空分站工艺流程简介
空分工艺流程
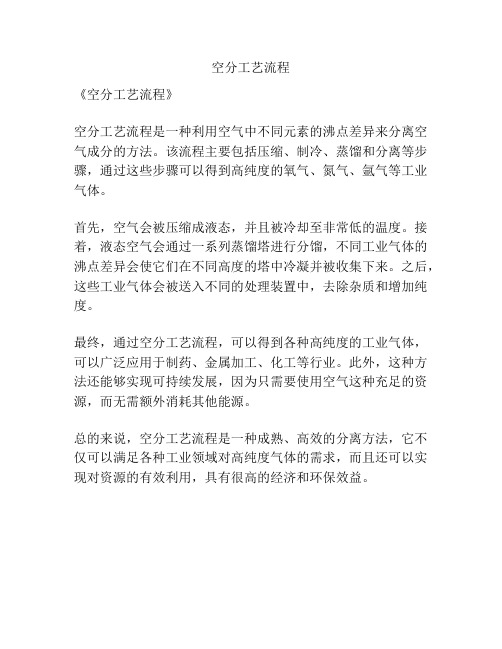
空分工艺流程
《空分工艺流程》
空分工艺流程是一种利用空气中不同元素的沸点差异来分离空气成分的方法。
该流程主要包括压缩、制冷、蒸馏和分离等步骤,通过这些步骤可以得到高纯度的氧气、氮气、氩气等工业气体。
首先,空气会被压缩成液态,并且被冷却至非常低的温度。
接着,液态空气会通过一系列蒸馏塔进行分馏,不同工业气体的沸点差异会使它们在不同高度的塔中冷凝并被收集下来。
之后,这些工业气体会被送入不同的处理装置中,去除杂质和增加纯度。
最终,通过空分工艺流程,可以得到各种高纯度的工业气体,可以广泛应用于制药、金属加工、化工等行业。
此外,这种方法还能够实现可持续发展,因为只需要使用空气这种充足的资源,而无需额外消耗其他能源。
总的来说,空分工艺流程是一种成熟、高效的分离方法,它不仅可以满足各种工业领域对高纯度气体的需求,而且还可以实现对资源的有效利用,具有很高的经济和环保效益。
空分工艺流程说明

2.2.2 工艺流程简述2.2.2.1压缩、预冷原料空气通过空气过滤系统,去除灰尘和机械杂质。
过滤后的空气由多级压缩机压缩到工艺所需压力,然后进入空冷塔进行冷却。
压缩过程中产生的冷凝疏水在厂房内凝液罐中汇集后,由凝液泵加压送入循环回水管线。
空气自下而上穿过空冷塔,以对流形式被循环冷却水和低温冷冻水分段冷却,同时也得到了清洗。
在空冷塔底部,空气被由冷却水泵送入的循环冷却水预冷。
在顶部,空气由冷冻水泵送入的冷冻水进一步冷却。
低温冷冻水是在水冷塔中产生,其产生的原理是利用从冷箱来的干燥的污氮气汽化小部分循环冷却水,水在汽化过程中吸收热量,同时使冷却水的温度降低。
空气离开空冷塔的温度越低,对于下游空气纯化单元的负荷就越小。
空气中的少量化学杂质也被冷却水吸收。
空冷塔和水冷塔为填料塔,在空冷塔顶部设置有除沫器以去除空气中的水雾。
2.2.2.2 吸附净化、氮氧化合物和绝大多数碳氢化合物都被吸附。
空气纯化单元包括两台交替运行的分子筛吸附器,压缩空气通过吸附器时,水、CO2吸附器交替循环,即一只吸附器吸附杂质而另一只吸附器被再生。
吸附和再生过程顺序自动控制以保证装置连续运行。
采用来自冷箱的污氮对吸附器进行再生。
再生时吸附器与吸附流程隔离,再生气放空。
与吸附流程隔离的吸附器先卸压,然后先用经蒸汽加热器加热的低压污氮进行再生,然后用从蒸汽加热器旁路来的冷低温氮气对吸附器进行冷却,之后再用吸附后的空气对吸附器升压并返回吸附流程。
再生循环主要有下面几个组成部分:泄压-加热-冷却-增压单台吸附器的设计切换周期不少于4小时。
法液空流程的纯化单元设置特殊再生加热器,必要时可用特殊再生加热器进行特殊再生。
针对厂区空气中CO2含量波动大的特点,在分子筛吸附器空气出口设有CO2在线分析仪,可以随时监测吸附器的运行工况,从而保证出口的CO2组分满足工艺要求。
净化后的空气分为两股:其中一股进入低压换热器;另一股去空气增压机增压。
2.2.2.3 空气精馏净化后的空气分为两部分:一部分净化空气主气流直接进入冷箱,并在低压主换热器中与返流产品进行热交换而冷却至接近于露点。
空分施工程序(3篇)

第1篇一、前言空分施工程序是指将空气进行分离,提取出氧气、氮气、氩气等稀有气体的过程。
空分技术在石油、化工、电子、医疗等领域有着广泛的应用。
以下是空分施工程序的详细描述。
二、空分施工程序1. 原料准备(1)空气:选择质量合格、无污染、无油气的空气作为原料。
(2)设备:空分设备包括空气预处理系统、空气压缩系统、精馏塔、冷凝器、蒸发器等。
2. 空气预处理(1)空气过滤:去除空气中的尘埃、水分、油污等杂质。
(2)空气干燥:降低空气中的水分含量,保证空气在后续处理中的稳定性。
3. 空气压缩(1)空气在压缩机中被压缩,提高压力。
(2)压缩机出口温度升高,需进行冷却处理。
4. 精馏塔处理(1)空气进入精馏塔,在精馏塔内进行多级分离。
(2)根据不同气体的沸点差异,将空气分离成氧气、氮气、氩气等。
5. 冷凝器与蒸发器(1)在精馏塔中,气体被冷却至低温,使部分气体冷凝成液体。
(2)液体在蒸发器中蒸发,转化为气体,以便再次进入精馏塔。
6. 产品收集(1)分离出的氧气、氮气、氩气等稀有气体,通过管道输送到各自的收集罐。
(2)收集罐内的气体,经过净化、干燥等处理,达到产品要求。
7. 产品包装与储存(1)将处理后的气体进行包装,确保产品在运输和储存过程中的安全。
(2)按照产品标准,对气体进行储存,保证产品质量。
8. 设备维护与保养(1)定期对空分设备进行检查、清洗、润滑,确保设备正常运行。
(2)对设备进行定期检修,更换磨损部件,延长设备使用寿命。
三、总结空分施工程序是分离空气中的氧气、氮气、氩气等稀有气体的过程。
通过原料准备、空气预处理、空气压缩、精馏塔处理、冷凝器与蒸发器、产品收集、产品包装与储存、设备维护与保养等步骤,实现空气分离。
空分技术在多个领域有着广泛应用,对提高生产效率和产品质量具有重要意义。
第2篇一、工程背景空分施工程序是指将空气进行分离,提取出氧气、氮气、氩气等产品的工艺流程。
随着工业和科技的发展,空分技术在石油、化工、电子、食品、医药等领域得到了广泛应用。
空分工艺流程介绍07
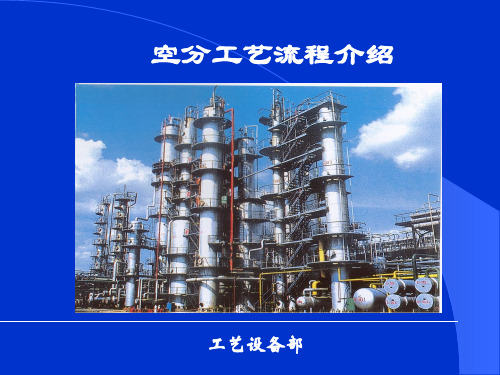
5.分子筛纯化系统
分子筛纯化系统由两台分子筛吸附器和 三台电加热器组成。
分子筛吸附器吸附空气中的水份、二氧 化碳和一些碳氢化合物,两台分子筛吸附 器一台工作,另一台再生,交替运行。再 生气的加热由电热器提供热量在其中完成。
6.分馏塔精馏系统 出分子筛吸附器的空气首先分为两部分:
第一部分直接进入主换热器冷却后进入 下塔;
第二部分通过空气增压机进一步压缩, 经增压机末级后冷却器冷却后再次分成两 部分。
一部分经膨胀机增压端增压并冷却后进 入主换热器,在主换热器合适的位置抽出, 进入膨胀机膨胀端膨胀后进入下塔参加精馏;
另一部分经过主换热器,然后经节流阀 节流成液体后进入下塔参加精馏。
下塔中的上升气体通过与回流液体接触 含氮量增加。所需的回流液氮来自下塔顶部 的冷凝蒸发器,在这里液氧得到蒸发,而气 氮得到冷凝。
利用双泵内压缩的流程使其投资低、安全 性能高、操作方便,还能控制优化。
二、工艺技术总述
本套制氧站工艺流程采用常温分子筛 预净化,空气增压透平膨胀机提供装置 所需冷量,双塔精馏,单泵内压缩流程, 同时设有液体贮存及汽化装置系统,整套 空分装置采用DCS系统控制。
三、总工艺流程图
四、工艺流程说明
空气经下塔初步精馏后,在下塔底部获 得液空,在顶部获得纯液氮。
6.1下塔从上到下产生以下产品或中间 产物:
·压力氮气 ·污液氮 ·富氧液空(36~40%) 下塔各产品去向如下:
①压力氮气:从下塔顶部抽出后经主换 复热后进入氮气压缩系统。
②污液氮:污液氮在过冷器中过冷后送 入上塔顶部作回流液。
1.流路简述 整套空分设备包括: 空气过滤系统、空气压缩系统、空气预 冷系统、分子筛纯化系统、分馏塔系统、 液体贮存系统、仪控系统、电控系统等八 大系统。
空分工艺流程描述(共8页)

2 工艺流程2工艺流程总体概述空气过滤及压缩来自大气中的空气经自洁式过滤器S01101,将空气中大于1μm的尘埃和机械杂质去除后,送离心式空气压缩机K01101,自洁式空气过滤器采用PLC控制,带自动反吹系统,反吹系统有时间、压差、时间和压差三种控制程序。
流量约168000Nm3〔A〕。
温度<105℃后进入空气预冷系统。
空气流量由空压机入口导叶B011101的开度来调节,空压机K01101采用3组内置段间冷却器冷却压缩空气;并在末级出口还设有一放空阀BV011121,在开车、停车期间,局部空气将由BV011121放空,以防止压缩机喘振。
润滑油系统:空压机和增压机共用一个润滑油站T011101,油系统包括润滑油系统、事故油系统〔2个高位油箱和4个蓄能器,空压机组和增压机组各1个高位油箱,2个蓄能器〕。
润滑油主要对机组各轴承起润滑、冷却及清洗杂质等作用。
油箱内的润滑油经润滑油泵加压后后送入润滑油冷却器E-011101A/B中冷却,经温度调节阀控制好油温后进入润滑油过滤器S-011101A/B,过滤掉油中杂质后进入润滑油总管,然后送到各润滑点经机组润滑后返回油箱;润滑油泵出口有一总管压力调节阀,用于调节润滑油过滤器S-011101A/B出口总管油压。
该油路同时为增压机提供润滑油,在空压机供油总管和增压机供油总管上分别设置有蓄能器和高位油箱。
以保证在主、辅油泵出现故障情况下向空压机、增压机供油,保证压缩机组的平安。
2.2空气预冷系统〔A〕、温度<105℃的空气由底部进入空冷塔C01201内;空冷塔的水分循环冷却水和循环冷冻水两路,进入空冷塔的空气首先经循环冷却水泵P01201A/B送至下塔顶部,流量为452t/h 、32℃的冷却水洗涤冷却,再经过循环冷冻水泵P01202A/B送至上塔上部流量为100t/h 、8℃的冷冻水进行洗涤冷却后由塔顶出来,温度被降至10℃送进入分子筛纯化系统。
循环冷却水流量由V012004〔FIC012002〕控制,空冷塔C01201下塔的液位由V012038〔LIC012001〕控制,循环冷却水流量设有高、低流量连锁,当循环冷却水到达联锁值时将自动启停泵用循环冷却水泵。
空分工艺流程详细工艺

空分工艺流程详细工艺空分工艺是一种广泛应用于工业领域的物理分离技术,用于从混合气体中分离出不同成分。
该工艺利用混合气体中成分之间的差异,通过压缩、冷却、膨胀等物理过程将混合气体中的不同组分分离出来。
空分工艺主要由压缩、冷却、分离和再压缩四个过程组成。
下面将详细介绍空分工艺的流程。
首先是压缩过程。
混合气体进入压缩机,经过增压泵给气体施加高压。
这样可以提高气体的密度和温度,为后续的冷却过程做好准备。
其次是冷却过程。
经过压缩的气体进入冷却器,通过传热的方式将气体冷却至低温状态。
通常采用的冷却介质为液氮或液氩,通过与气体接触而带走热量,使气体温度下降。
接着是分离过程。
经过冷却的气体进入分离塔,在塔内进行分离。
分离塔内通常装有分离柱,分离柱呈填料状或换热管状。
混合气体在分离柱内经过多次的上升和下降,通过相互的接触和负载传递,将气体中的不同组分分离出来。
分离柱上部进气口进入气体在塔内逐渐升温,饱和出口和活性出口一起出,分别为焦油沉着型和贮存型氧气。
最后是再压缩过程。
分离后的气体有些会被进一步利用,如氧气可以用于制造化学品、燃料等;而有些则需要进一步处理,如二氧化碳可以通过再压缩装置再次分离。
经过再压缩的气体再次进入压缩机,并进行再次增压。
这样可以提高气体的压力和纯度,使其适应不同的工业需求。
空分工艺流程中的每个环节都有其重要的作用。
压缩和冷却过程可以提高气体的密度和温度,为分离过程做好准备;分离过程则是将混合气体中的不同成分分离出来;而再压缩过程则是对分离后的气体进行进一步处理,以满足不同的工业需求。
空分工艺的应用十分广泛,被广泛应用于煤矿、石油、化工、冶金等行业。
它不仅可以提取出许多重要的工业气体,如氧气、氮气、氩气等,还可以用于处理废气排放、净化空气等环保领域。
同时,空分工艺也是一项高能耗的工艺,因此如何提高工艺的效率和降低能耗也是当前该领域面临的挑战之一。
空分流程详细讲解

空分流程详细讲解
在化工生产中,空分技术是一项非常重要的工艺,它能够将空气中的氧气、氮
气等气体进行分离,以满足工业生产和生活需求。
下面我们将详细介绍空分的工艺流程。
首先,空分的工艺流程可以分为压缩、预冷、精馏、蒸汽回收等步骤。
1. 压缩空气从大气中获取,首先需要将其进行压缩,以增加气体分子的密度,提高分离效率。
压缩后的空气会进入压缩机,经过一系列压缩工艺,压缩比达到要求后,进入下一个环节。
2. 预冷压缩后的空气含有大量水分和杂质,需要通过冷却器进行预冷处理。
在预冷过程中,空气中的水分和杂质会凝结成液体,然后通过分离装置将其分离出去,以保证后续工艺的顺利进行。
3. 精馏精馏是空气分离的核心步骤,通过精馏塔将空气中的氧气、氮气等气体按照其沸点的不同进行分离。
在精馏塔内,气体混合物被加热至沸点,然后在不同高度上凝结成液体,从而实现气体的分离。
4. 蒸汽回收在精馏过程中,会产生大量的废热,为了提高能源利用效率,通常会将废热通过蒸汽回收装置进行回收利用。
蒸汽回收装置可以将废热转化为蒸汽,用于加热其他部分的工艺设备,实现能量的循环利用。
通过以上流程,空分技术能够高效地将空气中的氧气、氮气等气体进行有效分离,为工业生产和生活提供了重要的物质基础。
在实际应用过程中,还需要根据不同的需求和工艺要求进行调整和优化,以实现最佳的分离效果和能源利用效率。
空分技术作为一种成熟的工艺,在化工领域中扮演着至关重要的角色,不仅广
泛应用于气体生产、化工生产等领域,还在医疗、食品加工等领域有着重要的应用价值。
随着工业化进程的不断推进,空分技术将继续发挥重要作用,为人类的生产生活提供更广阔的发展空间。
空分工艺流程简介

设备紧凑,能耗低,操作简便。但膜材料性能要求较高,分离效率受膜材料影响较大。
03
空分设备组成及功能
空气压缩机
01
将大气中的空气吸入并进行压缩,提高空气的压力 和温度。
02
为后续的冷却、纯化和分离过程提供必要的动力。
03
通常采用多级压缩和级间冷却的方式,以提高压缩 效率和降低能耗。
冷却器与纯化器
原理
空分工艺主要基于空气中氧气、氮气等组分的沸点不同,通过精馏方法将其分 离。在低温条件下,空气被液化后送入精馏塔,经过多次部分汽化和部分冷凝, 实现各组分的分离。
空分工艺应用领域
冶金工业
用于高炉富氧炼铁、炼 钢吹氧等,提高产量和
降低能耗。
化学工业
石油工业
医疗保健
作为合成氨、合成甲醇 等化工过程的原料气。
分离过程
精馏塔分离
利用精馏塔中的温度梯度和浓度梯度,使空气组分在塔内多次部分汽化和部分冷凝,实现氧气、氮气等组 分的分离。
冷凝蒸发法
通过冷凝器将空气液化后,利用不同组分的沸点差异进行分离。液氧在冷凝蒸发器中蒸发,同时吸收热量, 使液氮冷凝成液体,从而实现氧氮分离。
产品输出与储存
产品输出
将分离得到的氧气ቤተ መጻሕፍቲ ባይዱ氮气等产品通过管道 输送至用户端或储存设备。
再生技术
采用加热、减压等方法对 吸附剂进行再生,恢复其 吸附性能。
膜分离法关键技术与参数
膜材料选择
选用具有高渗透性、选择 性和稳定性的膜材料,如 有机膜、无机膜等。
膜组件设计
通过合理的膜组件结构设 计和优化,提高膜分离效 率。
操作条件
控制适当的操作温度、压 力和膜两侧浓度差,以实 现目标组分的有效分离。
- 1、下载文档前请自行甄别文档内容的完整性,平台不提供额外的编辑、内容补充、找答案等附加服务。
- 2、"仅部分预览"的文档,不可在线预览部分如存在完整性等问题,可反馈申请退款(可完整预览的文档不适用该条件!)。
- 3、如文档侵犯您的权益,请联系客服反馈,我们会尽快为您处理(人工客服工作时间:9:00-18:30)。
空分站工艺流程简介
空分装置(Air Separation Unit,ASU)是用来分离空气中的各组分气体,为全厂工艺装置及各辅助装置提供所需要的氧气、氮气、氩气等气体和液体产品的装置。
氧气和氮气是炼化装置中不可缺少的原料气和保护气。
在空分领域中’深冷法、变压吸附法、膜分离法是应用于工业生产的三大分离方法a深冷法是传统的制氧(氮)方法,在国内外的制氧(氮)行业中仍占据着统治地位,适用于氧(氮)气需求量大(PSA)高,a要求连续供气,并将液氧(氮)作为储
备气源的生产场合'变压吸附法(PsA)和膜分离法是新兴的制氧(氮)方法,其技术
日臻成熟,适用于氧(氮)气需求量小、纯度低、开停迅速、操作弹性大、无需液体产品的生产场合。
目前,国内外大型空分装置流程多数采用深冷法。
根据产品压缩情况,深冷法可分为外压缩流程和内压缩流程。
其中,内压缩流程较为广泛地应用在冶金、石油化工等行业。
根据循环增压机压缩介质的不同,内压缩流程通常可分为空气循环流程和氮气循环流程。
目前空分设备流程主要分为外压缩流程和内压缩流程。
外压缩流程就是空分设备生产低压氧气,然后经氧压机加压至所需压力供给用户。
内压缩流程是相对于外压缩而言的。
就是取消氧压机,直接从空分设备生产出中高压的氧气供给用户。
内压缩流程与外压缩流程的主要区别在于产品氧的供氧压力是液氧在冷箱内经液氧泵加压达到的。
在炼油和石油化工企业的生产中,作为常用吹扫介质的工厂空气及仪表动力来源的仪表空气是必不可少的。
因此,在炼油和石油化工企业的工厂设计中,经常能遇到作为重要辅助设施的空压站的设计。