镁合金压铸件成品设计
典型镁合金的模具设计
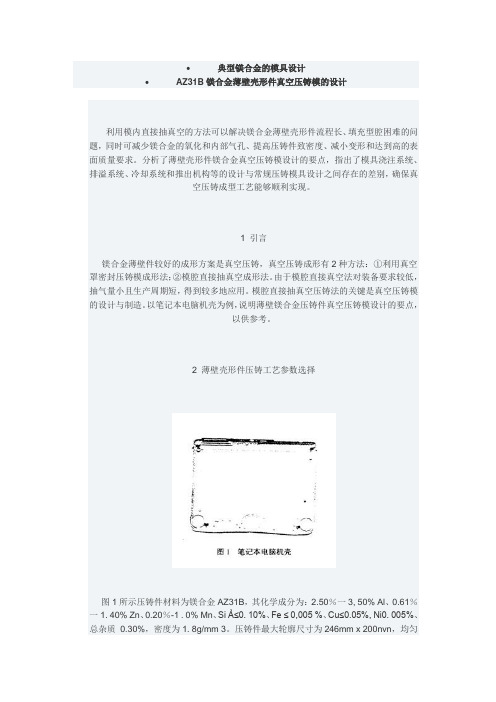
∙典型镁合金的模具设计∙AZ31B镁合金薄壁壳形件真空压铸模的设计利用模内直接抽真空的方法可以解决镁合金薄壁壳形件流程长、填充型腔困难的问题,同时可减少镁合金的氧化和内部气孔、提高压铸件致密度、减小变形和达到高的表面质量要求。
分析了薄壁壳形件镁合金真空压铸模设计的要点,指出了模具浇注系统、排溢系统、冷却系统和推出机构等的设计与常规压铸模具设计之间存在的差别,确保真空压铸成型工艺能够顺利实现。
1 引言镁合金薄壁件较好的成形方案是真空压铸,真空压铸成形有2种方法:①利用真空罩密封压铸模成形法;②模腔直接抽真空成形法。
由于模腔直接真空法对装备要求较低,抽气量小且生产周期短,得到较多地应用。
模腔直接抽真空压铸法的关键是真空压铸模的设计与制造。
以笔记本电脑机壳为例,说明薄壁镁合金压铸件真空压铸模设计的要点,以供参考。
2 薄壁壳形件压铸工艺参数选择图1所示压铸件材料为镁合金AZ31B,其化学成分为:2.50%一3, 50% Al、0.61%一1. 40% Zn、0.20%-1 . 0% Mn、Si À≤0. 10%、Fe ≤ 0,005 %、Cu≤0.05%, Ni0. 005%、总杂质0.30%,密度为1. 8g/mm 3。
压铸件最大轮廓尺寸为246mm x 200nvn,均匀壁厚为1. 26mm,最小壁厚为0. 8mm,筋厚为0. 6mm,压铸件总质量约为75.38。
依据压铸件的结构特点和要求,为增强镁合金液的充填能力、减少氧化、提高压铸件质量,采用模腔直接抽真空压铸法成形。
基本工艺过程为:镁合金液注人压室,压射冲头密封注料口后开始抽真空,达到一定真空度后,关闭总排气槽,此时压射冲头转为快速压射,经保压、冷却、开模取件,完成一次真空压铸成形过程。
成形工艺参数初选为:压射比压400MPa、压射速度0. 8m/s、合金的充填速度约35一40m/ s、充填时间取0.03S ,合金浇注温度660 一70090,模具温度取27090,涂料为聚乙烯煤油,精确工艺参数依据试模情况确定。
镁合金压铸件设计指南

± 0.35 ± 0.08
重要尺寸时的许容差
尺寸A的长度
锌合金 铝合金 镁合金 铜合金
25mm以下基准公差 ± 0.08 ± 0.1
± 0.1
A的长度 超过 25mm
25~300m
m每25mm ± 0.025
增加公差
300mm以
上每25mm ± 0.25
增加公差
± 0.04 ±0.025
± 0.04 ± 0.025
不好的案例 好的案例
二. 设计注意事项
不好的案例
好的案例
Rib
3.在选择壁厚时,应考虑压铸的铸造 简便性,且有一定的刚度和强度,为了 防止部分变形,增强强度,利于熔汤流 动可增加骨架.
4.为了节省原料,在有孔和凹进去 的部位将无用的场合减肉.需同时 考虑模具增加的费用,但最终要降 低总体的费用.
不好的案例
A
不重要尺寸时的许容差
尺寸A的长度
锌合金 铝合金 镁合金 铜合金
25mm以下基准公差 ±0.25
A的长 度超过 25mm
25~300m
m每25mm ± 0.04
增加公差
300mm以
上每25mm ± 0.025
增加公差
± 0.25 ± 0.05 ± 0.025
± 0.25 ±
± 0.05
± 0.025
三. 常见设计不良与改善建议
部位
常见不良与原因
建议
通孔
不要连续集中的通孔,制品散 热应考虑流动性及模具强度. 参考附图(二)。
1.以公模铺肉方式,再以机加 铣平。
2.后工程冲压成形。
滑块成 形 滑块易进毛边,且影响设置 Gate与Overflow的空间。
镁合金压铸件模具设计要点

浇、流道系统设计(6/10)
浇口设计
浇口面积计算公式
Ag V Vg t
V:压铸件体积(含溢流井体积)(cm3)
Vg:浇口速度 (m/s)
t:充填时间 (s)
Ag:浇口面积(mm2)
举例说明:铸件(含溢流井)重400g,平均壁厚1.4mm, V=400/1.8=222.22 cm3 (镁铸件比重为1.8) 假设Vg=55m/s, t=0.03 则Ag=222.22/(55*0.03)=134.68 mm2 , 另浇口厚度不得超出铸件厚度的一半,因而在此定为
精级拔模角 D 0.8( L / C) , (D/ L) / 0.01746度
一般级拔模角所需C值
精级拔模角所需C值
内表面(单边)=7
内表面(单边)=7.8
外表面(单边)=14
外表面(单边)=15.6
孔(全部)=4.76
孔(全部)=5.3
压铸方案设计程序 (1/2)
选择压铸机 决定压铸条件
4
4
5
6
6
镁压铸品模销孔径大于25mm时,直径与深度比 为1:6
镁压铸品模销孔直径 (mm)
3
4
5
7
10 13 16 20 25
镁压铸品模销孔标准深度
单位:倍
1
1 1.5 2
2
2
2.5 2.5
3
镁压铸品尺寸公差 (6/9)
平面之角度公差(ADCI-E11-65)
平面和基准面在同一模穴或同一侧滑模之一部份 面长75mm以下…………………………..0.13mm 超过75mm每25mm追加公差……………0.025mm
AZ61镁合金挤压模具毕业设计
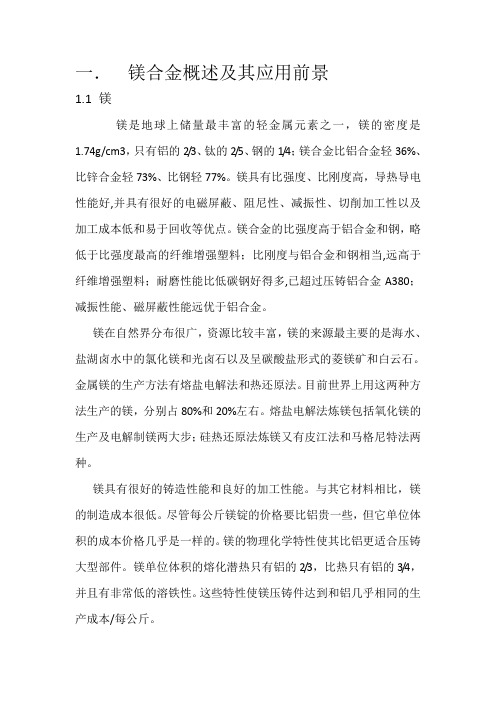
一.镁合金概述及其应用前景1.1 镁镁是地球上储量最丰富的轻金属元素之一,镁的密度是1.74g/cm3,只有铝的2/3、钛的2/5、钢的1/4;镁合金比铝合金轻36%、比锌合金轻73%、比钢轻77%。
镁具有比强度、比刚度高,导热导电性能好,并具有很好的电磁屏蔽、阻尼性、减振性、切削加工性以及加工成本低和易于回收等优点。
镁合金的比强度高于铝合金和钢,略低于比强度最高的纤维增强塑料;比刚度与铝合金和钢相当,远高于纤维增强塑料;耐磨性能比低碳钢好得多,已超过压铸铝合金A380;减振性能、磁屏蔽性能远优于铝合金。
镁在自然界分布很广,资源比较丰富,镁的来源最主要的是海水、盐湖卤水中的氯化镁和光卤石以及呈碳酸盐形式的菱镁矿和白云石。
金属镁的生产方法有熔盐电解法和热还原法。
目前世界上用这两种方法生产的镁,分别占80%和20%左右。
熔盐电解法炼镁包括氧化镁的生产及电解制镁两大步;硅热还原法炼镁又有皮江法和马格尼特法两种。
镁具有很好的铸造性能和良好的加工性能。
与其它材料相比,镁的制造成本很低。
尽管每公斤镁锭的价格要比铝贵一些,但它单位体积的成本价格几乎是一样的。
镁的物理化学特性使其比铝更适合压铸大型部件。
镁单位体积的熔化潜热只有铝的2/3,比热只有铝的3/4,并且有非常低的溶铁性。
这些特性使镁压铸件达到和铝几乎相同的生产成本/每公斤。
1.2 镁合金性能(1)、在实用金属中是最轻的金属镁的比重大约是铝的2/3,是铁的1/4。
它是实用金属中的最轻的金属。
应用范围:镁合金广泛用于携带式的器械和汽车行业中,达到轻量化的目的。
(2)、高强度、高刚性镁合金的比重虽然比塑料重,但是,单位重量的强度和弹性率比塑料高,所以,在同样的强度零部件的情况下,镁合金的零部件能做得比塑料的薄而且轻。
另外,由于镁合金的比强度也比铝合金和铁高,因此,在不减少零部件的强度下,可减轻铝或铁的零部件的重量。
应用范围:手机电话,笔记本电脑上的液晶屏幕的尺寸年年增大,在它们的枝撑框架和背面的壳体上使用了镁合金。
镁合金模具设计精要
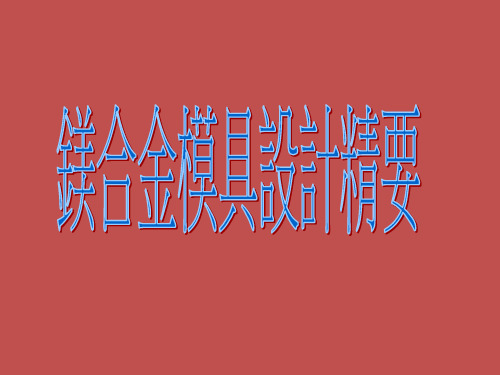
❖壓鑄方案設計
7.1.2 溢流井位置決定:
1> 熔湯最後到達處
2> 空氣模穴積留處
3> 產品頂出困難處
4> 模具溫度平衡處
❖壓鑄方案設計
8. 逃氣道設計:
<1> 逃氣總面積:> 1/3澆口面積 <2> 逃氣道深度為0.10~0.15,寬度:10~30
頂出銷間隙排氣 分模面排氣
❖壓鑄方案設計
3> 型芯間隙逃氣
❖模具結構設計
(三1). 壁內厚模:決設定計於(容模納仁冷部卻水分管) 通過,安排溢流井及固定螺
紋深度
2. 內模公差選用 (1)鑄件縮水率:4%0~6%0(阻礙) (2)6%0~8%0(混合) (3)8%0~10%0(自由) (鎂合金) (4)模具制造公差(成型部分)一般為鑄件公差的
1/5~1/4 (5)內外模配合: a. 高度方向內模應高出外模0.05~0.1mm (考慮到逃氣,應該高出0.15左右) b. 長寬配合為H8配h7(一般模仁為-0.02、模框為
功用:將產品、 gate及overflow頂出
頂針挫曲的計算公式
其中: K:安全係數,鋼取1.5~3; 一般取2.0. N:穩定係數,其值取20.19; E:楊氏模數,鋼取:2.1×106kg/cm2; I:頂出銷最小截面積處之慣性距(cm4), 對於圓形截面 (d為頂出銷直徑); P:為頂出銷所承受的實際壓力(kg); L:為頂出銷的長度(mm);
b.回位銷的常用規格: (Ø12,Ø15,Ø20,Ø25,Ø30,Ø35,Ø40等)
(2) 回位銷的長度計算公式
回位銷的長度 =可動外模高度+模腳高度-頂出板厚度-止位銷厚度
❖模具結構設計
镁合金压铸模具规划PPT教学课件

頂 出 排 氣 溢 料 井
模 溫 油 路 配 置
導 銷 模 座 大 小
模座及配件 市購品發包
客戶 出圖
A
會同客戶、業務人員 壓鑄人員、模具設計 治具設計方案討論
成品圖 3D構圖
倒勾尺寸 脫模角檢查
模仁圖 O.K 模具圖 3D拆圖 2D繪圖
圖面 OK
檢討
.
N.G
N.G
模仁素材 水孔攻牙
模仁CAM 程式製作
生產
操作規範 檢驗規範
模具移交記錄表
製程中檢、出貨檢查表 自主檢查表
2
XXXX 股 份 有 限 公 司
鎂合金壓鑄模具作業流程
入 料 方 式 位 置
模加 分滑合 穴工 模塊金 數位 毛倒公 目置 邊勾差 排方 位處縮 列式 置理水
肉月外 厚產觀 脫量形 模總狀 角產品 度量質
心 型 大 小 位 置
澆 口 流 道 料 管
試模 FAI
會議記錄
成品圖 模具設計流程圖
模具製作組立圖 (檢、治具)驗收
成品圖
協力廠提供製作規範
樣品製作進度表 托外加工單 樣品驗收單
模具設計進度表 模具設計圖面 模具結構圖 模具材料規範書 模具製作進度表 模具保養卡
模具托外製作合約書 模具驗收報告
試模報告 機台條件設定表
FAI 表
模具移交 品質規劃
電極CAM 程式製作
模仁CNC 銑床粗加工
淬火 熱處理
N.G
N.G
模仁CNC 銑床細加工
O.K 放電 檢驗 線割
加工
檢驗
O.K 整模 組模
試模
O.K
O.K
刻字
回火氮化 熱處理
量產Biblioteka 2020/12/10N.G
AE44镁合金油底壳压铸件本体组织与性能分析
··汽车发动机油底壳是汽车上重要的安全部件之一,对其各项力学性能尤其是抗拉强度有着明确的要求。
目前,油底壳压铸件大部分采用铝合金材料[1],而汽车轻量化的趋势使得我们需要寻找一种更轻的材料,镁合金因其自身的特点而在这方面得到应用。
近年来,对于镁合金材料的研究很多,但对于镁合金压铸件本体的研究却鲜见报道。
本试验以汽车油底壳镁合金材料AE44为例,结合其铸造及加工性能,分析AE44镁合金油底壳压铸件本体组织与性能,并对其工艺的改良提出建议。
合金的铸造性能是保证铸件质量的重要因素,铸造性能主要有流动性、收缩性、偏析倾向等,直接影响其加工性能。
流动性是指液态金属充满铸型的能力,流动性受很多因素的影响,其中最主要的是化学成分和浇注温度的影响。
收缩性是指铸件从浇铸温度至室温的冷却过程中,其体积和线尺寸减小的现象[2]。
偏析倾向是指铸件凝固过程中有产生组织不均匀的趋势,倾向性越强,出现偏析的几率就越大。
1试验材料与设备试验材料为Mg-40%RE 合金、AM50、纯镁,通过这三种材料的配比得到本油底壳所需材料。
油底壳本体在力劲DCC1600M 冷室压铸机上制得。
油底壳长约450mm ,宽端宽约325mm ,窄端宽约170mm ,高约170mm ,壁厚为8~13mm 。
显微组织观察试样及力学拉伸试样由线切割在本体上取得,拉伸试样采用矩形ⅠⅠⅠⅠⅠⅠⅠⅠⅠⅠⅠⅠ压铸董泰山,龙思远,廖慧敏,刘勇(重庆大学材料科学与工程学院,重庆400030)摘要:通过材料的替代研究,得到了AE44镁合金油底壳压铸件。
模拟结果显示该合金的充型能力和凝固顺序等铸造性能都满足此油底壳的工艺条件。
利用OM 、SEM 、XRD 对本体组织和物相分析,结果表明:本体组织主要由α-Mg 基体和沿晶界分布的Mg-RE 化合物组成,这些化合物主要为Al 11RE 3、Al 2RE 、Al 2.12RE 0.88。
Al 11RE 3和Al 2.12RE 0.88稀土相的存在,对材料性能的提高起到很大的作用。
汽车屏幕支架类镁合金压铸件的模具设计及压铸工艺分析
汽车屏幕支架类镁合金压铸件的模具设计及压铸工艺分析摘要:随着汽车行业和电子科技的迅猛发展,车载人机交互,人工智能蓬勃发展,汽车车载显示屏越做越大,从单一的主驾驶位单个屏幕,到副驾位双联屏、三联屏,使用传统单一结构的钣金件来做屏幕背板支架,已经不能满足其性能要求。
通过压铸工艺得到的零件,能实现复杂结构,同时可以经济快速地批量生产,正好能满足大尺寸屏幕支架的需求。
结合汽车轻量化的推进,镁合金压铸件用于汽车屏幕支架成了最佳的选择。
关键词:镁合金压铸件;汽车屏幕支架;压铸模设计;压铸工艺分析;随着新能源汽车的大量推广,续航里程的需求要求汽车车身重量不断减轻,汽车零部件轻量化需求不断扩大。
镁合金是新一代轻量化合金的代表,其相同的体积重量约是铝的15%,约是钢的18%,(镁密度1.4g/cm³、铝的密度g/cm³、钢的密度7.8 g/cm³),成为汽车轻量化的最佳选择。
镁合金压铸件在汽车屏幕支架上的应用,代替传统钢材质的钣金件,不仅在重量上有明显的降低,相较于结构单一的钣金件,更能实现复杂设计的要求,同时增加表面喷漆喷粉后,也能满足美观的要求。
屏幕支架需要安装液晶屏幕,对压铸件的平面度要求极为严格,同时屏幕支架上筋条结构复杂、立柱结构多,这就对模具设计和压铸生产过程的要求更高,因此探究镁合金屏幕支架压铸件的模具设计和压铸工艺十分必要。
1压铸及压铸模具介绍1.1压铸介绍压铸是压力铸造的简称,是一种将熔融合金液倒入压室内,以高速充填钢制模具的型腔,并使合金液在压力下凝固而形成铸件的一种铸造方法。
压铸区别于其它铸造方法的主要特点:①高压:金属液是在压力下填充型腔的,并在更高的压力下结晶凝固,常见的压力为15—100MPa。
②高速:金属液以高速充填型腔,浇口处速度通常在10—50米/秒,有的还可超过80米/秒,因此金属液的充型时间极短,约在0.01—0.2秒内即可填满型腔。
与其他铸造工艺相比,高压压铸工艺生产的产品尺寸更加精确,铸件表面光滑,生产速度更快。
镁合金压铸成型
环保与可持续发展
环保材料的应用
为了满足日益严格的环保要求,镁合金作为一种可再生资源,其 应用越来越广泛,有助于减少对有限金属资源的依赖。
节能减排技术
在镁合金压铸成型过程中,通过采用先进的节能技术和减排措施, 降低能耗和减少环境污染。
循环经济与资源回收
发展循环经济,推动镁合金废料的回收和再利用,实现可持续发展。
THANK YOU
感谢聆听
06
实际应用案例分析
汽车制造业中的应用
镁合金压铸成型在汽车制造业 中广泛应用于发动机、变速器 等零部件的制造。
由于镁合金具有轻量化、高强 度、高刚性等特点,使用镁合 金压铸成型能够显著降低汽车 重量,提高燃油经济性和动力 性能。
镁合金压铸成型还具有生产效 率高、成本低等优势,因此在 汽车制造业中具有广阔的应用 前景。
随着科技的不断进步,镁合金压铸成型技术也在不断创新,如研究 开发出高能效、高精度的压铸设备,提高生产效率和产品质量。
模具设计与制造技术
模具是压铸成型的关键,通过优化模具设计和制造技术,可以提升 镁合金压铸件的精度和表面质量,满足更高端产品的需求。
自动化与智能化生产
随着工业4.0的推进,镁合金压铸成型将逐步实现自动化和智能化生 产,提高生产效率和降低人工成本。
电子产品外壳制造中的应用
02
01
03
随着电子产品向轻薄化、小型化方向发展,镁合金压 铸成型在电子产品外壳制造中越来越受到青睐。
镁合金具有良好的电磁屏蔽性能和散热性能,能够满 足电子产品对外观、性能和轻量化的要求。
通过镁合金压铸成型,可以快速、高效地生产出高品 质的电子产品外壳,提高产品市场竞争力。
镁合金压铸成型
目
镁合金汽车零件压铸模具的加工成型技术
金属液 粘度 对充 型性 能 的影 响 。金 属 液 化 , 正确选 择各工艺 参数十分 重要 。 因此 粘度 显著影 响充 型流动状态 , 雷诺数 来表示 用 浇 注 系统设 计 。浇 注系 统对金 属液 流动 这种 性质 , 同时考 虑到流道 的几何形状 和金 的方 向、 溢 流条件 、 的温度分 布 、 它 排气 模具 压力 属 液 内 摩 擦 产 生 的 流 动 阻 力 。 以 G 的传 递 、 时 间的长短及 金属液通过 浇道处 D— 充填 M A9 n 与 G — 1i C g1 l Z D ASl u的粘 度作 比较 , 2 定 的速度和 流动状 态等各个 方面 , 起着重要 的控 性得 出浇 注速度 。 两者充型 时的流动特 征应相 制 与调节作 用 。 良好 的浇 注系统设 计是 模具成 同, 两者流 动时雷诺数 相等 。镁 合金 液平均 功与否的关键之一 , 故 不合理的浇注系统设计可 充填 型腔 速度 约为铝 合金 的 1 5 。根据 镁 能导 致 诸如 缩孔 、 .倍 2 流痕 、 隔 以及表 面质 量不 冷 合金 的 比热容 , 型时 间要短 ; 据镁 合金 的 理想 等各种 缺陷 。内浇道形状 尺寸 , 排溢 充 根 以及 内各主要汽车厂家对镁合金在汽车上的应用 粘度 , 型速度 要快 。 充 这两者 的一致性 , 表明镁 系统 对于能 否压铸 出合格产 品至关重要 , 模具 表 现出强劲需 求 , 中一些 厂家 已开 始将镁 合 合金是 一种非 常适宜压 铸的合金 。 其 设计 中必须 注意考虑 镁合金 的压铸特性 。 金 开发应用提 上重要议 程。 压力 对镁 合金 热物性 值 的影 响压 铸时 的 2 . 2计算 机数 值模 拟 高 压 会 影 响 金 属 的 某 些 热 物 性 值 。根 据 目前 , 值模拟 软件被 广泛认为是优化 汽 数 1镁合金 加工成 型技 术简介 镁合 金成 为重要 的工 程材 料 除 了本身 的 Cas sCaern l i — l yo 方程 ,当镁合 金体 收缩 为 车零件压铸模具工艺设计的必备工具。美国、 uu p 优异 性能外 , 以方便 的加 工成所需 要 的外 3 %及 铝合金 体收缩 为 6 3 ,熔点升 高 日本、 还可 . 8 %~%时 德国等国的镁合金压铸企业十分重视镁 形 。 合金成 型主要通过 塑性变形 和铸造两 种 率 为 0 0 ̄/1 P ,当充 型 压 力 为 5MP 合金 C DC E技 术在 产 品生 产 工艺 设 计上 镁 .6 0M a 0 C . O a A /A 方式 但是 用塑 性变形 法加 工镁 合金 存 在着 许 时, 镁合金的熔点可升高 3 这对压铸件质 的应用 , 取得 了一定成 果 。 ℃, 并 我国在铝 、 锌合金 多不利因素, 当前镁合金的成型主要依赖铸造 量几乎没 有影 响。 压铸模的数值模拟方面已经开展了大量 的工 的方法 。 镁合 金铸造 大致 分为 : 浇注 、 压 重力 低 镁合金的吸气性与压铸件中的气孔镁合 作 ,但在镁 压铸模 方面 的研究还 刚刚起步 , 对 浇注 、 固态压铸 、 变注射 成 型 、 半 触 高压铸 造 。 金 压铸件 中 的气孔 , 除少部分是 充 型过 程 中形 镁 压铸过 程 的充 型规律 、 型性能 与压 铸工艺 充 由于镁合 金热流动性好 , 以很适 合薄壁 件 的 成 的卷人性 气体外 ,主要是镁合 金在熔 炼 、 所 保 参数 的关 系 尚缺乏 深入 系统的研究 。因此 , 应 压 铸 生产 。现在 9%左 右 的镁合 金工 程结 构 持 、 注过程 中吸收 和溶解 的气 体在冷却 和凝 当抓 住 当前 市场发 展的有 利时机 , 0 浇 投人人 力物 件 是通过 压铸方法制造 的。 压力 铸造 的原理是 固过程中析出而形成的析出性气孔。 镁合金溶 力 ,在镁 合 金 C DC E研 究 领域迎 头赶 上 。 A /A 液 体 金属在 高压作 用下 压人 精密 加工 的 钢压 解氢的能力很强,铸锭上即使沾有一点水分 , 采用热室压铸机对镁合金手机外壳进行生产, 铸 模 内 , 全填充 压铸 模 , 而 获得 轮廓 清 也会 与镁锭 体反应 , 原除游离 氢并溶解 在镁 利用计算机辅助设计和模拟分析一体化技术 并完 从 还 晰的、 与压铸模型腔相符的压铸件。 锭体中。因此 , 镁合金熔体的含气量及其压铸 (A /A ) C DC E,通过 计算 机展 示镁 合金 液充 型 、 1 . 1压铸 的填 充过程 件 的气孔 数量 与熔炼 、 温 、 保 浇注 时的 空气 的 凝 固的全过程 , 并分析缺陷成因, 改进不合理 压铸的填充过程是复杂的, 早期的填充理 温度及炉料的干燥程度密切相关, 故镁锭及镁 的浇注 系统工 艺设计方 案 , 有效地 保证 了产 品 论 的一些 观点 都是在 特定 的试 验条 件 下获 得 回炉料 必须彻底 烘干后 才能投炉 。 氢在镁合 金 质量。 采用数值模拟方法可以大大缩短新产品 的 , 很 大的 局限性 , 用来 分析 一些 实 际 熔体 中的溶解度 随温度 降低而减小 , 外界 压 试制周期、 有 直接 在 降低工艺改进费用, 将缺陷降低到 问题 虽然有一定 的意义 , 但还 存在不 足之 处 , 力及本身压力的作用下 , 析出的游离氢在镁合 最低 限度 , 是在设计 早期 阶段 采用模拟软 特别 这在 生产实践 中 已得到证 实。 早期 较为典型 的 金凝固和冷却过程中在铸件中形成孔壁光滑 件 , 预测缺 陷 的产 生 , 浇注系 统设计 , 以 优化 可 三种填充 方式如 下 : 的不规则气孔。当铸件继续冷却时, 由于外界 有效避免由于结构、 工艺和模具的不合理设计 喷射 填充 。金属液 从 内浇 口处 喷射 至 型 压力的作用及气孔吸收残余镁液而形成伴有 所 造成 的损 失 。美 国芝加 哥 W i e l ht M t 铸造 e a 腔最 远端 , 击该 处 型壁后 , 金 属聚 积并 气孔的偏析( 撞 部分 即所谓的浸透固溶体)并使气孔 公 司采用 C E软件获 取薄壁 家电产 品机壳流 , A 产生涡 流 ,另一部分金 属则 向所 有方 向喷溅 , 直径显著减小。 场、 温度场的各种信息, 据此进行浇道 、 溢流槽 并沿型壁 自远端 向内浇 口返 回。 金属流 的速度 2镁 合金 汽 车零件 压铸 模具 的加工 成型 和冷却系统优化设计。 利用模拟结果绘制 P 2 Q 由内浇1截面积与型腔截面积之 比的大小来 技术 : 3 图, 综合考虑多种 因素的影响 , 最终确定生产 控制。 2 . 1镁合 金汽车 零件 , 压铸模 具 设计关 键 工 艺中采用 的最佳 工艺参数 值。 数值模拟 软件 全壁厚 填充 。金属 流从 内浇 口处开始 , 由 技 术 在汽车镁压铸件中应用最为普遍 , 德国的一些 后 向前充满 型腔 的整个厚度 流动 , 时不 产 流动 压铸机选择 。镁合金可以在冷室压铸机 汽车行 业 已经 成功地 模拟 了座椅 架 、 触变成 型 生涡流。 无论内浇口截面积与型腔截面积之 比 中压铸 , 也可以在效率更高的热室压铸机中压 燃油泵 、 奥迪 5 倍速变速箱、 车轮、 缸发动机 4 的大小 如何 , 流动形 态不受影 响。 铸。 采用何种形式的压铸机进行生产主要取决 缸体等汽车用镁合金压铸件, 有效地缩短了产 三 阶段填充 。填 充过程 大致 分 为三 个 阶 于铸件 的壁 厚 。 o n i 在对 “ 合金压铸 品开发周期, R l dFn a k 镁 极大增强了企业市场竞争能力。 段 : 阶段是 金属进 入 型腔后 , 第一 首先 冲击对 工 艺 的优化 ” 问题 进行 研究 的过 程 中 , 过对 通 3结 束语 面型壁, 并沿型腔表面向各方向扩展 , 在型壁 镁合金压铸经济性、 冷室压铸和热室压铸过程 镁合金汽车零件压铸模具 的加工成型技 上生成表层 , 这个表层即为铸件的外壳, 又称 分析提 出: 一般情况下, 小于 1 的铸件需要 术首先要运用先进的工具软件建立模具标准 为薄壳层 ; 阶段是 随后进入 的金属继 续沉 采用热室压铸机, 第二 以保证薄壁件的充满; 大件 件数据库和压铸模具设计 , 并进行计算机数值 积, 在薄壳层内的空间 , 直至填满 ; 第三阶段是 则推荐 采用 冷室压铸 机。 模拟 , 并且模 拟充 型和温度场 过程基础上 寻求 在压力的作用下, 型腔内的金属得到压实。 工艺参数。在压铸生产过程中, 选择合适 模具 的优 化设 计 才是 中 国镁合 金汽 车零件 的 1 - 2镁合金主要物理和化学性能对压铸 的工艺参数是获得优质铸件, 发挥压铸机最大 长远 出路 。 性 能的影响 生产率 的先决条件 ,是正确设计压铸模 的依 参考 文献 热焓 对充型性 能 的影 响. 属熔体 从 工 据。 。金 压铸时 , 影响合金液充填成型的因素很多, 【 马秋 . 金汽 车零件 压铸模 具设 计与数 值 1 ] 镁合 作温度到凝固温度释放的热量, 决定了其在相 其 中主要有压射压力、 压射速度、 充填时间和 模拟研究叨晗 尔滨理工大学, 0- 3J . 2 5 o- 1 0 0 同热导率下保持可铸性的时间, 因此这种热量 压铸模温度等等。这些因素互相影响、 互为制 便作为判断其最大可充型时间的尺度。 约 ,调 整一 个 因素会 引起 相 应 的工艺 因素 变
- 1、下载文档前请自行甄别文档内容的完整性,平台不提供额外的编辑、内容补充、找答案等附加服务。
- 2、"仅部分预览"的文档,不可在线预览部分如存在完整性等问题,可反馈申请退款(可完整预览的文档不适用该条件!)。
- 3、如文档侵犯您的权益,请联系客服反馈,我们会尽快为您处理(人工客服工作时间:9:00-18:30)。
小Pin易折斷。
不要設置太細太長 的成形Pin,若有, 則有補強肋比較好。
1.外圓角不足易踫傷.模具易龜裂. 2.內圓角不足易發生制品龜裂,及 應力集中。
R角至少0.3以上,以R0.5~R1最佳。 •當T型相交時,則R1=1~1.25 T1 •當T2 > T1時,則R1=2/3( T1+T2) & R2=0~(R1+T2) •當T1=T2時;若R2=R1+T1則R1=T1,若 R2=0,則R1=1~1.25 T1
34
34
135
無缺口衝擊強度
J
6
22
3.5
11
有缺口衝擊強度
J
1.5
3.2
延伸率
%
3
8-15
4
5
8
17
30-50
彈性模量
GPa Ambient
45
45
72
73
8.9
2.1
207
剪切模量
GPa Ambient
14
27
28
83
布氏硬度
65
60
80
80
140
泊松比
0.35
0.35
0.33
0.30
二.鎂合金壓鑄件成品設計要點
比熱 熔化潛熱 凝固範圍 腐蝕失重 3天5% NaCl
單位 g/cm3
AZ91
AM60
A380 DC
A356 T6
尼龍
ABS
鋼
1.81
1.79
2.74
2.69
1.4
1.05
7.8
W/m·k
51
61
96
159
0.33
0.28
14
μm/m·k
26
25.6
22
21.5
34.5
76.5
12
%@35MPa
29
4.不均一的肉厚
T(max) ~~ 1.5t
t
T
R
R
R R
六.其他設計參考
5.最小肉厚(Rib)
t
脫模角
3°~5°
H R T
H(mm) 1~4 4~10 10~20 20~25
t(mm) 0.4T 0.5T 0.7T 0.8T
R=0.5t
六.其他設計參考
6.機加工刀具的最小Size
最小T型刀
最小的Tap
應盡量避免。
四.設計尺寸公差
A、一般尺寸公差
A
A
不重要尺寸容許公差
尺寸A的長度
鋅合金 鋁合金 鎂合金
25mm以下基準公差 ±0.25
A長度超 過25mm
25~300mm 每25mm公
差增加
300mm以 上
每25mm公 差增加
±0.04 ±0.025
±0.25 ±0.05 ±0.025
±0.25 ±0.05 ±0.025
銅合金 ±0.35 ±0.08
---
重要尺寸容許公差
尺寸A的長度
鋅合金 鋁合金
25mm以下基準公差 ±0.08
25~300mm;
每25mm公 ±0.025
A長度超 過25mm
差增加
300mm以 上;每
25mm公差
±0.25
增加
±0.1 ±0.04 ±0.025
鎂合金 ±0.1 ±0.04
±0.025
1.為了避免鑄件傷著模具,所有 內外側尖角都應適當倒圓角.
2.盡可能使壁厚均一,在需要對壁厚 進行改變的部分,為避免應力集中而 壁厚徐徐改變.
不好的案例
R
好的案例
R
不好的案例 好的案例
五.鑄件形狀的注意事項
3.在選擇壁厚時,應考慮壓鑄的鑄造簡便性, 且有一定的剛度和強度,為了防止部分變 形,增強強度,利於熔湯流動可增加骨架.
成形時後退或尺寸不穩。
A
其公差如下:
注:此處的投影面積指的是滑塊上成品部投影面 積,而且此處的公差必須要再A項的一般形 狀公差。
鋅合金
鋁合金
鎂合金
銅合金
±0.1
±0.13
±0.13
±0.13
±0.15
±0.2
±0.2
一
±0.2
±0.3
±0.3
一
±0.3
±0.4
±0.4
一
四.設計尺寸公差
D、平面度公差
三次上塗(重工二次) 100~120um
厚0.4~0.6mm(視Rib高度5~10mm)
5‰~5.5‰
六.其他設計參考
1.Boss上的頂針設計
2.制品形狀之Pincut
Min0.3mm 避 免 這 種 形 狀
Min0.5t 肉厚t
六.其他設計參考
3.表面研模量(mm)
正面0.02~0.04
側面0.02~0.04
應用領域 (航空、汽車、軍事工業、3C產品) 1. 產品輕量化 2. 產品需要高強度 3. 產品需散熱性高 4. 產品需電磁屏蔽 5. 產品可重複利用
缺點 1. 材料成本高 2. 後加工處理成本高 3. 耐蝕性差 4. 製程危險 (粉塵易燃)
一.鎂合金特性
鎂合金與其他材料物理性比較
物理性能
密度比重 傳熱係數 膨脹係數 減振性能
4.為了節省原料,在有孔和凹進去的部 位將無用的場合減肉.需同時考慮模 具增加的費用,但最終要降低總體的 費用.
不好的案例
不好的案例
好的案例
Rib
好的案例
五.鑄件形狀的注意事項
5.細中子銷避讓性好,但易彎曲,需定 期更換,在壓鑄加工小孔時,採用細中 子銷不如一般情況下經濟劃算.
6.頂針是用於將鑄品從模具 處頂出而設置的, 它的配置應防止制品變形,在外觀上機能上應 將其放在不礙事的適當位置上且設置適當的 頂針數.
52
1.2
J/l·k
1900
2640
2590
1200
kJ/l
673
1066
℃
470-595 540-615 540-595 555-615
Mg/cm/d
0.02
0.05
0.1
0.5
一.鎂合金特性
鎂合金與其他材料機械性能比較
機械性能
單位
條件
AZ 91D
AM 60
A380壓 鑄合金
A356T6
尼龍
ABS
平面度
平面度的要求為太高,很難達成, 單向0.5~0.8 mm。
卡勾
卡勾以T型刀加工不采用內斜銷滑 塊成形。
卡勾以P.L面為基准,公差+0.05~0.1。 卡勾長邊一般50~60mm ,短邊為40mm設 計1支,寬幅10mm。
三.鎂合金壓鑄件成品設計建議
部位
攻牙
原因
攻牙深度要有規定,否則易發生 穿孔或扭力不足。
1. 肉厚的均一性是必要的。 2. 避免尖角。 3. 注意拔模角度。 4. 注意產品之公差標注。 5. 太厚太薄皆不宜。 6. 避免死角倒角(能少則少)。 7. 考慮後加工的難易度。 8. 盡量減少產品內空洞。 9. 避免有半島式的局部太弱的形狀。 10.太長的成形孔,或太長的成形柱皆不宜。
三.鎂合金壓鑄件成品設計建議
參考附圖
建議
去毛邊 應力集中 分模線
制品要考慮去毛邊作業的方便性, 尺寸也要考慮毛邊的去除量。
模具排氣應設計 0.05mm以下,減少 毛邊生成。
即使成形過程中克服了因應力集 中而產生的裂痕,但在組裝或強 度耐久試驗時,容易NG。
以內圓角來對應, 且強調肉厚均一化。
1.避免外觀面的分模 外觀因折模而發生的段差,容易 線。 因手工研磨而產生制口過磨過修。 2.公,母模相插成形
3
最小的 End Milling
六.其他設計參考
螺紋加工的規格尺寸(分兩種情況說明) 1.鑽孔後直接攻牙
A
B
絲攻
A:螺紋倒角(C0.3) B:有效牙深 C:絲攻的無效牙長度 D:絲攻底部與鑽孔最深處的距離 2 M2.5 M3
螺距
0.4 0.45 0.5
C尺寸
0.55 0.6 0.65
鎂壓鑄品圓形面直徑或矩形之對角線尺寸 75mm以下
75mm以上毎25mm追加
公差量mm 0.2 0.08
E、模銷孔之角度公差
最小公差—任意孔 孔深75mm以下
孔深75mm以上毎25mm追加
±0.13mm
0.25*D/M D:孔深 M:ADCI-E6之最大孔深 (右表)
每25mm追加0.075mm
五.鑄件形狀的注意事項
鋁合金 ±0.13 ±0.2 ±0.3 ±0.4
鎂合金 ±0.13 ±0.2 ±0.3 ±0.4
銅合金 ±0.13
一 一 一
四.設計尺寸公差
C、滑塊成形上的尺寸公差
型分割面
壓鑄的投影面積 65CM2以下 65~130CM2 130~320CM2 320~650CM2
A
滑塊成形因鎖模力分力的關系,更容易造成滑塊
部位
Rib
原因
脫模角不足易造成粘模; 太細時成形不良; 太厚時外觀易縮陷.
10以 下
建議
0.6
R0.53 ~5
Boss
脫模角不足,易粘模, 太粗時,外觀易縮陷。
肉厚 通孔
太薄時,增加鑄造及後工程的加 工難度。
最大肉厚4mm,一般在3mm以下, 末端壁厚需大於1.5mm以上,利 於加工。
不要連續集中的通孔,制品散熱應 考慮流動性及模具強度
產品應提供足夠進澆的空間
能設置Gate的地方, 有多少算多少,能 多盡量多。
三.鎂合金壓鑄件成品設計建議