铣加工参数自动计算表
UG数控加工的参数设置【大全】

切削参数打开“切削参数”图标,系统会显示“切削参数”对话框,第一栏:策略(既一些加工参数值的设定)1、切削方向:顺铣:刀具一般多采用顺铣,因为由顺铣加工完成时工件的表示光洁度比较好!另一个原因是顺铣时刀具的受损要比逆铣轻的多!所以多采用顺铣。
从外向内用逆洗。
从内向外用顺洗。
2、逆铣:多适用于一些粗糙的工件开粗,加工完成后工件的光洁度不好,而且刀具受损严重!所以一般不利用逆铣。
3、切削角:当使用“单向式”切削,“往复式”切削“单向带轮廓”铣切削三种方法时在切削参数里才显示切削角的定义,其意思为所生成的刀轨是平行X向为零,平行于Y向为90度,可根据自己的要求定义切削角度,多采用45度斜进刀可在切削角下的度数栏内,输入所定义的角度值,如果想看一下角度方向时,可点示显示切削方向的图标。
3、壁:当使用“单向铣削”,“往复式铣削”和“跟随周边”时切削参数里面才有壁选项,“单向”和“往复”铣削里面只有三项。
其一:无,它的意思为只切削腔,不去清壁,其二,在起点:刀具在下刀后先把壁清理完,然后再切削腔。
其三,在终点:刀具在下刀后把腔切削完成后,到最后一刀把壁清理干净,无论是“起点”清壁还是“终点”清壁,都是以层为单位,如果没有“自动”清壁的情况使用在“终点”清壁。
如果有“自动”清壁时优先使用“自动”清壁,“自动”清壁的意思是:系统给计算一个最适合清壁时清壁。
4、添加精割削刀路数本功能是以UG5.0版本才增加的新功能,它能有效的控制几何体的余量更加均匀,所以在型腔铣开粗时打上对号,让其忝加“1”刀路数,精加工的步距可根据情况而定,但本步距最好要小一些。
5、毛坯:1、本栏下的毛坯距离和外部(面铣削对话框中)毛坯距离相同。
2。
Extend to part outline :是指毛坯延展,默认延展至体的最大外形轮廓线因此我们不采用。
3、合并距离:当所加工的平面为两个或两个以上时,指定距离大于或等于两个面之间的距离,想要学习UG编程领取学习资料在群496610960可以帮助你两个面刀路会自动合并成一个刀路,但要求所选择的面必须在同一高度上,所指定的值可使用刀具的百分比或mm。
机加工时间计算器

机加工时间计算器
(最新版)
目录
1.机加工时间计算器的概念和作用
2.机加工时间计算器的主要参数和输入数据
3.机加工时间计算器的使用方法和步骤
4.机加工时间计算器的应用实例
5.机加工时间计算器的优缺点及发展趋势
正文
一、机加工时间计算器的概念和作用
机加工时间计算器是一种用于计算机械加工过程中各个工序所需时间的工具,可以帮助工程师和操作人员快速、准确地估算出零件加工所需的时间,从而提高生产效率、降低成本。
二、机加工时间计算器的主要参数和输入数据
机加工时间计算器主要需要输入以下数据:零件的工艺路线、各工序的加工方式、切削速度、进给速度、刀具类型、刀具直径等。
根据这些数据,计算器将自动计算出每个工序所需的加工时间。
三、机加工时间计算器的使用方法和步骤
1.输入零件的工艺路线:首先需要输入零件的工艺路线,包括各个工序的加工方式、加工顺序等。
2.输入加工参数:根据工艺路线,输入各个工序的加工参数,如切削速度、进给速度、刀具类型、刀具直径等。
3.启动计算:输入完所有数据后,启动计算器,计算器将自动计算出每个工序的加工时间。
4.查看结果:查看计算结果,确认无误后,可将结果用于制定生产计划、调度人员和设备等。
四、机加工时间计算器的应用实例
以加工一个轴类零件为例,其工艺路线包括:铣削外圆、车削端面、钻孔、攻丝等工序。
输入相应的数据后,计算器将自动计算出每个工序所需的时间,从而帮助工程师制定合理的生产计划。
五、机加工时间计算器的优缺点及发展趋势
优点:计算速度快、准确性高,有助于提高生产效率、降低成本。
缺点:需要输入的数据较多,对操作人员的技术水平有一定要求。
工时计算方法大全(各机床工时、各工序工时)
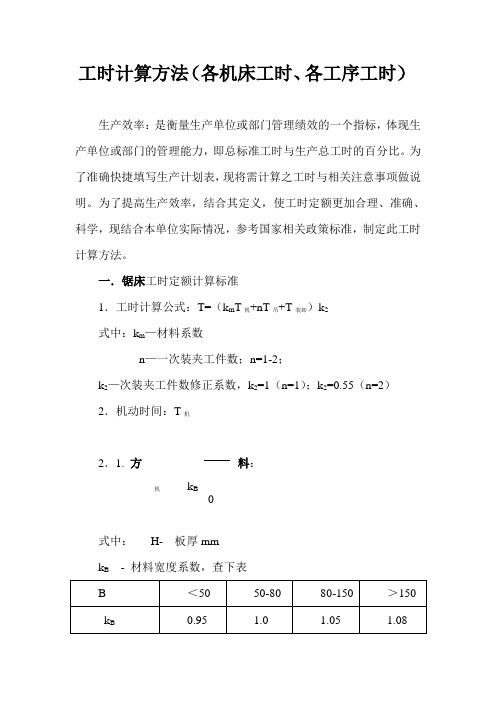
工时计算方法(各机床工时、各工序工时)生产效率:是衡量生产单位或部门管理绩效的一个指标,体现生产单位或部门的管理能力,即总标准工时与生产总工时的百分比。
为了准确快捷填写生产计划表,现将需计算之工时与相关注意事项做说明。
为了提高生产效率,结合其定义,使工时定额更加合理、准确、科学,现结合本单位实际情况,参考国家相关政策标准,制定此工时计算方法。
一.锯床工时定额计算标准1.工时计算公式:T=(k m T 机+nT 吊+T 装卸)k 2 式中:k m —材料系数n —一次装夹工件数;n=1-2;k 2—次装夹工件数修正系数,k 2=1(n=1);k 2=0.55(n=2) 2.机动时间:T 机 2.1. 方料:式中: H- 板厚mm k B - 材料宽度系数,查下表T 机=k BH22.2.棒料:式中D —棒料外径 mm2.3. 管料:式中d 0—管料内径;mm2.4..方管:式中:H—方管外形高mm ;H 0—方管内腔高mm ; B 0—方管内腔宽mm ;3.吊料时间:4.装卸料时间及其它时间:T机=D24T 机=D —d 02 2410000T 机=H—H 0*B 0208000T吊=L 1000 T装卸LD综上所述:方料:T=(0.12+n0.0519H+0.001L )k 2-0.00013 H 0*B 0 (min ) 圆料:T=(0.12+n0.0429D+0.001L )k 2-0.0001 d 02 (min ) n —一次装夹工件数;n=1-2;k 2—次装夹工件数修正系数,k 2=1(n=1);k 2=0.55(n=2)二.剪板冲压折弯工时定额计算标准1..剪板工时定额计算方法剪板单件工时定额:a —每块工时系数、见表b —剪角次数剪板工时系数表=0.12+1800840T =k *a+b a3注:准备工时按100件基数计算,每件0.2,共计200分剪板毛刺工时:T=0.3 + 处理长度/400剪板校正T校=k*T材料系数K=1~1.52.冲压每冲一次工时3..折弯工时定额计算方法折弯工时定额:t2=Σa i折弯工时定额系数表注:规格栏中,为折弯长度,a为每折一刀的工时(理论计算:每刀0.15分×折1.5=0.225+0.2=0.425→0.5)↓准备工时三.风割焊接工时定额计算标准1.风割工时公式:修磨工时含补焊工时: T 修磨 = T 风割 /22.焊接单件工时: T 焊接=T 工件装卸+T 点焊+ T 全焊 2.1 装卸工件工时:T 工件装卸=(T 01+0.2n )B式中:T 01—装卸基本工时;(取T 01=0.2); n-- 工件数 B-- 重量系数(见表)2.2. 点焊单件工时:T 点焊= T 02+0.1J+0.1N式中:T 02—点焊基本工时;J —点焊数;N —点焊时工件翻转次数;2.3. 全焊单件工时:T 全焊= T 03+0.1M+0.1N+L Σ/200+0.2NC 式中:T 03—全焊基本工时;M —焊缝段数;N —全焊时工件翻转次数;L Σ--焊缝长 NC---焊接参数调节次数注:小件装卸与点焊工时合并,统称点焊工时; 重量系数(B )T风割=风割长度×3+1.5V1、飞溅按焊接工时的二分之一计算+0.12、校正按焊接工时的二分之一计算+0.13、有辅助工帮助表卸模,从焊接工时中分取三分之一4、焊接有准备工时按每项20分钟5、点焊螺母按0.5分钟一个四.钻床工时定额1、T=kT机+ T装卸其中k—难度系数有工差要求k=1.5 有深度要求k=1.1 扩孔及攻丝k=0.82、机动时间:T机注:L/D≥8时,须另增排屑时间60%。
锯片铣刀切削速度计算【干货经验】
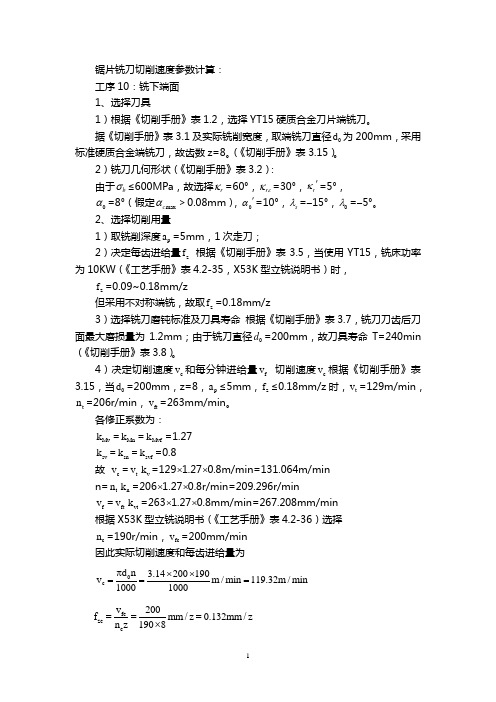
锯片铣刀切削速度参数计算: 工序10:铣下端面 1、选择刀具1)根据《切削手册》表1.2,选择YT15硬质合金刀片端铣刀。
据《切削手册》表3.1及实际铣削宽度,取端铣刀直径0d 为200mm ,采用标准硬质合金端铣刀,故齿数z=8。
(《切削手册》表3.15)。
2)铣刀几何形状(《切削手册》表3.2):由于b σ≤600MPa ,故选择r κ=60°,r εκ=30°,r κ'=5°,0α=8°(假定max c α>0.08mm ),0α'=10°,s λ=-15°,0λ=-5°。
2、选择切削用量1)取铣削深度p a =5mm ,1次走刀;2)决定每齿进给量z f 根据《切削手册》表3.5,当使用YT15,铣床功率为10KW (《工艺手册》表4.2-35,X53K 型立铣说明书)时,z f =0.09~0.18mm/z但采用不对称端铣,故取z f =0.18mm/z3)选择铣刀磨钝标准及刀具寿命 根据《切削手册》表3.7,铣刀刀齿后刀面最大磨损量为1.2mm ;由于铣刀直径0d =200mm ,故刀具寿命T=240min (《切削手册》表3.8)。
4)决定切削速度c v 和每分钟进给量f v 切削速度c v 根据《切削手册》表3.15,当0d =200mm ,z=8,p a ≤5mm ,z f ≤0.18mm/z 时,t v =129m/min ,t n =206r/min ,ft v =263mm/min 。
各修正系数为:Mv k =Mn k =Mvf k =1.27 sv k =sn k =svf k =0.8故 c v =t v v k =129⨯1.27⨯0.8m/min=131.064m/min n=t n n k =206⨯1.27⨯0.8r/min=209.296r/minf v =ft v vt k =263⨯1.27⨯0.8mm/min=267.208mm/min 根据X53K 型立铣说明书(《工艺手册》表4.2-36)选择c n =190r/min ,fc v =200mm/min 因此实际切削速度和每齿进给量为0c d n 3.14200190v m /min 119.32m /min 10001000π⨯⨯=== fc zc c v 200f mm /z 0.132mm /z n z 1908===⨯5)校验机床功率 根据《切削手册》表3.23,当b σ<560MPa ,e a ≤138mm ,p a ≤5.9mm ,0d =200mm ,z=8,f v =200mm/min ,近视为cc P =7.8KW根据X53K 型立铣说明书(《工艺手册》表4.2-35),机床主轴允许的功率为cM P =10⨯0.85KW=8.5KW故cc P <cM P ,因此所选择的切削用量可以采用,即p a =5mm ,f v =200mm/min ,n=190r/min ,c v =119.32m/min ,z f =0.132mm/z 。
数控铣加工参数自动计算表

机加工时间计算器
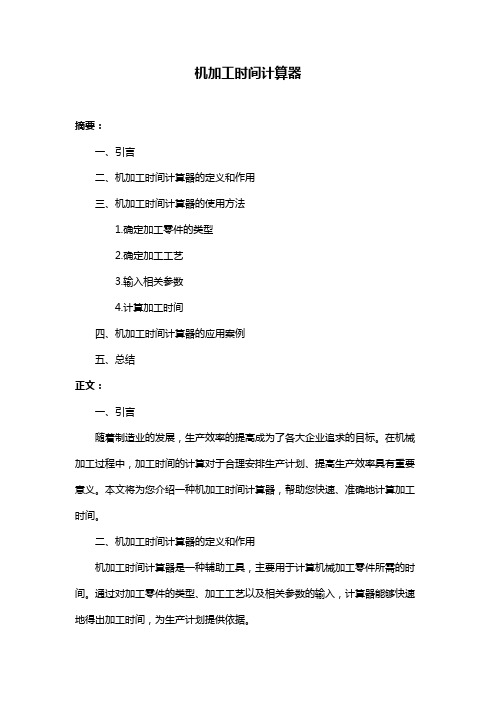
机加工时间计算器摘要:一、引言二、机加工时间计算器的定义和作用三、机加工时间计算器的使用方法1.确定加工零件的类型2.确定加工工艺3.输入相关参数4.计算加工时间四、机加工时间计算器的应用案例五、总结正文:一、引言随着制造业的发展,生产效率的提高成为了各大企业追求的目标。
在机械加工过程中,加工时间的计算对于合理安排生产计划、提高生产效率具有重要意义。
本文将为您介绍一种机加工时间计算器,帮助您快速、准确地计算加工时间。
二、机加工时间计算器的定义和作用机加工时间计算器是一种辅助工具,主要用于计算机械加工零件所需的时间。
通过对加工零件的类型、加工工艺以及相关参数的输入,计算器能够快速地得出加工时间,为生产计划提供依据。
三、机加工时间计算器的使用方法1.确定加工零件的类型:首先,您需要明确要加工的零件属于哪一种类型,例如轴类零件、盘类零件等。
不同类型的零件,其加工工艺和所需时间有所差异。
2.确定加工工艺:在明确零件类型后,您需要确定加工工艺,如车削、铣削、钻孔等。
每种工艺的加工时间计算方法不同,因此需要选择正确的工艺。
3.输入相关参数:根据所选工艺,您需要输入一些关键参数,如零件直径、长度、材料等。
这些参数将影响加工时间计算的准确性。
4.计算加工时间:在输入完所有参数后,点击“计算”按钮,计算器将自动为您计算出加工时间。
四、机加工时间计算器的应用案例某企业生产部门需要为一批轴类零件安排生产计划,他们使用机加工时间计算器进行计算。
首先,他们确定零件类型为轴类零件;然后,选择车削工艺;接着,输入相关参数,如零件直径、长度、材料等;最后,计算器自动计算出每个零件的加工时间为2 小时。
生产部门根据计算结果,合理安排生产计划,确保生产效率的提高。
五、总结机加工时间计算器是一种实用的工具,能够帮助企业快速、准确地计算加工时间,为生产计划提供依据。
机械零件加工工时计算公式

0.3
500.00 10
>硬质合金端铣、周精铣平面、凸台、凹槽理论工时计算<
零件参数 材料种类 材料硬度 HBS
加工特征类型
刀具、机床参数
灰铸铁 刀具直径 mm
300.0
150-225 刀具齿数
18
平面 走刀路径长度
430.00
表面粗糙度要求Ra
加工余量 mm
3.00
0.8
工件速度
5
工作台充满系数
0.25
工件要求尺寸精度
0.02
推荐磨削参数
15 0.3 0.15 0.04600 12.80
0.80 0.80
1.4
>>>>>>>高速钢半精铣平面、凸台、凹槽理论工时计算<<<<<<<
材料种类 材料硬度 HBS 加工特征类型 走刀路径长度 mm
零件、刀具参数 铝镁合金 刀具类型
1、该表 中每一种 加工方式 的理论工 时为单道 工步的切 削时间, 仅用于参 考,总的 切削时间 为所有工 步切削时 间的总和
2、总加 工成本可 以参考以 下计算公 式: C总 = 单位时 间机床的 切削成本 * 切削时 间 + 单位 时间机床 非切削成 本 * 所有 装夹、换 刀等动作 时间 + 其 它非加工 费用
车间内某 一工序的 生产率限 制了整个 车间的生 产率的提 高时,该 工序的刀 具寿命要 选得低 些;当某 工序单位 时间内所 分担到的 全厂开支 M较大 时,刀具 寿命也应 选得低些 。
大件精加 工时,为 保证至少 完成一次 走刀,避 免切削时 中途换 刀,刀具 寿命应按 零件精度 和表面粗 糙度来确 定。
机械加工工时定额(车、铣、镗)切削用量参考表
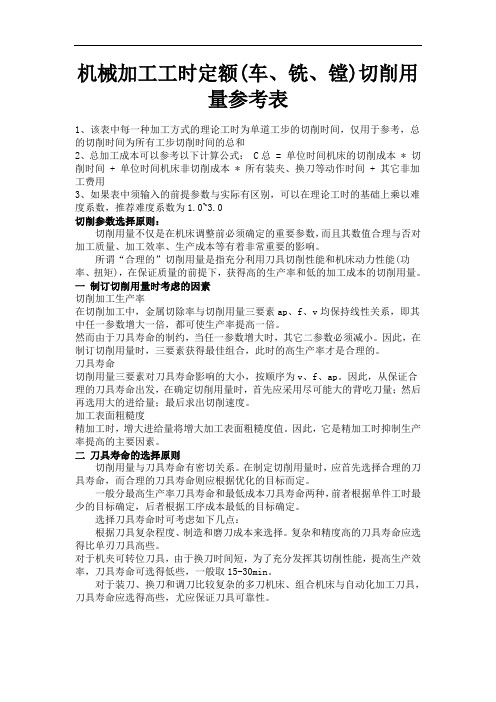
机械加工工时定额(车、铣、镗)切削用量参考表1、该表中每一种加工方式的理论工时为单道工步的切削时间,仅用于参考,总的切削时间为所有工步切削时间的总和2、总加工成本可以参考以下计算公式: C总 = 单位时间机床的切削成本 * 切削时间 + 单位时间机床非切削成本 * 所有装夹、换刀等动作时间 + 其它非加工费用3、如果表中须输入的前提参数与实际有区别,可以在理论工时的基础上乘以难度系数,推荐难度系数为1.0~3.0切削参数选择原则:切削用量不仅是在机床调整前必须确定的重要参数,而且其数值合理与否对加工质量、加工效率、生产成本等有着非常重要的影响。
所谓“合理的”切削用量是指充分利用刀具切削性能和机床动力性能(功率、扭矩),在保证质量的前提下,获得高的生产率和低的加工成本的切削用量。
一制订切削用量时考虑的因素切削加工生产率在切削加工中,金属切除率与切削用量三要素ap、f、v均保持线性关系,即其中任一参数增大一倍,都可使生产率提高一倍。
然而由于刀具寿命的制约,当任一参数增大时,其它二参数必须减小。
因此,在制订切削用量时,三要素获得最佳组合,此时的高生产率才是合理的。
刀具寿命切削用量三要素对刀具寿命影响的大小,按顺序为v、f、ap。
因此,从保证合理的刀具寿命出发,在确定切削用量时,首先应采用尽可能大的背吃刀量;然后再选用大的进给量;最后求出切削速度。
加工表面粗糙度精加工时,增大进给量将增大加工表面粗糙度值。
因此,它是精加工时抑制生产率提高的主要因素。
二刀具寿命的选择原则切削用量与刀具寿命有密切关系。
在制定切削用量时,应首先选择合理的刀具寿命,而合理的刀具寿命则应根据优化的目标而定。
一般分最高生产率刀具寿命和最低成本刀具寿命两种,前者根据单件工时最少的目标确定,后者根据工序成本最低的目标确定。
选择刀具寿命时可考虑如下几点:根据刀具复杂程度、制造和磨刀成本来选择。
复杂和精度高的刀具寿命应选得比单刃刀具高些。
对于机夹可转位刀具,由于换刀时间短,为了充分发挥其切削性能,提高生产效率,刀具寿命可选得低些,一般取15-30min。
- 1、下载文档前请自行甄别文档内容的完整性,平台不提供额外的编辑、内容补充、找答案等附加服务。
- 2、"仅部分预览"的文档,不可在线预览部分如存在完整性等问题,可反馈申请退款(可完整预览的文档不适用该条件!)。
- 3、如文档侵犯您的权益,请联系客服反馈,我们会尽快为您处理(人工客服工作时间:9:00-18:30)。
设定参数:请按提示选择或输入参数 根据设定之参数得到的机床信息 机床类型 机床设定 工件设定