镁合金压铸件设计指南
第7部分:压铸件设计指南
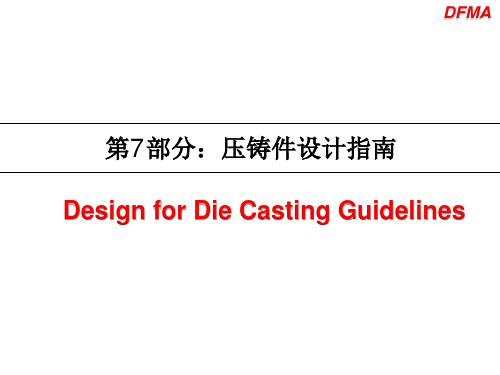
1. 零件壁厚 2. 压铸件最小孔 3. 避免压铸模局部过薄 4. 加强筋的设计
DFMA
5. 脱模斜度 6. 圆角的设计 7. 支柱的设计 8. 字符 9. 螺纹 10. 为飞边和浇口的去除提供方
便 11. 压铸件的公差 12. 简化模具结构、降低模具成
本 13. 避免机械加工 14. 使用压铸件简化产品结构
DFMA
B. 合理选择分模线,提高重要零件尺寸的精度
如果D1和D2的同心度很重要,选择C-C为分模线 如果D1和D3的同心度很重要,选择B-B为分模线 如果需要保证D1在左端或右端直径的一致,则选择A-A为分模线
27
12. 简化模具结构,降低模具成本
DFMA
A. 避免内部侧凹
内部侧凹通过侧抽芯机构或通过二次加工来获得,这会大幅增加模具或 者零件的成本
优点:
生产效率高,生产过程容易实现机械化和自动化; 压铸件的尺寸精度高,表面质量高; 压铸件的力学性能较高; 可压铸复杂薄壁零件; 压铸件中可嵌注其他材料的零件;
缺点:
压铸件中容易产生气孔; 不适宜小批量生产; 压铸高熔点合金时模具寿命较低;
DFMA
5
3. 独特优势
DFMA
独特优势:
原始的设计
C. 添加加强筋辅助熔化金属的流动,
优化的设计
辅助熔化金属的流动,提高零件的充填性能
加强筋的方向与熔化金属的流向一致
13
4. 加强筋的设计
D. 加强筋的位置分布要合理,尽量做到对称、均匀
DFMA
原始的设计
E.加强筋连接处避免局部壁太厚
优化的设计
原始的设计
优化的设计
14
5. 脱模斜度
【设计规范_07】压铸产品相关设计要求

【设计规范_07】压铸产品相关设计要求导读压铸产品开始流行,都忘了是什么时候了,记得moto的刀锋系列就是镁合金压铸的,着实火了一把,现在的手机产品中压铸件使用也越来越多,今天我们就介绍下压铸产品设计的注意事项:1什么是压铸?压铸(英文:die casting)是一种金属铸造工艺,其特点是利用模具腔对融化的金属施加高压。
模具通常是用强度更高的合金加工而成的,这个过程有些类似注塑成型。
压铸设备和模具的造价高昂,因此好的产品结构更为重要,产品不但影响模具寿命,甚至对机台都会有影响;2压铸产品设计要求1.壁厚须力求平均2.孔径与深度关系3.肋与壁厚关系D≦4~5t 在此比例下应不会产生缩水痕,但非必要还是以力求壁厚平均为佳。
4.圆角当T1=T2时,若R2=R1+T1则 R1=T1 ,若R2=0则 R1=1~1.25T1当T2 > T1时,则R1=2/3( T1+T2) & R2=0~(R1+T2)当十字或Y型相接时:当Θ=90°时,则 R1= T1当Θ=45°时,则 R1= 0.7 T1 & R2= 1.5 T1当Θ=30°时,则 R1= 0.5 T1 & R2= 2.5 T15.拔模角3产品结构规避风险设计1.压铸产品进胶与塑胶产品不同,产品必需要有足够的进浇空间,且进浇位置尽量要平缓(不要有较大的高度落差),尽量让进浇平缓均匀,如下图说明:不合理:1.1 两边包胶燕尾槽分布较多,进浇无足够的空间1.2 内框太深,模具上形成高的钢位,阻挡了进浇的流向,且钢位易被冲击腐蚀;1.3外部料位有较大的断开,进浇需走高低差,压铸模不现实改进方式:1.1 取消部分燕尾槽,减少其分布密度1.2 内框深度做浅,其深度尽量控制在2.0MM以内1.3 断开处在装配要求允许的情况下尽量加胶连接起来2.产品进浇尽量避开正面冲击产品通孔,插穿扣位及较小的碰穿孔,如下说明:弊端:2.1.产品进浇正面冲击模具上通孔的碰穿柱,影响进浇的走向2.2.由于碰穿柱较小,正面冲击易致其断裂,压铸后产品通孔不通改进方式:2.1.减少通孔的分布数量,加大孔径,以加强此通孔模具上碰穿柱的强度2.2.此通孔拉胶位可做成沟槽的形式,模具强度较好3.产品内侧壁的厚度不要过于单薄弊端:3.1.由于壁厚过薄,会影响进浇的流动性,导致产品不易打满,影响产品的致密性及整体强度3.2.由于薄壁处强度较弱,产品脱模时易断裂改进方式:3.1.其厚度最小做到0.8MM左右3.2.条件允许下,可做些补丁形式的骨位,加强其强度,如右下效果图4.燕尾包胶槽的设计上图所示的两种燕尾槽形式,在产品压铸后都需冲模冲切成型,由于上左图所示的燕尾槽开口宽度尺寸较小,导致冲模冲头钢位较弱,而且模具加工困难,所冲出的产品精度不易控制,右图形式较为合理,具体如下:1.燕尾槽开口处的尺寸最小在1.8-2.5MM左右,冲模冲头钢位强度相对较理想2.此通孔式的燕尾槽压铸模易成型,有利于模具生产及产品的稳定。
镁铝合金外观件之设计规范
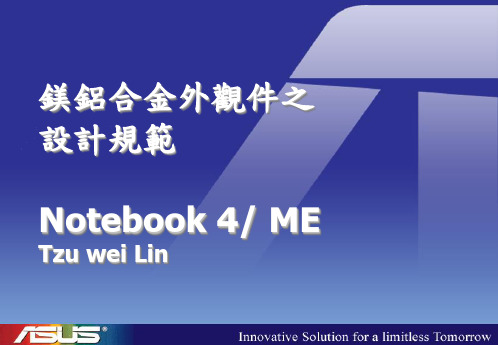
外觀
鎂鋁合金在噴漆,外觀修補痕跡,缺陷 等方面,均不同於一般塑膠及鈑金件, 宜另定新的外觀檢驗標準。
ห้องสมุดไป่ตู้
材料 1/2
一般使用的材料為AZ-91D,其成份及特性如下:
Magniesium Aluminum Zinc Manganese Iron Silicon Copper Nickel 90% 8.3~9.7% 0.35~1.0 % 0.15~0.5 % 0.005 % 0.10 % max 0.03 % max 0.002 % max
文字圖案: 成品文字圖案凹陷較不可行(除非線條寬度很大),以击起為可行 ,線條寬度b,線條高度h。 b≧0.5 mm h≦0.3 mm 但對表面烤漆件,為避免外觀不良無法處理,以印刷為宜。 考量模具壽命,不要設計公模斜梢之undercut,若無法避免,必須 以機械加工處理。 外滑塊可行,但拆模須延伸至Parting Line(隧道式滑塊不可行 )。 Rib 根部以R角與基材連接,可幫助充填及避免應力集中現象,一 般以R0.5~R2 為佳。Rib 寬度最小值小件如手機和PDA 應在0.6 mm 以上,大件如投影機和Notebook 應在0.8 mm以上,防止充填成形 不良。
Lead time
鎂鋁合金生產不同於一般流程,一般而 言,而壓鑄成品,設計階段約10~14 天(加工治具Ready 的狀況下),量產則 需2~3 週,必須對庫存做良好的控制, EC 亦需慎重。
修模
鎂鋁合金模具硬度較高,經焊補修模後 ,大大降低模具壽命(一般約10 萬模), 設計變更應儘量減少焊補部份。
5~10% 10~15% 10~20% 15~20% 10% 30~40%
鎂鋁合金件在開發過程的重點
設計 / 試模階段:
镁合金压铸件模具设计要点

浇、流道系统设计(6/10)
浇口设计
浇口面积计算公式
Ag V Vg t
V:压铸件体积(含溢流井体积)(cm3)
Vg:浇口速度 (m/s)
t:充填时间 (s)
Ag:浇口面积(mm2)
举例说明:铸件(含溢流井)重400g,平均壁厚1.4mm, V=400/1.8=222.22 cm3 (镁铸件比重为1.8) 假设Vg=55m/s, t=0.03 则Ag=222.22/(55*0.03)=134.68 mm2 , 另浇口厚度不得超出铸件厚度的一半,因而在此定为
精级拔模角 D 0.8( L / C) , (D/ L) / 0.01746度
一般级拔模角所需C值
精级拔模角所需C值
内表面(单边)=7
内表面(单边)=7.8
外表面(单边)=14
外表面(单边)=15.6
孔(全部)=4.76
孔(全部)=5.3
压铸方案设计程序 (1/2)
选择压铸机 决定压铸条件
4
4
5
6
6
镁压铸品模销孔径大于25mm时,直径与深度比 为1:6
镁压铸品模销孔直径 (mm)
3
4
5
7
10 13 16 20 25
镁压铸品模销孔标准深度
单位:倍
1
1 1.5 2
2
2
2.5 2.5
3
镁压铸品尺寸公差 (6/9)
平面之角度公差(ADCI-E11-65)
平面和基准面在同一模穴或同一侧滑模之一部份 面长75mm以下…………………………..0.13mm 超过75mm每25mm追加公差……………0.025mm
镁合金压铸产品设计要点

镁合金压铸产品设计要求1、尺寸公差要求
4、散热齿高度、厚度及拔模斜度等要求
此项指标与铝合金相比,同等尺寸下,高度可以稍高一点、厚度薄一些、拔模斜度稍小一点可行,若按原铝合金设计生产镁没有问题。
5、凸台/凹槽要求
这些没有特殊要求,主要根据产品结构而定,按铝合金设计可以再优化一点。
6、后面机加需留的余量
加工余量根据产品结构和精度要求而定,一般留0.5mm左右即可。
7、其他与铝合金压铸产品不同,设计上需要注意的地方
从制造工艺上来讲,铝合金生产时需用水来冷却,镁合金需加热,贵司产品结构设计考虑功能要求,有点问题我们可以从工艺上进行改良。
镁合金压铸手册
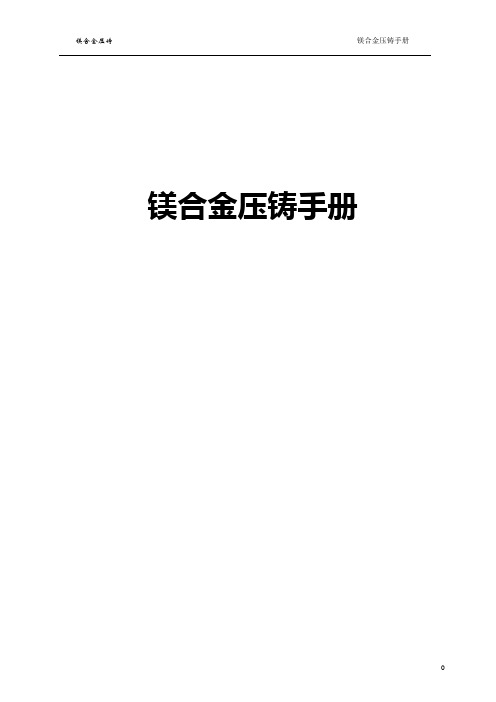
镁合金压铸手册目录一、前言二、镁合金压铸的安全方面三、压铸镁合金四、镁合金压铸设备五、镁合金熔化和处理六、镁合金压铸模具七、可供选择的工艺八、镁合金的腐蚀、表面处理一、前言本书的目的是论述有关镁合金压铸的基础知识,对于不熟悉压铸的读者可以作为入门书,对于有经验的压铸人士,可以参考其中有关的某些信息。
压铸是一种很好的铸造方法,特别适合于全自动,高效率大批量生产,压铸的零件重量从15克到15公斤,零件尺寸的可以接近实际要求,虽然压铸设备的机械和液压零件的基本原理已经利用100多年,压铸工艺仍在快速发展中,现在设备制造商可以供应镁合金,铝合金,锌合金,铜合金全自动压铸机,有的设备制造商全部负责供应包括模具在内的压铸设备,更常见的是压铸厂拥有一系列的压铸机,包括一定范围内不同吨位的压铸机,能够和不同产品的工模式相配合.开发新的应用领域,需要知道有关镁合金的性能,也要知道压铸工艺的限制和优势。
为保证最终产品符合规格和设计出具有最佳铸造性能的模具,产品设计者和模具设计者紧密合作是非常重要的。
开发压铸件需要团队努力,公差是模具成本的一个重要因素,太严格的公差会严重增加模具成本。
最基本的镁合金压铸技术和铝合金相似。
但是必须清楚重要的差别。
主要差别和熔化金属的处理有关,绝对不可以低估这些差别。
镁合金和铝合金具有不同的性能。
要求在压铸参数和模具设计方面作出相应的调整。
二、镁合金压铸的安全方面2.1概述注意安全是镁合金压铸成功运作的前提,在工厂管理系统中应包括如下:1.制订安全政策并传达所有员工。
2.制订年度安全指标,反应安全方面的连续改善。
3.建立系统的安全培训,在引入技术的同时进行安全培训。
4.在管理会议上应经常讨论安全问题。
5.应评估并记录各种工作中的危险建立各种有风险工作的安全政策。
这些政策应是书面的形式并及时更新。
6.应调查所有的事故和过失,应记录本调查结果并有跟进行动。
7.工厂就有应急计划并组织应急演习。
镁合金模具设计精要
❖壓鑄方案設計
7.1.2 溢流井位置決定:
1> 熔湯最後到達處
2> 空氣模穴積留處
3> 產品頂出困難處
4> 模具溫度平衡處
❖壓鑄方案設計
8. 逃氣道設計:
<1> 逃氣總面積:> 1/3澆口面積 <2> 逃氣道深度為0.10~0.15,寬度:10~30
頂出銷間隙排氣 分模面排氣
❖壓鑄方案設計
3> 型芯間隙逃氣
❖模具結構設計
(三1). 壁內厚模:決設定計於(容模納仁冷部卻水分管) 通過,安排溢流井及固定螺
紋深度
2. 內模公差選用 (1)鑄件縮水率:4%0~6%0(阻礙) (2)6%0~8%0(混合) (3)8%0~10%0(自由) (鎂合金) (4)模具制造公差(成型部分)一般為鑄件公差的
1/5~1/4 (5)內外模配合: a. 高度方向內模應高出外模0.05~0.1mm (考慮到逃氣,應該高出0.15左右) b. 長寬配合為H8配h7(一般模仁為-0.02、模框為
功用:將產品、 gate及overflow頂出
頂針挫曲的計算公式
其中: K:安全係數,鋼取1.5~3; 一般取2.0. N:穩定係數,其值取20.19; E:楊氏模數,鋼取:2.1×106kg/cm2; I:頂出銷最小截面積處之慣性距(cm4), 對於圓形截面 (d為頂出銷直徑); P:為頂出銷所承受的實際壓力(kg); L:為頂出銷的長度(mm);
b.回位銷的常用規格: (Ø12,Ø15,Ø20,Ø25,Ø30,Ø35,Ø40等)
(2) 回位銷的長度計算公式
回位銷的長度 =可動外模高度+模腳高度-頂出板厚度-止位銷厚度
❖模具結構設計
镁合金压铸零件的加工
镁合金压铸零件的加工镁合金密度较小,同等体积下比铝合金轻36%、比锌合金轻73%、比钢轻77%,被公认为是质量最小的结构金属材料,因此在航空航天产品上应用较多,在我们加工的产品中,就有部分镁合金压铸零件。
由于镁合金材料的机械性能与钢及铝合金有所不同,因此在加工过程中加工工艺、刀具、切削参数的选择也有区别。
因此,本文将对镁合金压铸零件的机械加工工艺及安全操作规程进行了概括性的介绍,以供参考。
1 镁合金的机械加工性能分析由于镁合金导热性好、切削力小,故在加工过程中的散热速度很快,因而刀具寿命长,粘刀量少,从而可以降低刀具费用。
因为镁合金易切削,其断屑性能十分良好,一般清况下只需经过一次精加工便可达到所要求的最终表面粗糙度。
同时由于镁的比热高、导热性良好,摩擦产生的热量会迅速地扩散到零件的各个部分,因此对镁合金进行切削加工时并不会产生较高的温度。
但是,在高切削速度和大进给量的情况下,零件所产生的热量也是相当高的,很可能因为温度过高而发生扭曲变形。
如果对成品零件的尺寸公差要求比较严格,则在设计中必须考虑到镁的热膨胀系数这一影响因素。
如果在上述加工条件下产生了相当多的热量,则很可能会影响到零件的加工精度。
镁的热膨胀系数略高于铝,明显高于钢。
在机械加工过程中,镁合金零件很少发生因为冷变形引起的扭曲变形或翘曲。
但刀具太钝、进给速度太慢以及刀具在加工过程中有停顿等不利因素时,也可能造成扭曲变形或翘曲。
2.刀具的选择加工钢和铝的刀具通常也适合于镁合金的加工。
但是,由于镁的切削力小,热容量也相当低,故其加工刀具应当具有较大的外后角、较大的走屑空隙、较少的刀刃数和较小的前角。
另外,保证刀具的各个表面很平滑也是十分重要的。
对镁合金进行机械加工的一条重要原则是,应当使刀具保持尽可能高的锋利和光滑程度,必须没有划伤、毛刺和卷刃。
如果刀具切削过其他金属,即使切削角没有改变,也应进行重新刃磨和晰磨。
3.切削液的选用由于镁的散热速度很快,可使被加工表面保持在较低的温度水平上,此外镁的易切削性使其不易与钢发生胶合,切削加工时一般不需要冷却液,但使用微小切削量时,要使用矿物油冷却液来降温。
镁合金压铸件成品设计要点
C尺寸 0.55 0.6 0.65
E
D尺寸 0.51~0.66 0.66~0.81 0.77~0.92
E尺寸(C+D) 尺寸(C+D) 1.06~1.21 1.26~1.41 1.42~1.57
六.幾個參數(Mg經驗值)
2.鑽孔後,再用銑刀加工,最後才攻牙
絲攻
A:螺紋倒角(C0.3)
B A
B:有效牙深 C:絲攻的無效牙長度
± 0.25
± 0.025
± 0.025
三.位於分模面上的尺寸公差
分模面上的直角方向因漲模 因素,公母模分開成形的尺 寸,較易變化,其與制品投 影面積成正比關系。
型分割面
壓鑄的投影面積 320CM2以下 320~650CM2 650~1300CM
2
鋅合金
A
鋁合金
鎂合金
銅合金
± 0.1 ± 0.15 ± 0.2 ± 0.3
以切削加工來通孔
一.關於鎂合金壓鑄件成品設計建議
溢流井 溢流井
滑塊 滑塊
L
滑塊
L
L
陰影區域 未充填
湯口
陰影區域 未充填
湯口
附圖( 附圖(二)
一.關於鎂合金壓鑄件成品設計建議
部位 小pin 外圓角 內圓角 原因
小Pin易折斷。 1.外圓角不足易踫傷. 2.模具易龜裂. 參考附圖(四) 內圓角不足易發生制品龜 裂,及應力集中。 參考附圖(四)。
± 0.05mm
2~3um 0.03~0.1mm 一次完成品 50~70um 二次上塗(重工一次) 70~80um 三次上塗(重工二次) 80~100um 一次完成品 60~80um 二次上塗(重工一次) 80~100um 三次上塗(重工二次) 100~120um 厚0.4~0.6mm(視Rib高度5~10mm) 5‰~5.5‰
镁合金压铸模具规划PPT教学课件
頂 出 排 氣 溢 料 井
模 溫 油 路 配 置
導 銷 模 座 大 小
模座及配件 市購品發包
客戶 出圖
A
會同客戶、業務人員 壓鑄人員、模具設計 治具設計方案討論
成品圖 3D構圖
倒勾尺寸 脫模角檢查
模仁圖 O.K 模具圖 3D拆圖 2D繪圖
圖面 OK
檢討
.
N.G
N.G
模仁素材 水孔攻牙
模仁CAM 程式製作
生產
操作規範 檢驗規範
模具移交記錄表
製程中檢、出貨檢查表 自主檢查表
2
XXXX 股 份 有 限 公 司
鎂合金壓鑄模具作業流程
入 料 方 式 位 置
模加 分滑合 穴工 模塊金 數位 毛倒公 目置 邊勾差 排方 位處縮 列式 置理水
肉月外 厚產觀 脫量形 模總狀 角產品 度量質
心 型 大 小 位 置
澆 口 流 道 料 管
試模 FAI
會議記錄
成品圖 模具設計流程圖
模具製作組立圖 (檢、治具)驗收
成品圖
協力廠提供製作規範
樣品製作進度表 托外加工單 樣品驗收單
模具設計進度表 模具設計圖面 模具結構圖 模具材料規範書 模具製作進度表 模具保養卡
模具托外製作合約書 模具驗收報告
試模報告 機台條件設定表
FAI 表
模具移交 品質規劃
電極CAM 程式製作
模仁CNC 銑床粗加工
淬火 熱處理
N.G
N.G
模仁CNC 銑床細加工
O.K 放電 檢驗 線割
加工
檢驗
O.K 整模 組模
試模
O.K
O.K
刻字
回火氮化 熱處理
量產Biblioteka 2020/12/10N.G
- 1、下载文档前请自行甄别文档内容的完整性,平台不提供额外的编辑、内容补充、找答案等附加服务。
- 2、"仅部分预览"的文档,不可在线预览部分如存在完整性等问题,可反馈申请退款(可完整预览的文档不适用该条件!)。
- 3、如文档侵犯您的权益,请联系客服反馈,我们会尽快为您处理(人工客服工作时间:9:00-18:30)。
± 0.35 ± 0.08
重要尺寸时的许容差
尺寸A的长度
锌合金 铝合金 镁合金 铜合金
25mm以下基准公差 ± 0.08 ± 0.1
± 0.1
A的长度 超过 25mm
25~300m
m每25mm ± 0.025
增加公差
300mm以
上每25mm ± 0.25
增加公差
± 0.04 ±0.025
± 0.04 ± 0.025
不好的案例 好的案例
二. 设计注意事项
不好的案例
好的案例
Rib
3.在选择壁厚时,应考虑压铸的铸造 简便性,且有一定的刚度和强度,为了 防止部分变形,增强强度,利于熔汤流 动可增加骨架.
4.为了节省原料,在有孔和凹进去 的部位将无用的场合减肉.需同时 考虑模具增加的费用,但最终要降 低总体的费用.
不好的案例
A
不重要尺寸时的许容差
尺寸A的长度
锌合金 铝合金 镁合金 铜合金
25mm以下基准公差 ±0.25
A的长 度超过 25mm
25~300m
m每25mm ± 0.04
增加公差
300mm以
上每25mm ± 0.025
增加公差
± 0.25 ± 0.05 ± 0.025
± 0.25 ±
± 0.05
± 0.025
三. 常见设计不良与改善建议
部位
常见不良与原因
建议
通孔
不要连续集中的通孔,制品散 热应考虑流动性及模具强度. 参考附图(二)。
1.以公模铺肉方式,再以机加 铣平。
2.后工程冲压成形。
滑块成 形 滑块易进毛边,且影响设置 Gate与Overflow的空间。
制品设计上能避免尽量避免 或以机加对应。
顶针
二. 设计注意事项
不好的案例
好的案例
好的案例
5.细中子销避让性好,但易弯曲, 需定期更换,在压铸加工小孔时, 采用细中子销不如一般情况下经 济划算.
顶针
6.顶针是用于将铸品从模具 处顶出而设 置的,它的配置应防止制品变形,在外观上 机能上应将其放在不碍事的适当位置上 且设置适当的顶针数.
二. 设计注意事项
一次完成品
60~80um
二次上涂(重工一次) 80~100um
三次上涂(重工二次) 100~120um
厚0.4~0.6mm(视Rib高度5~10mm)
5‰~5.5‰
2.制品厚度标准
正面 0.02~0.04
一. 通用设计标准
侧面0.02~0.04
t
T
R
R
R R
不均一的肉厚
一. 通用设计标准
2.制品厚度标准
镁合金
铜合金
一. 通用设计标准
1.3 滑块成形上的尺寸公差
A
A
滑块成形因锁模力分力的关系, 更容易造成滑块成形时后退或尺 寸不稳。 其公差如下:
型分割面
压铸的投影面积 65CM2以下 65~130CM2
130~320CM2 320~650CM2
锌合金
铝合金
镁合金
铜合金
注:此处的投影面积指的是滑块上成品部投影面积,而且此处的公差必须要符合A 项的一般形状公差。
太厚时外观易缩陷.
Boss
脱模角不足,易粘模, 太粗时,外观易缩陷。
肉厚
太薄时,增加铸造及后工程 的加工难度。
建议
0.6 3 ~5
R0.5
10以下
M2
R03.5 ~5
上盖 下盖
A4 0.8
0.9
A4 0.9~1.1 1.0~1.2
A4 1.0~1.2 1.1~1.3
三. 常见设计不良与改善建议
部位
常见不良与原因
建议
小pin
小Pin易折断。
尽可能不要设置太细太长的成形 Pin,若有,则有补强肋比较好。 参考附图(三)
外圆角
1.外圆角不足易踫伤. 2.模具易龟裂. 参考附图(三)
至少R0.3以上
内圆角
内圆角不足易发生制品龟裂, 及应力集中。 参考附图(三)。
至少0.3以上, 以R0.5~R1最佳。
镁合金压铸件设计指南
一. 通用设计标准 1.公差标准 1.1 一般形状公差 1.2 位于分模面上的尺寸公差 1.3 滑块成形上的尺寸公差 2.制品厚度标准 二.设计注意事项 三.常见设计不良与改善建议
内容目录
1.公差标准 1.1 一般形状公差
一. 通用设计标准
A
A的尺寸,会因其长度来定其尺寸公差如下表:
± 0.18 ± 0.05
1.2 位于分模面上的尺寸公差
一. 通用设计标准
A
分模面上的直角方向因涨模因素, 公母模分开成形的尺寸,较易变 化,其与制品投影面积成正比关 系。
型分割面
压铸的投影面积 320CM2以下 320~650CM2
650~1300CM2 1300~2000CM2
锌合金
铝合金 0.3
1.Boss上的顶针会影响组装; 顶针迹以凸0,凹0.15为基 2.顶针迹高度可能影响干涉. 准。
三. 常见设计不良与改善建议
部位
常见不良与原因
建议
尖角
因为易发生充填不良,组织不 致密,一踫就崩缺。参考附图 (五)。
特别是外尖角,宜应避免。
拔模角 拔模角不足易生粘模及拉模, 造成外观凹陷。
参考拔模角规范原则:能大 尽量大。
t
脱模角
3°~5°
H R T
H(mm) 1~4 4~10 10~20 20~25
t(mm) 0.4T 0.5T 0.7T 0.8T
R=0.5t
最小肉厚(Rib)
二. 设计注意事项
不好的案例
R
好的案例
R
不好的案例 好的案例
1.为了避免铸件伤着模具, 所有内外侧尖角都应适当 倒圆角.
2.尽可能使壁厚均一,在需要对 壁厚进行改变的部分,为避免应 力集中而壁厚徐徐改变.
不好的案例
好的案例
undercut
7.在产品设计时应考虑成品去毛 边,好的设计应使毛边容易去除.
8.可动中子无法除去的咬边应尽量避免, 因形状而使用置中子,破坏性中子等特殊 方法时,非不能充分补偿其花费不应使用.
不足易造成粘模;
Rib
太细时成形不良;
2.制品厚度标准
项目 局部最小成形肉厚
机加最高精度 化成膜厚 外观研磨量
涂装膜厚(液体)
涂装膜厚(粉体)
局部最细的Rib 缩水率
一. 通用设计标准
内容 0.4mm(视位置及面积大小)
2~3um
0.03~0.1mm
一次完成品
50~70um
二次上涂(重工一次) 70~80um
三次上涂(重工二次) 80~100um
成形孔( 太深的盲孔易产生模具PIN折
盲孔)
断及脱模不良。
避免不规则形状太深的盲孔, 若无可避免时,则拔模角能大 尽量大
三. 常见设计不良与改善建议
部位
常见不良与原因
建议
Gate
产品应提供足够进浇的空 间.
能设置Gate的地方,有多少算 多少,能多尽量多。
Overflow
产品应提供足够的 Overflow空间,特别注意 滑块的配置。