PCB外观检查作业指导书
PCB检验作业指导书
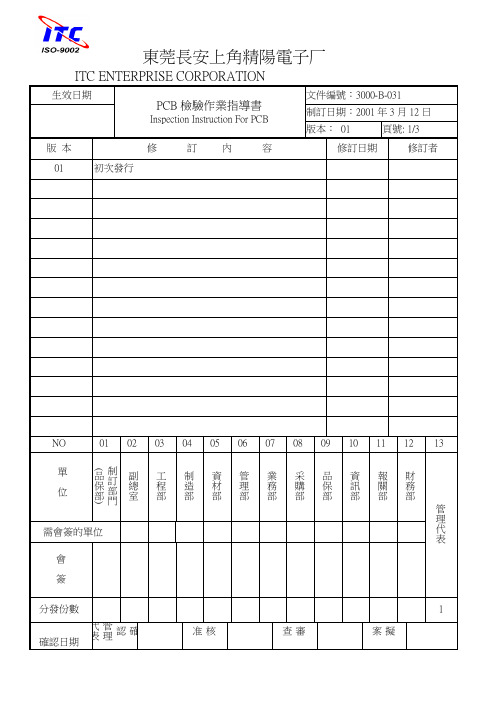
東莞長安上角精陽電子厂生效日期PCB檢驗作業指導書Inspection Instruction For PCB 文件編號:3000-B-031制訂日期:2001年3月12日版本:01 頁號: 1/3版本修訂內容修訂日期修訂者01 初次發行NO 01 02 03 04 05 06 07 08 09 10 11 12 13單位制訂部門(品保部)副總室工程部制造部資材部管理部業務部采購部品保部資訊部報關部財務部管理代表需會簽的單位會簽分發份數 1確認日期確認管理代表核准審查擬案東莞長安上角精陽電子厂ITC ENTERPRISE CORPORATION生效日期PCB檢驗作業指導書Inspection Instruction For PCB 文件編號:3000-B-031制訂日期:2001年3月12日版本:01 頁號: 2/31.目的:.為IQC的檢驗工作提供操作指南2.适用范圍:适用于本公司IQC對PCB的檢驗.4.職責:4.1 MQE或IQC主管負責該作業指導書的制作及修改.4.2 IQC檢驗員執行此作業指導書.5.定義:(略)6.內容:6.1 IQC依MRR單上的P/N,品名規格找出對應的BOM,材料規格承認書或樣品及材料歷史檔案夾(對于沒有規格承認書或樣品的材料,依照進料檢驗程序處理)6.2 IQC必須查閱該材料的歷史檔案夾,決定檢驗方式,并對材料作重點性的檢驗及追蹤6.3 IQC依MRR單上的批量,結合AQL的設置及檢驗方式,查閱MIL-STD-105E LEVEL II抽樣計划表決定抽樣數量,并到待驗區,對該材料進行抽樣.6.3.1 AQL的設置: 外觀:MA: 0.40 MI: 1.06.3.2 功能:抽檢30Pcs MA: 0 MI: 06.3.3剝离實驗:抽檢5PCS MA:0 MI:06.4 IQC抽樣時:6.4.1首先核對來料P/N,品名規格是否与MRR單上的相符.6.4.2在隨机抽樣的基礎上,對供應商不同D/C或LOT NO,不同班別的材料,必須都有抽樣到,即還必須做到有針對性的抽樣.6.4.3.确認包裝方式是否符合要求.6.5 檢驗6.5.1 核對來料的P/N,品名規格及供應商名稱必須与規格承認書或BOM上的相符.6.5.2 外觀檢驗6.5.2.1要求: 外觀不能有短路、斷路、綠油脫落、焊盤氧化、絲印偏移、板邊破損、面板划傷等現象,具体見<<PCB檢驗標准>>,外觀檢驗標准之要求6.5.2.2檢測工具: 3倍放大鏡6.5.3 尺寸檢驗6.5.3.1外圍尺寸:板長、板寬、板厚6.5.3.1.1要求:符合<<PCB檢驗標准>>外形尺寸公差之要求6.5.3.1.2.檢測工具: 游標卡尺6.5.3.2 定位孔6.5.3.2.1要求:符合<<PCB檢驗標准>>孔徑公差之要求6.5.3.2.2檢測工具:快測孔徑規6.5.3.3 插件最小孔,CONNECTOR插件孔6.5.3.3.1要求:符合<<PCB檢驗標准>>孔徑公差之要求.6.5.3.3.2檢測工具:針規6.5.4 板彎板翹量測.東莞長安上角精陽電子厂生效日期PCB檢驗作業指導書Inspection Instruction For PCB 文件編號:3000-B-031制訂日期:2001年3月14日版本:01 頁號: 3/36.5.4.1要求:符合<<PCB檢驗標准>> PCB平坦度允許公差之要求6.5.4.2檢測工具:平台(500*500*100mm),厚薄規6.5.4.3操作步驟:6.5.4.3.1將目視外觀檢出的板彎板翹不良品置于平台上.6.5.4.3.2用厚薄規試塞PCB最大板彎或板翹處,直到剛好試塞OK為止,此時厚薄規之尺寸即為量測之依据.6.5.4.3.3記錄量測數据于<<IQC進料檢驗記錄>>中.6.5.5 剝离檢驗6.5.5.1目的:檢驗文字印刷油墨強度.6.5.5.2要求:符合<<PCB檢驗標准>>之要求.6.5.5.3檢測工具:3MNO600膠帶.6.5.5.4操作步驟:6.5.5.4.1.將3MNO600膠帶貼于PCB的文字印刷油墨上,要求膠帶必須實貼于PC上,選取的位置必須有代表性,一般選取PCB4個角落及中間5個位置.6.5.5.4.2 撕拉膠帶,觀察文字印刷油墨有無脫落現象,并作出判定.6.6 缺點判定依照<<PCB檢驗標准>>對檢驗過程中所發現的缺點進行判定.6.7 檢驗結果的記錄以上之檢驗結果及之測量數据均應及時記錄于<<IQC進料檢驗記錄>>中,并做好材料歷史檔案夾.6.8 以上之操作必須配戴手套7. 表單:7.1 <<IQC進料檢驗記錄>> 3000-A-005-0018.相關文件:8.1 <<PCB檢驗標准>> 3000-B-033。
PCB半成品外观检验作业指导书

1、按即定的要求检查U盘,外壳的外观是否良好。
2、检查USB转接口是否擦拭干净有无手渍及其它污渍。
3、检查OK品装入内盒,不良品标识清楚分开存放。
二.注意事项:
1、作业员必须佩戴静电带及手套。
2、不良品要及时反馈给相关工作及管理人员。
3、注意生产是有无16M、32M、64M混在一起下拉的现象。
深圳安鸿实业有限公司
第页,共页
PCB半成品外观检验
文件编号:PZ-WI-20
产品编号:
版本:1.0版本
生效日期:2002/10/10
一、具体要求:
1、根据PCB半成品板上IC的丝印确认,该PCB板是否与现所生产的机型相符合
2、检查灯的焊接有未按要求加高,灯有无否斜,偏位现象
3、检查板底有无脚长,锡占领过大等不良现象,以免影响装配
4、做好QC检验记录。
三.使用工具:
手套、静电带
制定:
何耀霞
审核:
批准:
深圳市安仲惠杰电子有限公司
第1页共1页
作业指导书
U盘测试
文件编号:AVE—SC—002
产品编号:AVE-039
版本编号:V1.0
生效日期:2002.10.10
一、T1测试
插上U盘,等灯从快闪变成慢闪后(切记只能插一次),且“我的电脑”里面出现找到可移动磁盘时,开始运行T1的测试程序。
三、T3测试
T1、T2都测试OK的板子,并在装好壳待装盒之前都需100%进行此测试,主要检查容量大小、写保护开关、AUTOEXEC与UPDATA两文件,其中最需要注意AUTOEXEC.BAT中是否有UPDATA。
切记:T1、T2都测试OK不能连着测试。此规范只针对下线板!!!对于以前的截留板或维修坏板请
PCB成品检验OQC作业指导书

OQC作业指导书1.目的:为确保公司所有产品在出货时都能达到一定的品质标准且符合客户的要求。
2. 适用范围:公司所有的成品检验(客户提供检验标准除外)均适用之。
3. 定义:3.1 FQC:Final Quality Control(最终检验)3.2 FQA:Final Quality Assure(最终稽核)3.3 产品分级3.3.1. 产品分级(Classification)介绍:本公司按其功能可靠度(FunctionalReliability)与性能(Performances Requirement)两方面,分为如下:3.3.1.1 第一级(Class 1)Gerneral Electronic Productions:一般电子产品,此级包括:消费品,性产电脑与电脑周边产品,其主要品质要求在于电路板或其组装板是否能够发挥功能3.3.1.2 第二级(Class 2):Dedicated Service Electronics Products专用性电子产品。
此级包括:通信设备,复杂商务机器,仪器等,此级在品质上已讲究高性能及寿命长,同时希望能不间断地工作,但不是关键性的,因而某些外观缺陷是允许的。
3.4 弯曲度:四角在同一平面上,整板成圆柱形或球面弯曲的状况3.5 板翘曲:四角不在同一平面上4. 相关权责:4.1.FQC: 负责对成品进行全检,并将品质信息及时反馈给前制程及公司管理层.。
4.2.OQC: 负责对成品板进行抽检,及时反馈QC检板品质状况,并对相关品质问题跟踪处理和报告。
5.设备、工具及物料:检验台、手套、指套、刮刀、划线笔、90倍放大镜、万用表6.作业流程:无7. 检验标准(附表)8. 作业内容8.1 FQA人员将FQC置于待抽验之成品板依《产品检验与试验控制程序》对应取样,允收标准为XX公司抽样标准AQL:0.65,并依据附表<二>成品检验标准中所有检验类别及标准进行外观检验8.2 FQA人员在外观抽检过程中,如发现有不符合标准现象,则用红色三角标签标示,然后依XX公司零缺点抽样标准和检验标准(见附表)判定此批“允收”或“拒收”8.3 抽检合格后,FQA抽检人员将该批板转入合格区8.4 将检验结果记入《QA检查记录》中,其记录如下:8.4.1 日报表上须注明班别、日期;8.4.2 每批板须注明该批板生产型号(注明版本)、批量、抽检数;8.4.3 记录时,依照相应检验项目填写不良数及不良率并在判定栏中打“√”标明“拒收”或“允收”;8.4.4 如有批退板经FQC重检或重工后,转入重新检验时,FQA报表需能识别为重工板;8.4.5 对于库存品1个月以上,3个月以内由FQA做信赖度试验,合格则出货,不合格依《产品检验与试验控制程序》处理;8.4.6 对于库存品3个月以上直接退FQC返检,并做相关信赖度试验8.4.7 对库存品每周FQA按20箱抽取1箱开箱检验,判定是否可出货;8.4.8 新单、返单更改出货前依MI做全尺寸测量,具体依《产品检验与试验控制程序》。
PCB FQA作业指导书
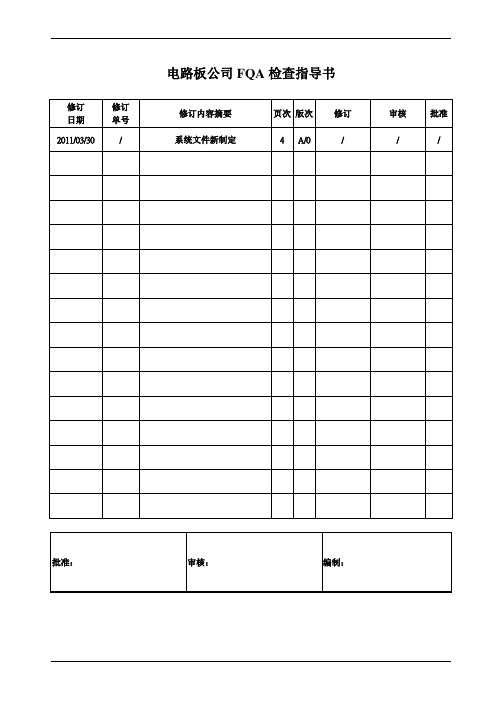
电路板公司FQA检查指导书PCB线路板公司FQA作业指导书1.目的:确保产品、出货达到公司的质量目标要求2.依据:参考生产指示MI参考本厂产品质量手册参考AQL抽检标准、客户收货要求3.检查方法:3.1按抽检依据:MIL-STD-105E(附表)(在装箱后按批量数进行AQL抽样数检查)3.2验收水平按AQLⅡ级水准:AQL=CR=0 MAJ=0.4 MIN=1.53.2.1尺寸检查:外围、孔径尺寸是否与工程制作MI分孔图、机械图、客户资料相符、测量工具、卡尺、针规每批抽检5块。
3.2.2附着性测试:(用不费时胶纸测试镀层或绿油、白字、碳油附着力,每批板抽检20块)。
3.2.3阻值检查(用万能表调到适合档位后测量检查阻值是否偏高是否符合要求,每批检查测量10块。
)3.2.4浸锡试验:(每批试验检查2-5块。
)3.3在允许范围内放行(但执出不良品)超出允许范围时,填写好《QA抽查不合格退单》及时退回FQC返工,并知会有关人员。
3.4板材、线路、镀层、绿油、字符、标记、碳油、孔、成形、尺寸、V坑、弯曲度、ROHS要求、外观、附着力、阻值、兰胶、浸锡试验等抽检合格在待装纸箱盖上合格PASS 章,抽检样板划上FQA个人记录色线,封好纸箱后入仓。
3.5FQA将抽查结果记录在《QA检查日报表》上,抽检不合格在报表上注明原因,连同不良样品知会有关负责人签字确认并安排返工。
3.6在抽检中如有按AQL标准抽样属不允许范围的轻微问题,可申请UAI出货。
3.7FQA员根据客户的需要,认真填写《成品检验出货报告》,并包装好附在包装箱上。
4.检查内容:4.1 板材:4.1.1检查板材是否符合资料要求4.1.2检查是否有混料、板材分层、变色或变质等问题4.1.3检查板材是否有白斑、纤维显露、厚薄超出公差等问题4.2 线路:4.2.1检查是否有开路、短路、幼线、肥线、线路或铜皮崩缺、狗牙、沙孔、擦伤、凹陷、蚀板过度、蚀板不净划花等问题。
PCB检验指导书1.doc

1目的为了规范印制电路板來料检验及抽样计划,特制定该检验规范。
2适用范围本规范适川于所冇印制电路板的來料检验。
3引用文件下列文件中的条款通过木标准的引用而成为木标准的条款。
凡是不注口期的引用文件,其授新版本适用于本标准。
來料检验工作流程MIL-STD-1916IPC-A-600H 电路板品质允收规格IPC-TM-650 试验方法手册4特殊要求4.1本规范抽样计划除特殊抽样计划外均按MIL-STD-1916执行。
4.2缺陷级别说明4.2.1致命缺陷(CR1):会导致川户人身健康或安全受到威胁的故障,如电源开关打火或爆炸等。
4.2.2严重缺陷(MAJ):影响客户使用的如:电气特性、零件错谋、组装功能、缺件、缺标识、版木错谋、零件破损、焊锡性、尺寸不符(影响应用)等。
4.2.3轻微缺陷(MIN):产品标识不清晰、刮伤(不露底材)、脏污、尺寸不符(不影响应用)、变色、外观不良等。
4.3客户若有指定规范、标准和抽样计划时,依客户耍求实施,本规范耒列举部分,依一般业界通用规范或标准为准。
4.4不盂记录检验值的,检验结果只做合格不合格判定。
4.5外观检验时,抽样数按照整包抽,肓至抽样数达到抽样要求。
外观抽样按照人板抽样,填写检验记录时填写大板数。
4.6取板时需戴上洁净的手套,取板过程小注意不要擦花、损伤到板面,有工艺边的注意不要损伤工艺边,不能接触焊盘、金手指、按键等部位。
4.7检验顺序要求:查询历史来料悄乃L►查找图纟I—►按检验项H进行检验及判定—> 新包装—►填写检验记录—►对检验物料进行标识。
5检验内容5.1具体检验内容见表1:表1检验内容表6翘曲度测试方法6."弓曲测屋:手指轻按待测板四角,使四角均接触台面,用塞规或塞尺量取最大处数值(A1),并作记录;6.2弓曲算法:弓曲度=(A1/A) *100%;6. 3扭曲测量:用手指轻按待测板三个角,使其接触台面,用塞规或塞尺测量另一个角的翘起量(B1), 并作记录;6.4扭曲算法:扭曲度二(Bl/2B)*100%;6.5翘曲度:収弓曲度、扭曲度最大值,即为翘曲度;图1 PCB弓曲和扭曲测量示意图7图纸末注尺寸公差要求7.1「图纸末注孔径公差参照以下要求执行。
PCB检验作业指导
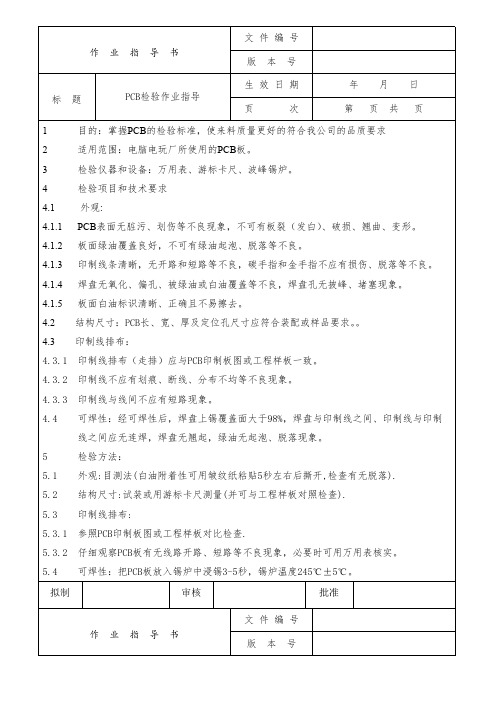
生效日期
页
次
年月日 第 页共 页
4.4 抗震性:从1m高处自由落体跌落后,面、底壳无破裂,配合良好,内部无松动,电气性
能无超标现象。
4.6 老化:在常温常压下老化4小时后,表面温度不能超过650C,面、底壳无变形、烧焦现象,
各性能指标在规格范围之内。
5
检验方法
5.1 外观:目测法
5.2 结构尺寸:用游标卡尺、卷尺测量。
4.3 印制线排布:
4.3.1 印制线排布(走排)应与PCB印制板图或工程样板一致。
4.3.2 印制线不应有划痕、断线、分布不均等不良现象。 4.3.3 印制线与线间不应有短路现象。
4.4 可焊性:经可焊性后,焊盘上锡覆盖面大于98%,焊盘与印制线之间、印制无起泡、脱落现象。
检验项目 外观
结构尺寸 开机检查 电气性能 抗震性
老化
附表
缺陷内容 外壳严重开裂、划伤、毛刺、变形、缩水、污迹等
判定 B
外壳轻微开裂、划伤、毛刺、变形、缩水、污迹等
C
金属件氧化、锈蚀、霉斑、污渍、少打螺钉
B
AC插脚、DC插头松动、AC插脚高度不一致
C
螺钉打花、打滑、松动(即未打紧)
C
线体烫伤、划伤、破损可见内线
B
线体烫伤、划伤、破损但内线无外露,线体脏污
C
铭牌贴贴错、漏贴、文字内容与样板不符
B
铭牌贴贴倒、贴歪、翘起、文字模糊不清
C
面、底壳配合缝隙大于1mm
B
面、底壳配合缝隙在0.5mm~1mm
C
结构尺寸超出技术规格要求范围,影响装配
B
结构尺寸超出技术规格要求范围,但不影响装配
C
AC插脚高度超出16±0.35mm
pcb作业指导书标准范文

pcb作业指导书标准范文
pcb作业指导书标准范文
1、准备好元器件,PCB板,烙铁,焊锡丝等物品。
2、准备作业前做好ESD静电防护措施,带好防静电腕带。
3、检杏PCB板是否完好无损,无断路,无绿油脱落,无划伤等缺陷,检查物料是否和PCB上所需的物料相符.如有缺陷停止使用,及时反馈给质检部。
4、板焊接将PCB板与印刷板的标注及印刷板图对照或参照印刷电路板样品,核对无误后将元器件插接到PCB板上。
然后将插接好元器件的PCB板翻过来,引线朝上,左手拿焊丝,右手握烙铁,等待焊接,要求烙铁头保持干净,无焊渣等气化物,并在表面镀有一层焊锡。
5、把烙铁头接触引脚/焊盘1-2S,焊锡丝从烙铁对面接触焊件,当焊丝熔化一定量后,立即向左上45°方向移开焊丝,焊锡浸润焊盘和焊件的施焊部位以后,向右上45°方向移开烙铁,结束焊接。
此过程一般为3S左右。
元件面上的部分焊盘。
6、注意不要过热且不要时间过长或者反复焊接,防止烫坏焊盘和元器件,尤其是塑料外壳元器件,防止塑料壳软化和引线断路。
焊接过程最多不能超过5秒。
元器件引线应该留有一定长度,防止烫坏元器件或者损坏元器件功能。
元器件按由矮到高的顺序进行焊接,否则较小元器件无法焊接。
焊接完元器件将诸如散热片类的机械固定的元器件固定在PCB板上。
不要使引线承受较大的压力。
用偏口钳将焊接完的元器件多余的引脚剪掉。
剪口光亮、平滑、一致。
清理锡点、助焊。
外观检查作业指导书
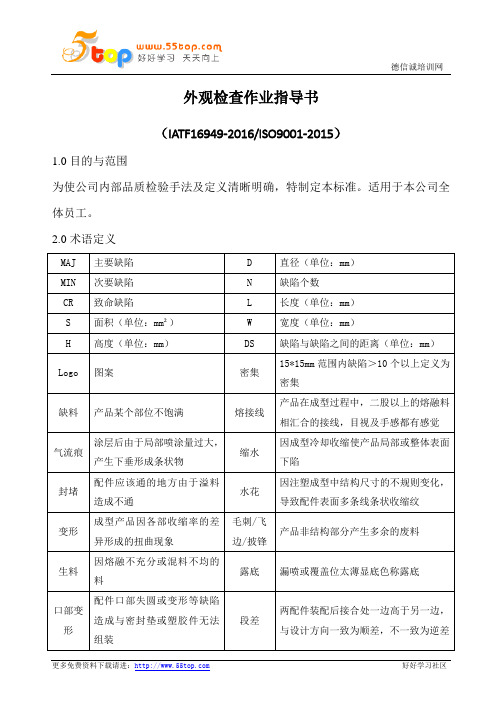
外观检查作业指导书(IATF16949-2016/ISO9001-2015)1.0目的与范围为使公司内部品质检验手法及定义清晰明确,特制定本标准。
适用于本公司全体员工。
2.0术语定义MAJ 主要缺陷 D 直径(单位:mm)MIN 次要缺陷N 缺陷个数CR 致命缺陷L 长度(单位:mm)S 面积(单位:mm²)W 宽度(单位:mm)H 高度(单位:mm)DS 缺陷与缺陷之间的距离(单位:mm)Logo 图案密集15*15mm范围内缺陷>10个以上定义为密集缺料产品某个部位不饱满熔接线产品在成型过程中,二股以上的熔融料相汇合的接线,目视及手感都有感觉气流痕涂层后由于局部喷涂量过大,产生下垂形成条状物缩水因成型冷却收缩使产品局部或整体表面下陷封堵配件应该通的地方由于溢料造成不通水花因注塑成型中结构尺寸的不规则变化,导致配件表面多条线条状收缩纹变形成型产品因各部收缩率的差异形成的扭曲现象毛刺/飞边/披锋产品非结构部分产生多余的废料生料因熔融不充分或混料不均的料露底漏喷或覆盖位太薄显底色称露底口部变形配件口部失圆或变形等缺陷造成与密封垫或塑胶件无法组装段差两配件装配后接合处一边高于另一边,与设计方向一致为顺差,不一致为逆差间隙装配时形成的缝与设计时固有的缝的叠加针孔/气泡由于喷涂、电镀或成型造成的气泡破裂产生的小孔白印由于内应力,在产品表面产生与本色不同的白色痕迹杂色/黑点与配件本身颜色不同的杂点或混入原料中的杂点暴露在表面上断裂配件材料局部断开后的不合格流纹产品表面上以浇口为中心而呈现出的年轮状条纹划伤因受外力作用造成的刮痕,分为有感和无感划伤磨痕产品因碰撞摩擦后所留下的痕迹烧焦塑胶件模温过高或五金件抛光局部温度过高造成的配件表面烧焦,局部发黄发黑缺陷色差材料差异及加工过程造成的颜色变化,使两个及以上相邻配件的表面有目视颜色差别麻点表面附着的有感的细小颗粒掉漆配件表面处理不当等原因造成的喷漆后液体脱落3.0职责3.1 工程:产品功能的标准制定。