加氢裂化飞温事故过程分析
加氢裂化温事故处理方法探讨
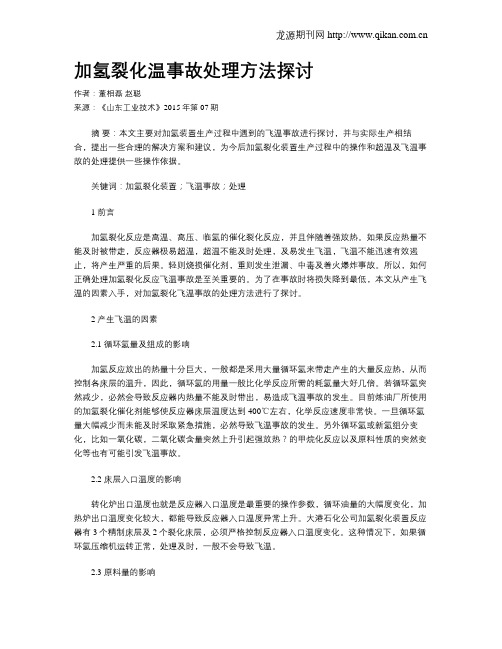
加氢裂化温事故处理方法探讨作者:董相磊赵聪来源:《山东工业技术》2015年第07期摘要:本文主要对加氢装置生产过程中遇到的飞温事故进行探讨,并与实际生产相结合,提出一些合理的解决方案和建议,为今后加氢裂化装置生产过程中的操作和超温及飞温事故的处理提供一些操作依据。
关键词:加氢裂化装置;飞温事故;处理1 前言加氢裂化反应是高温、高压、临氢的催化裂化反应,并且伴随着强放热。
如果反应热量不能及时被带走,反应器极易超温,超温不能及时处理,及易发生飞温,飞温不能迅速有效遏止,将产生严重的后果。
轻则烧损催化剂,重则发生泄漏、中毒及着火爆炸事故。
所以,如何正确处理加氢裂化反应飞温事故是至关重要的。
为了在事故时将损失降到最低,本文从产生飞温的因素入手,对加氢裂化飞温事故的处理方法进行了探讨。
2 产生飞温的因素2.1 循环氢量及组成的影响加氢反应放出的热量十分巨大,一般都是采用大量循环氢来带走产生的大量反应热,从而控制各床层的温升,因此,循环氢的用量一般比化学反应所需的耗氢量大好几倍。
若循环氢突然减少,必然会导致反应器内热量不能及时带出,易造成飞温事故的发生。
目前炼油厂所使用的加氢裂化催化剂能够使反应器床层温度达到400℃左右,化学反应速度非常快。
一旦循环氢量大幅减少而未能及时采取紧急措施,必然导致飞温事故的发生。
另外循环氢或新氢组分变化,比如一氧化碳,二氧化碳含量突然上升引起强放热?的甲烷化反应以及原料性质的突然变化等也有可能引发飞温事故。
2.2 床层入口温度的影响转化炉出口温度也就是反应器入口温度是最重要的操作参数,循环油量的大幅度变化,加热炉出口温度变化较大,都能导致反应器入口温度异常上升。
大港石化公司加氢裂化装置反应器有3个精制床层及2个裂化床层,必须严格控制反应器入口温度变化。
这种情况下,如果循环氢压缩机运转正常,处理及时,一般不会导致飞温。
2.3 原料量的影响原料量的突然减少,就会导致催化剂床层上原料油密度的下降或者不均匀分布,从而使反应热急剧的变化或者导致床层颈向温度差别较大,从而引起深度的二次加氢反应而引起飞温,先降温后降量是在原料油减少时我们尊守的原则,但反应床层上也有相当多的原料油量,如果原料减少时间较短,循环氢量没有变化的情况下,如果处理及时一般不会导致飞温。
加制氢装置安全事故案例
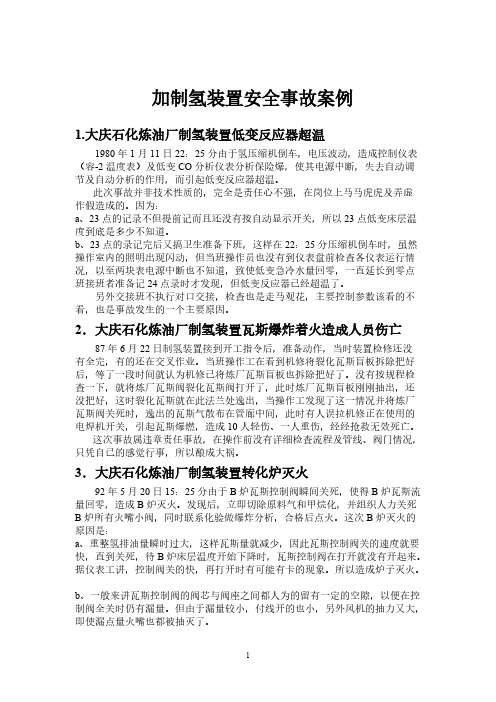
加制氢装置安全事故案例1.大庆石化炼油厂制氢装置低变反应器超温1980年1月11日22:25分由于氢压缩机倒车,电压波动,造成控制仪表(容-2温度表)及低变CO分析仪表分析保险爆,使其电源中断,失去自动调节及自动分析的作用,而引起低变反应器超温。
此次事故并非技术性质的,完全是责任心不强,在岗位上马马虎虎及弄虚作假造成的。
因为:a、23点的记录不但提前记而且还没有按自动显示开关,所以23点低变床层温度到底是多少不知道。
b、23点的录记完后又搞卫生准备下班,这样在22:25分压缩机倒车时,虽然操作室内的照明出现闪动,但当班操作员也没有到仪表盘前检查各仪表运行情况,以至两块表电源中断也不知道,致使低变急冷水量回零,一直延长到零点班接班者准备记24点录时才发现,但低变反应器已经超温了。
另外交接班不执行对口交接,检查也是走马观花,主要控制参数该看的不看,也是事故发生的一个主要原因。
2.大庆石化炼油厂制氢装置瓦斯爆炸着火造成人员伤亡87年6月22日制氢装置接到开工指令后,准备动作,当时装置检修还没有全完,有的还在交叉作业。
当班操作工在看到机修将裂化瓦斯盲板拆除把好后,等了一段时间就认为机修已将炼厂瓦斯盲板也拆除把好了。
没有按规程检查一下,就将炼厂瓦斯阀裂化瓦斯阀打开了,此时炼厂瓦斯盲板刚刚抽出,还没把好,这时裂化瓦斯就在此法兰处逸出,当操作工发现了这一情况并将炼厂瓦斯阀关死时,逸出的瓦斯气散布在管廊中间,此时有人误拉机修正在使用的电焊机开关,引起瓦斯爆燃,造成10人轻伤、一人重伤,经经抢救无效死亡。
这次事故属违章责任事故,在操作前没有详细检查流程及管线、阀门情况,只凭自己的感觉行事,所以酿成大祸。
3.大庆石化炼油厂制氢装置转化炉灭火92年5月20日15:25分由于B炉瓦斯控制阀瞬间关死,使得B炉瓦斯流量回零,造成B炉灭火。
发现后,立即切除原料气和甲烷化,并组织人力关死B炉所有火嘴小阀,同时联系化验做爆炸分析,合格后点火。
加氢裂化装置典型事故处理(二)
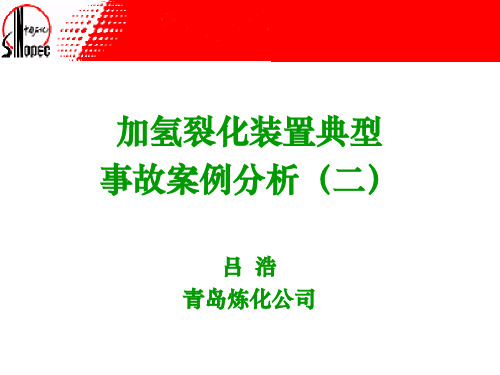
停电导致裂化反应器飞温
u 机组在1989r/min下运转15分钟后,裂化反应器四床 层TI1143温度开始上升,24:05最高达到470℃, 在场厂领导、技术部门、车间协商后决定立即启用 2.1MPa/min进行卸压,同时引入氮气进行置换。 u 停电前裂化反应温度CAT2为372℃,停电后22:17 裂化反应温度CAT2上升到391.7℃。但在24.:10循 氢机停机后,裂化反应器温度快速上升,停电前裂 化反应器四床中部温度TI1143B为373℃,24:00温 度为465℃,到24:58温度快速上升到了882℃。在 中压氮气引入反应系统后反应系统压力充至3.0MPa 后通过泄压阀进行泄压置换。
开工过程中飞温事故
三、事故教训 u 装置紧急泄压后,系统压力至0.1 MPa左右时,如果 反应器床层温度下降幅度不大(仍能大于300℃) ,则必须通过补入纯度99.99%的高纯氮气,边充边 放反应器床层降温至200℃后才可以重新恢复进料 。 u 循环机K102出口4.0MPa氮气日常生产中盲板要处于 通状态,三阀组双阀开,低点放空开,保证随时处 于备用状态。在紧急停工过程中及时联系化验对 4.0MPa氮气进行纯度分析,保证合格。 u 加强队反应器床层超温和循环机故障停运的反事故 处理能力培训工作。
停电导致裂化反应器飞温
此后精制裂化反应器各点温度逐步降低,9月5日 C1001开机前CAT1温度降至300℃,CAT2温度降至 326℃。 9月5日10:10左右,循氢机C1001再次启动,到11 :00左右,转速提至8000RPm,反应各点温度降低 速度加快,到9月5日20:00反应器各点温度都降到 了200℃以下。9月5日18:30装置启动P1001向反应 系统进低氮油进行了冲洗,到21:00停止冲洗。
加氢裂化反应器飞温的因素及控制措施
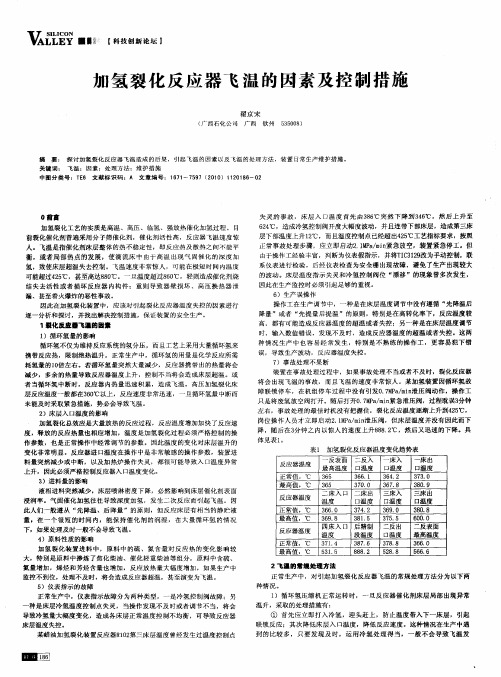
6 )生产 误操作
结 失去 活 性或 者 损 坏 反应 器 内构 件 ;重 则导 致 器 壁损 坏 、高压 换 热 器 泄
漏、甚 至着 火爆炸 的恶性 事故 。
因此在加 氢裂 化装 置 中,应 该对 引起裂 化反应 器温 度 失控 的因素 进行 逐一分 析和探 讨 ,并找 出解决控 制措 施 ,保 证装 置 的安 全生 产。
操作 工在 生产 调节 中, 一种是 在床 层温度 调 节 中没有 遵循 “ 降温 后 先
降量 ”或 者 “ 先提 量 后提 温 ”的原 则 ,特别 是在 高转 化 率下 ,反应 温度 较 高 ,都有 可 能造成 反 应器温 度 的超温 或 者失 控 ;另一 种 是在床 层温 度调 节
1曩 化反应 嚣飞 疆的 因素
可能超 过4 5 2 ℃,甚至 高达 80 。一旦温 度超过 80 8℃ 6 ℃,轻则造 成催化 剂烧
正常 事故 处理 步骤 ,应 立 即启 动2 1P/ J紧 急放 空 ,装置 紧 急停 工。但 . ̄a mn I 由于操 作工 经验丰 富 ,判断 为仪表假 指示 ,并将 TC 19 I32 改为手 动控 制 ,联 系 仪表 进行 检验 ,后经 仪表 检查 为安 全栅 出现 故 障,避 免 了生产 出现 较大 的波动 。床 层温 度 指示失 灵和 冷氢 控 制 阀位 “ 漂移 ”的现象 曾多次发 生 ,
一
反表面 二反入 一床入
一床 出 口温度 330 7.
上升 ,因此 必须严 格控 制反应 器入 口温度 变化 。
失 灵 的事 故 , 床层 入 口温 度 首先 由3 6C突 然 下 降到 3 6C, 然后 上 升 至 8" 4"
加氢裂化装置事故案例及分析

加氢裂化装置事故案例及分析李立权【摘要】针对加氢裂化装置近50年来发生的各类事故,包括电力事故、飞温事故、火灾事故、爆炸事故、泄漏事故、中毒事故、高压串低压事故、催化剂作业事故、仪表事故等,分析了事故发生的原因,总结需吸取的教训.指出:①电源故障造成集散控制系统(DCS)黑屏时,调节阀处于安全状态方能保证装置的本质安全;②飞温事故的安全处理必须坚持“一泄到底”原则;③防止火灾事故扩大必须紧急隔离火源,泄放可燃物;④高压管线、阀门、设备失效是爆炸、泄漏事故发生的主要原因,应定期检修、不定期在线检测;⑤正确执行防护管理规定,佩戴合适的防毒面具,可有效防止中毒事故发生;⑥加强高压仪表的防冻防凝可有效避免高压串低压事故的发生;⑦严格控制高压空冷器入口流速、Kp值、水相NH4HS浓度可有效防止腐蚀事故的发生;⑧原料氯离子含量高导致的垢下腐蚀是高压换热器事故的主要原因;⑨安全措施不到位是催化剂作业事故的主要原因;⑩维护保运不及时导致的仪表老化是仪表事故的主要因素;(⑥)腐蚀加高温是导致加热炉管事故的主要原因.【期刊名称】《炼油技术与工程》【年(卷),期】2016(046)012【总页数】5页(P5-9)【关键词】加氢裂化;事故;案例;分析;飞温;火灾;爆炸泄漏;中毒【作者】李立权【作者单位】中石化洛阳工程有限公司,河南省洛阳市471003【正文语种】中文加氢裂化装置处于高温、高压、临氢、易燃、易爆、有毒介质的操作环境,近50年来发生了多起安全生产事故,给企业造成了重大的经济损失,也导致了部分人员伤亡。
总结和分析这些事故原因,吸取教训,避免类似事故的发生对保障企业的安全生产意义重大。
事故案例:2000年的某日14∶27,某企业因110 kV变电所故障,引起加氢裂化装置晃电,造成装置机泵停运,废热锅炉过热段安全阀起跳,不间断电源(UPS)失灵,集散控制系统(DCS)停电黑屏,系统无法监测和控制DCS参数,只得人工启动2.1 MPa/min紧急泄压,装置紧急停工。
加氢裂化开工过程事故汇编解读
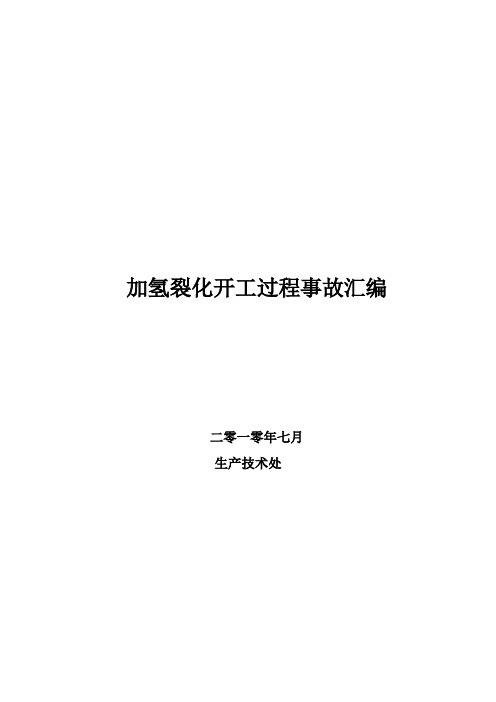
加氢裂化开工过程事故汇编二零一零年七月生产技术处1.循环氢压缩机故障循环氢压缩机及其辅机故障,严重制约了装置的顺利投产,反应系统气密过程中,当反应系统压力12.0~14.0MPa,因密封油泵压力不足,密封油系统热量分布不平衡,油冷却后温度较高,曾数次造成循环氢压缩机停机,影响气密进度,对密封油泵及冷却系统进行改造,16.0MPa氢气气密一次合格。
投料试生产后,循环氢压缩机频繁停机,且没有任何报警,给查找原因带来较大困难,其间陆续解决了润滑油泵出口安全阀弹簧损坏,调速油供油管径过小,DG505调速系统参数整定欠佳,冬季外供中压蒸汽管网过长,中压蒸汽温度低易带水,现场调速系统反馈信号接线短路等问题,使停机问题最终得以解决。
2.C101(循环氢压缩机)密封油液位导致机组联锁跳闸1986年7月9日,Q01机组在第一次试运中,8:05时密封油高位罐液位下降,电泵也无法维持液位。
8:08时由于高位罐液位低造成联锁跳闸,Q01自动停运。
事后发现液位自控回路调节阀处于关闭状态,经检查是该阀定位器供风定值器损坏,仪表风中断造成调节阀自动关闭,使密封油不能进入高位罐。
分析:调节阀出故障是操作中常见的现象,当运转设备正常而出现断流故障,应立即查看调节阀开度,必要时用旁路阀调节。
3. 1.0MPa蒸汽温度减温到180℃1986年8月21日,C101(循环氢压缩机)正在开机试运中,废热锅炉开除氧系统,(向CT1019循环氢压缩机蒸汽透平)背压蒸汽注碱温水,将1.0MPa蒸汽控制在250℃,由于除氧器温度升的过高液位波动,造成F106-P0lA泵(碱温水泵)抽空碱温水中断,背压汽温控表TC-713自动将注碱温水阀全开,备用泵起动后温控表调节滞后,大量碱温水注入C101背压汽中,使1.0MPa蒸汽温度降到180℃。
故障出现后,紧急将TC-713改手动将温度提回到250℃。
分析:加氢裂化装置的低压汽是排放到厂管网,1.0MPa蒸汽饱和温度为170℃,接近170℃时会造成蒸汽带水事故。
加氢裂化装置反应器飞温原因及处理对策

加氢裂化装置反应器飞温原因及处理对策摘要:加氢裂化装置反应器飞温原因较多,常见的有循环氢流量中断或减少、原料性质改变、床层径向温差较大。
为了提高加氢裂化装置反应器飞温处理效果,技术人员可从循环氢压缩机正常运转、对催化剂进行装填、硫化或钝化等方面着手,降低危险事故的发生率。
关键词:加氢裂化装置;反应器;飞温原因;处理对策飞温是反应器在非稳定操作条件下操作参数出现微扰动导致反应器温度升高的现象之一。
因加氢裂化装置活性较高,容易出现催化剂反应,增加了反应器的飞温速度,导致温度在短期内快速升高,催化剂烧结且失去活性,容易发生各类安全事故。
因此,为了保障加氢裂化装置及生产的安全,接下来本文就加氢裂化装置反应器飞温原因进行分析,提出相应的处理对策。
1加氢裂化装置反应器飞温原因1.1循环氢流量中断或减少反应器的床层放出的热量较多,需要通过循环氢携带,若出现循环氢流量中断或减少的情况,那么床层温度的能力就会失去。
从反应器温度控制方面分析,循环氢终端的影响相当重要,因为循氢机停运,无法往外携带热量,导致原料油和催化剂接触的滞留时间较长,和氢气在高温的反应器中容易继续发生反应且处于持续放热的状态,床层快速升温,必须第一时间采取有效的泄压方法[1]。
同时,还会出现个别床层入口冷氢量增加的问题,增加了其他床层入口氢气量被争夺的情况。
具体来说,循环氢压缩机停运发生的原因较多,常见的有干气密封泄漏量高连锁、冷高压分离器液位高联锁等。
1.2原料性质改变原料油的性质不同,若原料油的氮或含硫量智能机,又或者处理含烯烃量较多的原料时,精制催化剂所在的床层温升处于增加的趋势。
若精致床层的冷氢量较大,还会导致裂化床层入口冷氢降低。
因此,不仅要对加工减压蜡油进行考虑,掺炼焦化蜡油时,还要对混合原料油性质变化进行全面考虑。
针对采取尾油循环工艺装置,若循环油至反应系统流量发生变化,还会改变反应器进料性质。
1.3床层径向温差较大床层径向温差指的是在一个床层水平面上,不同位置的热电偶测量的最低和最高的温度差,可通过其反映不均匀的进料分配和催化剂装填问题,因而原料油在反应器横截面流量分布不够均匀,短路的问题比较常见[2]。
加氢裂化装置安全特点和常见事故分析

加氢裂化装置安全特点和常见事故分析摘要:对某公司五百万吨/年加氢裂化装置的工作原理进行了简单的阐述,并对该装置的安全特性、安全设计等方面进行了探讨,并对该装置的常见事故进行了归纳,并对该装置的运行和检修进行了分析。
关键词:加氢裂化;开工;安全一、装置的生产原理及简介加氢是指在高压条件下,碳氢和碳氢在催化上进行的催化分解和加氢,形成低分子的加氢工艺,以及加氢脱硫、脱氮和不饱和烃的加氢。
它的化学反应包括饱和,还原,裂化和异构。
碳氢化合物在加氢时的反应方向与深度与碳氢化合物组成、催化剂性能、运行环境有关。
加氢装置由反应、分馏、蒸汽发生三部分构成,利用 UOP单管双药全周期加氢裂解技术,实现了最大程度的中馏份,并将其用作洁净燃油的混合成分。
反应段为两组式串联全周期、预混氢、高温生产,并以湿法硫为原料进行硫化。
以低氮油钝化工艺对催化剂进行钝化,利用器外部再生技术对催化剂进行再生;分馏系统主要包括汽提塔、常压分馏塔和石脑油、航煤柴油等。
该设备的主要原材料是降压蜡和炼油,以液化石脑油、石脑油、航空煤油、轻柴油、重柴油等为主。
二、加氢裂化装置安全特点2.1临氢、易燃易爆氢是一种易扩散、燃烧和爆炸的气体。
氢是一种非常活跃的化学物质,它的火焰具有“不可见性”,它的燃烧非常迅速,如果是在空中,哪怕是一点点的火星,哪怕是剧烈的碰撞,都会引起它的爆炸。
2.2系统高温高压在此基础上,对加氢厂的加氢工艺进行了严格的实验研究,提出了高压15.89 MPa和382摄氏度的工艺要求,在生产过程中,必须保证液位的稳定性,避免了串压,不然会引起一场爆炸。
2.3有毒有害化学品多该设备含有大量有毒、有毒的化工原料,包括硫化剂、催化剂、碱液、液氨等,同时还会产生大量有毒的气体,如硫化氢、 CO、羰基镍、苯等,这些有毒的化合物中含有羰基镍和苯,硫化氢对神经系统的毒性很大,所以必须进行严格的监测。
能预防渗漏,熟悉危险化学品的特性和保护。
一旦发现问题,要立即进行处置,并向上级报告,避免事态进一步恶化。
- 1、下载文档前请自行甄别文档内容的完整性,平台不提供额外的编辑、内容补充、找答案等附加服务。
- 2、"仅部分预览"的文档,不可在线预览部分如存在完整性等问题,可反馈申请退款(可完整预览的文档不适用该条件!)。
- 3、如文档侵犯您的权益,请联系客服反馈,我们会尽快为您处理(人工客服工作时间:9:00-18:30)。
加氢裂化飞温事故过程分析作者:日期:2 01 0年3月5日蜡油加氢裂化装置事故开停工过程分析装置停工原因1. 1 0 6-K- 1 02背压蒸汽压力达到4.3MPa,造成汽轮机出口背压蒸汽线上安全阀(放空口为一向下弯头)起跳,并且安全阀未能及时复位,现场大量蒸汽喷向地面并向四周扩散,操作人员无法靠近,不能准确判断具体的泄漏位置,同时避免对系统蒸汽供应产生影响, 操作人员在1 0 9单元关闭进1 0 6装置的9.5MPa蒸汽手阀,循环氢压缩机K1 0 2停运,低速泄压阀启动,装置紧急停工。
事故停、开工经过3月5日5: 4 6装置紧急停工,K1 02停机,反应系统7b a r紧急泄压。
泄压前后床层温度对比如下:1. 3月5日7: 11时向反应系统补氢充压,同时通过7ba r放空泄压。
在开K1 02之前R 101A五床层温度升高约30C,升至38 0C,其他床层没有出现明显温升。
为了及时开启循环氢压缩机 K102恢复生产,通过新氢压缩机K101三回一将系统压力升至1.8MPa,9:38时开循环氢压缩机转速升至1 0 00rpm;3 7 .5m i n后转速升至31 0 0 rpm,防喘振阀打开,循环氢量20000m3/h;30min后循环氢压缩机转速升至5300rpm,R101 A第五床层温升得以控制;1 0min后(11: 05时)循环氢压缩机转速升至63 50r p m R101A/B第5、第6床层冷氢阀全开,此时R10 1A/B第六床层温度已快速升高,最终R 1 0 1A列在1 1: 14时出现下降拐点,而 R101B则在此时飞速上升,在11: 17时最高点温度达到800C, 3分钟后床层温度开始下降。
反应器床层继续循环降温至20 0C,反应系统压力逐渐往1 0M P a控制。
分馏系统热油运短循环,吸收稳定三塔循环。
2.3月5日19:06时开进料泵,反应系统开始进料,装置进入正常开工程序。
3月6日15: 00时柴油改入产品罐,15:36时重石改入产品罐;1 7: 05时轻石、航煤改入产品罐。
开工正常后遗留的主要问题及处理建议3月6日下午柴油产品质量发黄,尾油硫含量505p pm (正常小于3 0),热低分油S :31 8 pp m、N : 1 4 1 ppm(正常S :9 0 ;N:3-5)。
通过分别对E 104 A/ B 管程出口采样目测,发现R101 A生成油颜色蓝而透明,R 101B生成油颜色很黄,从而确定B系列高压换热器内漏,造成原料油泄漏至反应生成油中。
通过对E104 B、E 10 2 B/D、E10 1B管壳程出入口温度数据分析,怀疑E101B的内漏可能性最大。
1四经验教训1、对装置催化剂的性能估计认识不足,未预想到系统压力1 .8MPa左右,反应催化剂床层加氢反应激烈导致大量反应热产生,而此时由于 K102正在升速过程中,短时间内没有冷氢可用无法带走反应热。
2、反应器床层发生超温事故或循环机故障停运事故,系统泄压要一泄到底,至 0.1M Pa左右,避免催化剂床层温度进一步升高。
在反应床层温度超温阶段将反应系统压力泄放至最低是非常有效的降温方式。
3、循环机开机程序过程共需要1 .5h才能够带负荷运行。
延误了通过冷氢量来控制床层温度的时间。
4、装置紧急泄压后,系统压力至0.1 M Pa左右时,如果反应器床层温度下降幅度不大(仍能大于300 r ),则必须通过补入纯度99.99%的高纯氮气,边充边放反应器床层降温至2 00 r后才可以重新恢复进料。
5、循环机K102出口 4.0MPa氮气日常生产中盲板要处于通状态,三阀组双阀开,低点放空开,保证随时处于备用状态。
在紧急停工过程中及时联系化验对 4.0MPa 氮气进行纯度分析,保证合格。
6加强队反应器床层超温和循环机故障停运的反事故处理能力培训工作。
附件一 :PIC 30401操作记录M 2 010-03-05 0 t o Ma n ua 1 p M 20 10- 03-05 t o 47 . 7 0\par M2010-03-05 05 :14:1 7 P IC30401操作记录5 :14:12 1 0 9DM1 10903P_3 PI C 30 401 MA Au to a r 0 5:1 4: 17 1 09D M1 1 0 90 3 P 3 PIC 3 04 01 OUT 48.7 0 109DM1 1090 3 P _3 PIC30 401 O UT 47. 70 t op ar M 2010-03 - 05 0 5 :14:20 5 parM 20 1 0 - 0 3 -05 05: 1 4: 37 1 0 9DM1 1 0 90 3P_3 P IC 30401 OU T 4 5 .7 0M to 1 09 DM1 10903P_3P IC30401 O UT 4 6. 70 to 4 t o 44.70\p ar2 01 0-03-05 05:14 : 4 3. 7 0 pa r 3 7 109D M 1 1 090 3 P _3 PI C 304 01 OUT 44 .70 M2010-0 3 -05 05: 14: to 4 2.70\pa r M 2010-03-05 0 5: 14: o 41. 7 0\p a r M 2010-0 3 -05 to 40.7 0\ par2 0 1 0-03 -05 to 39 .05:14:53 8 1 0 9D M1 1 09 0 3P 3 P I C304 0 1 OUT 43.70 58 109DM1 1 09 03 P 3 PIC304 0 1 OUT 42.70 t 1 0 9D M 1 10903P_3 PIC3040 1 O UT 4 1. 7 0 05 :1 5 : P ar 0 1 10 9 DM1 10903 P_3 P I C30 4 01 O U T 40 .7 1 0 9DM1 109 0 3P _3 P I C30401 OUT 39.70 0 1 0 -03- 0 5 05:15:01 o 38. 7 0\pa r20 10- 0 3 -0 5 05:1 5 : 0 4 109 D M1 10903P_3 P IC 30 40 1 O UT 3 t M 8 .70 t o 37 . 7 0\pa rM 2 010-0 3 - 05 05 : 15:0 4 109 DM 1 10903P_3 PIC3 0 401 O U T 3 7. 70 to 36.70\p a r M 2010-03 — 05 05:15 : 1 1 1 09D M1109 03 P_3 PI C 30 4 01 O U T 3 6. 70 t o 35.70\pa r M 201 0- 03-05 0 5:15:12 109DM1 10903P _3 PI C 30401 OUT 35 .70 to 34. 7 0\par M 2010- 03-0 5 05: 1 5:13 109DML 10 9 03P_3 P IC 304 0 1 OUT to 33.70\pa rM 2010-03- 0 5 05: to M 32.15:18 10 9DM1 10 903P_3 PIC3 0 401 O U T 33. 3 4.70 3 2.7 2010-03 7 0 t o p ar 0 5 31. 0 5:15: 1 9 1 0 9 D M 1 109 0 3P_3 PIC 304 01 7 0\par O UT 5 0 5 :15 : 20 M 20 1 0 -03-0 to 3 0. 7 0 \ par M 2010- 0 3 - 0 5 0 5 :15:27 1 0.7 0 to 29. 7 0\ parM 2 0 10- 0 3- 05 05:1 5 :27109 DM1 10 903P 3 PIC30 4 01 OUT 31. 7 0 0 9D M1 1 0 9 03 P 3 PI C304 0 1 OUT 3 1 09DM1 10903 P_3 PIC30 4 01 OUT 2 9 .27 0 to 2 8.70\p a rM201 0 - 03 - 0 5 0 5: 15:28 1 0 9 DM110903 P _3 P I C30401 OUT28. 70 to 27. 7 0 pa rM 2010-03-05 0 5 : 1 5:35 6.70\ par M 20 1 0-03-05 05:15 : 35 to 25 . 70\par M 2010- 0 3 - 0 5 05: 5. 7 0 M 2 0 6.7 10 9DM1 10903P_3 PIC30401 O UT 27.70 to 109DML 10 9 03P 3 PIC 3 0401 OUT 2 6 .70 1 6: 03 1 0 9 DM1 1 09 0 3P_3 P I C3040 1 O U T 2 t o 2 6 1 0 - 0 3- 0 5 0 to 27.70 0 5 pa r 0 5: 1 6: 03 109D M 1 1 0 90 3 \ par05 : 1 6:04 1 0 9DM 1 10 P _3 PIC3 0 4 0 1 O UT 2 M 201 0-03 27.7 0 M20 1 0-03-0 5 o 2 9 p ar M2 0 1 0 -0 3 -05 05:16:04 o 30.7 0\p ar M 201 0- 0 3-05 05:16 : 05 3 1 .70\pa r M 2010 — 03 -05 0 5 : 1 6:05 1 09D M 1 1 09 0 3P_3 P I C 30401 O U T 3 1.7 0 to 3 2 .7 0 \p a r| M 201 0-03- 0 5 0 5: 1 6:0 7 1 09 DM1 109 03P_3 P I C 30 401 OU T 32 . 70 to 3 3.70\par M 20 10- 0 3— 0 5 0 5 :16:13 1 09DM1 1 0903P_3 PIC30401 O UT 33.70 to 3 2.7 0 \par M 2010-03-0 5 0 5: 1 6:31 1 0 9D M 1 1 0903P 3 P IC 30 4 01 M A Manua lto 2 8 .70\p a r 05: 1 6:04 109D M 1 109 0 3P _3 90 3P I p arP _3 P I C 3 0401 C30401 OUT28.70 OUT1 09D M11090 3P_3P I C 3 0 401 O U T2 9.70 10 9D M 1 109 0 3P3 PIC30401 OUT 30.70 toPIC 3 0 401趋势曲线图Mar 05 1005115:35.■'T< iriT.iiOUTA 10903P^3 picacwoi £5.70 100.00 0,O(KM)CLOSE人一■—I / J —、u H \J______________________________________ 、、、-05:10:00Mar 0505:15:00 Mar 0505:20:00 Mar 05update10903P_3 prcj040i MEAS6,0000 0,0000'=0 ------- i —C 304 0 1控制流程简图PI ■、.IIOLl] 4X1*0 < --------- ------ M_Thh4 ■吒—=_rf -- M ^S.- ■ I I I-.^E T - I ■ ■ P B -T-P 1-5 + T L - T +- ■-.£=■■ ■1-卩 彳扌~~I tJLcn 卜二二rFi —yiiuu L - -- 1 J *.Pi ITIU L131 I WKKlU(循环机转速与循环氢量的关系图)9 :38开循环氢压缩机,系统压力1.8M Pa,转速升至1 0 00 r p m ; 3 7 .5min 后转速逐渐升至3 1 00 rpm,循环氢2 0 000m 3/h 左右;3 0 mi n 后循环氢压缩机转速逐渐升至 5300rp m ,循环氢量40 0 0 0m3左右。