液使之部分气化送入塔内而得到。
(4)恒摩尔气化在精馏操作时,在精馏段内,每层塔板上升的蒸气的摩尔流量都是相等的,提馏段内也是如此,即:精馏段:V1 = V2 = …………=Vn= Vmol/s(下标为塔板序号,下同)提馏段:V′n+1 =V′n+2 =…………=V′m = V′mol/s但Vn不一定与V′m相等,这取决于进料状态。
(5)恒摩尔溢流(或称为恒摩尔冷凝) 精馏操作时,在精馏段内每层塔板下降的液体的摩尔流量都是相等的,提馏段也是如此,即:L1 = L2=…………= L n = L mol/sL′n+1 = L′n+2 =………… = L′m = L′ mol/s但L不一定与L′相等,这也取决于进料的状态。
(6)塔内各塔板均为理论塔板。
三、物料衡算和操作线方程1、全塔物料衡算图4-10 全塔物料衡算示意图如图4-10所示,设入塔进料流量为F,轻组分含量为x F,塔顶产量流量为D,轻组分含量为x D,塔底产品流量为W,轻组分含量为x w,流量单位均为mol/s,含量均为摩尔分率。
理论塔板简捷计算方法
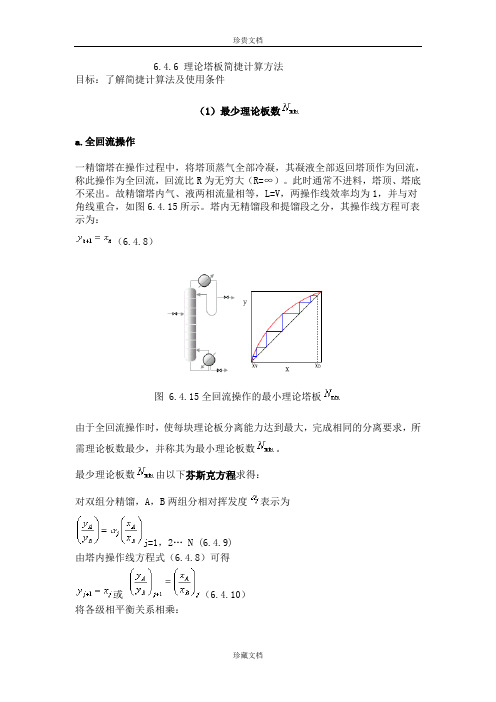
6.4.6 理论塔板简捷计算方法目标:了解简捷计算法及使用条件(1)最少理论板数a.全回流操作一精馏塔在操作过程中,将塔顶蒸气全部冷凝,其凝液全部返回塔顶作为回流,称此操作为全回流,回流比R为无穷大(R=∞)。
此时通常不进料,塔顶、塔底不采出。
故精馏塔内气、液两相流量相等,L=V,两操作线效率均为1,并与对角线重合,如图6.4.15所示。
塔内无精馏段和提馏段之分,其操作线方程可表示为:(6.4.8)图 6.4.15全回流操作的最小理论塔板由于全回流操作时,使每块理论板分离能力达到最大,完成相同的分离要求,所需理论板数最少,并称其为最小理论板数。
最少理论板数由以下芬斯克方程求得:对双组分精馏,A,B两组分相对挥发度表示为j=1,2… N (6.4.9)由塔内操作线方程式(6.4.8)可得或(6.4.10)将各级相平衡关系相乘:运用式(6.4.10)化简,在各板上的相对挥发度近似取为常数,则通过简化和整理获得Fenske方程:该方程也可用于多组分精馏,其区别是以轻、重关键组分的分离代替双组分的精馏。
芬斯克方程推导6.4.6 理论塔板简捷计算方法(续)(2)简捷计算法将许多不同精馏塔的回流比、最小回流比、理论板数及最小理论板数即R、Rmin、N、Nmin四个参数进行定量的关联。
常见的这种关联如图所示,称为吉利兰图(Gillilad)图,如图6.4.16所示。
图 6.4.16 吉利兰图·计算·由图6.4.16或式(6.4.11)求解Y值,代入下式。
·解得理论板数N及Nmin均含再沸器理论板。
采用简捷法也可估算精馏塔精馏段及提馏段理论塔板数或进料位置。
如果计算精馏段理论塔板数,则求精馏段最少理论板数,由进料组成代替,为精馏段平均相对挥发度,按以上步骤求得精馏段理论板数。
同理,求得提馏段理论板数。
例6.4.26.4.7 几种蒸馏操作方式的讨论目标:介绍几种不同操作的精馏过程在精馏过程中,常常有加热、进料方式不同,根据要求,其采出方式也有所区别,对此,分别讨论如下:(1)直接蒸气加热一般精馏是间接加热,主要是为避免对物料污染。
5-4 双组分精馏理论塔板数的计算2010

0 x W
xF
xD 1
结果:精馏段操作线下移,操作线与平衡线距离加大, N T ,但热耗 (以热耗为代价换取N T减少)
小 结
一般而言,在热耗不变的条件下,热量尽可能在塔 底输入,冷量尽可能在塔顶输入,即 “ 热在塔底”、 “冷在塔顶 ”,目的使气相回流及液体回流能经过
全塔而发挥作用。
(2)Rmin的求取
1.0 a
xD ye Rmin Rmin 1 xD xe
q
xD Rmin 1
ye
e
Rmin
xD ye ye xe
0 xW
xe
xF
xD 1.0
式中存在求取ye、xe的问题
因挟点为 q 线与相平衡线交点 坐标,联立二方程求解可得:
xf q ye q 1 xe q 1 xe y e 1 ( 1) xe
L D 物料在塔内循环的操作, W F 0,R D (2)全回流时精、提操作线与对角线重合 L D yn+1 xn xD xn V V
yn +1
L W xn xw xn V V
(3)平衡线与操作线间的距离最大,理论板数最少 (4) N Tmin 的求取
QF QB 定值
1
分析:
0 q 1
q0
q 1
q 1
y
若q值愈小,则Q F ,QB , 那么V ,提馏线斜率 , 提馏线向平衡线靠近,N T 。
q0
0
xW
xF
xD 1
工业上有时采用热态甚至气态进料,其目的: 不是为了:减少塔板数 而是为了:减少塔釜的加热量,避免塔釜温度过高, 物料产生聚合或者结焦。
- 1、下载文档前请自行甄别文档内容的完整性,平台不提供额外的编辑、内容补充、找答案等附加服务。
- 2、"仅部分预览"的文档,不可在线预览部分如存在完整性等问题,可反馈申请退款(可完整预览的文档不适用该条件!)。
- 3、如文档侵犯您的权益,请联系客服反馈,我们会尽快为您处理(人工客服工作时间:9:00-18:30)。
0.01
R − Rmin R +1
1.0
R = Rmin
lim
N → +∞
(曲线左端点)
R − Rmin =0 R → Rmin R +1 N − N min 1 − N min N lim = lim =1 R → Rmin N → +∞ 1 + 2 N N +2
(吉利兰图本质是反映N~R之间 的函数关系)
F , xF , q
V ' , y m +1 V ', yw
L ' , xm
适用场合: 被分离的二元混合物系 为水溶液,且水是重组分。
(即塔顶馏出液主要为非水组分,塔底 液体近于纯水)
L ' , x m +1 V0 , y 0
水蒸气全部冷凝,塔底液体等mol汽化 (轻组分优先汽化)
W , xW
进料板之上(精馏段)或之下(提馏段)的各板满足恒摩尔流 假定。故,r另一组分=r水 V0 = V ' , W = L'
L' W y 'm +1 = x'm − xw V' V'
√√ √ √
L' L + qF L + qF RD + qF = = = V ' V + ( q − 1) F L + D + ( q − 1) F ( R + 1) D + ( q − 1) F √
√ √ √
两种情况下提馏段操作线的斜率相同。
所以
与单股进料时对加料板的物料衡算、热量衡算类似,有:
L′′ = L + q2 (− D2 ) = RD1 − q2 D2
若,侧线出料为饱和液体,q2=1
L′′ = RD1 − D2
所以
V ′′ = V = ( R + 1) D1
(即采出板上下降的饱和液体的一部分作为侧线产品,而板上上升的饱和蒸汽不 采出)
两种加热方式的精馏段操作线,q线完全 相同。所以,两种情况下的提馏段操作线, 都经过相同的一点,d。 已证,两种情况下提馏段操作线的斜率相 同。故,两种情况的提馏段操作线是同一条线。
但,间接加热的釜液浓度(xw,间)为与对角线的
y
d e
a
b
交点,c;直接加热的塔底液浓度(xw,直)为与坐标轴 y=0的交点,g。
R=R
N = ? (不含再沸器)
2、简捷法步骤(例1-9) ①根据相平衡数据、精馏段操作线、提馏段操作线、 q线,算出 Rmin。选择合适的回流比R; ②根据操作温度、总压及分离要求,算出全回流时所需的最少理论 板数Nmin (不含再沸器) 。(对接近理想体系的混合物可以用 Fenske方程估算Nmin )。 xD xW lg[( ) ( )] 1 − xD 1 − xW −1 N min = lg α m
提馏段
加料板
L'
V'
①中间段操作线方程
总物料衡算 易挥发组分的物料衡算
V ′′ = L′′ + D1 + D2
进=出
V ′′y s +1 = L ′′x s + D1 x D1 + D2 x D 2
y s +1 D1 x D1 + D2 x D 2 L ′′ xs + = V ′′ V ′′
V ' ' = V + (q2 − 1)(− D2 ) = V − (q2 − 1) D2
c g
xF
x
xD
显然, xw,直< xw,间。由图解法知道,直接加热需要的理论板 数多。
(上述设计任务并未规定xW,所以两种情况下的值不同)
结论:直接蒸汽加热时的提馏段操作线与间接蒸汽加热时的提馏段 操作线是同一直线。只是一个端点不同,直接蒸汽加热时的xw较 小,故所需理论板数稍多,这是由于直接蒸汽的稀释作用所致。
α ' = α Dα F
m
(在理想溶液的情况下,一定温度、总压下汽液相平衡体系的α值简化为同温度下纯组分 的饱和蒸汽压之比)
八、几种特殊情况下(设计型问题)理论板数的求法
1、水蒸汽直接加热
提馏段塔板下降到塔底的液体,不用 间壁式换热器间接加热,使其部分汽化。 而是将高温水蒸汽直接引入塔底,使塔底 液体受热,部分汽化。
y s +1
D1 x D1 + D2 x D 2 RD1 − D2 xs + = ( R + 1) D1 ( R + 1) D1
(表示相临两板间汽液两 相组成之间的函数关系)
端点d:两条操作线的交点 (即精馏段操作线与q线的交点) 端点g: (xw,0)。
意即,直接蒸汽加热时,提馏段 操作线与坐标轴y=0的交点是其塔底液 体浓度。与对角线的交点c,不是塔底 液体浓度。 而,间接蒸汽加热时(常规塔), 提馏段操作线与对角线的交点,是釜液 浓度。
y
a
d e
b
' y n +1
d
b
e
c
xW
xq x F
xD
2多侧线的精馏塔(略讲) 侧线出料:在工业生产中,有时为了获得不同规格的精馏 产品,可根据需要在塔的不同位置开设出料口。 多股加料:有时为了利用同一个塔,同时分离组分相同, 但浓度和热状态不同的几股料液,可将它们分别在适当的 位置加入塔内。
所有这些情况构成了多侧线的精馏塔。
或
(形式上也符合常规塔提馏段操作线方程)
x、y随两板选取位置的不同而变,是变量。而L’、V’、xW是常数,由设计任务规定的设计参 数。故是一条直线。
③ q线方程
精馏段操作线方程(表示板间两相组成之间的函数关系):
Lxn − Vyn +1 + DxD = 0
提馏段操作线方程(表示板间两相组成之间的函数关系):
αm为全部理论塔板上平均相对挥发度,可取为塔顶第一块板上及塔釜中相平 衡体系相对挥发度的几何平均,即
α m = α Dα w
③利用吉利兰图,算出选定回流比R对应的全塔理论板数N(不含再 沸器)。
④确定加料板位置 用Fenske方程估算全回流时精馏段所需的最少理论板数N’min, 再利用前述Rmin,查吉利兰图,算出选定回流比R时精馏段所需总 理论板数N’。加料板为N’+1。 应用Fenske方程估算精馏段塔板数的方法:
y0 = 0
且由恒摩尔流假定: ' = V0 , W = L' V
(在提馏段内,任选不同的相邻两板都成立)
W x'm = V0 y 'm +1 +Wxw
即
W W y ' m +1 = x' m − x w V0 V0
L' W y 'm +1 = x 'm − xw V' V'
——直接蒸汽加热时的提馏段操作线方程
xw,直< xw,间的证明,除了图形证明,还可以通过公式推导证明:
√D
F √
D√ xD √
L
V
√x D
√x F
L' V '
W
间
√F √x F
L
V
V0 y0 = 0
L' V '
W
直
x W ,间
x W ,直
间接蒸汽加热 间:
直接蒸汽加热
F = D + W间 + V0 = D + W直
W间 = F − D W直 = F + V0 − D
V , y1 V , y1
1
全凝器
馏出液 D1, x D1
V , y2
精馏段
2
L, x1 L, x2
回流液 L, x D
侧线产品 出料板 D 2, x D 2
V ′′, y s
中间段
s
V ′′, y s +1 L′′, xs
s +1
可 以 采 出 饱 和 蒸 汽 , 或 饱 和 液 体
原料 (液 ) F , xF
直: F
W直 > W间
间: FxF 直: FxF
= DxD + W间 xw,间 = DxD + W直 xw,直
xw,直 < xw,间
图中标√的参数,表示两种 情况的取值相等。
②设计任务:达到相同的xD及xW时,直接蒸汽加热轻组分回收率低
D间
F √
D直
√F √x F
L
L
V
√x D
xD √
V
√x F
L' V '
c
xW
g
' xn
xF
x
xD
作图方法:联结g点与两条操作线的交点d。
精馏段操作线: 根据设计任务规 定的分离要求 xD,选取的操作 回流比R 。定出 a点和截距b。
1 2
a
3
d
q线: 根据进料的组成 和热状态。
b
4
e
提馏段操作线: 根据设计任务规 定的分离要求xW 定出g点,联结d 点。
5
g xW xF xD
(1)侧线出料(以 一个侧线出料为例)
出料板之上(精馏段), 加料板之下(提馏段)的各板 满足恒摩尔流假定。 精馏段操作线方程的推 导:由精馏段任意相邻的两板 间的以上塔段做物料衡算。 提馏段操作线方程的推 导:由提馏段任意相邻的两板 间的以下塔段做物料衡算。 故,精馏段、提馏段操作 线方程与常规塔的相同 中间段操作线方程的推导: 出料板与进料板之间的 各板满足恒摩尔流假定。由 中间段任意相邻的两板间的 以上塔段做物料衡算。