注塑问题及解决方法最终
注塑产品在生产中存在的问题及解决方法

管件在生产中存在的问题及解决方法(1)注塑产品收缩变形,达不到标准,如:注塑90°弯头不够90°或大于90°。
可能出现问题的原因:A、模具设计没有考虑管件收缩的因素,模具设计为90°,但半成品收缩后不够90°或大于90°。
B、冷却时间短,开模造成管件变形。
C、模具温度高。
D、保压时间短或保压压力小,管件收缩大。
补救方法:设计模具和调整工艺时应充分考虑管件收缩问题,注塑半成品冷却收缩后为90°;调整注塑工艺,延长冷却时间,使模具温度保持在30--50°范围内,增加保压时间或保压压力。
(2)注塑产品气孔。
(目前无法解决)。
半产品在车削过程中经常出现空穴和气孔,使产品合格率降低。
这与制品厚度有关,而且常因塑料冷却收缩离开注塑件中心而引起。
可能出现问题的原因:A、模具未充分填充或填充不实。
B、止流阀的不正常运行,有回流现象。
C、原料未彻底干燥,水分含量高。
D、预塑或注射速度过快。
E、模具浇口位置和形式设计不合理,模具形状设计不合理。
目前的补救方法:A、增加射料量;B、增加注塑压力;C、增加螺杆向前时间;D、降低熔融温度;E、降低或增加注塑速度;F、检查止逆阀是否裂开或无法运作;G、让原料彻底干燥(≤300ppm);H、适当降低螺杆转速和增大背压,或降低注射速度;I、改变浇口位置和形式,必要时改变模具的设计。
(3)注塑产品褶皱流纹,车削断削。
可能出现问题的原因:通常与表面痕有关,而且是塑料从模具表面收缩脱离形成的,也有注射时造成。
A、原料熔融温度不是太高就是太低;B、模腔内塑料不足;C、冷却阶段时接触塑料的面过热;D、流道不合理、浇口截面过小;E、模温是否与原料特性相适应;F、产品结构不合理(过厚或明显厚薄不一);G、模具冷却效果不好。
补救方法:A、调整料筒温度;B、调整螺杆速度以获得正确的螺杆表面速度和剪切温度;C、增加注塑量;D、保证使用正确的垫料;增加螺杆向前时间;增加注塑压力;增加注塑速度;E、检查止流阀是否安装正确,因为非正常运行会引致压力流失,造成注不实。
注塑车间问题点和改善对策

在注塑车间,可能会遇到各种问题,这些问题在生产过程中需要特别关注并寻求相应
的改善对策。
以下是常见的问题点以及相应的改善措施:
1. 产品质量问题:在注塑过程中,可能会出现短射、翘曲、裂纹、瑕疵等质量问题。
要改善这些问题,首先要进行原因分析,如模具设计、注塑工艺参数和原材料等。
针
对性地对问题进行调整(如调整注塑速度、压力、温度等),并进行严格的质量控制。
2. 设备故障:"机器、模具和辅助设备可能都会发生故障。
正确的维护和保养是防止故障的关键,例如定期检查润滑系统、更换磨损零件、定期清洁模具等。
3. 低生产效率:提高生产效率是提升注塑车间竞争力的关键。
改善方法包括:减少模
具更换和调试时间、采用自动化设备减少人工干预、优化生产排程和工艺参数等。
4. 浪费问题:在注塑过程中,可能会产生原材料、能源和人力等方面的浪费。
合理安
排生产计划、提高原材料利用率、节约能源(如优化加热和制冷系统)等措施,可以
降低浪费并提高整体效益。
5. 安全问题:注塑车间的生产安全非常重要,包括操作安全、消防安全、职业健康等
方面。
加强员工培训,提高安全意识和操作技能;确保车间内部的通风、照明和消防
等条件良好;合理布局生产线,以避免安全隐患。
6. 人员问题:员工流动性、技能短缺等问题可能影响注塑车间的生产效率和质量。
通
过制定合理的员工福利、培训和晋升政策,可以提高员工满意度和职业素养,从而提
高生产效果。
综上所述,在面对注塑车间的各种问题时,应想方设法地改进生产流程、提高效率和
质量、确保安全,并充分关注员工的发展及满意度。
注塑过程中常见的问题及解决方案

注塑过程中常见的问题及解决方案一、飞边(披锋)1. 问题描述- 这飞边就像塑料偷偷长出来的小翅膀,在注塑件的边缘或者分型面那里冒出来,看着可闹心了。
就像好好的一块蛋糕,边缘突然多出了一些不规则的奶油坨坨。
2. 解决方案- 首先得检查模具的合模力。
要是合模力不够,那塑料就会像调皮的小孩从门缝里挤出来。
适当增加合模力,把模具紧紧抱住,让塑料乖乖待在该待的地方。
- 模具的磨损也会导致飞边。
就像穿破了的鞋子会漏脚指头一样,磨损的模具缝隙变大了。
这时候就得修模啦,把那些磨损的地方补一补或者磨平。
- 注塑压力也不能太大。
如果压力太大,塑料就像被大力士猛推的水,到处乱流。
降低注塑压力,找到一个合适的值,既能把模具填满,又不会让塑料溢出来。
二、短射(缺料)1. 问题描述- 短射就像给一个杯子倒水,结果没倒满一样。
注塑件看着不完整,有些地方该有塑料的却空着,就像一个没发育好的小怪物。
2. 解决方案- 先看看注塑压力是不是太小。
压力小的话,塑料就像没力气的小蚂蚁,爬不到模具的每个角落。
增加注塑压力,让塑料充满整个模具型腔。
- 塑料的流动性也很关键。
如果塑料太黏,就像浓稠的糨糊,很难流到模具的远端。
这时候可以提高料筒温度,让塑料变得稀一点,流动性更好,就像把糨糊加热变成稀粥一样,能顺利流到各个地方。
- 浇口尺寸也可能有问题。
要是浇口太小,就像一个小得可怜的水龙头,水流不出来多少。
适当扩大浇口尺寸,让塑料能畅快地流进模具。
三、气泡(气穴)1. 问题描述2. 解决方案- 注塑速度可能太快了。
塑料像一阵风呼呼地冲进模具,把空气都裹在里面了。
降低注塑速度,让塑料慢慢流进去,就像散步一样,这样空气就有机会跑出来了。
- 模具的排气也很重要。
如果模具没有排气孔或者排气不良,空气就被困在里面出不来。
在模具上开排气槽或者使用透气钢材料,给空气一条逃跑的路。
- 塑料干燥不彻底也会产生气泡。
如果塑料里有水份,加热的时候就会变成水蒸气,形成气泡。
注塑缺陷原因分析与解决方案
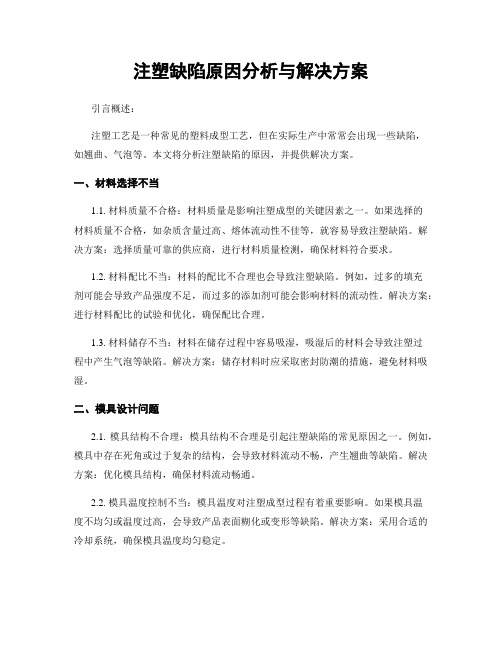
注塑缺陷原因分析与解决方案引言概述:注塑工艺是一种常见的塑料成型工艺,但在实际生产中常常会出现一些缺陷,如翘曲、气泡等。
本文将分析注塑缺陷的原因,并提供解决方案。
一、材料选择不当1.1. 材料质量不合格:材料质量是影响注塑成型的关键因素之一。
如果选择的材料质量不合格,如杂质含量过高、熔体流动性不佳等,就容易导致注塑缺陷。
解决方案:选择质量可靠的供应商,进行材料质量检测,确保材料符合要求。
1.2. 材料配比不当:材料的配比不合理也会导致注塑缺陷。
例如,过多的填充剂可能会导致产品强度不足,而过多的添加剂可能会影响材料的流动性。
解决方案:进行材料配比的试验和优化,确保配比合理。
1.3. 材料储存不当:材料在储存过程中容易吸湿,吸湿后的材料会导致注塑过程中产生气泡等缺陷。
解决方案:储存材料时应采取密封防潮的措施,避免材料吸湿。
二、模具设计问题2.1. 模具结构不合理:模具结构不合理是引起注塑缺陷的常见原因之一。
例如,模具中存在死角或过于复杂的结构,会导致材料流动不畅,产生翘曲等缺陷。
解决方案:优化模具结构,确保材料流动畅通。
2.2. 模具温度控制不当:模具温度对注塑成型过程有着重要影响。
如果模具温度不均匀或温度过高,会导致产品表面糊化或变形等缺陷。
解决方案:采用合适的冷却系统,确保模具温度均匀稳定。
2.3. 模具磨损严重:模具长时间使用后会出现磨损,磨损严重的模具会导致产品尺寸不准确或表面粗糙等缺陷。
解决方案:定期检查和维护模具,及时更换磨损严重的模具部件。
三、注塑工艺参数设置不当3.1. 注射压力过高或过低:注射压力是影响注塑成型的关键参数之一。
如果注射压力过高,会导致产品变形或开裂,而注射压力过低则会导致产品表面光洁度不高。
解决方案:根据产品要求和材料特性,合理设置注射压力。
3.2. 注射速度不合理:注射速度对产品的充填和冷却过程有着重要影响。
如果注射速度过快,会导致产品内部产生气泡或短射,而注射速度过慢则会导致产品表面瑕疵。
注塑工艺常见问题和解决
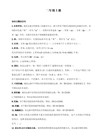
六、呈现问题:合模边挤出塑料。
原因:因料温及注压过高,或锁模力不足。
解决方法:1.降低注压及筒固化温度 2.缩短注时 3.减少注料速度 4.改用高锁模力机 5.改造合模表面紧配合及清理合模表面 6.转用低粘度料。
七、呈现问题:塑件表面呈凹痕。
原因:因塑件表面误时冷却,因其表面凹痕。
解决方法:1.增加注料速率 2.提高模槽内压(二次压力)3.降低筒料固化温度 4.提高注塑流量 5.增加注速 6.延长注时 7.使模具温度均匀 8.更改浇口位置 9.扩大浇口 10.缩短模具流道。
解决方法:1.提高料温 2.提高注温 3.增加注速 4.接缝线外设冷料池 5.设放气口 6.改变浇口位或浇口 7.不要用脱模剂 8.转用易流动的低粘度类原料。
四、呈现问题:塑件呈现空洞。
原因:因塑料在熔料固化期间表面接触低温模壁,收缩集中于厚壁段而造成空洞,或因夹气做成空洞。
解决方法:1.提高注压(及二次压力) 2.延长注时 3.降低料筒固化温度 4.消减模壁厚度至6mm以下,必要时设置等壁厚助线,及去除多余壁厚 5.扩大浇口 6.缩短流道 7.调匀模温 8.更改浇口位置,排除夹气。
二、呈现问题:塑件呈银纹形。
原因:因塑料含水份,混料不均匀,注塑时夹气,添加剂或脱模剂过多。
解决方法:1.加强回压 2.减慢注速 3.清理料筒 4.提高模温 5.改浇口位置 6.扩大流道及浇口 7.烘料 8.料门中安装红外线灯。
三、呈现问题:塑胶接口不良。
原因:因塑料温度太低,不能熔化,或因气体排泄不足导致两股以上分流混合而产生发状细线或气泡。
五、呈现问题:塑件欠注或缺料。
原因:因机械注塑及塑化性能不足,料流不良,浇口截面太细,模壁太薄或泄气不良。
注塑成型常见不良现象及处理措施

注塑成型常见不良现象及处理措施注塑成型常见的不良现象有以下几种:
1. 短射:指注塑料进模型中未充满模腔,导致产品缺陷。
处理措施:增加注射
压力、延长注射时间、增加料缸温度、增加模具温度、增加模具出料口直径等。
2. 气泡:指产品表面或者内部浮现气泡,影响产品质量。
处理措施:增加注射
压力、延长注射时间、增加模具温度、增加料缸温度、增加模具出料口直径、增加模具排气孔等。
3. 热熔线:指产品表面浮现细小的线状缺陷,通常是由于注射速度过快导致的。
处理措施:减小注射速度、增加模具温度、增加模具出料口直径等。
4. 毛刺:指产品表面浮现细小的凸起,通常是由于模具设计不合理或者模具磨
损导致的。
处理措施:修复模具、修改模具设计、增加模具温度、增加模具出料口直径等。
5. 缩水:指产品尺寸缩小,通常是由于注射压力不足或者冷却时间不足导致的。
处理措施:增加注射压力、延长冷却时间、增加模具温度等。
6. 毛洞:指产品表面或者内部浮现凹陷,通常是由于注射速度过快或者模具设
计不合理导致的。
处理措施:减小注射速度、修改模具设计、增加模具温度等。
处理不良现象的关键是找到问题的根源,然后针对性地采取相应的处理措施。
同时,注塑成型过程中的参数控制和模具维护也是关键的因素,需要进行定期检查和调整。
注塑不正常情况及处理办法
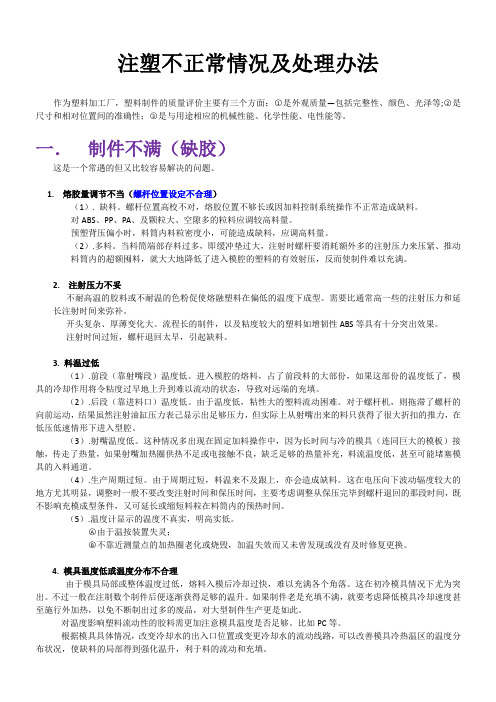
注塑不正常情况及处理办法作为塑料加工厂,塑料制件的质量评价主要有三个方面:○1是外观质量—包括完整性、颜色、光泽等;○2是尺寸和相对位置间的准确性;○3是与用途相应的机械性能、化学性能、电性能等。
一.制件不满(缺胶)这是一个常遇的但又比较容易解决的问题。
1. 熔胶量调节不当(螺杆位置设定不合理)(1). 缺料。
螺杆位置高校不对,熔胶位置不够长或因加料控制系统操作不正常造成缺料。
对ABS、PP、PA、及颗粒大、空隙多的粒料应调较高料量。
预塑背压偏小时,料筒内料粒密度小,可能造成缺料,应调高料量。
(2).多料。
当料筒端部存料过多,即缓冲垫过大,注射时螺杆要消耗额外多的注射压力来压紧、推动料筒内的超额囤料,就大大地降低了进入模腔的塑料的有效射压,反而使制件难以充满。
2. 注射压力不妥不耐高温的胶料或不耐温的色粉促使熔融塑料在偏低的温度下成型。
需要比通常高一些的注射压力和延长注射时间来弥补。
开头复杂、厚薄变化大。
流程长的制件,以及粘度较大的塑料如增韧性ABS等具有十分突出效果。
注射时间过短,螺杆退回太早,引起缺料。
3. 料温过低(1).前段(靠射嘴段)温度低。
进入模腔的熔料,占了前段料的大部份,如果这部份的温度低了,模具的冷却作用将令粘度过早地上升到难以流动的状态,导致对远端的充填。
(2).后段(靠进料口)温度低。
由于温度低,粘性大的塑料流动困难。
对于螺杆机,则拖滞了螺杆的向前运动,结果虽然注射油缸压力表己显示出足够压力,但实际上从射嘴出来的料只获得了很大折扣的推力,在低压低速情形下进入型腔。
(3).射嘴温度低。
这种情况多出现在固定加料操作中,因为长时间与冷的模具(连同巨大的模板)接触,传走了热量,如果射嘴加热圈供热不足或电接触不良,缺乏足够的热量补充,料流温度低,甚至可能堵塞模具的入料通道。
(4).生产周期过短。
由于周期过短,料温来不及跟上,亦会造成缺料。
这在电压向下波动辐度较大的地方尤其明显,调整时一般不要改变注射时间和保压时间,主要考虑调整从保压完毕到螺杆退回的那段时间,既不影响充模成型条件,又可延长或缩短料粒在料筒内的预热时间。
注塑常见缺陷及解决方法

注塑常见缺陷及解决方法
注塑是一种广泛应用于制造塑料制品的加工方法,但在实际生产中,由于原材料、工艺、设备等多种因素的影响,常常会出现各种缺陷。
下面是注塑常见缺陷及解决方法的详细介绍。
1. 气泡缺陷
气泡缺陷是注塑制品表面或内部存在的空洞或气泡。
一般由于原料过热、注模压力过高、模具进料不足等原因引起。
解决方法:降低原料温度、减小注射速度、增加进料量、调整模型温度、调整模具结构等。
2. 热胀冷缩缺陷
热胀冷缩缺陷是指塑料制品在注塑时由于热胀冷缩现象而导致的尺寸不稳定的现象。
解决方法:合理选择原材料、调整注塑工艺参数、改变模具结构、加入夹层等。
3. 毛刺缺陷
毛刺缺陷是指注塑制品表面出现的刺状物或毛细孔。
可能是由于模具设计不合理、注塑工艺不当、原材料污染等原因引起。
解决方法:调整模具设计、调整注塑工艺参数、更换清洗原材料。
4. 热裂缺陷
热裂缺陷是指塑料制品在注塑过程中由于温度过高而导致的开裂。
通常是由于原材料性能不佳、注塑工艺参数设置不当等原因引起。
解决方法:更换高品质的原材料、调整注塑工艺参数。
5. 毛边缺陷
毛边缺陷是指塑料制品表面出现的毛边或切口。
通常是由于模具设计不合理、注塑工艺参数不当、原材料品质差等原因引起。
解决方法:调整模具设计、调整注塑工艺参数、更换清洗原材料。
注塑制品的质量直接影响到其使用寿命和市场竞争力。
因此,在注塑生产中,应该重视并及时解决各种缺陷问题。
通过合理优化原材料、模具设计和注塑工艺参数等措施,不仅可以提高注塑制品的质量,还可以降低生产成本,提高企业的经济效益。
- 1、下载文档前请自行甄别文档内容的完整性,平台不提供额外的编辑、内容补充、找答案等附加服务。
- 2、"仅部分预览"的文档,不可在线预览部分如存在完整性等问题,可反馈申请退款(可完整预览的文档不适用该条件!)。
- 3、如文档侵犯您的权益,请联系客服反馈,我们会尽快为您处理(人工客服工作时间:9:00-18:30)。
塑件粘模
8.流入多模腔工模的熔胶流态不能适当平行 8.修正平行情形
利用热传导原理,将热传导油加热至适当温度,输送至成型机模具之管道内,加热模具至要求温度,并控制油温在 要求温度范围内。适合模温要求高的成型。改善塑料制品的质量,亦可提高生产效益。 PS SAN 10℃--70℃ 10℃--80℃ 10℃--80℃ HLPS LDPE PVC 10℃--75℃ 20℃--60℃ 20℃--60℃ ABS HDPE PC 10℃--80℃ 20℃--60℃ 70℃--115℃
4.延长工模冷却时间 5.减少冷却时间,使前后模有不同温度 6.延长保压并加强工模冷却 7.却除倒扣位,打磨抛光,增加脱兔 模部份的斜度 8.设立适宜的排气道 9.模腔壁再次抛光 1.升高料温 2.抹干净工模壁,不喷脱模剂或少脱模剂 3.再设定入水位或再加几个对称的入水 4.增设足够排气 5.再设计塑件及设定适当的入水位置 6.提高模温 7.升高注射压力或速度 1.提高模温 2.增加注射压力 3.增加注射速度 4.清洁和修理漏水裂痕或防止水汽在模壁凝洁 5.不用或少用脱模剂 6.检查材料是适合和混料时减少矿油用量 7.再次抛光模壁 1.增加熔胶筒各段 2.温度增加模温 3.增加压力 4.多啤几啤或用火焰加热射咀 5.不用或少用脱模剂 6.增加排气道数目及尺码 7.增加注射时间 9.扩大浇口 10.用较大的注塑机 1.提高熔胶筒温度 2.升高模温 3.加热干燥工模 4.清洁工模 5.调整适当的转压转速位置 6.烘干胶料
因 熔胶筒内壁烧焦,胶块脱落 解决方法 1.清洗炮筒内壁(拆螺杆清小洗) 2.用较硬胶料进入,以擦净炮筒内壁(小船坞机,如用清洗剂及亚加力等) 3.避免胶料长时间受高温(料温不宜太高,储料不能太多, 1.封盖料斗 黑点 2.胶料封闭好,保持干净 空气带来肮脏物或模腔腔内有空气引至 3.增加或减低熔胶筒和模具温度,以改变胶料进入模腔的速度 4.减低注塑压力或速度 1.料筒或螺杆不干净,原料不干净 2.料筒能胶料局部过热 1.清理料筒及螺杆并小心处理胶料不受污染 2.使炮筒之每段受热圴匀
1.charging barrel,screw and raw 2.barrel to rubber is overheating 3.friction against the cold glue size or friction against gun barrel then blackstreak burned 4.the Nozzle is overheated that scorch the plastic 5.have a big change of nozzle yellow spot yellow line brown stripe,discolo ur,Dark Dark white Blister 1 barrel soloverall or local 2 Plastic material stick barrel wall or 3 Rubber material stays long time in 4 Barrel has corner. raw material is moist lack of filling materials,reasons: 1.The thickness of product is thick,there is an extrude line in the cavity surface.
C 注塑时间太长 D 入料不足 2.胶料潮湿 3.模具温度不均匀 破裂或龟裂 1.填模太实 2.模温太低 4.顶针或环定不当 5.再用料过多(拉粒水口) 产品尺寸 1.模塑情况不稳定 性改变 2.注塑条件与正常时不一致 3.在检查塑件时周围空气温度不固定
3.不适当的脱模设计如角度斜位及倒扣位 3.修改工模
ing electric temperature controller
1.A reduce the temperature B reduce the spee 2.clean the nozzle or barrel screw 3.shorten the injection cycle 4.change the screw drying raw material and then reproduce
常见塑料 之模温要 求
PP
常见塑料 之模温要 求 PMMA 30℃--70℃ PA 50℃--80℃ POM 60℃--90℃
停机操作注意
PS,SAN ABS PE PP 因为硬胶的热稳定性好,在啤塑温度下长期受热也不会分解因此停机前只需把热并闭即可 此胶料的热稳定性也较好,停机时无需把机筒内的剩余胶料推出和清理 此胶料的热稳定性很好,在料筒内长期受热不会分解,故停机时不需推出料筒内的剩余胶料 和PE相似,但热稳定性比PE稍差 由于生产暂时停顿(如夜班不开工)需使料筒一直保持在160度C,以免胶料受潮,如需换料,则需用PE 清理料筒,并从热料筒中取出螺杆,用铜丝刷清理螺杆
开模时射 1.胶料过热 咀滴胶 2.注塑料料不够干燥 1.胶料不够热 2.模温不够热 3.注射压力太低
4.提高注塑速度 流纹和塑 4.注射速度太低 面起波纹 5.浇口太小引致胶料在模腔内有喷射现象 5.扩大浇口和降低注射压力 6.塑品切面厚薄不均匀 7.排气不足 1.模温太低 2.射速太慢 3.注射压力不足 4.射胶时间过长 6.A设计塑件俾切面厚薄均一 B去除制品上凸起的线条 7.增加排气 1.升高电热、升高模温 2.提高注射速度 3.提高注塑速度 4.缩短射胶时间 5.A清洁熔胶筒 B避免混入其它塑料 6.清洁模面,用小量润滑剂(脱模剂) 7.调节水口大小,使其得到良好的压力控制 降低温度及注射速度 1.A 降低温度 B 减少螺杆旋转速度或背压 2.降低模温 3.用计时表及加强管制工人的操作速度 4.增加温度和延长时间 5.A 改变模内冷却水道位置 B 用冷水机 1.减低注射压力 2.减少保压时间 3.使前且模温一致 4.再设计入水位置 5.尽可能保持切面厚度均匀 6.增高模温 7.升高料温C注6和7即变相减压 8.减少螺杆背压 1.A 减低注射压力或机筒温度 B 降低螺杆的旋转速度或螺杆背压 2.减少入料 3.减少注射时间
1.A 减低温度 B减低螺杆转速 C减低回料背压 2.清理射嘴或炮筒螺杆 3.缩短注塑周期 4.更换螺杆 烘干原料再生产
1.A 再设计模具
B
注塑压力太低
B 加大注塑压力 C 增加注塑时间 D 增加注塑速度及增加入水口阔度 2.模塑前胶粒避免受过大的温度变化及要干燥胶粒 3.重新排列运水信道,使模具温度一致 1.A减低速度;B减低压国 C 缩短注射时间 2.提高模温 4.再按放顶针让制品能顺利顶出工模 5.少用或不用拉粒或水口 1.A 调节操作情况,直至得到最大平稳操作 B 视乎啤塑工人的操作情况而决定啤塑时间长短 2.A 更正跟平常时不用的注塑条件 B 检查注塑温度,压力 ,工模温度,模塑时间,入料,电压, 3.A 保持周围空气温度固定 B 在同一条件下测量及检查制品
3.冷胶料互相磨擦或与炮筒壁磨擦时烧焦 3.A加入有外润滑剂的胶料 B胶料加小许白矿油 C增加炮筒后段温度 黑色条纹 4.射嘴过热烧焦胶料 4.减低射嘴温度
5.射嘴温度变化大
5.采用恒温控制器控制电热
1.溶胶筒全面或局部过热 黄点 2.胶料黏住炮筒内壁或射嘴以至烧 黄线 棕色条纹 3.胶料在炮筒内停留时间过长 变色 4.炮筒内存有死角 产品哑白 原料潮湿 气泡 模腔填料不足,原因: 1.A制品切面厚,模腔壁上有突起线
Problems of injection and solutions
Problem factors Solutions the inside wall of barrel was burned small black and the burned rubber block fall dots down into the product
1.when clean up charging barrel and screw sh 2.let each gun barrel well-heated
炮筒后段温度
3.A) add some sizing materail with lubricant Paraffin Oil in sizing materical C) increase posterior segment of gun barral 4.decrease the temperature of nozzle
清洗剂及亚加力等)
多,
的速度
black dot
1.to Clean the barrel(unload the screw ) 2.load hard rubber inside the barrel to clean th 3.Invoid the rubber long time under high temp 1.assemble the lodder with sealing cover. 2.to keep the rubber cleaning and seal it in a g the dirty stuff comes with the air or there are air in the mould cavity. 3.add or reduce the tempreture of barrel and m 4.reducing the inject pressure or speed
漏胶
1.胶料太热 2.注塑压力过高 3.模具或射咀凸凹两面接触不良 4.射台增压不够
1.A 降低胶料温度 B 减少螺杆转速和背压 2.A 降低压力 B 减少枕压时间 3.再次打磨模具唧嘴 4.检查机台射台射增压系统 1.A 降低炉咀温度 B 降低料筒温度 2.干燥胶料 1.增加胶料温度 2.增加工模温度 3.提高注射现象
2.过多入料
3.注射时间过长
塑件粘模
4.工模冷却不足(塑件热膨胀) 5.塑件因收缩而粘在阳模上 6.模内塑件未冷硬 7.工模内有倒扣位 8.模腔内深入部份空气压力小(真空状 态) 9.工模内壁光洁度不够 1.料温太低 2.模面有脱模剂等油渍 3.熔溶位离入水位太远 夹纹 4.排气不良 5.塑品切面厚薄转化大 6.模温太低 7.注塑压力低及速度慢 1.模温低 2.注射压力低 3.注射速度慢 塑件表面 4.模壁有水份 粗糙 5.用脱模剂过多 6.使用过多的内或外润滑剂 7.模表面粗糙 1.熔胶管各段不够 2.模温不够 3.压力不足 4.刚开机时射咀太冷 射胶不足 5.模温不均一 6.空气不能排出模腔(困气) 7.注射时间不够 9.浇口小 10.模腔熔胶量比注塑机大 1.料温不够 2.模温低 塑件表面 3.模内有水气 光亮条纹 4.工模有污渍 5.转压转速位置不当 6.料内有湿气 油温机