功率器件的热设计
功率放大器的热设计研究

Ke r s rl bl ; h n e mp rtr;h r a ssa c ywo d : ei it c a n le ea e te a i y t u m l eitn e r
大 器热设 计的方 法和 流程 ,对功 率放 大器进 行 了详
1 引言
热 失效 是 电子设备 的主要 失效 形式之 一 ,据 统
收稿 日期 :2 1—60 0 20 —4
.
1 8.
第l 卷第7 2 期
胡广华 ,钱兴成 ,汪
宇 :功率放大器的热设计研究
内部 大功 率 器件 分布 如 图 1 所示 。其 中 ,器件 Q。 为
高增益功率单片放大器 ,器件 Q 、Q为内匹配功 ,
率管。
3 利 用 软 件ANS YS热 仿 真 设 计
A bsr c :A st e c r fta s i c a e s t s a e p tf r r i h r q ie e t ff nci n a ta t h o e o n m t h nn l, a ksh v u o wa d h g e u r m n s o u to nd r p ro m a c . nsd rn he d m a so o e mpl e sf rhih r la ii ,t i a e i e he a e f r n e Co i e i g t e nd fp w ra i r o g e ib lt h sp p rg v s t r l i f y m
po e m p i e . t re d m e so a hem a o e fpo ra p i e sb itwi w ra l r A h e i n in lt r l i f m d lo we m l rwa u l i f t AN S o c lu ae h YS t ac lt
功率器件热设计及散热器的优化设计

功率器件热设计及散热器的优化设计1 表征功率器件热性能的主要参数功率器件应用时所受到的热应力可能来自器件内部,也可能来自器件外部。
器件工作时所耗散的功率要通过发热形式耗散出去。
若器件的散热能力有限,则功率的耗散就会造成器件内部芯片有源区温度上升及结温升高,使得器件可靠性降低,无法安全正常工作。
表征功率器件热能力的参数主要有结温和热阻。
一般将功率器件有源区称为结,器件的有源区温度称为结温。
这些器件的有源区可以是结型器件(如晶体管)的pn结区、场效应器件的沟道区,也可以是集成电路的扩散电阻或薄膜电阻等。
当结温T j高于周围环境温度Ta时,热量通过温差形成扩散热流,由芯片通过管壳向外散发,散发出的热量随着温差(Tj-T a)的增大而增大。
为了保证器件能够长期正常工作,必须规定一个最高允许结温 Tjmax。
Tjmax的大小是根据器件的芯片材料、封装材料和可靠性要求确定的。
功率器件的散热能力通常用热阻表征,记为 RT。
热阻越大,则散热能力越差。
热阻又分为内热阻和外热阻,内热阻是器件自身固有的热阻,与管芯、外壳材料的导热率、厚度和截面积以及加工工艺等有关;外热阻则与管壳封装的形式有关。
一般来说,管壳面积越大,则外热阻越小,金属管壳的外热阻就明显低于塑封管壳的外热阻。
当功率器件的功率耗散达到一定程度时,器件的结温升高,系统的可靠性降低,为了提高可靠性,应进行功率器件的热设计。
2 功率器件热设计功率器件热设计是要防止器件出现过热或温度交变引起的热失效,可分为器件内部芯片的热设计、封装的热设计和管壳的热设计以及功率器件实际使用中的热设计。
其主要关系如图1所示。
对于一般的功率器件,在生产工艺阶段,就要充分考虑器件内部、封装和管壳的热设计,当功率器件功耗较大时,依靠器件本身的散热(芯片、封装及管壳的热设计)并不能够满足散热要求。
功率器件结温可能会超出安全结温,此时需要安装合适的散热器,通过散热器有效散热,保证器件结温在安全结温之内且能长期正常可靠的工作。
一个3000W整流模块的热设计方案和计算实例

一个3000W整流模块的热设计方案和计算实例普天王海功率器件热设计和散热器优化设计方案示于图。
首先根据功率器件正常工作时的性能参数和环境参数,如环境温度、器件功耗和结温等,计算功率器件结温是否工作在安全结温之内,判断是否需要安装散热器进行散热,如功率器件需安装散热器进行散热,计算相应的散热器热阻,初选一散热器;重新计算功率器件结温,判断功率器件结温是否在安全结温之内,所选散热器是否满足要求;对于符合要求的散热器,应根据实际工程需要进行优化设计。
具体步骤如下:1.估算各部分的功率损耗1)整流桥(MP3510-W)输入最大功率:P in=3000/93%=3225.6W输入最大电流:I in=3225.6/185=17.44A正向损耗:P loss1=2×I in×0.9×V F=4×17.44×0.45×1.1=34.5W反向最大损耗:P loss2max=2×V r×1.1×I r=2×265×1.1×0.0005=0.3W合计:35W2)PFC电路的开关管(SPW47N60CFD)和快恢复二极管(SDT08S60)3)全桥变换初级四个开关管(SPW20N60CFD)4)次级整流二级管(DSEC30-02A)主要是正向导通损耗和开关损耗?假设:开关频率f=70KHz最大输出功率时,导通时间t on=7us ,开关时间t rr=140nsP F=6×I max/3×V F×t on×f=6×55/3×0.85×7×0.07=45.8WP cross=6×(I max/3/2×2×V out×t rr×f/6)=55/3×57.6×0.14×0.07×2=20.7WPloss=45.8+20.7=66.5W2.计算器件所用散热器的热阻一.以整流桥为例:1)MP3510-W的内热阻:R jc=1.4℃/W2)与散热器的接触面积:Ac=2.9×2.9-3.14×0.254×0.254=8.2cm2取8cm2,表面涂导热硅脂,加压,接触热阻:R tc=0.48/8=0.06℃/W3)根据导通电流与散热器温度的关系曲线和最大输入电流的需要,散热器温度应小于100℃,结温最大150℃,环境温度最高55℃,满足负荷输出时,散热器的热阻应:R tf≤(150-55)/35-1.4-0.06=1.25℃/W4)散热器的温度1.25×35+55=98.75℃二.以次级整流二级管为例:1)DSEC30-02A的内热阻:R jc=1.6/3=0.533℃/W2)与散热器的接触面积:Ac=3×(2.015×1.575-3.14×0.182×0.182)=9.21cm2表面涂导热硅脂,加压,接触热阻:R tc=0.48/9.21=0.052℃/W3)最大输出电流的需要,散热器温度应小于115℃,结温最大175℃,环境温度最高55℃,满足负荷输出时,散热器的热阻应:R tf≤(175-55)/66.5-0.553-0.052=1.2℃/W3.根据热阻估算散热器的散热面积一.以整流桥为例:假定流过肋片的风速在1m/s,根据结构散热片的长度允许3cm。
某大功率功放单元的热设计

管芯温度 一管芯 温度 和 功放 器件 底 面 的温 度
差 =功放器件底 面的温度
15— 0= 5 。 7 8 9 ( C、
计要 在预期 工作 的热 环 境 下 , 功 放器 件 的 热耗 把
所以, 功放器 件 底 面 的 可允 许 的最 高 温 度 为
首先, 自然冷却已经不能满足设备 的散热需
求, 如果采用液冷方式 , 护设 备 、 换某 个单元 相 维 更
作者简介 : 邵科峰 (9 8 , 助理工程师 , 17 一) 男热设计 。
维普资讯
5 8
值为:
K =20 ( 4 0 / 20)
靠、 易于维修保养、 成本相对较低 的优点, 所以, 结合
本功放 的特 点 , 合考 虑 各种 散 热方 式 , 综 我们 采 用 了强迫风冷 的散热方式 。具体散热方法如 下 : ( ) 70W 的热量快 速传导 至冷板 上 ; a将 3
C r oain 。 h n z o 5 0 5。 ma ) op rt o Z egh u4 0 1
Absr c A t o ft ema e in fra n w g t a t: meh d o r ld sg o e hih—p we mp i e s i t d c d,i i h t e c l h o ra lf ri nr u e i o n wh c od—p ae h lt a d f n ae s c e sul e .Th mp a i splc d o h e a nay i ft e d sg t n a r u c sf lyus d e e h ssi a e n t e t r l a l sso e in wi CFD o t r h m h h s fwae。 Ke r s: e a e i ; l y wo d T r ld sg Cod—p ae; n; e a ay i h m n lt Fa Th r la lss m n
MOS管热设计及发热分析详解

MOS管热设计及发热分析详解MOS管热设计,发热分析MOS管作为半导体领域最基础的器件之一,无论是在IC设计里,还是板级电路应用上,都十分广泛,尤其在大功率半导体领域。
然而大功率逆变器MOS管,工作的时候,发热量非常大,如果MOS管散热效果不好,温度过高就可能导致MOS管的烧毁,进而可能导致整个电路板的损毁。
MOS管的热设计避免MOS因为器件发热而造成的损坏,需要做好足够的散热设计。
若通过增加散热器和电路板的长度来供所有MOS管散热,这样就会增加机箱的体积,同时这种散热结构,风量发散,散热效果不好。
有些大功率逆变器MOS管会安装通风纸来散热,但安装很麻烦。
所以MOS管对散热的要求很高,散热条件分为最低和最高,即在运行中的散热情况的上下浮动范围。
一般在选购的时候通常采用最差的散热条件为标准,这样在使用的时候就可以留出最大的安全余量,即使在高温中也能确保系统的正常运行。
做好MOS管的热设计,需要足够的散热片以及导热绝缘硅胶垫片才能实现。
mos散热片是一种给电器中的易发热电子元件散热的装置,多由铝合金,黄铜或青铜做成板状,片状,多片状等,如电脑中CPU 中央处理器要使用相当大的散热片,电视机中电源管,行管,功放器中的功放管都要使用散热片。
通常采用散热片加导热绝缘硅胶的设计直接接触散热,如果MOS 管外壳不能接地,可以采用绝缘垫片隔离后再用导热硅脂散热。
也可以选用硅胶片覆盖MOS管,除了散热还可以起到防止电损的作用。
整个散热体系能使元器件发出的热量更有效地传导到散热片上,再经散热片散发到周围空气中去,使得器件的稳定性得到保障。
热设计之分析MOS管是电路设计中比较常见的器件,经常用在多种开关电路或者防反电路中,电流值从几个mA到几十个A。
来看看热方面的知识。
1、当MOSFET完全导通时,将产生I2RDS(on)的功率损耗2、I2RDS(on)的功率损耗将在器件内部或者外部产生温升3、MOSFET器件可能因温度过高而损坏一般MOSFET的结点温度都要保持在175°C以下,贴片MOSFET 的PCB的温度限值是120°C,由于 MOSFET 器件和焊接 PCB 处之间热耦合紧密,所以我们可以认为TPCB ≈ Tj,那么安全工作温度的上限将不再是 MOSFET的结点温度,而是 PCB 的温度(120 ℃)。
基于FLOTHERM的固态功率放大器热设计

基于FLOTHERM的固态功率放大器热设计文章对L波段固态功率放大器整机结构热设计进行了研究,并结合L波段固态功率放大器设计实例,最后给出了整机的仿真及实物测试结果。
标签:热设计;固态功率放大器;热仿真;FLOTHERM引言固态功率放大器主要由功率放大模块、增益放大模块、合成模块、耦合模块和控制电路等组成,功率放大模块在大功率条件下工作时,器件发热量大,使器件处于高温状态下工作。
而高温会使元器件电性能恶化,引起失效,导致设备可靠性下降。
资料表明:单个半导体元件的温度升高10 ℃~12 ℃,其可靠性降低50%[1]。
随着器件的密集化,电子设备的功率密度增大,对热设计的需求也日益强烈。
1 整机结构设计主要设计指标如下:频率范围1GHz~2.5GHz,功率增益≥50dB,最大输入功率≤10dBm,最大输出功率≥50dBm,环境适应性满足GJB3947A-2009环境4级设备要求,另外还有输入端口驻波比、输出功率平坦度、1dB压缩点输出功率、3dB压缩点输出功率、噪声系数、谐波抑制等指标要求。
功率放大模块采用某型号功率芯片,单个芯片无论在输出功率或功率增益方面都无法达到设计要求,因此,本方案选用两极放大串联的方式满足功率增益的要求,其中前级作为推动级,末级作为功率输出级,末级使用4路放大并联的方式满足输出功率的要求,前后两个放大级中的各单管放大电路设计成完全相同的形式。
信号流图如图1所示。
功率放大模块中的功率芯片满载时功耗较高达到115瓦。
五个功率放大模块共有10个芯片,芯片总功耗高达1150瓦,并且该芯片面积小,热流密度高,散热难度很大。
综合整机内部信号流、模块的功能、可装配性和可维修性等,為了更好的散热,整机结构布局如图2所示。
散热器由上下基板和中间散热片组成,在机箱高度方向放置于机箱中部,上下基板可以贴附散热器件,可以最大限度的增加机箱散热性能。
电源自带散热风机,因此将电源单独放置于机箱左侧的电源仓,不仅有利于散热,更有利于屏蔽强电信号。
浅析电子设备中功率器件的热设计与散热设计
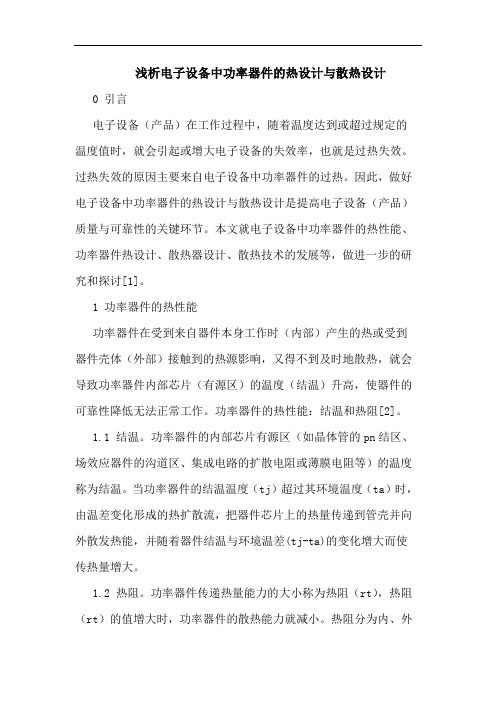
浅析电子设备中功率器件的热设计与散热设计0 引言电子设备(产品)在工作过程中,随着温度达到或超过规定的温度值时,就会引起或增大电子设备的失效率,也就是过热失效。
过热失效的原因主要来自电子设备中功率器件的过热。
因此,做好电子设备中功率器件的热设计与散热设计是提高电子设备(产品)质量与可靠性的关键环节。
本文就电子设备中功率器件的热性能、功率器件热设计、散热器设计、散热技术的发展等,做进一步的研究和探讨[1]。
1 功率器件的热性能功率器件在受到来自器件本身工作时(内部)产生的热或受到器件壳体(外部)接触到的热源影响,又得不到及时地散热,就会导致功率器件内部芯片(有源区)的温度(结温)升高,使器件的可靠性降低无法正常工作。
功率器件的热性能:结温和热阻[2]。
1.1 结温。
功率器件的内部芯片有源区(如晶体管的pn结区、场效应器件的沟道区、集成电路的扩散电阻或薄膜电阻等)的温度称为结温。
当功率器件的结温温度(tj)超过其环境温度(ta)时,由温差变化形成的热扩散流,把器件芯片上的热量传递到管壳并向外散发热能,并随着器件结温与环境温差(tj-ta)的变化增大而使传热量增大。
1.2 热阻。
功率器件传递热量能力的大小称为热阻(rt),热阻(rt)的值增大时,功率器件的散热能力就减小。
热阻分为内、外热阻:①内热阻是功率器件本身的热阻,并与功率器件的芯片、外壳材料的导热率、厚度和截面积等有关。
②外热阻是功率器件外部的热阻,并与功率器件外部(管壳)的封装形式(如金属管壳的外热阻<塑封管壳)有关,而且管壳面积越大,外热阻越小。
2 功率器件的热设计功率器件热设计的目的是为了防止器件工作时所产生的温度过高,致使器件(过热引起热失效)无法正常工作。
在功率器件热设计过程中,不仅要作好器件内部芯片、封装形式和管壳的热设计,还要加装合适的散热器进行有效散热,保证器件在安全结温之内正常可靠的工作[3]。
2.1 器件的性能参数和环境参数。
芯片电路热设计指南

芯片电路热设计指南半导体器件产生的热量来源于芯片的功耗,热量的累积必定导致半导体结点温度的升高,随着结点温度的提高,半导体器件性能将会下降,因此芯片厂家都有规定半导体器件的结点温度。
在普通数字电路中,由于低速电路的功耗较小,在正常的散热条件下,芯片的温升不会太大,所以不用考虑芯片的散热问题。
而在高速电路中,芯片的功耗较大,在正常条件下的散热不能保证芯片的结点温度不超过允许工作温度,因此需要考虑芯片的散热问题。
1、热量传递在通常条件下,热量的传递通过传导、对流、辐射3种方式进行。
传导是通过物体的接触,将热流从高温向低温传递,导热率越好的物体则导热性能越好,一般来说金属导热性能最好;对流是通过物体的流动将热流带走,液体和气体的流速越快,则带走的热量越多;辐射不需要具体的中间媒介,直接将热量发送出去,真空中效果更好。
散热时需要考虑3种传热方式。
例如使用导热率好的材料,如铜、铝及其合金做导热材料,通过增加风扇来加强对流,通过材料处理来增强辐射能力等。
2、简单热量传递模型热量分析中引入一个热阻参数,类似于电路中的电阻。
如果电路中的电阻计算公式为R=ΔE/I,则对应的热阻对应公式为R=ΔT/P(P表示功耗,单位W, ΔT表示温差,单位℃)。
热阻的单位为℃/W,表示功率增加1W时所引起的温升。
考虑集成芯片的热量传递,可以使用如下图形描述高速电路设计中的散热考虑在普通的数字电路设计中,我们很少考虑到集成电路的散热,因为低速芯片的功耗一般很小,在正常的自然散热条件下,芯片的温升不会太大。
随着芯片速率的不断提高,单个芯片的功耗也逐渐变大,例如:Intel的奔腾CPU的功耗可达到25W。
当自然条件的散热已经不能使芯片的温升控制在要求的指标之下时,就需要使用适当的散热措施来加快芯片表面热的释放,使芯片工作在正常温度范围之内。
通常条件下,热量的传递包括三种方式:传导、对流和辐射。
传导是指直接接触的物体之间热量由温度高的一方向温度较低的一方的传递,对流是借助流体的流动传递热量,而辐射无需借助任何媒介,是发热体直接向周围空间释放热量。
- 1、下载文档前请自行甄别文档内容的完整性,平台不提供额外的编辑、内容补充、找答案等附加服务。
- 2、"仅部分预览"的文档,不可在线预览部分如存在完整性等问题,可反馈申请退款(可完整预览的文档不适用该条件!)。
- 3、如文档侵犯您的权益,请联系客服反馈,我们会尽快为您处理(人工客服工作时间:9:00-18:30)。
关于“功率器件热设计及发展进程”的报告随着电子设备复杂性的增加,如果各种发热元件散发出来的热量不能够及时散发出去,就会造成热量的积聚,从而导致各个元器件的温度超过各自所能承受的极限,使得电子设备的可靠性大大降低。
当前,电子设备的主要失效形式之一就是热失效。
据统计,电子设备的失效有5 %是温度超过规定值引起的,随着温度的增加,电子设备的失效率呈指数增长趋势。
所以,功率器件热设计是电子设备结构设计中不可忽略的一个环节,它的好坏直接决定了产品设计的成功与否。
良好的热设计是保证设备运行稳定性与可靠性的基础。
1.功率器件热性能的主要参数功率器件应用时所受到的热应力可能来自器件内部,也可能来自器件外部。
器件工作时所耗散的功率要通过发热形式耗散出去。
若器件的散热能力有限,则功率的耗散就会造成器件内部芯片有源区温度上升及结温升高,使得器件可靠性降低,无法安全正常工作。
表征功率器件热能力的参数主要有结温和热阻。
一般将功率器件有源区称为结,器件的有源区温度称为结温。
这些器件的有源区可以是结型器件(如晶体管)的pn结区、场效应器件的沟道区,也可以是集成电路的扩散电阻或薄膜电阻等。
当结温Tj高于周围环境温度Ta时,热量通过温差形成扩散热流,由芯片通过管壳向外散发,散发出的热量随着温差的增大而增大。
为了保证器件能够长期正常工作,必须规定一个最高允许结温Tjmax。
Tjmax的大小是根据器件的芯片材料、封装材料和可靠性要求确定的。
功率器件的散热能力通常用热阻表征,记为Rt,热阻越大,则散热能力越差。
热阻又分为内热阻和外热阻,内热阻是器件自身固有的热阻,与管芯、外壳材料的导热率、厚度和截面积以及加工工艺等有关;外热阻则与管壳封装的形式有关。
一般来说,管壳面积越大,则外热阻越小,金属管壳的外热阻就明显低于塑封管壳的外热阻。
当功率器件的功率耗散达到一定程度时,器件的结温升高,系统的可靠性降低。
为了提高可靠性,应进行功率器件的热设计2.功率器件热设计功率器件热设计是要防止器件出现过热或温度交变引起的热失效,可分为器件内部芯片的热设计、封装的热设计和管壳的热设计以及功率器件实际使用中的热设计。
其主要关系如图1所示。
对于一般的功率器件,在生产工艺阶段,就要充分考虑器件内部、封装和管壳的热设计。
当功率器件功耗较大时,依靠器件本身的散热(芯片、封装及管壳的热设计)并不能够满足散热要求。
功率器件结温可能会超出安全结温,此时需要安装合适的散热器,通过散热器有效散热,保证器件结温在安全结温之内且能长期正常可靠的工作。
3.散热计算任何器件在工作时都有一定的损耗,大部分的损耗变成热量。
小功率器件损耗小,无需散热装置。
而大功率器件损耗大,若不采取散热措施,则管芯的温度可达到或超过允许的结温,器件将受到损坏。
因此必须加散热装置,最常用的就是将功率器件安装在散热器上,利用散热器将热量散到周围空间,必要时再加上散热风扇,以一定的风速加强冷却散热。
在某些大型设备的功率器件上还采用流动冷水冷却板,它有更好的散热效果。
散热计算就是在一定的工作条件下,通过计算来确定合适的散热措施和选择散热器。
功率器件安装在散热器上,它的主要热流方向是由管芯传到器件的底部,经散热器将热量散到周围空间,这称为自然冷却或自然对流散热。
热量在传递过程有一定热阻。
由器件管芯传到器件底部的热阻为Rjc,器件底部与散热器之间的热阻为Rcs,散热器将热量散到周围空间的热阻为Rsa,总的热阻Rjc=Rjc+Rcs+Rsa。
若器件的最大功率损耗为PD,并已知器件允许的结温为Tj、环境温度为Ta,可以按下式求出允许的总热阻Rja。
则计算最大允许的散热器到环境温度的热阻Rsa为:出于为设计留有余地的考虑,设Jt为125 ℃。
环境温度也要考虑较坏的情况,设。
Rjc的大小与管芯的尺寸封装结构有关,一般可以从器件的数据资料中找到。
Rcs的大小与安装技术及器件的封装有关。
如果器件采用导热油脂或导热垫后,再与散热器安装,其Rcs典型值为;若器件底面不绝缘,需要另外加云母片绝缘,则其Rcs可达1℃/W。
Pd为实际的最大损耗功率,可根据不同器件的工作条件计算而得。
这样,Rsa可以计算出来,根据计算的Rsa值可选合适的散热器了。
注意事项 :‘(1)在计算中不能取器件数据资料中的最大功耗值,而要根据实际条件来计算;数据资料中的最大结温一般为150 OC,在设计中留有余地取125 OC,环境温度也不能取25 OC(要考虑夏天及机箱的实际温度)。
(2)散热器的安装要考虑利于散热的方向,并且要在机箱或机壳上相应的位置开散热孔(使冷空气从底部进人,热空气从顶部散出). (3)若器件的外壳为一电极,则安装面不绝缘(与内部电路不绝缘)。
安装时必须采用云母垫片来绝缘,以防止短路。
(4)器件的引脚要穿过散热器,在散热器上要钻孔。
为防止引脚与孔壁相碰,应套上聚四氟乙稀套管。
(5)另外,不同型号的散热器在不同散热条件下有不同热阻,可供设计时参考,即在实际应用中可参照这些散热器的热阻来计算,并可采用相似的结构形状(截面积、周长)的型材组成的散热器来代用。
(6)在上述计算中,有些参数是设定的,与实际值可能有出入,代用的型号尺寸也不完全相同,所以在批量生产时应作模拟试验来证实散热器选择是否合适,必要时做一些修正(如型材的长度尺寸或改变型材的型号等)后才能作批量生产。
4.选取散热器小型散热器(散热片)由铝合金板料经冲压工艺及表面处理制成,而大型散热器由铝合金挤压形成型材,再经机械加工及表面处理制成。
它们有各种形状及尺寸供不同器件安装及不同功耗的器件选用。
散热器一般是标准件,也可提供型材,由用户根据要求切割成一定长度而制成非标准的散热器。
散热器的表面处理有电泳涂漆或黑色氧极化处理,其目的是提高散热效率及绝缘性能。
在自然冷却下可提高10~15%,在通风冷却下可提高3%,电泳涂漆可耐压500~800V。
散热器厂家对不同型号的散热器给出热阻值或有关曲线,并且在不同散热条件下的不同热阻值。
功率器件使用散热器是要控制功率器件的温度,尤其是结温Tj,使其低于功率器件正常工作的安全结温,从而提高功率器件的可靠性。
功率器件散热器随着功率器件的发展,得到了飞速发展,常规散热器趋向标准化、系列化、通用化,而新产品则向低热阻、多功能、体积小、重量轻、适用于自动化生产与安装等方向发展。
合理地选用、设计散热器,能有效降低功率器件的结温,提高功率器件的可靠性。
各种功率器件的内热阻不同,安装散热器时由于接触面和安装力矩的不同,均会导致功率器件与散热器之间的接触热阻不同。
选择散热器的主要依据是散热器热阻Rtf。
在不同的环境条件下,功率器件的散热情况也不同。
因此选择合适散热器还要考虑环境因素、散热器与功率器件的匹配情况以及整个电子设备的大小、重量等因素。
首先根据功率器件正常工作时的性能参数和环境参数,如环境温度、器件功耗和结温等,计算功率器件结温是否工作在安全结温之内,判断是否需要安装散热器进行散热,如功率器件需安装散热器进行散热,计算相应的散热器热阻,初选一散热器;重新计算功率器件结温,判断功率器件结温是否在安全结温之内,所选散热器是否满足要求;对于符合要求的散热器,应根据实际工程需要进行优化设计。
5.介绍功率器件散热几种方式方法信息业的巨大发展,给电源市场带来了巨大的市场机会和挑战,同时对电源提出了一些新的需求。
例如:多种物理设备放在一起,有电磁兼容的需求和机房面积和承重的要求;网络设备种类变多使电源的负载变大,负载种类变多,对电源效率和种类有要求;机房和基站数目增多,对电源的可靠性和易维护性提出更高的要求,以满足无人值守需要。
电源工作环境的差异对电源的应用环境也提出了新的需求。
1.复合相变储热材料的散热技术可广泛应用于各类电子产品中,是一种具有良好的应用前景。
与传统的散热方式不同,对于基于快速热响应储热材料的散热技术除要求相变材料的储热密度大之外,还要求材料具有较高的导热系数,传热速率快为解决传统相变材料高储热密度和低导热系数之间的矛盾,根据电子元件散热技术领域对快速热响应相变储热材料的性能(如密度、相变温度、储热密度)要求,实验选定导热系数高且密度低的膨胀石墨作为无机支撑材料,石蜡作为有机相变材料,利万方数据用石蜡与膨胀石墨间的固、液表面张力,孔隙结构的毛细作用力以及膨胀石墨的多孔结构和非极性等特性,筛选、制备出有机、无机复合相变材料,使得复合相变储热材料具有较高的导热系数。
2.地面设备可采用强迫风冷的方式对电子元器件进行散热,然而在真空环境中,增强元器件的散热能力,只能从辐射和传导两个方面考虑。
由于元器件本身的辐射散热面积不可能增加,而且不可能使用表面处理的方法增大元器件本身的表面辐射率,所以通过元器件的传导散热,成为这种情况下能够增加散热量的方式。
电子元器件有一散热面紧贴印制板面,然而由于印制板的基材是热的不良导体,元器件与印制板直接接触,两者之间不能构建良好的热流传导通路。
此时,在元器件与印制板之间安装一块金属导热冷板,元器件的散热面紧贴冷板表面,使元器件工作过程中产生的部分热量直接传导至冷板上,然后通过冷板的传导和辐射,将热量散发至外界环境中,使元器件的温升速度减慢,降低元器件长时间工作后的热平衡温度。
根据阿雷尼厄斯10度法则,电子元器件的使用温度每上升10℃,元器件的寿命缩短一半。
因此,电子元器件工作温度的降低,对提高设备的可靠性有十分重要的意义。
6.国内外发展进程全球通信电源技术发展呈现以下五大趋势:首先是高效率,高功率密度,宽松的使用环境温度。
其次是网络化智能化的监控管理。
再次是全数字化控制。
数字化技术的发展逐步表现出了传统模拟技术无法实现的优势。
第四表现为安全、防护、EMC。
考虑到设备复杂的运行环境,电源设备需满足相关的安全、防护、防雷标准,才能保证电源的可靠运行。
安全性是电源设备最重要的指标;商用设备需要通过相关的安全认证,如UL、CSA八T)E,CCC等。
最后要求环保。
环保一方面指标是,通信电源的电流谐波符合要求。
降低电源的输人谐波,不但可以改善电源对电网的负载特性,减小给电网带来严重的污染,也可减少对其他网络设备的谐波干扰。
另一个重要方面是,材料可循环利用和对环境无污染。
借助于微电子学(Microelectronics)和微电子技术的出现和发展,现在的电子器件及设备向着小型化、紧凑化、高性能的方向发展。
1965午4月,时任仙童公司电子工程师,Intel公司创始人之一的摩尔在《Electronics))杂志上发表文章提出了著名的“摩尔定律”。
根据“摩尔定律”推算:芯片上的晶体管数量每18个月翻一番。
1997年Intel公司推出的Pentium II芯片上有750万个晶体管,1999年推出的Pentium Ⅲ引入了O.25微米工艺,芯片上有950万个晶体管,其芯片面积只有20mmx20mm左右。