液压封头成形技术
封头冲压设备工艺分析和辅机总体方案设计研究

转移 两块 钢板 , 这样可 以提高工作效 率 , 减少 上料小 车 的运动
次数 。
钢板转移到 冲压主机 内。当需要 吸附钢板 时 , 使供给换 向阀打
开, 真空发生器 开始工作 ; 当需要放下钢 板时 , 供给 阀关闭 , 同 时真空吸盘 的破 坏真空换 向 阀打 开 ,使真 空吸盘 内真空度 降
需人工操作辅 机。 上下料辅 机在 2分钟之 内完成上 、 下料 任务 , 并且还需要
进行喷涂润滑液、 中定位等工作 。对直径 为 3米左 右的大型 对 坯料钢板来说 , 如果 依测 顿序完成上 料 、 下料 、 喷涂 润滑液 、 对 中定位等工作 , 时间要求 比较紧 , 难度很大 。 通过 工作 空间 的分 离 , 以在不 同位置 同时完成一些工作 。 可 例如 : 冲压 主机 冲压 在 过程中 , 喷涂润滑液机构 、 对中定心等工作可 以同时进行 , 在冲 压主机冲压工作完成后 , 下料小车开始取料 、 取料完成后 , 上料 工作准备就绪 , 上料小车直接上料 , 大大减少 了时间浪费。 把工 作空间分成四个部 分 , 依次为 : 量钢板堆放工位 、 批 喷涂润滑液 工位、 冲压机工位 、 下料 工位 。在上料过程 中, 首先把 坯料 钢板
2 冲压主机 结构特点
自动上 下料辅 机所要服务 的冲压主机为 4 0 0 0吨液压 机 , 冲压主机是 四柱 液压机 , 由于 四根柱 子的干涉 , 只能在 冲压机 前 后两个方 向进行上下料工作 。在 冲压工作 过程 中, 凹模 静止
不 动, 拉伸液压缸带动凸模冲压钢板成形。在上料 的过程 中可
பைடு நூலகம்
艺进行 了分析 的基础上 , 对设备 的方案进行初步探 讨。
【 关键 宇 】 封头; 压设备; 冲 工艺
液力传动与流体机械在航空航天中的典型应用 ppt

四.飞机液压系统的组成
飞机液压系统是指飞机上以油液为工作介质,靠油压驱动执行 机构完成特定操纵动作的整套装置。为保证液压系统工作可靠 ,特别是提高飞行操纵系统的液压动力源的可靠性,现代飞机 上大多装有两套(或多套)相互独立的液压系统。它们分别称为 公用液压系统和助力(操纵)液压系统。公用液压系统用于起 落架、襟翼和减速板的收放,前轮转弯操纵,驱动风挡雨刷和 燃油泵的液压马达等;同时还用于驱动部分副翼、升降舵(或 全动平尾)和方向舵的助力器。助力液压系统仅用于驱动上述 飞行操纵系统的助力器和阻尼舵机等,助力液压系统本身也可 包含两套独立的液压系统。为进一步提高液压系统的可靠性, 系统中还并联有应急电动油泵和风动泵,当飞机发动机发生故 障使液压系统失去能源时,可由应急电动油泵或伸出应急风动 泵使液压系统继续工作。
四.飞机液压系统的组成
四.飞机液压系统的组成
液压系统通常由以下部分组成:①供压部分:包括主油泵、应 急油泵和蓄能器等,主油泵装在飞机发动机的传动机匣上,由发 动机带动。蓄能器用于保持整个系统工作平稳。②执行部分:包 括作动筒、液压马达和助力器等。通过它们将油液的压力能转换 为机械能。③控制部分:用于控制系统中的油液流量、压力和执 行元件的运动方向,包括压力阀、流量阀、方向阀和伺服阀等。 ④辅助部分:保证系统正常工作的环境条件,指示工作状态所需 的元件,包括油箱、导管、油滤、压力表和散热器等。 液压系统具有以下优点:单位功率重量小、系统传输效率高、 安装简便灵活、惯性小、动态响应快、控制速度范围宽、油液本 身有润滑作用、运动机件不易磨损。它的缺点是油液容易渗漏、 不耐燃烧、操纵信号不易综合。它的缺点是油液容易渗漏、不耐 燃烧、操纵信号不易综合。与其他机械(如机床、船舶)的液压 系统相比,飞机液压系统的特点是动作速度快、工作温度和工作 压力高。
椭圆形封头标准

椭圆形封头标准椭圆形封头是一种广泛使用的压力容器部件,用于封堵容器开口,防止内部介质逸出。
在标准制定和实际应用中,椭圆形封头需满足以下要求:1.形状和尺寸标准化:椭圆形封头的形状和尺寸应符合国际或国内标准。
常见的标准包括ISO 14692、ASME B16.9等。
这些标准规定了椭圆形封头的直径、高度、壁厚等基本参数,以及与筒体连接的坡口形状和尺寸等内容。
形状和尺寸的标准化有利于降低制造成本、提高互换性,方便使用和维护。
2.材料选择:椭圆形封头的材料应具备足够的强度、耐腐蚀性和加工性能。
常用的材料包括碳钢、不锈钢、合金钢等。
具体材料的选用应根据封头的工作压力、介质特性、使用环境等因素进行选择。
3.制造质量:椭圆形封头的制造过程中,应确保材料质量、加工精度和焊接质量。
对于关键尺寸,如封头的几何中心、坡口角度等,应进行严格控制。
此外,焊缝应进行无损检测,确保无表面裂纹、气孔、夹渣等缺陷。
4.使用压力与温度:椭圆形封头的压力和温度参数应符合容器设计规范。
在正常使用条件下,封头应能承受容器的设计压力,且不会出现局部屈曲或塑性变形。
另外,封头在设计温度下应具有良好的韧性、高温稳定性和低温韧性。
5.结构完整性:椭圆形封头应具有足够的结构完整性,确保在各种工况下不会发生破坏。
这涉及到封头的几何形状、壁厚分布、过渡区设计等因素。
为了提高结构完整性,可以采用优化设计,如增加封头壁厚、采用热处理等方法。
6.与筒体的连接:椭圆形封头与筒体的连接部位,应采用相应的焊接工艺和连接结构,确保连接部位的结构强度和密封性能。
常见的连接方式包括对接焊接、角接焊接等,具体选用应根据设计要求进行选择。
7.防腐和耐磨性:对于暴露在腐蚀环境或工作介质具有磨损性的椭圆形封头,应考虑采取相应的防腐和耐磨措施。
例如,在封头表面喷涂防腐涂层、堆焊硬质合金等,以提高封头的耐腐蚀性和耐磨性。
8.检验与试验:制造完成的椭圆形封头应进行严格的检验和试验,确保其符合设计要求和使用性能。
椭圆封头最小成形厚度

椭圆封头最小成形厚度椭圆封头是压力容器中常见的一种部件,其形状与椭圆相似,由于其特殊的曲线形状,使得其工程计算和设计不同于其他封头。
本文将详细介绍椭圆封头的最小成形厚度。
1.椭圆封头的概念及应用范围椭圆封头是圆柱体上的两个椭圆形盖板,其与圆柱体相连接,用于封闭压力容器。
椭圆封头广泛应用于石油、化工、制药等行业的压力容器中,如锅炉、反应器等。
2.最小成形厚度的定义最小成形厚度是指椭圆封头在受到内压时,能够保证其不发生塑性变形或破裂的最小厚度。
成形厚度的大小直接影响封头的承载能力和安全性。
3.影响最小成形厚度的因素最小成形厚度受多个因素影响,其中包括材料的机械性能、椭圆封头的几何参数以及使用环境的工作条件等。
在设计椭圆封头时,需要综合考虑这些因素,以确保封头的结构强度和安全性。
4.最小成形厚度的计算方法最小成形厚度的计算需要结合椭圆封头的几何形状和所选用的材料的力学性能参数。
通常采用ASME标准或其他相关规范中的计算公式进行计算。
在进行计算时,需要考虑内压、封头的几何尺寸、材料的屈服强度等因素。
5.材料选择与尺寸优化在实际工程中,选择合适的材料是确保椭圆封头最小成形厚度满足要求的关键。
根据不同的工作条件和使用环境,可以选择不同的材料,如不锈钢、碳钢等。
同时,通过对椭圆封头的几何参数进行优化,可以进一步降低最小成形厚度,提高封头的性能。
6.封头的制造与质量控制封头的制造过程需要严格控制各项参数,包括材料的选择、成形工艺、焊接质量等。
同时,对于封头的质量进行检测和控制也是至关重要的,可以通过无损检测、压力测试等手段确保封头的质量合格。
通过本文的介绍,我们了解到椭圆封头最小成形厚度对于压力容器的安全性和可靠性至关重要。
在设计和制造过程中,应综合考虑材料的选择、封头的几何参数、工作条件等因素,并通过计算和优化来保证封头的性能。
坚持严格的质量控制和检测,才能确保封头的质量符合要求,从而保障压力容器的使用安全。
化工设备机械基础(第四版)第4章内压薄壁圆筒与封头的
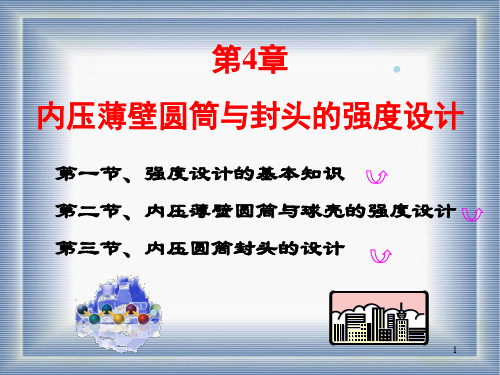
若取第三强度理论,
S
பைடு நூலகம்
PD
2 t
S PcDi S
2[]t
整理得到计算壁厚S的公式,
❖ 若基于外径:
S
Pc Di
2[ ]t
Pc
基于内径的圆筒 计算壁厚公式
同样取第三强度理论,S
PD
2 t
S
PcDo S
2[]t
整理得到计算壁厚S的公式,
S
Pc Do
2[ ]t
Pc
基于外径的圆筒 计算壁厚公式10
若考虑腐蚀裕量C2,得到 设计壁厚Sd, Sd S C2 名义壁厚 Sn Sd C1
对于承受均匀内压的薄壁容器,其主应力规定为:
环向应力 轴向应力
1
PD 2S
2
m
PD 4S
径向应力 3 r 0
5
2.1 第一强度理论
根据:当作用在构件上的外力过大时,材料就会沿着最大拉应力
所在的截面发生脆性断裂,也就是说,不论在什么样的应力状态
下,只要三个主应力中最大拉应力σ1达到了 材料的极限应力,材 料就发生破坏;
GB150-1998规定: • 碳素钢和低合金钢制容器,取Smin3mm • 高合金钢制容器,取 Smin2mm
24
4. 压力试验及其强度校核
➢ 为了检查容器的宏观强度和有无渗漏情况,容器投入使用之前, 必须作压力试验或气密性试验;
➢ 压力试验一般采用液压试验,对于不适合液压试验的容器,可进 行气压试验;
21
3.5.2 腐蚀裕量C2
• 由于容器在使用过程中会受到介质的腐蚀,因此必须考虑一定的 腐蚀裕量;
• 介质不同、材料不同,所考虑的腐蚀裕量值也不尽相同。
椭圆形封头标准规格尺寸
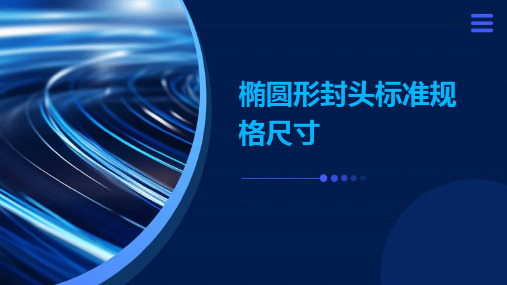
contents
目录
• 椭圆形封头简介 • 椭圆形封头标准规格尺寸 • 椭圆形封头的设计要求 • 椭圆形封头的检验标准 • 椭圆形封头使用注意事项 • 相关标准及法规
01
CATALOGUE
椭圆形封头简介
椭圆形封头的定义
• 椭圆形封头是一种用于压力容器、管道等设备的重要部件, 也称为椭圆封头、椭圆形封头。它是一种由旋转成形的封头 ,其形状呈椭圆形,由一个直边段和两个相同长度的半圆弧 组成。
较强的抗腐蚀能力
椭圆形封头在制作过程中通常采用耐腐蚀材料制成,具有 较强的抗腐蚀能力,能够有效地保护设备内部介质不被腐 蚀。
椭圆形封头的应用领域
• 椭圆形封头广泛应用于石油、化工、食品、医药 、轻工、纺织、核电、军工等领域。在这些领域 中,椭圆封头被广泛应用于各种压力容器、管道 等设备中,作为重要的连接部件和密封部件使用 。
04
CATALOGUE
椭圆形封头的检验标准
外观质量检验标准
表面质量
封头表面应光滑、连续,无 裂纹、气孔、夹渣、飞边等
缺陷。
1
形状公差
封头的几何形状应符合设计 要求,各部位的尺寸精度应
符合标准规定。
圆度
封头的圆度应符合标准规定 ,一般要求不大于封头内径 的千分之二。
平直度
封头的平直度应符合标准规 定,一般要求不大于封头内 径的千分之二。
系列4
δ4=12~34mm,每6mm递增
系列2
δ2=8~22mm,每3mm递增
系列3
δ3=10~28mm,每4mm递增
高径比尺寸系列
• H/D=1.0~1.5,每0.1递增
03
CATALOGUE
液压模具原理

液压模具原理液压模具是一种利用液压传动技术实现工件成形加工的模具。
它通过液压系统提供的压力来驱动模具的运动,从而实现对工件的成形加工。
液压模具在工业生产中扮演着重要的角色,它具有高效、精度高、稳定性好等优点,被广泛应用于汽车、航空航天、轨道交通等领域。
本文将介绍液压模具的原理及其工作过程。
液压模具的原理是利用液体传递压力的性质来实现工件的成形加工。
液压系统由液压泵、液压缸、液压阀等组成,通过液压泵将液体压力传递到液压缸中,从而驱动模具的运动。
液压系统中的液体是不可压缩的,因此能够提供稳定的压力来实现对工件的加工。
液压模具的原理可以简单地理解为利用液体传递压力来实现对工件的成形加工。
液压模具的工作过程可以分为四个步骤,加压、保压、回油和复位。
首先是加压阶段,液压泵将液体压力传递到液压缸中,驱动模具对工件进行加工。
在加压过程中,需要保持压力稳定,这就需要通过液压阀来控制液压系统的压力。
加压完成后进入保压阶段,液压系统会保持一定的压力,以确保工件的成形质量。
接下来是回油阶段,液压缸中的液体通过液压阀返回油箱,以便下一次的加压。
最后是复位阶段,液压缸回到初始位置,模具完成一次加工动作。
液压模具的原理是基于液体的不可压缩性和传递压力的性质来实现工件的成形加工。
它具有高效、精度高、稳定性好等优点,被广泛应用于工业生产中。
通过对液压模具的原理及工作过程的了解,可以更好地掌握其工作原理,为工业生产提供更好的技术支持。
总结,液压模具是一种利用液压传动技术实现工件成形加工的模具。
它通过液压系统提供的压力来驱动模具的运动,从而实现对工件的成形加工。
液压模具的原理是利用液体传递压力的性质来实现工件的成形加工,其工作过程包括加压、保压、回油和复位四个步骤。
液压模具具有高效、精度高、稳定性好等优点,被广泛应用于工业生产中。
通过对液压模具的原理及工作过程的了解,可以更好地掌握其工作原理,为工业生产提供更好的技术支持。
化工机械基础-第10章 内压容器封头设计

a.结构最简单,制造最容易的一种封头形式; b.对于同样直径和压力的容器,厚度最大。
Page31
化工设备机械 基础
各种封头比较
1)从受力情况看,半球形封头最好,椭圆形和碟 形其次,球冠形和锥形更次之,平板最差; 2)从制造角度看,平板最容易,球冠形和锥形次 之,碟形和椭圆形更次,而半球形最难; 3)从使用而论:
Page5
化工设备机械 基础
设计思路:
1)对于受均匀内压封头的强度计算,不仅 要考虑封头本身因内压引起的薄膜应力,还 要考虑与筒身连接处的边缘应力。
2)在封头设计中,薄膜应力作为强度判断 中的基本应力;而把因不连续效应产生的 应力增强影响以应力增强系数的形式引入 壁厚计算式。
Page6
化工设备机械 基础
a.由球面,过渡段和直边段组成; b.过渡段的存在,降低了封头深度,便于加工; c.三部分连接处,经向曲率突变,不连续应力比 薄膜应力大,受力不佳。
Page30
化工设备机械 基础
(4)锥形封头
a.就强度而论,锥形封头的结构不理想; b.封头的形式,决定了容器的使用要求,比如,对 于气体的均匀进入和引出,悬浮或粘稠液体和固 体颗粒的排放,不同直径圆筒的过度,是理想的 结构形式。
Page35
化工设备机械 基础
标准碟形封头壁厚:
d
1.325 pcDi
2 t 0.5 pc
C2
pC=2.2MPa;Di=600mm; []t=189MPa;j=1.0,C2=1.0mm 考虑钢板厚度负偏差,取C1=0.3mm
代入并经圆整后用n=6mm钢板。
Page36
平板封头壁厚:
化工设备机械 基础
§10.1 凸形封头
- 1、下载文档前请自行甄别文档内容的完整性,平台不提供额外的编辑、内容补充、找答案等附加服务。
- 2、"仅部分预览"的文档,不可在线预览部分如存在完整性等问题,可反馈申请退款(可完整预览的文档不适用该条件!)。
- 3、如文档侵犯您的权益,请联系客服反馈,我们会尽快为您处理(人工客服工作时间:9:00-18:30)。
补充材料
1
基于水压成形技术的液体运输罐车封头的成形工艺探索
摘要:通过经水压成形的液体介质运输车辆封头和目前国内常用的平面型
封头进行对比,介绍了液体运输车封头水压成形技术的工艺原理、工艺流
程,并设计了液体运输罐式车封头水压成形技术的简易工艺装置。分析了
水压成形技术在液体介质运输车封头成形上的简易性、经济性及可行性。
分析了封头水压成形技术易出现的问题及解决方法。
关键词:水压成形;液体运输罐车;浅碟形封头;圈模;试压泵
一、技术简介
液体运输罐车是用于油类、水类及盐酸、硫酸等化工介质的罐式运输
车辆。罐体的横截面形状通常设计为不规则的形状,通常为上小下大的横
截面形状。目的是降低罐体盛装液体介质后的重心,防止在液体运输车在
急停、急转等运动过程中介质对罐体产生冲击力,导致车辆发生危险。水
压成形工艺技术是用相应的模具,利用水、油等液体的压力提供形变应力,
使工件发生塑性变形,达到工件成形的一项加工工艺技术。其水压成形的
系统通常由压力供给装置、系统密封装置、工装成形装置组成。
二、水压成形工艺技术在液体罐式运输车上的应用
目前,国内外的各种液体罐式运输车的罐体横截面形状均为不规则的异
形截面。但其封头由于缺少理想的成形方式,多采用未经压力成形的平板
形式封头。由于液体罐式运输车此类移动式罐体的工况复杂,使用温度范
围跨度大(-20℃~40℃)。并且,车辆运行过程中的启动、急停、转向等
动作对罐体封头会产生破坏冲击,容易对罐体封头产生破坏。因此,经过
三维立体成形的浅碟型封头的使用情况明显好于平板形式的封头。该技术
补充材料
2
在国内处于领先地位。
三维立体成形的浅碟形封头形式:
该工艺技术可用于油类运输罐车、盐酸、硫酸、沥青等各种化工介质
运输罐车以及洒水车等液体罐式运输车的浅碟型封头加工成形。利用不同
型号尺寸的模具可满足不同容积的液体罐式运输车封头制作的需要。
另外,对于浅碟形封头的成形技术,国内外很多同类型产品的生产厂
家采用大型压力机+成形模具的方法制造。其能耗高,需要生产场地大,
设备费用投入大,模具结构复杂,制造费用高。利用水压成形工艺技术,
采用的是平板经水压成形后进行数控切割、旋边的封头加工方法。设备费
用投入低,模具设计结构简单,制造费用低,且工件成形效果好。能很好
的解决压力机+成形模具的成形方式的缺点。
水压成形技术封头加工的工艺流程:
下料 拼板 水压成形 数控切割 封头旋边加
工 表面处理 入库验收
三、技术原理及装置
依据流体介质压力各向均匀性和流体中压力的方向为作用面的内法线
补充材料
3
方向的特点。利用流体对待加工工件施加压力,当施加于工件的变形应力
大于工件材料的屈服强度σs时,工件发生塑性变形。液罐车封头常用的材
料为碳素结构钢Q235(GB/T700),材料板厚为6mm,材料屈服强度σs为
235MPa。又由于成形模具的限制,工件逐渐形成浅碟形状。由于加工过程
工件受力情况复杂,所以针对水压成形压力数据的选择进行了大量的试验。
根据大量的试验数据表明,当水压达到4~6MPa时,可达到工件的加工要
求。
具体原理是:按照液体罐式运输车罐体截面形状制作不易产生形变的
同截面形状圈形模具。将两平面板材通过两模具将封头成形原材料及密封
垫周边压紧,向两平面板材间通入高压的液体介质并在工件加工时,通过
密封胶垫避免成形液体介质的泄漏。,根据流体的力学特点,完成浅碟形封
头的加工。达到产品要求。
1、压力供给装置
补充材料
4
压力供给装置的作用是为封头成形提供原材料塑性变形的力量。压力
供给装置采用试压泵,型号为(3DY1150/15)电机功率1.5KW,泵机额定最
高水压压力12.5MPa,流量1150L/H。泵机上设置有上限为10MPa的卸压阀,
防止因压力过高发生危险。该泵机可在任意压力值上停止加压,并自动保
压。并设置有卸压、放水阀门。可在液罐车浅碟形封头成形尺寸达到要求
后,停止加压,通过卸压阀门降低压力腔内压力,保证操作安全。试压泵
通过高压管路及接头与待加压的压力腔相可靠连接。避免压力在传输过程
中的损失。
2、系统密封装置
压力腔的密封采用的是厚度为10mm厚的硅胶垫。沿模具周边布置,宽
度为200mm。在上下圈模上采用42颗TR40×3,长度为160mm的梯形螺栓
拉紧上下圈形模具、工件及中间的硅胶垫。完成压力系统的密封。
3、工装成形装置
水压成形用的上、下圈形模具是水压成形工艺技术的关键,它直接关
系着封头的最终成形。上、下圈形模具按照所需加工的封头的截面尺寸进
行设计。为降低模具的投入费用,按照加工封头的规格大小,分尺寸范围
段进行模具制造,最后将封头通过数控等离子切割达到产品尺寸要求。从
而提高了模具的利用率,增大模具的尺寸覆盖范围,降低模具制造成本。
模具制造采用厚度为40mm的优质碳素钢45钢钢板分段等离子数控切割后,
进行拼焊的方式制造,保证模具有足够的刚性。模具上的螺栓孔按照上、
下模具螺栓孔配钻的方式加工,保证了孔的同心度。另外,制作了模具的
支架,用于模具工作时的支撑和固定。
补充材料
5
圈形模具示意图:
四、封头水压成形技术应用的优点的经济性
首先,根据受力分析比对,经过水压成形的液体罐式运输车的浅碟形
封头在使用过程中承受盛装介质冲击应力的能力明显优于平板型封头。
浅碟形封头与平板封头的受力分析对比图:
其次,与传统的大型模具成形的加工方式相比较,其主要经济效益对
补充材料
6
比如下:
1. 在设备工装投入方面,传统的压力机成形方式需投入800T压力机,及
成形模具。其投入费用上百万。而采用水压成形的加工方式,其投入为
10MPa试压泵(0.8万元),成形圈模约1.008T(约1万元),压紧螺栓
Tr40*3,L=160mm,45件(约0.5万元)。密封垫(0.2万元)共投入
费用在5万元以内。因此,采用水压成形方式的一次性投入费用远低于
传统压力机成形方式。
2. 在封头工件加工方面,800T压力机其设备功率大,能耗高。而试压泵属
于小型设备,耗能较低。其水压成形方式的成形介质可循环重复使用。
能源消耗费用低。
五、水压成形技术在应用中存在的主要问题和解决方法
1、封头钢板鼓包
在水压成形的过程中,封头钢板有时候会出现非正常鼓包凸起的现象,
其直径通常在φ80mm~φ150mm范围内。其产生的原因是封头原材料板材
材质的局部变化或是板材厚度不均。产生此缺陷后,可在凸起形成的初期,
用榔头轻敲凸起的周边,分散凸起的应力分布,减小其变形量。另一种方
法是在封头成形后,采用火焰加热校正的方法消除缺陷。
2、压力介质泄漏
在水压成形的过程中,可能出现成形介质的泄漏情况,压力随着介质
的泄漏遭到损失,影响封头的成形。出现介质泄漏的原因有以下几点:1、
压紧螺栓未完全拧紧。2、密封硅胶垫老化,出现破损。3、密封接触面没
有打磨平滑。出现这些问题的解决方法是:进一步检查螺栓的紧固情况,
补充材料
7
充分拧紧螺栓;检查密封胶垫的状况,当密封垫出现老化、破损现象时,
应及时更换,通常密封胶垫的使用寿命最长在6~8个月;检查密封接触面
的情况,对于影响密封的地方应采取措施消除。
六、水压成形工艺技术应用的注意要点
首先,为了缩短封头水压成形的加工时间,试压泵机的选择应选择流
量较大、泵机缸的数量较多的试压泵;模具材料的选用应选择具有足够强
度的材料。以免封头成形后局部变形较大,影响后续工序的加工;压紧螺
栓应选择受力较好的梯形螺纹。其次,模具拼焊后焊缝、封头原材料板材
拼焊焊缝及封头原材料气割螺栓孔后的熔渣,应用砂轮机打磨光滑,且要
求与母材表面齐平,以免影响系统的密封性。最后,由于密封胶垫是分段
形成的,在各段的连接处,应用502胶水或其他胶水进行连接,以免螺栓
压紧后密封连接处产生缝隙,引起介质泄漏。如果封头上有对接焊缝,则
必须保证焊接质量,要求焊透,以免在水压成形时,发生焊缝爆裂。
七、结束语
目前,该工艺技术已经广泛应用于油罐车、洒水车、沥青运输车及盐
酸罐式集装箱等相关产品封头的制作,成形效果良好。此技术可向更多液
体介质运输类产品上推广应用。并着重研究该技术流体压力系统密封可靠
性和提高该技术的自动化程度两个方面。以便更好的应用该项工艺技术。