生产现场改善案例分析1.doc
现场改善案例[1]
![现场改善案例[1]](https://img.taocdn.com/s3/m/725adedb1ed9ad51f11df22f.png)
现场改善案例[1]
•仓库通道照明灯的改善
•改善前为 双排照明 灯,此灯仅 作通道照 明,对亮度 要求不高.
•改善后为 单排的照明 灯,照明灯 布置在通道 的中间,亮度 完全符合照 明要求.
•每年节省的电费=改善前通道一年的照明费用 -改善后通道一年的照明费用
•
=2742-1566=1176元人民币
•改善前,本体加工完,取下 时太古水会淋湿地面.
PPT文档演模板
•改善后,上料 口宽阔,上下料 很方便,动作协 调. •改善后,先转 运30件至放料 槽,.平均每天减 少弯腰动作452 次,减少手臂运 动距离300米.
•改善后,取本体时,太古水滴到上料 槽里,回流到机体里,不會淋湿地面.
现场改善案例[1]
•改善前, 六路机1 人操作, 钻铣床1 人操作.
PPT文档演模板
•改善后, 装夹,取放 手工完成, 进刀,工件 旋转机器 自动运行.
•改善后, 六路机,钻 铣床由1人 操作 .
现场改善案例[1]
•试水吹铜屑合并
•改善前,试 水之后由拖车 搬运50m到机 动区,然后由 一名作业员手 工吹铜屑.
•自动吹铜 •屑装置.
•
=4368元人民币。
•2.减少因碰伤不良品过多而影响出货交期的次数
•3.减少不良品管理时间
PPT文档演模板
现场改善案例[1]
3rew
演讲完毕,谢谢听讲!Байду номын сангаас
再见,see you again
PPT文档演模板
2020/11/23
现场改善案例[1]
•双手可同 时擦拭
PPT文档演模板
现场改善案例[1]
•把手装配的改善
•改善前
精益现场改善案例

精益现场改善案例
精益现场改善是一种基于精益生产理念的改善方法,旨在通过减小浪费、提高生产效率和品质,从而提高企业的竞争力。
下面是一个关于如何精益现场改善的案例:
某汽车零部件制造公司的生产线在生产过程中出现了很多浪费,如零部件运输过程中长时间的等待、物料的过度处理、无价值的运动等。
这些问题导致了生产效率低下、品质不稳定和成本增加。
为了解决这些问题,该公司采取了精益现场改善的方法。
首先,该公司进行了价值流分析,明确了产品从原材料到最终成品的生产流程,并找出了其中的浪费。
他们发现,运输、等待和处理环节占据了大部分的时间和资源,因此决定从这些环节入手进行改善。
接下来,他们采用了一系列的精益工具和方法,如Kanban系统、5S整理、单点设备保养等。
通过Kanban系统,他们建立
了一个可视化的物料运输系统,能够准确地控制物料的数量和运输时间。
通过5S整理,他们将工作区域做了优化,保持了
一定的整洁度和有序性,减少了运动浪费。
通过单点设备保养,他们定期对设备进行保养和维修,减少了因设备故障而停工的时间。
改善后,该公司的生产线的效率得到了明显提高,产品的品质也得到了保证。
运输时间和等待时间明显减少,减少了人员的
浪费和资源的浪费。
整个改善过程中,该公司注重对员工的培训和参与,使他们对改善目标和方法有了更好的理解并积极参与其中。
通过精益现场改善,该公司成功地解决了生产线上存在的问题,提高了生产效率和产品品质,降低了成本,提升了企业的竞争力。
生产车间改善提案案例
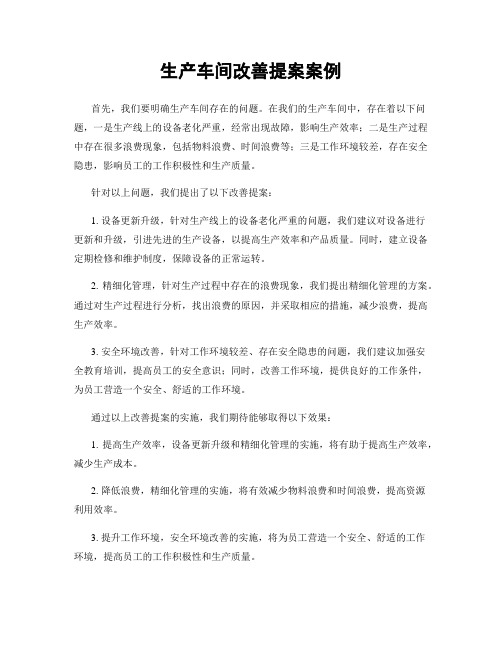
生产车间改善提案案例
首先,我们要明确生产车间存在的问题。
在我们的生产车间中,存在着以下问题,一是生产线上的设备老化严重,经常出现故障,影响生产效率;二是生产过程中存在很多浪费现象,包括物料浪费、时间浪费等;三是工作环境较差,存在安全隐患,影响员工的工作积极性和生产质量。
针对以上问题,我们提出了以下改善提案:
1. 设备更新升级,针对生产线上的设备老化严重的问题,我们建议对设备进行
更新和升级,引进先进的生产设备,以提高生产效率和产品质量。
同时,建立设备定期检修和维护制度,保障设备的正常运转。
2. 精细化管理,针对生产过程中存在的浪费现象,我们提出精细化管理的方案。
通过对生产过程进行分析,找出浪费的原因,并采取相应的措施,减少浪费,提高生产效率。
3. 安全环境改善,针对工作环境较差、存在安全隐患的问题,我们建议加强安
全教育培训,提高员工的安全意识;同时,改善工作环境,提供良好的工作条件,为员工营造一个安全、舒适的工作环境。
通过以上改善提案的实施,我们期待能够取得以下效果:
1. 提高生产效率,设备更新升级和精细化管理的实施,将有助于提高生产效率,减少生产成本。
2. 降低浪费,精细化管理的实施,将有效减少物料浪费和时间浪费,提高资源
利用效率。
3. 提升工作环境,安全环境改善的实施,将为员工营造一个安全、舒适的工作
环境,提高员工的工作积极性和生产质量。
总的来说,生产车间的改善提案是一个系统工程,需要全员参与,需要不断的改进和完善。
我们相信,通过我们的努力,生产车间的改善将会取得良好的效果,为企业的持续发展提供有力支持。
精益生产现场改善培训案例

精益生产现场改善培训案例近年来,精益生产成为了企业提高效率和降低成本的重要手段。
为了帮助员工更好地理解和应用精益生产的原则和工具,某公司决定开展精益生产现场改善培训。
以下是培训中的一些案例,展示了精益生产在实际生产现场中的应用。
1. 5S整理工作站在一家制造公司的生产线上,工作人员经常因为工具和物料摆放混乱而浪费时间。
通过培训,员工学习了5S整理原则,并开始整理工作站。
他们将工具、物料和文件按照使用频率和使用顺序进行了布置,使得操作更加流畅和高效。
2. 平衡生产线在一家汽车装配厂,生产线上的工作站之间存在明显的瓶颈,导致生产效率低下。
通过培训,员工学习了平衡生产线的方法,重新安排了工作站的任务分配,使得生产线上的工作负载更加均衡,提高了整体生产效率。
3. 精益布局设计一家仓库经常出现货物堆积、拣选错误等问题,影响了物流运转的效率。
通过培训,仓库管理人员学习了精益布局设计的原则,并重新规划了货物存放和拣选区域。
优化后的布局使得货物的流动更加顺畅,减少了物料处理时间和错误率。
4. 消除浪费在一家食品加工厂,员工经常因为物料不足、工具失效等原因停止工作,造成了生产线的停滞和浪费。
通过培训,员工学习了消除浪费的方法,如及时补充物料、定期检修和维护工具等。
这些措施使得生产线的运转更加稳定,减少了停机时间和浪费。
5. 持续改进一家电子产品制造公司发现产品的良品率低,经常出现质量问题。
通过培训,员工学习了持续改进的方法,如设立质量检查点、建立问题解决小组等。
员工积极参与改进活动,通过不断的问题分析和改进措施,最终提高了产品的质量和良品率。
6. 价值流映射在一家纺织厂,生产线上的流程繁杂,导致生产周期长和库存积压。
通过培训,员工学习了价值流映射的方法,绘制了整个生产过程的价值流图,并找出了各个环节中的浪费和瓶颈。
根据分析结果,他们采取了相应的改进措施,缩短了生产周期和库存周转时间。
7. 一次性设备准备在一家医药公司的生产车间,设备准备时间过长,影响了生产效率。
生产车间现场改善

上海德萨离合器有限公司生产车间现场改善[摘要]生产现场是企业直接创造效益的场所,是企业所有信息的原始发源地,也是各种问题萌芽产生的场所。
生产现场管理是制造型企业管理的重要组成部分,直接影响企业的生产效率和经济效益。
只有不断地优化生产现场管理,才能实现企业的整体优化。
所以,现场管理与改善越来越受到国内外企业的重视。
本文运用5s管理,全面质量管理,布局规划等生产现场改善方法,结合在上海德萨离合器有限公司生产车间发现的现场作业环境差、物品摆放杂乱无章无标识、人员效率低、设施布置不合理等问题进行了改善。
经过研究讨论后,运用工业工程的基础理论以及对现场问题的认真分析和改善,最终达到车间环境整洁,物品摆放归类整理和标示,物流路线缩短,优化工序流程,逐步减少生产过程中的浪费,提高了生产效率,降低生产成本,保证产品产能和质量的目的。
关键词:现场改善 5s 全面质量管理布局规划Shanghai Desa clutch Co., Ltd. workshop improvement[Abstract]Production site is the enterprise directly creates benefit places, is the enterprise all information of original birthplace of problems, but also produced places. But production site management in manufacturing enterprise management is an important pare of enterprise’s production, directly affects the efficiency and economic benefit. Only by continuously optimize production site management, can achieve enterprise’s production site management, can achieve enterprise’s whole optimization. So, on-site management and improve the attention of more domestic and foreign enterprises.In this paper, with 5 s management, total quality management, improve manufacturing methods, such as layout planning, combined with production workshop, the clutch Co., LTD in Shanghai found the poor working environment, items placed desultorily logos, personnel problems such as low efficiency, facility layout is not reasonable for improvement. After discussed, using the basic theory of industrial engineering as well as to the problem of serious analysis and improvement, finally reach the workshop clean and tidy environment, items catalogued, and labeled, simplify operation action, optimize the process flow, gradually reduce the waste in the process of production, improve the production efficiency, reduce production cost, production capacity and product quality assurance purposes.Key words: the scene to improve 5 s Total quality management The layout planning前言随着改革开放的深入,中国的制造业飞速发展,但也面临着复杂变化、竞争激烈的市场坏境以及劳动力成本上升的压力。
注塑车间现场改善案例

注塑车间现场改善案例收藏一、案例背景随着我国经济的快速发展,塑料制品在各个领域的应用越来越广泛,注塑行业也得到了迅猛的发展。
然而,在注塑车间现场管理方面,许多企业仍然存在着诸多问题,如生产效率低、产品质量不稳定、员工安全隐患等。
为了提高生产效率、降低成本、保障员工安全,某注塑企业决定对车间现场进行改善。
本文将介绍该企业注塑车间现场改善的案例,以供其他企业参考。
二、现状分析1.生产效率低在生产过程中,设备故障频发,导致生产中断,影响生产进度。
此外,生产计划不合理,导致生产任务无法按时完成。
员工操作不规范,生产过程中浪费严重。
2.产品质量不稳定由于设备老化、模具磨损等原因,导致产品质量参差不齐。
缺乏有效的质量控制手段,产品质量难以保证。
3.员工安全隐患车间现场环境较差,通道不畅,易发生意外事故。
员工操作过程中,存在烫伤、机械伤害等安全隐患。
4.管理混乱生产计划、物料管理、设备维护等方面存在管理不善的问题,导致生产效率低下,成本增加。
三、改善措施1.设备升级与维护针对设备故障频发的问题,企业对现有设备进行了全面的检查和维修,对部分老旧设备进行了升级换代。
同时,加强设备日常维护,降低设备故障率。
2.优化生产计划根据市场需求和设备状况,重新制定生产计划,合理安排生产任务。
采用滚动生产计划,确保生产进度的顺利进行。
3.提高员工素质加强对员工的培训,提高员工的操作技能和质量意识。
定期举办技能竞赛,激发员工的工作积极性。
4.改善车间环境对车间现场进行整理、整顿,保持通道畅通。
设置安全警示标志,提醒员工注意安全。
定期对车间进行清洁、消毒,提高车间环境卫生。
5.加强质量控制设立质量控制岗位,对生产过程进行严格监控。
采用统计质量控制方法,对产品质量进行分析和改进。
加强与供应商的质量沟通,提高原材料质量。
6.优化管理体系建立物料管理制度,确保物料供应及时、准确。
完善设备维护制度,降低设备故障率。
加强生产现场巡查,及时发现问题并解决。
生产车间现场改善案例

生产车间现场改善案例一、背景介绍公司是一家制造业企业,主要生产汽车零部件。
生产车间是公司的核心部门之一,但长期以来存在着效率低下、质量不稳定等问题,给企业带来了严重的经济损失和声誉损害。
为了解决这些问题,公司决定对生产车间进行现场改善。
二、问题分析1. 低效率:生产车间的工作流程不够清晰,物料运输和设备调整时间过长,导致工作效率低下。
2. 不稳定的质量:产品质量不稳定,出现了许多次品和废品,给企业带来了严重的经济损失和声誉损害。
3. 安全隐患:由于设备老化和操作人员不规范等原因,生产车间存在安全隐患。
三、现场改善方案1. 优化工作流程:通过对工作流程进行优化,减少物料运输和设备调整时间。
采用“单元生产”模式,在同一区域内设置多个工作单元,并将每个单元之间的距离缩短到最小。
同时,在每个单元内设置标准化作业指导书,并对操作流程进行标准化。
2. 提高质量稳定性:通过引入“6S”管理模式,对生产车间进行整理、整顿、清洁、清理、安全和素养的全面管理。
同时,建立完善的质量控制体系,对每个生产环节进行严格的质量把关,并及时发现和解决问题。
3. 加强安全管理:对老化设备进行更新和维护,并加强操作人员的培训和考核。
同时,建立安全隐患排查机制,定期开展安全检查,并及时处理发现的问题。
四、实施效果通过以上改善方案的实施,生产车间的效率得到了显著提升。
工作流程优化后,物料运输时间缩短了50%,设备调整时间减少了30%。
同时,质量稳定性也得到了明显提高,次品率下降了70%以上。
安全管理方面也取得了很好的效果,事故率下降了50%以上。
五、总结通过现场改善方案的实施,生产车间的工作效率、产品质量和安全管理都得到了显著提升。
企业在此基础上进一步推行精益生产等管理模式,在不断提高效率和质量的同时,也为企业的可持续发展奠定了坚实的基础。
5s现场管理精益改善案例

5s现场管理精益改善案例【案例一】汽车生产线5S管理精益改善1. 背景介绍:某汽车生产厂家为了提高生产效率和品质,引入了5S现场管理精益改善方法。
2. 目标:通过实施5S现场管理精益改善,目标是降低生产线上的浪费、提升工作效率、改善工作环境,提高产品质量和客户满意度。
3. 实施步骤:(1)Seiri(整理):对生产线上的物品进行分类,清理过期和损坏的设备,并将不必要的物品移出生产区域。
例如,通过对工作台材料的整理,减少了生产线上的杂乱,提高了操作者的工作效率。
(2)Seiton(整顿):对生产线上的物品进行规划和整顿,确保物品放置有序,方便取用,减少不必要的搜索时间。
例如,对工具车的布置进行重新规划,使操作者在工作时可以更方便地使用所需工具,节约了时间。
(3)Seiso(清扫):定期清洁生产线上的设备和工作区域,确保生产环境整洁,减少污染和事故的发生。
例如,制定了定期清洁工作台的计划,操作者需要每天清理并维护工作台,提高了工作环境的整洁度。
(4)Seiketsu(清洁标准化):建立清洁标准和清洁工作的检查机制,确保清洁工作的持续性和规范性。
例如,制定了每周例行检查的计划,由专人负责检查清洁工作的落实情况,并进行记录,以便及时纠正和改进。
(5)Shitsuke(遵守):通过培训和激励措施,使员工形成遵守5S规范的习惯,将5S管理精神融入到日常工作中。
例如,开展员工培训,宣传5S管理的意义和好处,并对积极参与5S活动的员工进行奖励和表彰。
4. 改善效果:经过5S现场管理精益改善的实施,汽车生产线取得了明显的改善效果。
生产效率得到提高,生产线上的浪费现象明显减少,工作效率显著提升。
同时,生产环境整洁,设备维护得到加强,产品质量得到改善,客户满意度提高。
5. 总结:汽车生产线的5S现场管理精益改善案例表明,通过清理、整顿、清扫、清洁标准化和遵守5S规范,可以有效提高生产效率,降低浪费,改善工作环境,提高产品质量和客户满意度。
- 1、下载文档前请自行甄别文档内容的完整性,平台不提供额外的编辑、内容补充、找答案等附加服务。
- 2、"仅部分预览"的文档,不可在线预览部分如存在完整性等问题,可反馈申请退款(可完整预览的文档不适用该条件!)。
- 3、如文档侵犯您的权益,请联系客服反馈,我们会尽快为您处理(人工客服工作时间:9:00-18:30)。
生产现场改善案例分析1生产现场改善案例分析经营企业并非作慈善事业,企业不赚钱是一种罪恶,企业追求的目标是创造利润。
而为达成此目标,非得有高效率的团队,高品质的产品,低成本的进料。
团队成员需有:A 经营企业不是第一,第二就要关闭;B 成员要有不畏艰难,不畏缩,不达目标,不罢休之精神。
—、品质管理外部市场的竟争不外乎是品质、价格、服务三要项。
谁要主宰市场就必需要取得品质、价格、服务的绝对领先。
经历过一些公司,皆有以下问题,为了达成产值、产量目标、从而投入大批人力、工时、反而造成新进人员低品质,多任务时,低效率。
从品质管理来看:从品质管理来看:1、大量新进员工缺乏品质管制意识。
2、基层干部缺乏工作教导实务经验。
3、整体忙于目标产值追求,问题盲点即不断发生。
4、虽然问题有分析,但是落实度很差,执行力度欠缺(说话一流,文章二流,做事三流)5、人的品质待教育,生产制程要改善,产品良率须提升。
内部品质管理1、内部品质管理包函三个层面:现品,现场,现人。
(即产品的品质,过程的品质和人的品质)。
只有高素质的人在最佳过程中,从事研发生产,才可能制造出优良的产品。
2、产品品质好坏必是决定于生产过程中5M(人、机、料、法、环)尤其人的品质是决定产品品质的关键。
3、品质异常处理:要以QC 手法(层别法、查检表、管制图、散布图、鱼骨图、直方图、柏拉图)依不良因素分析,但最重要的是对矫正对策及预防措施方案之执行,一般工厂不良因素主要是人为管理,物料异常最多,而人为管理疏失往往是产品重工及客诉的最大要因。
4.、对策:以教育训练提升人的品质,并落实改善品质措施。
A:短期(立即执行)用QC 手法对问题进行探讨,认真实施对策,依循PDCA (PLAN、DO、CHECK、ACTION)时时从不同角度考量如何改善。
B:中期(有效训练措施)实施班QCC 活动(每周两小时)针对每个岗位一周以来报表反应出来的品质状况(当然最起码报表必须是真实的)让作业员对品质管理提出看法与问题,使其有参与感,进而加重其责任心,品管圈活动中可运用脑力激荡,QC 手法, 品质改善提案,QCC 竟赛等各类管理训练措施。
C:长期(积极教育训练)1、不定期或按计划全面实施职前,在职,重点,机会品质教育。
2、公司举办年度品管圈竟赛,品质征文,征图,品质标语,并品质演讲等意识教育,用来凝聚形成公司全体品质意识,从而提升全员无形中的品质观念。
3、落实ISO9000 之精神,教导全员ISO 是平时的作业规范,而并非是应用一时审查稽核,ISO 精神在公司内作横向及纵向全面展开,则公司全员皆为审查员。
二、生产管理管理是让过去的问题不再重演,想出办法并实行改善;是对将来的问题先作预测。
并作出对策方法。
万一发生了问题,要想出如何在最短的时间内,正确并能把问题发生控制在最小范围内的方法,并立即实行。
生产管理重点是品质高,成本低,交期快,即通常所说的Q C D (QUALITY COST DELIVERY DATE)无论是ISO 精神,还是PDCA 或目标管理最重要的是决定好的事一定要遵守。
生产管理要对总体生产力进行管理,总体生产力=品质良率×生产效率×设备架动率×目标达标率×周转率。
如何提升总体生产力?如何提升总体生产力?1、实施中,基层干部实务教育训练,主要内容工作教导、工作方法、工作改善、工作安全四项基础训练,(巡视并立即指导改善是最常用一种方法)2、探讨效率改善:A、制程平衡B、源头管理C、突破制程瓶颈(针对制程中的瓶颈,必须能回答以下问题:)a、问题点:什么是当前的瓶颈?c、因:应该要改变什么事情?3、设备架动率提升采用轮班制。
b、目标:要改变成什么样子?d、方案:要如何改变?4、目标达标率的完成是通过节报(每二小时)对生产计划及时追踪,修正并实施追加等以达到目标三、成本(COST)控制成本()成本是料、工、费三方面支出的总和。
如何控制成本?1、材料方面、A、采购单价:要求厂商降价,寻找新厂商。
B、技术改善:制程改善。
C、损耗管理:人为原因采用记缺点扣薪处分;制程采用要因矫正预防。
D、呆料预防要求BOM 表100%准确,设计变更依实物落实进行。
2、直接人工、A、产量提升:追求生产绩效。
B、人员调节:实施人力支持制度。
C、技术品质:实施人员多能工训练,QCC 改善活动。
3、制造费用、A、用人费用:定员定额,加班要因改善对策。
B、合理利用资。
C、事务杂费:定额预算制度。
D、能源费用:教导员工养成随手关水电的习惯。
结语:结语:身为公司一名管理人员,要时时以公司经营绩效为已任,努力为公司创造利润,伴随公司成长而成长。
生产现场管理检查制度4生产现场管理检查制度(试行)1目的1.1 督导、检查、评估生产现场管理工作的推行效果,提升现场管理的工作水平。
1.2 使各生产单位在整理、整顿、清扫、清洁、素养及安全的实施过程中,进行比对,激发现场管理工作的参与热情及主动性。
1.3 持续改善,提高员工整体素质,营造良好工作环境。
2 适用范围《生产现场管理检查制度》适用于A公司各生产单位。
3 组织3.1生产现场管理检查工作,由行政部组织,定期进行例行督导、检查工作。
3.2 生产现场检查组由行政部综合处、盾构公司生产处、截齿综合处负责人,以及相关单位分管领导组成。
(附表1《生产现场管理相关责任人名单》)3.3 行政部负责人担任组长,检查组成员全权跟进检查执行过程中的各项工作,执行专员负责现场检查工作的前期准备、纠偏记录,以及评分统计、公示结果等后续工作。
3.4 生产现场管理检查对象为各生产单位,现场管理工作的责任人主要由各生产单位的负责人或主管组成。
(附表1《生产现场管理相关责任人名单》)4 现场检查4.1 分为定期例行检查和不定期巡查两种形式,定期检查工作由检查组实施,不定期巡查工作由执行专员独立完成。
4.2 定期检查时间为每周五上午9:00进行,检查组结合《现场管理检查表》(附表2)中的检查项,对各生产单位的现场管理情况进行现场评判。
4.3 不定期巡查,由执行专员依据《现场管理巡查表》(附表3)中内容,每周一次随机对各生产单位的生产现场保持及整改等情况进行检查。
4.4 检查内容依据《现场管理检查表》规定项目进行,不合格项目在《现场管理纠正预防表》(附表4)中进行记录。
严重的不符合项,用相机拍摄,并于公告栏中进行曝光。
4.5 检查组人员不得无故缺席例行现场检查工作,如应临时工作安排不能到场检查者,应安排其他人员接替其履行本次现场管理的检查工作。
4.6 现场管理定期检查过程中,被检查生产单位的当班相关责任人应当随同检查组完成对本生产单位的现场检查与督导工作。
5 考核评分5.1 现场管理检查评分由定期检查评分和不定期巡查评分组成,满分为100分。
5.2 定期检查分值为90分,检查内容为36项,评分者根据现场情况作出“很差、较差、一般、较好和很好”的主观判断。
5.3 不定期巡查分值为10分,检查内容为4项,由执行专员结合《现场管理巡查表》,独立完成巡查工作。
5.4 评分结果:定期检查平均分与不定期巡查评分之和,乘以调整系数,所得结果为该生产单位的最后得分。
评分结果在检查组检查工作完成后2日内公示。
6 调整系数根据各单位生产条件与环境的不同,在生产现场管理中的治理难度与执行效果也有所不同,特使用“调整系数”对评分结果予以调整,以利于考评体系的可操作性。
现场管理评分调整系数表7 奖惩规定7.1 检查组依据评分结果,对各生产单位分别进行周、月、季度和年度的考核奖惩工作。
7.2 周考核:将本周检查情况、评分结果和排名在各车间宣传栏公示。
7.3 月考核:当月各生产单位每周的考核结果进行汇总后取平均分;均分排名第一者被授予“现场管理先进班组”流动红旗;均分排名最后者在各生产单位宣传栏公示。
7.4 季度考核:当月各生产单位每月的考核结果进行汇总后取平均分;1)均分排名第一者奖励200元集体奖金,用于该生产单位的现场管理工作,并在公司网站、宣传栏等宣传平台公示。
2)均分排名最后的生产单位,将给予该生产单位相关责任人50元/人的现金处罚。
7.5 年度考核:将各生产单位每季度的考核结果进行汇总后取平均分;1)均分排名第1的生产单位,奖励相关责任人500元/人的个人奖金;2)均分排名第2的生产单位,奖励相关责任人200元/人的个人奖金;3)授予获奖生产单位“现场管理优秀团队”荣誉称号,颁发奖状予以表彰,并在公司网站、宣传栏等宣传平台公示。
7.6 周考评结果于每周定期检查后2日内公示,月考评结果与当月最后一周考评结果同期公示,季度考评结果与本季度最后一次月考评结果同期公示,年度考评结果于本年度工作结束后7个工作日内公示。
7.7 各阶段考评结果上报公司行政部,行政部依据本《生产现场管理检查制度》有关条例,对各考评单位实行奖惩。
8 持续改善8.1 本《生产现场管理检查制度》在实施过程中,将根据生产管理的要求,将会适时做必要调整使之更符合生产管理规范化、制度化的要求,使现场管理工作持续改善。
8.2 本《生产现场管理检查制度》实施时间为2011年1月1日。
A公司2010年12月8日附表1 《生产现场管理相关责任人名单》附表2 《现场管理检查表》附表3 《现场管理巡查表》附表4 《纠正预防措施表》附表1生产现场管理相关责任人名单附表2现场管理检查表很差归类放置,标识准确(加工区)归类放置,标识准确(周转区)注:“√”为考评人对某生产单位现场评分项目,分别作出的主观判断与评价。