日本精益生产研修汇报
赴日本三菱重工培训总结及心得体会

管理融于细节, 成功缘于持续改善——赴日本三菱重工研修汇报2011年7月3日~16日, 我带领22名优秀基层管理干部、1名翻译共赴日本三菱重工进行为期两周的现场管理专题培训, 三菱重工对本次培训高度重视, 在培训内容、培训资料、培训师资、培训日程等方面给予精心准备和妥善安排。
期间, 对三菱重工安全管理、质量管理、生产管理、技能教育管理等业务内容进行研修, 分别到三菱高砂制作所、神户三菱电机生产制造现场进行实地参观, 学员在培训期间诚恳谦虚、勤奋好学的态度获得三菱重工高度评价, 培训取得了圆满成功。
现简要总结并汇报如下:一、三菱重工概况三菱重工的前身可以追溯到明治维新年间, 以修船、造船为主业, 发展至1934年, 业务已拓展至重型机械、飞机、铁路车辆等领域, 公司由此更名为三菱重工业株式会社。
1950年被分割成了东日本、中日本、西日本重工业株式会社, 1964年三家重工业株式会社合并, 重建三菱重工株式会社发展至今。
期间, 三菱重工于1970年分离出“三菱自动车工业株式会社”, 1995年三菱核能工业株式会社加入, 至此三菱重工真正发展成当今规模庞大的企业涵盖能源装备、新能源、船舶、航空航天、轨道交通、船用柴油发电机、化工炼油成套设备、饮料装置、印刷、汽车、医疗设备、机器人、海水淡化、深潜等领域。
拥有14个事业所、6个研究所, 8家分公司, 10家海外事务所或代表处。
本次培训所在的三菱重工高砂制作所位于日本宾库县高砂市, 1962年从神户造船所分立, 开始作为一个专业公司研究设计制造涡轮机发展至今, 隶属于三菱重工原动机事业本部, 注册资本2656亿日元, 占地面积980500平方米, 建筑面积223206平方米, 截止2011年3月31日员工人数为4341人, 主要产品为火电、水电、核电发电机组, 燃气轮机, 泵, 制冷系统, 加热及冷却系统等, 年生产能力为燃汽轮机30台、火电及核电汽轮机各2台。
工匠计划赴日研修第三批汇报(置地工程管理之道)
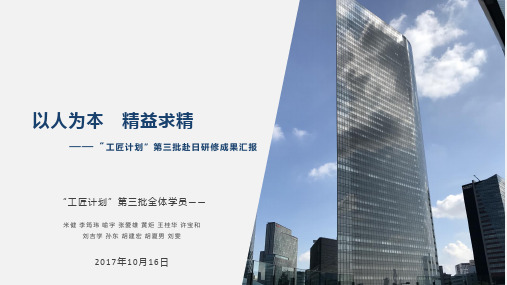
材料按生产线摆放
钢筋分色管理
砼试块分色管理
模板、配筋检查
混凝土坍落度试验
成品构件
20
3 日本工程精细化管理
01 技术 装配式工法——技术领先
超高层PCa施工法 Sky Park House西新宿塔项目,地下2层,地上60层,总建筑面积10万m2,
• 东京都港区 白金台 • 东茨木项目 • 横滨 户塚品浓町
销售展示3个
880项目
5
1 研修概述
日本学习期间,每人每天整理心得体会,当天晚上11点前发给领队,既巩固了当天所学知识,又能在班内及时交流 讨论。
6
Part 2
日本印象
2 日本印象
“以人为本”的理念体现在社会的方方面面,所有设施、设备、服务均着眼于人与环境的和协共生,造就了日本整
可移动马桶
方便坐轮椅人士使用 的洗手台
人性化设计
可折叠长臂花洒
集中安放方便使用
竖向拉手
人体工学尺度体验
灯光设计合理
12
2 日本印象
居中对缝,横平竖直,简洁美观。
圆顺挺直
居中对缝
幕墙成像清晰
美观精致
简洁美观 13
Part 3
日本工程精细化管理
01 技术 02 管理
3 日本工程精细化管理
什么是精细化管理?
屋面保温板,太阳直射时顶棚温 度仅为35度左右
采用超细微水珠(直径10-30um ) 替换式空调,室内2米高度以下范
喷雾降温,室温可减低4度
围进行冷气循环
屋面设置通气孔,形成室内外空 气流通
工厂内用采光板,和节能灯相比, 可以增加照度,同时降低成本
无需使用电力的自动门, 节省能源
“精益生产与敏捷制造技术高级研修班”总结

“精益生产与敏捷制造技术高级研修班”总结“精益生产与敏捷制造技术高级研修班”总结2019年8月25日-9月7日,本人参加了中船集团赴日“精益生产与敏捷制造技术高级研修班”,培训主要包括丰田的GPS生产方式理论与实操培训、日本知名企业参观学习两大内容。
系统全面剖析了丰田精益生产理念,精益制造在汽车行业的应用,针对性的现场改善实战演练和精益制造标杆企业的参观交流。
现将学习情况总结如下:一、学习总结丰田的生产方式又称TPS,而GPS理念则是在TPS的基础上关注人财的育成而发展起来,GPS注重与企业经营管理系统地无缝链接,其核心是通过省人和彻底消除浪费,实现高效高质低成本的生产方式。
GPS生产方式的2大核心为准时化生产(Just in time)和自働化(Jidoka),准时化是指把必要的物品在必要的时候,只按要求的数量进行生产和搬运,最终实现成本的控制,避免浪费;自动化则是当设备发生异常问题时,不需要人工操作,让设备、生产线自动停止的生产机制,强调人与机械的完美结合。
GPS生产追求一人工的工作实质,提高赋予产品附加值的动作,减少其余的动作浪费,通过改善省人,来提高具有附加值工作的比率,实现更加有效地工作。
培训期间,系统深入了解了GPS生产方式在丰田汽车制造各环节的应用,丰田GPS通过后工序领取、后补充生产,把前后工序有效连接起来,着重针对看板在后工序领取的作用及功能,如何使用进行了讲解,开展了工厂看板管理模拟运行和标准作业改善实战演练,真实模拟了丰田公司任务计划的制定、原材料采购、生产加工、运输等关键过程运行,通过看板管理和标准作业改善模拟运行实战训练,强化了以后工序生产为导向的看板管理系统、GPS不浪费、防纠错等内容的理论学习,更深入理解了以最少浪费的作业顺序,确保安全和品质,通过有效率的作业组合,来实现高效率的生产的方法,导入GPS精益生产的精髓。
丰田公司及日本标杆企业实地参观与交流期间,在丰田及其子公司车间现场,机器人、机械手臂有条不紊运作;各种物料小车按指令和程序,穿梭在各工位流程,机器和人的有机完美合作,标准化作业让人震惊。
赴日本丰田培训后总结心得体会

丰田印象
实操训练
对焊接作业流程进行改善,根据课
刹车装置流水生产线实习
题设定的客户需求,通过分解操作步骤,
通过流线化生产线实操,
观测手工作业、步行及设备自动加工时
对4个工位的操作步骤进行分解、
间,开展工序能力分析,绘制当前标准
重排,应用工序能力分析、标准
作业组合票,并查找出生产线存在的改
善点。按照分析结果,设定了改善目标,标准作业练习
.
丰田式生产管理哲理的理论框架
准时化(JIT-Just in time)生产。即以市场为龙头 在合适的时间、生产合适的数量和高质量的产 品,JIT需要以拉动生产为基础,以平准化 (Leveling System)为条件。所谓拉动生产是以看 板管理为手段,采用“取料制”即后道工序根 据“市场”需要进行生产,对本工序在制品短 缺的量从前道工序取相同的在制品量,从而形 成全过程的拉动控制系统,绝不多生产一件产 品。平准化是指工件的被拉动到生产系统之前 要进行人为的按照加工时间、数量、品种进行 合理的搭配和排序,使拉动到生产系统中的工 件流具有加工工时上的平稳性,保证均衡生产, 同时在品种和数量上实现混流加式运动,起到 对市场多品种、小批量需要的快速反应和满足 功能。
.
学习历程
一、 走进丰田
三、 丰田智慧
二、 丰田印象
四、 丰田启示
.
走进丰田
日本印象
此次在日本研修学习历时21天、两个城市,其中,在名古屋 丰田精益生产管理培训中心株式会社(MIC-J)研修学习14天, 东京7天,历经了GPS(丰田生产系统+人、财)生产方式基础知 识理论培训、道场实习和工厂参观,期间参观了岐阜车体精工工 厂、丰田高冈工厂、旭自动车工业株式会社、龟山铁工厂、须琦 工厂、 朝日新闻株式会社、东京都厅、NPO法人富士见教育交流 中心、麒麟啤酒工厂、东京湾物流港、东京燃气公司等企业,实 地考察了精益生产在各类团体的实践,并就精益生产体系化推进 不全面、不均衡、精益工具方法运用不深入、精益改善技法、精 益人才育成等问题与丰田公司相关人员做了深入交流,近距离走 进丰田,实地感受丰田几十年如一日孜孜不倦的持续改善,不断 提升产品制造水平和产品质量,减少浪费降低成本,应该说收获 很大。
第二组日本研修汇报(主讲人 李建树)
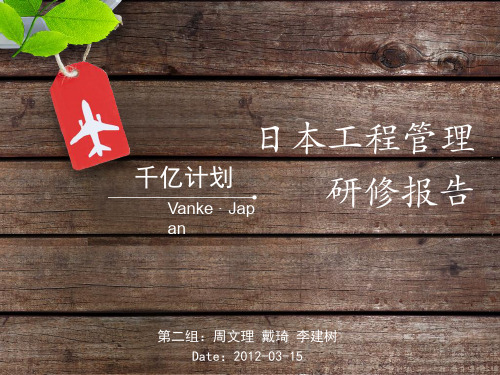
②
“工会”自主管理
职长会定期组织会议分配各会社轮 值,进行环境清理、材料堆放、卫生间 保洁、安全标识、车辆管理等工作、组 织活动增加班组间的融合,从下而上的 参与项目管理。
③
PART2
定尺加工
在日本,大到PC构件,小到水管、 电线工厂定尺加工,都是住宅工业化的 一种实现方式,目的都是为了施工提效。
⑥
排水管
铸铁排水管用锡箔纸包裹,外有隔音毡, 最后用铁丝网固定。排水管防水作法简单, 两张锡箔纸封堵排水管底部,从上面灌注无 收缩浆料即可。排水管管道井100mm、架空地面的120mm,在 220mm的空间内实现同层排水,日本进入老年社会, 整体卫生间地面与其他房间标高相同。
⑯
柔性连接管
配合高层建筑结 构基础免震隔震,管 线采用柔性连接。
⑰
双道止水层
为配合精装提前插入,现场设置两道止 水层,方法包括:预留套筒上部低于混凝土 完成面20mm,降板位置预留排水孔、外廊兼 作雨水收集,用临时雨落塑料管收集雨水等。
⑱
PART3
住宅产品说明书
内容 建造、销售、管理体系
售后服务 管理计划 结构设计 设备设计 室内环境 空气环境
安防系统 防灾策略 厨房收纳空间 卫浴部品 无障碍设计 网络环境 住宅性能评价
①
售后服务标准(部分参考)
保
部位、设 备
现象
修 时
间
屋顶、屋
漏雨
10
面阳台 排水不畅、膨胀 2
外部扶手、 晾衣架、 破损、掉漆 2
隔板等
漏水、排水不畅、 卫生设备 破损、使用不良、 2
安装问题
浴室设备
漏水
5
(整体浴
日本丰田精益研修之旅(B团)7.doc
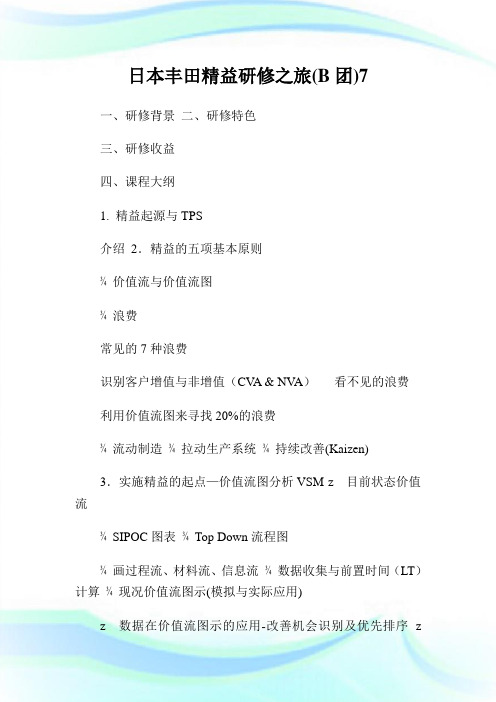
日本丰田精益研修之旅(B团)7一、研修背景二、研修特色三、研修收益四、课程大纲1. 精益起源与TPS介绍2.精益的五项基本原则¾价值流与价值流图¾浪费常见的7种浪费识别客户增值与非增值(CV A & NV A)看不见的浪费利用价值流图来寻找20%的浪费¾流动制造¾拉动生产系统¾持续改善(Kaizen)3.实施精益的起点—价值流图分析VSM z 目前状态价值流¾SIPOC图表¾Top Down流程图¾画过程流、材料流、信息流¾数据收集与前置时间(LT)计算¾现况价值流图示(模拟与实际应用)z 数据在价值流图示的应用-改善机会识别及优先排序z改善后的过程–未来状态价值流图示¾什么使价值流精益¾改善目标确定¾没有浪费的精益过程¾未来价值流图示(模拟与实际应用) z 过程价值流改善工具的检讨(案例) 4.精益工具的应用介绍¾5S 及目视管理5S 及目视管理介绍实施5S 的意义、计划、方法和步骤目视管理的应用¾快速换模与缩短前置时间前置工作与快速换模的价值分析快速换模及缩短前置时间的工具与方法¾TPM 改善理解OEE 及计算方法如何计划和实施TPM 工作¾拉动系统和看板Kanban,拉动式生产的支持系统介绍拉动系统设计案例KANBAN 卡的使用方法库存策略和解析批量¾标准化作业为什么需要标准化作业标准化作业实施方法¾Poka-YokePoka-Yoke 概念Poka-Yoke 的过程和步骤¾生产线设计柔性制造单元精益设备的选择员工多技能单件及小批量物流5.精益生产评估和衡量6.精益生产实例介绍五、行程安排当日主题:如何建立自己公司特色的生产方式第一天行程详细内容地点8:30-12:00 精益生产培训(主讲:汤纪国)上海酒店会议室12:00-13:00 午餐13:00-17:30 精益生产培训(主讲:汤纪国)第二天行程详细内容地点上午坐国际航班抵达日本国名古屋市,乘专用大巴前往下榻酒店,办理入住手续晚餐住宿酒店爱知县/ 丰田市HOTEL TOYOTA CASTLE (四星)第三天行程详细内容地点8: 30 - 9: 00开班仪式明确研修目的事务说明9: 00 - 12: 00 日本管理专家TPS 培训1 丰田生产方式概要2 如何建立独自的生产方式酒店会议室12: 00 - 13: 00 午餐13: 30 - 16: 00 丰田汽车总装厂优秀现场参观1 学习TPS 在丰田是如何运用的2 TPS 管理工具实物观摩3 丰田新款车试乘4 丰田企业文化体验16: 30 - 18: 00 日本管理专家培训本日总结,答疑酒店会议室18: 00 - 20: 00 晚餐住宿酒店爱知县/丰田市HOTEL TOYOTA CASTLE(四星)。
工厂精益生产工作总结汇报
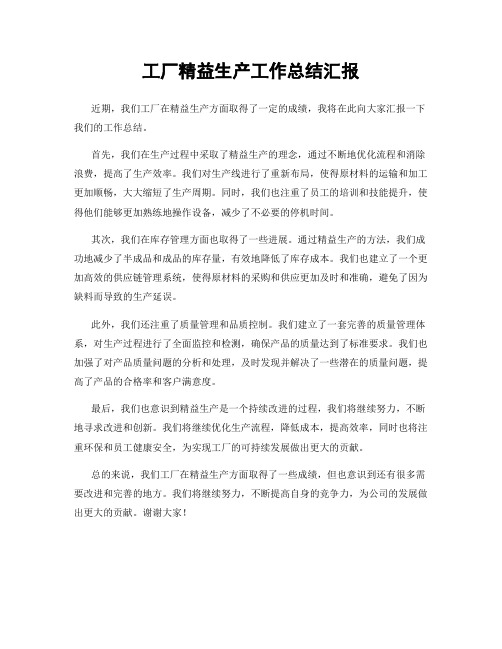
工厂精益生产工作总结汇报
近期,我们工厂在精益生产方面取得了一定的成绩,我将在此向大家汇报一下我们的工作总结。
首先,我们在生产过程中采取了精益生产的理念,通过不断地优化流程和消除浪费,提高了生产效率。
我们对生产线进行了重新布局,使得原材料的运输和加工更加顺畅,大大缩短了生产周期。
同时,我们也注重了员工的培训和技能提升,使得他们能够更加熟练地操作设备,减少了不必要的停机时间。
其次,我们在库存管理方面也取得了一些进展。
通过精益生产的方法,我们成功地减少了半成品和成品的库存量,有效地降低了库存成本。
我们也建立了一个更加高效的供应链管理系统,使得原材料的采购和供应更加及时和准确,避免了因为缺料而导致的生产延误。
此外,我们还注重了质量管理和品质控制。
我们建立了一套完善的质量管理体系,对生产过程进行了全面监控和检测,确保产品的质量达到了标准要求。
我们也加强了对产品质量问题的分析和处理,及时发现并解决了一些潜在的质量问题,提高了产品的合格率和客户满意度。
最后,我们也意识到精益生产是一个持续改进的过程,我们将继续努力,不断地寻求改进和创新。
我们将继续优化生产流程,降低成本,提高效率,同时也将注重环保和员工健康安全,为实现工厂的可持续发展做出更大的贡献。
总的来说,我们工厂在精益生产方面取得了一些成绩,但也意识到还有很多需要改进和完善的地方。
我们将继续努力,不断提高自身的竞争力,为公司的发展做出更大的贡献。
谢谢大家!。
【日本研修】日本研修学精益,道场实训看改善
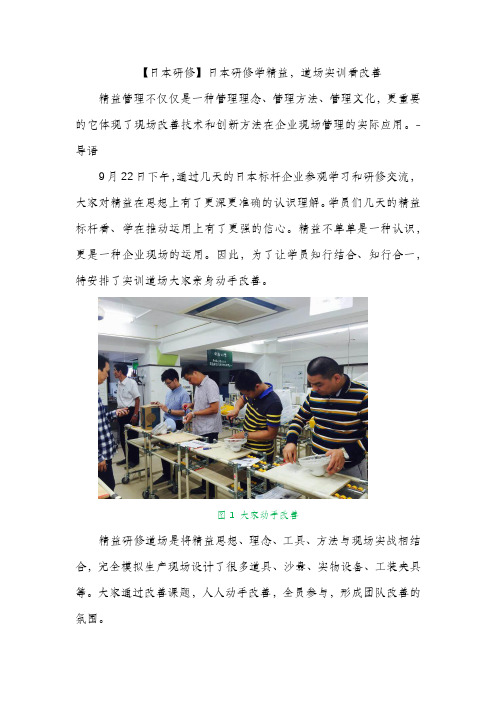
【日本研修】日本研修学精益,道场实训看改善精益管理不仅仅是一种管理理念、管理方法、管理文化,更重要的它体现了现场改善技术和创新方法在企业现场管理的实际应用。
-导语
9月22日下午,通过几天的日本标杆企业参观学习和研修交流,大家对精益在思想上有了更深更准确的认识理解。
学员们几天的精益标杆看、学在推动运用上有了更强的信心。
精益不单单是一种认识,更是一种企业现场的运用。
因此,为了让学员知行结合、知行合一,特安排了实训道场大家亲身动手改善。
图1大家动手改善
精益研修道场是将精益思想、理念、工具、方法与现场实战相结合,完全模拟生产现场设计了很多道具、沙盘、实物设备、工装夹具等。
大家通过改善课题,人人动手改善,全员参与,形成团队改善的氛围。
图2 改善前后的节拍时间
学员本次动手亲自改善,改善前需要5人才能完成的工作,通过改善动作和工装夹具达到只需要3.5人就能完成,真正达到省人化目的。
图3学员顺利完成改善获得研修证书
通过道场改善实训,大家对改善有了更深的认识-改善不是生产
员工的专利,而是全员参与的常规性、持续性活动,改善,从小的细节开始,以小见大,最终企业形成改善魂。
学员研修感受(摘抄)
下午的丰田生产模式TPS实训收益良多,总结:1、TPS生产模式追求在不增加成本的情况,通过改善动作和工装夹具,达到省人化少人化。
2、通过TPS改善把节省下来的优秀人员有改善思维的人员加入改善团队,而不是简单的优胜略汰。
3、丰田强调领导作用,提倡管理到现场带动大家做改善。