多路换向阀尺寸设计计算
多路换向阀 结构原理
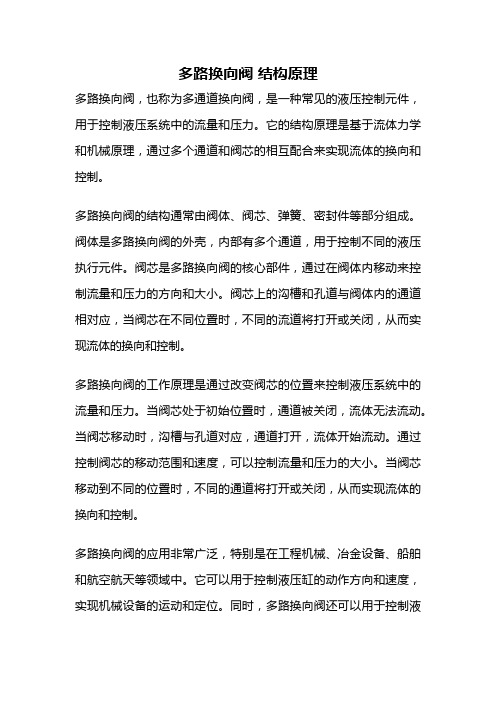
多路换向阀结构原理
多路换向阀,也称为多通道换向阀,是一种常见的液压控制元件,用于控制液压系统中的流量和压力。
它的结构原理是基于流体力学和机械原理,通过多个通道和阀芯的相互配合来实现流体的换向和控制。
多路换向阀的结构通常由阀体、阀芯、弹簧、密封件等部分组成。
阀体是多路换向阀的外壳,内部有多个通道,用于控制不同的液压执行元件。
阀芯是多路换向阀的核心部件,通过在阀体内移动来控制流量和压力的方向和大小。
阀芯上的沟槽和孔道与阀体内的通道相对应,当阀芯在不同位置时,不同的流道将打开或关闭,从而实现流体的换向和控制。
多路换向阀的工作原理是通过改变阀芯的位置来控制液压系统中的流量和压力。
当阀芯处于初始位置时,通道被关闭,流体无法流动。
当阀芯移动时,沟槽与孔道对应,通道打开,流体开始流动。
通过控制阀芯的移动范围和速度,可以控制流量和压力的大小。
当阀芯移动到不同的位置时,不同的通道将打开或关闭,从而实现流体的换向和控制。
多路换向阀的应用非常广泛,特别是在工程机械、冶金设备、船舶和航空航天等领域中。
它可以用于控制液压缸的动作方向和速度,实现机械设备的运动和定位。
同时,多路换向阀还可以用于控制液
压系统中的流量分配和压力调节,确保系统的稳定和安全运行。
多路换向阀是一种重要的液压控制元件,通过多个通道和阀芯的相互配合,实现流体的换向和控制。
它的结构原理基于流体力学和机械原理,通过改变阀芯的位置来控制液压系统中的流量和压力。
多路换向阀在工程机械、冶金设备、船舶和航空航天等领域中有着广泛的应用,可以实现机械设备的运动和定位,同时确保液压系统的稳定和安全运行。
4通3位换向阀 参数

4通3位换向阀参数
摘要:
1.换向阀的概述
2.4 通3 位换向阀的含义
3.4 通3 位换向阀的主要参数
4.4 通3 位换向阀的应用领域
正文:
换向阀是一种流体控制元件,主要用于改变流体的流向,以实现对流体输送系统的控制。
在众多的换向阀类型中,4 通3 位换向阀是一种常见的换向阀,广泛应用于各种流体输送系统中。
4 通3 位换向阀,顾名思义,是指具有四个出口和三个工作位置的换向阀。
其中,四个出口分别表示换向阀有四个流出口,三个工作位置则表示换向阀在工作时可以处于三个不同的状态。
这种结构的换向阀可以实现多种流向的切换,以满足不同工作场合的需求。
4 通3 位换向阀的主要参数包括以下几个方面:
1.公称压力:指换向阀在正常工作条件下所能承受的最大压力。
选用换向阀时,应确保其公称压力大于或等于流体输送系统的工作压力。
2.公称通径:表示换向阀的进出口尺寸,通常用来描述换向阀的流通能力。
选用换向阀时,应根据流体输送系统的流量要求选择合适的公称通径。
3.工作温度:指换向阀在正常工作条件下所能承受的温度范围。
选用换向阀时,应确保其工作温度范围与流体输送系统的工作温度相匹配。
4.驱动方式:4 通3 位换向阀可以采用手动、电动、气动等多种驱动方
式。
选用时,需根据实际应用场景选择合适的驱动方式。
4 通3 位换向阀广泛应用于各种流体输送系统中,如液压系统、气动系统等。
多路换向阀节流槽的等效阀口通流面积研究

多路换向阀节流槽的等效阀口通流面积研究多路换向阀是一种常用的液压元件,广泛应用于工程机械、农业机械及工业自动化设备等领域。
在多路换向阀中,节流槽是起到控制液压油流的作用,其等效阀口通流面积直接影响着阀的性能和稳定性。
对多路换向阀节流槽的等效阀口通流面积进行研究具有重要的理论意义和实际价值。
1. 多路换向阀的节流槽结构及工作原理多路换向阀是一种控制液压系统中液压油流方向的元件,通过改变阀芯的位置来实现液压油的流向切换。
而阀芯上的节流槽则是通过改变其位置和尺寸来控制液压油的流量大小,从而实现对液压系统的流量控制。
一般来说,多路换向阀的节流槽可以分为直通式和弯管式两种结构。
直通式节流槽是将一个直通的细小孔道作为节流口,通过改变阀芯的位置来控制孔道的开合程度,从而实现对液压油流量的控制。
而弯管式节流槽则是将一个细长的弯曲管道作为节流口,通过改变管道的弯曲程度来控制液压油的流量大小。
无论是直通式还是弯管式,都是通过改变节流口的尺寸和位置来实现对液压油流量的控制,其工作原理是相似的。
对多路换向阀节流槽的等效阀口通流面积进行研究,可以为多路换向阀的设计和优化提供理论依据。
2. 多路换向阀节流槽等效阀口通流面积的计算方法多路换向阀节流槽的等效阀口通流面积是指一个与其结构形状相同的标准圆孔的通流面积,通过等效阀口通流面积的计算可以得到多路换向阀的实际通流能力。
对于直通式节流槽,其等效阀口通流面积的计算方法可以通过理论公式来进行计算。
一般而言,可以通过流量系数、孔径等参数来计算直通式节流槽的等效阀口通流面积。
而对于弯管式节流槽,其等效阀口通流面积的计算方法则需要考虑到管道曲率、长度等因素,通常需要通过数值模拟或实验测试来获取。
3. 多路换向阀节流槽等效阀口通流面积的影响因素多路换向阀节流槽的等效阀口通流面积受多种因素的影响,主要包括节流孔径、节流长度、节流形状、液压油的流动性质等因素。
节流孔径是影响等效阀口通流面积的重要因素之一。
SX12多路阀

功能说明,剖视图
� � �
�
�
� �
�
��
�
�
�
�
1 2 3 4 5 6
阀体 阀芯 负载保持阀 压力补偿器 二次安全阀 堵头 制系统内的最高压力LS溢流阀集成。 每个SX型换向阀联由 阀体(1)、整体阀芯(2)、两个负载保持单向阀(3)、一个压力补 偿器(4)、插装组件或堵头(6)组成。插装组件可以是二次溢流 阀带补油阀功能总成和仅补油功能的单向阀。 尾联仅一个固定孔。
�
� �
�
��
�
�
�
RC 64 128/06.06 | 型号SX 12
行走机械液压
| 博世力士乐
/16
技术参数(若使用时超出了规定的参数,请与公司咨询!)
概述 结构 说明 型号 安装位置 油口 公称通径 液压参数 最大允许流量 进油口P 工作油口A, B 泄漏量(在100 bar时,36mm2/s) 每个油口的最高工作压力 P, M, LS A, B T 每个油口的最高控制压力 a, b bar 35 我们要求使用6到25 bar的控制曲线,并确保进油压力(最 小30巴) 液压油液 1)适合于丁腈橡胶密封 液压油温度范围 粘度范围 油液允许的污染等级 °C mm2/s 矿物油(HL,HLP),按DIN 51 524 1) 按 VDMA 24 568 的 HEES 油液以及按力士乐样本RE 90 221的油液:请向我公司咨询。 -20 to +80(如果温度更高,请咨询我们) 10 到 380 按NAS 1638的9级以上。因此我们要求使用最低过滤精度 ß10 ≥75的过滤器 bar bar bar 250 300 20 L/min L/min cm3/mn 120 70 15 最大值 法兰连接(最多10片换向阀联) 与压力和供油流量无关地分配各联所需流量。 SX 12 任意 螺纹连接 12
阀门设计自动计算公式

阀杆台肩与止推垫间的摩擦力矩
MMJ
MMJ=∏*64*f*(DT+df)2*P
f:摩擦系数
DT:台肩外径或止推垫外径
按材料同前面规定选取 选二者中小者(mm)
18011.04 ~0.472来自96.80.05 45
设计给定
4.1.2固定球阀 总转矩计算
MF MQZ MQZ MQZ1 MQZ1
MQZ2 MQZ2
dF:阀杆直径
P:计算压力
f= 设计给定 设计给定 设计给定 设计给定
0.05 10 5 40 1.0
(2)对橡胶O型 圈
M d FT=1/2*∏* F2*Z*(0.33+0.92*f0*d0*P)
Z:O型圈个数
设计给定
f0:橡胶对阀杆的摩擦系数
f0=
0.3
d0:O型圈的横截面直径
设计给定 4
MMJ
D=
160
2.1 壁厚的确定
壁厚计算公式:SB=S'B+C S'B:计算厚度,C:腐蚀余量
S’B S’B
P DN [σL] C SB
计算厚度 计算压力
内径 材料许用拉应力
腐烂余量 实际厚度
S’B=1.5P*Dn/2[σL]-P
1.685393
1.0
设计给定
100
设计给定
45
设计手册表3-3
5
设计给定
6.685393
3.1 球体与阀座之 间比压的计算
球体与阀座之间比压的计算
应该满足:qMF<q<[q]
qMF
qMF=1.2P
qMF=
1.2
P
计算压力
1.0
qMF
液压管路规格尺寸连接明细(铲运机)

H90º13*Ⅱ——1300
回油块——油箱
H90º13*Ⅱ——1200
双联泵——中间调节阀杆
行驶系统
H13*Ⅱ——630
转向油缸接头——转向油缸
转向系统
H90º13*Ⅱ——300
卷缆阀——精滤油器
卷缆系统
H90º8*Ⅱ——2550
蓄能器——脚踏式比例换向阀
制动系统
H90º8*Ⅱ——2450
蓄能器——脚踏式比例换向阀
滤油器—散热器
行驶系统
H90º19*Ⅱ——1200
主控阀——滤油器
行驶系统
H90º19*Ⅱ——1400
多路换向阀——举升油缸
工作系统
H90º19*Ⅱ——1250
多路换向阀——翻转油缸
工作系统
H90ºH90º19*Ⅱ——900 V 270º
双联泵——滤油器
行驶系统
H90º19*Ⅱ——700
滤油器——主控阀
制动阀——回油块
H90º8*Ⅱ——850
脚踏式比例换向阀——回油块
H90º6*Ⅱ——2200
脚踏式比例换向阀——轮边制动器接头
制动系统
H90º6*Ⅱ——1600
脚踏式比例换向阀——轮边制动器接头
制动系统
H90º6*Ⅱ——750
轮边制动器接头——轮边制动器
制动系统
H6*Ⅱ——450
轮边制动器接头——轮边制动器
制动系统
液压管路规格尺寸连接位置明细表
行驶系统
H16*Ⅱ——1200
双联泵——滤油器
制动系统
H90º16*Ⅱ——320
滤油器——充液阀
制动系统
H90º13*Ⅰ——3400
精滤油器——油箱
整体式多路换向阀阀芯结构研究

整体式多路换向阀阀芯结构研究邹雨霖; 张鹏; 葛菲; 李艳阳【期刊名称】《《能源与环保》》【年(卷),期】2018(040)010【总页数】5页(P170-173)【关键词】阀芯; 节流槽; 均压槽; 换向阀; 微小结构【作者】邹雨霖; 张鹏; 葛菲; 李艳阳【作者单位】河南永华能源有限公司嵩山煤矿河南偃师471924【正文语种】中文【中图分类】TH137.50 引言大型工程机械无论是民用还是军用中的液压系统中都采用有多路换向阀。
换向阀性能的好坏直接影响到液压系统的稳定性。
阀芯上阀肩与阀体之间的配合,阀芯上节流槽、均压槽的设计等直接影响整个阀的使用性能和使用寿命[1-3]。
矿用装岩机中液压换向阀系统由于其结构简单、布局灵活、元件之间自润滑性较好,便于和其他的传动方式联合使用,在矿用装岩机中被广泛使用[4-5]。
一般阀芯液压系统都为封闭式管路系统,具有故障隐蔽、处理困难的缺点,且机械换向阀阀芯在经过加工的过程中,因加工误差带有朝向高压腔的倒锥[6-8],或在阀芯的动作期间局部凸起或残留毛刺致使换向阀阀芯出现液压卡紧现象[9-11];至于手动换向阀,由于其结构上阀芯、阀孔都比较长,存在有直线度误差,且残余应力存在,换向阀阀芯在使用中经常发生弯曲,产生机械式卡紧[12-15]。
本文以矿用装岩机机械液压系统整体式多路换向阀中回转联滑阀阀芯的结构为研究对象,剖解整体式多路换向阀阀芯的结构,采取对阀芯节流口的面积进行数学分析、减小阀芯所受径向力的方法对阀芯结构、节流槽、均压槽进行专项研究来解决以上现象。
此联换向阀的使用要求为压力35 MPa,标准流量为400 L/min,且应具有流量微动特性和启动平稳性等。
1 阀芯结构换向阀是利用阀芯与阀体间相对位置的不同,来变换阀体上各主油口的通断关系,实现各油路连通、切断或改变液流方向的阀。
换向性能的好坏,直接影响液压系统工作性能。
对换向阀性能的主要要求有:液流通过换向阀时压力损失要小;液流在各关闭油口之间的缝隙泄漏量小,换向可靠,动作灵敏;换向平稳无冲击等[16-20]。
多路换向阀参数
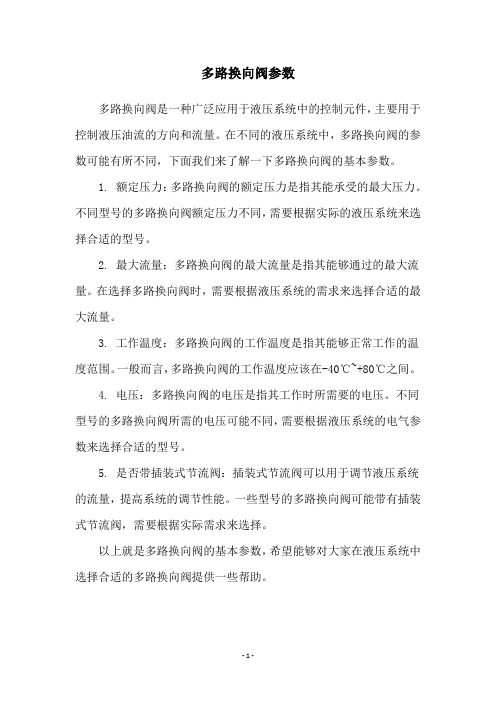
多路换向阀参数
多路换向阀是一种广泛应用于液压系统中的控制元件,主要用于控制液压油流的方向和流量。
在不同的液压系统中,多路换向阀的参数可能有所不同,下面我们来了解一下多路换向阀的基本参数。
1. 额定压力:多路换向阀的额定压力是指其能承受的最大压力。
不同型号的多路换向阀额定压力不同,需要根据实际的液压系统来选择合适的型号。
2. 最大流量:多路换向阀的最大流量是指其能够通过的最大流量。
在选择多路换向阀时,需要根据液压系统的需求来选择合适的最大流量。
3. 工作温度:多路换向阀的工作温度是指其能够正常工作的温度范围。
一般而言,多路换向阀的工作温度应该在-40℃~+80℃之间。
4. 电压:多路换向阀的电压是指其工作时所需要的电压。
不同型号的多路换向阀所需的电压可能不同,需要根据液压系统的电气参数来选择合适的型号。
5. 是否带插装式节流阀:插装式节流阀可以用于调节液压系统的流量,提高系统的调节性能。
一些型号的多路换向阀可能带有插装式节流阀,需要根据实际需求来选择。
以上就是多路换向阀的基本参数,希望能够对大家在液压系统中选择合适的多路换向阀提供一些帮助。
- 1 -。
- 1、下载文档前请自行甄别文档内容的完整性,平台不提供额外的编辑、内容补充、找答案等附加服务。
- 2、"仅部分预览"的文档,不可在线预览部分如存在完整性等问题,可反馈申请退款(可完整预览的文档不适用该条件!)。
- 3、如文档侵犯您的权益,请联系客服反馈,我们会尽快为您处理(人工客服工作时间:9:00-18:30)。
多路换向阀尺寸设计计算预设主阀的额定流量:Q =80L/min 预设主阀的额定压力:P S =31.4Mpa为了使换向阀的压力损失尽量小,应使得流道上任意端面的流速V 限制在2~6m/s 以内,高压时最大亦不应超过8m/s ,而且应使整个流道上的过流断面积只在很小范围内变化,以减小在过流断面积剧烈变化处附加压力损失。
故以下取速度V =6m/s 。
1 多路换向阀主要尺寸的确定1.1、进出油口的直径d从在进出油口的面积可以顺利通过额定流量考虑:Q V )d(≥⋅⋅π22即VQd ⋅π⋅≥4 (1-1) 式中d ——进出油口的直径;V ——进出油口直径d 处油液流速; Q ——主阀的额定流量;1.2 阀芯台肩大直径D 和小直径d 1,阀芯中间孔直径d 0 (1)、理论取值从强度考虑:d 1≥ 0.5×D ;从阀芯与阀体间环形通道流可以顺利通过额定流量考虑:0.25×π×(D 2-d 12)×V ≥ Q ; 由上两式解得:d D d VQ ⋅≤≤+⋅π⋅2421 (1-2) VQD d D 1⋅π⋅-≤≤⋅4212 (1-3) 式中D ——阀芯台肩大直径;d 1——阀芯台肩小直径;式(1-2)、(1-3)两式中对于阀芯无中间孔时常取:d 1=0.5×D (1-4) 以上计算所得的D 、d 1、都要圆整为标准值。
(2)、经验取值为使得阀芯中间孔壁厚面积42021d d ⋅-⋅ππ、阀杆外环形面积4212d D ⋅-⋅ππ、阀进出油口面积42d ⋅π相当。
当阀芯无中心孔时:取D =1.4×d ;d 1=d ; (1-5) 当阀芯有中心孔时:取D =1.7×d ;d 1=1.4×d ;d 0=d ; (1-6) 式中d 0——阀芯中间孔直径;以上计算所得的D 、d 1、d 0都要圆整为标准值。
1.3、有效封油长度l f 和封油长度L f 及间隙δ的确定 (1)、按照理论选取上述参数l f 、L f 、δ从泄漏量需要小于允许的最大泄漏量考虑:q ≤[q ] (1-7)带偏心圆环缝隙泄漏量公式为:)5.11(12223δμδπe l P D q f ⋅+⋅⋅⋅⋅⋅= (1-8)有效封油长度与封油长度的关系为:l f =L f -Z×b , (1-9)式中:D ——阀芯台肩大径;P ——缝隙前后压差; δ——单边间隙; μ——为油液黏度; e ——为偏心距离; Z ——均压槽个数; b ——均压槽宽度; [q ]——最大内泄漏允许值;结合目前加工工艺水平,设计时常定为[q ]=0.01Q 。
考虑当完全偏心时即e/δ=1此时内泄漏量最大。
由上式(1-7)、(1-8)、(1-9)解得:QP D l f ⋅⋅⋅⋅⋅⋅⋅≥μδπ01.0125.23(1-10)当完全偏心时,由式(1-9)得泄漏量与间隙成三次方的关系,为了减小泄漏量设计时取:δ=0.0035~0.01mm (1-11) (2)、按照经验选取有效封油长度l f表1-1 工作压力与封油长度推荐值1.4、沉割槽直径D 1及阀体沉割槽间距b阀体沉割槽直径D 1一般按下式计算:D 1=D +(5mm ~8mm )或D 1=(1.4~1.5)×D (1-12)、(1-13) 沉割槽间隔尺寸b ,一般b 不小于5~6 mm 或b =(2~3)×L f (1-14)2 多路阀铲斗联主要尺寸的确定2.1进出油口的直径d由式V Q d ⋅⋅≥π4取Q =80L/min ,V =6m/s 解得m VQd 016821.04=⋅⋅≥π 即进出油口直径d≥17mm 。
该联实际出油口直径选择了25mm ,满足要求。
2.2 阀芯台肩大直径D 和小直径d 1(1)、按式理论公式(1-2)、(1-3)计算上述参数当取d 1=0.5×D ,V =6m/s 时:解得m VQD 019423.0316=⋅⋅⋅≥π此时d 1≥0.009712m圆整后得D ≥20mm ,d 1≥10mm 。
该联实际情况下D =28mm ,d 1=18mm 满足要求。
当取D =28mm 时:带入式(1-3)中得14mm ≤d 1≤22.384mm ,圆整后得14mm ≤d 1≤22mm 。
该联实际情况下取d 1=18mm 满足要求。
当取d 1=18mm 时,带入式(1-2)中得25mm ≤D ≤36mm ,该联实际情况下取D =28mm 满足要求。
(2)、按经验公式(1-5)计算上述参数当取进出油口直径d=17mm 时带入式(1-5)得D =23.8mm ,d 1=17mm 。
当取进出油口直径d=25mm 时带入式(1-5)得D =35mm ,d 1=25mm 。
可见按式经验公式计算出来的阀芯台肩大、小径与实际有一定的差别。
2.3 有效封油长度l f 和封油长度L f ,及间隙δ的确定铲斗联阀芯处于中位时,选取间隙 δ=0.01mm ,考虑完全偏心时e/δ=1,取其运动黏度 μ=0.28448Kg/ms ,缝隙两端压差P =31.4Mpa ,阀芯台肩大直径D =28mm ,额定流量Q =80L/min 。
模型其均压槽个数Z =2,均压槽宽度b =0.4mm 。
将上列参数带入式(1-9)、(1-10)解得:mm .Q.P D .l f 517071*********=⋅μ⋅⋅δ⋅⋅⋅π⋅≥(1) mm .b Z l L f f 322≈⋅+≥如果按照经验选取则L f 应该在5mm 左右,此时l f =4.2mm 。
实际情况下铲斗联P →A 阀口、P →B 阀口处缝隙的封油长度L f 分别选取了4.5mm 、3.5mm 对应的l f 分别为3.7mm 、2.7mm ,其满足理论计算的范围。
2.4 沉割槽直径D1及阀体沉割槽间距b按照式(1-12)或(1-13)计算沉割槽的直径D1,取阀芯台肩大直径D=28mm,得:33mm≤D1≤36mm或39.2mm≤D1≤42mm合并得33mm≤D1≤42mm。
按照式(1-14)计算沉割槽间隔尺寸b,取L f=4.5mm,解得9mm≤b≤1.3.5mm。
测量多路阀铲斗联得沉割槽直径及阀体沉割槽间距参数:P口处沉割槽直径为40mm,A、B口沉割槽直径均为36mm。
A口与T口间的沉割槽间隔尺寸为12mm,P口与A口间及P口与A口间的沉割槽间隔尺寸均为11mm,B口与T 口间的沉割槽间隔尺寸为12.5mm。
这些尺寸都符合上列所求解的范围。
(其中P 为进油口,T为回油口,A、B为工作油口。
)3 多路阀其它联主要尺寸的确定:3.1、进出油口的直径d表3-1 进出油口的直径d单位(mm)3.2、阀芯台肩大直径D和小直径d1,阀芯中间孔直径d0表3-2 阀芯台肩大直径D和小直径d1,阀芯中间孔直径d0 单位(mm)备注:其中D'、d1'是取d1=0.5×D所求出的D和d1值,D''表示取d1为实际值所求出的D值;d1"表示取D为实际值所求出的d1值。
3.3、有效封油长度l f 和封油长度L f,及间隙δ的确定表3-3 效封油长度l f 和封油长度L f单位(mm)备注:以上参数均为以额定流量为80L/min,额的压力31.4Mpa,缝隙间隙取0.01mm求得。
其中封油长度L f的计算值和经验值可以根据l f的计算值和经验值按式(1-9)、(1-10)计算。
3.4、沉割槽直径D1及阀体沉割槽间距b表3-4 沉割槽直径D1及阀体沉割槽间距b单位(mm)备注:上述≈表示该处的沉割槽不是标准的圆形其,沉割槽直径D1用其等效水利直径代替,其中动臂2联结构与其它联不一致这里未给出。
4 换向阀换向可靠性分析及操作力计算换向阀的可靠性主要包括:1、换向信号作用下,阀芯能灵敏地动作到 指定位置。
2、在没有换向信号时,阀芯在弹簧力的作用下能自动复位到原始位置。
阀芯换向时:阀芯换向时阀芯受到摩擦阻力F m ,稳态液动力F W ,弹簧力P t ,阀芯两端压差引起的轴向力F Z 。
此处忽略了惯性力,如果换向阀高频连续换向,则惯性力不可忽略。
为满足换向可靠性即需满足F Z ≥F m +P t ±F W ;阀芯未换向时:阀芯换向时阀芯受到摩擦阻力F m ,稳态液动力F W ,弹簧力P t ,阀芯两端回油压差引起的轴向力F Z '。
为计算简便此处忽略F Z ',为满足复位功能P t ≥ F m ± F W 。
1、摩擦阻力F m换向阀的摩擦阻力包括纯牛顿流体剪切力F mJ ,液压卡紧力所引起的摩擦力F mK ',推杆与弹簧座及套筒密封表面的摩擦力F mf 。
(1)、牛顿流体剪切力F mJ由牛顿内摩擦定律:A vF mJ⋅⋅=δμ (4-1) 式中:μ—油液的运动黏度;v —阀芯的运动速度; δ—单边缝隙;A —阀芯与阀套接触的面积,A =π×D ×L -A (x );其中L 为阀芯与阀体接触的长度(减去所有均压槽宽度的总和),A (x )为该接触长度下所有节流槽与阀体接触的上表面面积总和。
由于A(x)相比A 很小可以忽略不计。
(2)、液压卡紧力所引起的摩擦力F mK '由于阀芯与阀体不可能是完全精确的圆柱形,径向间隙会存在杂质且径向间隙不处处相等,所以不可避免的会出现液压卡紧力。
⎥⎥⎦⎤⎢⎢⎣⎡-⋅-+∆⋅+∆⋅⋅-⋅⋅=14)2(24)(2221e t teP P L D F i mKπ (4-2) mKmK F f F ⋅='(4-3) 式中:D —滑阀直径;L i —滑阀长度; t —滑阀大小头半径差,e —滑阀偏心距;Δ—滑阀偏心距e =0时大端径向间隙; P 1、P 2—滑阀两端的油压;f —摩擦系数,对于矿物油其起到润滑作用,一般取f=0.04~0.08。
令∆=e 得:])/()/(4)/(2[][4)(221∆+∆⋅∆+⋅∆⋅=-⋅t t t t P P L D F i mKπ(4-4) 对式(4-4)左边求关于t /Δ的导数并令其等于0,得t /Δ=0.27时该式左边最大。
当阀芯处于一个固定的位置时上式左边的分母各参数为定值此时F mK 为最大值即:)(27.021P P D L F i mK -⋅⋅⋅≤ (4-5) 结合式(4-4)、(4-5)如果需要系数0.27尽可能的小,则需要t /Δ值尽可能的小即需要在阀芯和阀体孔的加工中尽量减小其锥度。
而精确的锥度在加工中又难以实现为此采用添加均压槽的方法。
实验表明在间隙密封的阀芯台肩处开一条均压槽后卡紧力减小为不开均压槽的40%。
开等距离的三条均压槽后卡紧力减小到不开均压槽的6%。
开等距离的7条均压槽后减小到不开均压槽的2.7%。