精益生产的定义和特征
精益生产的概念及特点分析

精益生产的概念及特点分析引言精益生产是一种以节约资源、增加价值为中心的生产管理理念,起源于日本汽车业。
它通过最小化浪费和提高效率,实现了生产过程的优化和产品质量的提升。
本文将介绍精益生产的概念,并分析其特点。
一、精益生产的概念精益生产(Lean Production)是一种通过消除浪费、提高效率和灵活性的生产方式。
它最早由日本丰田汽车公司开发和实践,并得到广泛推广和应用。
精益生产的核心理念是尽量减少浪费,提高价值创造,从而实现成本降低和效率提高。
它通过减少库存、减少不必要的活动和流程、优化资源使用等方式,确保生产过程能够快速、高效地运转。
二、精益生产的特点1.去除浪费:精益生产强调去除各种形式的浪费,包括等待时间、过程中的缺陷、运输和库存的浪费等。
通过识别和消除浪费,企业能够大幅度提高生产效率和产品质量。
2.价值流分析:精益生产通过价值流分析,识别出创造价值的步骤和非价值增加的步骤,以便优化生产过程。
通过削减或优化非价值增加的步骤,企业能够实现资源的最大利用。
3.持续改进:精益生产强调持续改进的理念。
企业应该不断地寻求改进的机会,不断优化生产流程和提升产品质量。
通过持续改进,企业可以不断提高效率和竞争力。
4.员工参与:精益生产注重员工的参与和协作。
员工是企业的核心资产,他们的经验和智慧对于改进生产过程非常重要。
通过培养员工的参与意识和团队合作精神,企业可以更好地实现精益生产的目标。
5.质量优先:精益生产强调质量的重要性。
企业应该始终把质量放在第一位,追求卓越的产品质量。
通过不断提高产品质量,企业可以提升品牌形象、增加市场竞争力。
6.灵活性:精益生产注重灵活性和适应性。
企业应该具备快速响应市场需求的能力,同时灵活调整生产流程,以适应市场变化。
通过灵活性,企业可以更好地满足客户需求并获得竞争优势。
三、精益生产的实施步骤1.识别价值流:通过价值流分析,识别出创造价值的步骤和非价值增加的步骤。
2.消除浪费:排除所有不必要的活动和流程,减少浪费,提高效率。
精益生产精益生产概述

精益生产概述什么是精益生产精益生产是一种优化生产流程的方法,旨在通过减少浪费和提高效率来提高产品和服务的质量。
它是源于日本汽车制造业的生产哲学,最早由丰田汽车公司引入并在全球范围推广。
精益生产的核心思想是通过消除不必要的浪费和无效的步骤,使生产变得更加高效和灵活。
它的目标是提供价值,使客户能够以最低的成本获得最高的价值。
精益生产的原则精益生产遵循一些重要的原则,以实现高效生产流程。
以下是其中的一些核心原则:1.价值的识别和增加:精益生产的关键是确定顾客真正关心的价值,通过在每个工作阶段中增加价值来实现产品质量的提高。
2.流程的流畅化:为了确保材料和信息的无缝流动,精益生产强调流程的流动性。
通过减少瓶颈和不必要的等待时间,可以大大提高生产效率。
3.拉动式生产:传统的推动式生产往往会导致过剩库存和资源的浪费。
精益生产采用拉动式生产,即根据顾客需求来启动下一个生产阶段,从而保持适当的库存和资源使用。
4.高效绩效:精益生产强调通过持续改进和培养高效的团队来提高绩效。
通过培训员工,建立透明和积极的沟通,并鼓励员工参与决策和问题解决,可以激发团队的创造力和生产力。
5.持续改进:精益生产是一个持续不断的过程。
它要求不断地寻找改进的机会,并通过内部和外部反馈来完善生产流程和产品质量。
精益生产的优势精益生产作为一种优化生产流程的方法,具有许多优势,可以帮助企业获得成功。
1.提高质量:通过消除浪费和不必要的步骤,精益生产可以提高产品和服务的质量。
减少错误和缺陷的发生,提高顾客满意度。
2.提高效率:精益生产通过优化工作流程和减少浪费,提高生产效率。
通过拉动式生产,可以避免过剩和库存积压的问题。
3.降低成本:精益生产致力于降低成本,通过减少浪费和提高效率来实现这一目标。
通过精确估算和订单驱动的生产,可以减少不必要的材料和资源的浪费。
4.提高响应能力:精益生产的流程设计注重灵活性和快速响应能力。
这使得企业能够更好地适应市场需求的变化,并及时提供客户所需的产品和服务。
精益生产方式的基本特征

精益生产方式的基本特征
精益生产方式,也被称为精益制造或精益生产管理,是一种以精确满足客户需求为目标的生产方式。
其基本特征包括:
1. 价值观导向:精益生产方式以提供价值给客户为导向。
它强调对产品或服务的实际需求进行准确理解,并通过最小化浪费和不必要的活动来创造价值。
2. 浪费的消除:精益生产方式致力于消除各种形式的浪费,包括过度生产、库存积压、物料运输、等待、瑕疵品等。
它通过优化生产过程和资源利用,追求高效和高质量。
3. 及时生产:精益生产方式追求及时交付产品或服务,减少等待时间和库存积压。
它强调按需生产,以最小化库存和减少不必要的资源消耗。
4. 持续改进:精益生产方式倡导持续改进的文化。
它鼓励员工在日常工作中提出改进建议,发现问题并解决问题,以不断提高生产效率和质量。
5. 灵活性和适应性:精益生产方式注重灵活性和适应性,使企业能够迅速应对市场需求的变化。
它通过减少批量生产和提高生产的灵活性来实现快速响应客户需求的能力。
6. 基于团队合作:精益生产方式鼓励员工之间的合作和团队工作。
它倡导员工参与决策、共同解决问题,并通过团队合作实现生产环节的优化。
7. 持续培训和发展:精益生产方式强调员工的培训和发展,以提升技能和知识水平。
它通过持续学习和培训来促进员工的专业素养和自我进步。
总之,精益生产方式的基本特征包括以价值观导向、消除浪费、及时生产、持续改进、灵活性和适应性、基于团队合作以及持续培训和发展等。
这些特征共同构成了一个高效、灵活且持续改进的生产方式。
精益生产的定义和特征

精益生产的定义和特征1、精益生产的定义精益生产的实践由日本人开始到现在已有半个世纪的时间,但把它提高到理论上来研究则仅仅是最近几年的事.麻雀理工学院的教授们把这种生产方式称为“精益生产”,但在论述精益生产的经典著作《改变世界的机器》一书中,却未见给出精益生产的确切定义;此处我们引用北京航空航天大学杨光京教授给精益生产下的定义:“精益生产是通过系统结构、人员组织、运行方式和市场供求等方面的变革,使生产系统能很快适应用户需求不断变化,并能使生产过程中一切无用、多余的东西被精简,最终达到包括市场供销在内的生产的各方面最好的结果”。
2、精益生产与大批大量生产方式的比较精益生产和大批大量生产各自的优缺点已经在上节介绍过,这里我们给出比较系统的比较,如表所示。
精益生产与大批大量生产方式的比较在《改变世界的机器》一书中,精益生产的归纳者们从五个方面论述了精益生产企业的特征。
这五个方面是:工厂组织、产品设计、供货环节、顾客和企业管理。
归纳起来,精益生产的主要特征为:对外以用户为“上帝”,对内以“人”为中心,在组织机构上以“精简"为手段,在工作方法上采用“Team Work”和“并行设计",在供货方式上采用“JIT"方式,在最终目标方面为“零缺陷”.1)以用户为“上帝”产品面向用户,与用户保持密切联系,将用户纳入产品开发过程,以多变的产品,尽可能短的交货期来满足用户的需求,真正体现用户是“上帝”的精神。
不仅要向用户提供周到的服务,而且要洞悉用户的思想和要求,才能生产出适销对路的产品.产品的适销性、适宜的价格、优良的质量、快的交货速度、优质的服务是面向用户的基本内容。
2)以“人”为中心人是企业一切活动的主体,应以人为中心,大力推行独立自主的小组化工作方式。
充分发挥一线职工的积极性和创造性,使他们积极为改进产品的质量献计献策,使一线工人真正成为“零缺陷”生产的主力军。
为此,企业对职工进行爱厂如家的教育,并从制度上保证职工的利益与企业的利益挂钩.应下放部分权力,使人人有权、有责任、有义务随时解决碰到的问题。
精益生产名词解释

精益生产名词解释一、何为精益生产?精益生产管理,是一种以客户需求为拉动,以消除浪费和不断改善为核心,使企业以最少的投入获取成本和运作效益显著改善的一种全新的生产管理模式。
它的特点是强调客户对时间和价值的要求,以科学合理的制造体系来组织为客户带来增值的生产活动,缩短生产周期,提高质量,从而显著提高企业适应市场万变的能力。
精益生产管理就是控制浪费、降低成本的最有效的一种生产管理方式。
二、什么叫八大浪费八大浪费是定义工厂在JIT生产方式中的,其浪费的含义与社会上通常所说的浪费有所区别。
对于JIT 来讲,凡是超出增加产品价值所必需的绝对最少的物料、设备、人力、场地和时间的部分都是浪费。
因此,JIT生产方式所讲的工厂的浪费归纳为八大种,分别是:不良、修理的浪费,过分加工的浪费,动作的浪费,搬运的浪费,库存的浪费,制造过多过早的浪费,等待的浪费和管理的浪费,简称为八大浪费。
三、何为6S6S 起源于日本,指的是在生产现场中将人员、机器、材料、操作方法等生产要素进行有效管理,它针对企业中每位员工的日常行为方面提出要求,倡导从小事做起,力求使每位员工都养成事事“讲究”的习惯,从而达到提高整体工作质量的目的。
6S就是整理(SEIRI)、整顿(SEITON)、清扫(SEISO)、清洁(SEIKETSU)、素养(SHITSUKE)、安全(SAFETY)六个项目,因均以“S”开头,简称6S。
四、价值流价值流是指从原材料转变为成品的物料、信息流、时间流等,并给它赋予价值的全部活动,包括从供应商处购买的原材料到达企业,企业对其进行加工后转变为成品再交付客户的全过程,企业内以及企业与供应商、客户之间的信息沟通形成的信息流也是价值流的一部分。
一个完整的价值流包括增值和非增值活动,如供应链成员间的沟通,物料的运输,生产计划的制定和安排以及从原材料到产品的物质转换过程等。
五、团队和团队建设团队是指为了实现某一目标而由相互协作的个体所组成的正式群体。
什么是精益生产

什么是精益⽣产 精益⽣产⼜称精良⽣产,其中“精”表⽰精良、精确、精美;“益”表⽰利益、效益等等。
精益⽣产就是及时制造,消灭故障,消除⼀切浪费,向零缺陷、零库存进军。
它是美国⿇省理⼯学院在⼀项名为“国际汽车计划”的研究项⽬中提出来的。
它们在做了⼤量的调查和对⽐后,认为⽇本丰⽥汽车公司的⽣产⽅式(JIT)是最适⽤于现代制造企业的⼀种⽣产组织管理⽅式,称之为精益⽣产,以针对美国⼤量⽣产⽅式过⼲肿的弊病。
精益⽣产综合了⼤量⽣产与单件⽣产⽅式的优点,⼒求在⼤量⽣产中实现多品种和⾼质量产品的低成本⽣产。
丰⽥⽣产⽅式⼜称精细⽣产⽅式,或精益⽣产⽅式。
精益⽣产的定义 精益⽣产是通过系统结构、⼈员组织、运⾏⽅式和市场供求等⽅⾯的变⾰,使⽣产系统能很快适应⽤户需求不断变化,并能使⽣产过程中⼀切⽆⽤、多余的东西被精简,最终达到包括市场供销在内的⽣产的各⽅⾯最好的结果。
精益⽣产的起源 精益⽣产(Lean Production,简称LP)是美国⿇省理⼯学院数位国际汽车计划组织(IMVP)的专家对⽇本丰⽥准时化⽣产JIT(Just In Time)⽣产⽅式的赞誉称呼。
精,即少⽽精,不投⼊多余的⽣产要素,只是在适当的时间⽣产必要数量的市场急需产品(或下道⼯序急需的产品);益,即所有经营活动都要有益有效,具有经济效益。
精益⽣产⽅式源于丰⽥⽣产⽅式,是由美国⿇省理⼯学院组织世界上17个国家的专家、学者,花费5年时间,耗资500万美元,以汽车⼯业这⼀开创⼤批量⽣产⽅式和精益⽣产⽅式JIT的典型⼯业为例,经理论化后总结出来的。
精益⽣产⽅式的优越性不仅体现在⽣产制造系统,同样也体现在产品开发、协作配套、营销⽹络以及经营管理等各个⽅⾯,它是当前⼯业界最佳的⼀种⽣产组织体系和⽅式,也必将成为⼆⼗⼀世纪标准的全球⽣产体系。
精益⽣产⽅式是战后⽇本汽车⼯业遭到的“资源稀缺”和“多品种、少批量”的市场制约的产物。
它是从丰⽥相佐诘开始,经丰⽥喜⼀郎及⼤野耐⼀等⼈的共同努⼒,直到20世纪60年代才逐步完善⽽形成的。
精益生产的定义
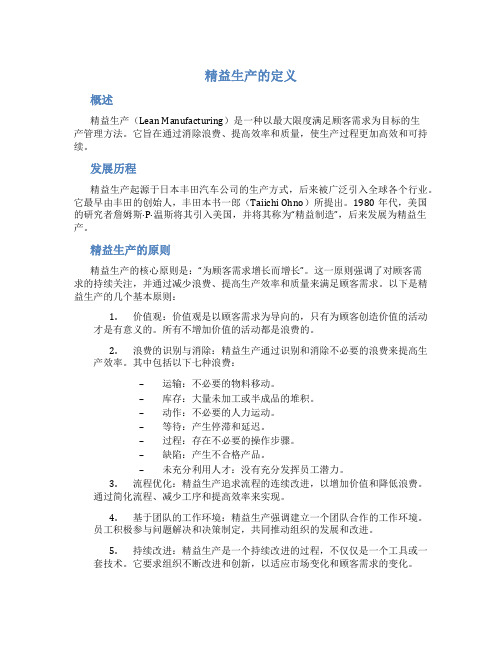
精益生产的定义概述精益生产(Lean Manufacturing)是一种以最大限度满足顾客需求为目标的生产管理方法。
它旨在通过消除浪费、提高效率和质量,使生产过程更加高效和可持续。
发展历程精益生产起源于日本丰田汽车公司的生产方式,后来被广泛引入全球各个行业。
它最早由丰田的创始人,丰田本书一郎(Taiichi Ohno)所提出。
1980年代,美国的研究者詹姆斯·P·温斯将其引入美国,并将其称为“精益制造”,后来发展为精益生产。
精益生产的原则精益生产的核心原则是:“为顾客需求增长而增长”。
这一原则强调了对顾客需求的持续关注,并通过减少浪费、提高生产效率和质量来满足顾客需求。
以下是精益生产的几个基本原则:1.价值观:价值观是以顾客需求为导向的,只有为顾客创造价值的活动才是有意义的。
所有不增加价值的活动都是浪费的。
2.浪费的识别与消除:精益生产通过识别和消除不必要的浪费来提高生产效率。
其中包括以下七种浪费:–运输:不必要的物料移动。
–库存:大量未加工或半成品的堆积。
–动作:不必要的人力运动。
–等待:产生停滞和延迟。
–过程:存在不必要的操作步骤。
–缺陷:产生不合格产品。
–未充分利用人才:没有充分发挥员工潜力。
3.流程优化:精益生产追求流程的连续改进,以增加价值和降低浪费。
通过简化流程、减少工序和提高效率来实现。
4.基于团队的工作环境:精益生产强调建立一个团队合作的工作环境。
员工积极参与问题解决和决策制定,共同推动组织的发展和改进。
5.持续改进:精益生产是一个持续改进的过程,不仅仅是一个工具或一套技术。
它要求组织不断改进和创新,以适应市场变化和顾客需求的变化。
实施精益生产的关键步骤要成功实施精益生产,组织需要采取一系列关键步骤:1.指定目标:设定明确的目标和指标,以推动改进工作的进行。
这些目标应该与顾客需求和组织的战略一致。
2.流程分析:对组织的生产流程进行详细分析,识别出存在的浪费和瓶颈,并确定改进的重点。
精益生产运营体系之精益生产3大特征
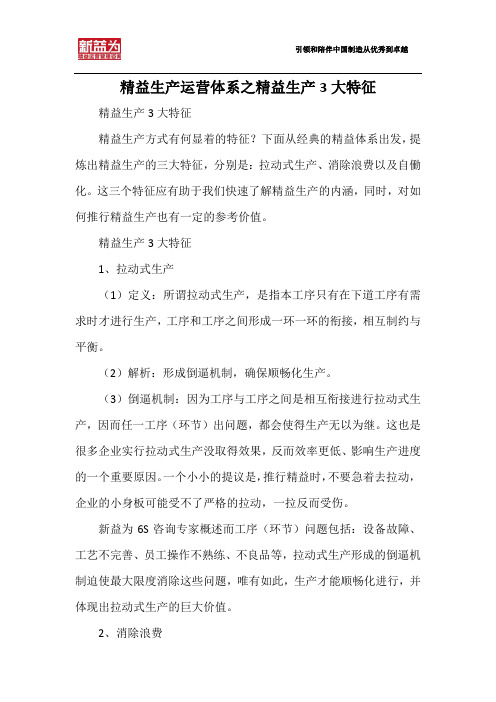
精益生产运营体系之精益生产3大特征精益生产3大特征精益生产方式有何显着的特征?下面从经典的精益体系出发,提炼出精益生产的三大特征,分别是:拉动式生产、消除浪费以及自働化。
这三个特征应有助于我们快速了解精益生产的内涵,同时,对如何推行精益生产也有一定的参考价值。
精益生产3大特征1、拉动式生产(1)定义:所谓拉动式生产,是指本工序只有在下道工序有需求时才进行生产,工序和工序之间形成一环一环的衔接,相互制约与平衡。
(2)解析:形成倒逼机制,确保顺畅化生产。
(3)倒逼机制:因为工序与工序之间是相互衔接进行拉动式生产,因而任一工序(环节)出问题,都会使得生产无以为继。
这也是很多企业实行拉动式生产没取得效果,反而效率更低、影响生产进度的一个重要原因。
一个小小的提议是,推行精益时,不要急着去拉动,企业的小身板可能受不了严格的拉动,一拉反而受伤。
新益为6S咨询专家概述而工序(环节)问题包括:设备故障、工艺不完善、员工操作不熟练、不良品等,拉动式生产形成的倒逼机制迫使最大限度消除这些问题,唯有如此,生产才能顺畅化进行,并体现出拉动式生产的巨大价值。
2、消除浪费(1)定义:消除浪费,即消除生产过程中影响顺畅化的各种障碍。
(2)解析:消除浪费被视为精益生产的核心,因为只有消除生产过程中的种种障碍,拉动式生产才能顺利进行。
即便不实施拉动式生产,消除浪费本身对提升生产效率也有明显的贡献。
消除浪费的另一大作用是推进生产作业从“省力化”向“少人化”过渡。
(3)七大浪费的管理:在精益生产中,总结有七大浪费,分别是:①运输浪费;②动作浪费;③加工浪费;④不良浪费;⑤等待浪费;⑥过量生产;⑦库存浪费。
其中,运输浪费、动作浪费、等待浪费及加工浪费一般可通过工业工程手法进行消除,这是精益生产与工业工程的共通之处。
不良浪费,是一种“显性浪费”,不良导致的成本损失是清晰可见的。
不良浪费的消除,不应局限于精益生产的工具(三现主义、五个为什么、全面质量管理、全员预防性防护等),可结合6西格码工具进行项目型改善。
- 1、下载文档前请自行甄别文档内容的完整性,平台不提供额外的编辑、内容补充、找答案等附加服务。
- 2、"仅部分预览"的文档,不可在线预览部分如存在完整性等问题,可反馈申请退款(可完整预览的文档不适用该条件!)。
- 3、如文档侵犯您的权益,请联系客服反馈,我们会尽快为您处理(人工客服工作时间:9:00-18:30)。
三、精益生产的特征
在《改变世界的机器》一书中,精益生产的归纳者们从五个方面论述了精益生产企业的特征。
这五个方面是:工厂组织、产品设计、供货环节、顾客和企业管理。
归纳起来,精益生产的主要特征为:对外以用户为“上帝”,对内以“人”为中心,在组织机构上以“精简”为手段,在工作方法上采用“Team Work”和“并行设计”,在供货方式上采用“JIT”方式,在最终目标方面为“零缺陷”。
1)以用户为“上帝”
产品面向用户,与用户保持密切联系,将用户纳入产品开发过程,以多变的产品,尽可能短的交货期来满足用户的需求,真正体现用户是“上帝”的精神。
不仅要向用户提供周到的服务,而且要洞悉用户的
思想和要求,才能生产出适销对路的产品。
产品的适销性、适宜的价格、优良的质量、快的交货速度、优质的服务是面向用户的基本内容。
2)以“人”为中心
人是企业一切活动的主体,应以人为中心,大力推行独立自主的小组化工作方式。
充分发挥一线职工的积极性和创造性,使他们积极为改进产品的质量献计献策,使一线工人真正成为“零缺陷”生产的主力军。
为此,企业对职工进行爱厂如家的教育,并从制度上保证职工的利益与企业的利益挂钩。
应下放部分权力,使人人有权、有责任、有义务随时解决碰到的问题。
还要满足人们学习新知识和实现自我价值的愿望,形成独特的,具有竞争意识的企业文化。
3)以“精简”为手段
在组织机构方面实行精简化,去掉一切多余的环节和人员。
实现纵向减少层次,横向打破部门壁垒,将层次细分工,管理模式转化为分布式平行网络的管理结构。
在生产过程中,采用先进的柔性加工设备,减少非直接生产工人的数量,使每个工人都真正对产品实现增值。
另外,采用JIT和Kanban方式管理物流,大幅度减少甚至实现零库存,也减少了库存管理人员、设备和场所。
此外,精益不仅仅是指减少生产过程的复杂性,还包括在减少产品复杂性的同时,提供多样化的产品。
4)Team Work和并行设计
精益生产强调Team Work工作方式进行产品的并行设计。
Team Work(综合工作组)是指由企业备部门专业人员组成的多功能设计组,对产品的开发和生产具有很强的指导和集成能力。
综合工作组全面负责一个产品型号的开发和生产,包括产品设计、工艺设计、编制预算、材料购置、生产准备及投产等工作。
并根据实际情况调整原有的设计和计划。
综合工作组是企业集成各方面人才的一种组织形式。
5)JIT供货方式
JIT工作方式可以保证最小的库存和最少在制品数。
为了实现这种供货方式,应与供货商建立起良好的合作关系,相互信任,相互支持,利益共沾。
6)“零缺陷”工作目标
精益生产所追求的目标不是“尽可能好一些”,而是“零缺陷”。
即最低的成本、最好的质量、无废品、零库存与产品的多样性。
当然,这样的境界只是一种理想境界,但应无止境地去追求这一目标,才会使企业永远保持进步,永远走在他人的前头。
四、精益生产的体系构成
如果把精益生产体系看作一幢大厦,它的基础就是在计算机网络支持下的、以小组方式工作的并行工作方式。
在此基础上的三根支柱就是:
1)全面质量管理,它是保证产品质量,达到零缺陷目标的主要措施;
2)准时生产和零库存,它是缩短生产周期和降低生产成本的主要方法;
3)成组技术,这是实现多品种、按顾客定单组织生产、扩大批量、降低成本的技术基础。
这幢大厦的屋顶就是精益生产体系。