液压阀块设计经验
液压阀块设计范文

液压阀块设计范文液压阀块设计涉及到液压传动系统的设计和组装过程中的一个重要环节。
液压阀块是液压系统中控制压力、流量和方向的设备,它由阀体、阀芯、阀座、弹簧和液压接口等部件组成。
液压阀块的设计需要满足系统的性能要求,并考虑到制造工艺和成本等因素。
首先,在液压阀块的设计中需要考虑系统的工作压力和流量等参数。
工作压力可由系统中的最大工作压力确定,而流量要根据系统的需求来确定。
这些参数对于阀芯、阀座和传动杆等部件的材料选取和尺寸设计有着直接的影响。
其次,液压阀块的结构设计需要考虑流体控制的种类和数量。
常见的流体控制方式有单向控制、双向控制和比例控制等。
在设计阀块时需要根据系统的需求确定所需的控制方式,并合理安排阀体中的控制孔和通道等结构。
另外,液压阀块的布局设计也是一个重要的环节。
布局设计包括阀体内的通道连接和布置,以及液压接口的位置和数量等。
在设计中需要考虑到系统的安装空间、管路连接和维护等因素,合理布局液压阀块的各个部件,以便于系统的集成和维护。
液压阀块的材料选取也是设计过程中需要注意的一个方面。
材料的选择一方面要考虑到阀块的工作压力和流量等参数,另一方面还需要兼顾材料的成本和可加工性等因素。
通常情况下,阀体和阀座等部件会选用高强度和耐磨性较好的材料,如铸铁、铸钢或铝合金等。
在液压阀块的设计中,还需要考虑到系统的启动和停止过程中的冲击和噪声等因素。
为了减小系统中的冲击和噪声,可以在阀芯和阀座之间设计减震装置,如液压缓冲器或阀芯孔的设计。
最后,设计液压阀块还需要进行系统的仿真和优化。
通过利用流体力学仿真软件对系统进行仿真,可以分析和优化阀块的性能和设计参数。
仿真结果可以帮助设计人员了解系统的工作状态,并进行进一步的优化和改进。
在液压阀块的设计过程中,需要综合考虑系统的性能要求、制造工艺和成本等因素。
通过合理的设计和优化,可以提高液压系统的性能和可靠性,达到更好的控制效果。
液压阀块设计
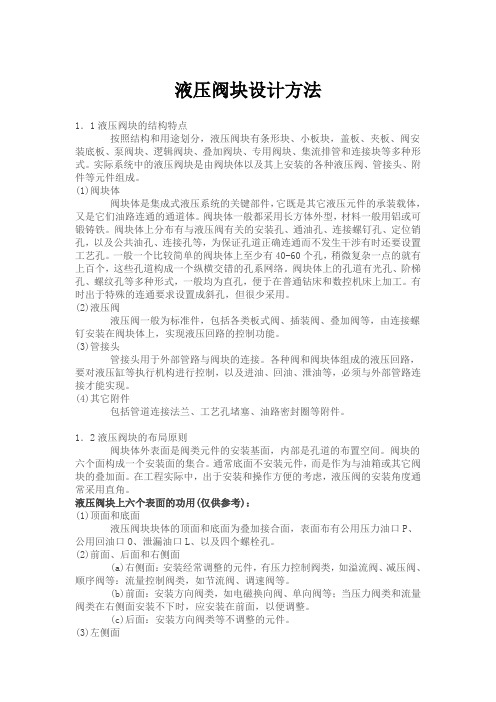
液压阀块设计方法1.1液压阀块的结构特点按照结构和用途划分,液压阀块有条形块、小板块,盖板、夹板、阀安装底板、泵阀块、逻辑阀块、叠加阀块、专用阀块、集流排管和连接块等多种形式。
实际系统中的液压阀块是由阀块体以及其上安装的各种液压阀、管接头、附件等元件组成。
(1)阀块体阀块体是集成式液压系统的关键部件,它既是其它液压元件的承装载体,又是它们油路连通的通道体。
阀块体一般都采用长方体外型,材料一般用铝或可锻铸铁。
阀块体上分布有与液压阀有关的安装孔、通油孔、连接螺钉孔、定位销孔,以及公共油孔、连接孔等,为保证孔道正确连通而不发生干涉有时还要设置工艺孔。
一般一个比较简单的阀块体上至少有40-60个孔,稍微复杂一点的就有上百个,这些孔道构成一个纵横交错的孔系网络。
阀块体上的孔道有光孔、阶梯孔、螺纹孔等多种形式,一般均为直孔,便于在普通钻床和数控机床上加工。
有时出于特殊的连通要求设置成斜孔,但很少采用。
(2)液压阀液压阀一般为标准件,包括各类板式阀、插装阀、叠加阀等,由连接螺钉安装在阀块体上,实现液压回路的控制功能。
(3)管接头管接头用于外部管路与阀块的连接。
各种阀和阀块体组成的液压回路,要对液压缸等执行机构进行控制,以及进油、回油、泄油等,必须与外部管路连接才能实现。
(4)其它附件包括管道连接法兰、工艺孔堵塞、油路密封圈等附件。
1.2液压阀块的布局原则阀块体外表面是阀类元件的安装基面,内部是孔道的布置空间。
阀块的六个面构成一个安装面的集合。
通常底面不安装元件,而是作为与油箱或其它阀块的叠加面。
在工程实际中,出于安装和操作方便的考虑,液压阀的安装角度通常采用直角。
液压阀块上六个表面的功用(仅供参考):(1)顶面和底面液压阀块块体的顶面和底面为叠加接合面,表面布有公用压力油口P、公用回油口O、泄漏油口L、以及四个螺栓孔。
(2)前面、后面和右侧面(a)右侧面:安装经常调整的元件,有压力控制阀类,如溢流阀、减压阀、顺序阀等:流量控制阀类,如节流阀、调速阀等。
液压阀块设计经验

液压阀块设计规范液压阀块的设计大多属于非标设计,需要根据不同的工况和使用要求进行针对性设计,设计阀块时大致分为以下几步:选材、设计、加工与热处理、去毛刺与清洗、表面防锈处理、试验。
1、选材:不同的材料决定了不同的压力等级,首先根据使用压力进行合理选材,一般来说遵循以下原则:工作压力P<6.3MPa时,液压阀块可以采用铸铁HT20一40。
采用铸铁件可以进行大批量铸造,减少工时,提高效率,特别适用于标准化阀块。
6.3MPa≤P<21MPa时,液压阀块可以选用铝合金锻件、20号锻钢或者Q235;低碳钢焊接性能好,特别适合与非标的硬管(使用中很多阀块需要和硬管进行焊接)进行焊接。
P≥21MPa时,液压阀块可以选用35号锻钢。
锻打后直接机加工或者机加工后调质处理HB200-240(一般高压的阀块,往往探伤、机加工与热处理循环进行)。
设计阀块时阀块最初的厚度定为最大通径的5倍,然后根据具体设计逐步才缩小;设计通道时应合理布置孔道,尽量减少深孔、斜孔和工艺孔,先安排大流量通道,最后是先导油通道,各孔道之间的安全壁厚不得小于3~5mm ,还应考虑钻头在允许范围内的偏斜,适当加大相邻孔道的间距;通道内液压油流速不能高于12m/s ,回油通道要比是进油通道大20-40%;阀块进油口,工作口,控制口要加工测压口;各阀口要刻印标号;对于质量较大的阀块必须有起吊螺钉口。
阀体设计的一般规定:1.阀块体的外形一般为矩形六面体。
2.阀块体材料宜采用35钢锻件或连铸坯件。
3.阀块体的最大边长宜不大于600mm ,所包含的二通插装阀插件数量宜不大于8。
4.当液压回路所含的插件多于8个时,应分解成数个阀块体,各阀块体之间用螺栓相互连接,结合面处的连接孔道用O 型密封圈予以密封,组成整体的阀块组。
连接螺栓的矩形性能应不低于12.9级。
5.设计阀块体的主级孔道时应考虑尽可能减小流阻损失及加工方便。
6.主级孔道的直径按公式(1)估算选取:maxv 61.4Q D 式中:D - 孔道直径,mm;Q - 孔道内可能流过的最大工作流量,L/min;vmax - 孔道允许的最大工作液流速,m/s 。
液压阀块设计指南与实例

液压阀块设计指南与实例液压阀块设计指南与实例一、引言液压阀块是液压系统中的重要组成部分,用于控制液压系统流体的方向、压力和流量。
本文将详细介绍液压阀块的设计指南与实例,包括阀块的选材、结构设计、孔道布局、阀门选型等方面的内容。
二、阀块选材1、阀块选材的基本要求a:耐压性能:阀块应具备足够的耐压能力,能够承受系统所需的工作压力。
b:耐腐蚀性能:阀块应选择能够防止介质对阀块材料腐蚀的材料。
c:密封性能:阀块的材料应具有良好的密封性能,确保阀块与阀门之间的连接处不会发生泄漏。
d:加工性能:阀块材料应易于加工,以便进行精确的孔道加工和表面处理。
2、常用阀块材料a:铸铁:适用于一般工作压力较低的液压系统。
b:铝合金:重量轻,热传导性能好,但强度较低,适用于中小型液压系统。
c:铜合金:具有良好的耐磨性和导热性能,适用于高速液压系统和高压液压系统。
d:不锈钢:耐腐蚀性能好,适用于酸碱介质工作的液压系统。
三、结构设计1、阀块结构类型a:单阀块结构:阀块中仅包含一个阀门,适用于简单的液压系统。
b:复合阀块结构:阀块中包含多个阀门,可灵活调配,并满足复杂系统需求。
2、阀块结构要求a:阀门间距:阀门之间的间距要足够,以便进行正确的安装和拆卸操作,并减小液压能量损失。
b:阀门布局:根据系统需求,合理布局阀门,使其操作灵活、方便,并充分考虑阻塞和泄漏问题。
c:孔径设计:阀块中的孔径设计应满足系统流量和压力的要求,确保系统运行稳定。
d:强度分析:对阀块的结构进行强度分析,确保其能够承受系统的工作压力和冲击负荷。
四、孔道布局1、孔道布局原则a:空间合理利用:在有限的阀块空间内,合理布局孔道,减小阀块尺寸,提高系统紧凑度。
b:流态分析:通过流态分析确定孔道布局,避免液压能量损失和压力波动。
c:加工方便性:孔道应设计成易于加工的形状,以减少加工难度和提高加工精度。
2、孔道布局实例:(此处可插入一个阀块孔道布局示意图)五、阀门选型1、阀门种类a:止回阀:用于防止流体倒流的阀门。
液压阀块设计指南及实例

液压阀块设计指南及实例液压阀块是液压系统中的重要组成部分,它将多个液压阀组合在一起,实现了液压系统的控制功能。
液压阀块的设计需要考虑液压系统的工作压力、流量、控制方式等因素,并确保阀块的结构紧凑、性能可靠,满足系统的控制要求。
本文将介绍液压阀块的设计指南,并提供一个实例。
液压阀块的设计指南如下:1.功能确定:根据液压系统的控制需求,确定阀块需要实现的功能,包括液压传动方向、流量控制、压力控制等。
2.结构设计:根据功能确定,设计阀块的结构布局。
阀块的结构应尽量紧凑,减小系统的占地面积。
3.阀种选择:根据液压系统的工作条件选择适合的液压阀,包括插装阀、堆装阀、适应性阀等。
同时,阀的尺寸和材料也需要根据系统的工作压力和流量来选择。
4.连接方式选择:根据阀和液压元件的连接方式来选择适合的连接方式,包括螺纹连接、焊接连接、法兰连接等。
连接方式的选择应考虑系统的工作压力、流量和连接的可靠性。
5.流路设计:根据系统的控制要求,设计阀块的流动路径。
流路设计应尽量简洁,减少流阻,同时保证流量的平稳性和可控制性。
6.液压损失分析:进行液压损失分析,评估阀块的性能和效率。
根据分析结果,进行优化设计,减小液压损失。
假设设计的液压阀块需实现以下功能:实现对两个液压缸的单向控制,并且实现液压缸的速度控制。
根据功能确定,液压阀块需要包括两个单向阀和一个溢流阀。
根据结构设计,可以将两个单向阀和溢流阀布置在同一块阀块上,减小系统的占地面积。
根据阀种选择,选择两个插装式单向阀和一个插装式溢流阀。
根据连接方式选择,选择插装式阀,阀与阀之间采用螺纹连接,阀与液压缸之间采用法兰连接。
根据流路设计,将两个单向阀和溢流阀连接成合适的流动路径,实现液压缸的单向控制和速度控制。
进行液压损失分析,根据分析结果进行优化设计,减小液压损失。
通过以上设计步骤,完成了液压阀块的设计。
设计完成后,还需要进行阀块的制造和装配,并进行实验验证,确保阀块能够满足系统的控制要求。
液压阀块设计指南与实例
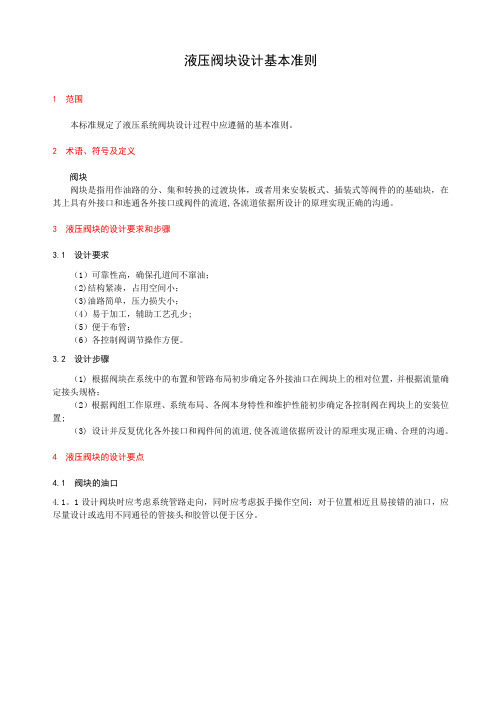
液压阀块设计基本准则1 范围本标准规定了液压系统阀块设计过程中应遵循的基本准则。
2 术语、符号及定义阀块阀块是指用作油路的分、集和转换的过渡块体,或者用来安装板式、插装式等阀件的的基础块,在其上具有外接口和连通各外接口或阀件的流道,各流道依据所设计的原理实现正确的沟通。
3 液压阀块的设计要求和步骤3.1 设计要求(1)可靠性高,确保孔道间不窜油;(2)结构紧凑,占用空间小;(3)油路简单,压力损失小;(4)易于加工,辅助工艺孔少;(5)便于布管;(6)各控制阀调节操作方便。
3.2 设计步骤(1) 根据阀块在系统中的布置和管路布局初步确定各外接油口在阀块上的相对位置,并根据流量确定接头规格;(2)根据阀组工作原理、系统布局、各阀本身特性和维护性能初步确定各控制阀在阀块上的安装位置;(3) 设计并反复优化各外接口和阀件间的流道,使各流道依据所设计的原理实现正确、合理的沟通。
4 液压阀块的设计要点4.1 阀块的油口4.1。
1设计阀块时应考虑系统管路走向,同时应考虑扳手操作空间;对于位置相近且易接错的油口,应尽量设计或选用不同通径的管接头和胶管以便于区分。
图1 SAB熨平板分集流块4。
1.2 阀块上的各油口旁均应标注注油口标识(例如:P、A、T、B、A1、A2、B1、B2、M1、M2……),其中,板式阀安装面的油口标识仅在图纸上体现,而用于与胶(钢)管相连接的外接油口和测压口旁则必须在阀块体上打相应钢印,为保证安装管接头(或法兰)后不将标识覆盖,钢印距离相应油口边缘大于7mm(可在技术要求中注明),具体可见附录A阀块工程图示例。
4。
1.3 阀块上的外接油口、测压口应根据管接头连接尺寸设计,沉孔外径、深度和螺纹深度均应留有合适的余量,避免安装时干涉。
具体可根据管接头螺纹规格由表1确定,并按《路机液压阀块管接头螺纹用沉孔规格系列》对沉孔外径进行圆整.图2 油口尺寸示意图表1 阀块油口设计推荐尺寸管接头螺纹d1管接头止口外径d7油口沉孔外径d4油口沉孔深度a1油口螺纹深度b1形位公差WM10×1 14 ≥15 ≤1 ≥8 0.1 M12×1。
液压阀块设计
液压阀块设计引言液压阀块是液压系统中的重要组成部分,主要用于调控液压系统中的液压流量和压力。
液压阀块的设计必须考虑各种工作条件和要求,以保证系统的稳定性和可靠性。
本文将介绍液压阀块的设计原则、设计流程和注意事项。
设计原则液压阀块的设计需要遵循以下原则:1.功能性:液压阀块的设计必须满足液压系统的功能需求,包括流量控制、压力调节、方向控制等功能。
2.可靠性:液压阀块设计必须考虑到系统的可靠性和安全性。
阀块的结构必须经过充分的强度计算和材料选择,以确保在高压环境下不会发生泄漏和破裂。
3.紧凑性:液压阀块设计应尽可能紧凑,以节约空间和降低系统的重量。
4.维护性:液压阀块的设计应考虑到维护和维修的便捷性。
易于拆卸和更换的设计能够降低维护成本和停机时间。
设计流程液压阀块的设计流程包括以下几个步骤:1.系统分析:首先需要对液压系统进行全面的分析,包括工作流量、工作压力、工作温度等参数的确定。
2.阀块选型:根据系统分析的结果,选择合适的阀块类型和规格。
一般可以选择单头阀块、双头阀块、多头阀块等。
3.阀芯设计:根据系统要求,设计阀芯的结构和尺寸。
阀芯的设计需要考虑流通通道的尺寸和形状,以及密封材料的选择。
4.阀座设计:设计阀座的结构和尺寸,确保阀座与阀芯之间的密封性和动作的准确性。
5.阀体设计:设计阀体的结构和尺寸,考虑液压系统的工作压力和流量,以确保阀体的强度和刚性。
6.材料选择:选择适合的材料制造阀块,考虑到材料的强度、耐腐蚀性和耐磨性等因素。
7.强度计算:进行强度计算,以验证阀块的结构是否满足设计要求。
8.总装与测试:将设计完成的阀芯、阀座和阀体组装在一起,并进行功能测试和密封性测试。
注意事项在液压阀块的设计过程中,需要注意以下几点:1.流通通道设计:流通通道的设计要尽量简洁,以减少液压阀块内的压力损失和能量损耗。
2.密封性设计:阀块的密封性设计要考虑到工作压力和温度,选择适当的密封材料和密封结构。
3.阀芯和阀座的配合:阀芯和阀座之间的配合要具有适当的间隙和精确的制造精度,以确保阀芯的动作灵活和密封性。
液压阀块设计指引和实例
液压阀块设计指引和实例液压阀块是液压系统中重要的组成部分,它用于控制液压系统中流体的流向、压力和流量。
一个好的液压阀块设计能够提高液压系统的性能、可靠性和效率。
下面是液压阀块设计的一些指南和实例:1.确定系统需求:在进行液压阀块设计之前,需要先明确液压系统的工作条件和要求。
包括工作压力、流量、温度、流体种类等参数。
根据系统需求选择适当的阀芯类型和控制方式。
2.选择适当的阀芯类型:液压阀块中最重要的部分就是阀芯。
常用的阀芯类型包括节流阀、换向阀和溢流阀等。
选择适当的阀芯类型要考虑到液压系统的工作条件,如流量要求、压力要求等。
3.安排阀芯布局:在液压阀块中,多个阀芯通常需要同时工作,因此需要合理安排阀芯的布局。
应根据系统需求和流体的流向来确定阀芯的位置和排列方式,以提高液压系统的效率和反应速度。
4.设计合理的通道和管道:液压阀块中的通道和管道连接着各个阀芯和液压元件。
通道的尺寸和形状对系统的性能和响应速度有着重要的影响。
合理的通道和管道设计可以降低系统的压降和流阻,提高液压系统的效率。
5.考虑泄漏和冲击:液压系统中常常会产生泄漏和冲击现象,这会对系统的性能和工作寿命产生负面影响。
在液压阀块设计中,要尽量减少泄漏和冲击,可以通过选择合适的密封材料和减震措施来实现。
6.考虑安全和可靠性:液压系统在工作过程中可能会面临各种风险和故障,如压力过大、温度过高等。
在液压阀块设计中,要考虑这些风险和故障,并采取相应的安全措施和故障保护措施,以确保系统的安全和可靠性。
以双工位带顶针多路阀为例,介绍液压阀块的设计过程和注意事项。
1. 确定系统需求:假设系统工作压力为20MPa,流量为50L/min,流体种类为液压油。
2.选择适当的阀芯类型:由于需要控制多个工位的流向,选择带顶针的多路阀作为阀芯类型。
3.安排阀芯布局:根据系统的工作要求,确定阀芯的位置和排列方式。
假设系统需要4个工位,每个工位需要控制4个液压缸。
因此,需要设计一个包含16个阀芯的阀块。
清洁车液压阀块的设计(2)
清洁车液压阀块的设计(2)清洁车液压阀块的设计(2)2 阀块材料的选取液压阀块材料可选用球墨铸铁、Q235钢、45号钢、铝合金等.球墨铸铁成本低,深孔加工性能好,是中、低压阀块的首选材料口。
钢材作为阀块材料较为普遍,强度较高,可用于中高压场合。
由于铸铁、钢材密度大,对于有重量限制的移动式机械设备是一个缺陷。
超硬铝合金具有强度大、重量轻、易切削、防腐性好等诸多优点,近年来在移动式机械设备中得到了广泛的应用。
沙滩清洁车因作业的地面是松软的沙滩,对重量比较敏感,因此选取密度较低的超硬铝合金6061-16作为阀块材料,其抗拉强度为290 MPa,屈服强度为240 MPa,杨氏弹性模量为69 GPa,泊松比为0.3。
3 相邻油道最小壁厚的计算阀块相邻油道最小壁厚的计算比较复杂,设计时可先按厚壁管道强度理论进行近似计算确定壁厚,设计完成后,再用有限元分析校核强度,当孔的长径比小于8时,最小壁厚不小于3 mm,孔的长径比大于10时,最小壁厚不小于5mm,以防止钻头因偏斜引起的加工误差。
当阀块材料为钢材或铝合金等塑性材料时,按第四强度理论初步确定壁厚:t=p y d/2[σ] (2)式中:t—最小壁厚,单位mm;d—油道孔直径,单位mm;p y—油孔最大试验压力,单位MPa,取Py=(1.5~1.75)p;p—工作压力,单位MPa;[σ]—材料许用应力,单位MPa,[σ]=σp0.2/n,当p y≤17.5 MPa时,n取3.5,当p y≥17.5MPa时,n取3,σp0.2为塑性材料的屈服强度。
沙滩清洁车液压系统工作压力p为16 MPa,选用超硬铝合金6061-T6为阀块材料,根据式(2)计算孔径分别为10、12、14、16mm时的最小壁厚值,数据如表1所示。
表1 阀块油道孔间最小壁厚计算表注:转载请与作者联系授权,作者:广州市新欧机械有限公司黄志坚教授,************。
液压阀块的设计思路、制造、安装与调试
液压阀块的设计思路、制造、安装与调试液压阀块是液压系统的重要组成部分,液压阀块在设计思路、制造、安装和调试的各个阶段对液压系统的总体性能都能产生影响。
文章对液压阀块的设计、制造、安装、调试各个阶段进行了介绍,阐述了各个阶段中应该注意的问题,以及遇到问题的解决措施。
这几个阶段按照相关规定来进行,能有效减少相关问题的产生,保证液压系统正常运行。
标签:液压阀块;设计思路;制造;安装;调试现在液压系统在现代工业中发挥着重要作用,同时对液压系统的各方面性能要求也不断提高。
在液压系统中,液压阀块是重要的组成部分,在液压系统中发挥着关键的作用。
随着现在对液压系统要求的提高,液压阀块的功能性和集成性的难度也不断增加。
液压阀块在设计思路、制造、安装、调试等方面都需要进行有效控制,这样才能保证液压阀块性能的正常发挥,液压系统才能正常运行。
下面是对液压阀块的设计思路、制造、安装、调试的分析。
1 液压阀块的设计液压阀块在设计之前一些准备工作需要做到位。
首先是能够看懂原理图,这是在液压阀块设计之前必须做的一个工作,对原理图清楚之后才能进行设计[1]。
另外是要对液压阀块的大小以及相关元件的分配需要有比较清楚的定位,阀块大小的确定主要依据液压系统的实际空间来确定。
液压阀块在设计时有一些事项需要加以注意。
阀块在设计的过程中液压油路的设计应该遵循简洁的原则,深孔、斜孔和工艺孔应该尽量少用。
阀块孔径尺寸的确定应该与流量相匹配,相通的孔需要有足够的通流面积。
阀块中A口和B口位置的确定在设计的过程中應该根据液压系统的空间位置、油口相接位置和装配方向等因素。
阀块图在绘制的过程中应该和阀块实际尺寸相一致,这样可以更好反映出阀块的实际情况,出错的几率会减少。
表示通道连接的情况时应该用剖视图来表示,设计图的每个面上要标示出装阀的接口的符号。
绘图中集成块的基准的绘制可以采用点坐标形式,这种方法是现在运用较为广泛的一种方法。
在设计的过程中除了阀块设计图之外还应当有独立的快装配图,这样有利于安装和检验。
- 1、下载文档前请自行甄别文档内容的完整性,平台不提供额外的编辑、内容补充、找答案等附加服务。
- 2、"仅部分预览"的文档,不可在线预览部分如存在完整性等问题,可反馈申请退款(可完整预览的文档不适用该条件!)。
- 3、如文档侵犯您的权益,请联系客服反馈,我们会尽快为您处理(人工客服工作时间:9:00-18:30)。
液压阀块设计规范
液压阀块的设计大多属于非标设计,需要根据不同的工况和使用要求进行针对性设计,设计阀块时大致分为以下几步:选材、设计、加工与热处理、去毛刺与清洗、表面防锈处理、试验。
1、选材:
不同的材料决定了不同的压力等级,首先根据使用压力进行合理选材,一般来说遵循以下原则:
工作压力P<时,液压阀块可以采用铸铁HT20一40。
采用铸铁件可以进行大批量铸造,减少工时,提高效率,特别适用于标准化阀块。
≤P<21MPa时,液压阀块可以选用铝合金锻件、20号锻钢或者Q235;低碳钢焊接性能好,特别适合与非标的硬管(使用中很多阀块需要和硬管进行焊接)进行焊接。
P≥21MPa时,液压阀块可以选用35号锻钢。
锻打后直接机加工或者机加工后调质处理HB200-240(一般高压的阀块,往往探伤、机加工与热处理循环进行)。
设计阀块时阀块最初的厚度定为最大通径的5倍,然后根据具体设计逐步才缩小;设计通道时应合理布置孔道,尽量减少深孔、斜孔和工艺孔,先安排大流量通道,最后是先导油通道,各孔道之间的安全壁厚不得小于3~5mm ,还应考虑钻头在允许范围内的偏斜,适当加大相邻孔道的间距;通道内液压油流速不能高于12m/s ,回油通道要比是进油通道大20-40%;阀块进油口,工作口,控制口要加工测压口;各阀口要刻印标号;对于质量较大的阀块必须有起吊螺钉口。
阀体设计的一般规定:
1.阀块体的外形一般为矩形六面体。
2.阀块体材料宜采用35钢锻件或连铸坯件。
3.阀块体的最大边长宜不大于600mm ,所包含的二通插装阀插件数量宜不大于8。
4.当液压回路所含的插件多于8个时,应分解成数个阀块体,各阀块体之间用螺栓相互连接,结合面处的连接孔道用O 型密封圈予以密封,组成整体的阀块组。
连接螺栓的矩形性能应不低于级。
5.设计阀块体的主级孔道时应考虑尽可能减小流阻损失及加工方便。
6.主级孔道的直径按公式(1)估算选取:
max
v 61.4Q D 式中:
D - 孔道直径,mm;
Q - 孔道内可能流过的最大工作流量,L/min;
vmax - 孔道允许的最大工作液流速,m/s 。
一般,对于压力孔道,vmax 不大于6m/s;对于回油孔道,vmax 不大于3m/s 。
按公式(1)估算出的孔道直径应园整至标准的通径值。
7.当主级孔道与多个插件贯通时,为减小贯通处的局部流阻损失,宜采用与插件孔偏贯通的方法(使主级孔道的中心线与插件孔的中心线偏移)。
一般使主级孔道中心线与插件孔孔壁相切。
同时也可以加大孔道通径,加大的通径应不超过GB2877的规定。
8.为改善深孔工艺性,设计时可考虑增大孔径或采用两端钻孔对接的方法。
9.设计时应尽量避免在阀块体内设置复杂连接的控制孔道和三维斜孔,应充分利用控制盖板内的控制孔道,或采用先导控制块等专用的控制孔道连接体。
先导孔道的直径应与GB2877的规定一致。
若因工艺需要而减小先导孔道的直径时,应作验算,确认不至影响对主级阀的控制要求。
10. 应避免采用倾斜孔道。
必须倾斜时,孔道的倾斜角度应不超过35°,并须保证孔口的密封良好。
对主级斜孔,应在有关视图上标注出因斜孔加工而造成的椭园孔口的长轴尺寸。
11. 当较小孔道孔径不大于25mm时,两相邻孔道孔壁之间的距离应不小于5mm;较小孔道孔径大于25mm时,两相邻孔道孔壁之间的距离应不小于10mm。
12. 为避免污染物的沉积,对于相通的孔道,孔深一般应到与之相通的孔道的中心线为止。
13.主级孔道的外接油口一般采用法兰连接。
对于通径为25mm以下的较小油口,也可采用螺纹连接。
先导孔道的外接油口宜采用螺纹连接。
14. 工艺孔道应采用螺塞、法兰等可拆方式封堵,以便孔道的清理、清洗和检查。
螺塞的螺纹应符合GB2878的规定。
在位置不允许时,对直径不大于12mm的孔道,允许采用球涨式堵头封堵。
15.主级孔道和主要的先导孔道上应设置必要的检测口,以便检测液压回路的工作参数。
检测口一般应安装具快速连接功能的测压接头。
16.阀块体的所有外接油口、检测口均应有油口标记,油口标记应与液压原理图上的相应标记一致。
17. 应在阀块体的醒目部位,预留铭牌安装位置。
18.阀块体应有吊装结构,一般采用吊环螺钉。
19.采用锻件毛坯时,应经正火处理以消除残余内应力。
必要时应进行无损探伤以检查其内部质量。
20.棱边倒角2×45°,阀体较小时则倒角×45°。
21.各油道孔口应保持尖边,勿倒角,但应去尽毛刺。
各管接头螺纹孔口倒角深度应不大于螺距的二分之一。
22.去毛刺、飞边,认真清除孔道内切屑、杂质,并清洗干净。
23.在各油口旁打上相应的油口标记钢印,钢印距孔口不小于6mm(以不影响O型密封圈的密封性能为准)。
24. 当阀块体表面采用化学镀镍处理时,镀层厚~。
25.加工完毕后的阀块体应有防锈、防尘等防护措施,表面应封盖,并存放于清洁干燥的场所
阀块设计完成后进行加工,其加工工艺大致如下:
(1)加工前处理。
加工阀块的材料需要保证内部组织致密,不得有夹层、沙眼等缺陷,加工前应对毛坯探伤。
铸铁块和较大的钢材块在加工前应进行时效处理和预处理。
(2)下料。
一般每边至少留2mm以上加工余量。
(3)铣外形。
铣削阀块6面,每边留粗磨量。
(4)粗磨。
粗磨阀块6面,每边留~精磨量,保证每对对应面平行度小于,两相邻面垂直度小于。
(5)划线。
有条件的可在数控钻床上直接用中心钻完成。
(6)钻孔。
各孔表面精糙度为。
(7)精磨。
磨削阀块6面,各表面磨至粗糙度。
阀块加工时必须严格控制形位公差以满足使用要求,形位公差值参考如下:
阀块6个面相互之间的垂直度公差为;相对面的平行度公差为;
各面的平面度公差为;螺纹与其贴合面之间垂直度公差;所有孔与所在端面垂直度的允差为如
3、去毛刺与清洗
为了保证液压系统的清洁度,阀块必须进行去毛刺。
目前很多厂家仍然采用毛刷进行人工去毛刺,也有采用甲烷爆破法去毛刺的。
阀块去毛刺完成后需通过内窥镜检验,以确保毛刺清理完毕。
最后对阀块进行清洗。
清除附着在阀块表面的各种颗粒污染物、腐蚀物、油脂等。
4、表面防锈处理
为了确保阀块在使用中不会过早的生锈,必须进行防锈处理。
阀块的内部油道可采用酸洗磷化,外表面防锈处理工艺主要有发蓝、镀镉、镀锌、镀镍等表面处理。
5、保压试验
根据设计要求对阀块进行保压试验。
不同的系统工作压力,其阀块的安全系数不相同:
工作压力小于16MPa,试验压力为倍
工作压力小于25MPa,试验压力为倍
工作压力小于31MPa,试验压力为倍
试验保压时间为5~10min,各密封面、各接头处不得有泄漏现象。