管件液压成形技术简介
现代液压成型技术

现代液压成型技术现代液压成型技术第1部分:液压成形技术的种类在介绍它的种类和特点之前首先让我们先了解它的定义,什么是液压成形?定义:液压成形是指利用液体作为传力介质或模具使工件成形的一种塑性加工技术,也称液力成形。
(可能文字解释有点抽象,下面请大家看一段视频),很直观的可以看到它的成形工艺大致可分为三个阶段:第一个阶段,填充阶段,将管材放在下模内,然后闭合上模,使管材内充满液体(并排除气体),将管的两端用水平冲头压封;第二个阶段,成形阶段,对管内液体加压胀形的同时两端的冲头按照设定加载曲线向内推进补料,在内压和轴向补料的联合作用下使管材基本贴近模具;第三个阶段,整形阶段,提高压力是过度区圆角完全贴靠模具而成形为所需的工件,这个阶段基本没有补料,从截面看可以把管材变为矩形、梯形、椭圆形或其他异型截面。
1.1 按使用的液体介质不同可将液压成形分为水压成形和油压成形。
1.1.1 水压成形:使用的介质为纯水或水添加一定比例的乳化油组成的乳化液1.1.2 油压成形:油压成形的介质为液压传动油或机油1.2 按使用坯料不同,可分为管材液压成形、板材液压成形、壳体液压成形。
1.2.1管材液压成形:板料(≤100MPa)和壳体液压成形(≤50MPa)使用的成形压力较低,而管材液压成形使用的压力较高(一般不超过400MPa),又称内高压成形(Internal High Pressure Forming)通过管材内部施加高压液体和轴向补料把管材压入到模具型腔使其成形为所需工件,所需管材多为电阻焊管(ERW)因其成本低且成型性好,其次是无缝管、拉拔管(DOM)激光焊管(成型性最佳)。
1.2.1.1变径管内高压成形技术变径管内高压成形是以管材作坯料,通过管材内部施加高压液体和轴向补料把管材压入到模具型腔使其成形为所需工件,把管材的圆截面变为矩形、梯形、椭圆形或其他异型截面。
(板书演示)1.2.1.2弯曲轴线变截面管件内高压成形弯曲轴线管件内高压成形工艺过程包括弯曲、预成形、内高压成形等主要工序。
管件液压成形技术及其在汽车零部件制造中的运用
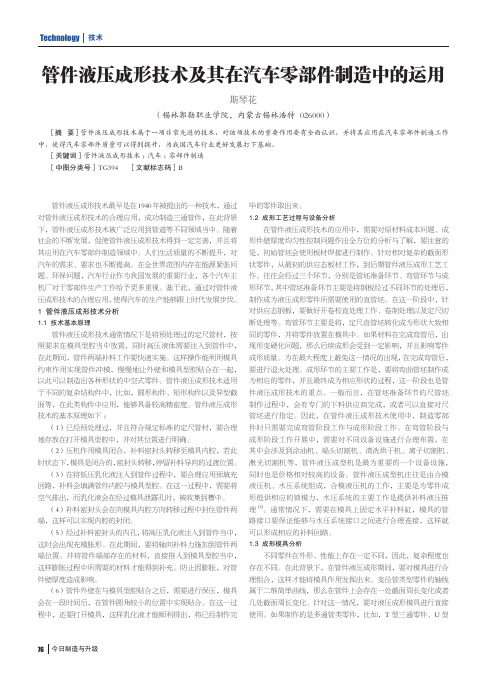
76 今日制造与升级Technology 技术管件液压成形技术最早是在1940年被提出的一种技术,通过对管件液压成形技术的合理应用,成功制造三通管件,在此背景下,管件液压成形技术被广泛应用到管道等不同领域当中。
随着社会的不断发展,促使管件液压成形技术得到一定完善,并且将其应用在汽车零部件制造领域中。
人们生活质量的不断提升,对汽车的需求、要求也不断提高。
在全世界范围内存在能源紧张问题、环保问题,汽车行业作为我国发展的重要行业,各个汽车主机厂对于零部件生产工作给予更多重视。
基于此,通过对管件液压成形技术的合理应用,使得汽车的生产能够跟上时代发展步伐。
1 管件液压成形技术分析1.1 技术基本原理管件液压成形技术通常情况下是将预处理过的定尺管材,按照要求在模具型腔当中放置,同时高压液体需要注入到管件中,在此期间,管件两端补料工作要快速实施。
这样操作能利用模具约束作用实现管件冲模,慢慢地让外壁和模具型腔贴合在一起,以此可以制造出各种形状的中空式零件。
管件液压成形技术适用于不同的复杂结构件中,比如,圆形构件、矩形构件以及异型截面等,在此类构件中应用,能够具备较高精密度。
管件液压成形技术的基本原理如下:(1)已经预处理过,并且符合规定标准的定尺管材,要合理地存放在打开模具型腔中,并对其位置进行明确。
(2)压机作用模具闭合,补料密封头转移至模具内腔,若此时状态下,模具是闭合的,密封头转移,停留补料导向的过渡位置。
(3)在将低压乳化液注入到管件过程中,要合理应用预填充回路,补料会填满管件内腔与模具型腔。
在这一过程中,需要将空气排出,而乳化液会在经过模具泄露孔时,被收集到槽中。
(4)补料密封头会在向模具内腔方向转移过程中封住管件两端,这样可以实现内腔的封闭。
(5)经过补料密封头的内孔,将高压乳化液注入到管件当中,这时会出现充模胀形。
在此期间,要将轴向补料力施加到管件两端位置。
并将管件端部存在的材料,直接推入到模具型腔当中,这样膨胀过程中所需要的材料才能得到补充。
波纹管液压成形原理及工艺方法

波纹管液压成形的原理是,将高压液体(如水或液压油)注入预制的管坯中,使管坯在模具中膨胀,然后压缩,管材发生塑性变形,最终得到成形的波纹管。
这种成形方式可以确保管壁减薄量适中,因为液压在管壁上的作用是均匀的。
波纹管液压成形的工艺方法可以分为以下步骤:
1. 按照设计尺寸截取管坯,将管坯放置在下半模上,并闭合上、下半模,左右冲头延伸至管坯的两个端口中形成密闭的空腔,同时向管坯内注入液体。
2. 增大管坯内部液体压力,高压液体均匀作用于模腔,左右冲头固定,利用液体压力和模腔的约束形成初波。
3. 在初波成形完成后,施加轴向压力使模具进给,直至贴合,将初波挤进模腔,之后进一步增大管坯内部液体压力,使得管壁与模腔贴合并固定波形。
4. 成形完成后先卸内压力,再卸载轴向推力,分开上下模具,冲头退出,取出波纹管管件。
按照管坯上波纹成形的顺序是否连贯,波纹管液压成形技术可以分为整体式成形和连续式成形。
其中整体成形是管坯在模具中加载一次,就可以成形管件上所有的波纹,而连续成形是指每次成形一个波纹,依次成形管坯上设计的所有波纹。
请注意,具体的工艺参数和操作细节可能会因波纹管的材料、尺寸和设计要求等因素而有所不同。
因此,在实际生产过程中,需要根据具体情况进行调整和优化。
液压成形工艺

优点:
原始管坯为低碳钢,管坯的外径 为69. 9mm ,厚度为2. 0mm 工艺过程包括弯曲、液力成形、 冲裁和切边等 左右零件同时用液力成形的方法 生产,然后在下道工序中切开
一、基本情况--成形原理
管件液压成形原理 1 2
合模
充填介质
3
4
液压胀形 轴向进给
脱模
一、基本情况--工艺流程
光管
分管
弯曲
切割
液压胀型
预成形
一、基本情况--主要设备
生产线主要设备:
• • • • • • • • •
CNC弯管机 预成形机及模具 润滑系统 液压成形机及模具 零件端面切割、孔加工及检测 清洗和烘干系统 输送单元 主控系统 测量装置
通用汽车的纵梁
原始管件外径为152. 4mm , 壁厚为2. 0mm , 长度为4876. 8mm 过去采用的方法是采用14 个冲压件焊接或铆接在一起而成 的。现采用液力成形件降低了造价,减轻了重量,并且空间结 构尺寸愈加紧凑
资料来源:管件内高压成型及其在汽车工业中的应用现状
二、应用领域
汽车车身框架
二、应用领域
车身 仪表盘支架 散热器支架 座椅架 车顶侧围横梁 车顶纵梁 底盘 发动机支架 梯形臂 副车架 前后桥 转向系 控制臂 转向柱 从动连杆 其它 排气管 凸轮轴 曲轴
二、应用领域
副车架
此件所采用管件外径为69. 9mm ,壁厚为2. 5mm 传统冲压焊接工艺成形需6 个零件,而液压成形 仅需要一个零件,重量节省了34 %
液压成形控制技术

形 压 力 一 般 在 6 MP '' 0 MP 0 a- 0 a范 围甚 至 更 高 , -2 成
别 通 过 粗一 细一 精 细 的滤 芯 进 行 过 滤 , 方 法 能 满 此 足 大 部 分 使用 要 求 , 需 要经 常清 洗 或 更换 滤 芯 。 但
工行业重要 制造技术之 一 , 国, 国, 美 德 日本 等发达 国
家均 已投入 大 量人 财物 力研 究 并 已经 投入 生产 或 试 生产 , 在其 它行 业 中的应用 也 不断扩 大 , 景十 分 它 前 广阔 。 目前 , 要 以板材 类和 管材类 如碳钢 、 主 不锈 钢 、 铜合金 、 铝合金 等为主 原料 。
的通道 ; 第二个用 途是堵 住金 属管 内 的液压 油 不让外 泄; 第三 个用途 是在成形 时推 动金 属管 向模 具 内移 动
1 引 言
液 压成 形 ( 也叫液 压胀形 ) 是最近 十 几年 来迅 速 发展起来 的一 门新 工艺 , 它一 出现 即受到制 造业 界 的 极大关注 而蓬勃发展 , 目前 已成 为 国外汽 车 、 船舶 、 轻
Hy r ul o mi n r l c n l g d a i F r ng Co to s Te h o o y c
W U a — u Xio y
艺 品和体育 用品等行 业 。缺 点是初 始投 资较大 , 制程
还 不太完 善, 大部分 生产 工 艺主要靠试 验总 结 。
( hn t r w sisttfrn ier g ein C i t e n t et tueo g ei s & a mid o h i e n nd g n
p e s r i r su e l o
液压成形技术

谢谢观赏
制作人: 学号:
09材料成型及控制工程 2012-5-14
成形特点及应用 特点:
• • • • 它具有成形产品质量轻、刚度好 形状及尺寸精度高,能产生复杂外形曲面 减少半成品数量,减少焊接及机械加工工序 模具简单和生产周期短
应用:
• 广泛应用于汽车、电力、船舶、洁具、工艺品和体 育用品等行业
参考文献
• 刘小旦, 周 林 , 程晓民.绿色节能制造技术——液压 成形研究现状及发展[J].浙江科技学院学 报,2009(3):243-246 • 直妍, 阳林, 吴道建.液压成形技术及其新进展[J].热 加工工艺.2004(12):63-65
主题:
液压成形技术
液压成形技术
也叫液压胀形技术
• 液压成形是指采用液态的水、油作传力介质 ,代替 刚性的凹模或凸模 ,使坯料在传力介质的压力作用 代替传统的刚性凹模或凸 模, 使坯料在液体的高压作用下贴模成形。
液压成形原理
• 管材液压成形的原理: 首先将原料( 直管或预先弯曲 成形的钢管) 放入底模, 然后管件两端的冲头在液压 缸的作用下压入, 将管件内部密闭, 冲头内有液体通 道, 液体不断流入管件, 此时上模向下移动, 与下模共 同形成封闭的模腔, 最后高压泵与阀门控制液体压力 不断增大, 冲头向内推动管件, 管壁逐渐贴近模具变 形, 最终得到所需形状的产品。
5.请简述液压成型技术加工方法原理及其优点

请简述液压成型技术加工方法原理及其优点液压成型技术是一种高效、精确、适用范围广、成本低、环保的加工方法。
下面将分别从高效性、精度高、适用范围广、成本低、环保性等方面介绍液压成型技术的原理及其优点。
1.高效性液压成型技术采用液体作为传力介质,通过施加高压液体来传递成型力,使得生产效率大幅提高。
在生产过程中,由于液压成型可以连续进行,减少了模具更换和调试的时间,进一步缩短了生产周期。
此外,液压成型技术可以同时进行多个工件的加工,提高了生产效率。
2.精度高液压成型技术采用液体作为传力介质,通过控制液体的压力和流量,可以精确控制成型力,从而保证了制品的精度和一致性。
此外,液压成型技术的模具精度高,从而进一步提高了制品的精度和质量。
3.适用范围广液压成型技术适用于各种材料和复杂形状的制品加工。
对于不同材质和厚度的材料,可以通过调整液体的压力和模具的形状来满足加工要求。
此外,液压成型技术可以加工各种复杂形状的制品,如曲面、镂空等,适用范围非常广泛。
4.成本低液压成型技术采用液体作为传力介质,可以重复利用液体,降低了能源成本。
此外,液压成型技术的模具更换和调试时间短,减少了人工成本。
同时,液压成型技术可以同时进行多个工件的加工,提高了生产效率,进一步降低了生产成本。
5.环保性液压成型技术采用液体作为传力介质,与传统的机械加工方法相比,噪音污染和废弃物减少。
在生产过程中,液压成型技术可以控制液体的使用量,避免浪费和污染环境。
此外,液压成型技术的模具可以重复使用,减少了资源浪费,进一步体现了环保性。
综上所述,液压成型技术具有高效性、精度高、适用范围广、成本低、环保性等优点。
在现代化的加工制造业中,液压成型技术已经成为一种重要的加工方法,为提高生产效率、降低成本、保护环境等方面做出了积极的贡献。
现代液压成形技术

2.5液力胀接和液压冲孔
• 液压冲孔就是在管内 液体压力的支撑作用 下,利用冲头将管壁 材料分离的一种冲孔 方法。一般采用冲孔 弯曲。 • 种类:由内向外冲孔、 由外向内冲孔。
•
图1 空心异形截面零件
2.1变径管内高压成形
• 变径管是指管件中间一处或几
处的管径或周长大于两端管径 或周长,其主要的几何特征是 管件直径或周长沿轴线变化, 轴线为直线或弯曲程度很小的 二维曲线,如图2所示,又分为 对称变径管和不对称变径管。 • 膨胀率是衡量变径管内高压成 形的技术水平和难度的一个重 要指标,它与零件材料,成形 区长度,润滑和加载路径有关。
典型实例:轿车副车架主管件内高压成 形 弯曲轴线异形截面管内高压成形技术广 泛以用于汽车制造领域。目前,世界上 最长的低碳钢内高压成形件是美国通用 汽车公司制造的长度为12m的卡车纵梁。 最长的铝合金内高压成形件是Volvo大吉 普上的纵梁,长度达5m,铝管直径达 100mm。
2.3薄壁多通管内高压成形
什么是液压成形?
——一种新型成型工艺
液压成形发展现状
0.1内高压成形
1)早在20世纪50年代,该技术已用于生产管路中使用的铜合金T型三通管和自行车车架上的连接件,所用 成形压力小于25MPa,随着科技的发展现代液压成形压力一般达到400MPa,有时可达到1000MPa。超高 压精度达到0.2-0.5MPa,位移精度达到0.5MPa。20世纪80年代德国和美国的研究机构系统地开展了内高 压成形的基础研究和应用技术,现在已广泛应用到汽车、航空、自行车、管路等当中,其中汽车应用最为 广泛。包括1.底盘类零件:副车架、纵梁、后轴、保险杠2.车体结构:座椅框、仪表盘支梁、顶梁等 3) 发动机和驱动系统:排气管凸轮轴 4)转向和悬挂系统:控制臂、摆臂等 2)成形工艺比较单一 0.2 板材液压成形 早在1890年,就出现了类似于充液成形的方法,在板材与液体间用橡胶模割开,并在第二次世界大战 时期在美国得到应用(钢制头盔)。生产效率低,质量不稳定等逐渐淘汰。为解决上述问题20世纪60年代 日本学者(春日保男)提出将液体直接作用于坯料上,强制润滑拉深,这就是现在说的现代充液拉深技术 原型。20世纪70年代进一步发展,1977年,安徽拖拉机厂用该工艺生产了50拖拉机的油底壳,这是我国 首次将该技术应用生产。 目前应用夜拉深技术制造的零件类型有筒形件,锥形件,抛物线件,盒形件以及复杂型面件,设计材 料包括碳钢、高强钢、不锈钢、铝合金等,材料厚度为0.2mm-3.2mm,板材液压成形与普通拉深相比成 形极限和拉深比大。对于低碳钢筒形件最大拉深比达到2.6,不锈钢2.7.铝合金2.5,如果采取特殊工艺还 可进一步提高拉深比。如 调压等 0.3 壳体液压成形技术 1)自从1985年王仲仁教授发明了球形容器无模液压成形技术以来该技术经历了三个发展阶段 壳体结构有平板类多面壳体扩展到单曲率多面壳体。 2)由低压及常压球形容器发展到三类压力容器。 3)有球形壳体扩展到非球形壳体。 图为1992年哈工大王教授采用壳体液压成形技术成功研制 200mm3液化气储罐,直径7.1m,壁厚24mm材 料为低合金钢16MnR,最高工作压力位1.77MPa。(造纸球直径2m,厚12mm,压力供水装置直径2.7m, 厚6mm;通信塔长轴6m、3m,短轴3m、2m)
- 1、下载文档前请自行甄别文档内容的完整性,平台不提供额外的编辑、内容补充、找答案等附加服务。
- 2、"仅部分预览"的文档,不可在线预览部分如存在完整性等问题,可反馈申请退款(可完整预览的文档不适用该条件!)。
- 3、如文档侵犯您的权益,请联系客服反馈,我们会尽快为您处理(人工客服工作时间:9:00-18:30)。
管件液壓成形技術簡介
金屬工業研究發展中心─鄭炳國工程師一、技術簡介:應用高壓流體中空管件使之塑性成形之技術。
(如圖1)
圖1.汽車零組件
二、技術發展:
1940年代”T”型管接頭成形可說是管件液壓成形技術之濫觴,歷經50-60年代美、英、日等國相關專利開發與產品應用,至70年代末期德國開始對管件液壓成形技術進行基礎研究,並於90年代初期率先應用於汽車體結構件生產,時至今日已成為國際間汽車製造技術上最具突破性之應用,並已躍升為主流製造技術之一,在其它產業應用亦不斷擴大中。
近年來,包括:德國雙B、AUDI、VW、OPEL,美國GM、FORD、CHRYSLER 均已投產,且市場需求正快速成長中;日本由於90年代泡沬經濟因素故導入期較歐、美略為落後(約自1997年開始),據了解:TOYOTA、HONDA、NISSAN、MAZDA、MITSUBISHI、SUBARU等車廠均已導入相關設備進行液壓成形零件之生產與開發,此
外,韓國HYUNDAI、KIA亦已應用管件液壓成形技術生產相關零組件。
三、技術特點:
(一)降低生產成本:根據Schuler Hydroforming公司分析,較傳統沖壓+銲接件降低
15-20%,模具費用降低20-30%。
(二)減輕重量/節省能源:較傳統沖壓+銲接件減輕20-30%,與車削/鎕孔相較,可減輕
40-50%,最多甚至可達75%。
(三)產品一體形化:複雜形狀產品可減少零件數,節省焊接、組裝道次及後處理。
(四)提高產品性能/精度:以散熱器支架(Radiator Support)為例,水平方向性能可提
高50%,垂直方向提高39%,外形精度亦大幅提高。
(五)創新性:克服傳統技術限制,使產品設計更具彈性。
四、技術應用:
(一)汽車:引擎系統(hollow camshafts, drive shafts, gear shafts)
底盤系統(engine cradles, frame rails, radiator support, instrument panels,
rear axle frames)
排氣系統(engine tubes, catalytic converters, pressure tubes, connectors
and manifolds)
(二)機車/自行車:車架結構(Section frame),接頭(joints)等。
(三)其他產業:波紋管(Bellows)、水龍頭、閥體外殼,各式把手等。
五、市場前景:
(一)Daimler Chrysler預估2005年THF零件將較2000年成長3倍。
(二)Dana預估2004年THF零件將佔汽車底盤零件的50%,且該公司在未來五年內將
於加州、泰國、巴西、委內瑞拉及阿根廷等國家至少建立12台以上液壓成形機生產線。
(三)日本迄今已有超過20台以上的專用設備投入汽車零件的生產與研發。
在Bellows
方面則有超60台專用設備,應用領域涵藝製閥業,、真空系統、精密控制元件及建
築業。
(四)北美、歐洲、日本生產水龍頭之領導廠商均已建立液壓成形生產線進行量產。
全球目前投入液壓成形設備開發/銷售之廠家超過30家,其中最大之設備製造商Schuler公司,因開發THF設備1996-1999年營業額成長10倍。
圖2.其他產業零組件。