GCr15钢接触表面塑性形变强化与裂纹萌生机制
GCr15钢的N-PIII强化
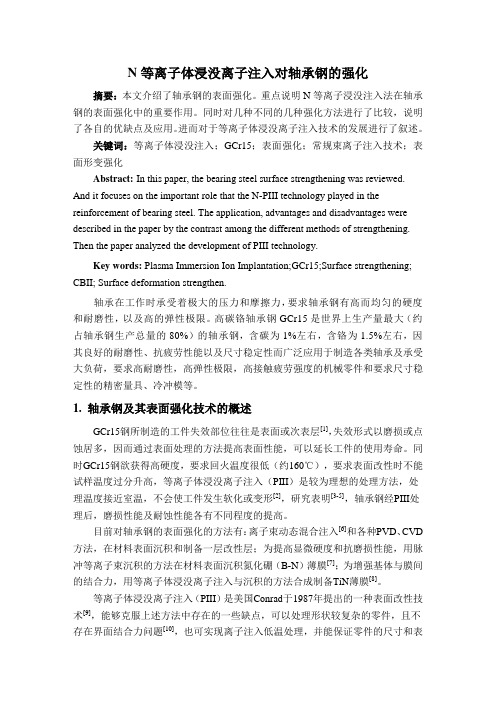
N等离子体浸没离子注入对轴承钢的强化摘要:本文介绍了轴承钢的表面强化。
重点说明N等离子浸没注入法在轴承钢的表面强化中的重要作用。
同时对几种不同的几种强化方法进行了比较,说明了各自的优缺点及应用。
进而对于等离子体浸没离子注入技术的发展进行了叙述。
关键词:等离子体浸没注入;GCr15;表面强化;常规束离子注入技术;表面形变强化Abstract:In this paper, the bearing steel surface strengthening was reviewed. And it focuses on the important role that the N-PIII technology played in the reinforcement of bearing steel. The application, advantages and disadvantages were described in the paper by the contrast among the different methods of strengthening. Then the paper analyzed the development of PIII technology.Key words: Plasma Immersion Ion Implantation;GCr15;Surface strengthening; CBII; Surface deformation strengthen.轴承在工作时承受着极大的压力和摩擦力,要求轴承钢有高而均匀的硬度和耐磨性,以及高的弹性极限。
高碳铬轴承钢GCr15是世界上生产量最大(约占轴承钢生产总量的80%)的轴承钢,含碳为1%左右,含铬为1.5%左右,因其良好的耐磨性、抗疲劳性能以及尺寸稳定性而广泛应用于制造各类轴承及承受大负荷,要求高耐磨性,高弹性极限,高接触疲劳强度的机械零件和要求尺寸稳定性的精密量具、冷冲模等。
GCr15钢球断裂分析

2.裂纹是由内向外扩展的,表明钢球断裂起始于内部疏松缺陷部位。但钢球是在磨制过
4
程中断裂的,因此残余应力和研磨产生的相变应力是可能的应力因素。通常研磨产生的应力
过大主要出现表面裂纹,故淬火残余应力应该是该钢球断裂的主要应力因素。
3.综合上述分析,钢球中部存在大面积疏松缺陷,使钢球强度不足是导致钢球开裂的主
断口分析 钢球是沿中剖面发生断裂的,断口低倍形貌如图 1(由于钢球直径较大,为了可以方便
分 地在 SEM 中进行观察,已将断口用线切割分为四块),断裂面完全垂直表面,中心部分断口
粗糙,边缘部分断口较平坦致密。在 SEM 中观察看出,钢球中部断口为严重的疏松缺陷断 口,如图 2,疏松缺陷分布区域较宽,其中集中分布区域在 1/2 半径以内的钢球中心部。钢
网
图 1 钢球断口形貌
1
中 国 应 急 分 图 2 钢球心部断口微观形态 析 网
图 3 钢球表面层断口的微观形态
2
中 国 图 4 钢球 2/3 半径处的断口微观形态
断口分析表明,裂纹是由内向外扩展的,钢球断裂起始于内部的疏松缺陷,钢球中部
应 存在大面积疏松缺陷是钢球开裂的重要原因。中心层和表面层之间的过渡区为准解理断口,
应 850~900℃)-球化退火-毛坯球软磨-钢球热处理(淬火,加热温度 825℃,保温 45 分钟,
水冷)-回火(160℃,8 小时)-钢球硬磨(转速 60n/分,压力 2~4KN)- 钢球研光。经上 述处理工序后要求钢球表面硬度为 58~64 HRC。对钢球发生断裂的原因进行了分析。
急 测试过程与结果
表明钢球该部分基体组织不都是回火隐针马氏体。 金相组织
急 在垂直断裂面的方向作钢球剖面,观察钢球从心部到表面层的金相组织。可以看出,该
GCr15钢超长寿命疲劳破坏的机理_李伟

钢 、合金钢和铸铁等金属材料在承受低于其疲劳强 度的交变载荷超过 107 周次后 , 仍然会发生疲劳破 坏 。 因此 , 为了满足工程安全及可靠性设计的要求 , 对材料在 107 周次以后的疲劳行为进行研究具有重 要意义 , 而此时的 疲劳称之为 超长寿命 疲劳(very high cycle fat igue , VH CF)。
按照线弹性断裂力学理论 , 材料内部较小夹杂 物处的应力强度因子幅值 ΔK 低于其表面裂纹扩展 门槛值 ΔK th , 在 夹杂物周 围不会形 成可扩展 的裂 纹 , 可是上述理论对于强度等级较高的高强度钢则 不适用 。 对经渗碳处理的铬-钼钢和铬钢以及镍-铬-
· 37 ·
李 伟 , 等 :GCr15 钢超长寿命疲劳破坏的机理
为 0 .99C , 0 .23Si , 0 .32M n , 1 .50C r , 0 .10Cu , 0.06Ni , 0 .02M o , 0 .02P , 0 .10S 。 试样 的形状及 尺 寸如图 1 所示 。 将试样先在 75 kW 的 RJ75 型电阻 炉里加热 , 其淬火温度为(840 ±5) ℃, 保温时间为 15 min , 接着投入 20 #机油里淬火至 200 ℃;然后在 160 ℃回火 , 时间 2 h , 空冷 。热处理后 , 其组织为回 火马氏体 , 组织中球形碳化物分布均匀 , 见图 2 。
(a) 刀痕引起的破坏 (b) 夹杂物引起的破坏
图 1 试样的形状及尺寸 Fig .1 Shape and dimension of specimen
形变热处理对GCr15钢机械性能的影响
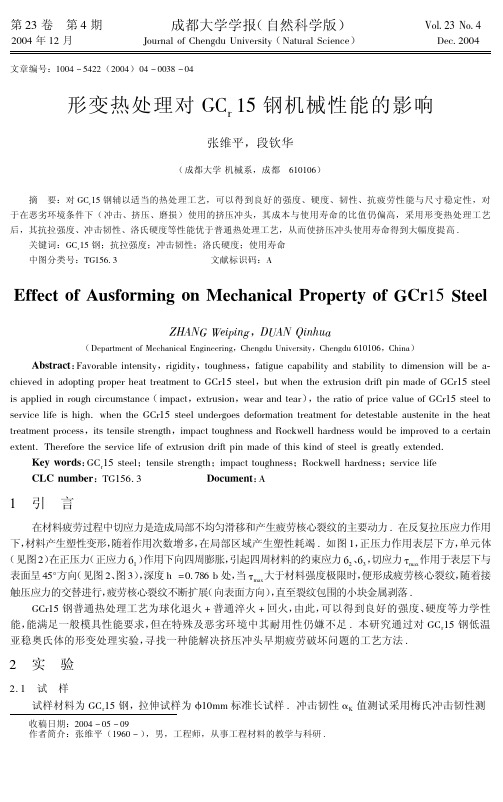
!""#$% &" ’()"&*+,-. &- /#$01-,$12 3*&4#*%5 &" 67*+A 8%##2
!"#$% &’()(*+,,-#$ .(*/01
( ?4H0.;I4/; &1 J4>30/8>0’ K/58/44.8/5,234/56- 7/894.:8;<,234/56- C+*+*C ,238/0)
・ $>・
! ! ! ! ! ! 图 "! 接触压应力的椭圆体分布! ! ! ! ! ! ! ! ! ! ! ! ! ! ! 图 #! 三向应力图
! ! ! ! 图 $! 应力圆示意图! ! ! ! ! ! ! ! ! ! ! ! ! 图 %! &’(") 钢热处理工艺曲线
试方法, 试样尺寸为 "* + "* + )),,, 缺口半径 ",,- 硬度试样用拉伸试样头部 ( . 形垫铁垫平) - 试样件 取平均值 - 材料为 &’(") 钢, 穿孔挤压冲头 ( !#),,) , 各两件 数各 ) 件, #/ #! 热处理工艺 热处理过程为先经球化退火, 再于淬火的低温亚稳奥氏体阶段进行形变热处理, 温度为 )"*0 时形 变 ( 不同形变量) , 再于 "1)0 回火 - 热处理具体工艺见图 %-
’9)%*1$%: L09&.0M’4 8/;4/:8;<,.85868;<,;&-53/4::,10;85-4 >0H0M8’8;< 0/6 :;0M8’8;< ;& 68I4/:8&/ N8’’ M4 0O >384946 8/ 06&H;8/5 H.&H4. 340; ;.40;I4/; ;& E2.+A :;44’,M-; N34/ ;34 4P;.-:8&/ 6.81; H8/ I064 &1 E2.+A :;44’ 8: 0HH’846 8/ .&-53 >8.>-I:;0/>4( 8IH0>;,4P;.-:8&/,N40. 0/6 ;40.) ,;34 .0;8& &1 H.8>4 90’-4 &1 E2.+A :;44’ ;& :4.98>4 ’814 8: 3853Q N34/ ;34 E2.+A :;44’ -/64.5&4: 641&.I0;8&/ ;.40;I4/; 1&. 64;4:;0M’4 0-:;4/8;4 8/ ;34 340; ;.40;I4/; H.&>4::,8;: ;4/:8’4 :;.4/5;3,8IH0>; ;&-53/4:: 0/6 R&>SN4’’ 30.6/4:: N&-’6 M4 8IH.&946 ;& 0 >4.;08/ 4P;4/;Q F34.41&.4 ;34 :4.98>4 ’814 &1 4P;.-:8&/ 6.81; H8/ I064 &1 ;38: S8/6 &1 :;44’ 8: 5.40;’< 4P;4/646Q :#5 ;&*<): E2 . +A :;44’;;4/:8’4 :;.4/5;3;8IH0>; ;&-53/4::;R&>SN4’’ 30.6/4::;:4.98>4 ’814 7=7 -(+9#*:FE+ACQ "# # # # # # >&$(+#-%: G
金属材料的塑性变形与强化机制

金属材料的塑性变形与强化机制金属材料广泛应用于制造业、建筑业、交通运输等领域,其具有高强度、优良的导电导热性能、易于加工等优点。
然而,金属材料的应力应变曲线呈现塑性区,即在一定范围内,随着应力的增大,材料的应变会逐渐增大,直到达到极限,然后发生塑性变形。
在工程实践中,如何控制金属材料的塑性变形,提高其性能,使其更加适用于各个领域,成为了当前研究的热点之一。
1. 金属材料的塑性变形与尺寸效应塑性变形过程中,材料内部原子的晶体结构和排列方式发生了变化,从而导致了材料的强化和塑化。
同时,尺寸效应也对金属材料塑性变形产生了重要的影响。
研究表明,当金属材料的直径小于100纳米时,由于晶体结构的变化,材料的电学性能和机械性能会发生显著变化。
在实际应用中,如何利用尺寸效应来控制金属材料的塑性变形是一个重要的研究课题。
一方面可以采用纳米技术加工制备金属纳米材料,如纳米管、纳米棒、纳米线等,来控制材料的晶体结构,使其具有更好的力学性能和导电性能;另一方面,可以利用不同的加工工艺和冷加工方法,来实现对材料晶体结构的调控,从而达到强化和塑化金属材料的目的。
2. 金属材料塑性变形的机理金属材料的塑性变形机理主要是由晶体滑移和重结晶两种过程组成。
晶体滑移是指晶格错位后,晶体中原子的移动和重组。
原子的移动发生在晶格中的间隙和空位中,导致晶体中的错位位移和变形。
观察金属材料的断面可以发现,断面中由于晶体滑移所引起的形变形成了大量细小的位错,从而促使晶体不断地沿位错的移动方向继续发生滑移。
另一种机理是重结晶。
当金属材料发生过大变形时,原本的晶粒会发生变化,小的晶粒会变成大的晶粒。
这个过程叫做重结晶,它会导致材料内部结构的变化,从而促进材料通道滑移和位错修复。
3. 金属材料强化机制金属材料的强化可以通过多种途径实现。
其中,冷加工是一种非常有效的方式。
通过冷加工(如轧制、拉伸、挤压等)可以使材料产生高密度的位错,而这些位错会增加晶体滑移的阻力,使得材料的屈服强度和拉伸强度得到了提高。
滚动轴承用钢GCr15钢的热处理原理-8页精选文档

第一章滚动轴承用钢GCr15钢的热处理原理一、滚动轴承用钢应具有的特性1、高的接触疲劳强度;2、高的耐磨性;(发生滑动摩擦的主要部位)1)、滚动体与滚道的接触面;2)、滚动体与保持架兜孔的接触面;3)、保持架引导与套圈引导档边的接触面;4)滚子的端面与套圈档边的接触面。
3、高的弹性极限;4、高的硬度;5、一定的韧性;6、好的尺寸稳定性;7、一定的防锈功能;8、良好的工艺性能。
二、GCr15钢的物理性能1、GCr15钢的临界点:Ac1:760℃ Acm:900℃Ar3:707℃ Ar1:6952、GCr15钢的Ms点:Ms点随着奥氏体固溶度的变化而变化,亦即随着奥氏体温度的升高而降低,GCr15钢在860℃温度Ms点为216~225℃。
三、铬轴承钢热处理基础1、基本概念1)、奥氏体:是碳及合金元素溶于r-Fe八面体间隙的间隙式固溶体。
特征:[1]、在钢的各种组织中,奥氏体的比容最小;[2]、奥氏体的塑性高,屈服强度低,容易塑性变形加工成型。
2)、珠光体:是过冷奥氏体共析分解的铁素体和碳化物的整合组织片状珠光体:是指在光学显微镜下能够明显看出F与Fe3C呈片状分布的组织状态。
根据片间距的大小分为普通片状珠光体、索氏体、屈氏体。
粒状珠光体:铁素体基体上分布着粒状Fe3C的组织。
GCr15的正常锻造后组织应为细珠光体类型组织及细小的网状碳化物组成,不允许有>3级的网状碳化物及明显线条状组织,不允许有粗针状马氏体和粗片状珠光体组织。
3)、马氏体:是碳在α-Fe中的过饱和固溶体。
马氏体分类:板条马氏体、片状马氏体、针状马氏体、隐晶马氏体。
GCr15钢淬火后得到的马氏体为隐晶马氏体或者细小结晶马氏体。
马氏体具有高的硬度、强度、耐磨性。
4)贝氏体:是过冷奥氏体在中温区域分解后所得的的产物,它一般是由铁素体和碳化物所组成的非层状组织。
贝氏体分类:上贝氏体、下贝氏体上贝氏体:是一种两相组织,有铁素体和Fe3C所组成的,大致平行的铁素体板条自奥氏体晶界的一侧或两侧向奥氏体晶粒内部长大,Fe3C分布于铁素体板条之间。
表面形变强化后GCr15钢球的显微组织和应力分布

表面形变强化后GCr15钢球的显微组织和应力分布*黄志涛 田文怀【摘 要】摘 要:以GCr15轴承钢球为主体,研究表面形变与钢球内部显微组织及性能的关系.利用光学显微镜、透射电子显微镜和能谱仪对经表面形变强化后的GCr15轴承钢球内部的显微组织和成分进行观察和分析;利用X射线衍射技术测试钢球亚表层的残余应力分布和残余奥氏体含量;利用显微维氏硬度计测试其硬度分布.结果表明:基体显微组织为回火隐晶马氏体、M3C型球状碳化物和少量残余奥氏体的混合体;残余奥氏体体积分数为9.75%,在基体中以薄膜状和块状两种形态存在;钢球表面强化后,产生了残余应力层,其分布深度大约为0.3mm,残余应力峰值及硬度峰值均出现在亚表层中,其深度约为表面以下0.1mm.【期刊名称】华南理工大学学报(自然科学版)【年(卷),期】2011(039)006【总页数】6【关键词】关键词:轴承钢球;表面形变;显微组织;残余应力;透射电子显微镜;碳化物轴承钢球表面形变强化工艺是提高钢球质量的一个重要手段.通过滚压、内挤压和喷丸等机械手段在金属表面产生压缩变形,使表面形成形变硬化层,硬化层的深度可达0.5~1.5 mm.钢球热处理后进行表面形变强化处理可显著提高钢球的表面硬度和终加工后的表面质量,延长其接触疲劳寿命[1-2].表面强化过程使得钢球表面产生了一定的机械强化作用,其耐磨性得到较大改善.然而,表面强化后,对于材料加工产生的残余应力,国内的多数研究[3-6]还停留在对表面应力分布的探索中,对表层深度方向的应力分布研究较少;有关亚表层损伤的研究[7-8],多数也只是针对亚表层损伤形貌特征而展开,没有从力学性能角度系统地进行分析.梅亚莉等[9]曾对不同直径的GCr15钢球表层进行过应力分析,得出残余应力峰值存在于亚表层中的结论,但未给出具体的应力值.文中通过对表面强化加工后GCr15钢球内部的微观组织进行观察,对表面形变强化后钢球的表层结构及内部应力进行分析,以揭示材料的内部组织特征,为指导生产及工艺改进提供参考依据.1 材料及方法1.1 材料实验材料为国内某厂提供的直径为11.32 mm的GCr15轴承钢球.其主要生产工艺为热处理-表面形变强化处理-硬磨-精磨-精研.轴承钢球的化学成分含量(质量分数)见表1.由表1中可以看出,其成分符合标准要求.1.2 显微组织分析方法将轴承钢球沿大圆面切开,制成金相样品.经研磨抛光后,用4%的硝酸酒精溶液进行侵蚀,利用OLYMPUS BX51M金相显微镜对轴承钢球的显微组织进行观察;从试样上切割厚度为0.5 mm的薄片,机械研磨至0.1mm,并将其冲成直径为3mm的圆片,用电解双喷法制备电镜薄膜试样.电解液采用10%的高氯酸酒精溶液,电流为4.5A,用液氮制冷,以满足电解抛光过程所需的温度要求.利用JEM-2100型透射电子显微镜(TEM)对材料的微观组织形态进行观察、分析.利用DMax-RB RKW旋转阳极X射线衍射仪(XRD)测定钢球残余奥氏体的含量(体积分数).测试条件为:Cu靶,波长0.15406nm,工作电流100mA,工作电压40 kV,步宽0.02°,步进时间1 s.根据《GB/T 15749—1995定量金相手工测定法》,利用其中的网格数点法估算碳化物的含量.1.3 表面层残余应力及显微硬度的测定利用MSF-2M型X射线应力测定仪对钢球进行表层应力测定,测定部位分别为距表面0.05、0.10、0.20、0.30、0.40、0.50 mm处.测量中需对钢球进行电解剥层,以对上述不同深度的残余应力进行准确测定.所用电解液为10%的NaCl溶液,电压为10 V.残余应力测试条件为:Cr靶,光阑发射角1°,管电流10mA,管电压30 kV,辐射面积9 mm2,无滤波片.利用DHV-100数显显微维氏硬度计,由轴承钢球外表面沿对应的径向向内部进行硬度测定,确定钢球沿直径方向的硬度分布状态.2 结果与分析2.1 轴承钢球的内部组织表征2.1.1 轴承钢球的基体显微组织分析图1为轴承钢球基体的金相显微组织及其TEM照片.从图1(a)中可以看出,基体组织为回火隐晶马氏体、粒状碳化物及少量残余奥氏体的混合体.图1(b)中显示的白色部分为残余奥氏体,其沿隐晶马氏体边界分布,形态有薄膜状和块状两种.利用透射电镜对图1(a)中所示的粒状碳化物进行了组织观察和晶体结构分析.图2(a)为粒状碳化物的明场像,可以看出碳化物呈球形,直径为500nm左右.图2(b)为球状碳化物的电子衍射谱图,经分析可知,晶体结构属于以面心立方为基的结构类型.图3(a)、3(b)分别为球状碳化物和基体的微区能谱(EDS)图,两相的具体化学成分含量(质量分数)见表2.由表2中可以看出,球状碳化物的碳含量相对较高,且含有Fe、Cr等元素.由于Fe、C原子比接近3.5∶1,因此可以认定球状碳化物与碳素钢中Fe3C的结构类似,属M3C型碳化物.2.1.2 轴承钢球亚表层的显微组织图4为轴承钢球亚表层及基体的显微组织观察结果.从图中可知,其组织可分3部分:首先在距离轴承钢球表面约20~30 μm以内存在一细密组织层;其次是距离轴承钢球表面300 μm以内的区域,为残余应力区域,这在下文2.2.1和2.2.2节残余应力和硬度分布的测定结果中也得到了证实;最后为离轴承钢球表面300μm以外的部分,即未受加工过程影响的基体区域.2.1.3 残余奥氏体含量残余奥氏体的体积分数φA按下式计算:式中,φC为碳化物体积分数,KA、KM分别代表奥氏体相和马氏体相的反射本领,IA、IM分别为奥氏体和马氏体的积分强度.图5为2θ/θ偶合连续扫描所得的XRD谱及衍射面标定结果.由于《GB 8362—87钢中残余奥氏体定量测定X射线衍射仪法》只适用于中、低碳钢和中、低碳低合金钢中残余奥氏体含量的测定,而GCr15钢属高碳合金钢系,因此,参考X射线定量相分析方法,使用直接比较法测定钢中残余奥氏体的含量[10],来进行部分参数的计算.经计算可得: KA(200)=117.30、KA(311)=104.19、KM(200)=35.99和KM(211)=75.41.为得到精确的衍射线积分强度,选A(200)、A(311)、M(200)和M(211)衍射峰进行2θ/θ偶合步进扫描,形成4对马氏体-奥氏体线对,从而得到4个残余奥氏体的体积分数,然后算出平均值,即得样品的残余奥氏体含量.图6为所选衍射峰的XRD谱图.从图中可以看出,曲线以下的面积即为积分强度,扣除本底影响后可得到计算所需的积分强度,即净积分强度I,如图中所示曲线封闭区的面积.测定结果已在该图中标出.根据GB/T 15749—1995,利用其中的网格数点法计算碳化物的含量,计算结果为:φC=23.5%.将φC及所得的K与I值分别代入式(1)中,得出4组φA值,取其平均值,计算结果为φA=9.75%.2.2 轴承钢球应力分布2.2.1 残余应力分布利用X射线衍射法测量残余应力沿层深的分布时,经腐蚀剥层后所测的表面残余应力并不等于原始状态时此层处的残余应力,为此,需对对测量数据进行修正.修正依据[11]为式(2)-(4):式中:σ(i)为修正后残余应力值;σi为试验所测残余应力值;σo(ij,j)与 σo(j+1,j)为修正参数;σo(i,i-1)为第i-1层剥掉后对第i层残余应力影响的修正系数,其它同类型项依次类推;H为试样厚度;Δh为剥层厚度.图7为GCr15轴承钢球表层未修正及修正后的残余应力分布曲线对比图.由图中可知,轴承钢球表层应力状态为压应力.残余压应力由表面向内部先增大再减小,最大值(-414MPa)出现在距表层0.1mm处;在表层0.3mm以下部分,应力分布趋于稳定.由此可见,经表面形变强化后,钢球表层产生了残余压应力,且应力最大值没有出现在表面,而是出现在亚表层中.2.2.2 硬度分布图8为GCr15轴承钢球从外表面向内、沿直径方向的硬度分布测定结果.由图8中可以看出,GCr15轴承钢球的基体平均硬度为HV883.6,硬度最大值为HV931.5,出现在距钢球表面0.1 mm附近.该最大值远大于基体平均硬度HV883.6.在距离表面0.3mm以内,硬度值逐渐接近基体的平均硬度.因此可以认为,强化区深度在0.3~0.5 mm之间.很明显,硬度分布测定结果与应力测试结果较符合.这进一步说明材料经形变强化及研磨后,受影响较大的部位不是表面,而是在表面以下某一深度的亚表层.通常,残余应力的大小应与残余变形的大小成正比,表面残余变形较大残余应力也应较大.结合2.2.1节中残余应力分布的测定结果,可用弹性理论[12]及文献[13]中结果来解释钢球经表面形变强化后残余压应力的产生及分布规律.由于轴承钢球基体具有较高的硬度和强度,在通常的外力作用下很难发生塑性变形,因此会在一定区域内产生微小的弹塑性变形,使得该区域产生残余应力,即产生残余应力层.强化过程中,钢球表层将发生残余奥氏体转变为马氏体的相变,体积膨胀受到内层约束,故而受压.由于作用于钢球表面上的垂直压力足够大时,塑性变形始于内部,最大静态剪切应力出现在亚表层某一深度处,同时由于表面属于二维平面结构,释放了部分已产生的残余应力,使得残余应力最大部位并不在表面而是存在于亚表层中.生产中,工件表面层的残余压应力可抵消部分工作时的拉应力,使其受力水平降低,从而有效提高工件的寿命.3 结论(1)GCr15轴承钢球的基体组织为回火隐晶马氏体、球状碳化物以及少量残余奥氏体的混合体.(2)球状碳化物与碳素钢Fe3C结构类似,属M3C型碳化物,残余奥氏体含量为9.75%,在隐晶马氏体晶界处以薄膜状和块状两种形态存在.(3)钢球表面形变强化后,在GCr15轴承钢球的表层产生了残余应力层,其分布深度大约为0.3mm,残余应力峰值并不在表面而是存在于亚表层中,即在距离表面下0.1mm附近.残余应力的分析对生产实践中应力的去除及利用具有重要的参考价值.参考文献:[1] 王保振,吴国荣.钢球表面硬化处理时对其寿命的影响[J].轴承,1985(6):30-32.Wang Bao-zhen,Wu Guo-rong.Effect of surface hardening on the life of steelballs[J].Bearing,1985(6):30-32.[2] 许正功,陈宗帖,黄龙发.表面形变强化技术的研究现状[J].装备制造技术,2007(4):69-71.Xu Zheng-gong,Chen Zong-tie,Huang Long-fa.Research on the outline of strengthening technology of surface deformation[J].Equipment Manufactring Technology,2007 (4):69-71.[3] 杨建东,田春林,金海峰,等.固着磨料研磨对工件表面残余应力的影响[J].中国表面工程,2002(4):37-38.Yand Jian-dong,Tian Chun-lin,Jin Hai-feng,et al.Effect of solid abrasive lapping on residual surface stress[J].China Surface Engineering,2002(4):37-38.[4] 薛进学,赵波,焦锋.超声高速研磨陶瓷表面残余应力特性研究[J].金刚石与磨料磨具工程,2009(4):56-61.Xue Jin-xue,Zhao Bo,Jiao Feng.Experimental research on the surface residual stress in ultrasonic lapped surface of engineeringceramics[J].Diamond&Abrasives Engineering,2009(4):56-61.[5] 陈建,原一高,吴贺龙,等.研磨工艺对工件表面粗糙度及残余应力的影响[J].工具技术,2009,43(5):16-18.Chen Jian,Yuan Yi-gao,Wu He-long,et al.Effect of lapping process on surface roughness and residual stress of part[J].Tool Engineering,2009,43(5):16-18.[6] Ren C Z,Wang T Y,Jin X M,et al.Experimental research on the residual stress in the surface of silicon nitride ceramic balls[J].Materials ProcessingTechnology,2002,129:446-450.[7] Yan Ji-wang,Asami Tooru,Harada Hirofumi,et al.Fundamental investigation of subsurface damage in single crystalline silicon caused by diamondmachining[J].Precision Engineering,2009,33:378-386.[8] Lucca D A,Shao L,Wetteiand C J,et al.Subsurface damage in(100)ZnSe introduced by mechanical polishing[J].Nuclear Instruments and Methods in Physics Research B,2006,249:907-910.[9] 梅亚莉,景国荣.GCr15钢球的表面形变强化性能[J].轴承,1997(5):34-46.Mei Ya-li,Jing Guo-rong.Surface deformation peening property of GCr15 steelballs[J].Bearing,1997(5): 34-36.[10] 李华瑞.材料X射线衍射分析实用方法[M].北京:冶金工业出版社,1994:39-48.[11] 胡华南,陈澄洲,周泽华.剥层测量残余应力的修正[J].华南理工大学学报:自然科学版,1992,20(4): 47-56.Hu Hua-nan,Chen Cheng-zhou,Zhou Ze-hua.On modification to measured data of residual stresses in machined surface layer by removal oflayer[J].Journal of South China University of Technology:NaturalScience,1992,20(4):47-56.[12] 米谷茂.残余应力的发生与对策[M].朱荆璞,邵会孟,译.北京:机械工业出版社,1983:152.[13] 朱光辉,高斌,仵永刚,等.圆锥滚子形变强化表层的残余应力分布[J].理化检验-物理分册,2007,43 (8):382-385.Zhu Guang-hui,Gao Bin,Wu Yong-gang,et al.Distribution of residual stress in strain strengthened surface layer of tapered roller[J].Physical Testing and Chemical Analysis (Part A:Physical Testing),2007,43(8):382-385.doi:10.3969/j.issn.1000-565X.2011.06.015*基金项目:国家自然科学基金资助项目(50671012)。
GCr15SiMn钢球开裂原因分析

GCr15SiMn钢球开裂原因分析作者:王姗姗梁华仇亚军朱勇来源:《上海有色金属》2013年第02期摘要:轴承钢球在热处理时发生开裂,采用宏观观察、微观检验及分析等方法对GCr15SiMn钢球心部缺陷的产生原因进行了较为全面的分析.结果表明,钢球心部的缺陷为缩孔残余,是钢材冶炼过程中形成的缺陷,属于冶金缺陷.同时,结合实际生产,提出了相关的防范措施,以避免此类裂纹的产生,从而保证了产品的质量.关键词:钢球;开裂;缩孔残余;冶金缺陷;措施中图分类号:TG142.41文献标志码: AThe Reason Analysis of GCr15SiMn Steel Ball CrackingWANG Shan-shan1, LIANG Hua1, QIU Ya-jun1, ZHU Yong2(1.Luoyang Bearing Science and Technology Co., Ltd., Luoyang 471039, China;2.Hi-P Precision Mould Co., Ltd., Shanghai 201206, China)Abstract:The steel balls cracked during heat treatment.The cracking reason was analysed by macro-observation and metallographic observation and scanning electron microscope and energy spectrum analysis.The result shows that steel ball cracking is caused by remaining shrinkage clarity.The defect is formed in the smelting process,and it is metallurgical defects.At the same time,combined with the actual production,the corresponding measures are put forward,thus the quality of products is guaranteed.Key words:steel ball; cracking; remaining shrinkage clarity; metallurgical defects; measures0 前言钢球是轴承工业的重要组成部分.在轴承工业中,钢球的加工方式主要有冷镦、热墩、热轧和热锻等.加工过程中钢球开裂的原因主要有原材料缺陷(显微孔隙、非金属夹杂物、发纹等)、冷镦裂纹、软磨疲劳、淬火裂纹及硬磨烧伤等.根据钢球缺陷的不同形貌,在实际过程中采取相应的分析方法,对轴承钢球开裂的原因进行分析和探讨.某公司送检半成品钢球一粒,规格为60 mm,材料为GCr15SiMn高碳铬轴承钢.钢球加工工艺为:中频感应加热,始锻温度为1 050~1 120 ℃,由45 mm原材料锻打至60 mm球坯.该批钢材共有30多t,在热处理时发现有十几粒开裂.通过宏观断口分析、热酸洗、金相及能谱分析等方法对钢球开裂原因进行了分析.1 检验与分析1.1 宏观形貌及断口分析送检钢球开裂为两半,观察钢球的断口发现:球心部的锻造流线贯穿钢球,为开裂的起源区;裂纹从钢球的心部沿贯穿钢球的锻造流线向两侧扩展,最后导致钢球完全开裂为两半.钢球的断裂方式为脆性断裂,从断口的扩展区和断裂区来看,断口为细瓷状,形貌见图1.1.2 金相检查将其中一半钢球从中心垂直于两极进行解剖,样品经制备后放置在MG显微镜下观察其心部的金相组织.结果发现:钢球心部局部有裂纹,多处存在灰色的块状异物,如图2所示.心部边缘及裂纹两侧有严重的脱碳现象,但多处铁素体的存在与裂纹的存在无关,如图3所示.钢球的淬回火组织按照JB/T 1255-2001标准评定为3级,网状碳化物为2级,为合格组织,如图4所示.清洗烘干后放置在JSM5610LV型扫描电子显微镜下,对钢球心部灰色异物形貌进行观察.结果发现:灰色异物大多呈条块状分布,色泽分浅灰和深灰两种,其分布状态及形貌见图5.采用falcon能谱仪对钢球心部的灰色异物进行定性成分分析.结果表明:钢球心部灰色块状异物的化学成分主要为氧、锰、硅、铬、铁及少量的硅、铝、钛等;相比较而言,A处锰、铬的含量高一些,而B处硅的含量高一些,其能谱曲线见图6(见下页).由此可以确定,钢球心部的灰色块状异物主要为锰和硅的氧化物,为材料夹杂物.1.4 热酸洗检查标准进行热酸洗,确定钢球心部的锻造流线沿轧制方向分布并贯穿两极,其他未见异常.断口的热酸洗形貌见图7.2 结果与分析缩孔是钢水凝固过程中,由于体积收缩,在钢锭或连铸坯心部未能得到充分填充而形成的管状或分散孔洞[1].一般集中在钢锭的上部和冒口部分,正常情况下可以清除掉.但如果切除冒口量过少或由于其他原因,则会使缩孔深及钢锭内部,而最终存在于被利用的成品材料之中,称为缩孔残余.在经热酸洗后的低倍试片中心区域呈不规则的折皱裂缝或空洞,其上或附近常伴有严重的夹渣、成分偏析和疏松.热轧钢球和冷冲压成型钢球的工艺过程不同,造成的材料流线形貌也不一样,冷冲压成型钢球内部如有缩孔一般贯穿两极,而热轧成型钢球由于材料塑性流动较大,尤其是对于轧制变形量较大的钢球,若钢材内部存在缩孔,经过热轧后两极可以完全封闭[2].根据断口、金相、热酸洗、扫描电镜和能谱分析,结果认为:钢球开裂始于心部,并沿材料轧制方向由内向外开裂;钢球的淬回火组织符合相关标准要求;钢球心部存在大量的夹杂物和严重的脱碳现象为钢材冶炼造成的冶金缺陷,属于缩孔残余.3 结论钢球心部存在缩孔残余是引起钢球开裂的主要原因.缩孔残余严重地破坏了钢材的连续性,是钢材不允许存在的缺陷,轧制(锻造)时必然会在钢坯上产生裂纹.为了避免缩孔残余遗留在成品钢材中,建议正确设计钢锭模和保温帽尺寸,并采用性能优良的保护渣、保温剂(发热剂)和绝热板,把缩孔控制在钢锭头部,以保证在开坯时切掉.控制浇铸速度不要太快,温度不要过高也可以减小缩孔的产生.参考文献:[1] 钟顺思,王昌生.轴承钢[M].北京:冶金工业出版社,2000.[2] 雷建中,梁华.热轧轴承钢球心部孔洞分析实例[J].轴承,2010(8):41-42.。
- 1、下载文档前请自行甄别文档内容的完整性,平台不提供额外的编辑、内容补充、找答案等附加服务。
- 2、"仅部分预览"的文档,不可在线预览部分如存在完整性等问题,可反馈申请退款(可完整预览的文档不适用该条件!)。
- 3、如文档侵犯您的权益,请联系客服反馈,我们会尽快为您处理(人工客服工作时间:9:00-18:30)。
GCr15钢接触表面塑性形变强化与裂纹萌生机制朱春莉; 赵凤平; 苏云帅【期刊名称】《《宁波大学学报(理工版)》》【年(卷),期】2019(032)006【总页数】6页(P61-66)【关键词】GCr15轴承钢; 滚动接触疲劳; 塑性变形; 晶粒细化; 裂纹【作者】朱春莉; 赵凤平; 苏云帅【作者单位】宁波大学机械工程与力学学院浙江宁波 315211【正文语种】中文【中图分类】TG113动轴承常在重载、高速、高温等特殊工况下服役, 这种恶劣工况很容易使轴承产生疲劳失效使其寿命缩减, 而塑性变形是疲劳失效的形式之一, 因此国内外学者对滚动轴承中出现的塑性变形展开了研究.由摩擦学理论可知, 滚动和滑动时均会产生摩擦力. 摩擦使两接触面发生磨损, 这种磨损在滚动轴承和列车轮轨的接触面均有出现[1-3]. 接触表面磨损属于宏观上的疲劳失效现象, 同时磨损伴随着接触亚表面产生塑性变形层. 滚动接触失效后的轴承材料内部还出现白色蚀刻裂纹(White Etching Cracks, WECs)[4-5]以及蝴蝶状形变区[6]. 在接触表面发现了晶粒细化的白层组织(White Layer, WL)[7-8]. 表面白层是一种塑性变形层, 由于碳化物溶解晶粒细化而不易被腐蚀[9]. Zhou等[10]研究了轮轨材料中载荷和滑差率对接触表面产生塑性变形层的影响, 并利用Abaqus软件模拟不同的载荷和循环周次下材料内部的应力分布. 程晓娟等[11]认为塑性变形是材料在循环载荷下循环累积的结果, 称其为棘轮效应, 发现单轴非对称应力循环下304不锈钢发生相变. 另外, Tyfour等[12]提出用剪切应变的方法来描述塑性变形程度. Lansler[13]研究了塑性变形对亚表面滚动接触疲劳裂纹扩展的影响. 郑逊昭等[14]认为亚表面最大应力夹杂处形成微孔洞, 微孔洞扩散连接形成剥落坑. Seo 等[15]对不同材料的滚动接触亚表面塑性变形区的演化做了相关研究, 得出亚表面塑性变形区的硬度相对基体材料有大幅度增加, 但没有给出材料发生塑性变形内裂纹扩展的内在机理. 上述研究是关于塑性变形对疲劳失效的影响以及表面材料的累积变形使表面硬度增加, 由于缺乏对塑性变形微观机理的认识, 导致塑性累积到何种程度才能使表面材料发生形变强化至最佳值, 达到抵抗磨损的效果还没有证据. 因此, 有必要开展对塑性变形层微观结构的分析, 以研究其本质.本文对GCr15轴承钢在不同条件下开展滚动接触疲劳试验, 分析塑性变形层内部微观组织和硬度变化, 探索塑性变形与疲劳失效之间的联系; 并讨论了塑性变形区边界的裂纹萌生机理, 以期为进一步研究接触表面塑性强化提供理论依据.试验材料为GCr15轴承钢, 其热处理工艺是在860℃下保温2h, 待其全部奥氏体化后油淬至室温, 然后在160℃保温1h得到回火马氏体组织, 其化学成分见表1. 试验前测得基体材料的硬度(630±10)HV. 试验在MJP-30型滚动接触疲劳试验机上进行, 2个轴承试样尺寸根据GB10622-89设计, 均用同种材料加工, 接触宽度5mm, 试样尺寸如图1所示.2组试验均在室温、油润滑环境下进行, 试验条件见表2. 2组轴承试样经过不同的循环周次后发生疲劳失效, 试验后沿圆周和轴向方向将试样切割, 将切割好的样品分别在240#、320#、500#、800#、1000#、3000#进行研磨, 然后用金相抛光机进行机械抛光, 抛光后用4%硝酸酒精溶液腐蚀. 使用日立SU5000型扫描电子显微镜(SEM)观察疲劳后的轴承试样亚表面组织形貌变化, 透射试样使用集成于Helios G4 CX型扫描电镜上的聚焦离子束(FIB)制备, FEI Talos-F200X型透射电子显微镜(TEM)用于对塑性变形层内部的微观结构进行分析观察, HysitronTI Premier纳米压痕仪表征变形区域不同深度的载荷位移曲线.图2为试件在不同区域的塑性变形区的SEM形貌. 从图2可知, 越是靠近接触面, 塑性变形越严重, 在稍微远离接触表面的区域则变形轻微. 图2(a)近表面有明显的塑性流动, 并在磨损表面点蚀坑处萌生裂纹, 裂纹沿着塑性变形线扩展, 当裂纹扩展到一定深度后改为平行于接触表面扩展. 通过局部放大(图2(b))可以看到仅在裂纹一侧发生塑性变形, 裂纹沿着塑性变形区边界向材料内部扩展, 并且扩展方向与接触表面呈锐角. 图2(c)中变形层的厚度约5μm, 在最近表层材料中变形最严重, 晶粒沿着运动方向被拉长, 变形层内碳化物的数量明显减少. 借助纳米压痕仪从接触表面开始每间隔1μm(图2(c))做一次压痕测试, 得出塑性区和基体的载荷位移曲线, 从中可看出载荷位移曲线从表面向内部呈梯度变化, 塑性区的硬度明显高于基体(图3).图4(a)和(b)分别是沿着周向及轴向剖面方向观察的塑性变形层形貌. 图4(a)有明显的塑性变形线, 并与接触面呈锐角; 图4(b)从横剖面观察塑性变形层的组织已经分层, 并且层与层之间存在孔洞, 这些孔洞使塑性变形区变成了一层一层的片状组织. 图5为不同的接触应力和循环周次下的疲劳试样表面塑性变形层形貌, 其中图5(a)塑性层的厚度约为23μm, 图5(b)塑性层厚度约为10μm, 图5(a)的样品循环周次比图5(b)样品的循环周次少了2个数量级. 图5中疲劳裂纹均沿着塑性变形线扩展, 其中图5(b)的裂纹在交变应力作用下裂纹扩展方向发生变化, 改向材料内部扩展, 这种类型的裂纹会对轴承类零部件造成致命的疲劳损伤.聚焦离子束(FIB)制取TEM样品位置(图2(b)). 将制取的样品放置于透射电子显微镜中观察, 从图6(a)和(b)中可看出, 塑性区晶粒尺寸相对于基材的晶粒发生明显细化及变形, 基材的晶粒尺寸在0.5~1μm之间, 晶粒清晰完整, 且没有变形和缺陷. 图6(c)和(d)为塑性变形区的组织, 晶粒间没有明显的边界, 晶粒发生细化, 尺寸达到纳米量级, 且几乎是小于100nm的纳米晶. 经过仔细观察发现, 塑性变形区除了晶粒细化变形外还有大量的位错簇以及部分碳化物发生溶解(图6(d)).从图6(a)和(b)中基材和塑性变形区的选区衍射图可以发现, 基材的衍射图(SAD-1)是排列有序的二维点阵衍射斑点, 说明晶粒没有发生变形, 晶粒比较粗大, 且在此区域内参与衍射的晶粒比较少. 塑性层组织的衍射图(SAD-2)衍射斑点被拉长变细, 有成环趋势, 这些拉长的衍射斑是由变形的晶粒参与衍射形成, 细小的衍射斑点由小晶粒参与衍射形成. 在这个区域内晶体取向发生了变化, 且有大量的细晶. 图6(b)中的多晶环是典型的纳米晶衍射特征. 另外, 小倍数下的衍射斑点(SAD-2)数量比大倍数下衍射斑点(SAD-1)更密集, 说明在小区域内含有更多的纳米晶. 从选区衍射结果看, 所有的纳米晶粒都是bcc结构, 无相变发生.塑性变形是材料对循环载荷的动态响应, 当轴承试样上的径向载荷和周向摩擦力大于其屈服强度时便产生塑性变形, 并以塑性流变的形式从接触表面以一定角度向材料内部延伸. 轴承钢GCr15是一种多晶体材料, 晶粒的取向和大小均不同, 所以各个晶粒的变形抗力也不同, 使得晶体内应力与应变的分布不均匀, 晶界的存在阻碍滑移, 也影响塑性变形过程. 当晶体受到外力作用时并不是所有的晶粒同时开始滑移, 而是在取向最有利的晶粒滑移系统上开始发出位错环. 当晶界上正常的原子结构被破坏后, 位错滑动到晶界附近. 由于另一侧的晶粒取向不同, 对接近晶界的位错产生斥力, 原先的位错环在晶界处受阻, 外力使后续的位错也移动到晶界附近产生了位错塞积, 产生应力集中. 应力集中到一定值后就启动相邻晶界的位错源, 位错从一个晶粒移动到另一个晶粒内. 由于晶界两侧取向不同和晶界的畸变使位错滑移受阻, 必须增加外力才能实现这一过程. 每个晶粒被其他晶粒所包围, 相邻的晶粒必须协调变形才能在不破坏晶界连续性的情况下使晶粒产生滑移变形.在滚动接触过程中, 内部夹杂处出现蝴蝶状的变形组织[6]就是一种塑性变形, 该变形区的晶粒变细拉长, 和基体组织之间有明显的界限, 部分边界与基体之间有裂纹间隔, 而且这种变形方向与滚动方向呈现30°~50°角, 可以推断是径向载荷和摩擦力的作用导致变形的产生. Seo等[15]证明了两接触体的滑差率对亚表面塑性变形的影响. 滑差率越高变形越严重. 纯滚动时的滚动体之间没有位移差, 只有径向压缩应力作用使接触表面组织细化. 在塑性变形层内有纳米晶生成, 并伴随着部分碳化物溶解, 没有相变发生, 越接近接触表面晶粒尺寸越小.当材料受到剪切作用时产生的相对变形量是剪切应变, 以塑性变形线的切线与接触表面法线之间夹角δ的正切值表示[16-17]. 剪切应变γ的计算公式为:通过这一计算方法可反映近表层材料塑性变形的严重程度. 从图2(a)和图4(a)可以看到, 塑性变形线之间几乎平行, 总体与接触面呈固定角度. 图2(c)的塑性变形线平行于接触面. 经统计分析, 接触面与塑性变形线的夹角越大越容易萌生裂纹, 并且裂纹沿着塑性变形线的方向扩展. 此外, 塑性变形线与接触面夹角并非固定不变, 越靠近表面, 塑性变形线与接触面的夹角越小; 随着与表面距离增加, 夹角的角度也逐渐增大. 根据式(1), δ值越大代表塑性变形线与滚动接触表面夹角越小, 剪切应变越严重; δ值越小代表塑性变形线与滚动接触表面夹角越大, 剪切应变量越小. 在摩擦力的作用下, 近表面组织发生累积塑性变形, 越靠近接触表面塑性应变越严重, 通过纳米压痕试验得出, 变形越严重硬度值越高. 由于变形区内位错密度不断增加, 使得位错运动越来越困难, 所以接触表面发生形变后会产生硬化从而强度提高, 但过度硬化会引起金属脆化而产生缺陷, 因此必然存在一个塑性变形量的临界值, 使材料表面产生形变强化, 而又不会使材料发生脆化, 从而增加其抗疲劳性能, 这为进一步研究GCr15钢表面形变强化提供了思路.裂纹是接触疲劳中常见的失效模式, 通常在表面加工缺陷、内部夹杂等应力集中处萌生. 在滚动接触试样剖面图中观察到有裂纹萌生的塑性变形区域, 裂纹沿着塑性区和非塑性区之间的边界扩展, 且塑性层的厚度几乎和裂纹扩展的深度一致. 由于载荷和裂纹面间摩擦力作用, 裂纹面间相对运动导致了较高的剪切应力[18]. 在裂纹扩展过程中, 裂纹面间的相互摩擦导致裂纹面周围材料发生剪切变形[19].图7是塑性变形层及裂纹形成过程示意图. 从图7可知, 当接触表面及近表面晶粒受到切向力作用后发生滑移, 由于相邻的晶粒取向不同, 位错运动在晶界处发生位错塞积而产生应力集中, 当应力集中超过临界值时, 裂纹或孔洞就在晶界处产生(图7(c)). 接触表面晶粒受到法向力作用被挤压变形, 同时微裂纹受周向摩擦力作用而逐渐形成(图7(d)), 最后经过长周期的循环作用形成塑性变形层和裂纹(图7(e)). 根据赫兹接触理论, 材料内部的最大应力在亚表面, 因此在亚表面某处晶界发生位错塞积产生应力集中, 当其超过材料的临界应力值时就在晶界处产生裂纹及孔洞, 孔洞在扩大过程中相连接形成更大的孔洞, 最终形成亚表面的微裂纹. 接触亚表面的塑性变形是在周向摩擦力作用下产生的, 塑性变形层是从裂纹萌生部位开始沿摩擦方向拉长、扭曲, 最终成为纤维状的片层组织[20].(1)在塑性变形层内有纳米晶生成, 并有部分碳化物溶解, 没有相变发生, 越接近接触表面晶粒越细. (2)在摩擦力作用下, 近表面组织发生累积塑性变形, 越靠近接触表面塑性应变越严重, 且变形越严重硬度值越高, 因此必然存在一个最佳的塑性变形量, 使材料表面产生形变强化, 从而增加其抗疲劳性能. (3)塑性变形区是层状的纤维状组织, 变形区内的晶粒在晶界处发生位错运动而产生应力集中, 当应力集中超过临界值时在晶界处产生孔洞, 孔洞在循环应力的作用下形成裂纹.【相关文献】[1] Robert E, Robert B, Rainer E. Investigations of bearing failures associated with white etching areas (WEAs) in wind turbine gearboxes[J]. Tribology Transactions, 2013,56(6):1069-1076.[2] 金学松, 张继业, 温泽峰, 等. 轮轨滚动接触疲劳现象分析[J]. 机械强度, 2002, 24(2):250-257.[3] 王文健, 郭俊, 刘启跃. 轮轨磨损与滚动疲劳裂纹损伤关系及预防研究[J]. 中国表面工程, 2010,23(3):106- 109.[4] Evans M H, Richardson A D, Wang L, et al. Serial sectioning investigation of butterfly and white etching crack (WEC) formation in wind turbine gearbox bearings[J]. Wear, 2013, 302(S1/2):1573-1582.[5] Gould B, Greco A. The influence of sliding and contact severity on the generation of white etching cracks[J]. Tribology Letters, 2015, 60(2):1-13.[6] Grabulov A, Petrov R, Zandbergen H W. EBSD investigation of the crack initiation and TEM/FIB analyses of the microstructural changes around the cracks formed under Rolling Contact Fatigue (RCF)[J]. International Journal of Fatigue, 2010, 32(3):576-583. [7] Hosseini S B, Klement U, Yao Y, et al. Formation mechanisms of white layers induced by hard turning of AISI 52100 steel[J]. Acta Materialia, 2015, 89:258-267.[8] Zhou Y, Peng J F, Luo Z P, et al. Phase and microstructural evolution in white etching layer of a pearlitic steel during rolling-sliding friction[J]. Wear, 2016, 362/363:8-17.[9] 杨姗洁, 任瑞铭, 陈春焕, 等. 动车组车轮轮缘塑性变形白层组织分析[J]. 摩擦学学报, 2016, 36(5):622-628.[10] Zhou Y, Peng J F, Wang W J, et al. Slippage effect on rolling contact wear and damage behavior of pearlitic steels[J]. Wear, 2016, 362/363:78-86.[11] 程晓娟, 王弘, 康国政, 等. 304不锈钢棘轮变形过程中应变诱发马氏体相变行为研究[J]. 金属学报, 2009, 45(7):830-834.[12] Tyfour W R, Beynon J H, Kapoor A. Deterioration of rolling contact fatigue life of pearlitic rail steel due to dry-wet rolling-sliding line contact[J]. Wear, 1996, 197(1): 255-265.[13] Lansler E. Influence of plastic deformations on growth of subsurface rolling contact fatigue cracks in railway wheels[J]. Journal of Rail & Rapid Transit, 2006, 220(4): 461-473.[14] 郑逊昭, 夏玉洲. GCr15轴承钢接触疲劳亚表面孔洞的形成[J]. 材料科学与工艺, 1996,4(3):29-33.[15] Seo J W, Jun H K, Kwon S J, et al. Rolling contact fatigue and wear of two different rail steels under rolling–sliding contact[J]. International Journal of Fatigue, 2016, 83:184-194.[16] Ringsberg J W, Loo-Morrey M, Josefson B L, et al. Prediction of fatigue crack initiation for rolling contact fatigue[J]. International Journal of Fatigue, 2000, 22(3): 205-215.[17] Donzella G, Faccoli M, Mazzu A, et al. Progressive damage assessment in the near-surface layer of railway wheel-rail couple under cyclic contact[J]. Wear, 2011,271(1/2):408-416.[18] 何成刚. 车轮材料摩擦疲劳损伤机理及微观组织演变行为研究[D]. 成都: 西南交通大学, 2018.[19] Ekberg A, Åkesson B, Kabo E. Wheel/rail rolling contact fatigue: Probe, predict,prevent[J]. Wear, 2014, 314(1/2): 2-12.[20] 蒋文娟. 钢轨材料对轮轨磨损及微观结构影响的研究[D]. 成都: 西南交通大学, 2012.。