外文翻译--生产线平衡
精益生产之线平衡模式LineBalanceModels中英文版
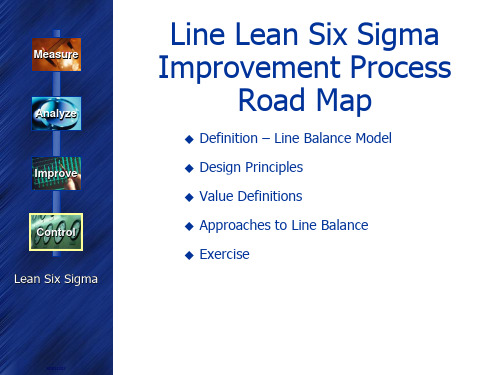
• 脑力风暴 • 拉系统 • 减少设置 • TPM • 流程图 • 标杆管理 • 亲和图 • DOE • 假设检验 • 力场分析图 • 树状图 • 甘特图
• 查检表 • 运行图 • 柱状图 • 散布图 • 控制图 • 柏拉图 ing Objectives
10
Primary Issues in Typical Control
Process Environments
Large or erratic batches Excessive WIP Poor floor space utilization Low employee efficiency Long/erratic cycle times Poor balance of operations and labor across process steps Conveyance, standby and motion waste Disorganized workspace and component/supply storage High variability of demand on multiple processing centers, e.g., call
How to design and implement a process supported by a line balancing model that ensures optimal use of: People Floor space Capital Assets Material
Line Balance Model
12
Control
Line Balance – Design Principles
Minimize Batch Size/Transfer Quantity/Work In Process Minimize/Stabilize Cycle Time Maximize Labor Efficiency Optimize number of workstations/process steps Balance tasks/labor across workstations Maximize space utilization Minimize takt variance Minimize NVA (conveyance, standby, and motion wastes) Minimize the need to re-balance as demand requirements change Minimize volume variability (combine product category demand) Maximize flexibility to allow for product introductions and discontinuations
产线平衡率术语英语

产线平衡率术语英语
English: Line balancing, also known as production line balancing or assembly line balancing, refers to the process of optimizing the workflow in a production line to ensure that all stations or workstations have a similar amount of work to do. This is achieved by analyzing the tasks required to complete a product, identifying any bottlenejsons or areas of inefficiency, and then rearranging the tasks or workstations to achieve a more even distribution of work. The goal of line balancing is to increase productivity, reduce idle time, and improve overall efficiency in the production process.
中文翻译: 产线平衡,也被称为生产线平衡或装配线平衡,指的是优化生产线工作流程的过程,以确保所有工位或工作站都承担类似数量的工作。
这是通过分析完成产品所需的任务,识别任何瓶颈或低效率的区域,然后重新安排任务或工作站,以实现工作的更均匀分配。
产线平衡的目标是提高生产效率,减少空闲时间,并改善生产过程的整体效率。
生产线平衡生产线平衡(linebalancing)
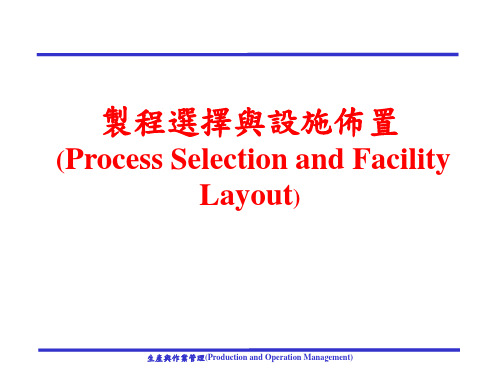
生產與作業管理(Production and Operation Management)
自動化 (automation)
• 指以機器代替人工,而此機器包括能夠 自動運作的感應器與控制裝置。 • 自動化的範圍從工廠的完全自動化到單 一自動化作業的形式。 • 服務業的自動化亦是一種選擇。
– 舉例:自動提款機 (ATM)、自動空調、自動 檢驗、自動存取系統、快遞包裹分類、郵件 處理、電子郵件、網路銀行以及電子收費器 等。
製程選擇與設施佈置
(Process Selection and Facility
Layout)
生產與作業管理(Production and Operation Management)
學習目標
解釋製程選擇策略的重要性。 2. 解釋製程選擇對一個組織的影響。 3. 描述基本製程型態。 4. 討論製程的自動化方法。 5. 解釋技術管理的必要性。 6. 列舉重新規劃設施佈置的原因。 7. 描述設施佈置的基本型態。 8. 列舉產品別佈置與製程別佈置的主要優點與缺點。 9. 解決簡單的生產線平衡問題。 10. 建立簡單的製程別佈置。
– 例如,軟磁碟、磁碟片或微處理器等
生產與作業管理(Production and Operation Management)
可程式自動化
• 機器人(robot):主要由三個部分組成:機 械手臂、動力供應及控制器。
生產與作業管理(Production and Operation Management)
– 為非例行性的工作,並在一段時間間隔內完成特定目 標。 – 設備彈性與作業人員技術的範圍也是從低至高皆有。
• 舉例:
– 從簡單到複雜都有,製作動畫、新產品或服務上市、 發行圖書、諮詢服務或興建橋梁等。
生产线平衡PPT课件
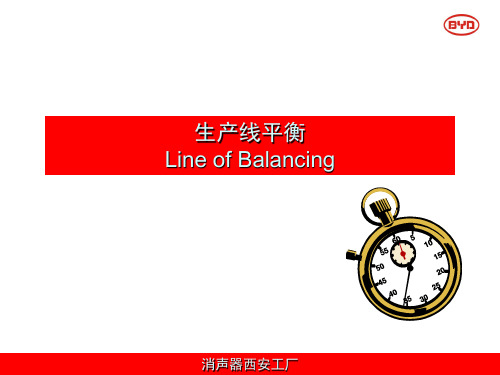
3.25
1.2
.5
1
Answer: 任务C决定了生产线的CT,也就决定了最大 产出率。
消声器西安工厂
生产线平衡: 确定CT
Question: 假定我们每天要装配100台风扇。 周期时间应是多少?
Answer:
要求的周期,C时=间 每 每期 期的 要生 求产 的时 产间 出
C=4120m 台 00/i天 n天 s=/4.m 2 in台 s/
消声器西安工厂
生产现场Loss
能量流失
物流 流失
有形流失
生产现场Loss
人的流失
无形流 失
设备流失
消声器西安工厂
6
操作者Loss
管理者Loss
操作者作业速度
资格不够的监督
标准作业的忽视
过剩人力投入
激励制度缺乏 熟练或培训不够 超过管理限度的不良增加
随时变更的生产计划 频繁的机器故障 过多的换线时间
后续任务 6 4 3 2 2 1 1 0
单件时 间min
工位 1 6
工位 2 7
工位 3 3
周期时间永远是由需时最长的工位决定的。上述工作的CT是 7分钟。其它两个工位有空闲时间。
消声器西安工厂
线平衡分析的目的 缩短产品的装配时间,增加单位时间的生产量。 减少工序之间的预备时间; 提高生产线的效率; 改善生产线的平衡; 改善生产方法。
生产线平衡: 画优先图(Precedence Diagram)
任务 紧前任务 A None
BA C None
D A, C
任务 E F G H
紧前任务 D E B E, G
A
B
G
H
C
D
E
精选生产线平衡改善5
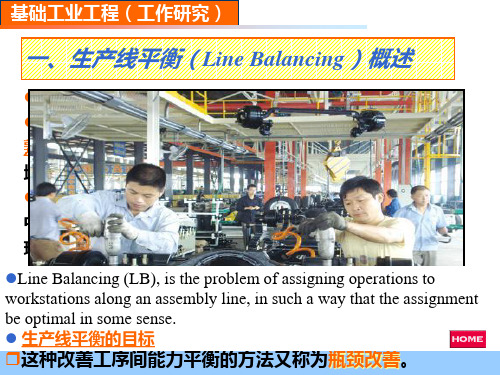
生产不平衡的损失时间: 7
7
T (Tmax Ti ) (61.52 Ti ) 135.96s
i1
i1
每日产量为:P1
总工时 生产周期
8*60*60 468,小于企业核定产量
61.52
的最小值500。
基础工业工程(工作研究) 图3 断路器装配线作业工时山积图(改善前) 单位:S(秒)
将各个工位的作业分解成可测量的作业单元,对作业单元按 照连续秒表测时的方法进行标准工时测定。 测时步骤:首先对装配线7个主要工位(暂未考虑工位⑧、 ⑨和⑩的贴牌封装,运输环节)的作业试观测10次。然后根 据观测数据,运用d2值法计算每个作业单元的观测次数,取 最大作业单元的观测次数进行观测。再次运用三倍标准差法 剔除观测数据中的异常值,得到各作业单元的平均值。最后 考虑评比和宽放,按照ST=平均作业时间*评比系数*(1+宽 放率)计算得到各个工位的总工时,如表1所示。 根据企业实际情况,确定评比系数为8%,宽放率为10%。
m
平衡率
ห้องสมุดไป่ตู้i
i1
*100% 272.26 80.4%
si * CT
48.35 * 7
由69.13%提高 到80.4%
生产不平衡率=1-平衡率=1-80.4%=19.6%
生产不平衡损失时间为:
7
7
T (Tmax Ti ) (48.35 Ti ) 66.18s
i1
i1
基础工业工程(工作研究)
基础工业工程(工作研究)
一般情况下,当生产线的平衡率处于:
50%一60%之间:进行的是一种根本没有任何科学管理意识 的粗放式生产;
60%一70%之间:存在人为去平衡生产线的因素,但并没有 解决一些深层次问题;
生产线平衡LineBalance

间隔标记距离 所耗时间
3-3
平衡率计算
平衡率:用于评价流程中各工位节拍符合度的一 个综合比值。
∑ 各工序作业时间 平衡率 = ------------------------------ 100% 瓶颈时间工位数
3-4
生产线平衡图
生产线平衡图 :
表明作业的工站数以及每个工站的作业时间与节拍时间的对比。 能够明显地看出哪些存在浪费的工站,鉴别出工站与工站间的不平衡性。 优化当前的生产线平衡图,并绘制出优化后的生产线平衡图 .
电源包装 改善
后 前
7.9" 7.1" 7.8"
9.4"
S10
S11
S10
S11
18
3 - 18
3 - 13
数据整理和计算
资料分析与处理
第三步:初步制定生产线平衡图
根据各工站时间表,绘制生产线平衡图 ( 山积表),计算初始 平衡率。 识别增值动作及非增值动作,通过 ECRS 减少各工站非增值动 作时间。 通过对各分解动作单元进行分解组合排列组合,并确定每个工 站的所需的人数,尽可能地使瓶颈时间接近节拍时间。 对于瓶颈工站,重点分析动作时间,通过减小动作幅度,优化 作业工位布局等方法来降低瓶颈时间,然后重新计算平衡率。 根据确定的生产线总人数,考虑合适的生产线布局。
3 - 12
拆解动作
时间观测
时间测量流程
数据与信息记录
作业内容
➊观测中判断作业员的速度,并如实记录 ,不可修改测量数据。 ➋ 如遇特殊情况,应作标记。 ➊观测完毕后,对数据进行整理计算,补 充测量有怀疑或错漏数据。 ➋ 计算出每个工站的作业时间,并列出每 个工站所需使用的工治具、设备等。 ➊ 标记并汇总可以自由移动的工序时间, 并计算这些工序所占时间的比例。 ➋ 分析工序流程中哪些工序的作业时间 容易改善优化。
8 生产线平衡

某流水线各工序作业时间
第一道序:0.8秒 善后第二道序:1.8秒
第三道序:1.5秒
通过作业改
请问:
该流水线1分钟最多能够生产多少产品?
一、生产线平衡概念
概念 生产线平衡(Line balancing)
• 生产线平衡是对生产的全部工序进行平均化,调 整作业负荷,以使各作业时间尽可能相近的技术 手段与方法。
172
93 49 11 19
130
12 13 20 28 37 20
130
12 13 20 28 37 20
121
10 18 25 18 13 15 12 10
121
10 18 25 18 13 15 12 10
156
11 49 35 10 51
196
26 24 15 73
7 51
1600
二、生产线平衡方法
②
( NG )
① ③
等待
等待
接触
方法
2、观测时间,了解员工实际作业时间
(1)各工序作业时间的测定 (2)了解生产线节拍
7-六角法兰面螺母 BQ/JRYP4-95707-08500 2 冲击扳手US-6SHK
12
法兰面螺母并紧固,再将排气管外保护罩
套筒12
装在消声器总成上并紧固。
5 用扭矩扳手确认螺母扭矩值,并用记号笔作 记号。
扭矩扳手NB(5-22.5Nm)
记号笔
100% 4
6 在消音器尾部(消音器护罩)的两安装孔内 厌氧胶不得外溢 涂适量厌氧胶。
PD-7
产品名称
JS110-9C
安全第一 质量绝对
工位号 作业名称
B15
特性标记
生产线平衡(实例版)
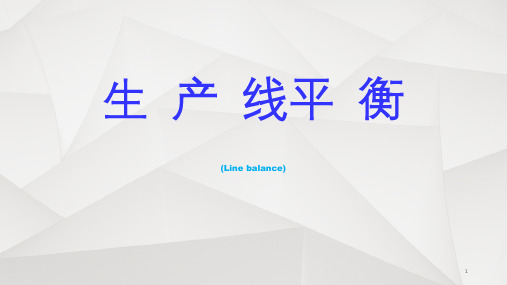
1﹑生产线平衡的相关概念
1.2工站及周期时间
时间
T2
T1
T3
T4
T5
工站
S1
S2
S3
S4
S5
CycleTime ﹕每工站中1个循环的作业所需的标
准工时(如图中所示﹕T1,T2,T3,T4,T5)
8
1﹑生产线平衡的相关概念
1.3瓶颈时间
时间
T2
瓶颈时间
T1
T3
T4
T5
工站
S1
S2
S3
S4
S5
瓶颈工时﹕生产线作业工时最长的工站的
生产单位:协助生产单位拟定及推动改善方案. 制工单位:改善前/后之工时测量,山积表制作﹑分析及改善方案之实施,
跟踪方案效果评估及各种相关文件修订及系统窗体发行﹔ 品管单位:负责改善前/后产品质量评估﹔ 工务单位:主导及其它改善事项协助﹐设备改善﹔ IE﹑经管﹑企划:改善前后产线效益评估及跟进.
50
THE END!
时间
S1
S2
S3
S4
S5
增加可供时 间
还有什么 方法 平均时间T CT
工站
41
Steps4:山积表平衡
3.平衡的步骤
若T略小于CT:将CT设为上限,消除瓶颈
时间
CT 平均时间T
S1
S2
S3
S4
S5
工站
42
Steps4:山积表平衡
3.平衡的步骤
若T严重小于CT:将CT设为上限,重排 消除瓶颈
时间
所有工站时间之和 平衡率= 瓶颈工站时间*工站总数
100%
16
1﹑生产线平衡的相关概念
1.6平衡率﹐平衡损失及其计算
- 1、下载文档前请自行甄别文档内容的完整性,平台不提供额外的编辑、内容补充、找答案等附加服务。
- 2、"仅部分预览"的文档,不可在线预览部分如存在完整性等问题,可反馈申请退款(可完整预览的文档不适用该条件!)。
- 3、如文档侵犯您的权益,请联系客服反馈,我们会尽快为您处理(人工客服工作时间:9:00-18:30)。
毕业设计(论文)外文资料翻译学院:经济管理学院专业:工业工程姓名:学号:外文出处: 附件: 1.外文资料翻译译文;2.外文原文。
(用外文写)生产线平衡这项研究的范围是探讨生产线的制造和平衡,生产线平衡的类型,设备平衡和故障分析的理解。
当每个工人的任务需要相同的时间来完成的时候,就是一个平衡的流水线。
线平衡,是一个制造工程的功能,即在整个生产线的任务都能够得到等分。
良好的平衡线,能避免无意义的劳动和提高生产效率。
生产线平衡线平衡的策略是,使生产线足够灵活,以避免外部和内部的违规行为。
有两种类型的生产线平衡,即:静态平衡:指的是几个小时或更长的时间内能力的长期分歧。
静态失衡是工作站,机器和人未能得到充分利用的结果。
动态平衡:指短期能力的差异,最多不超过几分钟或几个小时的时间。
动态不平衡源于产品结构的变化和产品结构无关的工作时间的变化。
劳资平衡和分配生产线的稳定策略的倾向是固定的劳动的平衡分配。
劳资的可行性的一个重要特征是战略的灵活性即生产线的个人技能和能力:当一名工人在执行分配给他的任务是有问题,遇到的延迟,由于技术问题(S),其他工人(S)应转移到帮助。
当一个工序运行出现问题时,熟练的技工应尽快接管其工序。
生产线的所有工人应交互在各个工序熟悉工序操作。
全技能即在一个单一的工作中心一个工人可以处理各种任务(自动化)。
设备平衡设备平衡应确保每一台设备在工作单元中有相同的工作量。
现在每个制造商都试图最大限度地利用所有可用的设备。
如此高的利用率往往适得其反,这可能是一个错误的目标,因为利用率高,通常伴随着高库存。
设备故障设备故障是一项重大而严肃的问题,有可能关闭一条生产线。
为了避免这种故障,应确保每个设备不会超载,并且应培训工人进行日常机器检查(预防性维护)和标准作业程序的训练。
维护部和工程部的优势不在于在运行后期的变化,因此应计算预防性维修时间,并安排活动。
分析线平衡的分析一般由主管技术人员进行。
分析之前应把流水线分成各个小任务,确定标准的任务时间,任务的排序的规范和约束的分析与生产线的工作分工。
如果瓶颈环节的任务是在于寻找良好的平衡的方式,技术过硬的员工应分析的任务,以减少所花费的时间来执行。
生产线平衡领导生产线工人应致力于生产线平衡而努力,这样他们才能够快速应对当产品和生产率变换导致失衡(静态和动态)时迅速作出反应。
结论生产线平衡的研究,往往聘请有新思路和经验的人来改变现状。
生产线的设计和操作是艺术多于科学。
工人的灵活性是有效的资源管理的关键所在。
工人的检查和对自己的设备做小型维修工作的想法可能降低了设备故障的风险。
选择一套合适的平衡机制是一个工作单元设计的一部分,它必须与许多其他决策系统建立良好的联系才能运作良好。
Production Line BalancingThe scope of this study is to explore the understanding of Production-line Manufacturing and Balancing, Types of Line Balancing, Equipment Balancing and its Failure and Analysis. A production line is said to be in balance when every worker’s task takes the same amount of time. Line balancing is a manufacturing-engineering function in which whole collection of production-line tasks are divided into equal portions. Well-balanced lines avoid labour idealness and improve productivity.Production Line BalancingLine-balancing strategy is to make production lines flexible enough to absorb external and internal irregularities. There are two types of line balancing, which we have explained as:∙Static Balance – Refers to long-term differences in capacity over a period of several hours or longer. Static imbalance results in underutilizationof workstations, machines and people.∙Dynamic Balance – Refers to short-term differences in capacity, like, over a period of minutes, hours at most. Dynamic imbalance arises fromproduct mix changes and variations in work time unrelated to product mix.Labour Balancing and AssignmentsStrategy of production line stability is the tendency for labour assignments to be fixed. Labour feasibility is an important feature in the strategy of production line flexibility linked to individual skills and capabilities –∙When one worker is having problem in performing his assigned task and experiencing delay due to technical problem(s), other worker(s) shouldmove into help.∙The management pr actice of deliberately pulling worker’s of the line when the line is running smoothly.∙The movement of whole crews from one dedicated line to another as the model mix changes.Group Technology – In which one worker can handle variety of tasks (automation) in a single work centre.Equipment BalancingWhile balancing equipment, attempt to ensure that each piece of equipment in the work cell has the same amount of work. Now days every manufacturer is attempting to maximize the utilization of all available equipments. Such high utilization is often counterproductive and may be the wrong goal because; high utilization is usually accompanied by high inventory.Equipment FailureAn equipment failure is a major serious matter, with the potential to shut down a production line. To avoid such failures one should not overload the equipments, and workers should be trained to perform a daily machine checking (preventive maintenance) and following standard operating procedures. The advantage for Maintenance and Engineering Department does not lie in running late shifts, hence calculate the preventive maintenance time and schedule the activity.AnalysisAnalysis is generally performed by Competent Technical Staff. Begin the analysis with division of production-line work into small tasks, determination of task time standards, specification of required task sequencing and notation of constraints. If bottle neck task is in the way of good balance, the Competent Technical Staff should analyze the task to reduce the time it takes to perform.Line Balancing LeadershipWorkmen should lead the production line balancing effort, so that they can react quickly when line imbalances (static and dynamic) crop up asa result of changeover to make a different item or changes in the output rate.ConclusionProduction-line balancing study tends to employ thought and ingenuity to change conditions. Production-line design and operation is more art than science. Labour flexibility is the key to effective resource management. The idea of worker’s checking and doing minor repair work on their own equipment possibly decreases the risk of equipment failure. Selecting an appropriate set of balancing mechanism is a part of work cell design and it must be linked with many other decisions for the system to function well.。