MRP的基本原理及运用
简述mrp的基本原理。

MRP 的基本原理
MRP 是 Material Requirements Planning 的缩写,意为“物料需求计划”。
它是一种用于确定企业所需物料和产品库存的管理工具和技术,旨在确保企业在生产过程中拥有足够的物料和产品库存,以满足客户需求和生产计划。
MRP 的基本原理是基于生产计划和物料清单 (Bill of Materials,BOM) 来确定所需物料的需求量和需求时间。
MRP 通过将生产计划和物料清单信息输入到计算机系统中,自动计算出每个物料的需求量和需求时间,从而为企业提供准确的物料需求计划。
MRP 的实施步骤包括以下几个方面:
1. 确定生产计划:首先需要确定生产计划,包括生产时间、生产数量和生产产品种类等信息。
2. 建立物料清单:每个产品都需要对应的物料清单,包括原材料、零部件和半成品等信息。
3. 确定物料需求:根据生产计划和物料清单,计算出每个物料的需求量和需求时间。
4. 检查库存:检查企业库存是否足够满足物料需求,如果不足则需要进行采购。
5. 制定采购计划:根据物料需求和库存情况,制定采购计划,包括采购时间、采购数量和采购供应商等信息。
6. 实施采购:根据采购计划,实施采购,并将采购物料入库。
7. 生产制造:根据生产计划和物料清单,进行生产制造,生产
出所需的产品。
mrp原理的应用
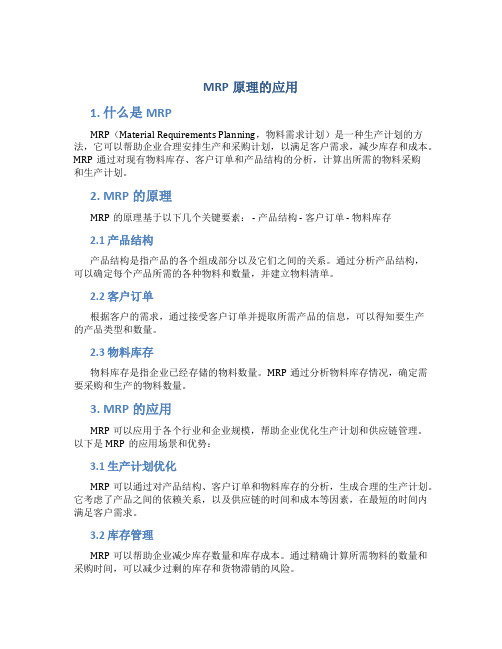
MRP原理的应用1. 什么是MRPMRP(Material Requirements Planning,物料需求计划)是一种生产计划的方法,它可以帮助企业合理安排生产和采购计划,以满足客户需求,减少库存和成本。
MRP通过对现有物料库存、客户订单和产品结构的分析,计算出所需的物料采购和生产计划。
2. MRP的原理MRP的原理基于以下几个关键要素: - 产品结构 - 客户订单 - 物料库存2.1 产品结构产品结构是指产品的各个组成部分以及它们之间的关系。
通过分析产品结构,可以确定每个产品所需的各种物料和数量,并建立物料清单。
2.2 客户订单根据客户的需求,通过接受客户订单并提取所需产品的信息,可以得知要生产的产品类型和数量。
2.3 物料库存物料库存是指企业已经存储的物料数量。
MRP通过分析物料库存情况,确定需要采购和生产的物料数量。
3. MRP的应用MRP可以应用于各个行业和企业规模,帮助企业优化生产计划和供应链管理。
以下是MRP的应用场景和优势:3.1 生产计划优化MRP可以通过对产品结构、客户订单和物料库存的分析,生成合理的生产计划。
它考虑了产品之间的依赖关系,以及供应链的时间和成本等因素,在最短的时间内满足客户需求。
3.2 库存管理MRP可以帮助企业减少库存数量和库存成本。
通过精确计算所需物料的数量和采购时间,可以减少过剩的库存和货物滞销的风险。
3.3 供应链优化MRP可以优化供应链流程,减少生产和采购的时间,并降低物料的成本。
它可以帮助企业与供应商建立更好的合作关系,提高供应链的可靠性和效率。
3.4 例子假设一家制造企业收到客户订单,要求生产100台产品A和200台产品B。
通过分析产品结构,产品A需要零件X和零件Y,产品B需要零件Y和零件Z。
然后,企业查看物料库存,发现零件X数量为50,零件Y数量为100,零件Z数量为80。
根据以上数据,MRP可以生成以下计划: - 采购50个零件X - 采购100个零件Y - 采购200个零件Z - 生产100台产品A - 生产200台产品B通过MRP计划,企业可以合理安排采购和生产计划,确保按时交付客户订单并减少库存成本。
简述mrp的基本原理。

简述mrp的基本原理。
MRP,即物料需求计划(Materials Requirement Planning),是一种基于需求的计划系统,通过分析产品结构和销售计划,以确定所需的原材料和零部件的数量和时间,从而满足产品生产和交付的需求。
MRP的基本原理是根据客户需求,通过分析产品结构和销售计划,计算出所需的原材料和零部件的数量和时间,并将其转化为采购计划和生产计划。
其核心概念是物料清单(Bill of Material,BOM)和主生产计划(Master Production Schedule,MPS)。
物料清单是一个层次结构,描述了产品的组成结构和各个部件之间的关系。
它包含了产品的每个组件、子组件以及所需的数量。
通过分析物料清单,可以确定每个组件的需求量,并根据销售计划进行排产。
主生产计划是根据销售计划和库存情况,确定每个产品的生产计划和交付时间。
它包括了产品的交付日期、数量和生产的时间表。
通过主生产计划,可以确定每个产品所需的原材料和零部件的数量和时间。
基于物料清单和主生产计划,MRP系统通过逐级向下的方式,计算出每个组件和零部件的需求量和时间。
它根据物料清单中的父子关系,逐级递归地计算出每个组件和零部件的需求量,并根据主生产计划确定其需求时间。
MRP还考虑了库存的现有量和未来的需求,通过计算净需求量,确定每个物料和零部件的采购计划和生产计划。
它会根据物料的供应周期和提前期,确定采购和生产的时间,并生成相应的订单。
通过MRP系统,企业可以在满足客户需求的同时,最大限度地降低库存成本和生产成本。
它可以实时跟踪产品的需求和供应情况,及时调整采购和生产计划,确保生产和交付的及时性和准确性。
MRP是一种基于需求的计划系统,通过分析产品结构和销售计划,以确定所需的原材料和零部件的数量和时间,从而满足产品生产和交付的需求。
它通过物料清单和主生产计划,计算出每个组件和零部件的需求量和时间,并生成相应的采购和生产计划。
mrp原理的七模块和应用

MRP原理的七模块和应用1. 介绍MRP(Material Requirements Planning,物料需求计划)是一种用于计划和控制生产过程的方法。
它基于物料清单、库存水平和生产需求等信息,通过计算和分析来确定所需的原材料和零部件,并合理安排生产计划。
MRP被广泛应用于制造业,可以提高生产效率、优化库存管理并降低生产成本。
2. MRP原理的七个模块2.1. 计划需求模块在这个模块中,根据销售订单、需求预测和订单交货期等信息,确定所需的成品数量。
通过计算未来的订单量和交货日期来制定生产计划。
2.2. 物料清单模块物料清单模块是整个MRP系统中非常重要的一部分。
它包含了产品的所有零部件和子组件的详细信息,包括物料编码、规格、类型和数量等。
在MRP过程中,通过物料清单的层级结构来计算所需的原材料和零部件。
2.3. 库存管理模块库存管理模块负责跟踪和管理当前库存水平。
它会记录进货、生产和销售等过程中的物料流动情况,并根据MRP计算出的需求量来预测和控制库存水平。
通过及时补充和调整库存,可以避免库存过剩或短缺的问题。
2.4. 采购模块采购模块用于规划和控制原材料和零部件的采购过程。
根据MRP计算出的需求量和交货时间,采购部门可以制定采购计划,并与供应商进行协商和交流。
采购模块还可以跟踪和管理采购订单的执行情况,并及时更新相关信息。
2.5. 生产计划模块生产计划模块主要负责制定和管理生产计划。
通过分析和计算销售订单、需求预测和库存状况等信息,生产计划模块可以确定生产所需的数量和时间,并安排生产工序和工作流程。
它还可以跟踪和控制生产进程,确保按时完成生产任务。
2.6. 容量规划模块容量规划模块用于确定生产资源的需求量和可用性。
它可以根据生产计划和工序特性等信息,计算出所需的机器、设备和人力资源,并分析其可用性和利用率。
容量规划模块可以帮助企业合理安排和调整生产能力,避免生产过程中的瓶颈和资源浪费。
2.7. 进度跟踪模块进度跟踪模块用于实时跟踪和监控生产进度。
MRP逻辑及原理

MRP逻辑及原理MRP(Materials Requirements Planning)是一种生产管理方法,通过对企业生产活动中物料需求量进行精确计划,以实现生产和物资供应的有效组织。
它的原理是通过分析销售订单、库存水平、物料清单和生产计划等信息,确定所需原材料和零件的准确数量,以满足生产要求,并避免库存过高或过低的情况。
MRP的逻辑基于以下几个原理:1.依赖关系:MRP逻辑中的材料需求是以依赖关系进行计算的。
每个成品都有一份清单,列出了制造该成品所需的原材料和零件。
这些材料可以是成品的直接组成部分,也可以是其他零部件的组成部分。
通过分析清单,可以确定成品制造所需的全部材料和数量。
2.主动计算:MRP是主动计算的过程,它根据销售订单、库存水平、物料清单等信息,自动推导出所需的原材料和零件数量。
通过实时计算,MRP可以快速反应生产需求的变化,并及时做出适应性调整,以确保生产计划的准确性和及时性。
3.时间驱动:MRP是一个时间驱动的系统,它根据生产时间表和库存水平,计算出每个物料的需求日期。
根据这些需求日期,可以确定购买和生产的时间,确保原材料和零件的供应和使用同步进行,以避免生产停滞和库存积压。
4.计划层次:MRP根据不同的计划层级进行计算和管理。
它可以根据需求进行总体计划,然后逐层进行分解,细化到具体的材料和零件级别。
通过层级计划,可以同时考虑整体产能和物资供应的平衡,确保生产计划的可行性和合理性。
MRP的实现过程通常包括以下几个步骤:1.确定需求:首先,需要收集和整理销售订单、库存水平、物料清单和生产计划等信息,以确定所需原材料和零件的需求。
2.计算需求量:根据销售订单和物料清单,计算出每个物料和零件的需求量,包括所需数量、需求日期和供应方式等。
3.确定供应计划:基于需求量和供应能力,确定原材料和零件的采购计划和生产计划。
要考虑到供应商的交货周期和企业的生产能力,以确保物资供应和生产的有效协调。
MRP原理及其应用

MRP原理及其应用1. 什么是MRPMRP(Material Requirements Planning)即物料需求计划,是一种主要用于生产计划及库存管理的方法。
它通过分析客户需求、当前库存情况以及供应链的其他相关信息,来确定物料的需求及其合理的采购或生产计划。
2. MRP的原理MRP的原理基于以下几个关键概念:2.1 主计划(Master Production Schedule)主计划是指根据企业内外部的需求信息,确定特定时间段内的产品生产计划。
主计划通常根据销售预测、订单和库存水平等数据来制定。
2.2 物料清单(Bill of Materials)物料清单是表示产品所需各个组件及其数量的列表。
它描述了产品的层次结构和组成关系,为MRP提供了基础数据。
2.3 库存状态记录(Inventory Status Record)库存状态记录是记录当前库存情况的数据库。
它包含了每个物料的库存数量、批次、有效期等信息。
MRP通过读取库存状态记录来进行需求计算和库存调整。
2.4 运算逻辑(Logic Calculation)MRP的运算逻辑包括两个核心计算:净需求计算和进行批量推算。
净需求计算是指根据主计划和物料清单,通过逐级展开和扣减,计算出每个物料在每个时间点上的净需求量。
批量推算是指根据净需求量和物料的生产批量等因素,推算出具体的采购或生产计划。
2.5 周期触发(Time Fence)周期触发是指设定一个时间点,在该时间点之前的需求变动不会影响已经计划的采购或生产计划。
周期触发可以保证计划的稳定性,在一定程度上降低需求变动对供应链的影响。
3. MRP的应用MRP可以应用于各种制造行业,如生产制造、加工制造等。
它可以帮助企业进行更精细化的生产计划和库存管理,提高生产效率、降低库存成本,并确保及时交付客户需求。
下面是MRP在实际应用中的几个主要场景:3.1 产品生产计划MRP可以根据销售预测和订单需求,结合库存状态记录和物料清单,计算出具体的产品生产计划。
MRP的基本原理和关键信息要素
MRP的基本原理和关键信息要素词条内容:所谓物料需求计划(materials requirement planning,简称MRP),就是要制定这样的原材料、零部件的生产与库存计划:决定外购什么、生产什么、什么物料必须在什么时候订货或开始生产、订多少、生产多少、每次的订货和生产的批量是多少,等等。
MRP(物料需求计划)的基本原理有两条:1、从最终产品的生产计划(MPS)导出相关物料(原材料、零部件、组件等)的需求量和需求时间;2、根据物料的需求时间和生产(订货)周期来确定其开始生产(订货)的时间。
例如,对于一个外构件来说,如第5周最终产品的装配要用到它,其订货周期为2周,则最晚第3周应开始订货;对于一个自加工件来说,如第5周需用于装配,而其本身的生产周期为1周,则最晚应第4周开工。
由此可见MRP(物料需求计划)的制定不是基于过去的统计数据,而是基于未来的需求。
因此,制定MRP所需的关键信息要素有三个:(1)主生产计划(MPS)。
即是每一最终产品的生产计划。
据此可以推算出所需的相关物料;(2)物料清单(bill of materials,简称BOM)。
它说明一个最终产品是由哪些零部件、原材料所构成的,这些零部件的时间数量上的相互关系是什么;(3)库存纪录。
它告诉计划人员,现在库存中有哪些物料,有多少,已经准备再进多少,从而在制定新的加工、采购计划时减掉相应的数量。
综上所述,MRP(物料需求计划)可以回答4各方面的问题:(1)要生产什么?(根据主生产计划)(2)要用到什么?(根据物料清单)(3)已经有了什么?(根据库存纪录)(4)还缺什么?何时生产或订购?(MRP运算后得出的结果)这四个问题是任何工业企业,不论其产品类型、生产规模、工艺过程如何,都必须回答的、带有普遍性的基本问题。
因此,MRP(物料需求计划)产生以后,很快就受到了广大企业的欢迎与应用。
MRP的工作原理
MRP的工作原理MRP(Material Requirements Planning,物料需求计划)是一种计划和控制生产过程中所需物料的方法。
它通过分析销售定单、库存水平和生产能力等数据,以确定所需的原材料和零部件,并安排其采购和生产,以满足生产计划和客户需求。
下面将详细介绍MRP的工作原理。
1. 数据采集与准备MRP的第一步是采集和准备必要的数据。
这些数据包括销售定单、库存记录、物料清单和生产计划等。
销售定单提供了客户需求的信息,库存记录提供了当前库存水平,物料清单列出了产品所需的所有原材料和零部件,生产计划确定了生产的时间表和数量。
2. 主生产计划(MPS)主生产计划是根据销售定单和预测需求制定的生产计划。
它确定了每种产品的生产数量和交货日期。
MPS是MRP的输入之一,用于确定物料需求计划。
3. 净需求计算净需求计算是MRP的核心步骤之一。
它通过将主生产计划减去现有库存和已计划的收货量,计算出每一个物料的净需求量。
如果净需求量为正数,则表示需要采购或者生产该物料;如果净需求量为负数,则表示库存充足,无需采购或者生产。
4. MRP计算在MRP计算中,根据净需求量、物料清单和库存记录等信息,计算出每一个物料的具体需求量和采购/生产计划。
MRP会考虑到供应商的交货时间、批量大小和生产能力等因素,以确定最佳的采购和生产计划。
5. 采购和生产定单释放根据MRP计算的结果,系统会生成采购定单和生产定单。
采购定单用于向供应商下达采购请求,生产定单用于指导生产线进行生产。
这些定单包含了所需物料的数量、交货日期和其他相关信息。
6. 跟踪和控制一旦采购和生产定单释放,MRP系统会跟踪和控制物料的采购和生产过程。
它会监控供应商的交货时间,确保物料按时到达,并及时调整生产计划以适应任何变化。
7. 库存管理MRP系统还负责库存管理。
它会跟踪物料的库存水平,根据实际情况进行调整。
如果库存过高,系统可能会减少采购数量或者推迟生产;如果库存过低,系统会提前采购或者加快生产进度。
物料需求计划基本原理
物料需求计划基本原理物料需求计划(Material Requirement Planning,简称MRP)是一种用于制定生产计划和控制库存的管理工具。
其基本原理是根据企业的产品需求、库存情况和供应能力,确定物料的采购计划和生产计划,确保物料的及时供应和合理运用,从而实现生产过程的优化和成本的控制。
物料需求计划的基本原理包括以下几个方面:1. 需求预测:物料需求计划的制定首先要根据市场需求和产品销售情况进行需求预测。
通过收集市场数据、分析销售趋势和产品周期等因素,预测出未来一段时间内产品的需求量,为后续的计划制定提供依据。
2. 库存管理:物料需求计划需要根据当前库存情况进行调整和控制。
通过对已有库存进行点数盘点或使用库存管理系统,准确了解当前的库存水平,以便根据需求量和安全库存的设定,确定采购和生产计划,避免过多或过少的库存现象。
3. 供应能力评估:物料需求计划需要评估供应能力,确保物料能够按时供应。
这个评估主要包括供应商的能力评估和生产资源的评估。
供应商的能力评估主要是考察供应商是否能够按时供应物料,并评估供应商的稳定性和质量控制能力;生产资源的评估主要是检查企业自身的生产能力和设备状态,以及评估是否需要进行扩充或改造。
4. 计划制定:物料需求计划根据需求预测、库存情况和供应能力,制定细化的采购和生产计划。
采购计划主要是确定采购物料的种类、数量和需求时间,以便及时向供应商下单并安排运输;生产计划主要是确定产品的生产数量、生产时间和生产工序,以便合理安排生产能力和生产流程。
5. 控制执行:物料需求计划制定后,需要进行控制和执行。
对于采购计划,需要及时与供应商联系、下单并跟踪物料的供应情况,确保物料的及时到货;对于生产计划,需要分配生产任务并跟踪生产进度,确保按计划进行生产。
同时,还需对计划执行情况进行监控和调整,及时处理计划执行中的问题和风险。
物料需求计划的基本原理在企业生产和供应链管理中具有重要作用。
MRP物料需求计划的原理及实施
MRP物料需求计划的原理及实施MRP(Material Requirements Planning,物料需求计划)是一种帮助企业有效管理物料需求的计划工具。
它通过预测和分析企业的生产需求,以便准确、及时地满足生产和销售的要求,同时最大程度地降低库存水平和成本。
MRP的原理是基于需求的推动,通过将销售订单和生产计划转化为对原材料和零部件的需求计划,从而确保生产过程中所需的物料适时到达。
其主要步骤包括:1. 制定销售计划:通过销售预测和市场需求,确定未来一段时间内的销售计划。
2. 确定净需求:根据销售计划、现有库存和安全库存等因素,计算出每个物料的净需求,即需求量减去库存量。
3. 转化成物料需求计划:根据净需求和物料的产出率,计算出所需的原材料和零部件的数量和时间。
4. 确定采购订单:根据物料的需求计划,生成相应的采购订单,以便及时从供应商处获取所需物料。
5. 跟踪和监控:持续监控销售和库存情况,及时调整需求计划和采购订单。
MRP的实施需要以下几个关键步骤:1. 系统准备:为了实施MRP,企业需要选择和实施适合其需求的MRP软件,并进行相关系统配置和设置。
2. 数据收集和整理:收集和整理与物料相关的数据,包括销售订单、库存信息、供应商信息、物料需求规格等。
3. 参数设置:根据企业的需求和生产特点,设置合理的参数,如安全库存、生产周期、物料提前期等。
4. 数据输入和处理:将收集到的数据录入MRP系统,并进行计算、分析和处理,生成物料需求计划和采购订单。
5. 跟踪和调整:持续跟踪和监控销售和库存情况,及时调整需求计划和采购订单,确保生产和销售的顺利进行。
通过实施MRP,企业可以实现以下好处:1. 减少库存成本:准确的物料需求计划可以避免过多的库存积压,减少了库存成本和有形资产的占用。
2. 提高生产效率:MRP可以帮助企业在需要时及时获得所需物料,提高生产的灵活性和效率。
3. 缩短交货周期:通过MRP的实施,企业可以更好地安排物料的供应,并在生产周期内及时完成订单。
- 1、下载文档前请自行甄别文档内容的完整性,平台不提供额外的编辑、内容补充、找答案等附加服务。
- 2、"仅部分预览"的文档,不可在线预览部分如存在完整性等问题,可反馈申请退款(可完整预览的文档不适用该条件!)。
- 3、如文档侵犯您的权益,请联系客服反馈,我们会尽快为您处理(人工客服工作时间:9:00-18:30)。
目录一. 透视 (5)生产与库存控制的目标 (5)生产与库存控制的演变 (6)今日的制造控制 (7)库存控制与生产控制之间的关系 (8)管理政策与制造控制 (10)将来 (11)二. 库存管理的基本原理 (12)库存的定义 (12)库存的功能 (13)库存的分类 (14)库存的成本 (15)按价值分布 (17)库存管理得怎么样? (19)三. 经济批量 (21)经济批量概念的价值 (21)EOQ的基本概念 (22)试错法 (23)无精确成本时的EOQ (24)平方根EOQ (24)EOQ公式中的成本 (27)平方根EOQ公式的变体 (28)非即时收货 (29)主调整与次调整 (29)数量折扣 (32)最小总成本法 (32)零件─期间平衡法 (33)瞻前/顾后 (34)最小单位成本法 (36)期间订货量(POQ) (36)批对批 (38)实际的考虑 (38)四. 需求管理 (41)需求管理的范围 (41)预测的重要性 (41)预测的演变 (44)预测的特征 (45)预测的实施 (48)判断预测 (51)统计预测 (51)总业务量的预测 (52)特殊预测 (59)预测为什么失败 (59)需求的源 (60)五. 物料控制:独立需求 (62)库存的补充 (62)订货点法的基础 (63)用目视法寻找订货点 (64)预测误差的估计 (65)订货点的计算 (70)预测间隔与提前期差别的调整 (72)泊桑分布的使用 (77)服务的概念 (79)统计量的价值 (80)使用的注意事项 (82)定期评审技法 (83)两种简单订货方法 (84)分时段订货点法 (85)服务件需求的处理 (86)分支仓库需求的处理 (87)独立/相关需求 (87)六. 物料控制:相关需求 (88)物料需求计划的逻辑 (88)计算机以前的MRP (88)MRP的前提条件 (93)MPS子系统 (93)零件代号化 (93)物料清单的构成 (94)工程更改的控制 (98)工程更改的历史记录 (100)MRP的机制 (101)对MRP的改进 (105)分配 (107)MRP的更新 (109)订货生产作业中的MRP (110)重复性制造业中的MRP (111)过程工业中的MRP (112)MRP:技法与逻辑 (112)七. 主计划 (114)计划的阶梯结构 (114)主生产计划(T HE M ASTER P RODUCTION S CHEDULE 缩写为MPS) (117)不同企业中的MPS (119)为了灵活性而超量计划MPS (122)MPS的视界 (123)MPS的格式 (125)关于MPS的误解 (126)MPS的问题 (127)MPS的用途 (128)管理层对MPS的作用 (129)八. 总量库存管理 (130)总量控制的必要性 (130)投入产出总量控制 (131)总量批量库存 (133)总量安全存货库存 (136)总量在制品库存 (142)总量期望库存 (143)总量运输库存 (143)总量屏障库存 (143)管理好总的库存投资 (144)九. 能力需求计划 (145)提前期:种类与要素 (145)能力计划的一种合理方法 (147)生产计划的制定 (147)季节性生产计划 (150)生产计划工作中的实际因素 (153)功能部门的粗能力计划 (155)细能力需求计划 (157)外购物料的能力计划 (158)订货生产工厂中的能力计划工作 (159)能力计划图解技法 (160)优先级与能力计划的结合 (161)十. 投入控制 (163)投入控制在有效制造控制中的作用 (163)选择恰当的投入 (164)从属工作中心的日程计划 (168)控制车间投入的行动 (171)安排日程计划的技法 (173)工作中心加负荷的方法 (179)对供应商的投入控制 (182)装配作业的日程计划安排 (183)线性规划与排队论 (185)十一. 产出控制 (189)控制的要素 (189)控制能力的必要 (189)投入/产出控制 (189)能力控制中的实际考虑 (196)产出控制中的相关要素 (197)优先级控制的目的 (198)催稽(E XPEDITING) (199)调度(D ISPATCHING) (200)流动控制(F LOW C ONTROL) (201)重新安排日程计划与优先级规则 (202)看板 (206)提前期控制 (206)任务车间仿真(J OB S HOP S IMULTION) (210)有效的车间现场控制 (211)产出控制技法的选择 (211)十二. 反馈与校正行动 (213)反馈──控制的基础 (213)订货生产厂中的反馈与校正行动 (214)备货生产厂中的反馈与校正行动 (216)采购中的反馈 (217)几种反馈技法 (217)绩效的度量 (220)作业控制(O PERATING C ONTROLS) (224)系统健康状况诊断 (226)校正行动的生成 (226)计划与控制职能的管理 (227)压缩库存 (230)缩短提前期 (231)制造控制的未来 (231)企业制造资源计划MRPII原理一. 透视生产与库存控制的目标大多数旨在获取利润的制造企业有三个主要目标:1、最大的客户服务2、最小的库存投资3、高效率(低成本)的工厂作业达成这些目标的过程中主要的问题是这些目标基本上是互相冲突的。
若把库存水平提得很高而且不惜通过改变生产水平与生产日程去满足客户需求的变化,就可以提供最大的客户服务。
但这种做法要以牺牲第二,第三个目标来达成第一个目标。
若生产水平难得更改,不发生加班加点,机器一旦调整好之后就长期地运转,只生产这一特定产品,则工厂作业可保持高效率;然而,其结果却是在达成最高工厂效率这一目标的同时带来巨大的库存量与不良的客户服务。
倘若使客户等待而且强迫工厂对客户需求的变化与生产的中断迅速作出响应,则库存可以保持低水平。
在现实世界中,由于上述的三个目标对于持久的成功几乎同等地重要,很少有哪家公司能当得起只顾全其中一个目标而排斥另外两个目标。
生产与库存控制基本上就是同为在工厂作业中协调这些目标所需的日常决策提供所需信息这件事打交道。
对于拥有自己的小小制造公司的一名经理,这些目标基本冲突这一事实是明摆着的。
他对工厂中的机器设备投入了他的资金,他控制着自己的制造日程,他又是他自己的销售代表。
当一家客户要求立即交货时,他的对策是清楚的─- 或者化钱去搞调整机器与加班加点,或者让客户等待。
他也可以采取为未来的生意持有库存──成品、零件或原材料──的对策,以便有可能给他的客户以更好的服务。
在这样一个只有一名经理的公司中就存在着这些目标之间的冲突,它们不是容易解决的,但至少该经理能看到这个冲突并权衡自己的诸种对策。
在今日的一家大的制造公司里,为客户服务的责任落在组织中的一个部门,即销售部,它很少考虑提高工厂效率或降低库存水平的责任。
另一方面,制造部门的人员通常对库存感有不多的责任,对客户服务也许感有稍多一点责任。
事实上,许多车间经理与监工人员恐怕从来也不是从客户的观点来看待他们的活动的。
往往,这些人员的绩效并非以他们对公司总体目标的贡献来衡量,而是以他们达成他们被委派的有限目的的能力来衡量的。
例如,很少有第一线的监工人员是以他们控制提前时间与保持存货中有物品的能力来衡量的。
但他们的事业很大程度上取决于他们完成生产任务有多好,同工会打交道有多好以及能否满足预算的开销目标。
由于同样的原因,很少有销售人员是按他们对利润的贡献来判断的;他们完全是根据销售更多产品的能力来评价的。
在今日的商业界有一种被说得过了头的陈词滥调,这就是:让一家公司内部的经理们互相竞争是健康的。
如果这些经理是为着同一些目标而竞争,那么这种说法之中确有真理,因为这样竞争能产生极好的结果,但若他们开始为着不同目标而竞争,则其结果将是浪费、冲突与挫折。
在一家现代化的公司里,经理们的责任已经明确划分,他们的绩效度量鼓励他们去搞次优化,在这种公司里要去协调这些互相冲突的目标成了一个挑战性的问题;试图解决这一问题便是生产与库存计划与控制的主要功能。
生产与库存控制要通过一个信息系统来起作用,它编制计划,对照计划度量实际绩效,然后将信息传递给必须采取校正行动的直线管理人员,其功能就是去协调这些目标以满足公司总的利润目标。
没有其它小组去干这件事。
生产与库存控制的演变生产控制与库存控制是分开来发展的。
在最初,生产控制只是直线主管人员要完成的许多功能之一。
他订购材料,通过雇佣与解雇人员确定工人人数与生产水平,通过他的部门催稽工作并通过库存来控制客户服务,而库存多少又是他努力的结果。
由于工作量的增加,用一名文书作他的助手,以关照计时,保管各种记录及电话应答等职能。
这使得文书在回答工作状态与有关交货允诺的查询时经常同销售部门发生接触;除了跟踪工作进展之外,文书还开始作物料订货与生产上所需的其它准备工作的计划。
这种文书实际上就是生产控制职能的开始。
后来,随着记录保管活动被转移到了主办公室,这个文书发展成为一名催货员。
在1890年代,一家著名的新英格兰公司中有一个部门就叫"催办部"──很容易想象这些人的责任与活动。
对生产控制有过一些使之成为更加有组织并更加科学的方法的企图;在1880年代某兵工厂(Watertow Arsenal)曾设置相当广泛的生产控制系统,但第二次世界大战以前它并未得到普遍的应用。
在第二次世界大战中,催货员的处境是名誉扫地,因为在同事心目中他是同危机、混乱、压力与麻烦相伴的。
造船公司老板Henny Kaiser把他公司里的催货员取名为催稽员。
他通过《读者文摘》上的文章,推广了催稽员作为一名志向行动的能干而有进取心并对满足生产日程作出极其重要贡献的人的概念。
1950年代时,在书本里往往用催稽这个词来定义生产控制。
当时的一位实际工作人员把他自己的活动描述为收到一位客户的订单之后他先订购装配所需要的零件,然后,当客户来查问为何未能如期交货时,则追踪订单,找出这些零件在哪里,并贴上“急件”标签。
即使今天,催稽员仍是大多数生产控制系统的必要组成部分之一。
库存控制是沿着更为科学的(至少在理论上)路线发展的。
经济批量的基本概念发表于1915年(1),确定订货点的统计方法在1934年由R.H.Wilson提出。
(8)然而,这些相当复杂的库存管理系统技法很少获得应用。
也许这是因为由于1930年代与1940年代不是鼓励科学管理的年代。
在1930年代的衰退时,对大多数公司而言最重要的目标是生存。
就像在大洋上空一架失事的飞机上的人们为了减轻飞机的载荷而往机外投掷食品与珍贵物品那样,在大衰退的年代里长期利润与成长变成次要的了。
1940年代后期,当被抑制的需求为所能生产出来的每件东西提供有一个现成的市场时,库存控制的目标──平准工作负荷或在客户服务的基础上竞争──在大多数企业经营中也不是重要问题。