中频炉设计方案
中频炉设计理念
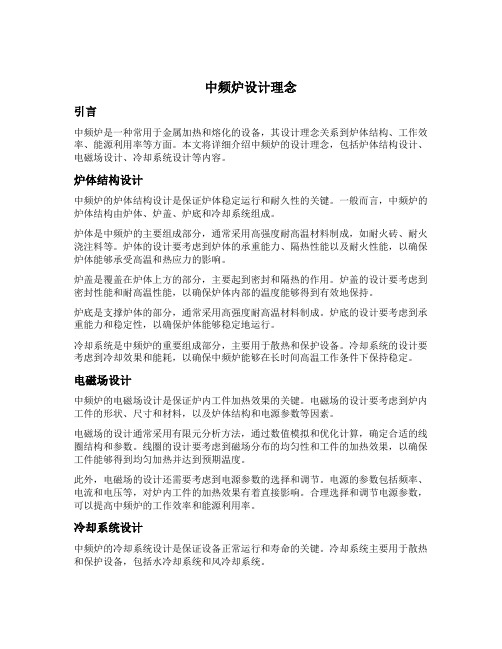
中频炉设计理念引言中频炉是一种常用于金属加热和熔化的设备,其设计理念关系到炉体结构、工作效率、能源利用率等方面。
本文将详细介绍中频炉的设计理念,包括炉体结构设计、电磁场设计、冷却系统设计等内容。
炉体结构设计中频炉的炉体结构设计是保证炉体稳定运行和耐久性的关键。
一般而言,中频炉的炉体结构由炉体、炉盖、炉底和冷却系统组成。
炉体是中频炉的主要组成部分,通常采用高强度耐高温材料制成,如耐火砖、耐火浇注料等。
炉体的设计要考虑到炉体的承重能力、隔热性能以及耐火性能,以确保炉体能够承受高温和热应力的影响。
炉盖是覆盖在炉体上方的部分,主要起到密封和隔热的作用。
炉盖的设计要考虑到密封性能和耐高温性能,以确保炉体内部的温度能够得到有效地保持。
炉底是支撑炉体的部分,通常采用高强度耐高温材料制成。
炉底的设计要考虑到承重能力和稳定性,以确保炉体能够稳定地运行。
冷却系统是中频炉的重要组成部分,主要用于散热和保护设备。
冷却系统的设计要考虑到冷却效果和能耗,以确保中频炉能够在长时间高温工作条件下保持稳定。
电磁场设计中频炉的电磁场设计是保证炉内工件加热效果的关键。
电磁场的设计要考虑到炉内工件的形状、尺寸和材料,以及炉体结构和电源参数等因素。
电磁场的设计通常采用有限元分析方法,通过数值模拟和优化计算,确定合适的线圈结构和参数。
线圈的设计要考虑到磁场分布的均匀性和工件的加热效果,以确保工件能够得到均匀加热并达到预期温度。
此外,电磁场的设计还需要考虑到电源参数的选择和调节。
电源的参数包括频率、电流和电压等,对炉内工件的加热效果有着直接影响。
合理选择和调节电源参数,可以提高中频炉的工作效率和能源利用率。
冷却系统设计中频炉的冷却系统设计是保证设备正常运行和寿命的关键。
冷却系统主要用于散热和保护设备,包括水冷却系统和风冷却系统。
水冷却系统是中频炉常用的冷却方式,通过冷却水对设备进行散热。
水冷却系统的设计要考虑到冷却水的流量、温度和压力等参数,以及冷却设备的结构和材料。
中频感应加热炉毕业设计

中频感应加热炉毕业设计引言中频感应加热炉是一种常见的工业加热设备,广泛应用于金属材料的加热、熔化和热处理等领域。
在本毕业设计中,我们将设计并实现一个中频感应加热炉,用于对金属材料进行加热实验。
本文将详细介绍设计方案和实施步骤。
设计方案系统结构中频感应加热炉由主机、感应线圈、冷却系统和控制系统等部分组成。
主机负责产生中频电流,通过感应线圈将能量传输到被加热物体上。
控制系统用于控制加热过程的参数和监测系统状态。
冷却系统用于保持设备工作时的温度,避免过热。
设计要点•输出功率调节:设计中频感应加热炉时需要考虑到不同材料的加热需求。
因此,要设计一种能够调节输出功率的机制,以便根据需要对被加热物体进行目标加热。
•温度控制系统:为了确保被加热物体加热至预定温度并保持稳定,需设计一个有效的温度控制系统。
可以采用PID控制算法对加热过程进行精确控制。
•安全保护机制:为了保证操作人员和设备的安全,需要设计多种安全保护机制,如过流保护、过热保护和过载保护等。
•易操作性:考虑到用户的使用体验,设计中频感应加热炉时应尽量简化操作界面,提供直观的操作指导和提示信息。
实施步骤1.梳理需求:明确实验要求和目标,确定所需材料和加热温度范围等。
2.选型和采购:根据需求和预算,选择适合的主机、感应线圈、冷却系统和控制系统等设备,并进行采购。
3.组装设备:根据设备说明书,按照标准流程组装设备,并进行连接和布线。
4.编写控制程序:根据需求,编写中频感应加热炉的控制程序。
该程序应具备调节功率、温度控制和安全保护等功能。
5.调试和测试:对设备进行调试和测试,通过加热实验验证设备功能和效果。
6.优化和改进:根据测试结果,对设备进行优化和改进,提高工作效率和加热质量。
结论通过本毕业设计项目,我们成功设计并实现了一个中频感应加热炉,用于金属材料的加热实验。
该设备具有输出功率调节、温度控制、安全保护和易操作性等特点。
在未来的工业应用中,该设备可以广泛应用于金属材料的加热和热处理领域,具备一定的商业价值。
中频炉冶炼工艺设计全

中频炉冶炼工艺设计全中频炉是一种常用的金属炉冶设备,具有操作灵活、能耗低、效率高等优点。
下面是中频炉冶炼工艺设计的详细步骤。
1.炉型选择:根据炼制金属的特性和要求,选择适合的炉型。
常见的中频炉有感应加热炉、电阻加热炉等。
2.容量确定:根据工艺要求和产能需求,确定中频炉的容量。
一般情况下,中频炉的容量范围为几十千克到几百吨不等。
3.工艺流程设计:制定炼炉的工艺流程。
包括原料准备、炉料配比、炉前处理、炉内炼炉、渣液处理等环节。
4.原料准备:选择合适的原料,并进行分类、计量、清洗等工序。
根据炼金属的需要,合理配制炉料。
5.炉料配比:根据工艺要求,确定炉料的配比。
炉料的配比应考虑到各种元素的含量及其比例,以保证炉内反应的顺利进行。
6.炉前处理:为了提高炉内炼炉的效果和减少能源消耗,常常需要进行炉前处理。
例如,对于含有脏杂质的废旧金属,可以进行热处理、除杂等工艺,以减少炉内渣液的产生。
7.炉内炼炉:根据工艺流程,在中频炉中进行炼炉操作。
根据金属的特性,调整加热功率、温度、保温时间等参数,使金属熔化、相互分离、净化等反应得以进行。
8.喷吹工艺:对于一些需要氧化的金属,可采用喷吹工艺。
通过将氧化剂喷吹到炉内,使金属与氧化剂发生反应,以氧化金属和去除有害元素。
9.渣液处理:炼炉过程中产生的渣液需要进行处理。
常见的渣液处理方式有渣否分离、净化、去除有害元素等。
10.产品处理:炼炉结束后,得到的金属产品需要进行后续处理。
例如,对于铸造产品,需要进行铸造成型、冷却、清洗等工序。
11.能源利用:中频炉的设计应充分考虑能源的利用效率。
例如,可以采用余热回收技术,将炉体散热的余热用于预热原料或供热供暖。
12.环保措施:设计中频炉时,应注重环保方面的考虑。
例如,通过合理的排放控制、废气处理等手段,减少对环境的影响。
综上所述,中频炉冶炼工艺设计的步骤包括炉型选择、容量确定、工艺流程设计、原料准备、炉料配比、炉前处理、炉内炼炉、喷吹工艺、渣液处理、产品处理、能源利用和环保措施。
中频感应加热炉技术方案设计

500kw×2中频感应加热炉技术方案一、加热工艺及技术要求1.1用途:与2500吨压力机配套,锻造汽车前桥的坯料加热;1.2 工件材质:中碳钢1.3 加热温度:1250℃1.4 温差要求:径向温差≤60℃,首尾温差≤80℃;1.5 加热部位:整体加热1.6 典型坯料尺寸:【注】:应厂方要求,按2台500kw组合加热方式。
二、总体设计方案概述:2.1、功率:中频加热炉2台总功率1000KW,标称频率500hz。
2.2、配置感应器型号与结构:GTR-190×2500,基本参数如下:2.3、炉子结构:按照厂方要求,炉体做成双工位,每一个工位500kw,组合加热,它们之间错开一个时间节拍,互补进料,交替出料,组合加热时的节拍180秒,单独运行时的节拍为360秒。
2.4、备料方式:采用地面提升机将坯料提升到储料架上。
储料台一次可储存4颗料;2.5、进料方式:采用气缸推料,步进式进料方法;2.6、出料方式:出料端采用辊道接送坯料;2.7、温度检测与分选:出炉口装有红外测温仪,对出炉坯料超高温、超低温、正常温度进行三分选2.8、整体结构如图示:三、供电变压器:3.1、为二台中频炉供电的变压器必须是专用整流变压器,这是因为大功率变频器会对电网产生谐波污染,因为整流变压器采用Y/△接法,阀侧Y-12和△-11的线电压相位相差30°使二台中频电源的Y组整流和△组整流电压纹波也有30°相位差,两组六相脉动波合成12相脉动波。
这两个电流波形在变压器网侧绕组当中的合成电流波形能有效抑制5次、7次谐波的产生。
3.2、整流变压器与二台中频电源的接法图示:3.3 、ZS-1250-10/0.38整流变压器技术参数:●额定容量:1250KVA;网侧额定电压:10±5%(KV)3Φ/ 50HZ●阀侧Ⅰ额定容量:625(KVA)●阀侧Ⅰ额定输出电压:380(V)●阀侧Ⅱ额定容量: 625(KVA)●阀侧Ⅱ额定输出电压:380 (V)●连接组别:D do yn11;●阻抗压降:Uk=7%●网侧、阀侧之间加屏蔽,减少谐波对网侧的冲击。
中频炉设计方案范文
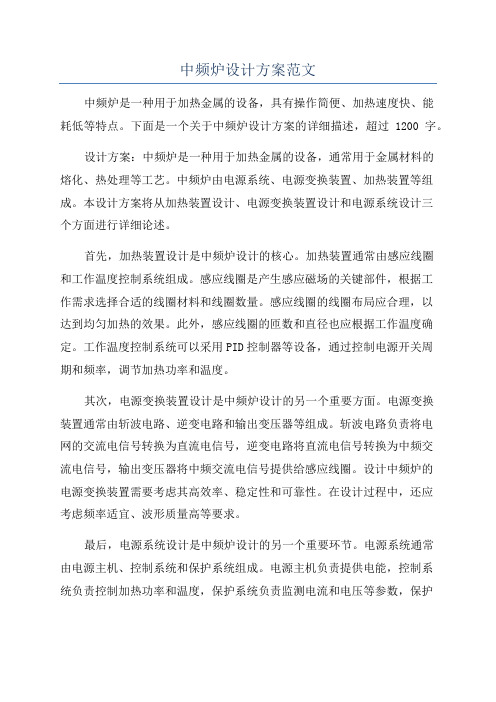
中频炉设计方案范文中频炉是一种用于加热金属的设备,具有操作简便、加热速度快、能耗低等特点。
下面是一个关于中频炉设计方案的详细描述,超过1200字。
设计方案:中频炉是一种用于加热金属的设备,通常用于金属材料的熔化、热处理等工艺。
中频炉由电源系统、电源变换装置、加热装置等组成。
本设计方案将从加热装置设计、电源变换装置设计和电源系统设计三个方面进行详细论述。
首先,加热装置设计是中频炉设计的核心。
加热装置通常由感应线圈和工作温度控制系统组成。
感应线圈是产生感应磁场的关键部件,根据工作需求选择合适的线圈材料和线圈数量。
感应线圈的线圈布局应合理,以达到均匀加热的效果。
此外,感应线圈的匝数和直径也应根据工作温度确定。
工作温度控制系统可以采用PID控制器等设备,通过控制电源开关周期和频率,调节加热功率和温度。
其次,电源变换装置设计是中频炉设计的另一个重要方面。
电源变换装置通常由斩波电路、逆变电路和输出变压器等组成。
斩波电路负责将电网的交流电信号转换为直流电信号,逆变电路将直流电信号转换为中频交流电信号,输出变压器将中频交流电信号提供给感应线圈。
设计中频炉的电源变换装置需要考虑其高效率、稳定性和可靠性。
在设计过程中,还应考虑频率适宜、波形质量高等要求。
最后,电源系统设计是中频炉设计的另一个重要环节。
电源系统通常由电源主机、控制系统和保护系统组成。
电源主机负责提供电能,控制系统负责控制加热功率和温度,保护系统负责监测电流和电压等参数,保护设备的正常运行。
在电源系统设计中,应注意电源的稳定性和可靠性。
此外,还需要考虑负载变化时的性能,以及响应速度和效率等因素。
综上所述,中频炉设计方案主要包括加热装置设计、电源变换装置设计和电源系统设计。
加热装置设计需要考虑线圈材料、线圈布局和工作温度控制系统等因素。
电源变换装置设计需要注意其高效率、稳定性和可靠性。
电源系统设计需要考虑电源的稳定性、负载变化时性能的变化和保护系统等因素。
中频电炉解决方案
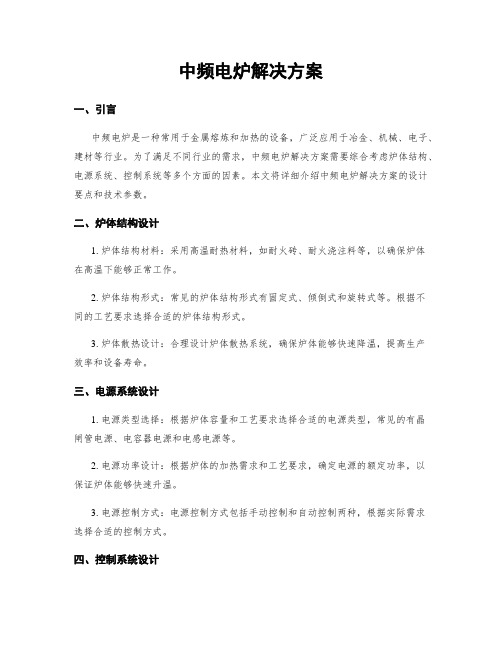
中频电炉解决方案一、引言中频电炉是一种常用于金属熔炼和加热的设备,广泛应用于冶金、机械、电子、建材等行业。
为了满足不同行业的需求,中频电炉解决方案需要综合考虑炉体结构、电源系统、控制系统等多个方面的因素。
本文将详细介绍中频电炉解决方案的设计要点和技术参数。
二、炉体结构设计1. 炉体结构材料:采用高温耐热材料,如耐火砖、耐火浇注料等,以确保炉体在高温下能够正常工作。
2. 炉体结构形式:常见的炉体结构形式有固定式、倾倒式和旋转式等。
根据不同的工艺要求选择合适的炉体结构形式。
3. 炉体散热设计:合理设计炉体散热系统,确保炉体能够快速降温,提高生产效率和设备寿命。
三、电源系统设计1. 电源类型选择:根据炉体容量和工艺要求选择合适的电源类型,常见的有晶闸管电源、电容器电源和电感电源等。
2. 电源功率设计:根据炉体的加热需求和工艺要求,确定电源的额定功率,以保证炉体能够快速升温。
3. 电源控制方式:电源控制方式包括手动控制和自动控制两种,根据实际需求选择合适的控制方式。
四、控制系统设计1. 温度控制:采用PID控制算法,根据炉体的温度变化调整电源输出功率,以保持炉体温度稳定。
2. 保护控制:设置过温保护、过流保护、漏电保护等功能,确保设备运行安全可靠。
3. 自动化控制:可根据工艺要求实现自动化控制,如定时启动、定时停止、温度曲线控制等功能。
五、安全性设计1. 设备接地:确保设备接地良好,减少漏电风险。
2. 防护罩设计:对炉体周围设置防护罩,防止操作人员误触热源,提高工作安全性。
3. 紧急停机装置:设置紧急停机按钮,一旦发生紧急情况,可立即切断电源,确保操作人员的安全。
六、技术参数1. 炉体容量:根据工艺要求确定炉体容量,常见的有100kg、500kg、1000kg 等。
2. 电源功率:根据炉体容量和工艺要求确定电源功率,常见的有100kW、500kW、1000kW等。
3. 控制精度:温度控制精度一般在±5℃以内,根据具体工艺要求可调整。
中频电炉解决方案
中频电炉解决方案一、背景介绍中频电炉是一种用于金属加热和熔化的设备,广泛应用于冶金、铸造、锻造、热处理等行业。
为了提高生产效率和能源利用率,中频电炉解决方案应运而生。
本文将详细介绍中频电炉解决方案的设计原理、技术参数、优势以及应用案例。
二、设计原理中频电炉解决方案基于电磁感应加热原理,通过高频电源将电能转换为高频电磁场,进而将金属材料加热至所需温度。
具体工作原理如下:1. 高频电源:中频电炉解决方案采用高频电源作为能源供应,高频电源输出的电能经过整流和逆变,转换为高频交流电。
2. 感应线圈:高频交流电经过感应线圈产生高频电磁场,金属材料放置在感应线圈内,受到高频电磁场的感应作用。
3. 电磁感应加热:金属材料中的电导体产生涡流,涡流在电阻中发生热量损耗,从而使金属材料加热。
4. 温度控制系统:中频电炉解决方案配备温度控制系统,通过传感器实时监测金属材料的温度,并根据设定的温度范围进行自动控制。
三、技术参数1. 功率范围:中频电炉解决方案可根据不同的应用需求提供不同功率的设备,通常功率范围从10千瓦到100兆瓦不等。
2. 频率范围:中频电炉解决方案的频率通常在1千赫兹到10兆赫兹之间,可以根据具体需求进行调节。
3. 加热效率:中频电炉解决方案具有较高的加热效率,能够实现快速加热和高温熔炼,加热效率通常在80%以上。
4. 控温精度:中频电炉解决方案配备先进的温度控制系统,控温精度可达±1℃,能够满足不同工艺要求。
5. 自动化程度:中频电炉解决方案可实现全自动化操作,配备PLC控制系统和触摸屏界面,操作简便,提高生产效率。
四、优势中频电炉解决方案相比传统燃气炉、电阻炉等加热设备具有以下优势:1. 高效节能:中频电炉解决方案采用电磁感应加热,加热效率高,能耗低,节约能源。
2. 温度控制精度高:中频电炉解决方案配备先进的温度控制系统,能够实现精确的温度控制,提高产品质量。
3. 加热速度快:中频电炉解决方案具有快速加热的特点,能够提高生产效率,缩短生产周期。
钢壳中频炉技术方案
钢壳中频感应熔炼设备制造项目设计技术方案钢壳中频炉改造技术方案一、项目改造范围及目标1.1改造要求应公司的要求,需对现有的两台铝壳中频熔炼炉体进行升级改造,现有铝壳炉体为2.5吨1台、3.0吨1台。
1.2改造范围及内容1.2.1将现有的两台铝壳中频炉体(2.5吨、3.0吨)拆除,根据现有铝壳中频炉体的相关参数,设计制造为钢壳中频炉体。
1.2.2变压器、中频电源柜、电容器保持不变利旧。
除尘设备主体不变利旧,对吸尘罩及旋转机构进行相应的调整改造。
设备冷却循环水只对炉体进、出水管道改造,每台中频炉安装符合安全要求的循环水系统,确保水温、水压、流量在设备允许的数值内运行及报警。
1.2.3中频炉基础重新设计,受场地的影响,两台钢壳中频炉布置不得影响安全和现场生产,在保证安全情况下,基础改动量要尽量小。
1.3改造的目标钢壳中频熔炼炉的设计、制作、安装及调试,要满足环保及安全要求,直至交付使用。
二、主要技术参数2.1钢壳3.0t中频炉主要技术参数2.2钢壳2.5t中频炉主要技术参数三、技术说明3.1技术方案本技术方案的主要设备包括: 1台3.0t钢壳中频熔炼炉体、 1台2.5t 钢壳中频熔炼炉体、1套液压倾炉传动系统(带2台钢壳炉倾动)、8条500mm2水冷电缆、2套龙卷风式除尘罩、2台炉体用不锈钢分水器、1只3.0t坩埚模和1只2.5t坩埚模及其它相关辅助工程及材料。
3.2钢壳熔炼炉无芯中频感应熔炼炉由炉壳、炉架、旋风式除尘炉盖、感应线圈、倾炉系统、水冷系统、控制系统等组成。
炉体结构由炉固定架和炉本体组成,炉固定架和炉体采用整体性钢体骨架结构。
3.2.1炉体结构炉体结构由炉固定架和炉本体组成,炉固定架和炉体采用整体性骨架结构。
如图所示:3.2.2炉本体钢结构炉壳采用优质型钢制焊接而成的鼠笼式框架结构体,窗口有可拆式盖板,框架底板采用优质厚钢板制作。
炉壳下部有炉衬顶出机构的固定支架。
炉壳内配有长方形体磁轭。
磁轭的屏蔽可以减小线圈漏磁防止炉体发热,提高电能效率,同时支撑感应圈,提高强度,在磁轭不取走情况下可以方便的拆装线圈和对线圈的维修、观察、散热。
中频电炉自动加配料系统的设计方案
中频电炉自动加配料系统的设计方案一、引言中频电炉是一种应用广泛的工业炉,用于熔化各种金属材料,广泛用于熔铁、钢、铜、铝等金属的生产过程中。
为了提高生产效率和产品质量,引入自动化配料系统是非常重要的。
二、系统需求分析1.自动化:系统能够自动完成配料过程,减少人工操作,提高生产效率。
2.准确性:系统需要具备高精度的配料能力,确保配料精度达到要求。
3.稳定性:系统需要稳定运行,能够长时间连续工作,避免因为系统故障导致生产中断。
4.可扩展性:系统需要具备可扩展性,能够适应未来生产扩大的需求。
5.安全性:系统需要具备安全性能,确保工作人员和设备的安全。
三、系统设计方案基于上述需求,设计一个中频电炉自动加配料系统,可以分为以下几个部分:1.传感器系统:通过各种传感器,如温度传感器、压力传感器等,实时监测炉内环境的变化,并将数据传输到控制系统中。
2.控制系统:控制系统接收传感器系统传来的数据,根据预设的配料方案进行计算,并控制配料系统的操作。
3.配料系统:配料系统由输送设备、称重设备和控制装置组成。
输送设备负责将配料从储存区域输送到炉下,称重设备用于精确测量配料的重量,并传输给控制装置。
4.通信系统:控制系统需要与上位机进行通信,接收生产计划、调整配料方案、传输生产数据等。
通信系统还可以与其他辅助设备进行联动,如温度控制系统、捣固设备等。
5.安全保护系统:安全保护系统用于监测和保护系统运行过程中可能出现的安全隐患,如传感器故障、设备异常等情况。
四、关键技术和设计细节1.传感器选择:选择合适的温度传感器、压力传感器等,具备高精度和长寿命特点,能够在高温、高强度的环境中正常工作。
2.控制系统设计:采用PLC(可编程逻辑控制器)进行控制,具备高稳定性和可靠性。
通过编程实现配料算法、故障检测和处理等功能。
3.配料系统设计:选择高精度的输送设备和称重设备,能够精确控制配料的重量,并具备自动校准和故障检测功能。
4.通信系统设计:采用可靠的通信协议和设备,确保与上位机的稳定通信,并能够传输大量的数据。
中频炉设计方案
中频炉烟气处理系统设计方案定稿(最终方案)一、设计依据1.本设计依据冶金工业部《重有色金属工业污染物防治》中有关规定执行。
2.废气排放执行GB9078-1996《工业炉窑大气污染物排放标准》中一级排放标准。
二、设计目标:1.烟气排放浓度<50mg/Nm32.系统除尘效率>99.8%3.投资省、结构合理、维护简便,运行费用低。
三、设计参数:正常不间断使用情况下,电炉烟气排放工艺参数:1、烟气来源:熔炼时所产生的烟气2、电炉烟气量: 2台1.5T中频炉:15000 m3/h,2台2T中频炉:20000m3/h。
四、工艺流程简介:设计依据以及改进:根据现场的实际情况,吸尘罩采用旋转高悬罩,在行车加料时能旋转至一边,不妨碍加料,吸尘罩口径为∮1300mm,离炉口高度为1000mm。
2台1.5T中频炉轮流使用(不同时使用),运行时粉尘含量比较高,吸口风速控制在3.0m/s,运行风量在15000 m3/h。
2台2T中频炉轮流使用(不同时使用),运行时候粉尘含量比较高,吸口风速控制在3.0 m/s左右,运行风量在20000 m3/h,在考虑到现场实际情况,吸罩口距离炉口在1米的高度,因气流在上升的过程中,易受侧向风干扰,吸罩口过高,则越易受侧风干扰,影响整体除尘效果。
1、方案名称:布袋除尘法2、设备选型:火星捕集器+布袋除尘器3、系统流程:(见附图)4、系统流程简介:该除尘方案采用火星捕集器+布袋除尘器除尘,避免了湿式除尘产生的二次污染。
在系统前道采用火星捕集器进行烟尘预处理,去除烟气中的火星,进过旋风除尘器去除一部分大颗粒的粉尘,余下的含有粉尘的烟气进入布袋除尘器后,进行烟尘的最后收集,达到除尘目的。
为确保使烟气温度降低至160o C左右进入布袋除尘器,结合现场实际情况,采用以下两种方法来控制烟气温度(1、火星捕集器进口安装气液雾化装置;2、火星捕集器进口安装野风阀)。
5、设备工作原理:火星捕集器:作为除尘器的主要组成部分之一火花捕集器的作用是:炉气和烟气的出口、阻挡未燃尽火花的排出和大部分烟尘的外逸保护后部袋式除尘器的滤袋。
- 1、下载文档前请自行甄别文档内容的完整性,平台不提供额外的编辑、内容补充、找答案等附加服务。
- 2、"仅部分预览"的文档,不可在线预览部分如存在完整性等问题,可反馈申请退款(可完整预览的文档不适用该条件!)。
- 3、如文档侵犯您的权益,请联系客服反馈,我们会尽快为您处理(人工客服工作时间:9:00-18:30)。
中频炉烟气处理系统
设计方案
定稿(最终方案)
一、设计依据
1.本设计依据冶金工业部《重有色金属工业污染物防治》中有关规定执行。
2.废气排放执行GB9078-1996《工业炉窑大气污染物排放标准》中一级排放标准。
二、设计目标:
1.烟气排放浓度<50mg/Nm3
2.系统除尘效率>%
3.投资省、结构合理、维护简便,运行费用低。
三、设计参数:
正常不间断使用情况下,电炉烟气排放工艺参数:
1、烟气来源:熔炼时所产生的烟气
2、电炉烟气量: 2台中频炉:15000 m3/h,
2台2T中频炉:20000m3/h。
四、工艺流程简介:设计依据以及改进:
根据现场的实际情况,吸尘罩采用旋转高悬罩,在行车加料时能旋转至一边,不妨碍加料,吸尘罩口径为∮1300mm,离炉口高度为1000mm。
2台中频炉轮流使用(不同时使用),运行时粉尘含量比较高,吸口风速控制在s,运行风量在15000 m3/h。
2台2T中频炉轮流使用(不同时使用),运行时候粉尘含量比较高,吸口风速控制在 m/s 左右,运行风量在20000 m3/h,
在考虑到现场实际情况,吸罩口距离炉口在1米的高度,因气流在上升的过程中,易受侧向风干扰,吸罩口过高,则越易受侧风干扰,影响整体除尘效果。
1、方案名称:布袋除尘法
2、设备选型:火星捕集器+布袋除尘器
3、系统流程:(见附图)
4、系统流程简介:该除尘方案采用火星捕集器+布袋除尘器除尘,避免了湿式除尘产生的二次污染。
在系统前道采用火星捕集器进行烟尘预处理,去除烟气中的火星,进过旋风除尘器去除一部分大颗粒的粉尘,余下的含有粉尘的烟气进入布袋除尘器后,进行烟尘的最后收集,达到除尘目的。
为确保使烟气温度降低至160o C左右进入布袋除尘器,结合现场实际情况,采用以下两种方法来控制烟气温度(1、火星捕集器进口安装气液雾化装置;2、火星捕集器进口安装野风阀)。
5、设备工作原理:
火星捕集器:作为除尘器的主要组成部分之一火花捕集器的作用是:炉气和烟气的出口、阻挡未燃尽火花的排出和大部分烟尘的外逸保护后部袋式除尘器的滤袋。
在处理木屑锅炉、稻壳锅炉、铝再生炉和冶炼炉等废气的袋式除尘器中,炉子中的已燃粉尘有可能随风管气流进入箱体,而使堆积在滤布上的粉尘着火,造成事故。
为防止火星进入袋式除尘器,应采取如下措施。
为防止火星进入袋式除尘器,应采取如下措施。
设置预除尘器和冷却管道。
以捕集粗粒粉尘和火星。
用这种方法太细的微粒火星不易捕集,多数情况下微粒粉尘在进入除尘器之前能够燃尽。
在预除尘器之后设置冷却管道,并控制管内流速,使之尽量低。
这是一种比较可靠的技术措施,它可使气体在管内有充分的停留时间。
?通过分析,设计在进风口即开始变径,以增大火花捕集器内部的空间,使其具有重力惯性沉降室式除尘器的效应。
重力除尘器称重力沉降室,基本结构是一个扩张室,尘粒速度在扩张室中降低到可靠重力沉降的速度,?在重力除尘器上部加上碰撞板,使气流改变方向以对尘粒附加一个向下的速度?,可提高尘粒的分离作用。
重力沉?降室中的气流速度应尽量?低一些?,一般在??m/s?改进设计后的干式火花捕集器?,内部设置百叶窗式的过滤板,起到撞板的作用,当烟气以较高气流进入与之撞?击后?,使气流改变方向对尘粒产生一个向下的速?度?,加之整个捕集器内部为一扩张室,流速降低使得大部分尘粒依其自重就沉降下来,火花捕集器就具备了重力惯性沉降室式除尘器的效应。
火花捕集器用于高温烟气中的火花颗粒捕集时,设备进出口速度一般在18~25m/s 之间;考虑粉尘的分离效果。
过滤板应有恰当的角度;设备结构设计要考虑到高温引起的设备变形。
布袋除尘器:经过冷却后的烟气切向进入布袋除尘器,大颗粒粉尘及凝聚尘粒在离心力作用下落入灰斗,微小尘粒悬浮于气体中通过气流分布装置,均匀进入过滤室中,弥散于滤袋间隙而被滤袋阻留,净化气体由主风机排出。
随着粉尘不断附着于滤袋外表面,粉尘层不断的增厚,系统阻力逐渐增加,当阻力值到达一定值时,除尘器的清灰系统发出指令开启清灰机构,高速高压的引射气流喷向滤袋,滤袋内出现瞬间正压,急剧膨胀,使滤袋外部的粉尘脱落,掉入灰斗,达到清灰目的;当滤袋阻力下降到下限时,清灰机构自动停止工作,维持除尘器的连续性工作。
6、设备参数:
两台中频炉
北边4台炉。