离心铸造的优势
什么是离心铸造
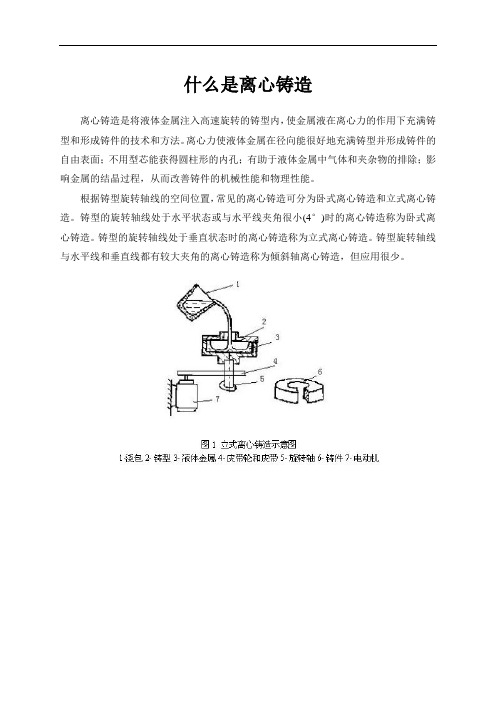
什么是离心铸造离心铸造是将液体金属注入高速旋转的铸型内,使金属液在离心力的作用下充满铸型和形成铸件的技术和方法。
离心力使液体金属在径向能很好地充满铸型并形成铸件的自由表面;不用型芯能获得圆柱形的内孔;有助于液体金属中气体和夹杂物的排除;影响金属的结晶过程,从而改善铸件的机械性能和物理性能。
根据铸型旋转轴线的空间位置,常见的离心铸造可分为卧式离心铸造和立式离心铸造。
铸型的旋转轴线处于水平状态或与水平线夹角很小(4°)时的离心铸造称为卧式离心铸造。
铸型的旋转轴线处于垂直状态时的离心铸造称为立式离心铸造。
铸型旋转轴线与水平线和垂直线都有较大夹角的离心铸造称为倾斜轴离心铸造,但应用很少。
离心铸造最早用于生产铸管,随后这种工艺得到快速发展。
国内外在冶金、矿山、交通、排灌机械、航空、国防、汽车等行业中均采用离心铸造工艺,来生产钢、铁及非铁碳合金铸件。
其中尤以离心铸铁管、内燃机缸套和轴套等铸件的生产最为普遍。
对一些成形刀具和齿轮类铸件,也可以对熔模型壳采用离心力浇注,既能提高铸件的精度,又能提高铸件的机械性能。
离心铸造的优点:1)几乎不存在浇注系统和冒口系统的金属消耗,提高工艺出品率;2)生产中空铸件时可不用型芯,故在生产长管形铸件时可大幅度地改善金属充型能力,降低铸件壁厚对长度或直径的比值,简化套筒和管类铸件的生产过程;3)铸件致密度高,气孔、夹渣等缺陷少,力学性能高;4)便于制造筒、套类复合金属铸件,如钢背铜套、双金属轧辊等;成形铸件时,可借离心力提高金属的充型能力,故可生产薄壁铸件。
离心铸造的缺点:1)用于生产异形铸件时有一定的局限性。
2)铸件内孔直径不准确,内孔表面比较粗糙,质量较差,加工余量大;3)铸件易产生比重偏析,因此不适合于合金易产生比重偏析的铸件(如铅青铜),尤其不适合于铸造杂质比重大于金属液的合金。
离心铸造工艺过程:金属过滤:有些合金液中有较多难于除去的渣滓,可在浇注系统中放各种过滤网清除渣子,如泡沫陶瓷过滤网、玻璃丝过滤网等。
离心铸造工艺
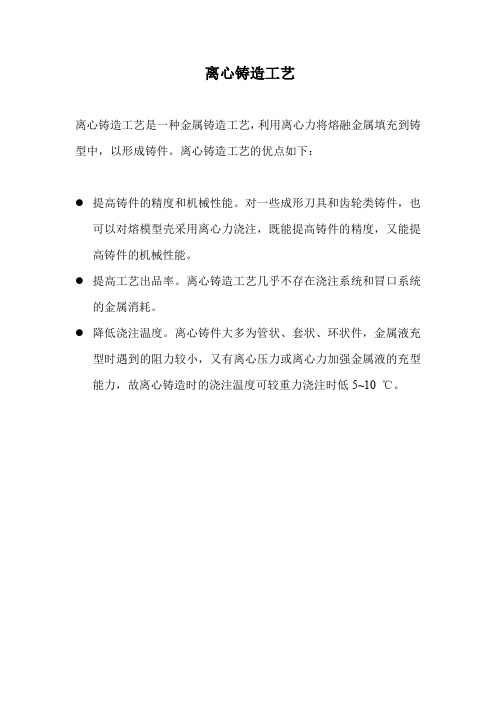
离心铸造工艺
离心铸造工艺是一种金属铸造工艺,利用离心力将熔融金属填充到铸型中,以形成铸件。
离心铸造工艺的优点如下:
●提高铸件的精度和机械性能。
对一些成形刀具和齿轮类铸件,也
可以对熔模型壳采用离心力浇注,既能提高铸件的精度,又能提高铸件的机械性能。
●提高工艺出品率。
离心铸造工艺几乎不存在浇注系统和冒口系统
的金属消耗。
●降低浇注温度。
离心铸件大多为管状、套状、环状件,金属液充
型时遇到的阻力较小,又有离心压力或离心力加强金属液的充型能力,故离心铸造时的浇注温度可较重力浇注时低5~10 ℃。
离心铸造名词解释

离心铸造名词解释
嘿,你知道离心铸造吗?离心铸造啊,就像是一场金属的奇妙舞蹈!想象一下,把液态金属放入一个高速旋转的“舞台”,那场面,哇塞!(就好比把颜料倒入旋转的画板,颜料会均匀地散开)。
在这个过程中,液态金属会在离心力的作用下,紧紧地贴在“舞台”
的内壁上。
这可太神奇了呀!(就像我们跑步时汗水被甩到衣服上贴
住一样)。
离心铸造有好多优点呢!它能让铸件组织致密,质量杠杠的!(这
就好比精心打造的艺术品,精致无比)。
而且它还可以铸造出形状复
杂的铸件,那些奇奇怪怪的形状都不在话下。
(你看那些精美的雕塑,不也是形态各异嘛)。
我记得有一次在工厂里,看到工人们操作离心铸造的过程,那真是
让人惊叹不已。
(哎呀,就像看到了一场精彩绝伦的魔术表演)。
他
们熟练地将金属液倒入旋转的模具中,然后就看着铸件一点点地成型。
“哇,这也太厉害了吧!”我当时就忍不住叫了出来。
旁边的师傅笑着说:“这算啥,离心铸造的本事大着呢!”
离心铸造在很多领域都有重要的应用哦,像汽车制造啦、机械工业
啦等等。
(就像我们生活中离不开水和电一样重要)。
它为我们的生
活带来了很多便利和惊喜。
总之呢,离心铸造就是这样一个神奇又厉害的工艺,它就像是金属世界里的一颗璀璨明星,照亮了我们的生活!。
离心铸造基本知识.

铜合金铸件铸造技术 精品资源共享课程
一、离心铸造方Leabharlann 的发展历史2.离心铸造的重要地位 离心铸造即是传统的、又是一种现代的铸造方法。2011年我国铸件的年
产量在4150万t,而离心铸造生产的铸件,可达到320万t以上,灰铸铁铸管件约 160万t,内燃机缸套80万t,各种轧辊10万t。铸造生产是获得机械产品毛坯的主 要方法之一,是机械制造工业的重要基础,在国民经济中占着相当重要的位置。 在许多机械中,铸件重量占整机重量的比例很高,内燃机80%,拖拉机65%— 80%,液压件、泵类机械50%—60%。
1.发展历史
我国在1368-1399年,就生产了铸管,用在南京武庙闸渠 。 1809年英国人埃尔恰尔特提出了第一个离心铸造法的专利。 1849年英国安德鲁逊克制造了第一台离心铸造机。 1914年巴西人代-拉奥德的水冷金属型和20世纪中球墨铸铁在铸管上的应用,开始了 用离心铸造工艺替代连续铸造工艺、用球墨铸铁替代灰铸铁在生产压力铸管方面的过 渡。 1917年美国姆尔发明砂型离心铸造法。 1951年,球墨铸铁发明后的第三年,就在欧洲首先被采用到铸管上。它跟水冷金属 型方法相结合,加之随后的热处理,给离心铸造带来了蓬勃的发展生机,也给供水管 线带来了革命性的转变。
具有更高的导热能力。在铸造厂为降低成本多使用废电极做铸型, 因为用来专制石墨型的成本很高。选用石墨棒或电极,经机械加工 成形可使其成本大幅下降。石墨型正常的寿命在50~100件,也有少 数情况下超过100件。石墨型耐热性能优良,它的损坏原因是机械强 度和硬度低,在取出凝固后的铸件时引起的磨损是影响其寿命的主 要因素。另外,如果操作者不小心提取铸件,有时会严重损坏铸型 甚至报废,所以工艺规程应规定出必要的操作注意事项。
离心浇铸

离心铸造是将液体金属浇入旋转的铸型中,使液体金属在离心力的作用下充填铸型和凝固形成的一种铸造方法。
为实现上述工艺过程,必须采用离心铸造机创造使铸旋转的条件。
根据铸型旋转轴在空间位置的不同,常用的有立式离心铸造机和卧式离心铸造机两种类型。
立式离心铸造机上的铸型是绕垂直轴旋转的,它主要用来生产高度小于直径的圆环类铸件,有时也可用此种离心铸造机浇注异形铸件。
卧式离心铸造机的铸型是绕水平轴旋转的(图2),它主要用来生产长度大于直径的套类和管类铸件。
由于离心铸造时,液体金属是在旋转情况下充填铸型并进行凝固的,因而离心铸造便具有下述的一些特点:1)液体金属能在铸型中形成中空的圆柱形自由表面,这样便可不用型芯就能铸出中空的铸件,大大简化了套筒,管类铸件的生产过程,使铸造工艺大大简化,生产率高、成本低;2)由于旋转时液体金属所产生的离心力作用,离心铸造工艺可提高金属充镇铸型的能力,因此一些流动性较差的合金和薄壁铸件都可用离心铸造法生产;3)由于离心力的作用,改善了补缩条件,气体和非金属夹杂也易于自液体金属中排出,因此离心铸件的组织较致密,缩孔(缩松)、气孔、夹杂等缺陷较少,力学性能好;4)消除或大大节省浇注系统和冒口方面的金属消耗,金属利用率高;5)离心铸造的铸件易产生偏析,不宜铸造密度偏析倾向大的合金;而且内孔尺寸不精确,内表面粗糙,加工余量大;不适于单件、小批量生产,目前,离心铸造已广泛用于制造铸铁管、气缸套铜套、双金属轴承、特殊的无缝管坯、造纸机滚筒等;6)便于生产双金属铸件,例如钢套镶铜轴承等,其结合面牢固,又节省铜料,降低成本。
离心铸造的第一个专利是在1809年由英国人爱尔恰尔特(Erchardt)提出的,直到二十世纪初期这一方法在生产方面才逐步地被采用。
我国在三十年代也开始利用离心管、筒类铸件如铁管、铜套、缸套、双金属钢背铜套等方面,离心铸造几乎是一种主要的方法;此外在耐热钢辊道、一些特殊钢无缝纲管的毛坯,造纸机干燥滚筒等生产方面,离心铸造法也用得很有成效。
离心铸造机研究报告
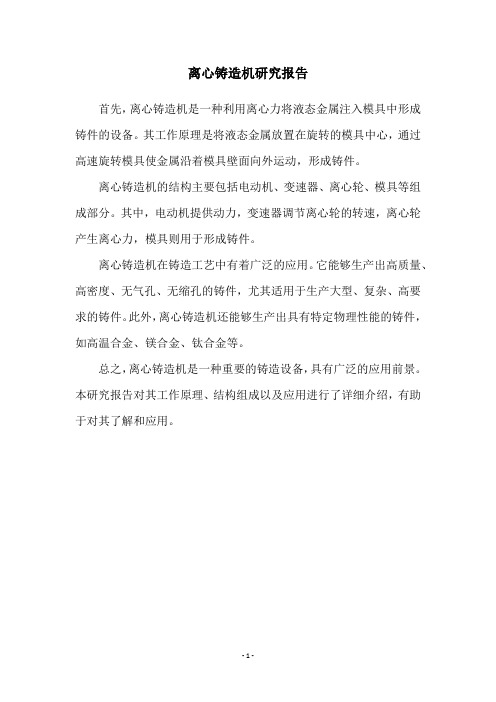
离心铸造机研究报告
首先,离心铸造机是一种利用离心力将液态金属注入模具中形成铸件的设备。
其工作原理是将液态金属放置在旋转的模具中心,通过高速旋转模具使金属沿着模具壁面向外运动,形成铸件。
离心铸造机的结构主要包括电动机、变速器、离心轮、模具等组成部分。
其中,电动机提供动力,变速器调节离心轮的转速,离心轮产生离心力,模具则用于形成铸件。
离心铸造机在铸造工艺中有着广泛的应用。
它能够生产出高质量、高密度、无气孔、无缩孔的铸件,尤其适用于生产大型、复杂、高要求的铸件。
此外,离心铸造机还能够生产出具有特定物理性能的铸件,如高温合金、镁合金、钛合金等。
总之,离心铸造机是一种重要的铸造设备,具有广泛的应用前景。
本研究报告对其工作原理、结构组成以及应用进行了详细介绍,有助于对其了解和应用。
- 1 -。
离心铸造基本知识.
铜合金铸件铸造技术 精品资源共享课程
四、离心铸造工艺的应用范围 从上述离心铸造的优点及局限性可以看出,离心铸造适用于特定
的、大批量生产的铸件。 目前在我国,离心铸造已成为一种应用较广泛的铸造方法,特别
在生产一些管、筒类铸件如铸铁管、铜套、缸套、双金属钢背铜套等 方面,离心铸造是一种主要的方法。此外在耐热钢辊道,一些特殊的 无缝钢管的毛坯,造纸机干燥滚筒等生产方面,离心铸造法很有成效。 几乎一切铸造合金都可用离心铸造法生产铸件,离心铸件的最小内径 为8mm,最大外径可达3m,铸件最大长度达8m,铸件的重量范围从几 千克至十多吨。
具有更高的导热能力。在铸造厂为降低成本多使用废电极做铸型, 因为用来专制石墨型的成本很高。选用石墨棒或电极,经机械加工 成形可使其成本大幅下降。石墨型正常的寿命在50~100件,也有少 数情况下超过100件。石墨型耐热性能优良,它的损坏原因是机械强 度和硬度低,在取出凝固后的铸件时引起的磨损是影响其寿命的主 要因素。另外,如果操作者不小心提取铸件,有时会严重损坏铸型 甚至报废,所以工艺规程应规定出必要的操作注意事项。
铜合金铸件铸造技术 精品资源共享课程
(2)按离心力应用情况的分类法 真正离心铸造:特点是铸件轴线与旋转轴线重合。 半真正离心铸造:特点是铸型形状仍是轴对称的,铸件复杂,铸型 旋转速度低,离心力有助于充型和凝固,不起成形作用; 非真离心铸造:零件形状随意,离心力仅增加金属液凝固时的压力, 铸型转速更低,铸件中心线也不和旋转轴线重合。
?
思考题:管子、活塞环分别可采用哪种 离心铸造方法?
铜合金铸件铸造技术课程组
铜合金铸件铸造技术课程组
④调整金属型的冷却速度,在确定的铸件壁厚范围内,能获得从 外壁到铸件内壁定向凝固的组织。
《离心铸造技术》课件
06 离心铸造技术的未来发展
离心铸造技术的研究方向
1 2 3
新型材料研究
随着新材料的发展,离心铸造技术将更多地应用 于新型材料的制备,如高强度轻质材料、高温合 金等。
工艺参数优化
进一步研究离心铸造过程中的工艺参数,如转速 、浇注温度、模具温度等,以提高铸件的质量和 性能。
智能化与自动化
结合先进的信息技术和自动化技术,实现离心铸 造过程的智能化和自动化,提高生产效率和产品 质量。
在离心铸造过程中,铸型的旋转速度和金属液的温度、成分等都会影响铸件的质 量和性能。
02 离心铸造工艺流程
铸型准备
01
02
03
铸型材料选择
根据铸件材质和尺寸选择 合适的铸型材料,如砂、 粘土、金属等。
铸型制作
根据铸件形状和尺寸制作 铸型,确保铸型结构合理 、易于脱模。
铸型预热
在离心浇注前对铸型进行 预热,以提高金属液的流 动性,减少铸件产生气孔 、缩孔等缺陷。
离心铸造在航空航天领域的应用
航空发动机涡轮叶片
01
离心铸造技术用于生产航空发动机涡轮叶片,能够提高产品的
耐高温性能和抗疲劳性能。
航天器结构件
02
离心铸造技术也应用于航天器结构件的生产,如火箭发动机喷
嘴和卫星支架等。
航空航天紧固件
03
离心铸造技术生产的紧固件具有高强度、高疲劳寿命等特点,
广泛应用于航空航天领域。
离心铸造在其他领域的应用
石油和天然气工业
离心铸造技术用于生产石油和天然气工业中的高 压阀门和管件,能够承受恶劣的工作环境。
船舶工业
离心铸造技术也应用于船舶工业中,如船用发动 机零件和船舶结构件的生产。
离心铸造实验报告
离心铸造实验报告篇一:离心铸造实验离心铸造实验实验目的:1、了解Yo-610立式离心铸造机的工作原理。
2、了解压模机压模工序及全自动力压模机的机械常识。
3、了解硅橡胶模制作工艺。
4、了解铅锡合金的配比及共晶点,各金属的物理性能5、掌握离心铸造的工艺过程,工艺原理,会分析离心力的大小对铸件的影响。
实验原理:离心铸造是将液态金属浇入旋转的铸型中,使之在离心力的作用下,完成充填和凝固成型的一种工艺方法。
主要设备简介:1、Yo-710全自动压模机基本参数:用途:用于橡胶模具的硫化成型。
使用方法:1)将整机放稳于水平地面,不能摇动。
2)接通200V电源。
3)预热设定50-100 C,放模具到压模机内,待预热温度达到,按启动按钮,在按油缸上升,达到一定压力后,自动逃脱。
4)设定加热时间10-20分钟,根据需要设定恒温度数,设定硫化时间,一般为60-90分钟。
5)硫化过程中,压模机会定时上升,下降,属于正常排气,到硫化时间结束后自动关机,压模机自动下降,开始冷却。
2、丫0-610立式半自动离心机基本参数:使用方法:1)将整机放稳于水平地面,不能摇动。
2)接通220V电源,打开主控开关,调好所需时间。
本实验一般设定时间为40-80秒。
3)接通气路,上盖自动打开,调好气压。
本实验设定气压为3-4 kg o 4)在调速面板上调节转动电动机的频率来控制其转速:转速二频率X 36每次调节频率后,要按enter键,用以确认,否则机器不能正常工作5)放置橡胶模于离心盘中心定位。
6)按启动按钮,上盖自动盖下,气缸上顶转动。
7)到设定时间后,上盖自动打开,停止转动。
取模。
实验过程:1、预先压制硅橡胶(耐温500 C)模具(浇道可用刀刻出)。
2、液态金属熔炼:本实验采用锡(熔点232 C)和铅(熔点327C)组成的合金浇注。
其中锡和铅的比例约为6: 4, 所得到的合金熔点约为183 C。
浇注温度控制在300-350 C。
3、调节离心机的参数:转动时间为50秒,气压为3-4 kgo4、在不同的转速(600r、1000r和1400r,对应的频率分别为16.7hz、27.8hz和38.9hz )下浇注,对比铸件的好坏。
特种铸造10第十章_离心铸造
离心力场 离心力: mω2r 重力:mg 重度 m g / V g 有效重度:离心力场中旋转状 态单位体积物质上的离心力。
m r / V r
2 2
ω O M mω2r mg
r
重力系数:G / 2r / g 2r / g 或:
Gg G
•
• • •
(4) 可减少甚至不用冒口系统,降低了 金属消耗。
(5) 对于某些合金(如铅青铜等)容易 产生重度偏析。 (6) 铸件内表面较粗糙,有氧化物和聚 渣产生,且内孔尺寸难以准确控制 (7) 应用面较窄,仅适合于外形简单且 具有旋转轴线的铸件如管、筒、套、辊、轮 等的生产。
离心铸造的特点
1.液体金属能在铸型中形成中空的圆柱形自由表面, 简化了套筒、管类铸件的生产过程。
力场一样,也会受到液体金属的压
力作用,这种压力称为离心压力。
离心压力的大小及其分布情况有其
本身的特点,现介绍如下。
图10-5 卧式离心铸造时离心压力的计算
离心压力
dr m r ddrdz dr 2 dV r ddrdz
y ω
2 2 O dr F r ddrdz 2 2 2 2 dr dr r ddrdz 2 r 2 2 dp 2 dr 2 rdr rddz r pr r 2 pr dp rdr
y
mω2r0cosα x x'
m xdx m ydy 0
2 2
B
x 2 y 2 r02
在卧式离心铸造的旋转铸型中,液体金属的 自由表面是一个绕水平转轴x的圆柱面。
•
图10-5所示为卧式离心铸造时截取液体 横断面的图形。在自由表面任取一质点M,其 质量为m,若不考虑重力场的影响,则作用在 该质点的离心力在x轴方向上的分力为X= mω2r0cosa= mω2x;在y轴方向上的分力为Y= mω2r0sina=mω2y;在旋转轴方向上的分力z= 0。将X、Y、Z分别代入式(10-3),得 mω2x dx+mω2y dy=0 x 2十y2=r02(10-7) (10-6) 将式(10-6)移项积分后,得如下方程式
- 1、下载文档前请自行甄别文档内容的完整性,平台不提供额外的编辑、内容补充、找答案等附加服务。
- 2、"仅部分预览"的文档,不可在线预览部分如存在完整性等问题,可反馈申请退款(可完整预览的文档不适用该条件!)。
- 3、如文档侵犯您的权益,请联系客服反馈,我们会尽快为您处理(人工客服工作时间:9:00-18:30)。
离心铸造技术在铝硅合金结构构件生产中的优势G. Chirita, D. Soares, F.S. Silva*Mechanical Engineering Department, School of Engineering, Minho University, Campus deAzurem, 4800-058 Guimaraes, PortugalReceived 12 June 2006; accepted 12 December 2006Available -online- 28 December 2006文摘本文探讨了利用立式离心铸造工艺生产结构零件相比传统重力铸造法的力学性能优势。
我们对由离心力引发的材料机械性能中最重要的性质进行了分析。
也对离心铸造技术和重力铸造技术所获得的式样的机械性能进行了比较。
研究表明,离心铸造技术较重力铸造技术可以多提高材料强度35%,刚度160%。
弹性模量也多增了18%。
抗疲劳寿命延长了约1.5%,抗疲劳极限提高了45%。
因此,就获得机械性能及抗疲劳性能而言,离心铸造技术比重力铸造技术更有效。
前期效果随浇铸情况而变化,这是依据样品从浇铸地被拿开的相对位置而言的。
与旋转中心(更大的离心力或重力)相距越远,机械性能提高得越好。
于是,机械性能随旋转轴的转动而改变了,材料也就具备了梯度功能。
这种功效在不同部位所需不同组件的生产中可能是有用的。
引擎活塞就是一个潜在的应用示例。
在本文献中,我们也将展示离心铸造技术在这些结构零件生产中是如何有优势的。
@2006 Elsevier Ltd. All rights reserved关键词:离心浇注、铝硅合金、机械的、抗疲劳性质1.简介铝硅铸造合金作为结构材料的使用是基于它们的物理性质(主要受其化学组织影响)和机械性质的(受化学成分及微观结构影响)。
铝合金较高的比抗拉强度受其多元组织微观结构强烈影响。
特殊合金的机械性能有助于零件主要相位的物理性质,提高容积比和改善组织形态。
根据[1]铸造铝合金的抗拉性能和抗断裂性能,半固态A356合金和A357合金相当依赖二次枝臂间距(二次晶壁间距)、镁合金以及尤其是共晶硅和富铁金属间化合物的大小和形状。
所以,铝硅铸造合金的机械性质不仅依赖化学组织成分,而且更重要的是微观结构特征,如枝晶形态、α铝、共晶体硅粒以及其它出现在微观结构中的金属间化合物。
现有不同的方法来控制这些微观结构特征,例如通过引进特殊元素[2,3]来细化晶粒。
然而,提高铝硅铸造合金机械性质最常见的措施是改善浇铸技术[4]。
每种技术都有干扰微观结构和影响机械性能的地方。
传统的离心浇铸工艺主要用于得到圆柱部分。
实际上有两个基本类型的离心浇铸机:卧式,绕水平轴旋转的;立式,绕垂直轴旋转的。
卧式离心浇铸机一般用来做管材,管件,套管,汽缸套(衬层),以及形状简单的圆柱或管状铸件。
立式离心浇铸机的应用范围相对较广:齿轮毛坯、滑轮组、叶轮、电机转子、阀体、插头、轭、支架。
非圆柱形铸件,甚至对称的,可以立式离心铸造法。
离心铸造部分有很大程度上的冶金清理和均匀微观结构,而且它们在轧制的/焊接的或者锻造的部分没有明显的各向异性力学性能[5,6]。
离心浇铸也是一种常见的获取梯度功能材料的方法,主要合成像碳化硅增强的绿基功能梯度材料或纳米材料,这种纳米材料在不同阶段具备高差异性的密度和低溶解度或者有同一合金[2]的不同材料。
可是,还没有研究肯定这个事实,即离心工艺可以成功地用来获得梯度功能材料和具有高溶解度及密度在不同阶段的差异性小的金属材料(合金),如硅铝合金。
本文的的目的是为了强调离心技术可以有效地获取梯度功能材料,而且这些材料和技术,尤其是铝硅合金,可能是一种非常有用的结构零件设计工具。
此外,当前还没有可靠及廉价的能够满足零件的批量生产的梯度功能材料制作方法。
现在的制作方法包括凝固工艺,化学气象沉积法,喷雾雾化沉积法以及粉末冶。
这些也许就是通过离心铸造[7]获得梯度功能材料的最经济最具吸引力的加工路线。
2.试验方法及原材料2.1原材料用于铸造的是一种由如下元素组成的AS12UN铝合金:含铁0.750%,含硅-(11.50-13.00)%,含锌0.20%,含镁-(0.75-1.30)%,含镍(0.80-1.30)%,含铅0.10%,含锡0.05%,含钛0.20%。
2.2方法把原材料在670度高温下熔化然后倒进已预热至130度的永久模具中。
一个高频感应离心浇铸炉(Titancast 700 mP Vac, from Linn High Term, 德国)配备了真空室,用于熔化及浇铸样品。
这个系统把金属液(炉缸)和模具定位在离心臂(见图1b)里绕一个中心轴旋转。
重达约140克的原材料用于每次试验,试验都是在真空条件下进行的。
对于离心铸造,当模具绕浇铸机的中心轴旋转时,熔化的铝液被倒入型腔。
浇铸工艺示意图见图1。
尽管重力浇铸是用了与离心浇铸中相同的感应真空熔化设备,但是在这种情况下,金属溶液是人工倒入模具中(见图1)。
切割三个拉伸试样的铸件来比较铸锭(见图2)在不同地方的铝合金的机械性质。
把经两种加工方法得来的圆形试样进行抗疲劳测试(见图3)。
拉伸试验在一个Dartec拉力试验机里室温下进行的,而抗疲劳试验是在室温下的一个回转弯曲疲劳试验机里进行的,并且是在不同的最大应力水平来获得S-N曲线。
从离心浇铸和重力浇铸的位置2处各取一个微元。
拉伸试验的位置2与抗疲劳试验的位置选取点相符。
二次枝晶间距是通过光学显微镜来测出来的。
3.结果结果显示在图5a-b及图6中。
拉伸试验的结果可以总结如下:●在离心铸造里的断裂强度显示出一个从位置3增加到位置1的趋势。
而在重力铸造中的不同位置的试验并没有本质上的差异(见图5)。
●离心铸造的断裂应变中显示出一个很大的从位置3增加到位置1 的趋势。
而在重力铸造中仍然没有大的变化(见图5b)。
●在离心铸造中的杨氏模量也显示出一个从位置3增加到位置1的趋势。
而在重力铸造依然没有大的变化。
●与重力铸造相比,离心铸造工艺在任何位置的所有机械性质都要好些(见图5a-b及图6)。
●在位置1的初步差异达到断裂强度提高约35%,断裂应变提高约160%,杨氏模量提高约18%。
●在所有负荷水平下,离心铸造试样比重力试样有一个叫较长的疲劳寿命(见图7)。
两种铸造技术的3个不同位置的二次枝晶间距如图8所示。
二次枝晶间距的结果可以总结如下:●离心铸造的二次枝晶间距比重力铸造的低。
●在两种铸造技术里二次枝晶间距都从位置1增加到位置3.4.讨论从结果中我们可以很清楚的知道离心铸造技术大幅度的提高了金属的机械性能及疲劳性能。
它们的提高是经过整个铸造过程而不仅仅是某一个方面的观察核实的,这种核实是很重要的。
对于金属性能的提高的绝对价值同样是很重要的,因为这给予了离心铸造技术一个很重要位置去替代传统的重力铸造技术。
事实上,当机械性能需要提高时,其它技术就被运用了以及最常见的就是挤压铸造法。
在文献[8]中可以得知当用挤压铸造法来代替重力铸造时,对于锌铝合金,屈服极限提高了约11.7140%,这取决于合金,它的疲劳极限提高了约8-40%。
在另一项研究中[9],与重力铸造相比,在铝硅合金(AA356)里显示出挤压铸造法将其抗裂强度提高了15%,抗裂应变提高了720%。
在本文的研究中,通过离心工艺,铸件一端的抗拉强度提高了35%,另一端提高了28%。
断裂应变提高了约160%,疲劳极限提高了45%(在位置2处)。
在位置1,差异性更大(见如下解释)。
就疲劳寿命而言,S-N曲线及主疲劳极限σw,有三个基本理论[10]。
第一个也很可能是最常用的一个,联系着材料的疲劳极限σw与静强度极限σu。
第二个理论使材料的疲劳极限与维氏硬度相互关联。
第三个联系疲劳极限与材料上的气孔、杂质或是一些脆弱相的大小。
对于铝合金,这样的三个理论使强度极限与气孔的大小相关联,而对于某些合金,它们的强度极限是与硅粒子大小相关的。
理论1:σw=0.5σu ;理论2:σw=1.6H V+0.1H v;理论3:σw=(√area);在本文有关合金的研究中,我们很清楚的知道疲劳极限σw与强度极限σu有很好的相关性(见图9)。
拉伸试验的价值就在于对位置2处的分析,因为它选择的这个位置与铸件做疲劳测试的试样上的选取点是相同的。
基于这种相关性以及由于与重力铸造相比,静力拉伸的结果使离心铸造后的铸件上的每个位置的性能得到改善,我们就有理由希望离心铸件上的所有地方的疲劳性能比重力铸件上的要好些。
这很明显的证明了铸件的一个方面,即它的疲劳寿命提高了约300%,疲劳极限提高了大约50%。
如果与其它铸造技术相比,在文献[10]里的铝-7硅-0.3镁-锑6的合金的铸造中我们可以看出,与重力铸造比,挤压铸造法多提高疲劳极限约18%。
在本文的研究中,离心技术促进疲劳极限提高了45%之多,如先前所见(见图7)。
尽管比较不同的铝合金不可能,因为每一种铝合金对每一种铸造技术有不同的敏感性,但是我们很清楚的是因离心浇铸而带来的金属性能的提高是事实,并且离心铸造技术有可能被选来替代传统的重力铸造,至少在一些铝合金的铸造中时可行的。
写本文的目的不是为了得到离心铸造技术在微观结构以及合金的机械性能上的影响的一个定量解释。
据对图4上的微元的微观组织的观察显示,离心铸造和重力铸造在各个阶段(枝晶阶段,共硅金阶段以及金属间化合物阶段)有差异。
可是,首选,金属相数与机械性能没有确切的相关性。
其次,对于因离心力的影响导致微观组织的改变还没有一个好的解释。
一些研究表明,在枝晶叉间隔(简称DAS)与强度极限[2,3,12]之间以及枝晶叉间隔与疲劳极限之间存在某种相关性.其它的研究[13]则表明,共金硅、金属间化合物以及硅相形状之间也存在一种关联。
然而,初看二次枝臂间距及拉伸试验结果,它显示出二次枝臂间距与断裂强度和断裂应变之间存在明显的关联。
当二次枝臂间距增加时,断裂强度和断裂应变也都跟着增加,这已经被普遍接受。
观察图8可知,离心铸造技术的二次枝臂间距比重力铸造技术的低(这意味着更好的断裂强度和应变)。
此外,断裂强度和应变都从位置3处增加到位置1处,同时二次枝臂间距以相同的幅度减少。
因此,二次枝臂间距似乎与机械性能之间有很好的相关性。
然而,为了深入了解铝合金里的所呈现的机械性能和相数之间的关系,我们还需要做进一步的研究。
对于离心现象的理解,本文的作者正在对微观组织上被测试的不同变量的影响进行一项更宽的研究,即:—浇铸过程中的模具上的不同点的温度曲线的测量所显示的流体动力学行为。
—通过有限元方法进行流体动力学分析。
此外,微观组织的机械性能的影响正通过如下方法进行研究:—铸造过程中的化学分析。
—铸件离心力方向上的不同阶段的定量金相分析。