通孔技术
如何在高速PCB设计中充分利用通孔技术(THT)
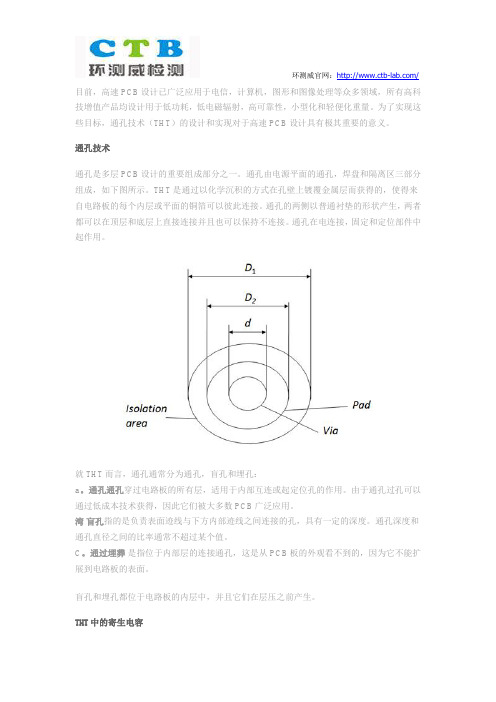
环测威官网:/目前,高速PCB设计已广泛应用于电信,计算机,图形和图像处理等众多领域,所有高科技增值产品均设计用于低功耗,低电磁辐射,高可靠性,小型化和轻便化重量。
为了实现这些目标,通孔技术(THT)的设计和实现对于高速PCB设计具有极其重要的意义。
通孔技术通孔是多层PCB设计的重要组成部分之一。
通孔由电源平面的通孔,焊盘和隔离区三部分组成,如下图所示。
THT是通过以化学沉积的方式在孔壁上镀覆金属层而获得的,使得来自电路板的每个内层或平面的铜箔可以彼此连接。
通孔的两侧以普通衬垫的形状产生,两者都可以在顶层和底层上直接连接并且也可以保持不连接。
通孔在电连接,固定和定位部件中起作用。
就THT而言,通孔通常分为通孔,盲孔和埋孔:a。
通孔通孔穿过电路板的所有层,适用于内部互连或起定位孔的作用。
由于通孔过孔可以通过低成本技术获得,因此它们被大多数PCB广泛应用。
湾盲孔指的是负责表面迹线与下方内部迹线之间连接的孔,具有一定的深度。
通孔深度和通孔直径之间的比率通常不超过某个值。
C。
通过埋葬是指位于内部层的连接通孔,这是从PCB板的外观看不到的,因为它不能扩展到电路板的表面。
盲孔和埋孔都位于电路板的内层中,并且它们在层压之前产生。
THT中的寄生电容环测威官网:/通孔具有寄生电容到地面。
地平面上隔离通孔的直径为D 2 ; 通孔垫的直径为D 1 ; PCB厚度为T ; 衬底材料的介电常数是ε。
然后,通孔的寄生电容可以通过公式来计算c ^ =1.41 εŤ d 1 /(d 2 - d 1)寄生电容对电路的主要影响是延长信号的上升时间和降低电路运行速度。
因此,较低的寄生电容越好。
THT中的寄生电感通孔也具有寄生电感。
在高速数字电路设计过程中,寄生电感引起的危害通常大于寄生电容引起的危险。
寄生串联电感会削弱旁路电容的功能,降低整个电力系统的滤波效果。
当通孔的电感表示为L,通孔长度为h,通孔直径为d时,通孔的寄生电感可以通过符合公式L = 5.08 h [In(4 h / d)+1 来计算出来]基于该公式,通孔直径很少与电感相关,影响电感的最大元素是通孔长度。
硅通孔技术TSV研究ppt课件

TSV技术面临的难题:
➢在价格与成本之间的极大障碍
➢新技术的不确定性所隐含的风险
➢实际的量产需求
1
概述
发展 状况
TSV 的 应用
GaAs 基TSV 20/03/2020
TSV的研究动态
TSV参数 最小TSV直
径 最小TSV间
3
TSV封装剖面图
概述
发展 状况
TSV 的 应用
TSV的研究动态
TSV的关键技术之一——通孔刻蚀
➢ 前通孔(via first):
在 IC 制 造 过 程 中 制 作 通 孔,分为前道互连和后 道互连
➢ 后通孔(via last) :
制造完成之后制作通孔
GaAs
基TSV 20/03/2020
4
概述
台积电有在28nm以下工艺量产三维LSI的意向。
TSV的 应用
GaAs 基TSV 20/03/2020
以多种尺寸和配置而形成的TSV 和再布线层
12
连接300mm晶圆和半导体芯片的微凸点
TSV的研究动态
概述
2010年12月三星公司采用TSV技术,成功开发出基于该 公司先进的绿色DDR3芯片的8GB RDIMM内存。
感测器
OsmiumTM from Aptina 9
TSV的研究动态
概述
发展 状况
应用TSV的影像感测器实例
2009年3月, 意法半导体推出市场上首款集成扩展景深 (EDoF)功能的1/4英寸光学格式3百万像素Raw Bayer传感器。 意法半导体最新的影像传感器可实现最小6.5 x 6.5mm的相机 模块,而且图像锐利度和使用体验非常出色,同时还兼有尺 寸和成本优势,是一款智能型自动对焦相机解决方案。
通孔插入安装技术

7.3 手工插件
元器件的通孔插入方法有手工插件和机械自动 插件两种,随着,装联水平的提高,在大批量稳定 生产的企业,普遍采用了机械自动插件的方式,但 即使采用机械自动插件后,仍有一部份异形元器件 (如集成电路、电位器、插座等)需要手工插件, 尤其在小批量多品种的产品装联中,采用机械自动
(5)专用测试点
印制板上应单独设计专用测试点、 作为调 试、检测时触针的触点,而不要借用元器件引 线的焊点来 测试,以免
造成对焊点
的损伤。
(6)安装或支撑孔
孔的四角必须有弧度,以免冲模的冲击引起裂缝
(7)拼板法 将印制板合理的拼接,适应机械自动焊的要 求。
2.加工的工艺性 (1)引线孔的加工要求 必须一次冲制成型。
而影响元器件的
可靠性。
②成型台阶
元器件插入印制板后的高度有两种安装要求。 一种是元器件的主体紧贴板 面,不需要控制; 另一种是需要与板面保持一
定的距离。
目的:
大功率元器件需要增加引线长度以利散热;
元器件引线根部的漆膜过长。
控制方法:将元器件引线的适当部位弯成台阶。 高度: 卧式元器件5~10毫米,
对插件工的工作质量应该有明确的考核指标,一 般插件差错率应控制在65PPM之内。 (插入1万个元件,平均插错不超过0.65个)
7.3.3不良插件及其纠正
插错和漏插
这是指插入印制板的元器件规格、型号、
标称值、极性等与工艺文件不符,
产生原因:它是由人为的误插及来料中有混
料造成的。 纠正方法:加强上岗前的培训,加强材料发放 前的核对工作,并建立严格的质量责任制。
立式元器件3~5毫米, 其中电解电容器约2.5毫米。
通孔技术

铜焊盘 元件引脚
非支撑孔(Unsupported Holes) 非支撑孔
元件本体 PCB板基材 板基材
铜焊盘 元件引脚
支撑孔(supported Holes) 支撑孔
元件本体 PCB板基材 板基材
铜焊盘 元件引脚
有引脚的镀通孔 – 最低可接受焊点
主面(焊接 主面 焊接 终止面)的 终止面 的 焊盘被润 湿的焊料 覆盖的百 分比
通孔元件介绍
Prepared by : Leo Xu
电子元件分类
1.极性: 无极性元件: 电阻,电容,排阻,电感; 有极性元件: 二极管,电解电容,三极管; 2.元件: 轴向元件 径向元件 3.方向: 水平 垂直
非支撑孔(Unsupported Holes) 非支撑孔
元件本体 PCB板基材 板基材
主面(焊接终 主面 焊接终 止面)上的引 止面 上的引 脚起始面) 焊接起始面 的焊盘被润湿的焊 料覆盖的百分比
辅面(焊接起始面 辅面 焊接起始面) 焊接起始面 上的引脚和内壁 润湿和填充
3D封装与硅通孔TSV工艺技术

TSV技术简介
TSV技术
TSV (through silicon via)穿透硅通孔技术,简称硅通孔技术。TSV是利 用垂直硅通孔完成芯片间互连的方法, 由于连接距离更短、强度更高, 它能 实现更小更薄而性能更好、密度更高、尺寸和重量明显减小的封装, 同时还 能用于异种芯片之间的互连。
图1所示是4层芯片采用载带封装方法 (图 1(a))和采用TSV方法(图1(b)) 封装的外形比较。
一体机示意图(东京精密PG200/300)
芯片减薄
存在的问题:
•机械研磨和化学机械抛光还可能会在硅晶圆表面产生严重的内应力,这些应力 会引发弯曲和翘曲。同时,由于是先用铜将 TSV填满后进行 CMP工艺这样在过 程中铜和硅容易发生扩散而且破坏绝缘层,从而破坏 TSV互连。
•针对以上问题,袁娇娇等人研究通过对硅晶圆进行局部减薄来实现的局部减薄, 即将硅晶圆的大部分减薄 利用没有减薄的部分支撑硅晶圆完成表面微加工工艺 局部减薄是通过对硅晶圆局部刻蚀一定深度以达到局部减薄的目的。
TSV技术简介
1.填埋型3D封装
——在各类基板内或多层布线介质层中“埋置”R、C或IC等元器件,最上 层再贴装SMC/SMD来实现立体封装。
TSV技术简介
2.有源基板型3D封装
——Si圆片规模集成(WLS)后的有源基板上再实行多层布线,最上层再贴装 SMC/SMD。
TSV技术简介
3.叠层型3D封装
芯片减薄
减薄技术面临的首要挑战就是超薄化工艺所要求的<50μm的减薄能力。传
统上,减薄工艺仅仅需要将硅片从晶圆加工完成时的原始厚度减薄到300~ 400μm。在这个厚度上,硅片仍然具有相当的厚度来容忍减薄工程中的磨削 对硅片的损伤及内在应力,同时其刚性也足以使硅片保持原有的平整状态。 另外,随着微电子工业的迅猛发展,圆片直径越来越大,当150mm、 200mm甚至300mm圆片被减薄到150μm以下时,圆片翘曲和边缘损伤问 题变得尤为严重。
通孔回流焊工艺要求

通孔回流焊工艺要求通孔回流焊是一种常见的表面贴装技术,在电子制造行业中广泛使用。
它通过将电子元件焊接到PCB板上进行连接,以实现电子设备的正常运行。
下面是通孔回流焊工艺的要求和相关参考内容。
1. 焊接温度控制:在通孔回流焊过程中,焊接温度是一个非常重要的参数。
焊接温度过高会导致元件损坏,焊接温度过低会导致焊接不良。
因此,对于不同类型的元件,应根据供应商提供的数据和规范来确定适当的焊接温度范围。
2. 焊接时间控制:除了焊接温度外,焊接时间也是影响焊接质量的重要因素。
焊接时间过长可能会导致焊接点过热,焊接时间过短可能会导致焊接不充分。
通常,焊接时间应根据焊接温度和元件类型进行调整,以确保焊接质量。
3. 焊接剂的选择:焊接剂在通孔回流焊工艺中起到重要的作用。
它可以帮助提高焊接质量,并防止氧化。
在选择焊接剂时,应根据焊接材料和工艺要求选择适合的类型和规格的焊接剂。
4. 焊接机器设备的选取:通孔回流焊需要使用专门的焊接设备,如回流焊炉。
在选购设备时,应考虑焊接速度、温度控制的精度、设备的稳定性等因素。
并且,设备的使用和维护也是确保焊接质量的关键。
5. PCB设计的要求:良好的PCB设计对于焊接质量的保证至关重要。
在PCB设计中,应考虑元件的布局、焊盘的大小和间距等因素,以便实现良好的焊接质量。
6. 焊接操作的执行:良好的焊接操作是保证焊接质量的重要保证。
操作人员应熟悉焊接工艺要求,并采取正确的焊接操作,包括元件的放置和固定、焊接温度和时间的控制、焊接剂的喷洒等。
7. 焊后检测的要求:焊接后的检测对于发现焊接缺陷和及时修复非常重要。
可以借助透光检查、高倍显微镜检查、飞针测试等方法来进行焊后检测。
8. 质量管理的要求:通孔回流焊工艺要求严格的质量管理,包括过程记录、检验记录、不良品管理等。
操作人员应按照质量管理程序要求进行操作,并确保焊接质量符合相关标准和规范。
综上所述,通孔回流焊工艺的要求包括焊接温度控制、焊接时间控制、焊接剂的选择、焊接机器设备的选取、PCB设计的要求、焊接操作的执行、焊后检测的要求和质量管理的要求。
通孔镀铜技术详解

通孔镀铜技术详解在印制电路板制造技术中,虽关键的就是化深沉铜工序。
它主要的作用就是使双面和多层印制电路板的非金属孔,通过氧化还原反应在孔壁上沉积一层均匀的导电层,再经过电镀加厚镀铜,达到回路的目的.要达到此目的就必须选择性能稳定、可靠的化学沉铜液和制定正确的、可行的和有效的工艺程序。
一.工艺程序要点:1.沉铜前的处理;2.活化处理;3.化学沉铜。
二.沉铜前的处理:1.去毛刺:沉铜前基板经过钻孔工序,此工序虽容易产生毛刺,它是造成劣质孔金属化的最重要的隐患。
必须采用去毛刺工艺方法加以解决。
通常采用机械方式,使孔边和内孔壁无倒刺或堵孔的现象产生.2.除油污:⊙油污的来源:钻头由于手接触造成油污、取基板时的手印及其它。
⊙油污的种类:动植物油脂、矿物等。
前者属于皂化油类;后者属于非皂化油类。
⊙油脂的特性:动植物油类属于皂化油类主要成分高级脂肪酸,它与碱起作用反应生成能溶于水的脂肪酸盐和甘油;矿物油脂化学结构主要是石腊烃类,烯属烃及环烷属烃类和氯化物的混合物,不溶于水也不与碱起反应。
⊙除油处理方法的选择依据:根据油的性质、根据油沾污的程度。
⊙方法:采用有机溶剂和化学及电化学碱性除油。
⊙作用与原理:□可皂化性油类与碱液发生化学反应生成易溶于水的脂肪酸盐和甘油。
反应式如下:(C17H35COO)3十3NAOH3C17H35COON a+C2H5(OH)2□非皂化油类:主要靠表面活性剂如OP乳化剂、十二烷基磺酸钠、硅酸钠等。
这些物质结构中有两种基团,一种是憎水性的;一种是亲水性.首先乳化剂吸附在油与水的分界面上,以憎水基团与基体表面上的油污产生亲和作用,而亲水基团指向去油液,水是非常强的极性分子,致使油污与基体表面引力减少,借者去油液的对流、搅拌,油污离开基体表面,实现了去油的最终目的。
3.粗化处理:⊙粗化的目的:主要保证金属镀层与基体之间良好的结合强度。
⊙粗化的原理:使基体的表面产生微凹型坑,以增大其表面接触面积,与沉铜层形成机械钮扣结合,获得较高的结合强度。
thr通孔回流焊技术要求(1)

通孔回流焊技术要求近年来,表面贴装技术(SMT)迅速发展起来,在电子行业具有举足轻重的位置。
除了全自动化生产规模效应外,SMT还有以下的技术优势:元件可在PCB的两面进行贴装,以实现高密度组装;即使是最小尺寸的元件也能实现精密贴装,因此可以生产出高质量的PCB组件。
然而,在一些情况下,这些优势随着在PCB上元件贴着力的减少而削弱。
让我们观察图1的例子。
SMT元件的特点是设计紧凑,并易于贴装,与通孔的连接器在尺寸和组装形式上有明显的区别。
图1 PCB上组装有SMT元件(左)和一个大理通孔安装的连接器(右)用于工业领域现场接线的连接器通常是大功率元件。
可满足传输高电压、大电流的需要。
因此设计时必须考虑到足够的电气间隙与爬电距离,这些因素最终影响到元件的尺寸。
此外,操作便利性、连接器的机械强度也是很重要的因素。
连接器通常是PCB主板与“外界部件”通信的“接口”,故有时可能会遇到相当大的外力。
通孔技术组装的元件在可靠性方面要比相应的SMT元件高很多。
无论是强烈的拉拽、挤压或热冲击,它都能承受,而不易脱离PCB。
从成本考虑,大部分PCB上SMT元件约占80%,生产成本仅占60%;通孔元件约占20%,生产成本却占40%,如图2所示。
可见,通孔元件生产成本相对较高。
而对许多制造公司来说,今后面临的挑战之一便是开发采用纯SMT工艺的印刷线路板。
图2 带有通孔无件和SMT元件的PCB根据生产成本以及对PCB的影响,SMT+波峰焊和SMT+压接技术(press in)等现有的工艺还不完全令人满意,因为在现有的SMT工序需要进行二次加工,不能一次性完成组装。
这就对采用通孔技术的元件提出了下列要求:通孔元件与贴片元件应该使用同样的时间、设备和方法来完成组装。
THR如何与SMT进行整合根据上述要求发展起来的技术,称之为通孔回流焊技术(Through-hole Reflow,THR),又叫“引脚浸锡膏(pin in paste,PIP)”工序,如图3所示。
- 1、下载文档前请自行甄别文档内容的完整性,平台不提供额外的编辑、内容补充、找答案等附加服务。
- 2、"仅部分预览"的文档,不可在线预览部分如存在完整性等问题,可反馈申请退款(可完整预览的文档不适用该条件!)。
- 3、如文档侵犯您的权益,请联系客服反馈,我们会尽快为您处理(人工客服工作时间:9:00-18:30)。
1
2020/6/27
7-95-1
7节- 通孔技术 - 元件安装位置/方向
本章给出标准仅关于通孔插装的元件/导线在组 件和接线柱上的放置与固定 标准陈述具通用概括性,可用于所有类似连接 目检由整体开始再到局部细节,包括零件标识, 安装次序以及零部件\元件或板子的损伤. 粘接材料的用量应足够支撑零部件但不能封盖 元件标识.
缺陷?
极性元件的安装错误
Figure 7-6
Defect- Class 1,2,3
14
2020/6/27
7-95-14
7.1.2.1 元器件的安放 引脚成形 - 弯曲
Figure 7-7
矩形截面的引脚 以脚厚作为直径
15
2020/6/27
7-95-15
7.1.2.1 元器件的安放 引脚成形 - 弯曲* 续…
弯脚处距离本体 < D Fig. 7-14
A*1; PI* 2; D*3
2020/6/27
7-95-20
无应力释放
Fig. 7-15 D*1, 2, 3
20
7.1.2.3 元器件的安放 引脚成形 – 损伤
判断标准: 引脚直径的宽度 或厚度的10%
Fig. 7-16 ; A* 1, 2, 3
弯曲变形
孔位不正确 极性错 错件 多脚元件取向 错
2020/6/27
Figure 7-3 Defect- Class 1,2,3
7--方向- 垂直
无极性元 件的标识 从上至下 读取 极性标识 位于顶部
Figure 7-4
Target - Class 1,2,3
2 倍 线 径 /厚 度
元器件内侧的弯曲半径不符合上表要求,如何判断?
ACC - 1级
PI - 2级
REJ - 3级
16
2020/6/27
7-95-16
7.1.2.1 元器件的安放 引脚成形 - 弯曲 续…
ACC,L≥一个引脚直径或0.8mm中的较大者
裂缝
Fig. 7-8
Fig. 7-11 Defect - Class 1,2,3
12
2020/6/27
7-95-12
7.1.1.2 元器件的安放-方向- 垂直 续…
无极性元件的色标应 从上至下读取
有与目标不符吗?
极性元件的标识 不可见(在顶部)
Figure 7-5
Acceptable- Class 1,2,3
13
2020/6/27
7-95-13
7.1.1.2 元器件的安放-方向- 垂直 续…
2020/6/27 Fig. 7-17 ; D* 1, 2, 3 7-95-21
钳子压痕
Fig. 7-18 ; D* 1, 2, 3 21
7.1.3 元器件的安放 – 引脚跨越导体
2020/6/27
7-95-6
7节 – 通孔技术 - 术语定义 续
以下2图有何差异?哪一个是支撑孔或非支撑 孔?
支撑孔:焊接后孔内 有焊锡
2020/6/27
7-95-7
非支撑孔:焊接后孔 内没有焊锡
7
通孔元件安装分类
第7章
安装方向 安装位置
轴向元件 径向元件
元件限位
弯月形引 脚包封
水平安装 7.1.1.1
IPC-610D 电子组装件的验收标准 熟练操作员认可培训
(Worker Proficiency Instruction Training)
LIKUI (li-kui-2008@)
2020/6/27
IPC-A-610-7
0
7节: 通孔技术
7.1 元器件的安放 7.2 散热装置 7.3 元件的固定 7.4 非支撑孔 7.5 支撑孔
2
2020/6/27
7-95-2
7节 - 通孔技术-元件安装位置/方向
轴向/径向元件 水平/垂直 安装标准 DIP、SIP封装元件及其插座引脚和连接器 安装标准 元件引脚成型和应力释放要求 引脚和元件损伤的要求 导线和端子的要求
3
2020/6/27
7-95-3
7节 – 通孔技术 - 术语定义
轴向/径向元件分别是如何定义的?
7.1.2.2 元器件的安放 引脚成形 – 应力释放 *
元件本体 平行
引脚垂直
弯曲应力 释放*
L>D
Fig. 7-12
Fig. 7-13 Acceptable - Class 1,2,3
Acceptable - Class 1,2,3
19
2020/6/27
7-95-19
7.1.2.2 元器件的安放 引脚成形 – 应力释放 续…
Figure 7-1
Target - Class 1,2,3
9
2020/6/27
7-95-9
7.1.1.1 元器件的安放-方向- 水平 续…
有与目标不符吗?
2020/6/27
无极性元件
Figure 7-2 Acceptable- Class 1,2,3
7-95-10
同向读取
10
7.1.1.1 元器件的安放-方向- 水平 续…
表7-1 最小内弯半径
脚 径 (D ) 或 脚 厚 (T )
最 小 内 弯 半 径 (R )
< 0 .8 m m [0 .0 3 1 in ]
0 .8 m m [0 .0 3 1 in ] ~ 1 .2 m m [0 .0 4 7 2 in ]
> 1 .2 m m [0 .0 4 7 2 in ]
1 倍 线 径 /厚 度 1 .5 倍 线 径 /厚 度
支撑孔 非支撑孔 7.5.1 7.4.1
7.1.7
垂直安装 7.1.2.2
支撑孔 非支撑孔 7.5.2 7.4.2
7.1.6 7.1.6.1 7.5.5.7
8
2020/6/27
7-95-8
7.1.1.1 元器件的安放-方向- 水平
• 元件位于其盘的中间 •元件标识可以辨识 •无极性元件按照标记同 向读取(从左至右或从上 至下)的原则定向.
Acceptable - Class 1,2,3
17
2020/6/27
7-95-17
7.1.2.1 元器件的安放 引脚成形 - 弯曲* 续…
内弯半径不满足表7-1的要求
Fig. 7-9&10 A*1; PI*2; D*3
ACC* ,L < 一个引脚直径或0.8mm中的较大者
18
2020/6/27
7-95-18
以下元件是轴向还是径向元件?
(轴向\径向)
4
2020/6/27
7-95-4
7节 – 通孔技术 - 术语定义 续
IPC是如何定义的===>
轴向 – 手臂
径向 – 脚
5
2020/6/27
7-95-5
7节 – 通孔技术 - 术语定义 续
支撑孔/非支撑孔分别是如何定义的?
以下是支撑孔还是/非支撑孔的?
6