电石生产工艺介绍
电石的生产工艺原理

电石的生产工艺原理电石是含有高纯度的钙 carbide 的固体化合物,它是通过石灰石与电弧炉产生的电弧作用进行电解反应产生的。
下面将详细介绍电石的生产工艺原理。
电石的生产工艺主要包括以下步骤:1.原料准备:将石灰石(CaCO3)与焦炭(C)作为主要原料进行混合。
石灰石主要提供钙,焦炭则提供碳。
此外,还需要添加一定量的煤粉和脱硫剂等辅助原料。
这些原料通过破碎和混合等工艺进行处理,使其均匀混合。
2.电弧炉反应:将混合好的原料装入电弧炉中进行反应。
电弧炉是一种高温设备,内部设置有两个电极,之间形成一道电弧。
当通电时,电极之间产生高温的电弧,在此高温下,原料中的碳与钙发生反应生成二氧化碳气体(CO2)和钙 carbide(CaC2)。
反应方程式如下:CaCO3 + 3C → CaC2 + CO23.冷却和除尘:产生的二氧化碳气体和电石在反应过程中产生的热量需要通过冷却来降温。
一般采用水冷却方式,将产生的气体和石灰石快速冷却。
在冷却的同时,还需要进行除尘处理,将电石中的杂质去除。
4.分选和包装:经过冷却和除尘处理后,得到的电石呈现出块状。
根据规定的尺寸和质量要求,对电石进行分选,去除不符合要求的样品,留下合格的电石进行包装。
电石的生产工艺原理主要是利用电弧炉中产生的高温电弧将石灰石与焦炭进行加热,并在高温下引发反应生成钙 carbide。
其中焦炭提供高温和过量的碳,促使钙与碳迅速反应。
随着反应进行,CaCO3分解为CaO和CO2,CaO与C反应生成CaC2。
产生的二氧化碳气体排出炉外,而生成的电石被收集下来。
电石的生产工艺具有高效、高纯度等优点。
通过调整原料的配比和电弧炉的操作参数可以控制电石的质量和产量。
同时,电石的生产过程中还可以产生一定的副产品,如工业气体、氮肥等,提高了资源的综合利用效率。
总之,电石的生产工艺原理是利用电弧炉进行高温电解反应,使石灰石与焦炭发生反应生成钙 carbide,经过冷却和除尘后得到电石的最终产品。
(完整版)电石生产工艺流程简介
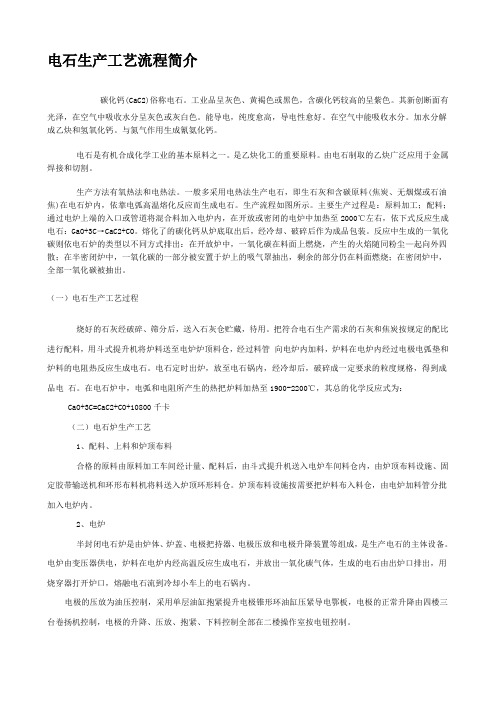
电石生产工艺流程简介碳化钙(CaC2)俗称电石。
工业品呈灰色、黄褐色或黑色,含碳化钙较高的呈紫色。
其新创断面有光泽,在空气中吸收水分呈灰色或灰白色。
能导电,纯度愈高,导电性愈好。
在空气中能吸收水分。
加水分解成乙炔和氢氧化钙。
与氮气作用生成氰氨化钙。
电石是有机合成化学工业的基本原料之一。
是乙炔化工的重要原料。
由电石制取的乙炔广泛应用于金属焊接和切割。
生产方法有氧热法和电热法。
一般多采用电热法生产电石,即生石灰和含碳原料(焦炭、无烟煤或石油焦)在电石炉内,依靠电弧高温熔化反应而生成电石。
生产流程如图所示。
主要生产过程是:原料加工;配料;通过电炉上端的入口或管道将混合料加入电炉内,在开放或密闭的电炉中加热至2000℃左右,依下式反应生成电石:GaO+3C→CaC2+CO。
熔化了的碳化钙从炉底取出后,经冷却、破碎后作为成品包装。
反应中生成的一氧化碳则依电石炉的类型以不同方式排出:在开放炉中,一氧化碳在料面上燃烧,产生的火焰随同粉尘—起向外四散;在半密闭炉中,一氧化碳的一部分被安置于炉上的吸气罩抽出,剩余的部分仍在料面燃烧;在密闭炉中,全部一氧化碳被抽出。
(一)电石生产工艺过程烧好的石灰经破碎、筛分后,送入石灰仓贮藏,待用。
把符合电石生产需求的石灰和焦炭按规定的配比进行配料,用斗式提升机将炉料送至电炉炉顶料仓,经过料管向电炉内加料,炉料在电炉内经过电极电弧垫和炉料的电阻热反应生成电石。
电石定时出炉,放至电石锅内,经冷却后,破碎成一定要求的粒度规格,得到成品电石。
在电石炉中,电弧和电阻所产生的热把炉料加热至1900-2200℃,其总的化学反应式为: CaO+3C=CaC2+CO+10800千卡(二)电石炉生产工艺1、配料、上料和炉顶布料合格的原料由原料加工车间经计量、配料后,由斗式提升机送入电炉车间料仓内,由炉顶布料设施、固定胶带输送机和环形布料机将料送入炉顶环形料仓。
炉顶布料设施按需要把炉料布入料仓,由电炉加料管分批加入电炉内。
电石生产工艺流程

电石生产工艺流程电石是一种由石灰石和焦炭经高温反应得到的产物,主要用于生产氯碱化工产品。
下面将介绍电石的生产工艺流程。
电石生产的第一步是选矿,必须选择纯度较高的石灰石作为原料。
石灰石在高温下会分解产生二氧化碳和石灰。
为了提高产量和质量,选矿过程中需要除去杂质。
选矿之后,下一步是将石灰石经过破碎和磨细处理,以获得适合反应的颗粒度。
破碎主要通过破碎机完成,而磨细则通过研磨机实现。
破碎和磨细处理完成后,石灰石粉末将进入煤气炉,石灰石与焦炭的混合物在此处进行高温反应。
煤气炉内需要控制好反应温度和氧气含量,使石灰石和焦炭充分反应而不会发生过度燃烧。
在高温煤气炉内,焦炭还原石灰石,产生一氧化碳和氮气。
石灰石中的碳酸钙经过反应变为氧化钙。
氧化钙与水反应会产生氢氧化钙,并放出大量的热量。
化学反应方程式如下:CaCO3 + 2C -> CaO + 2COCaO + H2O -> Ca(OH)2 + ΔH反应完成后,产生的氢氧化钙和二氧化碳会与煤气中的一氧化碳反应,生成乙炔。
乙炔是电石生产的主要产物。
得到乙炔之后,需要进一步纯化。
乙炔通过冷却和净化过程,去除其中的杂质,包括硫化合物、重金属等。
最后,经过纯化处理的乙炔被输送到电解槽中,与水反应,产生乙炔气体和氢气。
该电解槽设有铁阳极和铁阴极,分别与电源相连。
电解槽内的水通过电解分解成氢氧离子和氢离子。
乙炔和氢气会在电解槽中不断形成。
通过以上的工艺流程,电石生产的乙炔气体得以产生。
这些乙炔气体可以经过进一步的处理,生产出不同种类的化工产品,如聚氯乙烯、丙烯酸等。
电石生产工艺流程中,需要严格控制反应温度、氧气含量和杂质含量,以保证乙炔的产量和质量。
同时,在生产过程中要注意环保要求,有效处理和净化废水和废气,保护环境。
电石生产工艺

电石生产工艺电石是由硫酸钙(CaSO4)和煤炭(C)经过高温加热反应制得的一种化工原料,广泛应用于制备乙炔气和化学肥料等领域。
下面将介绍一种常见的电石生产工艺。
电石生产工艺主要分为四个步骤:原料准备、反应炉加热、乙炔气分离和电石产品处理。
首先,原料准备是电石生产的基础。
煤炭是主要原料,可选择不同种类的煤炭,如无烟煤、气化煤等。
同时,还需要准备一定质量比例的硫酸钙。
接下来,将煤炭和硫酸钙按照一定的比例混合,形成煤块。
这些煤块通常具有直径在2-4厘米之间。
这样的煤块便于放入反应炉中,并且保证了反应的充分进行。
然后,煤块被放入预热过的反应炉中,进行高温加热。
在反应炉中,煤块遇热分解,生成乙炔气和炔钙等产物。
乙炔气是电石生产的重要产品,可用于制备乙炔焊、化学分析和有机合成等领域。
最后,将反应炉中的气体通过冷却器进行冷却。
冷却器中的水能够使乙炔气液化,分离出来。
同时,过程中还会产生一些碳酸钙沉淀物。
这些沉淀物可以通过过滤、干燥等工艺进行处理,得到纯净的电石产品。
在这个工艺过程中,温度和时间是十分关键的参数。
高温能够促使煤块充分分解,生成更多的乙炔气。
合理的时间控制能够保证反应的稳定性和产率。
同时,还需要注意排放处理过程中产生的废气和废水。
在电石生产中,会排放出一些有害气体和废水,如一氧化碳和硫酸等。
这些废气和废水需要通过净化设备和处理工艺进行处理,以减少对环境的污染。
总结起来,电石生产工艺是一个复杂而又精细的过程。
它不仅需要严格控制温度和时间,还需要注意废气和废水的处理。
通过这一工艺,我们可以生产出乙炔气等重要的化工原料,为人类的生产和生活提供了有力支持。
电石生产工艺流程

电石生产工艺流程
电石是一种重要的化工原料,广泛应用于石化、冶金、化肥等
领域。
下面将介绍电石的生产工艺流程。
首先,原料准备阶段。
电石的生产原料主要包括石灰石和焦炭。
石灰石经过破碎、磨细处理后,与焦炭按一定比例混合,形成石灰
石焦混合料。
其次,熔炼反应阶段。
石灰石焦混合料通过熔炼炉进行加热,
使其在高温下发生熔融还原反应,生成石灰和一氧化碳。
石灰与氧
化铝反应生成氧化钙,再与电解质氯化钠反应生成氯化钙。
接着,电解制取氢氧化钠阶段。
氯化钙溶液经过电解制取氢氧
化钠和氯气。
氢氧化钠是电石生产的主要产品之一,广泛用于制取
化肥、造纸、皂类等工业。
最后,氯气利用阶段。
氯气作为副产品,可用于制取氯化烃、
聚氯乙烯和其他有机合成原料,也可用于消毒、漂白等领域。
在整个生产工艺流程中,需要严格控制炉内温度、原料比例和
电解条件,以确保产品质量和生产效率。
同时,还要加强环保措施,减少废气、废水和固体废物的排放,保护环境。
总的来说,电石生产工艺流程涉及原料准备、熔炼反应、电解
制取氢氧化钠和氯气利用等阶段,是一个复杂的化工生产过程。
只
有严格控制每个环节,才能保证产品质量和生产安全,实现可持续
发展。
电石生产工艺

电石生产工艺电石是一种非常重要的化工产品,它是通过工业过程制造而成的。
电石生产工艺在很多国家都有应用,尤其是在化工、矿业和冶金等领域。
电石的生产过程包括多个步骤,从石灰石、煤炭到电石,每个步骤都非常关键。
下面我们将详细介绍电石的生产工艺。
一、原料准备石灰石和煤炭是制造电石的两种主要原料。
为了获得最佳的生产效果,这些原料都必须符合一定的特定要求。
1.1 石灰石石灰石是可以在自然界中找到的矿物质,它的主要成分是碳酸钙 (CaCO3)。
制备电石的石灰石通常是高品质石灰石,包括以下特定要求:(1) 高品质石灰石的含钙量应在 98~99.5% 之间。
含钙量越高,生产出的电石质量越好。
(2) 石灰石的杂质含量应尽可能低,特别是含铁、硅等杂质。
杂质含量高的石灰石不仅会降低电石的质量,而且会磨损生产设备。
(3) 石灰石颗粒大小应均匀,通常在 10~50 mm 之间。
1.2 煤炭煤炭是制造电石的另一主要原料,它需要符合以下要求:(1) 煤种选择制造电石的煤种通常是贫煤和褐煤,因为这种煤种不仅价格相对低廉,而且富含挥发分和焦油,更适合于电石工艺中的加热过程。
(2) 煤炭质量要求煤炭的质量对生产电石的影响很大。
煤炭应具有以下特性:A. 挥发分含量要高,通常在 25% - 35%之间。
B. 灰分含量应低,不超过 15%。
C. 热值越高越好,热值在 23 - 28 MJ/kg;D. 粒度应均匀,通常是 3 - 25 mm。
二、石灰石碎矿和煤炭制备生产电石的下一个步骤是对石灰石和煤炭进行处理和准备,以便放入电石炉中进行反应。
2.1 石灰石碎矿在石灰石碎矿过程中,需要选择一台合适的破碎机,将石灰石进行粉碎和筛分,最终得到符合要求的颗粒状石灰石。
2.2 煤炭制备和石灰石碎矿类似,煤炭制备也需要选择一台破碎机,将煤炭粉碎和筛分,得到合适的颗粒状煤炭。
三、电石炉的制备电石炉是制造电石的核心设备,它需要精细的设计和制造。
电石炉是一种立式圆筒形的钢制容器,高度通常在 5-10 米左右。
电石生产工艺介绍
电石生产工艺介绍
电石,又称为石灰雪,是一种重要的化学原料。
其主要成分是氢氧化钙(Ca(OH)2)和氯化钙(CaCl2)。
电石生产工艺是
将石灰石与焦炭进行还原反应产生电石的过程。
电石生产工艺主要包括石灰石的预处理、焦炭的煅烧、电石炉的操作和产物的处理等步骤。
首先,石灰石的预处理是为了提高其活性和适应炉内反应条件。
一般情况下,石灰石要经过破碎、研磨和筛分等过程,确保石灰石的粒径和活性达到要求。
然后,焦炭的煅烧是为了获得高温下所需的还原剂。
焦炭在高温下反应性较强,可以提供充足的还原气。
焦炭在电石炉内经过一定时间的煅烧,使其获得高还原性。
接下来,将预处理好的石灰石和煅烧好的焦炭按一定比例送入电石炉。
电石炉是一个密封的反应器,通常是由石灰石和焦炭层交替堆积而成的。
在炉内,石灰石和焦炭在高温下发生还原反应,产生气体和电石。
最后,产物的处理是将产生的气体和电石进行分离和纯化。
气体主要是乙炔,通过冷却和洗涤等操作可以除去其中的杂质,得到纯净的乙炔气。
而电石则通过粉碎和洗涤等工序,去除杂质,最终得到纯净的电石产品。
电石的生产工艺不仅需要高温下的反应条件,还需要控制合适
的料层结构和反应时间等参数,以保证反应效果和产量。
同时,还需要对产生的气体和电石进行合理的处理,以达到环保要求和产品质量要求。
总体来说,电石生产工艺是一项复杂的过程,但其产生的乙炔气和电石等产物在化工、冶金、医药等领域具有重要的应用价值。
随着技术的发展,电石生产工艺也在不断改进和创新,以提高效率和产品质量,同时减少对环境的影响。
电石生产工艺流程
电石生产工艺流程
1.采石:首先从深层岩石中采掘出电石原料,将其运输到指定的加工厂。
2.粉碎:将原料进行粉碎,以便进行下一步的松碎处理。
处理后的粉体要求质量较高。
3.松碎:将前一步处理后的粉体经过松碎干挤,以便充分分离各种矿物质和有机物质。
4.称量:在保证重量准确的情况下,称量各种原料(电石渣和一定比例的电解质),以便后续的熔炼和渗滤加工。
5.电解:将前一步称量后的原料进行电解,在电解过程中产生的氢氧离子渗入原料中,从而产生电石。
6.熔炼:将电解后的原料进行熔炼,将产生的电石晶体脱离其他物质,形成浓缩液,经过脱油后冷却成固体,即得到电石产品。
7.粉碎:将熔炼后的电石经过粉碎、筛选和包装等处理,即可以得到最终的电石产品。
电石生产工艺
电石生产工艺电石生产工艺是一种重要的工业生产过程,用于生产乙炔和其他化工产品。
本文将介绍电石生产工艺的基本原理、设备和流程,并探讨其在化工行业中的应用和意义。
电石是一种有机化合物,化学式为CaC2。
它是由石灰石和焦炭经过高温反应而得到的。
电石在化学工业中起着重要的作用,可以用于生产乙炔、氯乙烯、染料和塑料等产品。
乙炔是电石最重要的产物,被广泛用于金属切割、焊接、化学合成和照明等领域。
电石生产工艺一般分为两个主要步骤:炼焦和电石炉反应。
首先,通过炼焦过程将石灰石和焦炭加热至高温,使其进行反应生成炼焦炉气和焦炭。
炼焦炉气中的CO、H2等气体是电石炉的主要燃料。
而焦炭则是电石炉的原料之一。
接下来,焦炭和石灰石混合物被投入到电石炉中。
电石炉是一种高温反应器,通常由炉体、电极和底部出料装置组成。
通过加热和电弧放电等方式,炉内的焦炭和石灰石进行高温反应,生成电石。
电石炉反应的化学方程式如下:CaCO3 + 2C → CaC2 + CO2在电石炉中,焦炭的还原作用导致了碳的活化,并与石灰石发生反应生成电石。
由于石灰石是硬质物质,需要经过一定时间的保温和反应才能充分转化为电石。
在反应过程中,产生的气体经过处理可以得到纯净的乙炔。
电石生产过程中,需要注意控制炉温、气氛和料位等参数,以确保反应的顺利进行和产物的纯度。
同时,应注意排放处理炉燃烧产生的废气,并采取相关措施减少环境污染。
随着化工行业的不断发展和技术的进步,电石生产工艺也在不断改进和优化。
现代电石炉的出料装置采用了更加先进的技术,提高了电石的产量和纯度。
同时,通过改进反应器结构和工艺参数,还可以减少资源消耗和环境污染。
电石生产工艺在现代化工行业中具有重要的应用价值。
乙炔是一种多功能气体,在化学合成、照明、焊接和切割等领域具有广泛的应用。
电石生产工艺为乙炔的大规模生产提供了可靠的技术支持,为相关产业的发展做出了贡献。
总之,电石生产工艺是一种重要的化工生产过程,能够高效地生产乙炔和其他化工产品。
电石制备
电石生产工艺流程简介碳化钙(CaC2)俗称电石。
工业品呈灰色、黄褐色或黑色,含碳化钙较高的呈紫色。
其新创断面有光泽,在空气中吸收水分呈灰色或灰白色。
能导电,纯度愈高,导电性愈好。
在空气中能吸收水分。
加水分解成乙炔和氢氧化钙。
与氮气作用生成氰氨化钙。
电石是有机合成化学工业的基本原料之一。
是乙炔化工的重要原料。
由电石制取的乙炔广泛应用于金属焊接和切割。
生产方法有氧热法和电热法。
一般多采用电热法生产电石,即生石灰和含碳原料(焦炭、无烟煤或石油焦)在电石炉内,依靠电弧高温熔化反应而生成电石。
生产流程如图所示。
主要生产过程是:原料加工;配料;通过电炉上端的入口或管道将混合料加入电炉内,在开放或密闭的电炉中加热至2000℃左右,依下式反应生成电石:GaO+3C→CaC2+CO。
熔化了的碳化钙从炉底取出后,经冷却、破碎后作为成品包装。
反应中生成的一氧化碳则依电石炉的类型以不同方式排出:在开放炉中,一氧化碳在料面上燃烧,产生的火焰随同粉尘—起向外四散;在半密闭炉中,一氧化碳的一部分被安置于炉上的吸气罩抽出,剩余的部分仍在料面燃烧;在密闭炉中,全部一氧化碳被抽出。
(一)电石生产工艺过程烧好的石灰经破碎、筛分后,送入石灰仓贮藏,待用。
把符合电石生产需求的石灰和焦炭按规定的配比进行配料,用斗式提升机将炉料送至电炉炉顶料仓,经过料管向电炉内加料,炉料在电炉内经过电极电弧垫和炉料的电阻热反应生成电石。
电石定时出炉,放至电石锅内,经冷却后,破碎成一定要求的粒度规格,得到成品电石。
在电石炉中,电弧和电阻所产生的热把炉料加热至1900-2200℃,其总的化学反应式为: CaO+3C=CaC2+CO+10800千卡(二)电石炉生产工艺1、配料、上料和炉顶布料合格的原料由原料加工车间经计量、配料后,由斗式提升机送入电炉车间料仓内,由炉顶布料设施、固定胶带输送机和环形布料机将料送入炉顶环形料仓。
炉顶布料设施按需要把炉料布入料仓,由电炉加料管分批加入电炉内。
- 1、下载文档前请自行甄别文档内容的完整性,平台不提供额外的编辑、内容补充、找答案等附加服务。
- 2、"仅部分预览"的文档,不可在线预览部分如存在完整性等问题,可反馈申请退款(可完整预览的文档不适用该条件!)。
- 3、如文档侵犯您的权益,请联系客服反馈,我们会尽快为您处理(人工客服工作时间:9:00-18:30)。
灰分 ≤10.0%
挥发分 ≤6.0%
0.06
0.08
0.10 85 5
水分 ≤10.0% 粉末含量 ≤5.0% 1.6.4、电极糊 电极糊质量应符合如下条件: 灰分 ≤4.0% 挥发分 13.0%~14.5% 抗压强度 ≥19.6MPa 电阻率 ≤75μΩm 体积密度 ≥1.36t/m3 2、电石生产历史
另外一部分用于生产聚乙烯醇、石灰氮等。电石还用于钢铁的脱硫 剂、分析化学中的水分测试剂、用于农业果树等经济作物处理剂,现在 还有用于环保行业用作废水的脱硫剂等。 3、电石的生成机理 3.1、反应机理
炉料凭借电弧热和电阻热在1800~2200℃的高温下反应而制得碳化 钙,电炉是获得高温的最好设备,而且能量非常集中。
在水过剩条件下,即将碳化钙浸于水中,反应依下式进行: CaC2+H2O=Ca(OH)2+C2H2
被滴加水分解时,还发生如下反应: CaC2+Ca(OH)2=CaO+C2H2
吸收空气中水份而分解: CaC2+H2O=CaO+C2H2
1.2.2 在没有任何水份条件下,将电石在氢气流中加热至2200℃以上 时,就有相当量的乙炔发生:
电炉还原法生产碳化钙是目前工业生产碳化钙的唯一方法。 电石主要用途是生产聚氯乙烯,2006年全国电石产能为1700万吨, 共计产量为1171万吨,同比增长27.71%。电石炉开车率69.23%。共生产
聚氯乙烯823.86万吨,其中采用电石法生产的聚氯乙烯产量为589万 吨,理论消耗电石884万吨,消费电石量电石总产量的75.11%。2007年 全国电石产能突破2000万吨,产量达到1481.8万吨。2008年电石产量为 1361万吨。
CaC2+H2O=Ca+C2H2 当加热到2275℃时,所生成的钙开始升华。 1.2.3 在高温下,干燥的氧气能氧化碳化钙而生成碳酸钙。 1.2.4粉状电石与氮气在加热条件下,反应生成氰氨化钙:
CaC2+N2=CaCN2+C 1.2.5碳化钙能还原铅、锡、锌、铁、锰、镍、钴、铬、钼及钒的氧化
物。
1.2.6 电石中夹杂的磷的化合物,当电石与水作用时,生常温和大气压下为无色气体,工业乙炔因含有杂质(特别是
磷化氢)而有特殊的臭味。
1.3.2 乙炔的密度随着温度和压力的变化而变化,当温度在20℃和压力
为760毫米汞柱时,乙炔的密度为1.091kg/m3。
1.3.3 乙炔溶于水和酒精,极易溶于丙酮。在15℃和1大气压下1升丙酮
可溶解乙炔25升,在15大气压下,1升丙酮可溶解乙炔的345升。
860――电热,1度电能完全转化为热能的数值(千卡/度); 64――碳化钙的分子量 实际上,工业电石炉生产1吨电石的时候,所消耗的电能远远超过计 算所得的数值,可见大量的电能损失了。这些损失主要有以下几个方 面: (1) 电石炉中有许多副反应存在, CaC2=Ca+2C-14.5千卡 CaCO3=CaO+CO2-42.5千卡 CO2+C=2CO-39.3千卡 H2O+C=CO+H2-39.6千卡 Ca(OH)2=CaO+H2O-26千卡
把电石和石灰按不同的比例混合,并分别测定其共熔点,把它绘成图, 从这张图上可以找到在一定温度下,共熔的电石和石灰的比例,也就是 熔融电石的成份,如果有超过这个比例的多余电石,那么,在这个温度 下,这一部分电石就凝固出来。这张图就叫相平衡图。
如果有多量石灰存在时,不可能在电石炉里得到与石灰分开的纯电 石。而高质量的电石(成份在80%以上)也不是在电石炉一开始就生成 的,因为电石的熔点高,当它一生成就和周围的石灰共熔成熔较低的共 熔体流了下去,由于含69~70%电石的共熔体的熔点最低,所以生成的 电石-石灰共熔体,大多是这个成份。电石与石灰共熔的速度是很快 的,只要纯的电石一生成就与石灰共熔了。共熔体的电石成份一般不会 高于70%,因为配料比高时,焦炭还来不及反应生成电石,而配料比低 时,石灰倒很容易与之共熔,使电石冲淡(稀释)到70%以下。这样, 在电石炉里就有两个速度。一个是焦炭与石灰不断化合生成电石的“反 应速度”,另一个是生成的电石不断与石灰共熔而稀释的共熔速度,这 个速度叫做“稀释速度”。电石的反应速度是由什么来的?如果我们考虑 最理想的情况,即一个石灰的分子和三个碳原子直接相遇而发生反应, 在2000℃以上的温度下,反应速度是很快的,比共熔速度还快。但是在 电石炉内,焦炭是以块状存在的,而不是一个碳原子的易破碎存在的, 焦炭没有明显的熔点,直到3000℃时,它还是固体。到3537℃时才汽 化,所以在电炉里焦炭是始终不熔化的固体。这样,它的有限的反应接 触面就大大阻滞了与熔化石灰的反应速度,甚至比共熔的速度更慢。在 电炉里熔化的石灰-电石共熔体是怎样与多孔的焦炭反应?第一步是电 石-石灰共熔体中的石灰与焦炭块表面上的碳反应,同时石灰熔液不断 渗入焦炭的毛细孔中,一边渗入,一边就与碳素反应,生成电石而共 熔,使焦炭变松,反应时产生的一氧化碳又使变松的焦炭崩裂成小块。 第二步是未崩裂的和已崩裂成小块的焦炭,再不断被石灰熔液渗入,边 反应、边崩裂,有一些焦炭就分散成微粒,悬浮在电石-石灰共熔体 中。这时如果配比低,石灰过剩,那么焦炭微粒在共熔体中通过扩散, 不断反应直到全部反应成电石。如果配比高,石灰没有过剩,那么焦炭
CaSiO4=2CaO+SiO2-29千卡 SiO2+2C=Si+2CO-137千卡 Fe2O3+3C=2Fe+3CO-108千卡 Al2O3+3C=2Al+3CO-291千卡 MgO+C=Mg+CO-116千卡 以上的反应都是吸热反应,都要消耗热量。 (2) 电石炉气和被炉气带走的粉尘及出炉电石所带走的显热; (3) 消耗在电炉变压器、短网、电极以及通过炉体的热损失等
1.3.4.2 乙炔和与它能起反应的气体的混合物具有较强的爆炸能力。
乙炔与氧混合时,如将混合物加热至300℃以上,则乙炔在大气压下
即行爆炸。
乙炔与氯混合时,在日光作用下就会爆炸。
乙炔与氧混合物的爆炸范围为2.3~93%(乙炔在氧气中的浓度)。 乙炔与空气混合物的爆炸范围为2.3~81%(乙炔在空气中的浓 度)。 1.3.4.3 当乙炔被某溶剂溶解时,乙炔的爆炸能力就降低。湿乙炔比 干乙炔的爆炸能力低关随着湿度的增高而减小。当水蒸汽与乙炔之体积 比为1:1.15时,通常不会发生爆炸。 1.3.4.4 在高分解压力与温度,容器的尺寸很大或管道很长时,乙炔会 发生爆震现象。爆震的传播速度为1800米/秒~3000米/秒,爆震时所发 生的局部压力达到600大气压。 1.3.4.5当乙炔与铜盐、银盐及汞盐的水溶液相互作用时,能生成各种 金属乙炔的沉淀物,此沉淀物具有爆炸性。 1.4工业电石的组成 工业电石中碳化钙含量常为65%~90%,其余为杂质。如碳化钙含量 为85.3%的电石,其大致组成如下: 碳化钙(CaC2) 85.3% 氧化钙(CaO) 9.5% 二氧化硅(SiO2) 2.1% 氧化铁和氧化铝(Fe2O3+Al2O3) 1.45% 氧化镁(MgO) 0.35% 碳(C) 1.2% 1.5 电石的质量标准 电石质量符合GB10665-2004标准。
1.3.4 乙炔的化学性质
1.3.4.1 乙炔属于不饱和烃,不稳定,在一定条件下,较易发生分解爆
炸,而且和与它能起反应的气体的混合物也会发生爆炸。
乙炔在高温高压下,具有分解爆炸的危险性。如压力为1.5表压以上
的工业乙炔,在温度超过550℃时,则可能使全部乙炔发生分解爆炸。
其反应式为:
C2H2=2C+H2+16.75MJ 当温度低于500℃,有接触剂存在时,也可能发生爆炸。
的微粒与共熔体中的大部分熔化石灰反应石生成电石。这种电石-石灰 共熔体中,石灰的含量极少,甚至还有多量分散而没有与石灰反应的焦 炭微粒,留存在电石中。
3.2关于电石-石灰的相平衡
在电石炉内存在两种速度,除了化学反应的“反应速度”之外,还有 另一种情况,就是石灰会很快熔化在生成的电石之中,它也有一个速 度。原来电石和石灰单独存在的时候,都有很高的熔点,纯电石熔点为 2300℃,纯石灰的熔点为2580℃。但是两者碰在一起,熔点就降低了。 熔点可降到比石灰和电石的熔点都要低,这个熔点叫做“共熔点”,而且 这个共熔点又是不固定的,它随着电石和石灰混合的比例不同而不同。
等。 理论消耗氧化钙=1000÷64×56=875公斤 理论消耗碳素=1000÷64×36=563公斤 所以理论炉料配比=563/875=64.3
电石的反应机理到目前为止还没有成熟的理论,一般的说法是: 以固态反应生成CaC2, CaO+C=CaO·C(互相扩散态) CaO·C(互相扩散态)=Ca+CO Ca+2C=CaC2 并有:mCaC2+nCaO=mCaC2·nCaO mCaC2·nCaO=(m-1)CaC2·(n-2)CaO=3Ca+2CO
电石生产工艺简介 1 产品说明 1.1 简介
化学名:碳化钙 工业名:电石(英文名:Calcium carbide) 分子式:CaC2
结构式:
分子量:64.10 1.2电石的化学性质
电石的化学性质很活泼,在适当温度下能与许多的气体、液体发生 化学反应。 1.2.1碳化钙不仅能被液态的或气态的水所分解,而且也能被物理的或 化学结合的水所分解。
1892年法国人H·迈桑和美国人T·L·威尔森同时开发出了电炉还原制 取碳化钙的方法。美国于1895年实现了工业化生产。当时电炉容量很 小,只有100~300kVA,一般采用单相电极,间歇操作,产量也很低。 当时电石产品主要用于点灯,后用于金属切割。
到二十世纪初,用电石生产石灰氮的方法问世后,电石生产逐渐有 所发展。出现了自动烧结电极和半密闭电石炉,电炉容量逐渐扩大。到 二十世纪二、三十年代,通过电石乙炔合成有机化工工业兴起,促进了 电石生产的大力发展。挪威和德国先后发明了埃肯炉和德马克炉,直至 现在世界主要的密闭炉炉型均出自于该两种炉型。美国对电石生产技术 作出了巨大的贡献,研制成功了空心电极以及计算机控制的全自动操纵 电炉的技术,尤其是计算机监控和观测电极糊软化烧结情况,避免了电 极事故的发生,通过计算机测量、控制电极工作端长度,保持电石炉在 恒定功率运行。并且电石炉容量不断向大型化发展,德国建成 75000kVA的电石炉,日本也建成了80000kVA以上的电石炉,并完善了 空心电极技术。