柴油机曲轴工艺设计方案[]
单缸柴油机曲轴课程设计

单缸柴油机曲轴课程设计一、课程目标知识目标:1. 学生能够理解单缸柴油机的结构组成,特别是曲轴的作用及其在发动机中的地位;2. 学生能够掌握曲轴的基本工作原理,包括转速与扭矩的转换关系;3. 学生能够描述曲轴的常见故障及其原因。
技能目标:1. 学生能够通过实际操作识别单缸柴油机的曲轴,并展示其工作原理;2. 学生能够运用所学的知识分析曲轴故障案例,提出合理的维修与保养建议;3. 学生能够设计简单的曲轴维修保养流程,并进行模拟操作。
情感态度价值观目标:1. 学生培养对机械工程领域的兴趣,特别是对柴油机这一传统工业产品的认识与尊重;2. 学生通过学习曲轴相关知识,增强对机械设备结构与功能的探索欲望,激发创新意识;3. 学生在学习过程中,培养团队合作精神,提高解决问题的能力和责任意识。
课程性质:本课程为实践性较强的技术学科课程,要求学生结合理论知识与实际操作,深入理解单缸柴油机曲轴的相关知识。
学生特点:考虑到学生年级特点,课程内容设计需兼顾知识性与趣味性,以激发学生的学习兴趣和动手操作的欲望。
教学要求:教学内容应紧密结合课本,通过实物展示、案例分析等教学方法,提高学生对曲轴知识的掌握与应用能力,同时注重培养学生的实践操作技能和解决问题的能力。
通过分解课程目标为具体的学习成果,为教学设计和评估提供明确的方向。
二、教学内容1. 引入概念:介绍单缸柴油机的整体结构,强调曲轴在发动机工作过程中的关键作用。
相关教材章节:第一章《内燃机概述》2. 理论知识:详细讲解曲轴的构造、工作原理及其与发动机性能的关联。
相关教材章节:第二章《曲柄连杆机构》3. 实物教学:通过拆解与组装单缸柴油机模型,直观展示曲轴及其附属部件。
相关教材章节:第三章《发动机主要部件》4. 故障分析:分析曲轴常见故障类型及其原因,如磨损、断裂等。
相关教材章节:第五章《发动机常见故障与维修》5. 维修与保养:介绍曲轴的维修方法、保养技巧及注意事项。
发动机6112曲轴国产化工艺设计

4 结论本系统的研制完全立足于国产化目标,通过实机运行考核,系统运行稳定、可靠,适用于发动机行业做缸内燃烧过程的测量和分析。
系统组合与国外同类产品相当,性能良好,操作使用方便。
采用光栅角标信号发生器使采样基本无漏码。
因而,该系统在功能和性能方面达到了国外同类产品的先进水平,对从事内燃机设计、研制、生产开发工作的用户来说,具有广泛的应用前景。
作者简介:段绍林,男,汉族,四川南充人,高工。
6112曲轴国产化工艺设计段绍林,王 仲(机械工业部第三设计院,重庆400039) 摘要:介绍广西玉柴机器股份有限公司引进福特公司的YC 6112柴油机曲轴的生产纲领、制造工艺以及国产化设计和国产化工艺流程。
曲轴国产化为国家节约了大量外汇,具有显著的经济效益和社会效益。
关键词:6112柴油机;曲轴;制造工艺中图分类号:TK 423.3+1 文献标识码:B 文章编号:1000-6494(2000)06-0015-05D esign of Na tiona l ized Techn ique for 6112Crankshaf tDUAN Shao 2lin ,WAN G Zhong(T h ird D esign and R esearch Institute ,MM I ,Chongqing 400039,Ch ina )Abstract :T h is paper introduces p roducti on p rogram ,m anufacturing techno logy ,nati onalized design and nati onalized techno logical p rocess of YC 6112diesel engine crank shaft i m po rted by Guangxi YuchaiM ach inery Jo int 2stock Co .,L td ..N ati onalizati on of crank shaft econom izes on a large num ber of fo reign currency fo r our country and ach ieves rem arkable econom ic results in society .Key words :6112diesel engine ;crank shaft ;m anufacturing technique 玉柴YC 6112系列柴油机是引进福特公司的系列产品,6112柴油机是福特公司发动机工程部历时四年开发成功的系列产品,1989年投产。
柴油机曲轴工艺过程及夹具毕业设计论文

重庆大学网络教育学院毕业设计(论文)柴油机曲轴零件加工工艺及夹具设计学生所在校外学习中心江苏张家港校处学习中心批次层次专业111 专升本机械设计制造及其自动化学号 w11107861学生指导教师起止日期 2013.1.21--2013.4.14摘要曲轴是发动机上的一个重要的旋转机件,装上连杆后,可承接活塞的上下(往复)运动变成循环运动。
曲轴主要有两个重要加工部位:主轴颈和连杆颈。
主轴颈被安装在缸体上,连杆颈与连杆大头孔连接,连杆小头孔与汽缸活塞连接,是一个典型的曲柄滑块机构。
发动机工作过程就是:活塞经过混合压缩气的燃爆,推动活塞做直线运动,并通过连杆将力传给曲轴,由曲轴将直线运动转变为旋转运动。
而曲轴加工的好坏将直接影响着发动机整体性能的表现。
曲轴的材料是由碳素结构钢或球墨铸铁制成的,有两个重要部位:主轴颈,连杆颈。
这次毕业设计介绍柴油机曲轴加工工艺规程及相关夹具的设计,及曲轴的规程制定中遇到问题的分析,经济性分析,工时定额,切削用量的计算。
同时还介绍曲轴加工中用到的两套夹具的设计过程。
在工艺设计中,结合实际进行设计,对曲轴生产工艺进行了改进,优化了工艺过程和工艺装备,使曲轴的生产加工更经济、合理。
根据现阶段机械零件的制造工艺和技术水平,本着以制造技术的先进性,合理性,经济性进行零件的形状、尺寸、精度等级、表面粗糙度、材料等技术分析。
并根据以上分析来选择合理的毛坯制造方法,设计工艺规程,夹具设计。
关键词:柴油机曲轴工艺夹具目录中文摘要 (I)1.引言 (1)2.曲轴的生产纲领 (2)3.零件的分析 (2)3.1曲轴的用途及工作条件 (2)3.2分析零件上的技术要求,确定要加工的表面 (3)3.3加工表面的尺寸和形状精度 (4)3.4尺寸和位置精度 (4)3.5加工表面的粗糙度及其它方面的质量要求 (4)3.6热处理要求 (4)4.曲轴材料和毛坯的定 (4)4.1确定毛坯的类型 (4)4.2确定毛坯的生产方法 (4)4.3确定毛坯的加工余量 (4)5.曲轴的工艺过程设计 (5)5.1粗、精加工的定位基准 (5)5.1.1粗加工 (5)5.1.2粗加工 (5)5.2工件表面加工方法的选择 (5)5.3曲轴机械加工的基本路线 (5)5.4加工余量及毛坯尺寸 (6)5.5工序设计 (6)5.5.1加工设备与工艺装备的选择 (8)5.5.2机械加工余量、工序尺寸及公差的确定 (9)5.6确定工时定额 (11)5.7机械加工工艺规程卡片和机械加工工序卡片 (12)5.7.1机械加工工艺过程卡片 (12)5.7.2机械加工工序卡片 (12)6.柴油机曲轴加工键槽夹具设计 (13)6.1.1夹具类型的分析 (13)6.1.2工装夹具定位方案的确定 (13)6.1.3工件夹紧形式的确定 (13)6.1.4对刀装置 (13)6.1.5分度装置的确定以及补补助装置 (14)6.1.6夹具定位夹紧方案的分析论证 (14)6.1.7夹具结构类型的设计 (15)6.2夹具总图设计 (16)6.4绘制夹具零件图 (16)7.结论 (17)8.参考文献 (18)1.引言曲轴是内燃机中的重要零件之一,是承受冲击载荷传递动力的关键零件,在内燃机五大件(机体、缸盖、曲轴、连杆、凸轮轴)中是最难以保证加工质量的零件。
本科毕业设计-柴油机曲轴设计

1前言1.1柴油机与曲轴1.1.1柴油机的工作原理柴油机的每个工作循环都要经历进气、压缩、做功和排气四个过程。
四行程柴油机的工作过程:柴油机在进气冲程吸入纯空气,在压缩冲程接近终了时,柴油经喷油泵将油压提高到10MPa以上,通过喷油器以雾状喷入气缸,在很短时间内与压缩后的高温空气混合,形成可燃混合气。
压缩终了时气缸内空气压力可达3.5~4.5MPa,温度高达476.85℃~726.85℃,极大地超过柴油的自燃温度,因此柴油喷人气缸后,在很短的时间内即着火燃烧,燃气压力急剧达到6~9MPa,温度升高到1726.85℃~2226.85℃。
在高压气体推动下,活塞向下运动并带动曲轴旋转做功。
废气同样经排气门、排气管等处排出。
四行程柴油机的每个工作循环均经过如下四个行程:(1)进气行程在这个行程中,进气门开启,排气门关闭,气缸与化油器相通,活塞由上止点向下止点移动,活塞上方容积增大,气缸内产生一定的真空度。
可燃混合气被吸人气缸内。
活塞行至下止点时,曲轴转过半周,进气门关闭,进气行程结束。
由于进气道的阻力,进气终了时气缸内的气体压力稍低于大气压,约为0.07~0.09MPa。
混合气进入气缸后,与气缸壁、活塞等高温机件接触,并与上一循环的高温残余废气相混合,所以温度上升到96.85℃~126.85℃。
(2)压缩行程进气行程结束后,进气门、排气门同时关闭。
曲轴继续旋转,活塞由下止点向上止点移动,活塞上方的容积缩小,进入到气缸中的混合气逐渐被压缩,使其温度、压力升高。
活塞到上止点时,压缩行程结束。
压缩终了时鼓,混合气温度约为326.85℃~426.85℃,压力一般为0.6~1.2MPa。
(3)做功行程活塞带动曲轴转动,曲轴通过转动把扭矩输出。
(4)排气行程进气口关闭,排气口打开,排除废气。
由上可知,四行程汽油机或柴油机,在一个工作循环中,只有一个行程作功,其余三个行程作为辅助行程都是为作功行程创造条件的。
因此,单缸发动机工作不平稳。
曲轴生产工艺流程
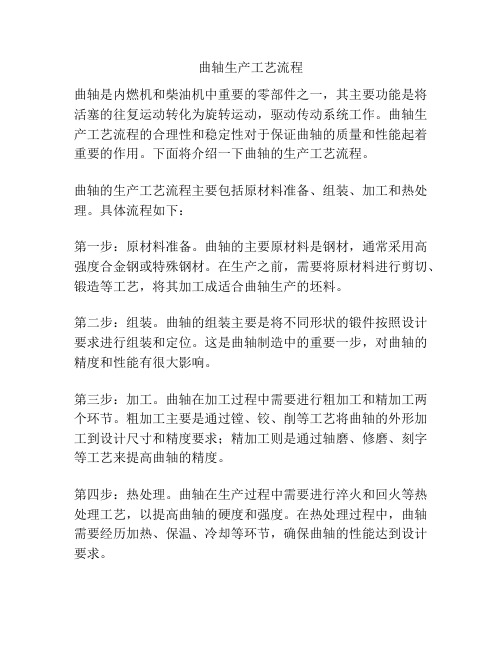
曲轴生产工艺流程
曲轴是内燃机和柴油机中重要的零部件之一,其主要功能是将活塞的往复运动转化为旋转运动,驱动传动系统工作。
曲轴生产工艺流程的合理性和稳定性对于保证曲轴的质量和性能起着重要的作用。
下面将介绍一下曲轴的生产工艺流程。
曲轴的生产工艺流程主要包括原材料准备、组装、加工和热处理。
具体流程如下:
第一步:原材料准备。
曲轴的主要原材料是钢材,通常采用高强度合金钢或特殊钢材。
在生产之前,需要将原材料进行剪切、锻造等工艺,将其加工成适合曲轴生产的坯料。
第二步:组装。
曲轴的组装主要是将不同形状的锻件按照设计要求进行组装和定位。
这是曲轴制造中的重要一步,对曲轴的精度和性能有很大影响。
第三步:加工。
曲轴在加工过程中需要进行粗加工和精加工两个环节。
粗加工主要是通过镗、铰、削等工艺将曲轴的外形加工到设计尺寸和精度要求;精加工则是通过轴磨、修磨、刻字等工艺来提高曲轴的精度。
第四步:热处理。
曲轴在生产过程中需要进行淬火和回火等热处理工艺,以提高曲轴的硬度和强度。
在热处理过程中,曲轴需要经历加热、保温、冷却等环节,确保曲轴的性能达到设计要求。
第五步:检测和质量控制。
曲轴生产完成后需要进行各项质量检测,确保曲轴的尺寸、硬度、表面质量等符合标准要求。
如果出现不合格品,需要及时进行返修或淘汰处理。
以上就是曲轴生产工艺流程的简要介绍。
在实际生产中,每个步骤都需要严格控制和把握,确保曲轴的质量和性能。
随着科技的发展和生产技术的提高,曲轴生产工艺也在不断的创新和改进,以适应不同类型发动机的需求和要求。
大型船用中速柴油机曲轴工艺设计

曲轴 淬火 机 床 上设 置 有 三 种 感 应 器 ,分 别 自动
重要因素 ,淬火冷却介质的浓度越 大,其冷却能力 越差 , 相对淬火 硬度低 。淬火冷却介质 的冷却速 度
是 影 响淬火 质 量 的决 定 性 因素 ,为 保 证 工 件 表 面 淬
对 曲轴 主 轴 颈 、曲 柄 销 和止 推 轴 承 两 侧 进 行 中频 淬 火 。淬 火机 床 的 感 应 器 独 立悬 挂 平衡 机 构 、数 控 浮
大型船用中速柴油机曲轴工艺设计
青 岛淄柴博 洋柴油机股份 有限公 司 ( 山东 2 60 ) 邱前进 67 0 张严芳 丁 晓
曲轴 是 柴 油 机 用 于 传 递 功率 的关 键 零 部 件 ,在 大 型船用 柴 油机 曲轴 的长 径 比较 大 ,刚 性较 差 ,
柴 油机 的工 作 循 环 中, 曲轴 承 受周 期 性 不 断变 化 的 压力 、往 复运 动 的惯 性 力 、旋 转 质 量 的离 心 惯 性 力 及力 矩等 复杂 的交 变 载 荷 ,承受 拉 、压 、弯 和磨 损 , 因此 要 求 曲轴 应 具 备 有 足 够 的强 度 、 刚 性 、韧 性 、
耐磨性 及 良好 的平衡性 。
尺 寸 、形位 公差 精 度 较 高 ,因此 加工 工 艺 比较 复 杂 。 柴 油 机 曲 轴 有 6 缸 、 8 缸 两 种 ,6 缸 曲 轴 长
4055 m, 8.m 8缸曲轴长 51 .m 1 5 m,主轴颈 t 9m 5 h 5 m, 2
连杆 轴颈 4 8 m , 0 m,材料 为 ¥ 4 Y,轴 颈及 止 推 面淬 2 4S 火处 理 。图 1 为某 船用 中速 柴油 机 8缸 曲轴 的外形 。
( )连 杆 轴 颈 的 加 工 曲 轴 连 杆 轴 颈 的 加 工 4 在 双头 曲轴 车 床 上 完 成 ,根 据 车 床 的 结 构 和 曲 轴 加工 的要 求 ,设 计 了 曲 轴 车 床 专 用 夹 具 。该 夹 具
四缸柴油机曲轴工艺工装设计
毕业设计(论文)说明书题目四缸柴油机曲轴工艺工装设计学生系别专业班级学号指导教师摘要在这次毕业设计中,进行了曲轴的测绘及根据实物模型了解曲轴的外型和曲轴斜油孔的位置结构。
本设计为四缸柴油机曲轴工艺工装设计:绘制曲轴零件图、确定加工方法、制定加工工艺、编制加工工序卡、曲轴斜油孔加工的工装设计。
曲轴由轴颈和轴柄构成。
曲轴是受冲击载荷、传递动力的重要零件,在五大件中最难以保证加工质量。
由于曲轴工作条件恶劣,因此对曲轴材质以及毛坯加工技术、精度、表面粗糙度、热处理和表面强化、动平衡等要求都十分严格。
如果其中任何一个环节质量没有得到保证,则可严重影响曲轴的使用寿命和整机的可靠性。
曲轴材质有球墨铸铁和钢两类。
由于球墨铸铁的切削性能良好,可获得较理想的结构形状,并且和钢质曲轴一样可以进行各种热处理和表面强化处理来提高曲轴的抗疲劳强度、硬度和耐磨性。
球墨铸铁曲轴成本只有调质钢曲轴成本的1/3左右,所以球墨铸铁曲轴在国内外得到了广泛应用。
关键词:曲轴斜油孔工装设计可靠疲劳强度球墨铸铁1ABSTRACTIn this graduation project, has carried on the crank mapping and the basis working model understands the crank the outlook and the tune axle tilt oil hole position structure.This design is four cylinder diesel engine crank craft work clothes design: Plan crank detail drawing, determination processing method, formulation processing craft, establishment processing travel chart, tune axle tilt oil hole processing work clothes design.The crank constitutes by the journal and the axis handle.The crank is in the engine withstands the impact load, the transmission power important components, guarantees the processing quality most with difficulty in the engine five big-ticket items.Because the crank working condition is bad, therefore to the crank material quality as well as the semifinished materials processing technology, the precision, the surface roughness, the heat treatment and the surface strengthens, requests and so on transient equilibrium extremely is all strict.If any link quality has not obtained the guarantee, then may affect the crank seriously the service life and the complete machine reliability.The crank material quality has the modular cast iron and the steel two kinds.Because the modular cast iron cutting value is good, may obtain the ideal structure shape, and may carry on each kind of heat treatment and superficial strengthening processing equally with the steel crank enhances the crank the anti-fatigue strength, degree of hardness and the resistance to wear.Modular cast iron crank cost only then about quenched and tempered steel crank cost 1/3, therefore the modular cast iron crank in domestic and foreign obtained the widespread application.Key word:Cranks Slanting oil holes Work clothes designs Reliability Fatigue strength Modular cast irons.II目录摘要 (Ⅰ)Abstract.......................................................................................... . (Ⅱ)第1章设计的相关知识 (1)1.1 毕业设计的目的、要求和内容 (1)1.1.1 毕业设计的目的 (1)1.1.2 毕业设计的基本要求及主要内容 (1)1.2 毕业设计的步骤 (2)1.2.1机械加工工艺规程设计 (2)第二章零件的分析 (3)2.1 零件的作用及分析 (3)2.2 曲轴的制造技术及工艺进展.............................................................................. . (3)2.2.1 曲轴的毛坯制造技术 (3)2.2.2 机械加工技术 (4)2.2.3 热处理和表面强化处理技术 (4)第三章零件的工艺路线及加工工艺 (5)3.1拟定工艺路线应注意的事项 (5)3.2 零件的工艺路线 (6)3.2.1 基准的选择 (6)3.2.2 曲轴工艺路线内容 (6)3.2.3 零件加工工序内容 (7)第四章专用夹具设计及撰写说明 (35)4.1 专用夹具设计 (35)4.1.1 设计说明 (35)4.1.2 夹具设计分析 (35)4.2 撰写说明书应注意的事项 (36)第五章结论 (37)参考文献 (38)致谢 (39)XX大学毕业设计第一章设计的相关知识1.1 毕业设计的目的、要求和内容了解毕业设计的目的和要求能知道设计的重要性。
柴油机曲柄工艺说明书
柴油机曲柄工艺规程及专用夹具设计说明书目录第一章柴油机曲柄加工工艺规程步骤和内容1.1 零件的工艺分析1.2 确定毛坯、绘制毛坯简图1.3拟定曲柄工艺路线1.4机床设备及工艺装备的选用第二章加工余量和加工尺寸的确定2.1加工余量、工序尺寸和公差的确定2.2切削用量、时间定额的计算第一章 柴油机曲柄加工工艺规程设计1.1 零件的工艺分析 一、柴油机曲柄的用途柴油机中,曲柄通常称为曲轴,起旋转作用;活塞由燃气作功作往复运动;连杆联结活塞与曲轴。
二、曲柄的技术要求 加工表面 mm尺寸及偏差公差及精度等级mRaμ表面粗糙度形位公差/mm曲柄左端面 64 IT12 3.2曲柄右端面 64 IT12 3.2①面 18005.0-IT9 3.2 ⊥ 0.03 A②面28033.00+IT8 3.2 φ12的孔 φ12018.00+ IT7 1.6φ16的孔 φ16027.00+ IT8 1.6 ∥ φ0.02 Aφ5的孔φ5IT12 3.2 M6螺纹孔 M6IT123.2三、确定曲柄的生产类型 计算零件体积:公式:V=(π×162-π×82)×18×2+(π×112-π×62)+2×23×6×6 =41280.908mm 3m=v ρ=41280.908×109-×7.8×103=0.322kg已知N=500件/年,根据书上表1-3和表1-4可判定此为轻型零件且为小批量生产。
1.2确定毛坯、绘制毛坯简图一、铸件尺寸公差与机械加工余量(摘自GB/T6414-1999) 1、 基本概念⑴ 铸件基本尺寸 机械加工前的毛坯铸件的尺寸,包括必要的机械加工余量(图2-1)。
⑵ 尺寸公差 允许尺寸的变动量。
公差等于最大极限尺寸与最小极限尺寸之代数差的绝对值;也等于上偏差与下偏差之代数差的绝对值。
⑶ 错型 由于合型时的错位,逐渐的一部分与另一部分在分型面处相互错开。
船用低速柴油机组装式曲轴制造工艺与设备
I(盏豢)l
l {}口】] 7了寸田 T’LJ‘∞11●
深孔加工 ( 数控深孔钻
半精车各部 ( 重型车床)
抽哪尉。
l 麓,l ∞纂蓦麓
2) 曲拐外廓、开档、主轴孔、曲柄轴粗加一
精车各部 ( 数控重车)
工, 小端圆锥 面及曲 轴轴心 孔不加工 。主轴 孔 如用割炬切出要留出热影响区。
精车主轴孔各部 ( 数控曲拐车床)
【Abst 旧ct 】A娼embl y c髓nksk岔s功圳l 丘ccI l 陀a bi l i t y c蛆 唧缁 em
出e 1evd of a cou唧’s shi pbui l di I lg i I l dus 町,bec 撒吐忙觚enl l )l y
∞砌【shmweigbt i ssol argeand甜s础幽cn腓t echl l icis so c伽叩lex
sel ecd on
是由锻造和铸造的曲拐组装或焊接的组装式曲轴, 组装式曲轴主要用于大型船舶和发电用低速二冲程 柴油发动机阁。
随着我国船舶工业的迅速发展,目前我国造船 业对船用锻件的要求急剧上升,这就要求我国的锻 件制造厂家改变观念,尽快 开发出新锻件和新工艺, 满足造船业的要求嘲。由于组装式曲轴重量大、加工、 制造技术难度高,其制造能力代表了一个国家的造 船工业水平。以往相当长时间里,只有日本、韩国、捷 克、西班牙、 波兰等少数几个国家具备制 造大型船用 半组合式曲轴能力【4】。目前,在我国上海船用曲轴有 限公司和大连重工·起重集团曲轴公司已实现国产 化,为我国的造船业发展打破了曲轴这个“瓶颈”。下 面主要介绍一下船用组装式曲轴的具体制造工艺过 程及其主要的加工设备选型。
用传动端曲拐单元作为基础精车主轴孔各部数控曲拐车床中间轴锻件xl推力轴锻件粗车各部重型车床深孔加工数控深孔钻半精车各部重型车床精车各部数控重车曲拐主轴颈预热装轮轴压装机曲轴整体热装曲轴热装机精车各部数控曲轴车床镗各部孔铣键槽数控落地铣镗床检验入库图3曲轴加工装配工艺流程图粗车各部重型车床深孔加工数控深孔钻半精车各部重型车床精车各部数控重车3主要加工设备选型31重型车床法兰轴中间轴及推力轴经粗加工后为减少在数控重车上精加工工序的劳动量先用重型车床进行半精加工
柴油机曲轴工艺过程及夹具设计
柴油机曲轴⼯艺过程及夹具设计重庆⼤学⽹络教育学院毕业设计(论⽂)柴油机曲轴零件加⼯⼯艺及夹具设计学⽣所在校外学习中⼼江苏张家港校处学习中⼼批次层次专业111 专升本机械设计制造及其⾃动化学号 w11107861学⽣指导教师起⽌⽇期 2013.1.21--2013.4.14摘要曲轴是发动机上的⼀个重要的旋转机件,装上连杆后,可承接活塞的上下(往复)运动变成循环运动。
曲轴主要有两个重要加⼯部位:主轴颈和连杆颈。
主轴颈被安装在缸体上,连杆颈与连杆⼤头孔连接,连杆⼩头孔与汽缸活塞连接,是⼀个典型的曲柄滑块机构。
发动机⼯作过程就是:活塞经过混合压缩⽓的燃爆,推动活塞做直线运动,并通过连杆将⼒传给曲轴,由曲轴将直线运动转变为旋转运动。
⽽曲轴加⼯的好坏将直接影响着发动机整体性能的表现。
曲轴的材料是由碳素结构钢或球墨铸铁制成的,有两个重要部位:主轴颈,连杆颈。
这次毕业设计介绍柴油机曲轴加⼯⼯艺规程及相关夹具的设计,及曲轴的规程制定中遇到问题的分析,经济性分析,⼯时定额,切削⽤量的计算。
同时还介绍曲轴加⼯中⽤到的两套夹具的设计过程。
在⼯艺设计中,结合实际进⾏设计,对曲轴⽣产⼯艺进⾏了改进,优化了⼯艺过程和⼯艺装备,使曲轴的⽣产加⼯更经济、合理。
根据现阶段机械零件的制造⼯艺和技术⽔平,本着以制造技术的先进性,合理性,经济性进⾏零件的形状、尺⼨、精度等级、表⾯粗糙度、材料等技术分析。
并根据以上分析来选择合理的⽑坯制造⽅法,设计⼯艺规程,夹具设计。
关键词:柴油机曲轴⼯艺夹具⽬录中⽂摘要 (I)1.引⾔ (1)2.曲轴的⽣产纲领 (2)3.零件的分析 (2)3.1曲轴的⽤途及⼯作条件 (2)3.2分析零件上的技术要求,确定要加⼯的表⾯ (3)3.3加⼯表⾯的尺⼨和形状精度 (4)3.4尺⼨和位置精度 (4)3.5加⼯表⾯的粗糙度及其它⽅⾯的质量要求 (4)3.6热处理要求 (4)4.曲轴材料和⽑坯的定 (4)4.1确定⽑坯的类型 (4)4.2确定⽑坯的⽣产⽅法 (4)4.3确定⽑坯的加⼯余量 (4)5.曲轴的⼯艺过程设计 (5)5.1粗、精加⼯的定位基准 (5)5.1.1粗加⼯ (5)5.1.2粗加⼯ (5)5.2⼯件表⾯加⼯⽅法的选择 (5)5.3曲轴机械加⼯的基本路线 (5)5.4加⼯余量及⽑坯尺⼨ (6)5.5⼯序设计 (6)5.5.1加⼯设备与⼯艺装备的选择 (8)5.5.2机械加⼯余量、⼯序尺⼨及公差的确定 (9)5.6确定⼯时定额 (11)5.7机械加⼯⼯艺规程卡⽚和机械加⼯⼯序卡⽚ (12)5.7.1机械加⼯⼯艺过程卡⽚ (12)5.7.2机械加⼯⼯序卡⽚ (12)6.柴油机曲轴加⼯键槽夹具设计 (13)6.1.1夹具类型的分析 (13)6.1.2⼯装夹具定位⽅案的确定 (13)6.1.3⼯件夹紧形式的确定 (13)6.1.4对⼑装置 (13)6.1.5分度装置的确定以及补补助装置 (14)6.1.6夹具定位夹紧⽅案的分析论证 (14)6.1.7夹具结构类型的设计 (15)6.2夹具总图设计 (16)6.4绘制夹具零件图 (16)7.结论 (17)8.参考⽂献 (18)1.引⾔曲轴是内燃机中的重要零件之⼀,是承受冲击载荷传递动⼒的关键零件,在内燃机五⼤件(机体、缸盖、曲轴、连杆、凸轮轴)中是最难以保证加⼯质量的零件。
- 1、下载文档前请自行甄别文档内容的完整性,平台不提供额外的编辑、内容补充、找答案等附加服务。
- 2、"仅部分预览"的文档,不可在线预览部分如存在完整性等问题,可反馈申请退款(可完整预览的文档不适用该条件!)。
- 3、如文档侵犯您的权益,请联系客服反馈,我们会尽快为您处理(人工客服工作时间:9:00-18:30)。
0 引言本次毕业设计是关于R180柴油机曲轴的工艺设计及其中两道工序的夹具设计。
曲轴是柴油机中的关键零件之一,其材质大体分为两类:一是钢锻曲轴,二是球墨铸铁曲轴。
由于采用铸造方法可获得较为理想的结构形状,从而减轻质量,且机加工余量随铸造工艺水平的提高而减小。
球铁的切削性能良好,并和钢制曲轴一样可以进行各种热处理和表面强化处理,来提高曲轴的抗疲劳强度和耐磨性。
而且球铁中的内摩擦所耗功比钢大,减小了工作时的扭转振动的振幅和应力,应力集中也没有钢制曲轴来的敏感。
所以球墨铸铁曲轴在国内外得到广泛采用。
本次设计中曲轴的材质为球铁。
从目前整体水平来看, 毛坯的铸造工艺存在生产效率低,工艺装备落后,毛坯机械性能不稳定、精度低、废品率高等问题。
从以下几个工艺环节采取措施对提高曲轴质量具有普遍意义。
①熔炼国内外一致认为,高温低硫纯净铁水的获得是生产高质量球铁的关键所在。
为获得高温低硫磷的纯净铁水,可用冲天炉熔化铁水,经炉外脱硫,然后在感应电炉中升温并调整成分。
②球化处理③孕育处理冲天炉熔化球铁原铁水,对铜钼合金球铁采用二次孕育。
这对于防止孕育衰退,改善石墨形态,细化石墨及保证高强度球铁机械性能具有重要作用。
④合金化配合好铜和钼的比例对形成珠光体组织十分有利,可提高球铁的强度,而且铜和钼还可大大降低球铁件对壁厚的敏感性。
⑤造型工艺气流冲击造型工艺优于粘土砂造型工艺,可获得高精度的曲轴铸件,该工艺制作的砂型具有无反弹变形量的特点,这对于多拐曲轴尤为重要。
⑥浇注冷却工艺采用立浇—立冷,斜浇—斜冷、斜浇—反斜冷三种浇注方式较为理想,其中后一种最好。
斜浇—反斜冷的优点是:型腔排气充分,铁水充型平稳,浇注系统撇渣效果好,冒口对铸件的补缩效果好,适应大批量流水线生产。
目前,国内大部分专业厂家普遍采用普通机床和专用组合机床组成的流水线生产,生产效率、自动化程度较低。
曲轴的关键技术工程仍与国外相差1~2个数量级。
国外的机加工工艺大致可归纳为如下几个特点。
①广泛采用数控技术和自动线,生产线一般由几段独立的自动化生产单元组成,具有很高的灵活性和适应性。
采用龙门式自动上下料,集放式机动滚道传输,切削液分粗加工与精加工两段集中供应和回收处理。
②曲轴的主要加工工序基准中心孔,一般采用质量定心加工方式,这样在静平衡时,加工量很少。
③轴颈的粗加工一般采用数控铣削或车拉工艺。
工序质量可达到国内粗磨后的水平,且切削变形小、效率高。
铣削和车拉是曲轴粗加工的发展方向。
④国外的曲轴磨床均采用CNC控制技术,具有自动进给、自动修正砂轮、自动补偿和自动分度功能,使曲轴的磨削精度和效率显著提高。
⑤油孔的加工采用鼓轮钻床和自动线,近几年随着枪钻技术的应用,油孔的加工大多已采用枪钻自动线钻孔—修缘—抛光。
⑥曲轴的抛光采用CNC控制的砂带抛光机,所有轴颈一次抛光只需20多秒,粗糙度可达Ra0.4以下,大大减小了发动机的磨合期。
⑦动平衡一般采用CNC控制的综合平衡机,测量、修正一次完成。
⑧检验一般在生产线上配备MARPOSS或HOMWORK综合检测机,实现在线检测,对曲轴的几乎所有机加工工程均可一次完成检测、显示和打印。
⑨曲轴的清洗采用专用精洗机定点定位清洗,保证了曲轴清洁度要求。
⑩广泛采用了轴颈过渡圆角滚压技术。
专用圆角滚压机自动控制,对所有轴颈圆角进行一次滚压,而且滚压力和滚压角度可自动调节,使圆角处产生最佳的残余压应力,提高了曲轴的疲劳强度。
曲轴热处理的关键技术是表面强化处理。
一般均正火处理,为表面处理作好组织准备。
表面强化处理一般采用感应淬火或氮化工艺,少数厂家还引进了圆角淬火技术和设备。
球铁曲轴具有诸多优点,国内外广泛采用。
但整体水平与国外还有相当差距,除生产规模小、管理落后外,主要差距仍是制造工艺的落后。
借鉴国外的先进技术和工艺方法是提高我国曲轴制造水平的捷径。
制定工艺规程的思路是:①收集和熟悉制定工艺规程的有关资料图样,进行零件的结构工艺性;②确定毛坯的类型及制造方法;③选择定位基准;④拟定工艺路线;⑤确定各工序的工序余量、工序尺寸及其公差;⑥确定各工序的设备,刀具、夹具、量具和辅助工具;⑦确定各工序的切削用量及时间定额;⑧确定主要工序的技术要求及检验方法;⑨进行技术经济分析,选择最佳方案;⑩编制工艺文件。
机械制造技术的新发展包括计算机辅助工艺规程设计和计算机辅助制造。
计算机辅助制造是指通过计算机直接或间接地与企业中的物质资源和人力资源交换信息,实现计算机对制造过程各环节的管理、控制和操作。
柔性制造系统工作内容有:①生产工程分析和设计;②生产计划调度;③工作站和设备的运行控制;④工程监测和质量保证;⑤物资供应与财会管理。
计算机集成制造系统包括计算机辅助设计、计算机辅助工艺规程、计算机辅助制造、计算机辅助质量管理和自动存取等。
夹具设计的思路是:①明确设计任务,收集设计资料;②拟订夹具的结构方案、绘制结构草图;③绘制夹具总装图。
绘制夹具总装图的顺序和方法:①用双点化线或红色笔绘出工件的轮廓外形和主要表面,并用网纹线表示出加工余量;②视工件轮廓为透明体,分别绘出定位、导向、夹紧及其他元件或装置,最后绘制夹具体,形成一个夹具整体;③标注尺寸、公差与配合和技术要求;④对零件进行编号,填写零件明细栏和标题栏;⑤绘制夹具零件图。
计算机辅助绘制夹具装配图:1、通常采用“菜单”的形式,对夹具元件图形进行编目和检索。
2、夹具装配图由若干夹具元件图形拼接而成。
在微机上开发的系统中可采用以下几种方法进行图形消隐:①按配合形式分别存图;②利用图形软件的一些基本命令作消隐处理;③参数化建库的消隐处理。
1 R180柴油机曲轴工艺设计1.1 分析零件图1.1.1 零件的作用曲轴是柴油机的一个主要零件。
曲轴主要用于作往复运动的机械中。
1.1.2 零件的工艺分析曲轴图样的视图、尺寸、公差和技术要求齐全、正确;零件选用材料为QT800-2,该材料具有较高的强度、韧性和塑性,切削性能良好;结构工艺性比较好。
根据各加工方法的经济精度及一般机床所能达到的位置精度,该零件没有很难加工的表面,上述各表面的技术要求采用常规加工工艺均可以保证。
1.2确定生产类型已知零件的年生产纲领为120000件,零件质量 3.76kg,由《机械制造工艺及设备设计指导手册》表15—2可确定其生产类型为大量生产。
故初步确定工艺安排的基本倾向为:加工设备以自动化和专用设备为主,通用设备为辅;机床按流水线或自动线排列;采用高效专用夹具;广泛采用专用夹具;广泛采用专用量具、量仪和自动检验装置。
这样生产效率高。
1.3确定毛坯1.3.1 确定毛坯种类根据零件材料确定毛坯为铸件。
并依其结构形状、尺寸大小和生产类型,毛坯的铸造方法选用金属模机械砂型铸造。
根据《机械制造工艺及设备设计指导手册》表15—5铸件尺寸公差等级采用CT9级。
1.3.2 确定铸件余量及形状根据《机械制造工艺及设备设计指导手册》表15—7,取加工余量为MA-G级。
查《机械制造工艺及设备设计指导手册》表15—8确定各表面的铸件机械加工余量。
对于金属模机械砂型铸造,根据《机械制造工艺及设备设计指导手册》表15—9铸件最小孔的直径,故本零件上的孔不铸出。
1.3.3 画铸件—零件综合图<见曲轴零件毛坯图)1.4 机械加工工艺过程设计1.4.1 选择表面加工方法根据各表面加工要求和各种加工方法所能达到的经济精度,查《机械制造工艺及设备设计指导手册》表15—32~表15—34选择零件主要表面<依次为从长头到短头)的加工方法与方案如下:M36X2螺纹:粗车<IT12)—精车<IT6)—割槽Ф33X4.8<IT11)—车螺纹M36X2。
1:8圆锥面:粗车<IT12)—半精车<IT10)—铣键槽12N9<IT8)—磨削<IT6)。
Ф45圆柱面:粗车<IT12)—半精车<IT10)—磨削<IT6)—抛光<IT5)。
Ф50圆柱面:粗车<IT12)—半精车<IT10)—割槽Ф47X2.2—粗磨<IT7)—精磨<IT6)。
Ф60圆柱面:粗车<IT12)—半精车<IT10)。
K面:铣<IT9)—钻孔4—Ф8<IT12)—铰孔4—Ф8<IT9)—钻孔2—M10<IT12)—攻丝2-M10。
Ф45连杆颈圆柱面:粗车<IT12)—半精车<IT10)—粗磨<IT7)—精磨<IT6)—抛光<IT5)。
Ф14.2斜孔:钻<IT12)。
Ф5斜油孔:钻<IT12)—抛光<IT8)。
Ф60圆柱面:粗车<IT12)—半精车<IT10)。
Ф50圆柱面:粗车<IT12)—半精车<IT10)—粗磨<IT7)—精磨<IT6)。
Ф40圆柱面:粗车<IT12)—半精车<IT10)—割槽Ф38.5X3<IT10)—铣键槽5N9<IT8)—粗磨<IT7)—精磨<IT6)。
Ф19孔:钻孔Ф18.5<IT12)—铰孔Ф19<IT8)。
M6螺纹:钻孔2—Ф5<IT12)—攻丝2-M6。
1.4.2 确定工艺过程方案<1)拟定方案由于各表面加工方法已基本确定,现按照“先粗后精”、“先主后次”、“先面后孔”、“基准先行”的原则,初步拟定两种工艺过程方案,见表1。
表1 工艺过程方案<2)方案论证方案Ⅰ的优点在于基本遵循粗精加工划分阶段的原则。
方案Ⅱ的不足之处是加工过程中的检验太少,不利于控制曲轴的加工质量。
根据以上分析,确定方案Ⅰ为曲轴零件加工的工艺路线。
1.5 选择加工设备与工艺装备1.5.1 选择机床考虑到大量生产,尽量选用高效机床。
①工序070、080、090、100均为圆柱面的车削加工,用CJK6140数控车床加工方便且效率高。
②工序180、190、260、270、280、290均为圆柱面的磨削加工,用JK101数显曲轴磨床加工方便且效率高。
③其余表面加工均采用通用机床。
如:C6140卧式车床、X62W万能铣床、Z5125立式钻床等。
1.5.2 选择夹具考虑到大量生产,均采用专用夹具。
1.5.3 选择刀具①在车床上加工的工序,均采用YG6硬质合金外圆车刀,并尽量采用成形车刀。
②在铣床上加工的工序,铣平面选用YG6A硬质合金圆盘铣刀,铣键槽选用键槽铣刀。
③在磨床上加工的工序,磨主轴颈选用砂轮P600X63X305,C46K2B35,其外径为600mm,厚度为63mm,内径为305mm;磨连杆颈选用砂轮P600X25X305,C46K2B35,其外径为600mm ,厚度为25mm ,内径为305mm 。