产品质量检验规程
产品出厂质检规程

产品出厂质检规程目的本质检规程旨在确保产品在出厂前经过严格检验,以满足质量标准和客户需求。
通过执行此规程,我们将提供高质量的产品,增强客户满意度,并维护本公司声誉。
范围本质检规程适用于所有产品的出厂质量检验,包括但不限于以下方面:1. 外观检查2. 尺寸和尺寸精度3. 材料成分和硬度4. 功能性测试5. 安全性测试6. 包装完整性和标识7. 文件和相关记录的完整性和准确性质检流程1. 检查员根据产品规范和相关标准准备质检任务清单。
2. 外观检查:检查产品外观是否有任何缺陷、损伤或表面不整洁。
3. 尺寸和尺寸精度检查:使用合适的仪器和测量工具对产品的关键尺寸进行测量和检查。
4. 材料成分和硬度检查:通过样品取样和实验室测试确认产品使用的材料成分和硬度是否符合要求。
5. 功能性测试:根据产品规范和测试计划执行功能测试以验证产品的性能和功能是否达到预期。
6. 安全性测试:如适用,进行安全性测试以确保产品在正常使用情况下不会对用户造成伤害。
7. 包装完整性和标识:检查产品包装是否完好无损,并确认产品标识是否准确和清晰可辨认。
8. 文件和相关记录的完整性和准确性:审查相关文件和记录,确保其完整性,准确性和合规性。
检验标准产品出厂质检应根据产品规范以及国家和行业相关标准进行评判。
合格的产品必须符合以下标准:1. 外观良好,无明显缺陷2. 尺寸和尺寸精度符合规定的容差范围3. 材料成分和硬度满足要求标准4. 功能性测试通过,符合产品规范5. 安全性测试合格,符合相关安全标准6. 包装完好无损,标识准确可读7. 文件和相关记录完整、准确、合规质检记录每次质检都需要记录以下信息:1. 产品信息:产品型号、批次号、生产日期等2. 检验员信息:检验员姓名、检验日期等3. 检验结果:检查每个检验项目的结果,包括合格或不合格4. 异常处理:如有不合格项目,记录异常情况和采取的纠正措施所有的质检记录都应妥善保管并便于查阅,以备将来评估和审计之用。
产品质量检验规程
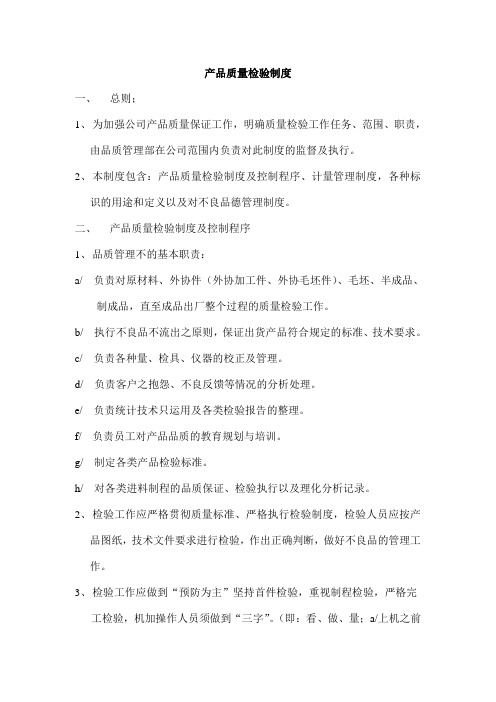
产品质量检验制度一、总则;1、为加强公司产品质量保证工作,明确质量检验工作任务、范围、职责,由品质管理部在公司范围内负责对此制度的监督及执行。
2、本制度包含:产品质量检验制度及控制程序、计量管理制度,各种标识的用途和定义以及对不良品德管理制度。
二、产品质量检验制度及控制程序1、品质管理不的基本职责:a/ 负责对原材料、外协件(外协加工件、外协毛坯件)、毛坯、半成品、制成品,直至成品出厂整个过程的质量检验工作。
b/ 执行不良品不流出之原则,保证出货产品符合规定的标准、技术要求。
c/ 负责各种量、检具、仪器的校正及管理。
d/ 负责客户之抱怨、不良反馈等情况的分析处理。
e/ 负责统计技术只运用及各类检验报告的整理。
f/ 负责员工对产品品质的教育规划与培训。
g/ 制定各类产品检验标准。
h/ 对各类进料制程的品质保证、检验执行以及理化分析记录。
2、检验工作应严格贯彻质量标准、严格执行检验制度,检验人员应按产品图纸,技术文件要求进行检验,作出正确判断,做好不良品的管理工作。
3、检验工作应做到“预防为主”坚持首件检验,重视制程检验,严格完工检验,机加操作人员须做到“三字”。
(即:看、做、量;a/上机之前先看一下代加工件有无不良;b/确认后再上机;c/下机后测量一下是否符合要求。
)加强关键工序、关键零件、关键产品的质量检验,并须建立质量记录存档。
4、检验人员要努力做好“三员”(质量检验员、质量宣传员、质量分析员)检查工艺操作规程,贯彻执行情况,遇到违规操作情况应及时劝阻,必要时向该部门负责人反映,迅速采取措施。
5、不定期组织抽查库存、合格半成品、成品,考核检验工作的质量。
6、做好计量理化工作、严格量检具,周期检定维护。
7、生产过程的质量检验;a/ 各环节检验人员,应按产品图纸,技术标准和工艺规程的要求进行检验,合格产品,由检验人员签字后随《产品QC工程表》流入下道工序,不良品应开具《不良品通知单》交品管部办理手续处理。
产品质量检验操作规程

产品质量检验操作规程一、概述产品质量检验操作规程旨在确保产品质量的稳定和可靠,并规范产品质量检验的流程和要求。
本规程适用于各类产品的质量检验,旨在为相关人员提供操作指引,以确保产品符合质量标准和客户要求。
二、检验流程1. 准备工作a. 确定检验样品的数量和类型。
b. 验收并确认检验设备的完好性和准确性。
2. 样品接收与登记a. 在样品接收登记表中记录样品的基本信息,包括样品编号、接收时间等。
b. 对样品进行初步检查,确保外观完好,并记录初步检查结果。
3. 样品准备a. 根据检验项目的要求,对样品进行处理,如切割、分离等。
b. 对样品进行标记,并记录标记信息。
4. 检验操作a. 根据产品的质量标准和检验项目,进行相应的检验操作。
b. 检验操作包括外观检查、尺寸测量、功能测试等,根据具体产品和标准调整检验项目。
c. 严格按照检验标准进行操作,确保检验结果的准确性和可靠性。
5. 结果记录与分析a. 对检验结果进行记录,并在检验报告中标注。
b. 如发现不合格项,及时通知相关部门进行处理,并记录处置情况。
6. 报告编制与审核a. 根据检验结果,编制检验报告。
b. 检验报告包括样品信息、检验结果、不合格项处理情况等。
c. 报告由检验人员编制,并由质量部门进行审核和确认。
7. 结论和处置a. 根据检验结果和质量要求,给出产品的质量结论。
b. 对不合格项进行合理的处置,如修理、退货等。
8. 数据分析与反馈a. 定期对产品质量检验的数据进行汇总和分析。
b. 根据分析结果提出改进措施,并向相关部门反馈。
三、责任与权限1. 质量部门负责制定、修订和执行本操作规程,并对检验结果负责。
2. 检验人员应具备相关的专业知识和技能,并按照规程要求进行操作。
3. 各部门及时提供所需的样品和设备,并配合检测工作的开展。
4. 质量监督部门定期对检验过程进行监督和检查,确保规程的有效实施。
四、附则1. 本操作规程的修订应经过质量部门审核和确认,并进行合理的培训和推广。
产品质量 检验规程(二)2024
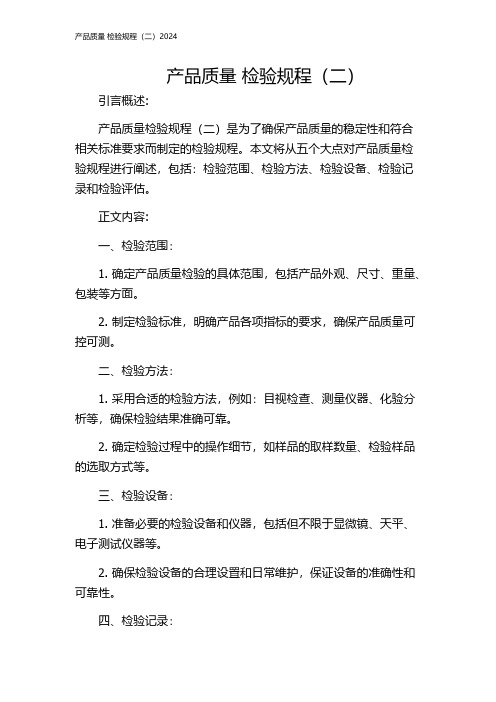
产品质量检验规程(二)引言概述:
产品质量检验规程(二)是为了确保产品质量的稳定性和符合相关标准要求而制定的检验规程。
本文将从五个大点对产品质量检验规程进行阐述,包括:检验范围、检验方法、检验设备、检验记录和检验评估。
正文内容:
一、检验范围:
1. 确定产品质量检验的具体范围,包括产品外观、尺寸、重量、包装等方面。
2. 制定检验标准,明确产品各项指标的要求,确保产品质量可控可测。
二、检验方法:
1. 采用合适的检验方法,例如:目视检查、测量仪器、化验分析等,确保检验结果准确可靠。
2. 确定检验过程中的操作细节,如样品的取样数量、检验样品的选取方式等。
三、检验设备:
1. 准备必要的检验设备和仪器,包括但不限于显微镜、天平、电子测试仪器等。
2. 确保检验设备的合理设置和日常维护,保证设备的准确性和可靠性。
四、检验记录:
1. 记录每次检验的过程和结果,包括样品编号、检验日期、检验员等信息。
2. 运用科学的标准和方法记录检验数据,确保数据的真实性和可追溯性。
五、检验评估:
1. 对检验结果进行评估和分析,判断产品是否符合质量要求。
2. 提出改进意见和措施,优化产品质量的检验流程和控制方法。
总结:
产品质量检验规程(二)对于确保产品质量的稳定性和符合相关标准要求起着至关重要的作用。
通过明确检验范围、采用合适的检验方法、配置必要的检验设备、记录检验过程和结果、以及对检验结果进行评估,可以有效提升产品质量的控制和管理水平。
公司应严格按照该检验规程的要求进行产品质量检验,促进产品质量的不断改进,提升企业竞争力。
生产过程产品质量检验操作规程

生产过程产品质量检验操作规程一、前言生产过程中,产品质量的检验工作起着至关重要的作用。
为了确保产品质量的稳定性和可靠性,制定本操作规程以规范生产过程产品质量的检验工作。
二、适用范围本操作规程适用于生产过程中对产品质量进行检验的各个环节,包括原材料进货、加工过程、包装过程等。
三、检验设备1.检验设备应满足国家标准和标准化要求,并定期进行校验和维护。
2.检验设备应按照使用要求进行放置和保管,保持清洁、整齐。
四、检验步骤1.原材料进货检验:(1)对进货的原材料进行外观检验,包括颜色、形状、尺寸等;(2)进行物理性能检验,如硬度、抗拉强度等;(3)进行化学性能检验,如成分含量、腐蚀性等。
2.加工过程检验:(1)在加工过程中,对每个工序进行质量检验,确保加工精度和工艺流程的合理性;(2)对加工过程中的产生的废品进行分类和记录,及时进行整改和改进。
3.包装过程检验:(1)对包装材料进行外观检验,确保包装材料的质量符合要求;五、检验记录1.检验过程中的各个环节都应进行详细的记录,包括检验结果、检验人员、检验时间等;2.记录需要真实准确,遵循保密原则,不得外泄。
六、异常处理1.当发现产品质量不合格时,应及时停止生产,并进行确认和调查原因;2.对于不良品,应进行分类和记录,以便进行整改和改进;3.合格的产品应分类存放,做好防潮、防尘等工作。
七、检验结果处理1.检验结果正确的产品,可以进行下一步生产工序;2.检验结果不符合要求的产品,应及时进行整改和改进,直到符合要求为止;3.不合格产品的处理应按照内部流程进行,严禁私自流入市场。
八、操作规范所有检验工作人员都必须按照本操作规程进行检验工作,确保操作规范、一致性和稳定性。
九、培训与考核对所有进行检验操作的人员应进行岗前培训,并进行考核,确保其掌握正确的操作方法和技能。
十、操作安全进行检验操作时,必须戴好安全防护用具,遵守安全操作规程,确保人员的安全。
十一、附则1.本操作规程应定期进行检查和更新,确保其适应生产过程的实际情况;2.对于重大问题或不符合规程的情况,应及时上报质量管理部门进行处理。
质量检验规程
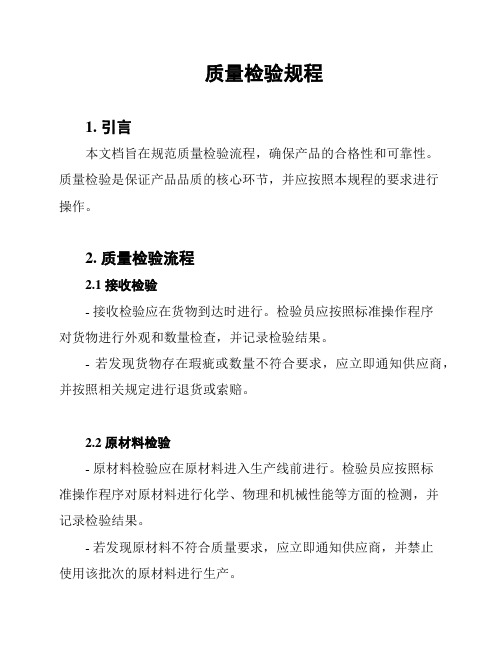
质量检验规程1. 引言本文档旨在规范质量检验流程,确保产品的合格性和可靠性。
质量检验是保证产品品质的核心环节,并应按照本规程的要求进行操作。
2. 质量检验流程2.1 接收检验- 接收检验应在货物到达时进行。
检验员应按照标准操作程序对货物进行外观和数量检查,并记录检验结果。
- 若发现货物存在瑕疵或数量不符合要求,应立即通知供应商,并按照相关规定进行退货或索赔。
2.2 原材料检验- 原材料检验应在原材料进入生产线前进行。
检验员应按照标准操作程序对原材料进行化学、物理和机械性能等方面的检测,并记录检验结果。
- 若发现原材料不符合质量要求,应立即通知供应商,并禁止使用该批次的原材料进行生产。
2.3 在线检验- 在线检验应在生产过程中进行。
检验员应按照标准操作程序对产品的关键环节进行检测,并记录检验结果。
- 若发现生产过程存在问题或产品不符合要求,应立即采取纠正措施,并记录整改情况。
2.4 出厂检验- 出厂检验应在产品制作完成后进行。
检验员应按照标准操作程序对产品进行全面检查,并记录检验结果。
- 若发现产品存在质量问题,应立即进行整改,并禁止出厂销售。
3. 检验记录与报告3.1 检验记录- 每一次的检验应有详细的记录,包括检验日期、检验人员、检验项目、检验方法和检验结果等。
- 检验记录应进行分类归档,并保存一定时间,便于追溯和分析。
3.2 检验报告- 针对每一次的出厂检验,应编制相应的检验报告。
报告应包括产品信息、检验项目、检验结果和评价等。
- 检验报告应及时归档,并将重要报告备份保存。
4. 质量问题处理4.1 非符合品处理- 若发现产品存在质量问题,应按照相关流程进行处理,包括整改、追溯和召回等。
4.2 持续改进- 针对质量问题,应进行深入分析,找出问题的根本原因,并制定相应的改进措施。
- 改进措施应经过验证后实施,并对改进效果进行评估。
5. 结论本质量检验规程为确保产品质量提供了明确的操作流程和要求。
产品质量检验规程及评分标准
产品质量检验规程及评分标准
1. 引言
本文档旨在制定产品质量检验的规程及评分标准,以确保产品
质量符合标准,并提供统一的评分体系。
2. 质量检验规程
2.1 检验范围
- 检验范围应涵盖所有产品的关键要素,包括但不限于外观、
尺寸、性能等。
- 检验范围应根据产品的特性进行调整,以确保检验的全面性
和适用性。
2.2 检验方法
- 检验方法应明确具体的操作步骤和要求。
- 检验方法应采用合适的仪器和设备,以获取准确的检验结果。
- 检验方法应标明检验人员的资质要求,确保检验的专业性和
可靠性。
2.3 检验频率
- 检验频率应根据产品的重要性和风险等级进行确定。
- 高风险和重要产品应进行更频繁的检验,以确保产品质量的
稳定性和一致性。
2.4 检验记录
- 检验记录应清晰、完整、准确地记录检验过程和结果。
- 检验记录应包括检验日期、检验人员、样本数量、检验结果
等关键信息。
3. 评分标准
3.1 评分体系
- 制定产品质量评分体系,根据产品的各项指标进行评分,以
综合评价产品的质量水平。
- 评分体系应具体明确各项指标的权重和得分标准。
3.2 评分标准
- 不同指标的评分标准应根据产品的特性和标准要求进行制定。
- 评分标准应包括合格标准和不合格标准,以便清晰判定产品
质量的优劣。
4. 结论
本文档为产品质量检验制定了规程和评分标准,旨在确保产品质量的稳定性和一致性,提高产品质量管理水平。
产品质量检验规程
产质量量查验规程1进货查验规程目的:规定与产品相关的采买物质(如原资料、包材、外加工品、采买物品等)进货查验的方式和标准,保证产品质量达到预期要求。
范围:适用于对外购的原资料、辅助物料、包材及外加工品、表面办理件等的查验过程.1.3职责:仓管员依照采买计划对供方来料的规格,数量等进行接收,表记,报检。
做到帐、物、卡清楚和一致。
进货质检员 (IQC):依照仓管员的报检信息,比较《外购、外协件检查作业指导书》、《机械加工工序卡片》、图纸和相关附表进行查收作业。
1.4弊端定义:A类为致命弊端 : 预计能引起产品功能丧失的或会造成安全事故的,顾客会索赔的。
如:功能性能,抗拉强度不良,化学成份不达标、错装,漏装等。
B类为严重弊端 : 可能严重影响产品功能或引起产品局部功能无效。
如:特别特点,主要尺寸不良等。
C类略微弊端 : 吻合产品标准,不影响产品的使用功能,但不吻合产品特点内控标准,影响产品外观或整体赏析。
如:外观不良、产品表记不良、包装不良等。
1.5进货查验流程:相关单位操作流程仓管员表记,报检查验、记录、表记查验员仓管员办理手续要点仓管员接到来料后,依照采买计划或技术协议(查收协议)比较来料的数量,规格或图号等核对,作好待检表记。
开出《产品送检通知单》向外检员报检,若有要求供应商供应相关试样的自检报告或合格证明时,则应在报检时一同送到。
查验员依照《机械加工工序卡片》或成品图纸及相关附表对来料进行查验或试验,并作好记录和产品状态表记,通知仓管员办理相关手续。
对于送检通知单信息不完满时查验员有权拒绝查验。
记录填写规定:抽样数多于 5 时,一般记录 5 个数据,少于 5个时全数记录,但若是不合格数量高出 5 个时,如实且有代表性的记录不合格数据。
仓管员按《产质量量查验单》的结果办理相关手续。
未经检验的产品不得投入使用、加工,企业不允许“因急放行” 。
产质量量查验规程1.6进货查验不合格办理流程:相关单位操作流程查验员表记,开单质量部 / 技术要点查验员发现不合格品时,由质量部查验员对产品状态表记好后,开出《不合格评论审单》交质检科长。
产品检验规程
产品检验规程
1. 目的和范围
本规程旨在确保产品的质量和符合标准要求。
适用于公司所有生产的产品。
2. 定义
2.1 产品:指公司生产的所有商品和物资。
2.2 检验:指对产品进行全面详细的测试和评估,以确保符合质量和标准要求。
3. 检验流程
3.1 接收产品:产品从生产线上下来后,由负责人接收,填写接收登记表,并将产品送至检验部门。
3.2 外观检验:检验部门对产品进行外观检查,包括检查外观是否完整、无明显瑕疵等。
3.3 功能检验:检验部门对产品进行功能测试,确保产品能够正常使用,并符合技术要求。
3.4 安全检验:检验部门对产品进行安全性测试,确保产品无安全隐患,并符合相关法规和标准要求。
3.5 记录结果:检验部门根据检验情况记录检验结果,并做出相应处理措施。
4. 检验标准
4.1 外观检验标准:根据产品外观设计和相关标准,判断产品外观是否符合要求。
4.2 功能检验标准:根据产品技术规格书和相关标准,测试产品功能是否正常。
4.3 安全检验标准:根据安全测试要求和相关法规,判断产品是否存在安全隐患。
5. 检验结果
5.1 合格:产品在各项检验中均符合标准要求。
5.2 不合格:产品在任何一个检验项目中未能达到标准要求。
5.3 处理措施:对于不合格产品,检验部门将通知生产部门进行整改,并追踪整改进展。
6. 术语定义
6.1 合格品:指符合产品质量和标准要求的产品。
6.2 不合格品:指未能达到产品质量和标准要求的产品。
7. 修订记录
版本号修订日期修订内容修订人。
机械行业产品质量检验规程
机械行业产品质量检验规程一、前言机械行业作为现代工业的重要组成部分,其产品的质量检验至关重要。
本文将介绍机械行业中常见的产品质量检验规程,旨在确保产品的质量达到规定标准,以提升行业整体竞争力。
二、原材料检验1. 材料标识检查:对原材料提供商提供的标识进行核对,确保材料符合标准要求。
2. 外观检查:对原材料的表面进行详细检查,包括表面平整度、颜色、氧化层等指标。
3. 尺寸检验:对原材料的尺寸进行测量,确保符合设计要求。
4. 化学成分分析:对原材料进行化学成分分析,确保符合相关标准。
5. 物理性能测试:对原材料进行物理性能测试,包括硬度、耐磨性等指标。
三、加工工艺检验1. 切削工艺:对机械零部件的切削工艺进行检验,包括刀具选择、切削速度、加工精度等指标。
2. 焊接工艺:对焊接工艺进行检验,包括焊接材料的选择、焊接接头的强度、焊接形式等指标。
3. 铸造工艺:对铸造工艺进行检验,包括铸造温度、浇注速度、铸件内部结构等指标。
4. 熔融处理:对机械制造中的熔融处理工艺进行检验,包括热处理温度、保温时间、冷却速率等指标。
四、装配质量检验1. 尺寸配合检验:对机械产品的配合尺寸进行检验,确保各零件之间的配合精度。
2. 装配工序检验:对机械产品的装配工序进行检验,确保每个装配工序都符合规定要求。
3. 整机功能测试:对机械产品进行功能测试,包括启动、停止、运行时间等指标。
4. 外观检查:对机械产品的外观进行检查,确保没有明显的缺陷或损坏。
五、试验和性能验证1. 负载试验:对机械产品进行负载试验,测试其在正常工作负荷下的性能表现。
2. 寿命试验:对机械产品进行寿命试验,测试其在一定时间内的使用寿命。
3. 安全性能测试:对机械产品的安全性能进行测试,确保其符合相关安全标准。
4. 环境适应性测试:对机械产品在不同环境条件下的适应性进行测试,包括温度、湿度、振动等指标。
六、成品出厂检验1. 成品外观检查:对机械产品的外观进行检查,确保无明显的缺陷或损坏。
- 1、下载文档前请自行甄别文档内容的完整性,平台不提供额外的编辑、内容补充、找答案等附加服务。
- 2、"仅部分预览"的文档,不可在线预览部分如存在完整性等问题,可反馈申请退款(可完整预览的文档不适用该条件!)。
- 3、如文档侵犯您的权益,请联系客服反馈,我们会尽快为您处理(人工客服工作时间:9:00-18:30)。
《全尺寸检验报告》
编制/日期 审核/日期 批准/日期
修订状态 A B CD E F GH
更改/日期
审核/日期
批准/日期
附表 2:适用配件毛坯的来料检→GB/正常检查一次抽样方案表(AQL=;外观检查水平=Ⅱ,尺寸检查水平=S-3, AQL=。Ac 为接收
数,Ae 为拒收数。
批量(N)
2至8 9 至 15 16 至 25 26 至 50 51 至 90 91 至 150 151 至 280 281 至 500 501 至 1200 1201 至 3200 3201 至 10000 10001 至 35000 35001 至 150000 150001 至 500000 500001 以上
进货质检员(IQC): 根据仓管员的报检信息,对照《外购、外协件检查作业指导书》、《机械加工工序卡片》、
图纸和相关附表进行验收作业。
1.4 缺陷定义:
A 类为致命缺陷: 预计能引起产品功能丧失的或会造成安全事故的,顾客会索赔的。如:功能性能,抗拉强
度不良,化学成份不达标、错装,漏装等。
B 类为严重缺陷: 可能严重影响产品功能或引起产品局部功能失效。如:特殊特性,主要尺寸不良等。
3 成品检验规程
目的: 规定成品检验方法,确保产品符合规定要求,严格把关,最终满足客户要求。
范围: 本规程适用于最终检验和试验。
职责: 质量部负责编制《产品质量检验规范》,《成品检验指导书》,《自制件检查作业指导书》。 检验员按《产品质量检验规范》,《成品检验指导书》,《自制件检查作业指导书》执行产品的最终检验和试验。
案表(AQL=;外观检查水平=Ⅰ,尺寸检查水平 S-3=AQL=
表面热处理工序的测试抽样判定:按附表 1 中“金相及成份”一栏抽样,C=0 接收执行。
抽检的结果记录按执行。
2 产品过程检验规程 目的:
规定过程检验的方法,使检验工作有章可循,确保产品质量能够及时管控或整改,防止批量不良品产生。 范围:
对本厂未有检测手段的性能试验项目,委托外部合格的实验室进行试验,并以其出具的检验试验结果作为 本厂产品符合规定要求的证据。
全尺寸检验和性能试验出现不合格品/批,应加倍抽样,如仍不合格,应立即停止出货,并根据不合格的风险 程序决定是否需要通知顾客或追回已发运的产品。具体执行《不合格品控制程序》。 全尺寸检验和性能试验的结果在顾客要求时,应可供顾客评审。
如果处理结果是要求供应商挑选时,则必须要求供应商在本 公司执行且在规定时间里完成,不允许退回完成。
质量部跟踪处理的结果,并验证其整改的情况。
1.7 验收原则: 进货检验员接仓管员的报检通知,应对待检物料及时进行检验:
1.7.1 正常情况,接报检通知后 1 小时至 1 个工作日内应完成检验。(除相关试验有时间规定以外。) 1.7.2 紧急情况,进货到货后质量部应首先安排急需物料的检验。 1.7.3 异常情况,不超过 3 个工作日应完成验证工作。(除相关试验有时间规定以外。) 1.7.4 特殊情况下,如:晚班无检验员或检验条件不具备等,可由生产部以《紧急放行申请单》提出,经上报批
3201-10000
5
20
5
20
01 12 12 12
壳体几何尺寸及表面质量的检验项目及要求按《机械加工工序卡片》检验。
外协配件原材料检验和试验:
对原材料的性能试验按《外购、外协件检查作业指导书》,且要求原材料供方在每批交货中提供对应的检测报告及
材质证明书,检验员对照产品原材料的标准核查各项实测结果及有效性。对金属配件每年至少两次对原材料
操作规定: 壳体和其他配件的成品检验,检验员按照《自制件检查作业指导书》和图纸,总成按《成品检验指导书》及总 成图纸进行检验和试验,并做《成品检验记录》,出厂前依据《成品检验记录》出成品报告。抽样标准见附表 4。相关性能用《自动调整壁装配检测台》和手动调整臂传感技术全数检测;检验时发现不合格按《不合格品 控制程序》进行处理。
操作流程
要点
检验员
标识,开单
检验员发现不合格品时,由质量部检验员对产品状态标识好 后,开出《不合格品评审单》交质检科长。
质量部/技术 部/生产部
会同评审
质量部
跟踪、验证
由质检科长会同质量部长、技术部、生产部和其他相关部门主 管一起评审,质量部汇总评审意见后,意见统一时,则由采购 员负责人通知供方或公司相关单位按处理结果执行,如各部门 意见不统一时,由总经理作最终处理意见,则按最终处理意见 执行。
记录填写规定:抽样数多于 5 时,一般记录 5 个数据,少于 5 个时全数记录,但如果不合格数量超过 5 个时,如实且有代表 性的记录不合格数据。
仓管员
办理手续
仓管员按《产品质量检验单》的结果办理相关手续。未经检
验的产品不得投入使用、加工,公司不允许“因急放行”。
1.6 进货检验不合格处理流程:
相关单位
b) 金相要求:球化 1-4 级,石墨 5-8 级,珠光体控制在 5%-30%范围内,渗碳体≤1%,磷共晶<%,布 氏硬度 HB160-210。
c) 化学成份:C()%,Si()%,Mn≤%,P≤%。S≤%,Re。
附表 1:材料(或売体毛坯)及硬度的抽样规定及接收准则:(参照编制)
接收准则 AQL
准后先上线试用,试用不合格退回仓库,通知质量部按不良品处理。 1.8 壳体原材料检验项目:
按汉德车轿有限公司的要求,QT450-10 的力学性能和金相组织按 GB/T1348-1988 中的规定,其它按汉德车 轿企业标准 SQB6117-2000 的要求执行。具体要求如下:
a) 机械性能:抗拉强度 σb≥450MPa;屈服强度 σ≥310 MPa;延伸率 δ≥10%(壳体供应商每炉产 品提供 3 根样棒,且样棒要与壳体是同一炉铁水)。
外观 检查水平Ⅱ
抽样样本 2 3 5 8 13 20 32 50 80
125 200 315 500 800 1250
允收水平 AQL=
Ac
Re
0
1
0
1
0
1
0
1
1
2
1
2
2
3
3
4
5
6
7
பைடு நூலகம்
8
10
11
14
15
21
22
21
22
21
22
批量(N)
2至8 9 至 15 16 至 25 26 至 50 51 至 90 91 至 150 151 至 280 281 至 500 501 至 1200 1201 至 3200 3201 至 10000 10001 至 35000 35001 至 150000 150001 至 500000 500001 以上
1 进货检验规程
目的:
规定与产品有关的采购物资(如原材料、包材、外加工品、采购物品等)进货检验的方式和标准,确保产品
质量达到预期要求。
范围:
适用于对外购的原材料、辅助物料、包材及外加工品、表面处理件等的检验过程.
1.3 职责:
仓管员依据采购计划对供方来料的规格,数量等进行接收,标识,报检。做到帐、物、卡清晰和一致。
适用于本公司车间产品的加工过程。 职责:
车间检验员负责按《机械加工工序卡片》检验方法、检验项目进行首件复查确认和巡检,需要时(当巡检发现过程 质量不稳定时)要做完工检。检查操作员的自检记录情况。
车间操作员负责按《机械加工工序卡片》进行产品加工,在每个过程开始或换人、换机、换产品,更换工装、刀 具,调整尺寸等情况下应进行首件自检和送检(报检),确保产品符合要求,并做好自检记录。有责任对本 工序加工的不合格品进行分选。
操作规定 首件检验:为避免批量加工失误,每班开始或更换操作者、更换工艺装备、更换产品等情况加工时,操作员
应对生产的第一件产品进行自检。原则上是自检合格并经检验员确认后方可继续生产,根据公司的实际情 况和存在的客观因素,允许在连续 3 件产品自检合格的前提下同步生产,如测量结果不能判定或自检能力 不足、检测设备不齐全时,必须送检验员确认合格后才能生产。首件检验不合格,则调整工装、加工方法 等,直到生产出合格的首件产品才能批量生产。检验员在首、巡检记录单上记录检验结果。 2.4.2 巡检:检验员按《机械加工工序卡片》规定的检验方法、检验项目、容量和频率执行,并判断是否合格; 如不能明确判断,则应通知质管科长。检验员应将巡检的结果记录在《首、巡检记录单》上,并签名或盖 章。 自检:为确保产品质量,操作者应按规定的检验频次进行自检。自检项目按《机械加工工序卡片》规定的加工项 目,容量和频率执行,并做好自检记录。自检不合格,应对前频次生产的产品进行 100%检验。 总成装配过程以操作工自检为主、检验员抽查验证不作记录。在总成最终检测时,计算一次交检合格率。 车间检验员在首、巡检过程中未发现不合格品时,则在物料流程卡上签字或盖章,操作员自己办理相关入库手续; 若巡检过程中发现不合格品时,对不合格零件立即作好标识,开出检验单,通知操作员把本批产品送往检验 室进行隔离,复查,必要时由责任人全检。 车间操作员在自检时发现的不合格品要及时对不合格品进行标识,隔离,报当班检验员进行处理。检验员应同时 对前频次做的产品进行抽检。 工序完工检,壳体及配件 A、B 类特性按附表《零缺陷抽样判定标准》中的接收质量限 AQL=,C=0 执行;C 类特性 按附表 3 执行。抽检时发现不合格按《不合格品控制程序》进行处理。 报废品须由责任人确认签字;当批量不合格或报废品达到 20 只以上或质量问严重和质量问题重复发生时,需填写 《不合格评审单处置单》逐级递交处理。