《极限配合与尺寸公差》公差原则讲解
4极限与配合制基础(2)
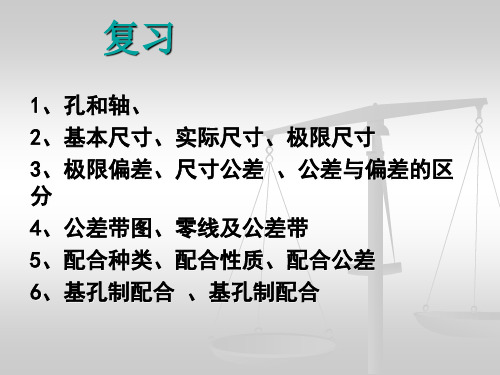
公差等级— 确定尺寸精确程度的等级 不同的零件或零件上不同部位的尺寸,对精确程度的要求往往不 相同的,为此,极限与配合制对标准公差规定了20个等级以满足 生产需要。 标准公差代号用符号IT和公差等级数字表示。 I—ISO T—— Tolerance公差的缩写 如IT8(IT+数字) 当其与代表基本偏差的字母一起组成公差带时省略IT字母如H8
复习
1、孔和轴、 2、基本尺寸、实际尺寸、极限尺寸 3、极限偏差、尺寸公差 、公差与偏差的区 分 4、公差带图、零线及公差带 5、配合种类、配合性质、配合公差 6、基孔制配合 、基孔制配合
互换性与测量技术
第四讲 2.1极限与配合制基础(2) --尺寸的公差与配合
第二章 尺寸极限与配合 2.1极限与配合制基础(1)--基本术语及其定义 2.1 2.1极限与配合制基础 极限与配合制基础(2)-(2)--尺寸的公差与配合 尺寸的公差与配合 2.2光滑孔、轴的公差与配合设计(1) 2.2光滑孔、轴的公差与配合设计(2) 2.3 其他尺寸公差带规定
补充实例
在实际应用中,标准公差值可直接查表2-1,而不必另行计算。 查表时要注意①尺寸分段 ②公差单位 ③表格附注
2.1极限与配合制基础(2)--尺寸的公差与配合
一、标准公差系列 二、基本偏差系列 二、基本偏差系列 三、极限与配合在图样上的标注 四、一般、常用和优先的公差带与配合
二、基本偏差系列
(大间隙以及 大多数过盈配 合需要加中间 段落)如补充 表所示
又如课本表2-1所示的标准公差教值表的基本尺寸为主要段落
2-1
1800.1-2009
4. 基本尺寸分段
基本尺寸分段后,标准公差是按尺寸分段中首尾两个尺寸的几何 平均值来计算 例如在>50~80mm尺寸段内 D=(50×80)1/2=63.25mm 同一尺寸段内的所有基本尺寸都规定同样的标准公差因子。按首 尾两个尺寸(D1和D2)的几何平均值代入式(2-1)或(2-2)计 算公差因子及用式IT=αi计算公差值
极限配合与测量技术-公差原则

按两者关系的不同,相关要求又分为包容要求和最大实体 要求。
1.包要求
(1)包容要求的涵义。
包容要求是尺寸要素的非理想要素不得违反其最大实体边界
的一种尺寸要素要求。
该理想形状极限包容面的尺寸等于最大实体尺寸时称为最大实体 边界。
差也不能超出给定的直线度公差
0.01mm。
图3.7 对直线误差进一步限制
单一要素遵守包容要求,检测时必须按极限尺寸判断原则(泰
勒原则)来判定,即用通端极限量规控制被测要素的作用尺寸不得超 越最大实体边界;
用两点法测量(包括用不全形止规)提取组成要素的局部尺寸, 使其不得超越最小实体尺寸。
关联要素遵守包容要求,检测时用综合量规(其测量部分模拟
与基准平面B保持垂直的最大 实体边界,如图3.6(b)所示。
根据包容要求的合格条件可知:
图3.6 关联要素遵守包容要求
当零件的内孔直径处处均为最大实体尺寸20mm时,垂直度 误差必须是零,其作用尺寸才不会超越最大实体边界;
当内孔的实际(组成)要素偏离最大实体尺寸为 (20+)mm时,
其偏离量 即为垂直度误差的允许值,如图3.6(c)所示;
它们各自是独立的,只有两者同时满足要求,销轴才合格;
否则,其中有一项超出了,即为废品。
2.图样标注、检测和应用 独立原则在图样上的标注不需附加任何表示相互关系的符
号,如图3.4所示。
按独立原则要求的零件,其实际(组成)要素按两点法测量,通 常使用千分尺、游标卡尺或卡规等;
几何误差需采用通用量具或量仪单独测出具体数值,而不能采用 综合量规。
2.最大实体要求
第二章 尺寸极限与配合

2. 偏差、公差与公差带
1)
第 二 章 尺 寸 极 限 与 配 合
2)
下
第 二 章 尺 寸 极 限 与 配 合
极限尺寸、公差与偏差
3)公差带 第 二 章 尺 寸 极 限 与 配 合
在公差带图解中,由代表上偏差和下偏差 的两条直线所限定的一个区域称为公差带
ES + 0 基本尺寸
TD Td
EI es ei
δmax
二
δmax
孔
Smax
第
轴
3)配合公差:组成配合的孔、 3)配合公差:组成配合的孔、轴公差之和 配合公差 第 二 章 尺 寸 极 限 与 配 合 ∣Smax-Smin∣ -(EI- ) = - -( Tf= ∣Smax-δmax∣=|ES-ei-( -es)|=TD+Td |δmin-δmax |
第 二 章 尺 寸 极 限 与 配 合
孔或轴允许的最大尺寸称为最大极限尺寸; 孔或轴允许的最小尺寸称为最小极限尺寸 孔和轴的最大极限尺寸分别用Dmax和dmax表示, 最小极限尺寸分别用Dmin和dmin表示。
尺寸合格条件: 尺寸合格条件:
Dmin≤Da≤Dmax dmin≤da≤dmax
最小极限尺寸
公差 最大最小极 T(mm) 限或过盈
Smax或 δmin Smin或 δmax
(mm) Max
1 2 3
孔 轴 孔 轴 孔 轴
20
20.033 19.980
20.000 19.959 40.000 40.017 59.949 59.981
+0.033
0 -0.041 0 +0.017 -0.051 -0.019
度、中心距等
3)基本尺寸:通过它并应用上、下偏差可算出极限尺寸的尺寸。它可
尺寸公差和极限偏差
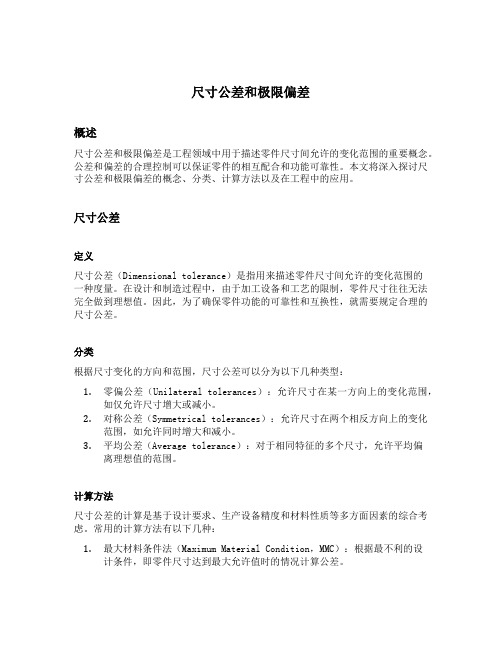
尺寸公差和极限偏差概述尺寸公差和极限偏差是工程领域中用于描述零件尺寸间允许的变化范围的重要概念。
公差和偏差的合理控制可以保证零件的相互配合和功能可靠性。
本文将深入探讨尺寸公差和极限偏差的概念、分类、计算方法以及在工程中的应用。
尺寸公差定义尺寸公差(Dimensional tolerance)是指用来描述零件尺寸间允许的变化范围的一种度量。
在设计和制造过程中,由于加工设备和工艺的限制,零件尺寸往往无法完全做到理想值。
因此,为了确保零件功能的可靠性和互换性,就需要规定合理的尺寸公差。
分类根据尺寸变化的方向和范围,尺寸公差可以分为以下几种类型:1.零偏公差(Unilateral tolerances):允许尺寸在某一方向上的变化范围,如仅允许尺寸增大或减小。
2.对称公差(Symmetrical tolerances):允许尺寸在两个相反方向上的变化范围,如允许同时增大和减小。
3.平均公差(Average tolerance):对于相同特征的多个尺寸,允许平均偏离理想值的范围。
计算方法尺寸公差的计算是基于设计要求、生产设备精度和材料性质等多方面因素的综合考虑。
常用的计算方法有以下几种:1.最大材料条件法(Maximum Material Condition,MMC):根据最不利的设计条件,即零件尺寸达到最大允许值时的情况计算公差。
2.最小材料条件法(Least Material Condition,LMC):根据最不利的设计条件,即零件尺寸达到最小允许值时的情况计算公差。
3.中间材料条件法(Median Material Condition,MMC):根据设计要求和生产设备的精度范围,计算公差使得零件可以在各种材料条件下都保持功能和互换性。
示例假设某个机械零件的设计尺寸为50mm,要求尺寸公差为±0.1mm。
根据对称公差原则,该零件允许尺寸在50mm±0.1mm的范围内变化,即实际尺寸可以在49.9mm和50.1mm之间。
2.2公差与配合国家标准

2.2 公差与配合国家标准
标准公差 (表2-4)
标 准 公 差 数 值 表
11
2.2 公差与配合国家标准
2 基本偏差系列
1) 基本偏差(基本偏均指靠近零线的偏差,与公差等级无关)及其
代号 标准对轴和孔各规定了28个公差带位置,分别由28个基本偏 差表示。 基本偏差代号用英文字母表示。小写代表轴,大写代表孔。 在26个字母中去掉5个容易混淆的字母I(i)、L(l)、O(o)、 Q(q)、W(w),增加7个双写字母CD(cd)、EF(ef)、FG(fg) 、JS(js)、ZA(za)、ZB(zb)、ZC(zc),作为基本偏差代号, 共有28个代号。
下偏差 EI/µm
上偏差 ES/µm
基本偏差
JS
基
A B C CD D E EF F FG G H
J
K
M
N
本 基本尺寸 偏 /mm
公
差
等
级
差 大于 至
所有公差等级
6 7 8 ≤8 >8 ≤8 >8 ≤8 >8
数 值 ( 孔
3 +270 +140 +60 +34 +20 +14 +10 +6 +4 +2 0 上 +2 +4 +6 0 0 -2 -2 -4 -4 3 6 +270 +140 +70 +46 +30 +20 +14 +10 +6 +4 0 偏 +5 +6 +10-1+Δ -4+Δ -4 -8 +Δ 0 6 10 +280 +150 +80 +56 +40 +25 +18 +13 +8 +5 0 差 +5 +8 +12-1+Δ -6+Δ -6 -10+Δ 0
尺寸公差与配合

5.2. GB/T4458.5—2003 机械制图尺寸公差与配合注法5.2.1 概述完整地看,“GB/T4458.5—2003 机械制图尺寸公差与配合标注”只是“极限与配合”知识领域中比较具有表现意义的一个如何标注的标准,故有必要大致认识一下“极限与配合”。
5.2.1.1.极限与配合概念极限与配合属于几何精度中尺寸精度的范畴。
极限与配合概念的产生、建立与发展与大工业的发展密切相关,并与社会的技术经济相联系。
18世纪后半期,以机器为主体的工厂逐渐代替以手工为主体的工场,零件的生产由以前的单件或小批量,发展到必须大批量可以“互换性”的生产。
“互换性”要求同一批零件的尺寸不必绝对一致准确,而只要求尺寸在某一合理的范围之内即可以保证一批零件可以不加挑选地“配合”,这里的尺寸的合理范围,即是尺寸“公差”的萌芽。
允许尺寸的最大最小值,即是尺寸的极限。
5.2.1.2.极限与配合标准化随着资本主义大工业的快速发展迫切要求零部件“互换性”的范围要扩大。
1902年,英国的一家名为纽瓦尔(Newall)的公司制定并出版了一本《纽瓦尔标准—极限表》,这是现在看到的最早的极限与配合制。
1906年,英国发布了“极限与配合”的国家标准“B.S.27”。
1925年,英国出版的《A.S.A.B4a》中,包括了“极限与配合”的内容。
1962年,ISO正式发布了“ISO/R286—1962 极限与配合第1部分公差与偏差”。
其后至今,又相继发布了一系列相关标准,开始了新“极限与配合”制。
1959年,中国发布了“GB159~174—1959 公差与配合”,是参考原苏联标准制定的,属于旧的“极限与配合”制。
1979年中国发布了第二部“GB1800~1804—1979 公差与配合”,这套标准采用了当时国际上最先进的新“极限与配合”制,ISO“极限与配合”制是由“标准公差系列”和“基本偏差系列”组成,对“公差带位置”和“公差带大小”分别进行标准化,形成了“基孔制”或“基轴制”下的“间隙配合”、“过盈配合”或“过渡配合”,只可惜当时未下决心把名字改为“极限与配合”,却仍叫“公差与配合”。
尺寸的公差配合
4)在基孔制配合中: H/a-h为间隙配合, H/j-n为过渡配合, H/p-zc为过盈配合。 在基轴制配合中: A-H/h为间隙配合, J-N/h为过渡配合, P-ZC/h为过盈配合。
公差带代号
公差带的代号由基本偏差代号与公差等级代号 组成,如H7、h6、M8、d9等等。在图样上标 注尺寸公差时,可以标注极限偏差,(上偏差 放在基本尺寸的右上角,下偏差放在基本尺寸 0.025 0.025 500 、 500.041 的右下角,例);如: ,也可以 标注尺寸公差带代号,如:ø 50H7、 ø 50f6或 者两者都标注ø 50H7 ( +0.025 0 )、 -0.025 ø 50f6( -0.041 ) 。
2.偏差 1)定义:某一尺寸减去其基本尺寸所得的代数 差(为正或为负,为零 )称为尺寸偏差(简称 偏差)。 2)实际偏差:实际尺寸减去其基本尺寸所得的 代数差称为实际偏差。 3)极限偏差:极限尺寸减其基本尺寸所得的代 数差。
(1)上偏差:最大极限尺寸减去其基本尺寸所 得的代数差称为上偏差。孔的上偏差用ES表 示;轴的上偏差用es表示。 (2)下偏差:最小极限尺寸减去其基本尺寸所 得的代数差称为下偏差。孔的下偏差用EI表 示;轴的下偏差用ei表示。 (3)偏差:某一尺寸减去其基本尺寸所得的代 数差称为偏差
2)基本尺寸分段 GB进行了尺寸分段 ,同一尺寸分段内的所有 基本尺寸,只要公差等级相同就规定了同一 标准公差值. GB将≤500mm的尺寸分成了13个尺寸段。 3)标准公差值 特点:同一尺寸段,随公差等级的下降,数值越 来越大;同一公差等级,随尺寸段的增大,数值 越来越大.
三.基本偏差 定义:用以确定公差带相对于零线位置的上偏 差或下偏差,称为基本偏差。一般为公差带靠 近零线的那个偏差为基本偏差。 1.基本偏差系列 国标对孔轴分别规定了28种基本偏差,其代 号用拉丁字母表示,大写表示孔,小写表示轴。 如图所示
公差原则的名词术语及公差原则
公差原则的名词术语及公差原则:(根据“ GD &T(形位公差 )简解陈一士”整理)1.公差原则的名词术语1.1问题的提出图 1图 2设计人员绘制图1、 2 孔、轴配合之目的是:要求这一对零件的最小间隙为0、最大间隙为0.034。
但当孔和轴尺寸处处都加工到 20 时,由于存在形状误差,则装配时的最小间隙将不可能为0。
这就产生了线性尺寸公差与形位公差之间的关系问题。
1.2 有关术语为了明确线性尺寸公差与形位公差之间关系,对尺寸术语将作进一步论述与定义。
1.2.1局部实际尺寸—在实际要素的任意正截面上,两对应点之间测得的距离。
(图3)图 3特点:一个合格零件有无数个。
1.2.2作用尺寸A 体外作用尺寸—在被测要素的给定长度上,与实际内表面(孔 )体外相接的最大理想面(轴 ) ,或与实际外表面(轴 )体外相接的最小理想面(孔 )的直径或宽度。
(图4)图 4B 体内作用尺寸—在被测要素的给定长度上,与实际内表面 (孔 ) 体内相接的最小理想面 (轴 ) ,或与实际外表面 (轴 )体内相接的最大理想面 (孔 )的直径或宽度。
(图 5)图 51.2.3最大实体状态(MMC) 和最大实体尺寸(MMS)A最大实体状态 (MMC) —实际要素在给定长度上处处位于尺寸极限之内,并具有实体最大(即材料最多 )时的状态。
B最大实体尺寸 (MMS) —实际要素在最大实体状态下的极限尺寸。
内表面 (孔 ) D MM =最小极限尺寸 D min;外表面 (轴 ) d MM=最大极限尺寸 d max。
1.2.4 最小实体状态 (LMC)和最小实体尺寸 (LMS)A最小实体状态 (LMC) —实际要素在给定长度上处处位于尺寸极限之内,并具有实体最小(即材料最少 )时的状态。
B最小实体尺寸 (LMS) —实际要素在最小实体状态下的极限尺寸。
内表面 (孔 ) D LM = 最大极限尺寸 D max;外表面 (轴 ) d LM = 最小极限尺寸 d min。
公差与配合的选择原则
二、极限与配合的选用
计算法选择配合 若两工件结合面间的过盈或间隙量确定后,可以通 过计算并查表选定其配合。根据极限间隙(或极限过 盈)确定配合的步骤是: 1) 首先确定基准制, 2) 根据极限间隙(或极限过盈)计算配合公差, 3) 根据配合公差查表选取孔、轴的公差等级, 4) 按公式计算基本偏差值, 5) 反查表确定基本偏差代号, 6) 校核计算结果。
活塞 连杆 过渡配合 活塞销 + 0 _ m6 H7 g6 m6
+ 0 _
fD
G7
M7
h6
M7
Байду номын сангаас
间隙配合
教材图2-16基准制选择示例(一)
fD
过渡配合
(4)与标准件配合的基准制选择 若与标准件(零件或部件)配合,应以标准件为 基准件、来确定采用基孔制还是基轴制。 如平键、半圆键等键联接,由于键是标准件, 键与键槽的配合应采用基轴制;滚动轴承外圈与箱 体孔的配合应采用基轴制,滚动轴承内圈与轴的配 合应采用基孔制。
极限与配合的选择原则:实质上是尺寸的精度设计。
圆柱结合的精度设计
圆柱结合的精度设计实际上就是圆柱结合 的公差与配合的选用,它是机械设计与制造中 至关重要的一环,公差与配合的选用是否恰当, 对机械的使用性能和制造成本有着很大的影响。 圆柱结合的精度设计包括:
配合制的选用 公差等级的选用 配合的选用
配合制的选用
二、极限与配合的选用
配合种类的选择 本质:在确定了基准制的基础上,根据使用 中允许间隙或过盈的大小及变化范围,选定非 基准件的基本偏差代号。有的配合同时确定基 准件与非基准件的公差等级。 方法:1.计算法 2.试验法 3.类比法
二、极限与配合的选用
《极限配合与尺寸公差》公差原则
第二部分 形状和位置公差及其检测 3.最小实体要求(LMR)
定义:控制被测要素的实际轮廓处于其最小实体实效边界 之内的一种公差要求。 标注:在被测要素形位公差框格中的公差值后标注符号 “L” 。应用于基准要素时,应在形位公差框格内 的基准字母代号后标注符号“ L ”。 应用:适用于中心要素。主要用于需保证零件的强度和 壁厚的场合。 边界:最小实体实效边界。即:体内作用尺寸不得超出 最小实体实效尺寸,其局部实际尺寸不得超出最 大实体尺寸和最小实体尺寸。 DLV=DL±t 内表面为“+”,外表面为“-”。
Lmin 是孔的最小极限尺寸;
lmax 是轴的最大极限尺寸。
轴:
式中:La、la 分别是孔、轴的实际尺寸;
(2)最大实体要求应用于基准要素
当最大实体要求应用于基准要素时,在形位公差框格内的基准字母后标注符号M。 最大实体要求应用于基准要素时,形位公差值是在基准处于最大实体尺寸时给定 的,当基准要素偏离其最大实体尺寸时,被测要素的形位公差值得到补偿。
面取“-” 。
最大实体实效边界:尺寸为最大实体实效尺寸的边界。
6)最小实体状态和最小实体尺寸 最小实体状态(LMC):指提取要素在给定长度上处处 位于尺寸极限之内并具有最小实体时的状态。 最小实体尺寸(LMS):指提取要素在最小实体状态下 的极限尺寸。 对于内表面为最大极限尺寸,对于外表面为最小极限 尺寸。即:
1.独立原则的含义及特点
(1)尺寸公差仅控制要素的局部实际尺寸,不控制其形 位误差。 (2)给出的形位公差为定值,不随要素的实际尺寸变化 而改变。 (3)形位误差的数值采用通用量具测量。
2.独立原则的应用
第二部分 形状和位置公差及其检测
一、独立原则概念
1、定义:图样上给定的每一个尺寸和形状、位置要求 均是独立的,应分别满足要求。
- 1、下载文档前请自行甄别文档内容的完整性,平台不提供额外的编辑、内容补充、找答案等附加服务。
- 2、"仅部分预览"的文档,不可在线预览部分如存在完整性等问题,可反馈申请退款(可完整预览的文档不适用该条件!)。
- 3、如文档侵犯您的权益,请联系客服反馈,我们会尽快为您处理(人工客服工作时间:9:00-18:30)。
Lm in 是孔的最小极限尺寸;
lm a x是轴的最大极限尺寸。
(2)最大实体要求应用于基准要素
当最大实体要求应用于基准要素时,在形位公差框格内的基准字母后标注符号M。 最大实体要求应用于基准要素时,形位公差值是在基准处于最大实体尺寸时给定 的,当基准要素偏离其最大实体尺寸时,被测要素的形位公差值得到补偿。
应用较多,在有配合要求或虽无配合要求,但有功能 要求的几何要素都可采用。适用于尺寸精度与形位精度要求 相差较大,需分别满足要求,或两者无联系,保证运动精度、 密封性,未注公差等场合。
测量:应用独立原则时,形位误差的数值一般用通用量具 测量。
三、相关要求
相关要求是指图样上给出的尺寸公差与形状公差相互有 关的设计要求。它分为包容要求、最大实体要求、最小实体 要求和可逆要求。可逆要求不能单独采用,只能与最大实体 要求或最小实体要求联合使用。
最大实体尺寸(MMS):指提取要素在最大实体状态下 的极限尺寸。
对于外表面为最大极限尺寸,对于内表面为最小极限 尺寸。即:
MMS(孔): Lm ax ,
MMS(轴): lm in 。
第二部分 形状和位置公差及其检测
5)最大实体实效状态和最大实体实效尺寸 最大实体实效状态(MMVC):图样上给定的被测要素的
3)体内作用尺寸(Dfi、dfi) 是在被测要素的给定长度上,与实际内表面(孔)体内相 接的最小理想面,或与实际外表面(轴)体内相接的最大理 想面的直径或宽度,称为体内作用尺寸(如图所示)。
第二部分 形状和位置公差及其检测
4)最大实体状态和最大实体尺寸
最大实体状态(MMC):指提取要素在给定长度上处处 位于尺寸极限之内并具有实体最大时的状态。
2.最大实体要求(MMR)
定义:控制被测要素的实际轮廓处于其最大实体实效 边界之内的一种公差要求。
标注:在被测要素形位公差框格中的公差值后标注符 号“M” 。应用于基准要素时,应在形位公差 框格内的基准字母代号后标注符号“ M”。
应用:适用于被测中心要素和基准中心要素。 主要用于不需要配合场合。
边界:最大实体实效边界。即:体外作用尺寸不得超 出最大实体实效尺寸,其局部实际尺寸不得 超出最大实体尺寸和最小实体尺寸。
第二部分 形状和位置公差及其检测
第二部分 形状和位置公差及其检测
(1)最大实体要求应用于被测要素
最大实体要求应用于被测要素,应在图样中标注符号M.当实际尺寸偏离 最大实体尺寸时,允许形位误差值超出给定公差值。用尺寸公差补偿给形位 公差值。公式如下:
t允 t给 t增
式中:t允 — 形位公差允许达到的数值;
t给 — 图样上给定的形位公差值;
t增 — 零件实际尺寸偏离最大实体尺寸时形位公差获得的补偿值。
由上式所示,允许的形位公差值,不仅取决于图样上给定的公差值,也 与零件的相关要素的实际尺寸有关。
第二部分 形状和位置公差及其检测
孔、轴增大值的计算公式为
孔: t增 La Lmin
轴: t增 lm ax la
1、包容要求
(1)包容要求的定义及特点 定义:实际要素应遵守最大实体边界,其局部实际
尺寸不得超过最小实体尺寸。 标注:在单一要素尺寸极限偏差或公差带代号之后
加注符号“E ” 应用:适用于单一要素。主要用于需要严格保证配
合性质的场合。 边界:最大实体边界。 测量:可采用光滑极限量规(专用量具)。
第二部分 形状和位置公差及其检测
(2)给出的形位公差为定值,不随要素的实际尺寸变化 而改变。
(3)形位误差的数值采用通用具测量。
2.独立原则的应用
第二部分 形状和位置公差及其检测
一、独立原则概念
1、定义:图样上给定的每一个尺寸和形状、位置要求 均是独立的,应分别满足要求。
2、标注:
第二部分 形状和位置公差及其检测 二、独立原则的应用
第二部分 形状和位置公差及其检测
形位公差和尺寸公差都是控制零件精度的两类不同性 质的公差。它们彼此是独立的,但在一定条件下,二者又 是相关并互相补偿。形位公差在某种条件可以用尺寸公差 补偿的称为最大实体要求;在某种条件下不能用尺寸公差 补偿的称为独立原则。
1.独立原则的含义及特点
(1)尺寸公差仅控制要素的局部实际尺寸,不控制其形 位误差。
位于尺寸极限之内并具有最小实体时的状态。 最小实体尺寸(LMS):指提取要素在最小实体状态下
的极限尺寸。 对于内表面为最大极限尺寸,对于外表面为最小极限
尺寸。即:
LMC(孔): L max
LMS(轴): l min
第二部分 形状和位置公差及其检测
7)最小实体实效状态和最小实体实效尺寸 最小实体实效状态(LMVC):在给定长度上,实际尺寸
第二部分 形状和位置公差及其检测
3.最小实体要求(LMR)
定义:控制被测要素的实际轮廓处于其最小实体实效边界 之内的一种公差要求。
标注:在被测要素形位公差框格中的公差值后标注符号 “L” 。应用于基准要素时,应在形位公差框格内 的基准字母代号后标注符号“ L ”。
最大实体尺寸。 最大实体实效尺寸(MMVS):和该要素轴线、中心平面
的定向或定位形位公差所形成的综合极限状态。 MMVS:最大实体实效状态下的体外作用尺寸。 MMVS=MMS±t形·位 其中:对外表面取“+”;对内表
面取“-” 。 最大实体实效边界:尺寸为最大实体实效尺寸的边界。
6)最小实体状态和最小实体尺寸 最小实体状态(LMC):指提取要素在给定长度上处处
要素处于最小实体状态,且其中心要素的形状或位置误差等 于给出公差值时的综合极限状态。
最小实体实效尺寸(LMVS):最小实体实效状态下的体 内作用尺寸。
LMVS=LMS ± t形·位(其中:对外表面取“-”;对内表 面取“+”)。
最小实体实效边界:尺寸为最小实体实效尺寸的边界。
第二部分 形状和位置公差及其检测
(2)有关术语及定义 1)局部实际尺寸(Da、da):实际要素的任意正截面上,
两对应点间测得的距离(如图所示)。 2)体外作用尺寸(Dfe、dfe):在被测要素的给定长度
上,与实际内表面(孔)体外相接的最大理想面,或与实际 外表面(轴)体外相接的最小理想面的直径或宽度,称为体 外作用尺寸,即通常所称作用尺寸(如图所示)。