分解炉缩口结皮的原因分析及解决措施
【免费下载】分解炉频繁结皮原因分析及处理

分解炉频繁结皮原因分析及处理-中国水泥技术网2009-5-23 作者: 瞿学坤刘飞姚公放,义煤集团水泥公司,河南渑池472411我公司5000t/d生产线于2006年6月26日投料试生产,其中分解炉采用喷—旋结合形成复合流场的炉型。
投产后,分解炉频繁结皮严重影响生产。
1 结皮情况每次结皮均在分解炉的4根三风道燃烧器周围并向分解炉锥体延伸,向上可到分解炉直段都有结皮,严重影响窑风入炉,造成分解炉燃烧器出口堵塞,分解炉多处发生过红炉,甚至造成窑系统无法运行而停产。
由于分解炉结皮严重造成停窑清理6次,每次清理费时费力,安全性极差,最长的一次清理用了5d。
窑运转率极低,最长的运转1个半月左右,最短的只有10d。
2原因分析该生产线最初设计使用长焰煤和贫瘦煤搭配的燃料,分解炉锥体上对称分布着4根法国皮拉德公司产的三风道燃烧器,用来强化煤粉在分解炉内的燃烧。
正式生产时考虑整个系统的适应能力,生产用原煤是陕西神木产优质烟煤,挥发分在25%~30%,与最初设计差别较大。
因燃烧器与下料点位置相距较远,煤粉燃烧放出的热能不能迅速被物料吸收,在炉锥体较小的空间形成局部高温造成结皮,甚至红炉;其次就是系统处于试生产,各种设备、电气故障多,开停窑次数较多,加上中控操作水平不熟练,导致分解炉温度波动大产生结皮。
3第一次改造及预防措施3.1 改造方案1)取消4号燃烧器(即三次风入炉口右侧第一根),改为3根燃烧器供煤;3根燃烧器位置均向上提高1m;旋转角度由原来的20°改为0°;水平夹角由原来的30°改为10°;3根燃烧器与分解炉的中心的定位角度不变;燃烧器头部伸出炉浇注料表面300mm(改造示意见图1)。
图1 分解炉改造示意2)C4下料管撒料盒位置不变,用浇注料在撒料盒板体上浇注一个斜坡,即改现有板体与水平夹角15°为30°。
3.2 预防措施1)关小三次风,加强分解炉的喷腾效应。
分解炉锥部结皮的影响及处理

分解炉锥部结皮的影响及处理摘要:近年来,新型干法生产线预热器锥部及下料管处结皮堵塞很少,但烟室和分解炉锥部结皮仍然较多。
本文从对分解炉锥部结皮的原因及特征的分析入手,进而对其结皮现象产生的影响及处理方法进行了相关论述,希望能够起到抛砖引玉的作用。
关键词:分解炉锥部结皮影响处理一、概述我公司2500/d生产线于2012年5月2日点火试生产。
采用的是喷旋结合的管道炉炉内采用的两个直筒式燃烧器。
投产后,随产量的增加,分解炉锥部结皮愈来愈严重。
造成窑内产生还原气氛,煤粉不完全燃烧。
在投产后一个半月里因分解炉解皮停窑四次每次都要耽误生产12小时以上,开始在预热器锥体开了三个200×200的门子用人工清结皮而只是能够维持不停,清理十分危险,并且漏风严重,影响到热工制度的稳定,严重影响了熟料的生产质量,针对上述情况我公司积极联系设计院于2012年6月中旬进行了一系列的调整和技改。
二、分解炉锥部结皮原因及特征分析分解炉结皮,与生料中碱含量有关,有关方面测定,结皮中K20含量占10%左右。
同时与分解炉温度控制有关,一般炉温控制在900℃左右,就很少出现熔块和结皮现象,一旦超过950℃,炉内物料粘性增加,容易造成Ⅳ级下料管堵塞。
为保证分解炉正常工作,炉温不要控制过高,CaCO3,分解率也没必要达到100%,控制在85%~90%即可。
通常情况下,分解炉锥部结皮较为严重, 一般情况下,3~4天就需停窑处理。
其结皮主要发生在分解炉三次风入口至进料口之间部位, 见图1。
根据结皮与物料成分分析情况表明,结皮主要是由煤灰渣熔结其它物料而形成大块。
一般来说,分解炉锥体部位煤灰渣结皮的形成主要是由以下两方面原因造成的:A、燃煤的焦渣特征情况,只有焦渣特征值大于一定等级时方能形成具有一定强度的煤渣结皮;B、分解炉内燃料起火预燃速度快,炉内存在偏流造成锥体部位温度场分布不均、局部高温。
但此类结皮的分布特征是在分解炉锥体内衬局部位置形成结皮。
分解炉缩口结皮的原因分析及解决措施

(2)三次风闸板烧坏。我公司三次风是从窑头罩抽取的,其中的熟料细颗粒没有经过旋风沉降,会不断冲刷三次风闸板上的浇注料。浇注料被磨损后闸板上的耐热钢板经不住900℃以上的热风的烘烧而烧坏。由于三次风阀板烧坏,窑内通风与三次风分配平衡被破坏,窑内通风量减小,窑头加煤温度上不去,形成还原气氛,产生黄心料。同时,三次风量明显增加,使预燃炉风速加快。由于无烟煤燃尽时间较长,风速增加造成煤粉在预燃炉滞留时间变短,煤粉被带至预燃炉出口处附近煅烧,形成炉中温度较低,而出炉温度较高的“温度倒挂”现象,引起分解炉下缩口结皮严重,导致分解炉出口与五级下料管负压增高。此时,为保证熟料质量,只得降低产量生产。
1.3 窑炉用煤比例不当
当分解炉缩口结皮严重且清烟室用的高压水枪出现故障时,有的操作员为了使熟料f-Ca0量合格,采取了加大窑头用煤量的强烧办法。结果窑尾废气带入分解炉的热量过高,势必减少分解炉用煤量,使入窑生料分解率降低,分解炉不能发挥应有的作用;同时窑内还原气氛加剧,煤粉不完全燃烧现象更严重,使分解炉缩口结皮进一步增多。
2.2 合理用风
在喂料量不变的情况下,三次风闸板开度加大,能增加分解炉燃烧空气量,降低了系统阻力;同时相应增加分解炉用煤量,有利于尾煤的充分燃烧,提高了入窑生料CaCO3分解率。正常生产情况下,我公司三次风闸板开度一般控制在55%~65%。
当三次风闸板烧坏后,运转期内,为了完成当月的生产任务,可以采用向三次风管内扔耐火砖的办法,以改变窑炉的风量分配;系统检修时,则应及时对烧坏的三次风闸板进行更换处理。
2.3 保持合适的窑、炉用煤比例
窑头用煤量的大小主要是依据入窑生料的喂料量和CaCO3分解率、生料易烧性、熟料f-CaO和升重、窑速及窑皮等因素来确定的。分解炉用煤量主要是根据入窑生料分解率、生料易烧性、分解炉出口气体温度来调节的。如果风量分配合理、入炉煤粉燃烧充分,但分解炉出口气体温度偏低,入窑生料分解率低,C5出口气体温度低,这说明分解炉用煤量过少,应增加。如果预分解系统温度偏高,热耗增加,甚至出现分解炉内煤粉燃尽率低,煤粉到C5内继续燃烧,导致预分解系统产生结皮或堵塞,这说明分解炉用煤量过多,应降煤。
分解炉锥部结皮原因分析及解决措施

管
通 过对 水 泥 窑 、预 热 器 系 统 的详 细 检 查 发 现 ,预 热
器旋风筒 、分解炉上部都没有结皮 ,但分解炉锥部靠
三 次风 管 沿燃 烧 器旋 流 方 向 3/4圈 结 皮 严 重 ,最 严
重处结皮厚度达到800mm左右 ,高度达到4m左右 , 分 解 炉缩 口结 皮达 到 1/3左右 。
4 效 果
(编辑 :刘翠荣 )(收稿 日期 :2012—05—25)
通过 以上改造及参数的调整 ,水泥窑开启后运
(上 接 第 3页 )
系统 烘 干 。
储存一定的物料 ,可 以延长待料时间 ;三是辊压机可
(4)缺陷情况 。辊压机功率为 3 350kW的减速 视情况关 闭气动阀止料 ,减少工作压力 ,使辊压机空
分解炉 炉锥体浇注料基本平齐(见 图 1),同时燃烧 窑头喂煤量过多 ,窑内煤粉的燃尽率较差 ,窑内出现
器位置正好处于三次风进分解炉处 (见 图2)。在运 后结圈 ,窑 内通风状况变差 ,未燃尽的煤粉与物料粘 行过程 中,窑尾煤粉经燃烧器 喷出后遇到高温富氧 附在烟室及分解炉缩 口形成结皮。
宋宏 昌:分解炉锥部 结皮原因分析及 解决措施
-一 一 臻#臻 孽≯i甍蹲秀鼙甏§毫0 誊叠曩_劳
囊棼鬣蒜磐 |薯
中图分类号 :TQ172.62 文献标识码 :B 文章 编号 :1007—0389(2013)0l一40—02
分解炉锥部结皮原 因分析及解决措施
宋 宏 昌(青海祁连山水泥有限公司,青海 西宁810021)
2 原 因分 析
图2 燃烧器、三次风管位置
式 计 算 ,当地 大 气 压 力 72.633 kPa,是 海 平 面 的 71.68% ;大 气 密 度 1.031 kg/m’,是 海 平 面 的
窑尾烟室、缩口结皮的原因及解决措施

仁鑫煤较稳定,而通金瑞煤稳定性差,匕d波动较 大。匕d低的煤粉,着火温度高,燃烧速度缓慢, 使部分头煤被带到窑尾烟室和缩口处集中燃烧,导 致该部位温度过高而引起结皮。从操作参数看,结
皮严重期间,窑尾烟室温度达到1 100七左右,这 就进一步加剧了低熔点矿物提前出现液相,为恶化 结皮创造了条件。
2.3硫碱比的影响
项目
结皮样 入窑生料
熟料
烧失量
1.41 35.27 0.49
SiO2
9.30 12.57 21.89
表1窑尾烟室结皮料与生料、熟料全分析对比
Ag
Fe2O3
CaO
MgO
£0
3.51
1.88
57.05
1.61
5.03
2.75
2.25
45.02
1.48 0.18
5.01
3.18
67.06
2.31
0.37
Na.0
生料、熟料及结皮料硫碱比数据见表5。
表5生料、熟料及结皮料的硫碱成分及硫碱比
项目 so3 /% £0/% Na/)/% R2O/% S/R
0.54 0.02 0.04
S03
19.07 0.06 0.39
% z 99.40 99.36 100.25
47
2020年第2期 No.2 2020
李桦溶,等:窑尾烟室、缩口结皮的原因及解决措施
矿物组成/% C3S C2S C3A 67.46 11.86 7.91
表2系统结皮期间熟料的矿物组成及物理性能
25结皮部位浇注料的影响我公司窑尾烟室和分解炉缩口使用碳化硅抗结皮浇注料由于烟室缩口结皮清理频繁使一部分浇注料表面损坏变得粗糙不平这也为结皮的附着创造了条件铁3采取的针对性技术改进措施31加强进厂原煤的管理强化原煤的均化工作加强了对进厂原煤工业分析检验对挥发分较低的煤停止购进同时抓好原煤搭配工作增加堆料层数严格采用横堆竖取方式减少堆端效应引起的离析现象以确保煤粉质量的稳定
分解炉结皮原因的分析及处理

分解炉结皮原因的分析及处理我公司分解炉于2004年8月20日至9月底期间,结皮严重并且掉结皮堵三次风管多次,造成窑热工制度不稳、投料低、能耗高,甚至造成停窑事故的发生,严重影响生产。
现将前一阶段出现的分解炉结皮问题作一简要分析,供同行参考。
1 、炉型及工艺特性:我公司分解炉的炉型属于史密斯公司的SLC-S型,根据SLC型分解炉的流场分布来看,其基本上属于喷射流,并且喷射流的基本特征:轴向风速大,切向和径向风速很小,并且随着与炉体中心线距离的增大,轴向风速逐步降低,特别分解炉下锥体部位,在锥体边缘位置轴向风速锐减。
由于轴向风速的变化,在炉体内部形成紊乱的流场结构并存在立涡,一方面也造成物料分布产生区域性不均匀(立涡区),同样也造成燃料在喷射燃烧的同时形成涡旋。
2 、结皮及分解炉检查情况:2004年8月20日至9月底期间,分解炉频繁出现结皮并脱落,多次检查均发现分解炉下锥体部位周围结皮,严重时撒料箱位置的结皮已和扬料板持平,喷煤管两侧结皮厚达30~50cm。
根据塌落的结皮及入炉检查,结皮外观属多孔状熔渣,其间夹裹松散粉状料粉形成大块,在炉内检查时发现结皮松散、易脱落。
3 、结皮原因分析:根据结皮与物料成分分析情况表明,结皮主要是由煤灰渣溶解其他物料而形成的大块。
我厂分解炉下锥体结皮的分布情况及结皮形成时各物料成分、理化性能情况表明,我厂结皮及其形成具以下特征:3.1结皮产生主要由煤灰渣溶解其他物料而形成的大块。
3.2 结皮产生时分解炉锥体部位物料分布较为均匀,但喷煤管处偏厚一些,且结皮速较快。
3.3 结皮产生期间燃煤的焦渣特性值均在5以上,且入窑煤灰分均在38~43%,发热量小于5000千卡/千克.煤。
3.4 分解炉出口负压升高500~600Pa,出口温度由850~890ºC升高到950~1000ºC;分解炉锥部温度由于结皮包裹而下降,锥部压力下降。
根据以上特征各种物料分析表(1~4)及分解炉运行现象,可以充分说明我厂分解炉锥体部位结皮的原因如下:我厂的燃煤灰分较高,发热量较低,挥发分较正常,煤在分解炉内燃烧属辉焰燃烧,从外观观察火焰浊红。
浅析分解炉结皮原因及处理措施

浅析分解炉结皮原因及处理措施
白银涛
【期刊名称】《河南建材》
【年(卷),期】2012(000)003
【摘要】综合分析了我公司分解炉锥体结皮的原因,提出处理措施,认为生产中加强操作,加强工艺管理,合理配料,有效控制原燃料有害成分,避免结皮。
【总页数】2页(P159-160)
【作者】白银涛
【作者单位】邓州中联水泥有限公司,474150
【正文语种】中文
【中图分类】TQ172.622
【相关文献】
1.水泥预分解系统的结皮、积料和堵塞的原因及处理措施浅析 [J], 邓德新
2.1000t/d预分解窑预热器结皮原因及处理措施 [J], 张淑广
3.分解炉锥部结皮原因分析及解决措施 [J], 宋宏昌
4.TSD分解炉预燃炉结皮原因及预防 [J], 史高勇
5.分解炉锥部结皮的原因与处理 [J], 楼美善;王广杰
因版权原因,仅展示原文概要,查看原文内容请购买。
TSD分解炉预燃炉结皮原因及预防
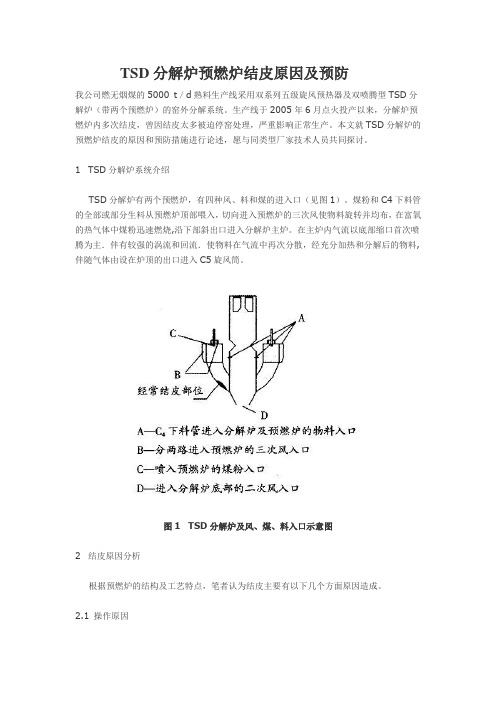
TSD分解炉预燃炉结皮原因及预防我公司燃无烟煤的5000 t/d熟料生产线采用双系列五级旋风预热器及双喷腾型TSD分解炉(带两个预燃炉)的窑外分解系统。
生产线于2005年6月点火投产以来,分解炉预燃炉内多次结皮,曾因结皮太多被迫停窑处理,严重影响正常生产。
本文就TSD分解炉的预燃炉结皮的原因和预防措施进行论述,愿与同类型厂家技术人员共同探讨。
1 TSD分解炉系统介绍TSD分解炉有两个预燃炉,有四种风、料和煤的进入口(见图1)。
煤粉和C4下料管的全部或部分生料从预燃炉顶部喂入,切向进入预燃炉的三次风使物料旋转并均布,在富氧的热气体中煤粉迅速燃烧,沿下部斜出口进入分解炉主炉。
在主炉内气流以底部缩口首次喷腾为主.伴有较强的涡流和回流.使物料在气流中再次分散,经充分加热和分解后的物料,伴随气体由设在炉顶的出口进入C5旋风筒。
图1 TSD分解炉及风、煤、料入口示意图2 结皮原因分析根据预燃炉的结构及工艺特点,笔者认为结皮主要有以下几个方面原因造成。
2.1 操作原因(1)预燃炉温度控制太高,物料发粘,容易结皮。
由于使用无烟煤作燃料,其着火温度高,再加上三次风温不稳定,因此为使窑尾煤粉能完全燃烧,要控制预燃炉有较高的温度。
但往往因为热电耦反映的温度不准或是操作员经验不足(如调节幅度过大造成分到预燃炉的料太少、对预燃炉内的温度变化预知不敏感)等原因,使预燃炉温度过高而导致物料提前出现液相而造成结皮(结皮部位见图1)。
(2)入预燃炉三次风量不足。
预燃炉是蜗壳旋流进风,三次风从切向进入,形成高速旋转气流逐渐向下推进物料。
如果风量小,则风速低,形不成旋流,或是旋流速度低而中途短路,那预燃炉就差不多是沉降室,容易在边壁、拐角积料甚至结皮。
我们在预燃炉中部检查孔处就经常能发现疏松结皮,而且有10 cm左右厚,应该就是风量不足造成的。
如果旋流风速很大,风是贴着边壁走的,足可以“飞砂走石”,不会在中部直筒部分形成结皮。
影响三次风量的因素除三次风门开度外,还有就是三次风管内的积灰量,积灰太多阻力变大,通风量就会减小。
- 1、下载文档前请自行甄别文档内容的完整性,平台不提供额外的编辑、内容补充、找答案等附加服务。
- 2、"仅部分预览"的文档,不可在线预览部分如存在完整性等问题,可反馈申请退款(可完整预览的文档不适用该条件!)。
- 3、如文档侵犯您的权益,请联系客服反馈,我们会尽快为您处理(人工客服工作时间:9:00-18:30)。
分解炉缩口结皮的原因分析及解决措施
2009-5-27作者: 江超,郝延辰,朱建妨
0 前言
河南新乡平原同力水泥有限责任公司(以下简称“我公司”)第一条5000t/d水泥熟料生产线于2005年4月上旬建成投产运行。
2006年4月该生产线分解炉缩口结皮严重,使系统通风量减小,造成窑内产生还原气氛和煤粉不完全燃烧。
采用加大拉风后,则增大了高温风机的电耗,且把烧成带向窑尾移动,导致熟料提前成球而结粒偏大,黄心料、欠烧料较多。
据统计,此时熟料叫w(f-CaO)值平均在2.0%左右,28 d强度约降低5 MPa,严重影响了熟料产质量。
采取相应措施后,分解炉缩口结皮很少,熟料产量大幅度提高、质量明显好转。
1 分解炉缩口结皮原因分析
1.1煤质的影响
我公司原煤采用低挥发分无烟煤(煤的工业分析见表1)。
原煤的供应商较多(少时有3家,最多时有7~8家)。
为了降低成本,允许供应商在满足我公司原煤各项质量指标要求的前提条件下对原煤进行搭配调整。
但在经济利益的驱动下,有的供应商会掺加一些价格低廉的高硫煤。
虽然进厂混合煤全硫含量(质量分数)控制都小于1.5%,但混合煤可能是由含硫量差别不大的三
种煤组成,也可能是由低含硫量煤[w(S
bad )=0.3%~0.5%]与高含硫量煤[w(S
bad
) =3.5%~
4.0%]与其他煤按比例混合而成,这在煤的工业分析中是难以分析清楚的。
若是后者且均化措施又不到位,那高硫煤燃烧时,在无旁路放风的情况下,在硫和碱反应达到平衡后还有过剩,过剩的硫会在分解炉缩口形成致密的结皮。
表1 煤粉工业分析
M ad /% V
ad
/% A
ad
/% S
bad
/% Q
net,ad
/(kJ·kg-1)
1.38 10.57 30.71 1.91 2345
2.68
另外,煤粉细度偏粗也是造成分解炉缩口结皮的原因之一。
因对正常运行中的回转窑来说,在燃烧温度和系统通风量基本稳定的情况下,煤粉的燃烧速度与煤粉的挥发分、灰分、水分含量和细度有关。
在选定矿点原煤后,煤粉的挥发分、灰分和水分含量基本固定,则煤粉细度成为满足特定燃烧工艺的关键参数。
但煤粉若磨得过细,不仅增加电耗,还容易引起煤粉的自燃和爆炸。
根据天津水泥工业设计研究院烧无烟煤煤粉的细度经验公式:R=V/2-(0.5~1.0)。
我公司煤粉细度控制指标确定为5.0%以下,但实际煤粉细度经常偏粗(一般在5.2%~6.4%之间,特别是煤粉仓仓位低的时候为了快速增加仓位,煤粉细度会达到8.0%)。
1.2 窑炉风量不平衡
(1)三次风闸板开度过小。
窑和分解炉用风量是通过窑尾三次风闸板开度来调节的。
2006
年4月,我公司三次风闸板开度正常生产情况下一般控制在30%~35%。
窑头、窑尾负压比较大、窑内火焰较长、窑尾烟室温度较高(一般在1130℃)、分解炉用煤量增加时炉温有所下降,窑皮偏长。
这说明此时三次风闸板开度过小、窑内通风量偏大。
(2)三次风闸板烧坏。
我公司三次风是从窑头罩抽取的,其中的熟料细颗粒没有经过旋风沉降,会不断冲刷三次风闸板上的浇注料。
浇注料被磨损后闸板上的耐热钢板经不住900℃以上的热风的烘烧而烧坏。
由于三次风阀板烧坏,窑内通风与三次风分配平衡被破坏,窑内通风量减小,窑头加煤温度上不去,形成还原气氛,产生黄心料。
同时,三次风量明显增加,使预燃炉风速加快。
由于无烟煤燃尽时间较长,风速增加造成煤粉在预燃炉滞留时间变短,煤粉被带至预燃炉出口处附近煅烧,形成炉中温度较低,而出炉温度较高的“温度倒挂”现象,引起分解炉下缩口结皮严重,导致分解炉出口与五级下料管负压增高。
此时,为保证熟料质量,只得降低产量生产。
1.3 窑炉用煤比例不当
当分解炉缩口结皮严重且清烟室用的高压水枪出现故障时,有的操作员为了使熟料f-Ca0量合格,采取了加大窑头用煤量的强烧办法。
结果窑尾废气带入分解炉的热量过高,势必减少分解炉用煤量,使入窑生料分解率降低,分解炉不能发挥应有的作用;同时窑内还原气氛加剧,煤粉不完全燃烧现象更严重,使分解炉缩口结皮进一步增多。
2 采取的措施
2.1 稳定煤质
首先,根据原煤的煤质、价格及供应商的信誉等因素确定2~3家作为长期稳定的供应商;其次,加强原煤的进厂质量检验,避免或减少使用高硫煤(如必须使用高硫煤,则应加强原煤预均化和均化工作);第三,降低煤粉筛余控制指标,由5.0%降低到3.0%,并在生产中严格控制,以提高煤粉的燃尽率。
2.2 合理用风
在喂料量不变的情况下,三次风闸板开度加大,能增加分解炉燃烧空气量,降低了系统阻力;同时相应增加分解炉用煤量,有利于尾煤的充分燃烧,提高了入窑生料CaCO
分解率。
正常
3
生产情况下,我公司三次风闸板开度一般控制在55%~65%。
当三次风闸板烧坏后,运转期内,为了完成当月的生产任务,可以采用向三次风管内扔耐火砖的办法,以改变窑炉的风量分配;系统检修时,则应及时对烧坏的三次风闸板进行更换处理。
2.3 保持合适的窑、炉用煤比例
窑头用煤量的大小主要是依据入窑生料的喂料量和CaCO
分解率、生料易烧性、熟料f-CaO
3
和升重、窑速及窑皮等因素来确定的。
分解炉用煤量主要是根据入窑生料分解率、生料易烧性、分解炉出口气体温度来调节的。
如果风量分配合理、入炉煤粉燃烧充分,但分解炉出口气体温度偏低,入窑生料分解率低,C5出口气体温度低,这说明分解炉用煤量过少,应增加。
如果预分解系统温度偏高,热耗增加,甚至出现分解炉内煤粉燃尽率低,煤粉到C5内继续燃烧,导致预分解系统产生结皮或堵塞,这说明分解炉用煤量过多,应降煤。
操作中,窑炉用煤比例取决于入窑生料分解率、生料易烧性、窑速及燃料的特性等。
一般情况下,窑头用煤控制在40%~45%、分解炉用煤控制在60%~55%时比较合适。
杜绝出现窑炉用煤比例倒置现象,应注意。
2.4 扩大分解炉主炉下缩口
预分解窑窑尾气体成分表征了窑内燃料的燃烧状况及窑内的通风情况。
要求既不能使燃料
在空气不足的情况下燃烧而产生大量CO,又不能有过多的过剩空气而增大热耗。
一般控制窑尾烟气中φ(O
2
)为1.0%~l.5%比较合理。
我公司分解炉主炉下缩口原设计尺寸为φ2050 mm。
但在实际生产中,由于结皮较多造成缩口实际尺寸变小(2006年4月21日停窑检修时,实测尺寸仅为φl900 mm),窑内因通风量减小
而产生还原气氛(窑尾烟室气体成分分析显示φ(CO)=3%,φ(O
2
)=0.8%~0.2%)。
由于窑内
氧气不足,使Fe
2O
3
变成Fe0,液相提前出现、料容易在窑内结大球产生黄心料,影响熟料质量;
同时也限制了产量的提高。
此时中控操作员为了使f-Ca0合格,往往采用关小三次风闸板、加大窑头用煤量的办法。
虽能暂时加大窑内通风、提高烧成带温度,但三次风闸板关得过小,必然造成预燃炉内的风量减小,使低挥发分无烟煤在炉内燃烧不完全。
导致分解炉出口及C5下料管温度偏高,造成窑尾烟室、分解炉下缩口结皮严重并再次产生黄心料形成恶性循环,最终不得已减产煅烧。
后来曾采用高压水枪清理烟室及分解炉下缩口(每班两次),高温风机拉风到900 r/min(进口风压-6700Pa),也未能从根本上解决问题。
经过研究,决定将主炉下缩口扩大,并于2006年底利用检修时间实施。
改造时,将主炉下缩口膨胀节更换,使其净尺寸扩大到φ2400mm。
更换后没有出现塌料现象,窑内通风明显好转。
2.5 其他措施
降低分解炉出口气体温度油895℃降低到880~885℃),避免尾温过高,液相提前出现形成结皮;清理结皮要少时多次,既要减小清理结皮对煅烧温度的影响,又要防止结皮因清理不及时越结越厚;采用新型耐火材料,在分解炉缩口使用抗结皮浇注料。
3 结语
通过采取以上措施,特别是扩大主炉下缩口后,我公司分解炉缩口结皮很少,窑内通风明显好转,熟料日产量由5000t提高到5500~5800t,熟料强度明显提高(3 d抗压强度稳定在32MPa,28 d扰压强度由53~55MPa提高到62MPa)。
这说明提高窑内通风量,同时保证分解炉内的风量不减小,对于预防和减少分解炉下缩口结皮、提高产量和改善质量,效果非常明显。