《压铸模及其他模具》第三章_压铸模设计
压铸模具设计范文

压铸模具设计范文压铸模具设计是指为了生产压铸件而设计的模具,其主要任务是将液态金属注入模具中,并在模具中冷却、凝固,最终得到所需形状的金属零件。
压铸模具设计的主要工作包括设计模具的结构、选材、计算模具的合理尺寸和形状等。
一、压铸模具结构设计1.模具整体结构设计:根据压铸件的形状和尺寸,确定模具的整体结构。
一般情况下,压铸模具采用上下模结构,上模为固定模,下模为活动模。
针对复杂形状的压铸件,可能需要设计多个滑模和拉杆。
2.模腔设计:根据压铸件的形状和尺寸,确定模腔的几何形状和尺寸。
模腔的设计应保证在模具关闭时,模腔中的液态金属能够充满整个腔体,并且在冷却凝固过程中,金属能够均匀收缩,避免产生缩孔和其他缺陷。
3.浇口和导流系统设计:浇口和导流系统的设计对于压铸件的质量和生产效率有着重要的影响。
浇口的设计应尽量避免金属的湍流流动,避免气泡的产生。
导流系统的设计应考虑金属的顺序填充和排气,以及冷却和凝固过程中的温度控制。
二、压铸模具选材压铸模具的选材应根据金属的性能和压铸工艺的要求来确定。
通常情况下,模具会选用高强度和耐磨损的合金钢作为材料,以保证模具的使用寿命和精度。
同时,还需要考虑模具的热传导性能,以确保压铸件能够快速冷却、凝固。
三、压铸模具尺寸和形状计算1.模具尺寸计算:模具尺寸的计算包括模腔尺寸、模板尺寸、滑模尺寸、导流系统尺寸等。
模具尺寸的计算需要考虑压铸件的最终尺寸、缩孔和收缩率等因素。
2.模具形状计算:模具的形状计算主要是指模腔内部的曲面和棱角的设计。
对于复杂形状的压铸件,需要使用CAD软件进行三维建模和形状优化,以确保模具的制造精度和压铸件的质量。
压铸模具设计需要充分考虑压铸件的形状和尺寸、材料的性能、压铸工艺要求等因素,通过合理的结构设计、选材和计算,能够提升压铸件的质量和生产效率。
在设计过程中,还需要考虑模具的制造难度和制造成本,以确保模具的可行性和经济性。
《压铸模及其他模具》第三章_压铸模设计

4.导向零件的设计
(1)导柱和导套的设计要点 导柱应有足够刚度,在开合模时运动灵活,没有卡死现象。 (2)导柱、导套的尺寸和结构形式 在压铸模中,一般均设四根导柱。导向部分的直径可按下式经验公 式计算:
dK A
导柱和导套已经标准化,有A型和B型两种。
第三节 浇注系统和溢排系统的设 计
一.浇注系统的组成
压铸模与其他模具
第三章 压铸模设计
目 录
第一节 第二节 第三节 第四节 第五节 第六节 第七节 第八节 第九节
压铸模的基本组成 压铸模零部件的设计 浇注系统和排溢系统的设计 侧向分型抽芯机构的设计 推出机构的设计 冷却和加热系统的设计 压铸模的设计步骤和实例 压铸模的失效分析 压铸模的缺陷分析与排除措施
(1)按动力源分类 手动推出机构、机动推出机构、液压推出机构 (2)按推出元件的类别分类 推杆推出机构、推管与推叉推出机构、推件板 推出机构、斜滑块推出机构和组合推出机构。 (3)按模具结构特征分类 常用推出机构、二级推出机构和定模推出机构。
二.常用推出机构
1.推杆推出机构
(1)推杆的基本形式和固定方式
当按上式计算还会妨碍压铸件的脱模时,需根据压铸件和模具结构 来确定。如图所示圆形骨架压铸件,图a、b分别采用二等分和多等分合 模机构,抽芯距计算方法分别为:
三.常用抽芯机构的设计
1.斜销抽芯机构
斜销抽芯机构结构简单,制造方便,可利用开模、合模动力实现抽 芯和复位,在中小型压铸模中应用广泛。
(1)斜销直径和长度计算 斜销上所承受最大弯矩: 斜销直径受其抗弯强度的限制: 抗弯截面系数: 得斜销直径:
第三章压铸模设计第一节压铸模的基本组成第二节压铸模零部件的设计第三节浇注系统和排溢系统的设计第四节侧向分型抽芯机构的设计第五节推出机构的设计第六节冷却和加热系统的设计第七节压铸模的设计步骤和实例第八节压铸模的失效分析第九节压铸模的缺陷分析与排除措施随着车辆和电动机等产品向轻量化发展压铸模的比例不断增加同时对压铸模的寿命和复杂程度的要求也将提高
压铸模具设计方案
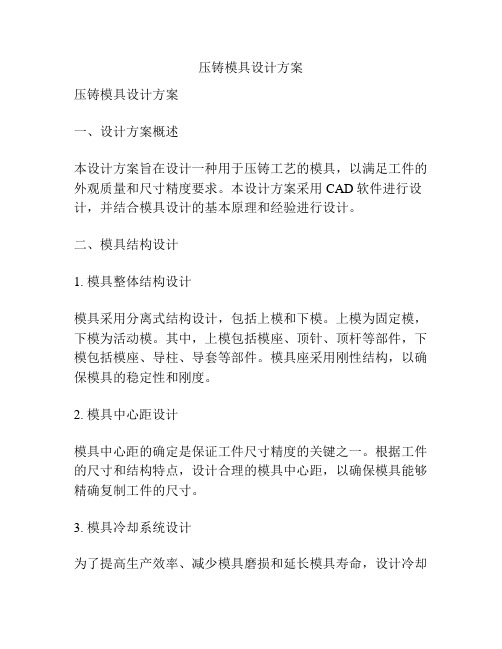
压铸模具设计方案压铸模具设计方案一、设计方案概述本设计方案旨在设计一种用于压铸工艺的模具,以满足工件的外观质量和尺寸精度要求。
本设计方案采用CAD软件进行设计,并结合模具设计的基本原理和经验进行设计。
二、模具结构设计1. 模具整体结构设计模具采用分离式结构设计,包括上模和下模。
上模为固定模,下模为活动模。
其中,上模包括模座、顶针、顶杆等部件,下模包括模座、导柱、导套等部件。
模具座采用刚性结构,以确保模具的稳定性和刚度。
2. 模具中心距设计模具中心距的确定是保证工件尺寸精度的关键之一。
根据工件的尺寸和结构特点,设计合理的模具中心距,以确保模具能够精确复制工件的尺寸。
3. 模具冷却系统设计为了提高生产效率、减少模具磨损和延长模具寿命,设计冷却系统对模具进行冷却。
冷却系统包括冷却孔和进水口,通过冷却水的流动,迅速冷却模具,以提高生产效率和模具寿命。
4. 模具材料选择模具的材料选择是保证模具寿命和使用效果的重要因素。
根据工件的材料和要求,选择适当的模具材料,保证模具具有良好的硬度和耐磨性。
三、模具生产工艺1. 加工工艺规程模具的加工工艺包括数控加工、外圆磨削等。
根据模具的具体结构和工艺要求,制定合理的加工工艺规程,以确保模具的加工质量。
2. 检测工艺模具加工完成后,进行检测以验证模具的质量。
检测工艺包括模具尺寸检测、表面质量检测等,通过合适的检测工艺,确保模具符合设计要求。
四、模具的维护、维修和更换为了保证模具的正常使用和延长其寿命,进行模具的定期维护、维修和更换。
维护工作包括清洁模具、添加润滑剂等,维修工作包括修复模具损伤、更换模具部件等,更换工作包括根据模具磨损程度,定期更换模具部件。
五、结论本设计方案是一种用于压铸工艺的模具设计方案,通过合理的结构设计、材料选择和加工工艺,可以满足工件的外观质量和尺寸精度要求。
同时,通过模具的定期维护、维修和更换,可以保证模具的正常使用和延长其寿命。
压铸模具设计基础知识

压铸模具设计基础知识一、概述压铸模具是用于压铸工艺的模具,在金属、塑料等材料的制品生产过程中起到关键作用。
压铸模具的设计质量直接影响产品的质量和生产效率。
本文将介绍压铸模具设计的基础知识,包括设计原则、材料选择、结构设计等内容。
二、设计原则1.功能性原则压铸模具应该符合产品的设计要求,能够满足产品的结构、尺寸、表面质量等要求。
设计过程中需要充分考虑产品的功能性需求,确保模具能够满足生产要求。
2.可制造性原则在设计压铸模具时,需要考虑到模具的加工工艺和生产成本。
设计应尽量简化,避免复杂的结构和加工工艺,以降低生产成本。
3.可靠性原则压铸模具在长期使用中需要具有稳定可靠的性能。
设计中需要考虑模具的寿命、耐磨性等因素,确保模具能够长时间稳定运行。
4.易维护性原则模具在使用过程中可能会有损坏或磨损,设计时需要考虑模具的易维护性,便于维修和更换受损部件。
三、材料选择压铸模具的材料选择直接影响模具的寿命和性能。
常用的模具材料包括工具钢、合金钢、硬质合金等。
在选择材料时需要考虑以下因素:1.硬度模具材料应具有足够的硬度和强度,能够抵抗压力和磨损,确保模具的稳定性和寿命。
2.热稳定性压铸过程中温度较高,模具材料需要具有良好的热稳定性,不易变形或烧损。
3.耐磨性压铸模具在长期使用中会有磨损,需要选择耐磨性好的材料,延长模具的使用寿命。
4.耐蚀性部分压铸过程中会有化学物质接触,模具材料需要具有良好的耐腐蚀性,避免腐蚀损坏。
四、结构设计压铸模具的结构设计直接影响产品质量和生产效率。
在设计时需要考虑以下因素:1.分型设计合理的分型设计能够提高产品的成型效率和质量,减少缺陷产生。
分型设计应考虑产品的结构特点和成型过程中的收缩变形。
2.冷却系统设计冷却系统设计影响压铸过程中的温度控制和冷却速度,直接影响产品的组织和性能。
设计时应考虑冷却系统的布局和冷却介质的选择。
3.排气系统设计在压铸过程中需要排除模具内的气体,避免气泡和气孔产生。
常见的压铸模具结构及设计

常见的压铸模具结构及设计压铸模具是利用压力将熔融金属注入模具腔中,通过冷却固化后得到所需形状的金属制品。
它由模具座、模具芯、模具板等组成,其结构设计直接影响到压铸产品的质量和生产效率,因此压铸模具的结构设计是相当关键的。
1.单向模具结构:即模具腔和模具芯的投入方向相同,熔融金属由一边流入模具腔,另一边流出。
这种结构适用于形状简单的压铸产品,生产效率较高。
但由于金属在流动过程中存在进气孔和气泡的产生,容易影响产品质量。
2.双向模具结构:即模具腔和模具芯的投入方向相反,熔融金属同时从两个方向流入模具腔,避免了进气孔和气泡的产生,使产品质量更加稳定。
但此种结构制造难度较大,因此适用于形状复杂的产品。
3.多向模具结构:即模具腔和模具芯的投入方向可以有多个选择,根据具体产品的形状和要求来设计。
这种结构适用于有多个几何孔形和复杂造型的产品。
4.滑动式模具结构:适用于有突出部分或凹陷部分的产品,模具芯和模具腔可以相对滑动,来实现产品形状的复杂性。
滑动式模具结构使得产品成型更加容易,同时也增加了模具制造的难度。
5.注射式模具结构:适用于较大规模的压铸产品生产,通过在模具腔中注入压力来驱动熔融金属充满整个模具腔,从而制造大型、复杂的产品。
在压铸模具的设计中,需要考虑以下几个方面:1.模具材料的选择:通常采用高速钢、合金钢或特殊合金作为模具材料,以保证模具的耐磨性和耐蚀性。
2.模具结构的合理性:要满足产品的形状和要求,保证产品质量和生产效率。
通过模具芯、模具腔和模具座的设计,确定模具的结构。
3.模具冷却系统的设计:合理的冷却系统设计可以缩短模具的冷却时间,提高生产效率。
同时可以有效控制模具温度,避免模具受热膨胀。
4.维修和更换模具的方便性:设计模具时要考虑到日常维修和更换部件的便利性,提高模具的使用寿命。
总结起来,压铸模具的结构设计需要根据产品形状和要求来确定,考虑到产品质量和生产效率。
同时还要合理选择模具材料,设计冷却系统,并考虑维修和更换模具的方便性。
《压铸模及其他模具》压铸模设计共80页文档

15、机会是不守纪律的。——雨果
1、最灵繁的人也看不见自己的背脊。——非洲 2、最困难的事情就是认识自己。——希腊 3、有勇气承担命运这才是英雄好汉。——黑塞 4、与肝胆人共事,无字句处读书。——周恩来 5、阅读使人充实,会谈使人敏捷,写作使
11、战争满足了,或曾经满足过人的 好斗的 本能, 但它同 时还满 足了人 对掠夺 ,破坏 以及残 酷的纪 律和专 制力的 欲望。 ——查·埃利奥 特 12、不应把纪律仅仅看成教育的手段 。纪律 是教育 过程的 结果, 首先是 学生集 体表现 在一切 生活领 域—— 生产、 日常生 活、学 校、文 化等领 域中努 力的结 果。— —马卡 连柯(名 言网)
压铸模具设计毕业设计说明书
目录第一章压铸合金与压铸件的设计 (3)1.1 压铸合金 (3)1.1.1 工件的材料性能 (3)1.1.2工件注意事项 (3)1.2 压铸件的设计 (4)1.2.1 铸孔的设计 (4)1.2.2 脱模斜度的设计 (5)1.2.3 齿轮的设计 (5)第二章压铸机的选用与压铸工艺 (6)2.1 压铸机的分类和特点 (6)2.1.1 压铸机的分类 (6)2.1.2 压铸机的特点 (6)2.2 压铸机的型号及主要参数 (6)2.3 压铸机的选用 (7)2.3.1 压铸机的基本参数选择 (7)2.3.2 计算压铸机的锁模力 (7)2.3.3 压室容量的校核 (9)2.4 压铸工艺 (10)2.4.1 压射压力的选择 (10)2.4.2 充填速度的选择 (11)2.4.3 压铸时间的选择 (11)第三章分型面、浇注系统和排溢系统设计 (13)3.1 压铸模的结构组成 (13)3.2 分型面的设计 (14)3.2.1 分型面的类型 (14)3.2.2 分型面的选择原则 (14)3.2.3 浇注系统设计 (15)3.2.4 溢流与排气系统的设计 (16)第四章成型零件与模架设计 (18)4.1成型零件的结构设计 (18)4.2 成型零件的成型尺寸的计算 (18)4.3 模架的设计 (20)4.4 加热与冷却系统设计(该模具不采用加热冷却系统,略) (20)第五章抽芯结构设计 (21)参考文献 (22)附录(翻译) (23)摘要随着我国与国际接轨脚步的不断加快,市场竞争的日益加剧,,人们开始越来越认识到产品食量、成本和新产品的开发能力的重要性。
而模具制造是整个链条中最基础的要素之一,模具制造技术现已成为衡量一个国家制造业水平高低的重要标志。
压力铸造简称金属压铸。
它是通过将熔融的液态金属注入压铸机的压室,运用压射冲头的运动,是液态金属在高压力的作用的,高速通过模具的浇注系统填充型腔,在压力下结晶并迅速冷却凝固形成铸件的一种高效率的少、无切削金属的成型工艺。
压铸工艺及压铸模具设计要点
压铸工艺及压铸模具设计要点摘要:压铸机、模具与合金三者,以压铸件为本,压铸工艺贯穿其中,有机地将它们整合为一个有效的系统,使压铸机与模具得到良好的匹配,起到优化压铸件结构,优选压铸机、优化压铸模设计、提高工艺工作点的灵活性的作用,从而为压铸生产提供可靠保证。
所以,压铸工艺寓于模具中之说,内涵之深不言而喻。
关键词:压铸机;模具;压铸工艺;模具设计The Main Points of Die Casting Process andDie Casting Die DesignPAN Xian-Zeng, LIU Xing-fuAbstract: The die casting machine, die and alloy, the three on the basis of die castings, running through with the die casting process forms organically a whole and an effective system. Making the machines well to mate with dies, optimization of die casting construction, optimization of selecting die casting machine, optimization of die design and improving the flexibility of die casting process conveys in the die, this has a profound intension.Key words: die casting machine; die; die casting process; die design1 压铸机—模具—合金系统压铸机、模具和合金这三个因素,在压铸件生产过程中,它们构成了一个系统,即压铸机-模具—合金系统,它是以压铸件为本,工艺贯穿其中,赋予系统活力与效率,而模具则是工艺进入系统的平台。
第三章 压铸模设计
4.导向零件的设计
(1)导柱和导套的设计要点 导柱应有足够刚度,在开合模时运动灵活,没有卡死现象。
(2)导柱、导套的尺寸和结构形式 在压铸模中,一般均设四根导柱。导向部分的直径可按下式经验公
式计算:
dK A
导柱和导套已经标准化,有A型和B型两种。
第三节 浇注系统和溢排系统的设 计
一.浇注系统的组成
(1)镶块的主要尺寸 1)镶块壁厚尺寸见教材表3-1; 2)整体镶块的台阶尺寸见表3-2; 3)组合形式成型镶块固定部分长度见表3-3。
(2)圆型芯的主要尺寸 见表3-4。
(3)影响铸件尺寸精度的因素 1)成型零件的制造误差; 2)压铸件的收缩率;
L模 L铸 100%
L模 3)成型零件的磨损; 4)模具结构及压铸工艺的影响。
(4)成型零件工作尺寸的计算
1)型腔尺寸计算
DM
2
D
2
D
2
% c
2
标注制造公差后得:DM D D% 0.70
同理型腔深度尺寸:HM H H% 0.70
2)型芯尺寸计算
dM
2
d
2
d
2
%
c
2
标注制造公差后得: dM d d% 0.70 同理型芯深度尺寸: hM h h% 0.70
F pb A
(2)动模支承板厚度推荐尺寸 见表3-7。
(3)动模支承板的加强结构
3.动、定模座板的设计
(1)定模座板的设计 定模座板与定模套板构成压铸模定模部分基体,安装在压铸机的固
定模板上。
(2)动模座板的设计
动模座板与垫块构成压铸模动模部分基体,安装在压铸机的活动模 板上,因此动模座板上也必须留出安装压板或紧固螺钉的位置。
压铸工艺及压铸模具设计
压铸工艺及压铸模具设计1.压铸工艺简介压铸是一种将熔化金属注入模具腔内,然后通过压力固化成型的工艺。
它具有高效、高精度、高复杂度的特点,被广泛应用于制造各种金属零件,如汽车零件、电子零件等。
压铸工艺主要分为准备工作、铸造操作和后处理三个阶段。
准备工作包括选材、设计和制造模具等;铸造操作包括将金属加热至熔点、注入模具等;后处理包括去除模具、修整铸件等。
压铸模具是实现压铸工艺的重要工具,它直接影响着产品质量和生产效率。
模具设计需要考虑以下几个方面。
首先是材料选择。
模具的材料需要具备高强度、高耐磨性、高热稳定性等特点,以保证模具长期使用。
其次是结构设计。
模具结构应该简单、合理,易于加工和维修。
同时,对于复杂的产品,需要设计合适的分型面和可抽出芯等特殊结构。
再次是流道系统设计。
流道系统是将熔化金属导入模腔的通道。
优化的流道系统能够保证铸件充型充满、减小气泡和炸破等缺陷的产生。
最后是冷却系统设计。
良好的冷却系统能够快速、均匀地将铸件冷却,提高生产效率和产品质量。
常见的冷却系统包括水冷却、气冷却等。
3.常见问题及解决方法在压铸工艺和模具设计过程中,常会面临一些问题和挑战。
以下是一些常见问题及其解决方法。
首先是翘曲和变形问题。
由于金属在冷却过程中会有收缩和变形,容易导致铸件产生翘曲和变形。
解决方法可以是增加冷却系统,控制金属温度等。
其次是气孔和缺陷问题。
气孔和缺陷是常见的铸件质量问题,可能是由于金属中的气体未能完全排出或模具内部有不完全填充的区域导致。
解决方法可以是优化流道和冷却系统,增加压力等。
最后是模具使用寿命问题。
模具在使用过程中会受到磨损、冲击和热应力等的影响,容易损坏。
解决方法可以是选用高耐磨材料、增加模具表面硬度等。
4.发展趋势随着科技的发展和需求的变化,压铸工艺和模具设计也在不断发展和改进。
未来的发展趋势主要包括以下几个方面。
首先是数字化和智能化。
通过数字化技术和智能化设备,可以实现对压铸工艺和模具设计的更精确和高效的控制。
- 1、下载文档前请自行甄别文档内容的完整性,平台不提供额外的编辑、内容补充、找答案等附加服务。
- 2、"仅部分预览"的文档,不可在线预览部分如存在完整性等问题,可反馈申请退款(可完整预览的文档不适用该条件!)。
- 3、如文档侵犯您的权益,请联系客服反馈,我们会尽快为您处理(人工客服工作时间:9:00-18:30)。
二.成型零件的设计
设计压铸模时,需要合理设计成型零件的结构形式,准确计算尺寸 公差,保证足够的强度、刚度和良好的表面质量。
1.成型零件的结构设计
(1)成型零件的结构形式
(2)镶块的固定形式
其安装形式分为通孔和不通孔两种形式。
(3)型芯的固定形式
型芯通常采用台阶固定、铆接和螺钉连接等方式。
2.成型零件的尺寸计算
F pb A
(2)动模支承板厚度推荐尺寸 见表3-7。
(3)动模支承板的加强结构
3.动、定模座板的设计
(1)定模座板的设计 定模座板与定模套板构成压铸模定模部分基体,安装在压铸机的固
定模板上。
(2)动模座板的设计
动模座板与垫块构成压铸模动模部分基体,安装在压铸机的活动模 板上,因此动模座板上也必须留出安装压板或紧固螺钉的位置。
0
3)中心距尺寸计算
LM
L
L %
2
4)螺纹型环和螺纹型芯尺寸计算
①型环尺寸
DM
D D%
3
4
4 0
D2M
D2
D2%
3 4
2
0
2 4
D1M
D1
X min 1 %
3 4
2
0
2 4
②型芯尺寸
dM
d
d%
3 4
2
0
2
4
d2M
d
2
d2%
3 4
2
0
2
4
d1M
d1
d1
(1)根据压铸件结构和质量选择压室、喷嘴和浇口套的尺寸; (2)分流锥脱模斜度4~6°,长度 L=50~70mm,端面至分流锥顶端距 离l=10~22mm,d=12~24, R=4~5mm,h=2.5~3.5mm。 (3)通常在浇口套及分流锥的内部 设置冷却系统。
第二节 压铸模零部件的设计
一.分型面的选择
1.分型面的类型
2.分型面的选择原则
(1)尽可能使压铸机开模后留在动模; (2)分型面应尽量设计在压铸件端面轮廓最大的地方; (3)分型面应尽量设在金属流动方向的末端; (4)分型面的选择应有利于保证压铸件的质量; (5)尽可能选择平直分型面; (6)分型面的选择应保证侧向活动型芯能顺利抽出。
(1)镶块的主要尺寸 1)镶块壁厚尺寸见教材表3-1; 2)整体镶块的台阶尺寸见表3-2; 3)组合形式成型镶块固定部分长度见表3-3。
(2)圆型芯的主要尺寸 见表3-4。
(3)影响铸件尺寸精度的因素 1)成型零件的制造误差; 2)压铸件的收缩率; L模 L铸 100% L模 3)成型零件的磨损; 4)模具结构及压铸工艺的影响。
第一节 压铸模的基本组成
一.成型零件
决定压铸件几何形状和尺寸精度的零件。成形压铸机外表面称为型 腔,内表面称为型芯。
二.结构零件
包括支承固定零件和导向合模零件。支承固定零件使模具能够安装 到压铸机上;导向合模零件保证合模是正确定位和导向。
三.浇注系统
是引导熔融合金从压铸机的压室流到模具型腔的通道。它由直浇道、 横浇道、内浇口和分流锥等组成。
压铸模与其他模具
第三章 压铸模设计
目录
第一节 压铸模的基本组成 第二节 压铸模零部件的设计 第三节 浇注系统和排溢系统的设计 第四节 侧向分型抽芯机构的设计 第五节 推出机构的设计 第六节 冷却和加热系统的设计 第七节 压铸模的设计步骤和实例 第八节 压铸模的失效分析 第九节 压铸模的缺陷分析与排除措施
概述
随着车辆和电动机等产品向轻量化发展,压铸模的比例不断增加, 同时,对压铸模的寿命和复杂程度的要求也将提高。
压铸模结构图
1- 限位块 2,16,23,28-螺钉 3-弹簧 4-螺栓 5-螺母 6-斜销 7-滑块 8-楔紧块 9-定模套板 10-销钉 11- 侧型芯 12,15-动模镶块 13-定模镶块 l4-型芯 17-定模座板 18-浇口套 19- 导柱 20-动模套板 21-导套 22-浇道镶块 24,26,29-推杆 25-支承板 27-限位钉. 30- 复位 杆 31- 推板导套 32-推板导柱 33-推板 34-推杆固定板 35-垫块 36-动模座板
(4)成型零件工作尺寸的计算
1)型腔尺寸计算
DM
2
D
2
D
% 2
c 2
标注制造公差后得:DM
D
D
%
0.7
0
同理型腔深度尺寸:H M
H
H
%
0.7
0
2)型芯尺寸计算
dM
2
d
2
d
2
%
c 2
标注制造公差后得: dM
d
d
%
0.7
0
同理型芯深度尺寸:
hM
h
h
%
0.7
%
3 4
1
0
1
4
三.结构零件的设计
1.动、定模板边框厚度设计
(1)圆形套板边框厚度
b
Dpb H1
2 H
b
Dpb
2
(2)矩形套板边框厚度
b F2
F22 8H F1L1 4 H
(3)动、定模套板边框厚度推荐尺寸 见表3-6。
2.动模支承板厚度尺寸
(1)动模支承板的厚度计算
FL
h 2B W
浇注系统主要由直浇道、横浇道、内浇口和余料等组成。
二.直流道设计
1.立式冷压室压铸机用直浇道
(1)喷嘴导入口直径d1一般为8~22mm; (2)浇口套与喷嘴连接处的直径比喷嘴出口处的直径每边大0.5~1.0mm; (3)喷嘴部分脱模斜度1°30′,浇口套的脱模斜度取1°30′~3°; (4)分流锥出环形通道的截面积一般为喷嘴导入口截面积的1.2倍,直浇
4.导向零件的设计
(1)导柱和导套的设计要点 导柱应有足够刚度,在开合模时运动灵活,没有卡死现象。
(2)导柱、导套的尺寸和结构形式 在压铸模中,一般均设四根导柱。导向部分的直径可按下式经验公
式计算:
dK A
导柱和导套已经标准化,有A型和B型两种。
第三节 浇注系统和溢排系统的设 计
一.浇注系统的组成
四.排溢系统
一般包括排气槽和溢流槽,根据熔融合金的充填情况开设。
五.侧向抽芯机构
压铸机侧面有凸台或孔穴时,需要用侧向型芯来成型。
六.推出与复位机构
推出机构是指将压铸件从模具的成型零件上脱出的机构;复位机构 是指合模时将推出机构回复到原始位置的机构。
七.加热与冷却系统
达到压铸模的热平衡。
八.其它
如紧固件、定位件等。
道底部分流锥的直径d3,一般可按下式计算:
(5)直浇道与横浇道连接处圆角半径R=6~20mm。
2.卧式冷压室压铸机用直浇道
(1)根据压室比压选定压室直径D; (2)直浇道厚度H一般取压室直径的 1/2~1/3,直浇道脱模斜度1°30′~2°; (3)压室内径和浇口套内径应保持同轴度。
3.热压室压铸机用直浇道