金属基复合材料的研究现状
金属基复合材料发展和应用前景

金属基复合材料的发展现状与应用前景金属基复合材料( M MCs) 问世至今已有30 余年。
M MCs 的耐温性较高, 力学性能( 特别是刚度) 比一般金属的好, 此外它还具有导电性以及在高真空条件下不释放小分子的特点, 克服了树脂基复合材料在航宇领域中使用时存在的缺点, 因此受到航空航天部门的青睐。
然而, 尽管MM Cs 在航天飞机以及其他一些尖端技术中已经获得应用, 但用量很小, 不足以推动其发展。
近年来虽然努力在民用领域寻找机遇, 但终因成本偏高而缺乏与金属等其他传统材料竞争的优势。
因此发展MM Cs 的出路在于寻找降低成本的措施, 同时也要探索能充分发挥其特色的应用领域。
鉴于复合材料的成型工艺占其成本的60% ~ 70% , 所以研究发展高效、省时、低能耗、设备简单、能实现近似无余量成型的工艺方法是当务之急。
1、金属基复合材料制备技术1.1各种制备方法简评MMCs 通常按增强体的形式分类, 如连续纤维增强、短纤维或晶须增强、颗粒增强以及片层叠合等。
由于连续纤维增强的MM Cs 必须先制成复合丝或复合片等先驱体, 工艺复杂而成本高, 因此除了极少量有特殊要求的零件(如航天飞机的结构梁)采用外,目前尚看不到有扩大应用的可能性。
本文着重叙述的是颗粒、短纤维或晶须等非连续增强体的MM Cs, 其中, 颗粒增强的M MCs 已具备批量生产条件, 有良好的发展前景。
迄今, 已开发出不少非连续增强体MMCs的制备方法,见表1在表 1 列出的各种制备方法中, 搅拌混合法和挤压铸造法比较成熟,已具备批量生产的条件。
对搅拌混合法工艺已完成了大量研究工作,其中包括对增强体进行表面处理,以改善其与基体金属的浸润性;调整基体合金元素以减轻界面反应对MMCs性能的影响;在设备方面则改进了搅拌桨的形式以改善增强体分布的均匀性,此外,研究了增强体的加入机构,为降低气孔率还制作了施加负压的装置;在工艺条件上则研究了搅拌速度和金属熔体温度对混合均匀度和产生气泡的影响。
金属基复合材料的研究进展
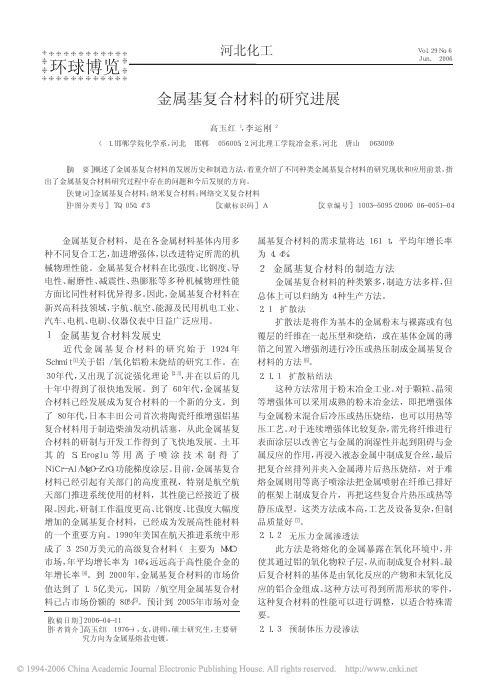
金属基复合材料,是在各金属材料基体内用多种不同复合工艺,加进增强体,以改进特定所需的机械物理性能。
金属基复合材料在比强度、比钢度、导电性、耐磨性、减震性、热膨胀等多种机械物理性能方面比同性材料优异得多。
因此,金属基复合材料在新兴高科技领域,宇航、航空、能源及民用机电工业、汽车、电机、电刷、仪器仪表中日益广泛应用。
1金属基复合材料发展史近代金属基复合材料的研究始于1924年Schmit[1]关于铝/氧化铝粉末烧结的研究工作。
在30年代,又出现了沉淀强化理论[2,3],并在以后的几十年中得到了很快地发展。
到了60年代,金属基复合材料已经发展成为复合材料的一个新的分支。
到了80年代,日本丰田公司首次将陶瓷纤维增强铝基复合材料用于制造柴油发动机活塞,从此金属基复合材料的研制与开发工作得到了飞快地发展。
土耳其的S.Eroglu等用离子喷涂技术制得了NiCr-Al/MgO-ZrO2功能梯度涂层。
目前,金属基复合材料已经引起有关部门的高度重视,特别是航空航天部门推进系统使用的材料,其性能已经接近了极限。
因此,研制工作温度更高、比钢度、比强度大幅度增加的金属基复合材料,已经成为发展高性能材料的一个重要方向。
1990年美国在航天推进系统中形成了3250万美元的高级复合材料(主要为MMC)市场,年平均增长率为16%,远远高于高性能合金的年增长率[4]。
到2000年,金属基复合材料的市场价值达到了1.5亿美元,国防/航空用金属基复合材料已占市场份额的80%[5]。
预计到2005年市场对金属基复合材料的需求量将达161t,平均年增长率为4.4%。
2金属基复合材料的制造方法金属基复合材料的种类繁多,制造方法多样,但总体上可以归纳为4种生产方法。
2.1扩散法扩散法是将作为基本的金属粉末与裸露或有包覆层的纤维在一起压型和烧结,或在基体金属的薄箔之间置入增强剂进行冷压或热压制成金属基复合材料的方法[6]。
2.1.1扩散粘结法这种方法常用于粉末冶金工业。
高导热金属基复合材料的制备与研究进展

高导热金属基复合材料的制备与研究进展摘要:随着电子器件芯片功率的不断提高,对散热材料的热物理性能提出了更高的要求。
将高导热、低膨胀的增强相和高导热的金属进行复合得到的金属基复合材料,能够兼顾高的热导率和可调控的热膨胀系数,是理想的散热材料。
本文对以 Si、 SiCp、金刚石、鳞片石墨为增强相的铜基及铝基复合材料的研究进展进行了总结,并就金属基复合材料目前存在的问题及未来的研究方向进行了展望。
关键词:制备;研究进展;金属复合材料提升相和基体原材料的润滑性对复合材料的热性能有很大影响。
除此之外,基体中加强相的趋向和分布、复合材料的相组成和微观结构也会影响到原材料的导热系数。
为了防止复合材料中加强相分别不匀、趋向不匀等问题造成导热系数降低,在挑选复合材料制备方式时,应充分考虑各种方法的优缺点,并完善相关工艺指标,就可以获得导热系数最理想的金属基复合材料。
现阶段,铜基和铝基复合材料的制备技术大概可以分为固相法和液相法两类。
固相法有热压烧结法、高温高压烧结法和等离子放电烧结法等,液相法有搅拌铸造法和熔渗法等。
一、热压烧结法热压是制备复合材料传统的方式,主要加工工艺是将基体与加强相粉末混合匀称,然后放入磨具中增加工作压力,除气后升温至固相线环境温度下,在空气、真空泵及保护气中致密化,产生复合材料。
热压烧结法是金属基复合材料的重要制备方式,此方法的优势是生产出的复合金属质量稳定,加强相和金属粉占比可调。
可是,缺陷非常明显,烧结必须使用磨具,无法制备外观繁杂、尺寸大的金属基复合材料,且工艺成本高。
Goryuk 研发了电子元件基材使用于SiC/Al复合材料的压合工艺流程之中,通过隔热保温时间与压力对SiC/Al复合材料相对密度和导热系数产生的影响。
通过Goryuk的研究最佳的制备参数为:烧结环境温度700摄氏度、烧结工作压力20 MPa、隔热保温时长1 h、保护气为N2。
选用该加工工艺所得到的复合材料导热系数为240 W m-1K-1。
金属基复合材料的现状与发展趋势

金属基复合材料的现状与发展趋势金属基复合材料是指将金属作为基体材料,与其他非金属材料(如陶瓷、复合材料纤维等)进行复合制备的材料。
目前,金属基复合材料在诸多领域中得到了广泛的应用,包括航空航天、汽车、电子、建筑等。
金属基复合材料的现状主要体现在以下几个方面:1. 材料种类丰富:金属基复合材料的种类非常多样,包括金属基陶瓷复合材料、金属基纤维复合材料、金属基聚合物复合材料等。
不同种类的金属基复合材料具有不同的特性和应用领域。
2. 性能优良:金属基复合材料具有金属和非金属材料的优势,综合性能较好。
例如,金属基纤维复合材料具有较高的强度和刚度,金属基陶瓷复合材料具有较高的耐磨性和耐高温性能。
3. 制备技术成熟:金属基复合材料的制备技术已经较为成熟,包括热压、热等静压、粉末冶金、特殊金属/陶瓷涂覆等多种制备方法。
这些方法能够制备出具有均匀组织结构和良好性能的金属基复合材料。
未来,金属基复合材料的发展趋势主要包括以下几点:1. 变革材料设计:研究人员将继续探索金属基复合材料的设计、制备和性能调控方法,以实现更好的性能和应用。
例如,通过优化复合材料的界面结构和增加金属间化合物相的形成,进一步提高复合材料的力学性能和耐磨性能。
2. 发展新型金属基复合材料:随着科学技术的不断进步,新型金属基复合材料将不断涌现。
例如,碳纳米管增强金属基复合材料、石墨烯增强金属基复合材料等具有很高研究和应用价值。
3. 应用拓展:金属基复合材料在航空航天、汽车、电子等领域的应用将进一步拓展。
例如,开发具有轻质、高强度和高温耐受性能的复合材料,可用于制造飞机、汽车零件、电子器件等。
金属基复合材料具有广阔的应用前景,并且随着技术的发展和研究的深入,其性能和应用将得到进一步提高和扩展。
金属基复合材料力学性能研究进展

4、疲劳与断裂行为研究:疲劳与断裂是金属基复合材料在实际应用中面临的 重要问题。研究者们通过研究复合材料的疲劳性能、断裂韧性、裂纹扩展行为 等,深入了解了其在实际应用中的可靠性和寿命预测,为提高金属基复合材料 的应用安全性提供了有力支持。
三、未来研究方向与展望
虽然金属基复合材料的力学性能研究已取得显著进展,但仍存在许多挑战和问 题需要解决。未来研究可以下几个方面:
二、实验方法
1、材料制备
高体积分数金属基复合材料SiCpAl的制备方法包括熔融搅拌法、粉末冶金法 和喷射沉积法等。本次演示采用熔融搅拌法,将铝基体和碳化硅颗粒按一定比 例混合,在高温炉中熔炼,并搅拌均匀,然后浇注成标准试样。
2、实验测试
对制备好的标准试样进行动态力学性能实验,包括拉伸、压缩和冲击等测试。 实验过程中采用有限元分析方法对试样的应力、应变和断裂行为等进行详细分 析。
摘要:本次演示对高体积分数金属基复合材料SiCpAl进行了动态力学性能研 究。实验测试和有限元分析结果表明,该材料具有优异的力学性能和耐磨性能, 在工业领域具有广泛的应用前景。同时,本次演示也提出了材料在应用过程中 可能存在的问题及解决方案。
一、引言
高体积分数金属基复合材料是一种以金属或合金为基体,以陶瓷颗粒或其他增 强体为增强体制成的复合材料。由于具有优异的耐磨、耐高温和抗疲劳等性能, 因此在工业领域具有广泛的应用前景。SiCpAl是一种常见的高体积分数金属 基复合材料,由铝基体和碳化硅颗粒增强体制成。本次演示旨在探讨该材料的 动态力学性能及其在工业领域的应用。
本次演示主要研究了高体积分数金属基复合材料SiCpAl的动态力学性能及其 在工业领域的应用。通过实验测试和有限元分析,探讨了材料的力学行为、断 裂机制以及耐磨性能等方面的表现。本次演示的研究成果对于优化材料的应用 和提高工业设备的运行效率具有重要意义。
金属基复合材料简介及研究现状

3D打印技术
02
利用3D打印技术,实现金属基复合材料的定制化、高效制造
。
多尺度复合技术
03
发展多尺度复合技术,实现金属基复合材料的多层次结构设计
。
05
结论与展望
研究成果总结
金属基复合材料的制备技术得到改进,包括粉末冶金法、喷射沉积法、机械合金 化法等复合材料的应用领域不断扩大,涉及到能源、环保、医疗、航空航天等领 域,且在各个领域中都有显著的应用成果。
02
金属基复合材料的性能与 特点
力学性能
01
02
03
强度与硬度
金属基复合材料具有较高 的强度和硬度,能够承受 较大的应力和压力。
韧性
金属基复合材料的韧性比 金属单质更强,能够吸收 更多的能量,抵抗冲击和 振动。
疲劳性能
金属基复合材料的疲劳性 能较好,能够在反复应力 作用下保持稳定的性能。
物理性能
由于金属基复合材料具有高强度、高刚性和 轻质等优点,因此在航空航天领域得到广泛 应用,如飞机结构件、卫星部件等。
金属基复合材料在汽车工业中也有广泛应用 ,如汽车发动机部件、变速器齿轮等。
能源领域
生物医学领域
金属基复合材料在能源领域也有广泛应用, 如太阳能电池板支架、核反应堆结构件等。
金属基复合材料在生物医学领域也有广泛应 用,如人工关节、牙科种植体等。
扩散法
将增强体和金属基体在高温下进行扩散处理,使两者相互 渗透、结合,形成复合材料。该方法适用于制备连续或非 连续增强金属基复合材料。
喷射沉积法
将增强体和金属熔体通过喷射、雾化等方法制备成复合材 料。该方法适用于制备连续或非连续增强金属基复合材料 。
金属基复合材料的应用领域
金属基复合材料的制备方法及发展现状
金属基复合材料的制备方法及发展现状赵鹏鹏;谭建波【摘要】金属基复合材料具有较高的比强度和比刚度,广泛用于军事、航天等领域,其研究和发展受到了各行各业,尤其是重工业产业的密切关注.介绍了金属基复合材料的研究历史和发展现状,根据基体类型和增强相形态对其进行了分类.常见的金属基复合材料制备方法包括粉末冶金法、铸造凝固成型法(搅拌铸造法和挤压铸造法)、喷射成型法和原位复合法,重点介绍了粉末冶金法和铸造凝固成型法.指出了现阶段金属基复合材料发展需解决成本偏高、工艺复杂、分布不均匀、高温下易发生界面反应及偏聚等问题.%Due to their high specific strength and high specific stiffness,metal matrix composites are widely used inmilitary,spaceflight,etc.,and the research and development of which has been widely concentrated,especially in heavy industry.The research history and development status of metal matrix composites are introduced,andthe classification of metal matrix composites is given according to the types of the matrix and the morphology of the reinforcing phase.The common methods for the preparation of metal matrix composites include powder metallurgy,casting solidification molding (stir casting and squeeze casting),spray forming and in situ compounding.The powder metallurgy method and casting solidification forming method are mainly introduced.The problems that need be solved for the development of metal matrix composites including high cost,complicate craft,uneven distribution,and incident surface reaction and segregation under high temperature are pointed out.【期刊名称】《河北工业科技》【年(卷),期】2017(034)003【总页数】8页(P214-221)【关键词】金属基复合材料;基体类型;增强相;粉末冶金法;挤压铸造【作者】赵鹏鹏;谭建波【作者单位】河北科技大学材料科学与工程学院,河北石家庄 050018;河北省材料近净成形技术重点实验室,河北石家庄050018;河北科技大学材料科学与工程学院,河北石家庄 050018;河北省材料近净成形技术重点实验室,河北石家庄050018【正文语种】中文【中图分类】TG146.4近些年来,由于一些高新技术的兴起,一些传统材料已无法满足多种产业对其比强度、比刚度等性能的要求。
金属基复合材料研究现状与发展
金属基复合材料起步于 60年代初期。当时 由于受到增强纤维品种少的限制,仅发展了硼 纤维增强铝、钛等少量品种。多沿用树脂基复 合材料的成型方法,如铺层工艺和缠绕工艺。 生产的复合材料,价格高昂(如硼 -铅复合材料 的价格约为热轧钢的 1860倍),仅限于用在航 空航天上。
80年代中期,长纤维增强、短纤维增强、
在纤维增强金属基复合材料中适当的界面结合 强度是材料具有最高性能的保证,此时界面既 能有效地传递载荷,又能有效地阻止裂纹的扩 展,充分发挥纤维的作用。
过强的界面结合可能使材料发生早期的低 应力破坏,反应产物呈脆性,在应力作用下往 往首先断裂,成为裂纹源,引起复合材料的整 体破坏。
有些反应产物本身不稳定,容易分解造成 界面分离。如 Al4C3,与水接触时发生水解生成 甲烷,严重时使复合材料解体。因此必须尽量 控制界面脆性相的生成。
2. 金属基体与增强材料之间浸润性差。 增强材料与基体之间应具有很好的润湿性 (即接触角小于90°),基体才能均匀覆 盖于增强材料表面和渗入到增强材料的间 隙之间,因此,这是得到性能良好的复合 材料的前提。
绝大多数有前景的金属基复合材料体 系中,如碳-铝、碳-镁、碳化硅-铝、氧化 铝-镁等,基体与增强材料之间的浸润性都 很差,必须采取技术措施加以改善。
1. 增强材料以设计的体积分数和排列均匀地分布于 基体中;
2. 尽量不使增强材料和金属基体原有性能下降, 特别是不能对高性能增强材料造成损伤,应使增强材料 和金属的优良性能得以叠加和互补;
3. 尽量避免增强材料和金属基体之间发生不利的化 学反应,应得到合适的界面结构和性能,充分发挥增强 材料的增强效果;
金属基复合材料的研 究现状与发展
材料学院 耿浩然
基本概念
金属基复合材料的研究进展及发展趋势(DOC)
金属基复合材料界面的研究进展及发展趋势周奎(佳木斯大学材料科学与工程学院佳木斯 154007)摘要本文介绍了目前金属基复合材料界面的研究现状,存在的问题及优化的有效途径。
重点阐述了金属基复合材料在各个领域的应用情况。
最后在综述金属基复合材料界面的研究进展与应用现状的基础上,对学者未来研究呈现的趋势进行了简述并对其发展趋势进行了展望。
关键词金属基复合材料界面特性应用发展趋势The research progress of metal matrix composites interface and development trendZHOU Kui(jiamusi university school of materials science and engineering jiamusi 154007) Abstract:Interface of metal matrix composites are introduced in this paper the current research status, existing problems and the effective ways to optimize. Expounds the metal matrix composites and its application in various fields. Finally in this paper the research progress and application of metal matrix composites interface status quo, on the basis of research for scholars in the future the trend of the present carried on the description and its development trend is prospected.Keywords: metal matrix composites application Interface features the development trend1前言金属基复合材料(MMCS)是以金属、合金或金属间化合物为基体,含有增强成分的复合材料。
陶瓷颗粒增强金属基复合材料的制备方法及研究进展
陶瓷颗粒增强金属基复合材料的制备方法及研究进展1. 引言1.1 陶瓷颗粒增强金属基复合材料的制备方法及研究进展陶瓷颗粒增强金属基复合材料是一种具有高强度、高硬度和耐磨性的新型材料,广泛应用于航空航天、汽车制造、电子设备等领域。
在材料科学领域,研究人员们一直在探索更好的制备方法和性能调控途径,以提高这种复合材料的性能和应用范围。
近年来,众多研究表明,陶瓷颗粒增强金属基复合材料的制备方法对其性能至关重要。
常见的制备方法包括粉末冶金、热等静压、等离子烧结等。
这些方法能够有效控制复合材料的成分比例、颗粒尺寸和分布,从而影响材料的力学性能和耐磨性。
研究人员还通过调控复合材料的组织结构,如晶粒尺寸、晶界分布等,来进一步提高材料的性能。
他们还通过添加不同类型和含量的陶瓷颗粒,实现对复合材料性能的调控,使其更适用于不同工程领域的需求。
陶瓷颗粒增强金属基复合材料的制备方法及研究进展是一个充满挑战和机遇的领域,未来研究将继续探索新的材料合成途径和性能调控方法,推动这一材料在工程领域的广泛应用。
2. 正文2.1 陶瓷颗粒增强金属基复合材料的研究背景陶瓷颗粒增强金属基复合材料是指将陶瓷颗粒与金属基体进行复合,以提高金属材料的性能和功能。
这种复合材料具有优良的力学性能、耐磨、耐腐蚀等特点,因此在航空航天、汽车制造、机械加工等领域有广泛的应用。
陶瓷颗粒在金属基复合材料中起着增强作用,能够有效地阻碍金属晶粒的移动和形变,提高复合材料的强度和硬度。
陶瓷颗粒还可以改变金属基复合材料的热膨胀系数和导热性能,使其更适合特定的工作环境和工作要求。
在过去的几十年中,陶瓷颗粒增强金属基复合材料的研究得到了广泛关注和深入探讨。
通过合理设计和制备工艺,研究者们不断优化复合材料的组织结构,探索不同的性能调控方法,推动了该领域的快速发展。
本文将详细介绍陶瓷颗粒增强金属基复合材料的研究背景,探讨其制备方法、组织结构控制、性能调控等方面的进展,并探讨其在工程领域的应用前景。
- 1、下载文档前请自行甄别文档内容的完整性,平台不提供额外的编辑、内容补充、找答案等附加服务。
- 2、"仅部分预览"的文档,不可在线预览部分如存在完整性等问题,可反馈申请退款(可完整预览的文档不适用该条件!)。
- 3、如文档侵犯您的权益,请联系客服反馈,我们会尽快为您处理(人工客服工作时间:9:00-18:30)。
1. 固态法
固态法是指基体处于固态来制备金属基复合 材料的方法。在时为了复合得更好,希望有少量 液相存在,也即温度控制在基体合金的液相线和 固相线之间。由于整个过程处于较低温度,因此 金属基体与增强材料之间的界面反应不严重。
固态法包括粉末冶金法、热压法、热等静压 法、轧制法、挤压和拉拔法、爆炸焊接法等。
2. 金属基体与增强材料之间浸润性差。 增强材料与基体之间应具有很好的润湿性 (即接触角小于90°),基体才能均匀覆 盖于增强材料表面和渗入到增强材料的间 隙之间,因此,这是得到性能良好的复合 材料的前提。
绝大多数有前景的金属基复合材料体 系中,如碳-铝、碳-镁、碳化硅-铝、氧化 铝-镁等,基体与增强材料之间的浸润性都 很差,必须采取技术措施加以改善。
缺点是工艺复杂,生产效率低,成本高,在实际 生产中受到限制。
(3)原位生成法
原位复合的概念原于原位结晶。原位MMC及 其制备技术已成为材料科学工作者普遍关注的研 究课题。
根据参与合成增强体的两反应组分存在的状 态不同,可将该技术分为气—液、固—液、液— 液和固—固等各种相应模式。
气-液反应法
a . VLS法
优点:能制得增强相与基体润湿性好、结合 性好的复合材料,但需要比较复杂的设备, 生产效率低,比较适合生产长纤维增强的复 合材料,生产其它形式增强相的复合材料难 度较大。
(2)电镀、化学镀和复合镀
利用电化学、氧化还原等原理在增强相(主要 纤维)获得一层改善增强相与基体润湿性和结合 性的沉积层,从而制备复合材料的方法。
固-液反应法
a. 直接反应法
将固态碳粉或硼粉直接加入到高温合金熔体
中,使C或B同合金液中的个别组元反应,在基 体中形成了碳化物或硼化物的增强粒子, A.Chrysanthou等人在氩气保护下,将碳粉与熔 体中的Ti不断发生反应生成了TiC,使得熔体表 面的C粉逐渐减少,直到完全消失,搅拌浇注后 即获得了TiC/Cu复合材料。D.M.Kocherginsky等 人从理论上计算和分析了Al-Si-C三元系中原位生 成SiC颗粒的热力学条件,并在1200℃保温一段 时间后,使Al-30%Si与加入的碳粉完全反应, 生 成 了 原 位 SiC 颗 粒 增 强 的 铝 基 复 合 材 料 。 B.S.Terry等人用这种方法制备了原位TiC/Fe复合 材料。
金属基复合材料起步于60年代初期。当时 由于受到增强纤维品种少的限制,仅发展了硼 纤维增强铝、钛等少量品种。多沿用树脂基复 合材料的成型方法,如铺层工艺和缠绕工艺。 生产的复合材料,价格高昂(如硼-铅复合材料 的价格约为热轧钢的1860倍),仅限于用在航 空航天上。
80年代中期,长纤维增强、短纤维增强、 晶须增强、颗粒增强金属基复合材料开始多种 增强材料(硼、碳、碳化硅、碳化钛、硼化钛、 氧化铝等)、多种基体材料(钢、铝、钛、镁、 锌等)、多种复合方法较为全面的发展。
对制造技术的要求
为得到性能良好、成本低廉的金属基复合材料,制 造技术应满足以下要求:
1. 增强材料以设计的体积分数和排列均匀地分布于 基体中;
2. 尽量不使增强材料和金属基体原有性能下降, 特别是不能对高性能增强材料造成损伤,应使增强材料 和金属的优良性能得以叠加和互补;
3. 尽量避免增强材料和金属基体之间发生不利的化 学反应,应得到合适的界面结构和性能,充分发挥增强 材料的增强效果;
金属基复合材料的研 究现状与发展
材料学院 耿浩然
近代复合材料的发展从基体上来看,首先发 展的是软基体,然后逐渐发展较硬和硬的基体, 即从树脂到金属到陶瓷基体。现代复合材料形成 了树脂基复合材料、金属基复合材料和陶瓷基复 合材料三大类。
金属基复合材料(简称MMC)的性能既优于 金属材料,也优于树脂基复合材料。它既有金属 的性能,也有树脂基无法达到的使用温度高、剪 切强度高、阻燃、不老化、不吸潮、不放气、耐 磨损、导电、导热等金属属性,在一些工业领域 中有广泛的应用前景。
C(s)+Al-Ti(1) — Al(1)+TiC(s)
N2(g) +Al-Ti(1) — Al(1)+TiN(s)+AlN(s)
b. Lanxide法
美国Lanxide公司开发的Lanxide法利用了上述 气 液 反 应 的 原 理 , 它 由 金 属 直 接 氧 化 法 ( DLMOXTM)和金属无压浸渗法(PRLMEXTM)两者 组成:
4. 工艺简单易行,适于批量生产,增强材料价格低, 尽可能直接制成接近最终形状和尺寸的零件。
金属基复合材料制造的难点及解决途径
与树脂基复合材料相比,由于金属固有的物理、 化学特性,使金属基复合材料在制造上存在一些技 术上的困难,需要采取特殊的措施解决:
1.为了保证金属基体有足够的流动性,使之充 分渗透到增强材料之间的间隙中并与之复合,需要 高的制造温度(高于或接近基体的熔点),在高温 下增强材料与基体容易发生界面反应,但也可能氧 化,产生有害的反应。例如,在远低于熔点的温度 下成伤铝,TiC与 容、碳 易Ti生 造5S成 成i3或过AlT4强CiS3的i、2。界与这面硼些结生反合成应。A造lB2成、增钛强与材碳料化的硅损生
是液态金属搅拌铸造法。该法是一种适合于工业规
模生产颗粒增强金属基复合材料的主要方法,工艺 过程简单,生产效率高,制造成本低廉,适于多种 基体和颗粒。基本原理是将颗粒直接加入到基体金 属熔体中,通过一定方式的搅拌使颗粒均匀地分散 在金属熔体中并与之复合,然后浇注成锭坯铸件。
该法制造颗粒增强金属基复合材料存在的主要 困难:(1) 为了提高增强效果要求加入尺寸细小 的颗粒,目前一般在10~30μm之间,陶瓷颗粒与金 属熔体的润湿性差,不易进入和均匀分散在金属熔 体中,易产生团聚;(2) 强烈地搅拌易造成金属 熔体的氧化和大量吸入空气。
金属基复合材料制造技术
金属基复合材料的性能、应用、成本等在 很大程度上取决于材料的制备技术,因此研究 和发展有效的制备技术是金属基复合材料研究 中最重要的问题之一。
冶金工业中现有的常规技术如粉末冶金、 铸造、塑性成型等被用来制造金属基复合材料, 但鉴于材料本身的特殊性质和对材料的要求, 不同类型的金属基复合材料在其制造技术上存 在着很大的差别,有各自的难点,需根据不同 情况采用不同措施加以解决。
还原反应法
利用了化学上的还原反应的原理,即将不稳 定的化合物加入到合金熔体中,使合金熔稳定的陶瓷增强颗粒。
日 本 的 小 桥 真 等 人 将 CuO, 、 ZnO, 、 SnO, 、 C探料r2讨的O3了可和制能Si备性O2原,等位结氧生果化长表物的明加A.入l2C到Ou3O1粒0-A0子l0的增℃反强左应A右l最基的为复Al强液合烈中材, , 生反应成困的难Al2。O3颗粒细小且分布均匀,而Cr2O3-Al的
目前,利用Lanxide法主要用于制备Al基复 合材料或陶瓷基复合材料,其制品已在汽车、 燃气涡轮机和热交换机上得到一定的应用。
c. 反应喷射沉积法(RAD)
该工艺是在DLMOXTM法和喷射沉积工艺的 基础上发展起来的。它是利用一个特殊的液体 喷射分散装置,在氧化性气氛中,将铝液分散 成这撞冷增大些却使强带量 凝表的有细 固层Al基小A,All22复的从OO33合液而膜膜滴形材的破成,料液碎使具。滴分有其R在散A弥表沉D,散面工积同氧分艺过时布化将程内的生金中部成A属,Al2lA的O液相l23O熔迅互 粒3化膜 碰 子速、, 陶瓷增强颗粒的反应合成以及快速凝固等工艺 结合在一起,既使得基体金属的晶粒细小和增 强颗粒的分布均匀,也保证了增强颗粒与基体 的牢固结合,因此,所制得的复合材料可望有 较高的性能。
(a)DLMOXTM法
让高温金属液(如Al、Ti、Zr等)暴露于空气 中T表iO,层2、使扩Z其散rO表,2等面暴)首露,先空里氧气层化中生金后成属又一再被层通氧氧过化化氧,膜化如(层此如逐反A渐复l2O向,3、 最终形成金属氧化物增强的MMC或金属增韧的陶 瓷基复合材料(CMC)。
(b)PRLMEXTM法
优点和缺点:在基体合金中颗粒(晶须)可达到较 高的含量,尺寸也可以在较大范围内变化,产品的 组织均匀致密,无缩孔、气孔等缺陷,形状、尺寸 精确、性能均匀。但设备投资大、工艺周期长、材 料的成本较高,制造大尺寸的零件和坯料有一定困 难。
2. 液态法
液态法是指基体金属处于熔融状态下与固态的 增强材料复合在一起的方法。
这种方法由M.J.Koczak等人发明。其工艺是将 含有C或N的气体通入高温合金液中,使气体中的C 或N与合金液中的个别组分反应,在合金基体中形 成稳定的高硬度、高弹性模量的碳化物或氮化物, 冷却凝固后即获得这种陶瓷颗粒增强的金属基复合 材料。该工艺一般包括如下两个过程:
(a)气体的分解,如
CH 4(g)— C(s)+2H2(g) (b) 气体与合金的化学反应及增强颗粒的形成,如
因此必须采取有效的措施来改善金属熔体对颗 粒的润湿性,防止金属的氧化和吸气。
SiC颗粒增强镁基复合材料
SiC颗粒在铝基体中的分布
SiC晶须在铝基体中的分布
3 其它制造方法
(1)物理气相沉积法和化学气相沉积法
它们都以某种材料气相沉积到增强体表 面上,形成与基体润湿性、相容性和结合性 均好的沉积层,进而获得复合材料的方法。
3. 将增强材料按设计要求均匀分布于基 体中是金属基复合材料制造时的另一困难,增 强材料种类很多,应该针对各自的特点,使用 合适的方法将其均匀分布于基体中。主要途径: