材料表面与界面-第四章-复合材料的界面及界面优化
4 复合材料的界面理论和界面控制

4 复合材料的界面理论和界面控制一般情况下,复合材料的界面产生于复合材料的制造过程,当由不同化学成分的增强体和基体组成复合材料时,这些组元通过接触,它们中的某些元素在相互扩散、溶解后往往发生化学反应生成新相,称为界面相。
此外,这种新相也可以是人为添加的,例如,为了增进基体对增强体的润湿,或者为了缓冲它们之间的残余应力而在增强体表面预先设置了各种涂层,在制造后被保留在复合材料中,成为界面相。
界面相的化学组成和物理性能与增强体和基体均不相同,在复合材料承受载荷时,由于界面相所处的特殊力学和热学等环境,对复合材料的整体性能产生着重大影响,因而通过认识、控制界面相来改善复合材料性能的研究越来越引起人们的重视。
研究复合材料界面的组成、结构、控制、性能和改进界面相的工作被称为“界面工程”。
虽然目前对复合材料的界面理论和界面控制的研究尚不成熟,但是,在指导聚合物基、金属基和陶瓷基复合材料的工艺和性能改善上已经起着十分明显的作用。
本节主要介绍复合材料界面的基本概念和各类复合材料的界面控制。
4.1 复合材料界面的基本概念4.1.1 界面定义在复合材料中,两相(如纤维与基体)之间某种材料特性出现不连续的区域叫做界面。
这种材料特性的不连续可能是陡变的,也可能是渐变的。
材料的特性包括:元素的浓度、晶体结构、原子的配位、弹性模量、密度、热膨胀系数等。
很显然,一个给定的界面,其所涉及的材料特性不连续性可以是一种也可以是几种。
上述大多数物理、化学或力学特性的不连续性较容易理解,而原子配位的概念则需要进一步详细说明。
根据界面处原子配位的类型,可以将界面分为共格界面、半共格界面和非共格界面。
这三种界面示意于图4-1(a )、(b )、(c )。
共格界面是指界面处的原子属于两侧晶体所共有,即在界面两侧,原子位置之间存在一一对应的关系。
图4-1(a)是理想共格界面——孪晶界面(左)和一般共格界面(右)的示意图。
显然,共格界面的界面能比较低。
复合材料的界面工程与性能优化
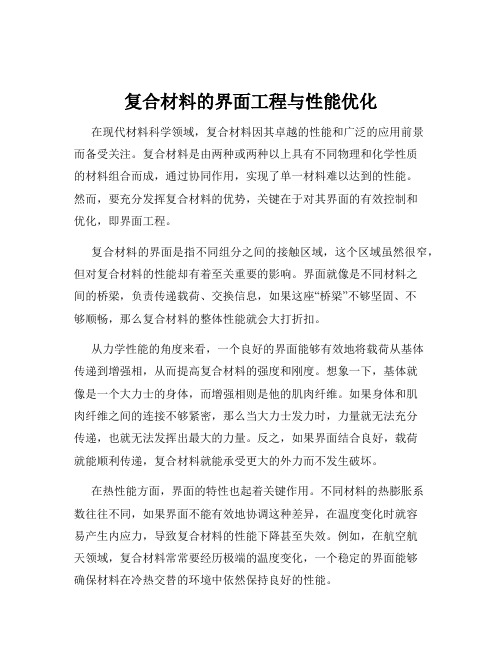
复合材料的界面工程与性能优化在现代材料科学领域,复合材料因其卓越的性能和广泛的应用前景而备受关注。
复合材料是由两种或两种以上具有不同物理和化学性质的材料组合而成,通过协同作用,实现了单一材料难以达到的性能。
然而,要充分发挥复合材料的优势,关键在于对其界面的有效控制和优化,即界面工程。
复合材料的界面是指不同组分之间的接触区域,这个区域虽然很窄,但对复合材料的性能却有着至关重要的影响。
界面就像是不同材料之间的桥梁,负责传递载荷、交换信息,如果这座“桥梁”不够坚固、不够顺畅,那么复合材料的整体性能就会大打折扣。
从力学性能的角度来看,一个良好的界面能够有效地将载荷从基体传递到增强相,从而提高复合材料的强度和刚度。
想象一下,基体就像是一个大力士的身体,而增强相则是他的肌肉纤维。
如果身体和肌肉纤维之间的连接不够紧密,那么当大力士发力时,力量就无法充分传递,也就无法发挥出最大的力量。
反之,如果界面结合良好,载荷就能顺利传递,复合材料就能承受更大的外力而不发生破坏。
在热性能方面,界面的特性也起着关键作用。
不同材料的热膨胀系数往往不同,如果界面不能有效地协调这种差异,在温度变化时就容易产生内应力,导致复合材料的性能下降甚至失效。
例如,在航空航天领域,复合材料常常要经历极端的温度变化,一个稳定的界面能够确保材料在冷热交替的环境中依然保持良好的性能。
除了力学和热性能,界面还对复合材料的电学、光学等性能产生影响。
比如在电子封装材料中,界面的电学特性直接关系到信号的传输速度和稳定性;在光学材料中,界面的平整度和折射率匹配程度决定了光线的透过率和反射率。
那么,如何进行复合材料的界面工程来优化其性能呢?这涉及到多个方面的策略和技术。
首先是对界面的物理和化学改性。
通过物理方法,如表面打磨、等离子体处理等,可以增加界面的粗糙度和活性,从而提高界面的结合强度。
化学改性则包括对基体和增强相表面进行化学处理,引入官能团,以增强它们之间的化学键合。
第四章 复合材料的界面
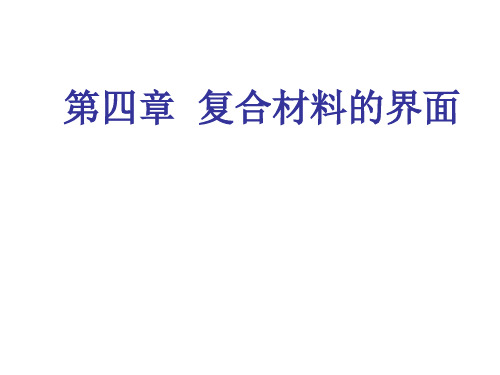
• 第二阶段是聚合物的固化阶段。在此过程中聚 第二阶段是聚合物的固化阶段。 固化阶段 合物通过物理的或化学的变化而固化,形成固 合物通过物理的或化学的变化而固化, 定的界面层。固化阶段受第一阶段影响, 定的界面层。固化阶段受第一阶段影响,同时 它直接决定着所形成的界面层的结构。 它直接决定着所形成的界面层的结构。以热固 性树脂的固化过程为例, 性树脂的固化过程为例,树脂的固化反应可借 助固化剂或靠本身官能团反应来实现。 助固化剂或靠本身官能团反应来实现。在利用 固化剂固化的过程中,固化剂所在位置是固化 固化剂固化的过程中, 反应的中心, 反应的中心,固化反应从中心以辐射状向四周 扩展,最后形成中心密度大、 扩展,最后形成中心密度大、边缘密度小的非 均匀固化结构。 均匀固化结构。
表面结合化学键示意图
五、 界面反应或界面扩散理论 在复合材料组分之间发生原子 或分子间的扩散或反应,从而形 成反应结合或扩散结合。 界面反应结合或扩 散结合示意图
4. 3 聚合物基复合材料界面
• 一、界面的形成 • 对于聚合物基复合材料,其界面的形成可以分成两 对于聚合物基复合材料, 个阶段: 个阶段: • 第一阶段是基体与增强纤维的接触与浸润过程。由 第一阶段是基体与增强纤维的接触与浸润过程。 接触与浸润过程 于增强纤维对基体分子的各种基团或基体中各组分 的吸附能力不同, 的吸附能力不同,它总是要吸附那些能降低其表面 能的物质, 能的物质,并优先吸附那些能较多降低其表面能的 物质。 物质。因此界面聚合层在结构上与聚合物本体是不 同的。 同的。
•
1、外力场 2、基体 3、基体表面区 4、相互渗透区 5、增强剂表面区 6、增强剂 复合材料的界面示意图
二、界面结合方式的分类
1)机械结合。基体与增强材料之间不发生化学反应, 1)机械结合。基体与增强材料之间不发生化学反应,纯粹靠机械 机械结合 连结,靠纤维的粗糙表面与基体产生摩擦力而实现的。 连结,靠纤维的粗糙表面与基体产生摩擦力而实现的。 2)溶解和润湿结合。基体润湿增强材料, 2)溶解和润湿结合。基体润湿增强材料,相互之间发生原子扩散 溶解和润湿结合 和溶解,形成结合。界面是溶质原子的过渡带。 和溶解,形成结合。界面是溶质原子的过渡带。 3)反应结合。基体与增强材料间发生化学反应,在界面上生成化 3)反应结合。基体与增强材料间发生化学反应, 反应结合 合物,使基体和增强材料结合在一起。 合物,使基体和增强材料结合在一起。 4)交换反应结合 基体与增强材料间发生化学反应,生成化合物, 交换反应结合。 4)交换反应结合。基体与增强材料间发生化学反应,生成化合物, 且还通过扩散发生元素交换,形成固溶体而使两者结合。 且还通过扩散发生元素交换,形成固溶体而使两者结合。 5)混合结合。这种结合较普遍,是最重要的一种结合方式。 5)混合结合。这种结合较普遍,是最重要的一种结合方式。是以 混合结合 上几种结合方式中几个的组合。 上几种结合方式中几个的组合。
第4章复合材料的界面
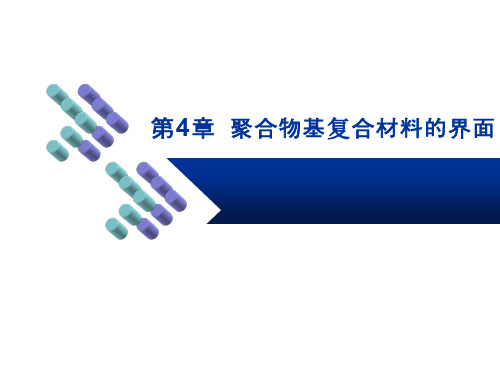
界面的形成与作用机理
§界面的形成
通常认为界面不是一个单一的结合面,而是有一定厚度和 不同作用区域的界面层。
聚合物基复合材料的界面形成分两个阶段: ①基体与增强纤维的接触与浸润过程。 ②聚合物的固化阶段。通过物理的或化学的变化而固化, 形成固定的界面层。树脂固化借助固化剂或靠本身官能团反 应来实现。固化反应以固化剂为中心,以辐射状向四周扩展, 中心密度大的称为胶束或胶粒,密度小的称为胶絮。
界面的形成与作用机理
§界面的作用机理
该理论认为粘结是由化学键和分子扩散的共同作用, 并在一定厚度的界面层中形成相互穿插的网络联接。
为了改善纤维和基体的相容性, 在两相的界面上加入改性剂,如偶联 剂等,便形成一种新的界面。
界面的基本概念
事实证明,多种组分组成的复合材料,其整体综合性能 并不是个单一组分性能线性关系的简单加和。 各组分起着独立的作用,相互依存,依存关系由组成复 合材料之间的界面来实现的。 界面效应
• 物理效应,引起各组分间相互浸润、扩散、相溶性、界面吉布斯自 由能等变化; • 化学效应,导致界面上的化学反应,形成新的界面层结构; • 力学效应,引起界面上的应力分布。具有弱界面的复合材料有较低 的强度和刚度,但它的断裂抗力较高;具有强界面的复合材料有较高 的强度和刚度,但非常脆。
第4章 聚合物基复合材料的界面
本章主要内容
1 第一节 界面的基本概念 2 第二节 界面的形成与作用机理 3 第三节 界面的破坏机理 4 第四节 纤维的表面处理 5 第五节 复合材料界面的研究
界面的基本概念
• 界面——纤维复合材料中增强纤维和基体之间
共有的接触面。
• 聚合物基复合材料的三要素:界面、纤维和基 体。
• 影响复合材料性能的因素:①增强材料的性能,
复合材料的界面性能与优化分析
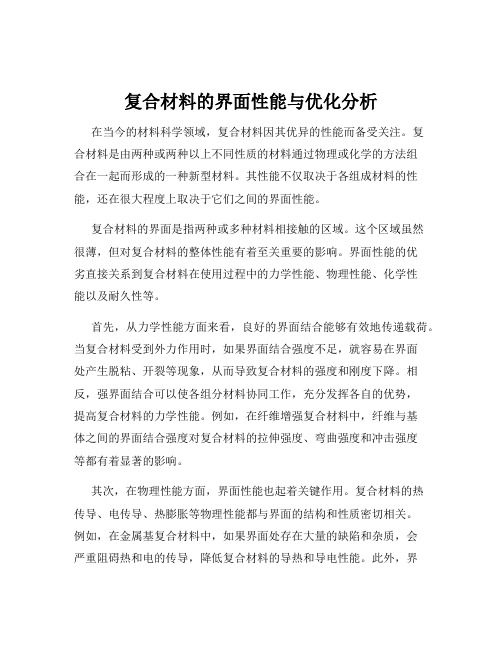
复合材料的界面性能与优化分析在当今的材料科学领域,复合材料因其优异的性能而备受关注。
复合材料是由两种或两种以上不同性质的材料通过物理或化学的方法组合在一起而形成的一种新型材料。
其性能不仅取决于各组成材料的性能,还在很大程度上取决于它们之间的界面性能。
复合材料的界面是指两种或多种材料相接触的区域。
这个区域虽然很薄,但对复合材料的整体性能有着至关重要的影响。
界面性能的优劣直接关系到复合材料在使用过程中的力学性能、物理性能、化学性能以及耐久性等。
首先,从力学性能方面来看,良好的界面结合能够有效地传递载荷。
当复合材料受到外力作用时,如果界面结合强度不足,就容易在界面处产生脱粘、开裂等现象,从而导致复合材料的强度和刚度下降。
相反,强界面结合可以使各组分材料协同工作,充分发挥各自的优势,提高复合材料的力学性能。
例如,在纤维增强复合材料中,纤维与基体之间的界面结合强度对复合材料的拉伸强度、弯曲强度和冲击强度等都有着显著的影响。
其次,在物理性能方面,界面性能也起着关键作用。
复合材料的热传导、电传导、热膨胀等物理性能都与界面的结构和性质密切相关。
例如,在金属基复合材料中,如果界面处存在大量的缺陷和杂质,会严重阻碍热和电的传导,降低复合材料的导热和导电性能。
此外,界面的存在还会影响复合材料的热膨胀系数,如果界面结合不良,在温度变化时容易产生热应力,导致复合材料的变形和破坏。
化学性能方面,界面是复合材料与外界环境相互作用的前沿阵地。
界面的化学稳定性决定了复合材料的耐腐蚀性、抗氧化性等化学性能。
如果界面处容易发生化学反应,如氧化、腐蚀等,就会削弱复合材料的性能,缩短其使用寿命。
例如,在聚合物基复合材料中,界面的亲水性或疏水性会影响其对水分的吸收和扩散,进而影响复合材料的耐湿性和耐老化性能。
那么,如何优化复合材料的界面性能呢?这需要从多个方面入手。
一方面,可以通过对原材料的表面处理来改善界面性能。
例如,对于纤维增强复合材料,可以对纤维表面进行氧化、涂层等处理,增加纤维与基体之间的化学键合和物理结合,提高界面结合强度。
第4章复合材料的界面
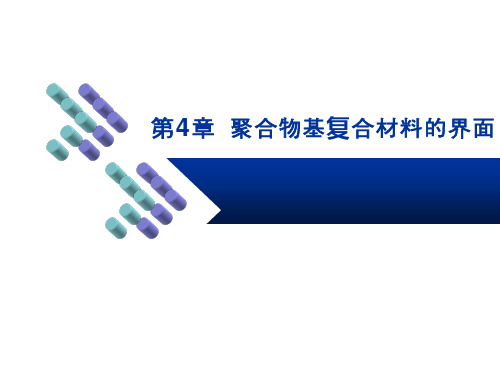
该理论认为复合材料的纤维——基体界面是由化学键作用完成其间粘 着或吸附的,作用的基础是界面层中的化学健接形式。 最典型的是玻璃纤维与基体间的偶联剂。偶联剂是涂覆在玻璃纤维表 面的一层物质,具有双官能团特征。其中一部分官能团能与玻璃纤维表面 分子形成化学共价键结合,而另一部分又能与基体树脂形成化学键联接, 由此将两者牢固的结合在一起。 局限性:对许多未使用偶联剂或使用偶联剂但理论上根本不能形成化 学键的复合体系无法解释。
界面的破坏机理
§界面破坏机理
(1)如果界面上的化学键是集中的,当裂纹扩展时,较多的能量集中于裂纹尖 端,可能在还没有引起集中键断裂时就已冲断纤维,导致复合材料破坏。
(2)界面上化学键集中的另一种情况是,在裂纹扩展过程中,还未能冲断纤维 已使集中键破坏,引起能量流散,仅造成界面黏结破坏。如果裂纹尖端集中的能 量足够大,或继续增加能量,则不仅使集中键破坏,还能引起纤维断裂。
5种基本破坏形式 综合体现
复合材料的破坏 与失效
界面的破坏机理
§界面破坏机理
(1)裂纹扩展引起界面破坏
微裂纹受外界因素作用时,其扩 展的过程将逐渐贯穿基体,最后 达到纤维表面。如果没有能量消 耗,能量集中于裂纹尖端,直接 穿透纤维,导致纤维及复合材料
破坏,这属于脆性破坏。
界面的破坏机理
§界面破坏机理
界面的形成与作用机理
§界面的作用机理
(六)变形层理论和抑制层理论
•变形层理论认为,如果增强材料经处理剂处理后,处理剂在界面形成一
层塑性层,它能松弛界面的应力,减小界面应力的作用。
•抑制层理论认为,表面处理剂是界面的一个部分,它的力学性质,尤其
是模量应介于纤维与基体之间,这样可以起到均匀传递应力、减弱界面应 力的作用。而且此界面过渡层的密度应随纤维表面到基体表面距离的不同 而逐渐变化,在极薄的界面区域中形成一密度梯度区,以起缓冲作用。
第四章 复合材料的界面..
界面区(包括偶联剂部分)的模量介于树脂基体和增 强材料之间时则可最均匀的传递应力。偶联剂的作用是一 端拉紧界面上的聚合物分子结构,一端以硅醇基团与玻璃 等无机材料粘结。接受者不多,缺乏必要的实验根据。
2018/10/6
10
B. 金属基复合材料的界面 a. 界面的结合机制 界面的结合力
产生良好结合的条件如下: 1) 液体粘度尽量低; 2)S 略大于L
2018/10/6
8
b. 化学键理论
在复合材料组分之间发生化 学作用,在界面上形成共价键结 合。偶联剂含有与增强体和基体 反应的官能团。实质是强调增加 界面的化学作用是改进复合材料 性能的关键。
c. 物理吸附理论
表面结合化学键示意图
第四章
复合材料的界面
2018/10/6
1
复合材料性能
=
基体性能
+ 增强体性能
玻璃纤维断裂能 10J/m2 聚酯断裂能 100 J/m2
玻璃纤维增强聚酯复合材 料断裂能 105 J/m2
1+1 > 2
2018/10/6
2
Outline
• • • • • 概述 复合材料的界面 增强材料的表面处理 复合材料界面的表征 复合材料的界面优化处理
传递给增强相,起到基体和增强相之间的桥梁作用。
(2)阻断效应:基体和增强相之间结合力适当的界面有阻 止裂纹扩展、减缓应力集中的作用。
(3)不连续效应:在界面上产生物理性能的不连续性和界
面摩擦出现的现象,如抗电性、电感应性、磁性、耐热性和磁 场尺寸稳定性等。
2018/10/6
5
(4)散射和吸收效应:光波、声波、热弹性波、冲击波 等在界面产生散射和吸收,如透光性、隔热性、隔音性、耐机 械冲击性等。
第四章 复合材料界面及增强材料的表面处理
∴界面是复合材料产生协同效应的根本原因。
4.为什么CM断裂能比其组成材料树脂和纤维大很多倍?
首先是在应力作用下产生裂纹,裂纹的 尖端是应力集中点,促使裂纹在基体中 发展,遇到纤维:
<1>因为纤维强度高,阻止裂纹前进,裂纹被迫沿界面发展,
使界面脱粘;
<2>裂纹在发展中若遇到纤维的薄弱部分,也可导致纤维断裂,
此理论适于:
2、拘束层理论(抑制层理论): 理论认为:在基体和增强体之间存在的松弛应力的过渡层 结构不是柔性的变形层,而是模量介于基体和增强体之间 的界面层,这种中间模量的界面层起到了均匀传递应力的 作用。
低 本体基体
模量 临近增强剂 表面的基体 高 界面区的优先吸附
抑制层是通过优先吸附形成的, 增强剂的模量一般比基体树脂高 的多,在CM成型过程中,因为 优先吸附作用,增强剂表面附近 的集体堆砌得比本体更加紧密, 有较高模量。随着离增强剂表面 距离的增大,基体堆砌渐松,模 量渐低,所以形成一个模量由高 到低的梯度减小的过渡区。
所以在此理论之上又提 出
“优先吸附”理论
“柔性层”理论
认为:塑性层不仅是由偶联剂,而是由偶联剂和优先吸附形成的
柔性层组成。柔性层厚度与偶联剂本身在界面区的数量无关。 聚合物基的石墨碳纤维CM 在增强纤维表面接枝上柔性的XJ分子,以 在形成CM中通过XJ分子的形变松弛内应力, 抑制裂纹的发展,提高界面粘结。
由方程式:W=γL+γS+γSL —— <1> COSθ=(γS -γSL)/ γL —— <2> W:润湿时粘附力(液体在固体表面的粘合功) γL γS γSL 分别为液体、固体、固液的表面张力 θ:基体与粉粒填料、纤维间的接触角
复合材料-第四章复合材料界面
(1)物理因素
例1 粉末冶金制备的W丝/Ni,钨在镍中有很大的固溶度,在1100℃左右使用50小时后,钨丝发生溶解,造成钨丝直径仅为原来的60%,大大影响钨丝的增强作用,如不采取措施,将产生严重后果。为此,可采用钨丝涂覆阻挡层或在镍基合金中添加少量合金元素,如钛和铝,可以起到一定的防止钨丝溶入镍基合金的作用。
如何防止碳在镍中先溶解后析出的问题,就成为获得性能稳定的Cf / Ni的关键。
例2 碳纤维增强镍基复合材料。在800℃高温下,在界面碳先溶入镍,而后又析出,析出的碳是石墨结构,密度增大而在界面留下空隙,给镍提供了渗入碳纤维扩散聚集的位置。而且随温度的提高镍渗入量增加,在碳纤维表层产生镍环,严重损伤了碳纤维,使其强度严重下降。
4.2.1 聚合物基复合材料的界面
1.界面的形成 聚合物基复合材料界面的形成可以分成两个阶段: ①基体与增强纤维的接触与浸润过程; 增强纤维优先吸附能较多降低其表面能的组分,因此界面聚合物在结构上与聚合物基体是不同的。 ②聚合物的固化阶段。聚合物通过物理的或化学的变化而固化,形成固定的界面层。
1
2
复合材料中的界面并不是一个单纯的几何面,而是一个多层结构的过渡区域,这一区域由五个亚层组成。
界面是复合材料的特征,可将界面的机能归为以下几种效应。……P61
复合材料界面设计的原则(总的原则)
界面粘结强度要保证所受的力由基体通过界面传递给增强物,但界面粘结强度过高或过弱都会降低复合材料的强度。
复合材料的界面性能与优化
复合材料的界面性能与优化在现代材料科学领域,复合材料因其出色的性能而备受关注。
复合材料是由两种或两种以上具有不同物理和化学性质的材料组合而成,其性能并非各个组分材料性能的简单加和,而是通过各组分之间的协同作用实现了性能的优化和提升。
而在这其中,复合材料的界面性能起着至关重要的作用。
复合材料的界面,简单来说,就是不同组分材料之间相互接触和作用的区域。
这个区域虽然在尺寸上相对较小,但却对复合材料的整体性能产生着深远的影响。
就好像一个团队中各个成员之间的沟通与协作环节,虽然看似细微,却决定着整个团队的运作效率和成果。
首先,我们来探讨一下复合材料界面性能的重要性。
良好的界面性能能够有效地传递载荷。
当复合材料受到外力作用时,如果界面能够将应力从一种材料传递到另一种材料,那么整个复合材料就能更好地承受外力,从而表现出更高的强度和韧性。
界面性能还对复合材料的热性能有着重要影响。
不同的材料具有不同的热膨胀系数,如果界面结合不好,在温度变化时就容易产生热应力,导致材料性能下降甚至失效。
此外,界面性能也会影响复合材料的耐腐蚀性能和电性能等。
那么,复合材料的界面性能具体包括哪些方面呢?界面的结合强度是一个关键因素。
如果结合强度过低,在使用过程中容易出现界面脱粘,从而降低材料的性能;而结合强度过高,又可能导致材料在受到冲击时无法通过界面的解离来吸收能量,造成脆性断裂。
界面的化学稳定性也是不容忽视的。
在一些恶劣的环境中,界面处容易发生化学反应,从而影响材料的长期使用性能。
界面的微观结构同样重要,它决定了界面的物理和化学性质,进而影响复合材料的整体性能。
接下来,我们看看影响复合材料界面性能的因素。
材料的表面处理方式是一个重要方面。
通过对增强材料表面进行化学处理、物理处理或者涂层处理,可以改变其表面的化学组成和物理形貌,从而提高与基体材料的相容性和结合力。
制备工艺条件也会对界面性能产生影响。
例如,在复合材料的制备过程中,温度、压力、时间等参数的控制都会影响界面的形成和性能。
- 1、下载文档前请自行甄别文档内容的完整性,平台不提供额外的编辑、内容补充、找答案等附加服务。
- 2、"仅部分预览"的文档,不可在线预览部分如存在完整性等问题,可反馈申请退款(可完整预览的文档不适用该条件!)。
- 3、如文档侵犯您的权益,请联系客服反馈,我们会尽快为您处理(人工客服工作时间:9:00-18:30)。
研究和设计界面时,不应只追求界面结合强度而应考 虑到复合材料综合力学性能。
不同界面结合强度断裂纤维周围基体形态模型
a. 弱界面结合状况 b. 界面结合适中状况 c. 界面结合过强状况
界面剪切强度太低:
许多因素影响着界面结合强度,如表面几何形状、 分布状况、纹理结构、表面杂质、吸附气体程度、吸 水情况、表面形态、在界面的溶解、扩散和化学反应、 表面层的力学特性、润湿速度等。
4.3 复合材料组分的相容性
物理相容性:
1. 是指基体应具有足够的韧性和强度,能够将外部载 荷均匀地传递到增强剂上,而不会有明显的不连续 现象。
二、叠层复合材料
叠层复合材料是指在基 体中含有多重层片状高 强高模量增强物的复合 材料。
层状陶瓷复合材料断口形貌 三明治复合
双金属、表面涂层等也是层状复合材料。 结构层状材料根据材质不同,分别用于飞机制造、运输
及包装等。
有TiN涂层的 高尔夫球头
铝
合
层 状 复 合
金 蜂 窝 夹 层
板
三、粒子增强型复合材料
陶瓷中增韧纤维受外力作用, 因拔出而消耗能量,耗能越 多材料韧性越好。
C/C复合材料 Si/Si复合材料
用晶须作为增强相可以显著提高复合材料的强度和弹 性模量,但因为价格昂贵,目前仅在少数宇航器件上 采用。现在发现,晶须 (如SiC 和Si3N4)能起到陶瓷材 料增韧的作用。
ZnO晶须 自增韧Si3N4陶瓷
cm f,cm V m fV f
纤维的临界长径比 纤维最小体积分数
Lc fy d 2 my
Vfc
mu fu
m
m
2. 粒子增强型复合材料的增强机制
粒子增强型复合材料按照颗粒尺寸大小和数量多少可分为: 弥散强化的复合材料;颗粒增强的复合材料。
(1)弥散强化的复合材料的增强机制
将粒子高度弥散地分布在基体中,使其阻碍导致塑性变形 的位错运动(金属基体)和分子链运动(聚合物基体)。
3、破断安全性好 4、优良的高温性能。 5、减震性好。复合材料中的大量
界面对振动有反射吸收作用,不易 产生共振。
\ \ \
比 强 度 比 较 碳 硼 玻钛 钢 铝 纤纤璃 维维纤 树树维 脂脂树 脂
常用的复合材料
一、纤维增强复合材料
1. 常用增强纤维
(1)玻璃纤维:用量最大、价格最便宜。
(2)碳纤维:化学性能与碳相似。
不连续效应
电阻R1 电阻R2 电阻R1
4.2 界面的效应(3)
(4)散射和吸收效应:光波、声波、热弹性波、 冲击波等在界面产生散射和吸收,如透光 性、隔热性、隔音性、耐机械冲击及耐热 冲击性等。
散射和吸收效应
4.2 界面的效应(4)
(5)诱导效应:一种物质(通常是增强物)的表 面结构使另一种与之接触的物质(通常是聚 合物基体)的结构由于诱导作用而发生改变, 由此产生一些现象,如强的弹性、低的膨 胀性、耐冲击性和耐热性等。
2. 由于裂纹或位错移动,在基体上产生的局部应力不 应在增强剂上形成高的局部应力。
3. 基体与增强相热膨胀系数的差异对复合材料的界面 结合产生重要的影响,从而影响材料的各类性能。
思考:
当复合材料使用条件要求基体韧性好而增强材 料是脆性材料时,该如何考虑基体材料的热膨胀系 数?
4.3 复合材料组分的相容性
碳
承载组分,其增强效果主要取决于纤维的 纤
维
特征、纤维与基体间的结合强度、纤维的 体积分数、尺寸和分布。
弹性模量及强度
外力方向与纤维轴向相同时,c= f = m (f-纤维、 m-基体、 c-复合材料),则
cfV fm V m ,E c E fV f E m V m
当外力垂直于纤维轴向时,则
二、复合材料的分类
1、按基体材料分
(1)非金属基复合材料
SiC颗粒
增
(2)金属基复合材料。
强 相
三
2、按增强材料分
种 类
型
(1) 纤维增强复合材料
Al2O3片
(2) 粒子增强复合材料
(3)叠层复合材料。
Al2O3纤维
三、复合材料的命名
(1)以基体为主来命名 例如金属基复合材料。 (2)以增强材料来命名 如碳纤维增强复合材料。 (3)基体与增强相并用 如“C/Al复合材料”即
诱导效应
聚合物表面
R
R
R
Si
Si
Si
H O
H2O O
O H
HH
O
O
H
H
O
O
O
M
M
M
无机表面
HH
界面效应是任何一种单一材料所没有的特 性,它对复合材料具有重要的作用。界面效 应既与界面结合状态、形态和物理-化学性质 有关,也与复合材料各组分的浸润性、相容 性、扩散性等密切相关。
界面结合较差,增强体不能发挥作用;界面结合过强, 材料破坏过程的裂纹容易扩展到界面,直接冲击增强体则 呈脆性断裂。
MMC虽强度和弹性模量(刚度)增加,但塑性和韧性 因使用陶瓷纤维而有所降低。这在一定程度上限制了 MMC的应用范围。
航天飞机内 MMC (Al / B
纤维)桁架
4. 纤维--陶瓷复合材料
陶瓷材料耐热、耐磨、耐蚀、 抗氧化,但韧性低、难加工。 在陶瓷材料中加入纤维增强, 能大幅度提高强度,改善韧 性,并提高使用温度。
4.4 界面理论(1)
机械结合 基体与增强材料之间不发生化学反应,靠纤维的 粗糙表面与基体产生摩擦力而实现的。
在钢筋与混凝土之间的界面上会产生剪应力,为此,在预 应力钢筋的表面带有螺纹状突起。
表面越粗糙,互锁作用越强,机械粘结作用越有效。 但表面积随着粗糙度增大而增大,其中有相当多的孔穴, 粘度大的液体是无法流入的。造成界面脱粘的缺陷,而 且也形成了应力集中点,影响界面结合。
着垂直于纤维方向向基体内部发展。 界面结合过强时复合材料呈脆性断裂。
界面剪切强度适中:
应力分布的区域化,没有在某点处因应力集中而造成破坏 并产生裂缝。因为纤维断裂时,相邻界面处可以适当脱粘 或滑移很小的一部分,分散了集中于断口处的应力点。保 护了基体不在纤维断口处产生破坏和裂缝,而且能够通过 很微小的脱粘和滑移吸收一定的能量,从而提高了材料整 体的力学性能。
芳纶刹车片
3. 纤维--金属(或合金)复合材料
金属的熔点高,故高强度纤维增强后的金属基复合材料 (MMC)可以使用在较高温的工作环境之下。
常用的基体金属材料有铝合金、钛合金和镁合金。
作为增强体的连续纤 维主要有硼纤维、SiC 和C纤维;Al2O3纤维 通常以短纤维的形式 用于MMC中。
MMC的SEM照片
化学相容性:
指组成材料的各组元(基体与增强体)之间有无 化学反应及反应速度的快慢。包括热力学相容性 和动力学相容性。
化学相容性是一个复杂的问题: ➢ 对原生复合材料,在制造过程是热力学平衡的,其两相
化学势相等,比表面能效应也最小。 ➢ 对非平衡态复合材料,化学相容性要严重得多。 ➢ 纤维和基体间的直接反应则是更重要的相容性问题。
聚合物基粒子复合材料如酚醛树 脂中掺入木粉的电木、碳酸钙粒 子改性热塑性塑料的钙塑材料 (合成木材)等。
陶瓷基粒子复合材料如氧化锆增
韧陶瓷等。
粒子增强SiC陶瓷基复合材料
颗粒增强铝基泡沫复合材料
碳黑增强橡胶
金属基粒子复合材料又称金
属陶瓷,是由钛、镍、钴、
铬等金属与碳化物、氮化物、
氧化物、硼化物等组成的非
金属基体复合材料和陶瓷复合材料有这类结合方式。
在大多数情况下,纯粹机械粘结作用很难遇到,往 往是机械粘结作用与其它粘结机理共同起作用。
4.4 界面理论(2)
溶解和润湿结合主要是聚合物基体复合材料的结合形式。 基体润湿增强材料,相互之间发生原子扩散和溶解,即 物理和化学吸附作用。界面是溶质原子的过渡带。
均质材料。 碳化物金属陶瓷作为工具材
硬质合金组织(Co+WC) 硬质合金铣刀
料已被广泛应用,称作硬质
合金。硬质合金通常以Co、
Ni作为粘结剂,WC、TiC等
作为强化相。
4.1 复合材料的界面
复合材料的界面是指基体与增强物之间化学成分 有显著变化的、构成彼此结合的、能起载荷传递作用 的微小区域。
复合材料的界面是一个多层结构的过渡区域,约 几个纳米到几个微米。此区域的结构与性质都不同于 两相中的任何一相。这一界面区由五个亚层组成,每 一亚层的性能都与基体和增强相的性质、复合材料成 型方法有关。
纵向抗拉强 度 MPa
69
环氧树脂 / E级玻璃纤维 1020
环氧树脂 / 碳纤维(高弹性)
1240
环氧树脂 / 芳纶纤维(49) 1380
环氧树脂 / 硼纤维(70 % Vf ) 1400-2100
纵向弹性模 量 GPa
6.9
45
145 76
210-280
聚合物基纤维增强复合材料零件
碳纤维增强聚酰亚胺复合材料制航空 发动机高温构件
表明界面结合过弱。在拉伸时纤维与基体脱粘、滑 移,纤维断裂点周围基体的形态呈空管状,而且界 面上没有任何曾经有过强烈相互作用的迹象。在这 种状况下,纤维高强度和高模量的优势得不到充分 发挥,复合材料得不到有效增强。
界面剪切强度过高:
纤维断裂,应力集中到断口周围基体上; 界面结合强度大于基体强度,应力不能松弛,裂缝沿
对于韧性基体材料,最好具有较高的热膨胀系数。这是 因为热膨胀系数较高的相从较高的加工温度冷却时将受 到张应力;
对于脆性材料的增强相,一般都是抗压强度大于抗拉强 度,处于压缩状态比较有利。
对于像钛这类高屈服强度的基体,一般却要求避免高的 残余热应力,因此热膨胀系数不应相差太大。