分解炉结皮原因分析
【免费下载】分解炉频繁结皮原因分析及处理

分解炉频繁结皮原因分析及处理-中国水泥技术网2009-5-23 作者: 瞿学坤刘飞姚公放,义煤集团水泥公司,河南渑池472411我公司5000t/d生产线于2006年6月26日投料试生产,其中分解炉采用喷—旋结合形成复合流场的炉型。
投产后,分解炉频繁结皮严重影响生产。
1 结皮情况每次结皮均在分解炉的4根三风道燃烧器周围并向分解炉锥体延伸,向上可到分解炉直段都有结皮,严重影响窑风入炉,造成分解炉燃烧器出口堵塞,分解炉多处发生过红炉,甚至造成窑系统无法运行而停产。
由于分解炉结皮严重造成停窑清理6次,每次清理费时费力,安全性极差,最长的一次清理用了5d。
窑运转率极低,最长的运转1个半月左右,最短的只有10d。
2原因分析该生产线最初设计使用长焰煤和贫瘦煤搭配的燃料,分解炉锥体上对称分布着4根法国皮拉德公司产的三风道燃烧器,用来强化煤粉在分解炉内的燃烧。
正式生产时考虑整个系统的适应能力,生产用原煤是陕西神木产优质烟煤,挥发分在25%~30%,与最初设计差别较大。
因燃烧器与下料点位置相距较远,煤粉燃烧放出的热能不能迅速被物料吸收,在炉锥体较小的空间形成局部高温造成结皮,甚至红炉;其次就是系统处于试生产,各种设备、电气故障多,开停窑次数较多,加上中控操作水平不熟练,导致分解炉温度波动大产生结皮。
3第一次改造及预防措施3.1 改造方案1)取消4号燃烧器(即三次风入炉口右侧第一根),改为3根燃烧器供煤;3根燃烧器位置均向上提高1m;旋转角度由原来的20°改为0°;水平夹角由原来的30°改为10°;3根燃烧器与分解炉的中心的定位角度不变;燃烧器头部伸出炉浇注料表面300mm(改造示意见图1)。
图1 分解炉改造示意2)C4下料管撒料盒位置不变,用浇注料在撒料盒板体上浇注一个斜坡,即改现有板体与水平夹角15°为30°。
3.2 预防措施1)关小三次风,加强分解炉的喷腾效应。
水泥窑预分解系统内的结皮、积料以至堵塞现象分析

2.5.6、窑炉操作不协调
如果在回转窑和分解炉上两头操作不能前后兼顾,协调一致,如片面强调窑内通风,系统负压,过高的提高入窑分解率,会容易导致两把火配合不好,很容易造成高温结皮、堆积、棚料、塌料等而堵塞预热器系统。
3、防止产生结皮、积料和堵塞的措施及处理方法
3.1、开窑前的系统检查
在对预热器系统进行检修时,一定要对系统进行认真仔细的全面检查,一定要将预热器各管道内的所有杂物清理干净,检查预热器内耐火砖的砌筑、混凝土的浇注等是否牢固,防止开窑后掉下卡死料管。开窑前,应对所有排灰阀逐级检查,看转动是否灵活,有无卡死或损坏,对各级排灰阀应进行配重调整,防止过轻或过重,造成机械转动不灵或封闭不严形成内漏风,引起堵塞。
导致预分解窑预分解系统结皮、积料和堵塞的因素有好多,所以要想操作好这种窑,必须严格管理、强化气操作,
预热器出现积料和堵塞应找出原因及时处理,以防止处理不及时而产生结硬块,增加处理的难度。在处理时,先用压缩空气吹,若积料堵塞不严重,即可吹通,若堵塞严重,应止料停窑,但不要停排风,将人孔门打开,用风管、长铁棒等进行人工捅捣,捅完后检查各处是否清理干净,各处压力是否恢复正常方可升温开窑下料。若是因掉内套、掉砖、掉混凝土块及其它杂物而造成积料堵塞,必须止料、停窑,加大排风,待预热器冷却后,方可进到预热器内去处理,清理完毕后,方可开窑投料生产。
2.2、回灰造成的结皮堵塞
电收尘、增湿塔收集下来的物料,已经经过高温物理化学反应,有的甚至已成为半成品,所以对收集下来的这种物料重新进入预热器时,要严格控制操作温度。如仍按正常的温度去操作,那么就很容易造成物料的过早分解反应,液相提前出现,来不及到达窑内就在预热器内形成熔融状态而粘附在旋风筒内壁上,形成结皮,严重时导致预热器结皮堵塞。
分解炉缩口结皮的原因分析及解决措施

(2)三次风闸板烧坏。我公司三次风是从窑头罩抽取的,其中的熟料细颗粒没有经过旋风沉降,会不断冲刷三次风闸板上的浇注料。浇注料被磨损后闸板上的耐热钢板经不住900℃以上的热风的烘烧而烧坏。由于三次风阀板烧坏,窑内通风与三次风分配平衡被破坏,窑内通风量减小,窑头加煤温度上不去,形成还原气氛,产生黄心料。同时,三次风量明显增加,使预燃炉风速加快。由于无烟煤燃尽时间较长,风速增加造成煤粉在预燃炉滞留时间变短,煤粉被带至预燃炉出口处附近煅烧,形成炉中温度较低,而出炉温度较高的“温度倒挂”现象,引起分解炉下缩口结皮严重,导致分解炉出口与五级下料管负压增高。此时,为保证熟料质量,只得降低产量生产。
1.3 窑炉用煤比例不当
当分解炉缩口结皮严重且清烟室用的高压水枪出现故障时,有的操作员为了使熟料f-Ca0量合格,采取了加大窑头用煤量的强烧办法。结果窑尾废气带入分解炉的热量过高,势必减少分解炉用煤量,使入窑生料分解率降低,分解炉不能发挥应有的作用;同时窑内还原气氛加剧,煤粉不完全燃烧现象更严重,使分解炉缩口结皮进一步增多。
2.2 合理用风
在喂料量不变的情况下,三次风闸板开度加大,能增加分解炉燃烧空气量,降低了系统阻力;同时相应增加分解炉用煤量,有利于尾煤的充分燃烧,提高了入窑生料CaCO3分解率。正常生产情况下,我公司三次风闸板开度一般控制在55%~65%。
当三次风闸板烧坏后,运转期内,为了完成当月的生产任务,可以采用向三次风管内扔耐火砖的办法,以改变窑炉的风量分配;系统检修时,则应及时对烧坏的三次风闸板进行更换处理。
2.3 保持合适的窑、炉用煤比例
窑头用煤量的大小主要是依据入窑生料的喂料量和CaCO3分解率、生料易烧性、熟料f-CaO和升重、窑速及窑皮等因素来确定的。分解炉用煤量主要是根据入窑生料分解率、生料易烧性、分解炉出口气体温度来调节的。如果风量分配合理、入炉煤粉燃烧充分,但分解炉出口气体温度偏低,入窑生料分解率低,C5出口气体温度低,这说明分解炉用煤量过少,应增加。如果预分解系统温度偏高,热耗增加,甚至出现分解炉内煤粉燃尽率低,煤粉到C5内继续燃烧,导致预分解系统产生结皮或堵塞,这说明分解炉用煤量过多,应降煤。
分解炉锥部结皮原因分析及解决措施

管
通 过对 水 泥 窑 、预 热 器 系 统 的详 细 检 查 发 现 ,预 热
器旋风筒 、分解炉上部都没有结皮 ,但分解炉锥部靠
三 次风 管 沿燃 烧 器旋 流 方 向 3/4圈 结 皮 严 重 ,最 严
重处结皮厚度达到800mm左右 ,高度达到4m左右 , 分 解 炉缩 口结 皮达 到 1/3左右 。
4 效 果
(编辑 :刘翠荣 )(收稿 日期 :2012—05—25)
通过 以上改造及参数的调整 ,水泥窑开启后运
(上 接 第 3页 )
系统 烘 干 。
储存一定的物料 ,可 以延长待料时间 ;三是辊压机可
(4)缺陷情况 。辊压机功率为 3 350kW的减速 视情况关 闭气动阀止料 ,减少工作压力 ,使辊压机空
分解炉 炉锥体浇注料基本平齐(见 图 1),同时燃烧 窑头喂煤量过多 ,窑内煤粉的燃尽率较差 ,窑内出现
器位置正好处于三次风进分解炉处 (见 图2)。在运 后结圈 ,窑 内通风状况变差 ,未燃尽的煤粉与物料粘 行过程 中,窑尾煤粉经燃烧器 喷出后遇到高温富氧 附在烟室及分解炉缩 口形成结皮。
宋宏 昌:分解炉锥部 结皮原因分析及 解决措施
-一 一 臻#臻 孽≯i甍蹲秀鼙甏§毫0 誊叠曩_劳
囊棼鬣蒜磐 |薯
中图分类号 :TQ172.62 文献标识码 :B 文章 编号 :1007—0389(2013)0l一40—02
分解炉锥部结皮原 因分析及解决措施
宋 宏 昌(青海祁连山水泥有限公司,青海 西宁810021)
2 原 因分 析
图2 燃烧器、三次风管位置
式 计 算 ,当地 大 气 压 力 72.633 kPa,是 海 平 面 的 71.68% ;大 气 密 度 1.031 kg/m’,是 海 平 面 的
分解炉结皮原因的分析及处理

分解炉结皮原因的分析及处理我公司分解炉于2004年8月20日至9月底期间,结皮严重并且掉结皮堵三次风管多次,造成窑热工制度不稳、投料低、能耗高,甚至造成停窑事故的发生,严重影响生产。
现将前一阶段出现的分解炉结皮问题作一简要分析,供同行参考。
1 、炉型及工艺特性:我公司分解炉的炉型属于史密斯公司的SLC-S型,根据SLC型分解炉的流场分布来看,其基本上属于喷射流,并且喷射流的基本特征:轴向风速大,切向和径向风速很小,并且随着与炉体中心线距离的增大,轴向风速逐步降低,特别分解炉下锥体部位,在锥体边缘位置轴向风速锐减。
由于轴向风速的变化,在炉体内部形成紊乱的流场结构并存在立涡,一方面也造成物料分布产生区域性不均匀(立涡区),同样也造成燃料在喷射燃烧的同时形成涡旋。
2 、结皮及分解炉检查情况:2004年8月20日至9月底期间,分解炉频繁出现结皮并脱落,多次检查均发现分解炉下锥体部位周围结皮,严重时撒料箱位置的结皮已和扬料板持平,喷煤管两侧结皮厚达30~50cm。
根据塌落的结皮及入炉检查,结皮外观属多孔状熔渣,其间夹裹松散粉状料粉形成大块,在炉内检查时发现结皮松散、易脱落。
3 、结皮原因分析:根据结皮与物料成分分析情况表明,结皮主要是由煤灰渣溶解其他物料而形成的大块。
我厂分解炉下锥体结皮的分布情况及结皮形成时各物料成分、理化性能情况表明,我厂结皮及其形成具以下特征:3.1结皮产生主要由煤灰渣溶解其他物料而形成的大块。
3.2 结皮产生时分解炉锥体部位物料分布较为均匀,但喷煤管处偏厚一些,且结皮速较快。
3.3 结皮产生期间燃煤的焦渣特性值均在5以上,且入窑煤灰分均在38~43%,发热量小于5000千卡/千克.煤。
3.4 分解炉出口负压升高500~600Pa,出口温度由850~890ºC升高到950~1000ºC;分解炉锥部温度由于结皮包裹而下降,锥部压力下降。
根据以上特征各种物料分析表(1~4)及分解炉运行现象,可以充分说明我厂分解炉锥体部位结皮的原因如下:我厂的燃煤灰分较高,发热量较低,挥发分较正常,煤在分解炉内燃烧属辉焰燃烧,从外观观察火焰浊红。
TSD分解炉预燃炉结皮原因及预防
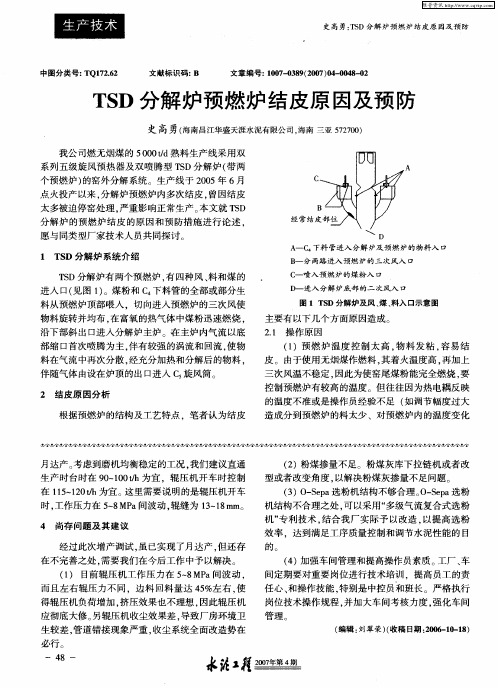
21 操 作原 因 . ()预燃 炉 温 度 控 制 太 高 , 料 发 粘 , 易结 1 物 容 皮 。 由于使用 无 烟煤作 燃 料 , 着火 温度 高 , 其 再加 上 三 次风 温不稳 定 , 因此 为使 窑尾 煤粉 能完 全燃 烧 , 要 控制 预燃 炉 有较 高 的温度 。但往 往 因为热 电耦 反 映 的温 度 不准 或是操 作 员经验 不足 ( 如调节 幅 度过 大 造成 分 到预燃 炉 的料 太少 、对预 燃 炉 内的温 度变 化
的。
经过 此次增 产 调试 , 已实现 了月 达产 . 还存 虽 但
在不完善之处 , 需要我们在今后工作中予以解决 。 () 目前辊 压 机 工作 压力 在 5 8 a间波 动 , 1 MP
而 且左 右 辊压 力 不 同 ,边料 回料 量 达 4 %左 右 . 5 使 得辊 压 机负荷 增 加 . 压效 果也 不理 想 . 挤 因此辊 压 机
维普资讯
史 高 勇 :S T D分 解 炉预 燃 炉 结 皮 原 因及预 防
中 图 分 类 号 : Q1 26 T 7 .2
文 献 标识 码 : B
文 章 编 号 : 0 7 0 8 (0 7 0 一 0 8 0 10 - 3 9 2 0 )4 O 4 _ 2
C 喷入 预 燃 炉 的煤 粉 入 口 一 D 进 入 分 解 炉 底 部 的 二 次 风入 口 一
图 1 T D 分 解 炉 及 风 、 、 入 口 示意 图 S 煤 料
主要 有 以下几 个 方面原 因造成 。
沿下部斜出 口 进入分解炉主炉。在主炉内气流 以底
部缩 口首 次喷腾 为 主 . 有较 强 的涡流 和 回流 . 伴 使物 料在气 流 中再 次分 散 , 充分 加热 和分 解后 的 物料 , 经
TSD分解炉预燃炉结皮原因及预防
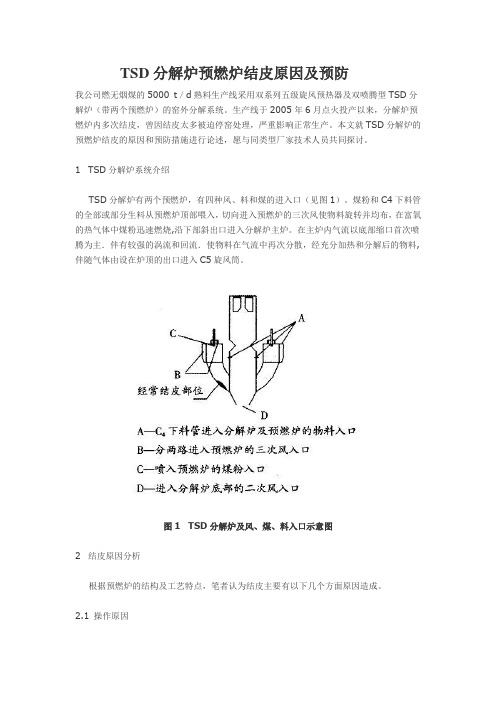
TSD分解炉预燃炉结皮原因及预防我公司燃无烟煤的5000 t/d熟料生产线采用双系列五级旋风预热器及双喷腾型TSD分解炉(带两个预燃炉)的窑外分解系统。
生产线于2005年6月点火投产以来,分解炉预燃炉内多次结皮,曾因结皮太多被迫停窑处理,严重影响正常生产。
本文就TSD分解炉的预燃炉结皮的原因和预防措施进行论述,愿与同类型厂家技术人员共同探讨。
1 TSD分解炉系统介绍TSD分解炉有两个预燃炉,有四种风、料和煤的进入口(见图1)。
煤粉和C4下料管的全部或部分生料从预燃炉顶部喂入,切向进入预燃炉的三次风使物料旋转并均布,在富氧的热气体中煤粉迅速燃烧,沿下部斜出口进入分解炉主炉。
在主炉内气流以底部缩口首次喷腾为主.伴有较强的涡流和回流.使物料在气流中再次分散,经充分加热和分解后的物料,伴随气体由设在炉顶的出口进入C5旋风筒。
图1 TSD分解炉及风、煤、料入口示意图2 结皮原因分析根据预燃炉的结构及工艺特点,笔者认为结皮主要有以下几个方面原因造成。
2.1 操作原因(1)预燃炉温度控制太高,物料发粘,容易结皮。
由于使用无烟煤作燃料,其着火温度高,再加上三次风温不稳定,因此为使窑尾煤粉能完全燃烧,要控制预燃炉有较高的温度。
但往往因为热电耦反映的温度不准或是操作员经验不足(如调节幅度过大造成分到预燃炉的料太少、对预燃炉内的温度变化预知不敏感)等原因,使预燃炉温度过高而导致物料提前出现液相而造成结皮(结皮部位见图1)。
(2)入预燃炉三次风量不足。
预燃炉是蜗壳旋流进风,三次风从切向进入,形成高速旋转气流逐渐向下推进物料。
如果风量小,则风速低,形不成旋流,或是旋流速度低而中途短路,那预燃炉就差不多是沉降室,容易在边壁、拐角积料甚至结皮。
我们在预燃炉中部检查孔处就经常能发现疏松结皮,而且有10 cm左右厚,应该就是风量不足造成的。
如果旋流风速很大,风是贴着边壁走的,足可以“飞砂走石”,不会在中部直筒部分形成结皮。
影响三次风量的因素除三次风门开度外,还有就是三次风管内的积灰量,积灰太多阻力变大,通风量就会减小。
预热器和分解炉结皮的分析及处理

预热器和分解炉结皮的分析及处理2010.No.12我公司2500t/d 生产线于2008年8月24日点火试生产。
采用喷、旋结合的CDC 分解炉,炉内采用2个皮拉德多通道型燃烧器。
投产后,预热器、分解炉及炉缩口结皮严重,使系统通风量减小,造成窑内产生还原气氛和煤粉不完全燃烧现象。
采取常规措施后,没有解决问题。
从投产到2009年5月底,共有23次分解炉严重结皮导致被迫停窑处理的事故,最长的一次清理用了3天,最短的也有1天,窑运转率极低,最长运转周期在半个月左右,严重影响了熟料产质量,熟料fCaO 含量的平均值在2.0%左右,3d 抗压强度仅23~25MPa 。
针对上述情况,我公司于2009年5月底进行了一系列的调整和技改。
1原因分析及处理措施1.1分解炉设计问题分解炉设计时两个燃烧器在下锥体呈对称布置,与撒料盒垂直,与水平方向呈30°夹角向下插入分解炉,燃烧器头部伸出浇注料400mm ,三次风与分解炉圆周切线呈20°夹角进入分解炉,如图1a 所示。
预热器和分解炉结皮的分析及处理陈德谦,周振山(攀枝花钢城集团瑞丰水泥有限公司,四川攀枝花617016)中图分类号:TQ172.622.26文献标识码:B文章编号:1002-9877(2010)12-0030-02图1分解炉技改示意在试生产阶段,分解炉下锥体结皮严重,经取样分析,结皮物结构致密,明显为高温熔融结皮,有时还夹杂有生料粉。
这种现象表明分解炉内风料混合不均匀,物料有局部沉淀现象,结皮料化学分析见表1,其硫碱比在0.7~0.8之间,在一个恰当的范围内,说明原料硫碱比不是导致结皮的主要原因。
表1结皮料化学分析及硫碱比30--2010.No.12时间熟料标准煤耗/(kg/t)熟料电耗/(kWh/t )技改前(2009年1~5月加权平均值)150.77102.12技改后(2009年6~12月加权平均值)137.0293.30经综合分析认为,结皮的主要原因是分解炉设计不当,主要表现在以下三方面:1)燃烧器布置不当燃烧器位置过于靠下,距离C 4下料口太远,燃烧产生的高温气体不能迅速与物料混合,产生局部高温,导致结皮。
- 1、下载文档前请自行甄别文档内容的完整性,平台不提供额外的编辑、内容补充、找答案等附加服务。
- 2、"仅部分预览"的文档,不可在线预览部分如存在完整性等问题,可反馈申请退款(可完整预览的文档不适用该条件!)。
- 3、如文档侵犯您的权益,请联系客服反馈,我们会尽快为您处理(人工客服工作时间:9:00-18:30)。
版社出版, ’33-,!
水泥技术 (++( 4 $
!!
#
炉型及其工艺特性 我公司分解炉的炉型属于史密斯
烧的同时形成涡旋。
%
结皮及分解炉检查情况 我 公 司 于 #002 年 1 月 试 生 产 至
公司的 456*4 型, 根据 456 型分 解 炉 的流场分布来看,其基本上属于喷射 流并具有喷射流的基本特征:轴向风 速大, 切向风速和径向风速很小, 并且 随着与炉体中心线距离的增大,轴向 风速逐步降低,特别分解炉下锥体部 位, 在锥体边缘位置轴向风速锐减。由 于轴向风速的变化,在炉体内部形成 紊乱的流场结构并存在立涡,一方面 使得物料与燃煤充分混合,另一方面 也造成物料分布产生区域性不均匀 ( 立涡区) ,同样也造成燃料在喷射燃
1
结皮期间分解炉运行特征 分解炉内煤粉的燃烧根据其特点
应属于辉焰燃烧,从外观上判断火焰 浊红,煤粉较为均匀地与物料混合燃 烧。我厂一般控制分解炉出口温度 物 料 分 解 率 0);30+; 。 在 22)9#): , 正常情况下,适当增加分解炉的喂煤 时,分解炉出口温度及物料分解率皆 有所提高。在分解炉结皮期间, 分解炉 炉体测点由于被结皮包裹, 无法实测, 分解炉出口温度偏低, 一般在 2’): 以 下, 物料分解率保持在 0);左右。 在提 高炉内喂煤的情况下,分解炉出口温 度基本上未发生变化且造成五级筒锥 部温度偏高。在结皮期间, 通过分解炉 锥体连接法兰变形处观察炉内情况, 发现锥体部位炉内发亮。
今,已运行近 , 年半的时间。在 #000 年, 分解炉系统曾经出现过结皮现象, 但时间较短且在停窑后检查未发现异 常; %))# 年 , 月至 ## 月期间,分解炉 频繁出现结皮并脱落,多次检查均发 现分解炉下锥体部位周圈结皮,严重 时撒料箱下位置的结皮已和扬料板持 平, 喷煤嘴两侧结皮厚达 1)3+)78。 根据塌落的结皮及入炉检查, 结 皮外观属多孔状质硬熔渣,其间夹裹 松散状粉料形成大块,在炉内检查时 发现结皮下炉衬表面形成黑硬的浇注 料熔融体。
煅 烧工艺
分解炉结皮原因分析
!"#$% &’"()$*$ +’ ,-%."(.*’%- !+"/*’0
!! 连志明
中图分类号: !"#$%&’%%&%’ 文献标识码: ( 文章编号: #))#*’#$# ( %))% ) )’*))+,*)%
国 投 海 南 水 泥 有 限 公 司 %)))- . / 熟料新型干法生产线原为海南昌江水 泥厂工程, 属海南省“ 八五” 重点工程, 位于海南省昌江县石碌镇水尾村西 侧 , 工 程 设 计 规 模 为 年 产 熟 料 ’) 万 吨, 水泥 $0&1$ 万吨。 生产线于 #00+ 年
+ 月正式开工建设, #002 年 1 月 生 产
出第一批合格水泥产品。烧成系统
#002 年 % 月 #2 日 点 火 烘 窑 , %1 日 投
料试产出第一批合格熟料, 同年 #% 月
%3+ 日通过系统考核,生产线运转 基
本正常。现将前一阶段烧成系统出现 的分解炉结皮问题作一简要分析, 供 同行参考。
! $
未发生结皮期间物料成分情况( 表 结皮原因分析 根据结皮与物料成分分析情况表 明,结皮主要是由煤灰渣熔结其它物 料而形成大块。 一般来说,分解炉锥体部位煤灰 渣结皮的形成主要是由以下两方面原 因造成的: 燃煤的焦渣特征情况, 只 %、 有焦渣特征值大于一定等级时方能形 成具有一定强度的煤渣结皮; &、分解 炉内燃料起火预燃速度快,炉内存在 偏流造成锥体部位温度场分布不均、 局部高温。但此类结皮的分布特征是 在分解炉锥体内衬局部位置形成结 皮。 根据我厂分解炉下锥体结皮的分 布情况及结皮形成时的各物料成分、 理化性能情况表明,我厂结皮及其形 成具有以下特征: ( 结皮主要是由煤灰渣熔结其 ’) 它物料而形成的大块; ( 结皮产生时分解炉锥体部位 () 物料分布较为均匀, 未存在偏流现象; ( 形成结皮期间燃煤的焦渣特 )) 征值均在 * 以上; ( 结皮产生期间煤粉的细度均 *) 在 +,+-.. 筛筛余 $/以下; ( 当燃煤的焦渣特征值在 ) 或 !) 以下时, 即使煤粉细度在 +,+-.. 筛筛 余 $/以下也不形成结皮; ( $)当燃煤的焦渣特征值在 *"$ 时, 若煤粉的细度控制在 +,+-.. 筛筛 余 -/ 以上, 分解炉锥体部位也不产生
,
结皮样及同期其它物料成分情况 为了确定分解炉的结皮原因, 对
各种物料进行了分析 < 表 #3,) 。
通讯地址: 国投海南水泥有限公司 = 海口
+$)#)) ;
收稿日期: %))%*)2*%) ;
编辑: 沈 颖
+,
6>?>@! !>6A@B5BCD ’ . %))%
煅 烧工艺
结皮。 根据以上特征及分解炉运行的现 象,可以充分说明我厂分解炉锥体部 位结皮的原因是:我厂采用的燃煤挥 发分普遍偏高, 基本都在 )+/ 以上, 而 且原煤热值较高,由于煤粉制备时为 满足窑头要求,煤粉的细度一直控制 在 +,+-.. 筛筛余小于 -/ , 因此, 在煤 粉喷入分解炉后,迅速起火燃烧且燃 烬速度快, 甚至形成明焰燃烧, 造成分 解炉内燃料燃烧集中在分解炉上游部 位,从而在分解炉下锥体部位形成区 域性温度偏高,一方面造成分解炉下 锥体部位内衬烧损,另一方面在燃煤 焦渣特征值大于 * 时,煤灰易熔结其 它物料在此部位形成结皮。
#
处理措施 根据结皮原因的分析和判断, 为
了确保分解炉的良好运行,我厂于
(++’ 年 ’’ 月 份 原 煤 采 购 时 将 焦 渣 特
征值作为重点指标进行控制, 要求在 * 以下,并且在煤粉制备时将煤粉细度 控 制 在 +,+-.. 筛 筛 余 在 ’+/"’(/ , 以确保分解炉内煤粉的燃烧分布合 理。通过调整和控制, (++’ 年 ’’ 月份 以后分解炉系统的燃烧状况明显改 善, 炉内温度场的分布更趋合理, 至今 未再出现结皮掉渣现象。
结束语 通过对分解炉下锥体结皮原因的
!"#)
分析, 可以得到以下的启示: 在分解炉 的优化操作中,应以充足的炉容及良 好的流场结构来确保炉内物料适宜的 料气滞留时间以及物料的均匀分布, 从而实现出炉物料的分解率。在实际 控制中应尽可能确保分解炉内温度场 的稳定、 合理, 避免因偏流或原燃材料 理化性能波动等造成炉内温度场的局 部偏差, 从而保证分解炉系统的良好、 稳定运行。