重卡铝合金轻量化
一种重卡车架轻量化结构设计及有限元分析
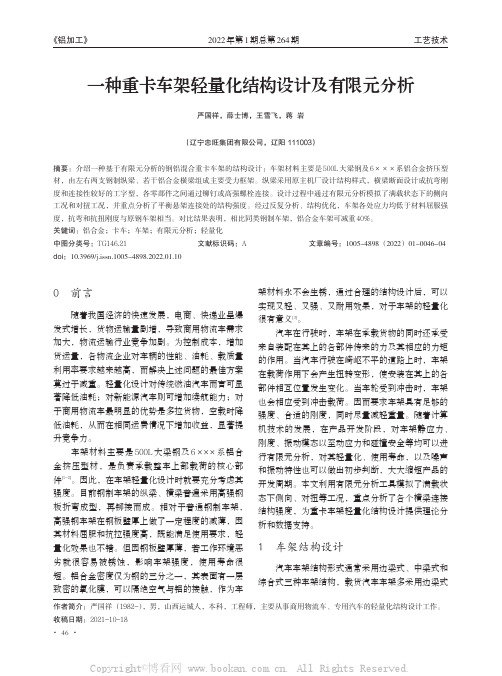
作者简介:严国祥(1982-),男,山西运城人,本科,工程师,主要从事商用物流车、专用汽车的轻量化结构设计工作。
收稿日期:2021-10-18一种重卡车架轻量化结构设计及有限元分析严国祥,薛士博,王雪飞,蒋岩(辽宁忠旺集团有限公司,辽阳111003)摘要:介绍一种基于有限元分析的钢铝混合重卡车架的结构设计:车架材料主要是500L 大梁钢及6×××系铝合金挤压型材,由左右两支钢制纵梁、若干铝合金横梁组成主要受力框架。
纵梁采用原主机厂设计结构样式,横梁断面设计成抗弯刚度和连接性较好的工字型,各零部件之间通过铆钉或高强螺栓连接。
设计过程中通过有限元分析模拟了满载状态下的侧向工况和对扭工况,并重点分析了平衡悬架连接处的结构强度。
经过反复分析、结构优化,车架各处应力均低于材料屈服强度,抗弯和抗扭刚度与原钢车架相当。
对比结果表明,相比同类钢制车架,铝合金车架可减重40%。
关键词:铝合金;卡车;车架;有限元分析;轻量化中图分类号:TG146.21文献标识码:A文章编号:1005-4898(2022)01-0046-04doi:10.3969/j.issn.1005-4898.2022.01.100前言随着我国经济的快速发展,电商、快递业呈爆发式增长,货物运输量剧增,导致商用物流车需求加大,物流运输行业竞争加剧。
为控制成本,增加货运量,各物流企业对车辆的性能、油耗、载质量利用率要求越来越高,而解决上述问题的最佳方案莫过于减重。
轻量化设计对传统燃油汽车而言可显著降低油耗;对新能源汽车则可增加续航能力;对于商用物流车最明显的优势是多拉货物,空载时降低油耗,从而在相同运费情况下增加收益,显著提升竞争力。
车架材料主要是500L 大梁钢及6×××系铝合金挤压型材,是负责承载整车上部载荷的核心部件[1-2]。
因此,在车架轻量化设计时就要充分考虑其强度。
目前钢制车架的纵梁、横梁普遍采用高强钢板折弯成型,再铆接而成。
轻量化铝合金的用途

轻量化铝合金的用途铝合金是一种重要的轻量化材料,具有重量轻、强度高、耐腐蚀等优点,因此在各个领域有着广泛的应用。
下面将从航空航天、汽车制造和建筑领域三个方面介绍轻量化铝合金的用途。
一、航空航天领域在航空航天领域,轻量化铝合金被广泛应用于飞机的制造。
相比于传统的钢材,铝合金具有更高的强度和更低的密度,可以显著减轻飞机的重量,提高燃油效率和飞行性能。
轻量化铝合金制成的机身、机翼和发动机零部件,可以减少飞机的自重,提高机动性和载重能力,同时也降低了碳排放量,符合环保要求。
此外,铝合金还具有良好的耐腐蚀性能,可以有效延长飞机的使用寿命。
二、汽车制造领域在汽车制造领域,轻量化铝合金被广泛应用于车身和发动机部件的制造。
相比于传统的铁质材料,铝合金具有更高的强度和更低的密度,可以有效减轻汽车的重量,提高燃油经济性和行驶性能。
轻量化铝合金制成的车身结构,可以提高车辆的刚性和安全性,同时也降低了碰撞时的冲击力。
此外,铝合金还具有良好的导热性能,可以有效降低发动机温度,提高热效率和动力输出。
三、建筑领域在建筑领域,轻量化铝合金被广泛应用于建筑结构和外墙装饰材料的制造。
相比于传统的混凝土和钢材,铝合金具有更高的强度和更轻的重量,可以减少建筑物的自重,提高抗震性能和建筑物的稳定性。
轻量化铝合金制成的建筑结构,可以实现更大跨度和更薄的墙体,增加建筑内部的空间利用率。
此外,铝合金还具有良好的耐候性能和装饰效果,可以实现建筑外墙的多样化设计和个性化装饰。
轻量化铝合金具有广泛的应用前景。
在航空航天、汽车制造和建筑领域,轻量化铝合金的优异性能可以带来更高的效益和更好的环境效益。
随着科技的发展和工艺的提升,相信轻量化铝合金会在更多领域发挥重要作用,为人类的生活带来更多便利和进步。
铝合金在汽车轻量化中的应用
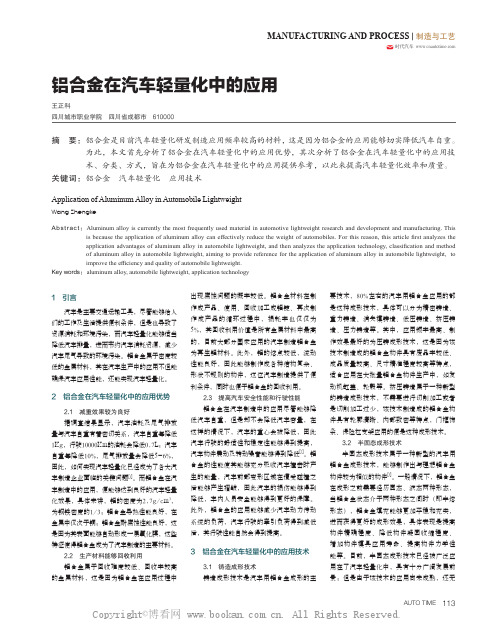
MANUFACTURING AND PROCESS | 制造与工艺 时代汽车 铝合金在汽车轻量化中的应用王正科四川城市职业学院 四川省成都市 610000摘 要: 铝合金是目前汽车轻量化研发制造应用频率较高的材料,这是因为铝合金的应用能够切实降低汽车自重。
为此,本文首先分析了铝合金在汽车轻量化中的应用优势,其次分析了铝合金在汽车轻量化中的应用技术、分类、方式,旨在为铝合金在汽车轻量化中的应用提供参考,以此来提高汽车轻量化效率和质量。
关键词:铝合金 汽车轻量化 应用技术1 引言汽车是主要交通运输工具,尽管能够给人们的工作及生活提供便利条件,但是也导致了资源消耗和环境污染,而汽车轻量化能够适当降低汽车排量,进而节约汽车消耗资源,减少汽车尾气导致的环境污染。
铝合金属于密度较低的金属材料,其在汽车生产中的应用不但能确保汽车应用性能,还能实现汽车轻量化。
2 铝合金在汽车轻量化中的应用优势2.1 减重效果较为良好据调查结果显示,汽车油耗及尾气排放量与汽车自重有着密切关系,汽车自重每降低1Kg,行驶10000Km的油耗会降低0.7L;汽车自重每降低10%,尾气排放量会降低5-6%,因此,如何实现汽车轻量化已经成为了各大汽车制造企业面临的关键问题[1]。
而铝合金在汽车制造中的应用,便能够达到良好的汽车轻量化效果,具体来讲,铝的密度为2.7g/cm3,为钢铁密度的1/3;铝合金导热性能良好,在金属中仅次于铜;铝合金耐腐蚀性能良好,这是因为其表面能够自动形成一层氧化膜,这些特征使得铝合金成为了汽车制造的主要材料。
2.2 生产材料能够回收利用铝合金属于回收难度较低、回收率较高的金属材料,这是因为铝合金在应用过程中出现腐蚀问题的概率较低。
铝合金材料在制作成产品、使用、回收加工成铝锭、再次制作成产品的循环过程中,损耗率也仅仅为5%,其回收利用价值是所有金属材料中最高的,目前大部分国家应用的汽车制造铝合金为再生铝材料。
此外,铝的熔点较低,流动性能良好,因此能够制作成各种结构复杂、形状不规则的构件,这位汽车制造提供了便利条件,同时也便于铝合金的回收利用。
9.6米厢式货车铝合金车厢轻量化设计及优化

9.6米厢式货车铝合金车厢轻量化设计及优化9.6米厢式货车铝合金车厢轻量化设计及优化随着物流运输业的不断发展,货车作为一种重要的运输工具,其设计和制造也面临着挑战。
在货车设计中,车厢的负重能力和车身的轻量化是关键的考虑因素之一。
本文将着眼于9.6米厢式货车铝合金车厢的轻量化设计和优化。
首先,我们需要了解铝合金在车身设计中的优势。
相对于传统的钢材,铝合金具有更高的强度和较低的密度。
这使得铝合金适合于重量敏感的应用,如货车车厢。
同时,铝合金具有良好的耐腐蚀性能,可以延长车身的寿命。
在设计过程中,我们需要考虑车厢的稳定性和刚性。
通过材料替换,使用铝合金能够减少车身的自重,从而提高整体的有效载重能力。
此外,车厢的结构设计也需要满足载货稳定性的要求,确保货物在运输过程中不会发生移动或损坏。
在保持结构稳定性的前提下,轻量化设计需要考虑到材料的合理分布和形状优化。
通过使用优化设计软件和有限元分析方法,我们可以确定最佳的材料厚度和材料位置,以提高整体的刚度,并减少不必要的材料浪费。
此外,使用铝合金还可以采用回收再利用的方式,减少资源浪费和环境污染。
除了材料的优化,我们还可以通过其他设计手段来进一步降低车身的重量。
例如,可以采用空心结构、蜂窝结构或者梁柱结构来代替传统的实心结构,以实现更高的强度和更低的重量。
此外,采用高强度螺栓和焊接技术可以提高连接处的强度和刚度,进一步降低车身的重量。
此外,我们还需要考虑到车辆的安全性。
在轻量化设计中,我们不能仅仅追求减少重量而忽视安全性。
因此,在设计过程中,我们需要对车辆进行全面的结构强度分析和碰撞模拟,以确保车身在意外情况下能够提供足够的保护。
这可以通过使用高强度材料、加厚关键结构部件和合理布置吸能区域来实现。
综上所述,9.6米厢式货车铝合金车厢的轻量化设计和优化是一项挑战,但也是十分重要的。
通过合理的材料选择、优化的结构设计和全面的安全考虑,我们可以实现车身重量的降低,提高车辆的负载能力,并减少资源的消耗。
铝合金对车体轻量化的意义

铝合金对车体轻量化的意义铝合金是工业中应用最普遍的一类有色金属结构材料,在航空、航天、汽车、机械制造、船舶及化学工业中已大量应用。
尤其是在油罐车和集装箱制造行业,随着工业经济的飞速进展,对铝合金焊接结构件的需求日趋增多。
国外百分之八十的集装箱油罐车用材都是采纳了铝合金,因为它的优势显而易见。
其中最重要的一点确实是,采纳铝合金的车体轻量化,更经济有效。
针对那个优势咱们做了以下分析研究。
一、车体轻量化的意义所谓汽车轻量化,确实是采纳科学方式和手腕对汽车产品进行优化设计,在确保汽车综合性能指标的前提下,通过利用新型材料,尽可能降低汽车产品自身重量,达到减重、降耗、环保、平安的综合目标。
研究说明,汽车所用燃料约60%消耗于汽车自重,汽车的质量每减轻100 kg,每千米的燃油消耗将减少 L~ L,CO2排放量也将减少。
燃油效率提高,意味着降低汽车的耗油量和排污量,改善人类生存环境。
同时汽车轻量化也提高了车辆性能,在一样的输出功率下,较轻的车关于发动机来讲确实是较轻的负载,汽车的操控稳固性也有所提高。
因此减少汽车车体重量对降低发动机的功耗和减少汽车总重量具有双重的效应。
国家标准对汽车的设计进行了严格的规定,专门是轴荷和总质量的限制。
关于油罐车而言,罐体自重占整车重量比例较大,减轻罐体的重量已成为企业关注的核心。
二、车体轻量化的途径由于铝的比重约为钢的1/3,铝合金被公认是汽车轻量化的理想材料。
最近几年来,在欧美发达国家,利用铝合金制作的液罐车已超级普遍。
而在我国通常利用钢板制作罐体。
由于钢罐体自重专门大,无形中加大了燃油的消耗,使得运输本钱大大提高。
铝是最先用于汽车制造的轻质金属材料,也是结构材料中最为经济有效、最具竞争力的汽车用轻金属材料。
从生产本钱、零件质量、材料利用率等方面,铝合金具有多种优势,如密度较小,用其替代传统钢铁,可减小整车重量的30%~40%。
回收率高,仅次于钢铁,目前可达87%,符合环保要求。
铝合金汽车轻量化材料生产工艺流程

铝合金汽车轻量化材料生产工艺流程下载温馨提示:该文档是我店铺精心编制而成,希望大家下载以后,能够帮助大家解决实际的问题。
文档下载后可定制随意修改,请根据实际需要进行相应的调整和使用,谢谢!并且,本店铺为大家提供各种各样类型的实用资料,如教育随笔、日记赏析、句子摘抄、古诗大全、经典美文、话题作文、工作总结、词语解析、文案摘录、其他资料等等,如想了解不同资料格式和写法,敬请关注!Download tips: This document is carefully compiled by theeditor. I hope that after you download them,they can help yousolve practical problems. The document can be customized andmodified after downloading,please adjust and use it according toactual needs, thank you!In addition, our shop provides you with various types ofpractical materials,such as educational essays, diaryappreciation,sentence excerpts,ancient poems,classic articles,topic composition,work summary,word parsing,copy excerpts,other materials and so on,want to know different data formats andwriting methods,please pay attention!水利回填灌浆工艺流程一、施工准备阶段。
在开展水利回填灌浆施工之前,有诸多准备工作需妥善完成。
货车轻量化涉及的几种新材料技术
附件:货车轻量化涉及的几种新材料技术铝合金。
与钢铁相比,铝合金具有质量轻(其密度为钢的1/3)、耐腐蚀性好、易于加工等特点,但成本较高,是近20年来在国内外载货汽车上使用最多的轻量化材料。
常用的包括:铸造铝合金——活塞、气缸盖、车轮、离合器盖、曲轴箱、进气歧管等;型变铝合金——发动机罩、货箱地板、保险杠、车轮、热交换器(散热器与加热器)、温度调节器(冷凝器与蒸发器)、油冷却器以及冷藏车厢、保温车厢、半挂车的车厢与车架等。
欧、美、日等国多年来铝合金在汽车上的用量平均年增幅为10%。
据统计,2003年全球每辆汽车用铝已从1978年的50kg上升为140kg,增长1.8倍。
镁合金。
与钢铁相比,镁合金密度小(比铝还小)、易于加工、压铸经济,其最大特点是阻尼减振性和抗凹性好。
镁合金早在20世纪40年代末就开始被一些公司采用。
镁合金在应用上比铝合金发展得慢,主因是因为其铸造性差、后处理工艺复杂、成本较高。
当前世界上所有汽车镁合金平均用量仅2.3kg。
随着研制该材料技术水平的提高,目前正以每年15%-20%的速度递增。
塑料及其复合材料。
汽车塑料制品一般分为内饰件、外装件和功能件等。
据统计,美国的汽车塑料使用量自1975年至1980年曾经以每年30%-40%左右的增速发展,后来因某些部件用塑趋于饱和及发展新品技术难度日益增大等因素增速逐渐放缓。
目前世界主要汽车用塑料件的内饰化已基本完成。
玻璃纤维增强塑料(FRP)等新品种已随着技术的成熟而正在扩大应用,主要用于车身的外装件和功能件。
可用于车门、发动机罩、前脸板、叶子板、保险扛骨架、门梁柱、通风百叶窗、导流罩等近20种车身板件。
具有高比强度和高比弹性模量的碳纤维增强塑料(CFRP)及有机合成纤维复合材料(Kevlar)是欧美等国已着手研究的新材料,并已开始使用,但成本较高。
如果能将其成本降至当前的1/3,将有望成为汽车功能件和结构件轻量化的优选用才。
高强度钢。
在轻量化材料中,与铝合金、塑料相比,高强度钢具有以下特点:(1)价格低;(2)基本上可利用原有生产线;(3)其弹性模量高、刚性好、耐冲击性好及较高的疲劳强度,有些高强度钢的抗拉强度为普通钢的2~3倍;(4)耐腐蚀性差。
铝合金在汽车轻量化中的优势
铝合金在汽车轻量化中的优势导读:汽车工业在蓬勃发展的同时,由于环保和节能的需要,汽车轻量化已成为世界汽车发展的潮流。
实施汽车轻量化过程中铝合金材料将发挥其天然优势,主要用来改造和替代车身材料。
汽车工业在蓬勃发展的同时,由于环保和节能的需要,汽车轻量化已成为世界汽车发展的潮流。
实施汽车轻量化过程中铝合金材料将发挥其天然优势,主要用来改造和替代车身材料。
汽车轻量化大致可以分为车身轻量化、发动机轻量化、底盘轻量化三类,其目的均是在保证性能的前提下通过使用更轻材料降低车重,从而实现节能环保功能。
很显然,铝合金在汽车轻量化中有其天然的优势:一、减重和节能效果明显。
铝的力学性能好,其密度只有钢铁的1/3,具有良好的导热性,仅次于铜,机械加工性能比铁高4.5 倍,且其表面自然形成的氧化膜具有良好的耐蚀性,因此铝成为实现汽车轻量化最理想的首选材料。
二、乘客的舒适性和安全性获得提高。
铝合金汽车是在不降低汽车容量的情况下减轻汽车自重,车身重心减低,汽车行驶更稳定、舒适。
由于铝材的吸能性好,在碰撞安全性方面有明显的优势,汽车前部的变形区在碰撞时会产生皱褶,可吸收大量的冲击力,从而保护了后面的驾驶员和乘客。
三、铝易于回收。
铝制品在使用过程中几乎不发生腐蚀或仅发生轻微的腐蚀,工业上使用的常规材料中,铝的回收价值率是最高的。
在铝材—铝制品—使用—回收再生铝锭—再加工成铝材的循环过程中,铝的损耗也仅5%左右,其再生性能比任何一种常用金属都高。
我们可以通过图表的形式直观的了解一下铝合金材料在汽车轻量化中的典型应用:目前东轻公司在产汽车轻量化方面合金材料1. 轿车车门用5754铝合金板材、6005A型材:东轻公司结合国内的市场,自主开发的《轿车车门用5754铝合金板材》被列入国家“九五”轿车新材料技术开发项目,并得到国家的大力支持。
产品质量达到了国外同类产品实物质量水平和标准要求,完全替代了进口,并实现了产品定型、批量生产的目标,制定出了完整的生产工艺操作规程与质量保证体系。
改装牵引汽车的轻量化部件选择指南
改装牵引汽车的轻量化部件选择指南随着汽车行业的发展,越来越多的车主开始关注汽车的轻量化改装。
汽车轻量化不仅可以提升车辆的性能和燃油经济性,还可以减少对环境的污染。
其中,牵引汽车的轻量化部件选择是改装过程中的重要环节。
本文将为您介绍改装牵引汽车的轻量化部件选择指南。
首先,牵引汽车的轻量化部件主要包括底盘、悬挂系统、制动系统和传动系统。
下面将针对每个部件进行详细介绍及选择指南。
底盘是汽车重要的支撑系统,直接影响到车辆的操控性和稳定性。
在选择底盘轻量化部件时,要注意材料的选择和强度的平衡。
常见的轻量化底盘材料有铝合金和碳纤维复合材料。
铝合金具有重量轻、强度高的特点,在减轻车辆重量的同时,保持了良好的刚性和强度。
碳纤维复合材料具有更高的强度和刚度,但价格较高。
根据预算和需求,选择合适的底盘材料。
悬挂系统是汽车悬挂部件的总称,其作用是减震、支撑和保持车身稳定。
在选择悬挂系统的轻量化部件时,应注重减少组件的重量,同时保持足够的刚度和强度。
常见的轻量化悬挂部件包括减震器、弹簧和转向节等。
可以选择使用铝合金或钛合金材料制作的悬挂部件,这些材料具有重量轻、强度高的特点。
同时,在设计中合理考虑杆件结构的刚度和优化布局,以实现轻量化效果。
制动系统是汽车行驶过程中的重要安全保障,对于牵引汽车尤为重要。
在选择制动系统的轻量化部件时,应注重选择轻量化、耐高温和高刚度的材料。
常见的轻量化制动部件有碳陶瓷刹车盘和钛合金刹车卡钳等。
碳陶瓷刹车盘具有重量轻、导热性好的特点,可以有效减少车辆重量,提高刹车性能。
钛合金刹车卡钳可以减少制动系统的质量,并提供足够的刹车力。
根据需求和预算,选择合适的轻量化制动部件。
传动系统是将发动机输出的动力传递到车轮的系统。
在选择传动系统的轻量化部件时,应注重减轻传动组件的重量,提高传动效率。
常见的轻量化传动系统部件包括离合器、变速器和传动轴等。
可以选择使用铝合金或钛合金材料制作的传动部件,这些材料具有重量轻、强度高的特点,并可以提高传动效率。
浅谈铝合金在氢能重卡上的应用
管理及其他M anagement and other 浅谈铝合金在氢能重卡上的应用高 翔,高培君,范 超摘要:氢能重卡在降低燃油车比例,实现重卡汽车CO2零排放方面有特殊独到益处,为建设资源节约型、环境友好型社会提出新途径、新方案。
文章综述了汽车常用铝合金材料的特点及氢燃料电池系统对铝合金的新需求,对未来氢能重卡上铝合金的应用进行展望。
关键词:氢能重卡;铝合金;应用展望轻量化已成为整车行业进行市场竞争、成本挤压的重要途径,重卡行业因为其自重高、载重多、能源消耗量大,更加需要汽车轻量化技术的相关开发,以增加续航里程,降低使用成本。
针对传统重卡在燃油经济性、碳排放控制上的弊端,市场上正在掀起一阵新能源重卡的研发及生产浪潮,首当其冲的就是氢燃料电池重卡(后文称氢能重卡)。
本文以铝合金轻量化为途径,立足于新型氢能重卡市场,分析在氢能重卡领域铝合金轻量化的前景,对未来相关产业发展进行评估。
1 氢能重卡的介绍按照中国汽车工业协会出具的行业内公认分类标准,载货汽车按照总质量划分总质量>14t为重型载货车(重卡),6t<总质量≤14t为中型载货车,1.8t<总质量≤6t为轻型载货车,≤1.8t为微型载货车四类。
主体上重卡又可根据两种方向进行细致划分,一是根据车身类型分类,分为重卡整车、重卡底盘车和半挂牵引车;二是按照能源和供给类型分为燃油重卡、天然气重卡、纯电动重卡、混合动力重卡、燃料电池重卡、替代燃料重卡等。
作为陆上运输的主角之一,相比民用车、乘用车而言,重卡载重高、行驶里程长、生产周期长、对驾驶员要求高,并且在使用传统动力时,能源消耗高、排放量高,对环境的污染程度高,有数据表明单台传统燃油重卡的尾气排放量是300辆小型客车的排放量,因此重卡如何有效实现节能减排,成为建设环境友好型社会、资源节约型社会和顺利完成“双碳”目标的关键。
氢能重卡严格意义上应该称之为氢燃料电池重型卡车,是属于燃料电池重卡中的一种类型。
- 1、下载文档前请自行甄别文档内容的完整性,平台不提供额外的编辑、内容补充、找答案等附加服务。
- 2、"仅部分预览"的文档,不可在线预览部分如存在完整性等问题,可反馈申请退款(可完整预览的文档不适用该条件!)。
- 3、如文档侵犯您的权益,请联系客服反馈,我们会尽快为您处理(人工客服工作时间:9:00-18:30)。
Bonnet 80 KG Radiator Shutters 7 KG Bumpers 15 KG
Suspension 110 KG
Engine Parts 50 KG
Transmission Housing 75 KG
Wheels 200 KG
Fuel Tanks 25 KG
5
基本工艺-折弯、打孔
6
美铝铝合金副梁的成功案例
Aluminum Cross Members for Class 8 trucks
Volvo NA offers 2 different aluminum cross members as customer options Volvo 北美分公司为客户提供2种不同的铝合金副梁的选择 Kenworth and Peterbilt use 2 aluminum cross members as standard on their chassis Kenworth和Peterbilt采用2个铝合金副梁作为底盘的标准配置
12
2
美铝重卡铝合金底盘成功案例
Daimler DOE Supertruck chassis
3
重卡底盘主梁
典型的重卡钢制主梁Typical steel rails of HDT
高度 300 mm, 法兰边宽度 90 mm,厚度 7 mm 大约重量 198 kg/根
Typical steel rails of HDT
Alcoa/Holland FW (kg)
90 174
Competitor B (kg)
141 221
Weight Save (kg)
51 47
Forged 6061-T6 Aluminum Load Capacity: 25 ton Max. Vertical Weight Save: up to 57 kg
重型卡车轻量化技术交流 Technical Discussion for HDT Li采用铝合金减重的方向(1137kg)
Cab 200 KG
Cab Doors 15 KG
Body Trim 10 KG
Cross members 150 KG
Equivalent Aluminum Frame rails are 330 mm x 100 mm x 9.5 mm thick
Weight Savings = 190 kg per truck
节约的重量最高可达:190 kg
4
基本工艺-滚压
Aluminum Frame Rails Produced at Metalsa
300 mm high, 90 mm wide flanges and 7 mm thick
Weight = 198 kg/each
替换方案:在不改变现有的生产线的基础上,采
用高强度的铝合金,滚压成形加自动化钻孔
等效的铝合金主梁尺寸:330 mm x 100 mm x 9.5
mm
Proposed aluminum rails made of a high strength Al alloy using the same production facility as the current steel rails – roll formed, and automatic punched holes
7
某副梁的减重设计
8.27 kg
3.33 kg
2.46 kg
Total Weight: 19.85 kg
8
某副梁的设计分析
“Tie Plate” vertical wall = 9 mm thick Cross-member = 11mm thick
9
某副梁减重效果
Weight (kg)
Existing Steel Cross Member 现有钢制副梁设计 Proposed Aluminum Cross member 铝合金副梁设计 34
Total : 46 kg
11
Truck Chassis/Frame – Forged Aluminum 5th Wheel
Weight Save vs. the Competition
Bracket Style Stationary Mount 24” Travel Slider Bracket Style Stationary Mount 24” Travel Slider Alcoa/Holland FW (kg) 90 174 Competitor A (kg) 145 231 Weight Save (kg) 55 57
Weight Savings
19.85
14.15 kg (42 %)
10
各个副梁的可能减重机会
Weight savings potential by converting all truck cross members to aluminum:
(如果以铝代替钢,各个部分的副梁的减重效果) ‒ Taper rear cross 2 kg ‒ Bogie 16 kg ‒ Front of bogie 7 kg ‒ Intermediate 7 kg ‒ After transmission 6 kg ‒ Over transmission 3 kg ‒ Front Closing 5 kg