高炉数学模型的进展
高炉炉料结构的研究及其优化配料数学模型的建立

1 高炉优化配料数学模型建立原理
1. 1 优化配料模型的设计思路
本模型的设计 ,以吨铁成本为目标函数 ,结合
高炉炉料结构的专家知识 ,建立了十几个约束条
件 ,通过优化配料模型计算出成本最低 、冶金性能
得到优化的配料方案 。
1. 2 优化配料计算的数学模型
n
(1)目标函数 M inZ = ∑Ci X i
在高炉炉料结构的研究过程中 ,我们对烧结 矿 、球团矿 、天然块矿进行了不同的冶金物化性能 研究 ,由于篇幅限制 ,以两种天然块矿和与烧结矿 的综合配料研究为例 ,简要说明在本模型中如何 使用这些专家知识 。实验对象是宝钢常用的 A、B 块矿和烧结矿 S1,在进行微观特性 、热分解特性 、 热爆裂特性 、还原性 、软化特性和综合炉料的熔滴
Keywords: blast furnace; burden structure; mathematic model; burden op tim ization; linear p rogramm ing
0 前言 我国典型的生铁制造成本分析表明 ,主要原
材料占生铁制造成本的 60%左右 [ 1 ] 。其中含铁 原料的性能又决定了入炉焦比的高低 ,这也就说 明 ,含铁原料即高炉炉料结构是制约高炉生铁成 本的主要因素 。以往对高炉炉料结构的研究 ,大 多停留在定性分析 ,如提出合理的高炉炉料结构 就是无熔剂或少熔剂的情况下造出适宜碱度和成 分的炉渣 、要求具有良好的高温冶金性能 ,能在高 炉内形成合理稳定的软熔带等等 。这些定性分析 的确是高炉炉料结构研究的原则 ,但是对于不同 的钢铁企业来说 ,从这些原则中却找不到具体的 炉料配比 。
XSJK TFeSJK + XQTK1 TFeQTK1 + XQTK2 TFeQTK2 + XTRKK1 TFeTRKK1 + XTRKK2 TFeTRKK2 + XTRKK3 TFeTRKK3 +
高炉炼铁新技术的数学模拟研究

高炉炼铁新技术的数学模拟研究
储满生;郭宪臻;沈峰满;八木顺一郎
【期刊名称】《东北大学学报(自然科学版)》
【年(卷),期】2007(028)006
【摘要】利用多流体数学模型对革新高炉炼铁技术进行了数学模拟,分析评价了革新操作对炉内现象及高炉生产指标的影响.这些革新炼铁技术包括高炉喷吹含氢物质实现富氢还原,高炉使用热压含碳球团实现低温炼铁,以及高炉炉顶煤气喷吹加强C和H的利用.多流体模型的模拟解析表明,高炉超高效率操作(高产、低能耗和低CO2排放)可通过这些革新技术的实际应用来实现.
【总页数】5页(P829-833)
【作者】储满生;郭宪臻;沈峰满;八木顺一郎
【作者单位】东北大学,材料与冶金学院,辽宁,沈阳,110004;安阳钢铁集团公司,炼铁厂,河南,安阳,455004;东北大学,材料与冶金学院,辽宁,沈阳,110004;东北大学,多元物质科学研究所,日本,仙台,980-8577
【正文语种】中文
【中图分类】TF531
【相关文献】
1.基于高炉炼铁和非高炉炼铁的能耗比较 [J], 栗聖凯
2.低碳高炉炼铁新技术及在安钢应用的可行性 [J], 刘润生
3.比较分析高炉炼铁与非高炉炼铁技术 [J], 贡献锋
4.高炉炼铁和非高炉炼铁能耗比较浅析 [J], 刘洋
5.广钢高炉炼铁系统工程设计及采用的新技术 [J], 阎峰
因版权原因,仅展示原文概要,查看原文内容请购买。
采用数学模型计算高炉炉缸侵蚀状况
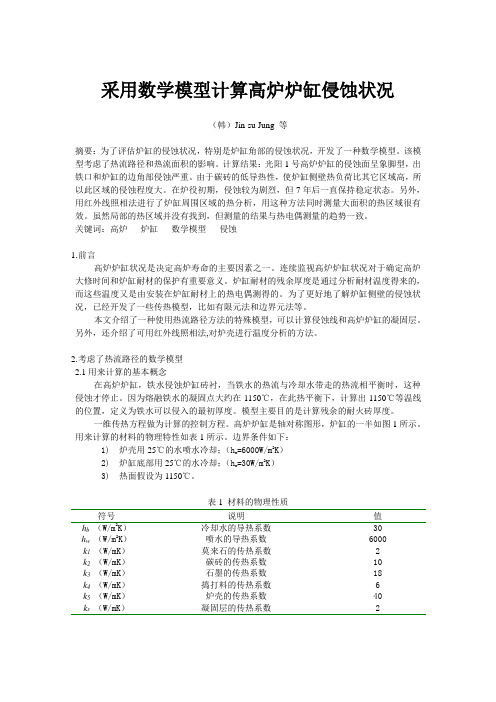
采用数学模型计算高炉炉缸侵蚀状况(韩)Jin-su Jung 等摘要:为了评估炉缸的侵蚀状况,特别是炉缸角部的侵蚀状况,开发了一种数学模型。
该模型考虑了热流路径和热流面积的影响。
计算结果:光阳1号高炉炉缸的侵蚀面呈象脚型,出铁口和炉缸的边角部侵蚀严重。
由于碳砖的低导热性,使炉缸侧壁热负荷比其它区域高,所以此区域的侵蚀程度大。
在炉役初期,侵蚀较为剧烈,但7年后一直保持稳定状态。
另外,用红外线照相法进行了炉缸周围区域的热分析,用这种方法同时测量大面积的热区域很有效。
虽然局部的热区域并没有找到,但测量的结果与热电偶测量的趋势一致。
关键词:高炉炉缸数学模型侵蚀1.前言高炉炉缸状况是决定高炉寿命的主要因素之一。
连续监视高炉炉缸状况对于确定高炉大修时间和炉缸耐材的保护有重要意义。
炉缸耐材的残余厚度是通过分析耐材温度得来的,而这些温度又是由安装在炉缸耐材上的热电偶测得的。
为了更好地了解炉缸侧壁的侵蚀状况,已经开发了一些传热模型,比如有限元法和边界元法等。
本文介绍了一种使用热流路径方法的特殊模型,可以计算侵蚀线和高炉炉缸的凝固层。
另外,还介绍了可用红外线照相法,对炉壳进行温度分析的方法。
2.考虑了热流路径的数学模型2.1用来计算的基本概念在高炉炉缸,铁水侵蚀炉缸砖衬,当铁水的热流与冷却水带走的热流相平衡时,这种侵蚀才停止。
因为熔融铁水的凝固点大约在1150℃,在此热平衡下,计算出1150℃等温线的位置,定义为铁水可以侵入的最初厚度。
模型主要目的是计算残余的耐火砖厚度。
一维传热方程做为计算的控制方程。
高炉炉缸是轴对称图形,炉缸的一半如图1所示。
用来计算的材料的物理特性如表1所示。
边界条件如下:=6000W/m2K)1)炉壳用25℃的水喷水冷却;(hw2)炉缸底部用25℃的水冷却;(h=30W/m2K)w3)热面假设为1150℃。
表1 材料的物理性质符号说明值h b(W/m2K)冷却水的导热系数30h w(W/m2K)喷水的导热系数6000k1(W/mK)莫来石的传热系数2k2(W/mK)碳砖的传热系数10k3(W/mK)石墨的传热系数18k4(W/mK)捣打料的传热系数6k5(W/mK)炉壳的传热系数40k s(W/mK)凝固层的传热系数22.2计算过程图2是计算耐火砖厚度的过程。
高炉过程控制讲义

第一章绪论1.1 高炉过程控制的基本概念高炉过程控制就是高炉操作者根据从仪表上获取的检测数据,对高炉运行状况进行判断与预测。
高炉控制的目标是要及时发现并调整不稳定的炉况,生产出合格生铁,同时要注意降低燃料消耗和高炉长寿的问题。
1.2 高炉过程控制的发展概况高炉冶炼过程控制模型可以归纳为三种类型:1)高炉冶炼过程数学模型2)高炉冶炼过程优化模型3)高炉冶炼过程专家系统1.3 高炉过程控制的发展趋势实现高炉炼铁过程的闭环自动化。
结论:高炉冶炼过程控制模型以现代炼铁理论、自动控制理论和计算机技术为基础,由低级向高级发展,正在日臻完善,而且逐步形成了自己的一套比较系统的理论,并在生产中得到日益广泛的应用。
第二章高炉过程控制系统的构成2.1 高炉生产的特点1)过程复杂。
高炉冶炼过程为非均相、非线性、非稳态连续的物理和化学变化过程。
高炉内各种物理化学现象及其影响因素之间相互作用、相互影响,表现出很强的分布特性和耗散系统特征。
另外,高炉冶炼过程与外部环境之间的关系复杂。
冶炼过程涉及的物料流量大,相关处理设备繁多,前后工序的连贯性强,外部环境发生的变化都将对冶炼过程产生重要影响。
2)检测信息不完全。
高炉冶炼过程是在密闭状态下进行,内部情况大多无法直接观测,炉内高温、多相、含尘和机械冲刷等特点给过程变量的检测带来极大困难,一些用于建模和控制所需要的重要参数和变量目前还难以测得,一些测得的信息也含有较大噪声。
具体表现在检测项目少,且多局限于过程的边界(炉顶、渣铁、风口、炉身静压力等),很多重要检测数据的采样频度低。
3)反应迟钝。
即对控制动作的响应十分缓慢,时间常数很大,各个操作参数对过程的作用具有很大的滞后期,如:各操作变量对控制目标之一的[Si]的动态变化响应的延迟时间约为3-7小时。
4)可控范围狭窄。
一方面,铁水质量必须满足用户的要求,这使得高炉的各种控制参数可调范围相对较小;另一方面,炉况必须早调、小调,才不致于发生过大的波动,否则炉况将急剧恶化而导致失控。
高炉能源利用效率建模与分析

变 量 。如 今 的 多 流体 高 炉 数 学 模 型 基 于 多 流 体理 论 、冶 金 传输 原 理 、反 应 动 力 学 以及 计 算 流体 力
学 等理 论 模拟 “ ,具 有 更好 的通 用 性 。但这 些模
型 主 要 针 对 高 炉 内 部 热 力 学 、流 体 力 学 等 进 行 分
[ 4 ] 第3 卷 12 3
第1 期 2
21— 2上 ) 01 1 (
l
能 效 的 分 析 需 要 大 量 的 数 据 ,而 且 所 需 的数
据 需 要 一 定 的相 关 性 , 因此 只有 很 少 量 的数 据 能 够 用 于 深 层 次 分 析 ,从 而 达 到 找 出各 能 源 间及 其 与 产 量 之 间 的关 系 ,大 多 数 数 据 只能 够 计 算 出基 本 的 评 价 指 标 ,仅 能 够 为 企 业 提 供 考 核 的 依 据 , 缺 乏 深 层 次 分 析 的 价 值 。基 于 这种 情 况 ,建 立 了 能 耗 统 计 模 型 、能 效 分 析 模 型 、 能 源 需 求 预 测模 型 ,一 方 面 可 以 利 用 计 算 出 的 结 果 来 代 替 缺 少 的
图 。系统 的分 析 整 个 系统 是 一 件很 复 杂 的事 情 , 需 要 消耗 大 量 的人 力 物 力 ,但 仍 可 能 得 不 到理 想
中的结果 。
菊 、杜 涛 等 教 授 在 此基 础 上 ,建 立 了企 业 的 平 衡
模 型 、产 耗 模 型 等 ,细致 的分 析 了各 个 流 程 的 能 耗 情况" l 。邱 东 等 人 则 将 能 源 模 型 划 分 为 企 业 级 、工厂 级 等层 次 。他 们和其 他 一 些学者 的 众 多 】 研 究 成 果为 我 国钢 铁 工 业 的 研 究做 出 了 巨大 的贡
高炉软熔带数学模型研究

6
k
i= 1
ΒiR 3 i = 0
( 2)
( 2) E rgun 方程 g rad P = - ( f 1 + f
f f
1 2 2
2
Gg ) Gg
3 2 3
→
→
( 3) ( 4) ( 5)
) Λg [ Θ = 150 ( 1 - Ε dp) ] gΕ (< ) (Θ = 1175 ( 1 - Ε dp) gΕ <
图 1 高炉软熔带数学模型数据输入画面
F ig 11 D a ta inp u t m enu of b la st fu rnace cohesive zone m odel
・1 6 ・
钢 铁 ቤተ መጻሕፍቲ ባይዱ 第 39 卷
图 2 高炉软熔带数学模型主画面
F ig 12 T he m a in m enu of b la st fu rnace cohesive zone m odel
Study on M a thema t ic M odel of Cohes ive Zone in Bla st Furnace
JI N G W enbo, TAN G Feila i
(T echn ica l Cen ter of N anchang Iron and Steel Co. , L td 1, N anchang 330012)
→ →
n
G
( 7)
流强度等。 根据炉衬化学侵蚀机理知, 高炉长寿高效 要控制内衬表面热流强度, 当内衬表面热流强度小 于 2312 kJ (m 2 ・ s) , 可防止炉衬侵蚀。 4 应用 将其应用到南昌钢铁有限责任公司炼铁厂 1 号 高炉 上, 其 硬 件 配 置 如 下。 ① 计 算 机 主 机 2 台, P III733 128 M b 20Gb 1144M b 50X 网 卡 1 台; 486DX 66 8M b 400 M b 网 卡 1 台。 ② 显 示 器, PH I L P 21 英寸与 COM PAQ 14 英寸 1 台。 高炉软熔带数学模型数据输入与主画面如图 1 和图 2 示意。 模型中所需参数通过模型主画面上的 命令键进行自动或手动输入。 运用该模型可对影响 软熔带的具体参数 ( 利用系数、 矿批重、 焦炭负荷、 料 ) 线、 角和 角等 进行计算并显示出高炉内衬表面 Α Χ 热流强度分布和软熔带位置、 形状等。 南钢 1 号高炉的高炉软熔带模型计算研究发现 该高炉有如下特点: 炉身下部、 炉腰和炉腹内衬表面 热流强度比其他部位大, 但属正常范围 ( 1116 ~ 2312 2 kJ (m ・ s) ) 下限。正常生产时, 软熔带形状基本上 是 “ 型。 为实现高炉长寿高效, 采用正分装或等料 W” 线装料顺序。 控制: 料线, 018 ~ 112 m ; 矿石批重≥ 12 1 0 t; 溜槽倾角 , 3 0~ 3 4 ° ; 焦炭负荷 , 3 1 8~ 4 1 2 t t。
基于反应动力学的全高炉数学模型概述

基于反应动力学的全高炉数学模型概述储满生(东北大学)摘要 高炉是一个气固向流的复杂冶金反应器。
为了更好地理解、控制和改进高炉炼铁过程,更多的努力被用于开发高炉数学模型,特别是基于反应动力学理论而开发的反应动力学模型。
本文简述了全高炉反应动力学模型的发展历程,介绍了该类模型的代表-基于多流体理论、反应动力学、冶金传输理论而创建的多流体高炉数学模型,并对全高炉数学模型的未来发展做出了若干展望。
关键词 高炉 数学模型 炼铁 计算流体力学REV I E W S O N TO TAL BLAST FURNACE M ATHEM AT ICALMOD EL BASE D O N REACT IO N-K I NET ICSChu Mansheng(Northeastern University)ABSTRACT B last furnace is a comp lex metallurgical react or with gas-s olid counter-fl ow.I n order t o understand, contr ol and i m p r ove the blast furnace p r ocess,more eff orts are made t o devel op mathe maticalmodels,es pecially ones based on the theories of reacti on-kinetics.A t first,hist oric revie ws on t otal blast furnace model of reacti on-kinetics are made in the paper.Then,multi-fluid blast furnace is intr oduced as one of the latest reacti on-kinetics models.Multi-fluid model is devel oped on basis of multi-fluid theory,kinetics,trans port phenomena theory and computati onal fluid dyna m2 ics.Finally,s ome pers pectives are made f or the future devel op ing trends of t otal blast furnace models.KE Y WO RD S blast furnace mathe matical model ir on making computati onal fluid dyna m ics0 前言在高炉操作过程中,由炉顶加入炉料,从炉缸渣铁口排放渣铁;而从风口鼓入热风和喷吹煤粉,产生的煤气从炉顶逸出。
高炉布料数学模型的开发及应用
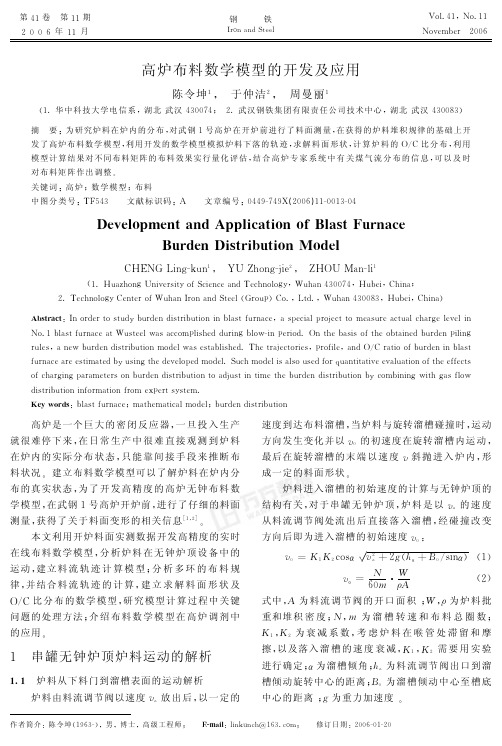
U # * # 0 . # " / ) " ,9 0 + 2 ) / + "3K 0 ) 6 /I E $ " ) 2 # F F F K E $ , # "U + 6 / $ + : E / + "X , # 0
" # " ! ! B@c 2A O F ) > W D ) C ( ) > F . @ZK b * ) > / F !HK ? !? I I U
# % $ 3 Q ( S 3 6 S F ) " !’ !$ " 5" $ $0 "0 # * 4# $ & 47
&
本文利用开炉料面实测数据开发高精度的实时 在线布料数学模型 ! 分析炉料在无钟炉顶设备中的 运动 ! 建立 料 流 轨 迹 计 算 模 型 # 分析多环的布料规 律! 并结合 料 流 轨 迹 的 计 算 ! 建立求解料面形状及 % 研究 模型计 算 过 程中 关 键 Z B 比 分布的数学模 型 ! 问题的处理方法 # 介绍布料数学模型在高炉调剂中 的应用 &
沿’ 方向的匀速运动及= 方向的自由落体运动 $ 炉料斜下抛运动轨迹的水平投影距离为 %
>$
" # # # 3 646 3 (3 5" ! 43 = 4# $ (= $# =* ’ () ’ ’ 5 " # 7
? " # " # " 式中 ! # # " 为 炉 料 在 炉 内 的 堆 角’ # 为炉料的自然堆 角’ 为修正系数 ’ 为料线深度 ’ 0 ? " 为炉喉半径 $
( "! #)
- 1、下载文档前请自行甄别文档内容的完整性,平台不提供额外的编辑、内容补充、找答案等附加服务。
- 2、"仅部分预览"的文档,不可在线预览部分如存在完整性等问题,可反馈申请退款(可完整预览的文档不适用该条件!)。
- 3、如文档侵犯您的权益,请联系客服反馈,我们会尽快为您处理(人工客服工作时间:9:00-18:30)。
第17卷第4期2007年4月 中国冶金 China Metallurgy Vol.17,No.4 Apr.2007作者简介:储满生(19732),男,博士后; E 2m ail :chumansheng @ ; 修订日期:2006211222高炉数学模型的进展储满生1, 郭宪臻2, 沈峰满1, 八木顺一郎3(1.东北大学材料与冶金学院,辽宁沈阳110004;2.安阳钢铁集团公司炼铁厂,河南安阳455004;3. 北大学多元物質科學研究所,日本仙台980-8577)摘 要:高炉是一个复杂的气固向流反应器。
为了理解、控制和改进高炉炼铁过程,更多的努力被用于开发数学模型。
全高炉动力学模型经历了从一维到多维、稳态到非稳态、简单到复杂的发展过程。
多流体高炉模型是全高炉动力学数学模型研究的最新成果之一。
该模型基于多流体理论,可对炉内主要现象进行多维数学模拟,并能精确地预测高炉在指定条件下的操作指标。
未来的高炉数学模型应朝复杂化和实用化方向发展,并拓展解析范围、提高模拟精度。
关键词:高炉;数学模型;多流体理论中图分类号:TF531 文献标识码:A 文章编号:100629356(2007)0420010205Development of B last Furnace Mathem atical ModelC HU Man 2sheng 1, GUO Xian 2zhen 2, SH EN Feng 2man 1, YA GI J un 2ichiro 3(1.School of Materials and Metallurgy ,Northeastern University ,Shenyang 110004,Liaoning ,China ;2.Iron 2Making Plant ,Anyang Iron and Steel Co Ltd ,Anyang 455004,Henan ,China ;3.Institute of Multidisciplinary Research for Advanced Materials ,Tohoku University ,Sendai ,980-8577,J apan )Abstract :Blast f urnace is a complex metallurgical reactor with gas 2solid counter flow.In order to understand ,con 2trol and improve the blast f urnace process ,more efforts are made to develop mathematical models.In the past dec 2ades ,the reaction 2kinetics models of total blast f urnace have generally developed f rom one 2dimensional ,stead state and simple models to multi 2dimensional ,transient and complex ones.Multi 2fluid blast f urnace model is one of the latest reaction 2kinetics models ,which is based on multi 2fluid theory and can make multi 2dimensional treatment of in 2furnace phenomena and accurate prediction of operational parameters under the given conditions.The f uture models of blast f urnace should be more complicated and applicable after enlarging simulation range and improving computation exactness.K ey w ords :blast f urnace ;mathematical model ;multi 2fluid theory 高炉生产是由炉顶加入炉料,从炉缸渣铁口排放渣铁;而从风口鼓入热风和喷吹煤粉,煤气从炉顶逸出。
所以,可将高炉看作是存在炉料下降和煤气上升2个逆向运动的反应器,炉内所有传输现象和反应均发生于炉料与煤气的向流运动中。
高炉内多种多相物质共存且相互作用,且诸多物理化学现象同时发生,故高炉在化工领域被认为是最复杂的冶金反应器之一。
随现代测控技术的发展和对实际运行高炉的炉体解剖,人们获得了大量有用数据,对高炉有了更深理解,但光凭这些仍很难详细掌握炉内的现象。
因此,为更好地理解、控制和改进高炉炼铁过程,更多的努力用于开发高炉数学模型[1]。
根据对高炉内传输现象描述方法的不同,数学模型分为平衡理论模型、热化学模型和反应动力学模型;按所考虑的空间坐标维数,分为一维、二维和三维模型;考虑时间变量与否,有稳态模型和非稳态模型[1~2]。
高炉炼铁技术在过去几十年中得到长足的进步。
为提高产量、降低能耗和减少环境负荷,喷吹煤粉和有效利用含碳含铁废弃物等大量新技术逐渐被采用,高炉的功能不断扩大,炉内现象更趋复杂化。
而建立在反应动力学和传输现象理论基础上的反应动力学数学模型是一有用的工具,可用其详细分析炉内状态和精确预测高炉操作性能。
1 高炉数学模型的发展历程 高炉反应动力学模型的发展历程见图1。
最早获得发展的是高炉一维模型,且先有稳态模型,随后逐渐发展为非稳态。
鞭严等人在20世纪60年代末开发的高炉稳态一维模型最具代表性[2]。
在鞭严的模型中,考虑了炉内主要化学反应和传热过程,模拟结果给出了主要工艺变量沿高炉高度方向上的分布。
后来,许多研究者仿效鞭严的建模思想建立了一系列用于解决不同问题的高炉数学模型。
这些早期的高炉模型很好地把握了对局部和全高炉的能量平衡和物质平衡这一基本规律,因而在模拟高炉现象、分析操作参数对炉况和冶炼指标的影响、指导开停炉等方面获得了相当的成功。
如一些模型应用于分析鼓风压力波动对高炉操作的影响、预测最低燃料比以及模拟顶压操作等实践[2]。
但是,对于一维高炉模型来说,过程参数被假设为径向均布,而高炉的解剖和取样分析证实了气体温度和炉内物质成分等在径向上都是不均匀的。
另外,在其建模过程中,炉内物质和能量的传输过程只能通过常微分方程来描述。
再加上边界值设定不合理等缺陷,这些早期一维模型的预测精度和应用范围都很有限。
到80年代,计算机技术的发展允许模型处理更大的矩阵,新建立的模型可采用偏微分方程作为其控制方程。
在此期间,大量二维高炉模型被开发,其中较为知名的有Hatano和Kurita的模型,Yagi、Takeda和Omori的模型,Sugiyama和Sugata的BRIGH T模型[1,2]。
二维模型主要被用于描述炉内更为复杂的现象,即评估操作条件对高炉操作性能和炉况的影响,分析软熔带的变化和影响,模拟和开发高炉炼铁新技术等。
总体来说,这些模型对指导实际高炉操作和促进炼铁技术的进步做出了一定的贡献。
到90年代初,一个基本概念“多流体理论”被提出,即用多相流和相间双向相互作用来描述发生在炉下部的现象,且炉内物质相应通过流动机制来加以区分。
因此,除了最基本的气2固2液态物质外,被炉内气流挟带的未燃煤粉被处理为一独立的粉相[3]。
在随后基于这个理论而发展的高炉数学模型中,根据物性的不同,液相又进一步划分为渣相和铁水相,而粉相分为静态滞留粉相和动态滞留粉相。
这些模型都总称为“多流体高炉数学模型”[4~10],属于较为复杂全面的全高炉反应动力学模型。
目前,多流体模型能合理处理二维和三维的问题。
2 多流体高炉数学模型 多流体高炉数学模型基于多流体理论、冶金传输原理、反应动力学以及计算流体力学等理论模拟高炉炼铁过程[4,5,7]。
模型主要考虑了从渣面到料面的整个填充区域,且认为高炉是轴对称的。
多流体模型中将气相、固相(焦炭和含铁炉料)、铁水、熔渣和粉相分别视为具有各自流动机制的独立相,每相由1个或多个组元组成,且每个组元具有独立的成分和物性。
模型中考虑的物质和相见表1。
图1 全高炉反应动力学模型的发展历程Fig.1 Development of blast furnace m athem atical models表1 多流体模型中考虑的相和物质T able1 Ph ases and chemical species considered in multi2fluid model 相物质气相CO,CO2,O2,H2,H2O,N2,SiO,CH4固相块矿Fe2O3,Fe3O4,FeO,Fe,脉石(CaO,Al2O3,MgO),SiO2,H2O 烧结矿Fe2O3,Fe3O4,FeO,Fe,脉石(CaO,Al2O3,MgO),SiO2,H2O球团Fe2O3,Fe3O4,FeO,Fe,脉石(CaO,Al2O3,MgO),SiO2,H2O焦炭C,SiC,脉石(CaO,Al2O3,MgO),SiO2,H2O铁水Fe,C,Si熔渣FeO,脉石(CaO,Al2O3,MgO),SiO2粉相煤粉(废塑料)C,脉石(CaO,Al2O3,MgO),SiO2,挥发分11第4期 储满生等:高炉数学模型的进展 多流体模型中各相间的相互作用见图2。
图中实线代表动量、质量和能量的完全相互作用,点线代表质量的传输。
模型认为气2固相与其它相之间均有完全的质量、动量和能量交换,而不连续相(液相和粉相)间不进行动量交换,但通过化学反应和相变进行质量和能量的交换。
图2 多流体模型中相间相互作用示意Fig.2 Diagram of interphase interactions consideredin multi 2fluid model 多流体模型采用一系列偏微分方程来描述炉内各相的行为。
由于各相之间同时且双向相互作用,故这些偏微分方程是强烈耦合的,须同时求解。
所有方程可用一个统一化的形式来加以描述,即: 99x (εi ρi u i ψ)+1r 99r (r εi ρi v i ψ)=99xεi τψ9ψ9x + 1r 99rr εi τψ9ψ9r +S ψ(1)式中i ———要考虑的气相、固相、铁水、熔渣和粉相; ψ———求解的变量,通过改变ψ,分别代表质量、动量、能量方程以及连续性方程; εi ———相i 的体积分数; τψ———有效扩散系数,根据所求解的独立变量具有不同的意义。