世界 强精益生产系统 框架介绍
如何构建精益生产体系

如何构建精益生产体系精益生产体系的构建方法精益生产是一种高效率、高质量、灵活性强的生产方式,其基本原理和方法对制造业有着积极的意义。
以下是构建精益生产体系的几种方法:1.准时化准时化是指在需要的时间、按需求量生产所需的产品。
为了实现准时化,需要采用及时生产(JIT)方式控制现场生产流程。
看板管理是其中的一种工具,可以使信息流程缩短,使生产过程中的物料流动顺畅。
及时生产方式的看板信息包括零件号码、品名、制造编号、形式、容量、发出看板编号、移往地点、零件外观等。
看板在生产线上分为领取看板和生产看板。
2.标准作业标准作业是将作业人员、作业顺序、工序设备的布置、物流过程等问题做最适当的组合,以达到生产目标而设立的作业方法。
它是以人的动作为中心、按没有浪费的操作顺序进行生产的方法。
标准作业是管理生产现场的依据,也是改善生产现场的基础。
3.少人化精益生产提高效率的目标之一是少人化。
少人化就是根据产量的多少来增减人工,从而达到用最少的人员满足顾客的生产需求。
实现少人化,必须满足以下3个前提条件:采用一个流生产;要经常审核、修改作业标准和作业标准组合;有具备能操作多种工序的能力的训练有素的作业人员。
4.快速换产快速换产是一种能有效缩短产品切换时间的理论和方法。
切换时间是指从前一种产品加工结束转换到能生产出后一种产品的合格时所需要的时间。
快速换产的理论和方法称为SMED。
5.柔性化柔性生产是通过系统结构、人员组织、运作方式和市场营销等方面的改革,使生产系统能对市场需求变化作出快速的适应,同时消除冗余无用的损耗,力求企业获得更大的效益。
计算机及自动化技术是柔性生产的物质技术基础。
例如柔性制造系统(FMS)是以统一的信息控制系统和自动物料储运系统连接起来的一组加工设备,能在不停机的情况下实现多品种工件的加工,并具有一定管理功能。
柔性生产是全面的,不仅是设备的柔性,还包括管理、人员和软件的综合柔性。
与柔性生产相适应,当前国际上柔性管理也开始出现。
与时俱进的精益:世界三大精益生产体系及应用比较
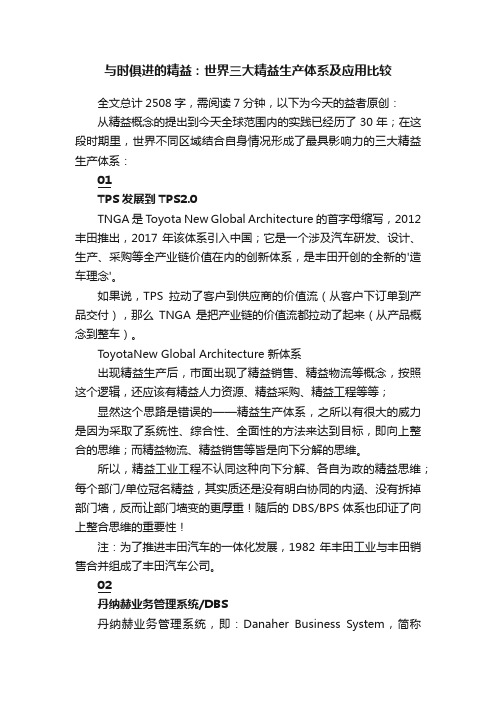
与时俱进的精益:世界三大精益生产体系及应用比较全文总计2508字,需阅读7分钟,以下为今天的益者原创:从精益概念的提出到今天全球范围内的实践已经历了30年;在这段时期里,世界不同区域结合自身情况形成了最具影响力的三大精益生产体系:01TPS 发展到TPS2.0TNGA是Toyota New Global Architecture 的首字母缩写,2012丰田推出,2017年该体系引入中国;它是一个涉及汽车研发、设计、生产、采购等全产业链价值在内的创新体系,是丰田开创的全新的'造车理念'。
如果说,TPS拉动了客户到供应商的价值流(从客户下订单到产品交付),那么TNGA是把产业链的价值流都拉动了起来(从产品概念到整车)。
ToyotaNew Global Architecture 新体系出现精益生产后,市面出现了精益销售、精益物流等概念,按照这个逻辑,还应该有精益人力资源、精益采购、精益工程等等;显然这个思路是错误的——精益生产体系,之所以有很大的威力是因为采取了系统性、综合性、全面性的方法来达到目标,即向上整合的思维;而精益物流、精益销售等皆是向下分解的思维。
所以,精益工业工程不认同这种向下分解、各自为政的精益思维;每个部门/单位冠名精益,其实质还是没有明白协同的内涵、没有拆掉部门墙,反而让部门墙变的更厚重!随后的DBS/BPS体系也印证了向上整合思维的重要性!注:为了推进丰田汽车的一体化发展,1982年丰田工业与丰田销售合并组成了丰田汽车公司。
02丹纳赫业务管理系统/DBS丹纳赫业务管理系统,即:Danaher Business System,简称DBS;提到丹纳赫系统,必须提一个人。
那就是1984年加盟丹纳赫公司的原执行副总裁亚特·伯恩(Art Byrne)先生,他曾经在通用电器学习丰田生产方式,也是当时丹纳赫唯一一个知道丰田生产方式的人。
丹纳赫业务管理系统/DBS构建历程1985年,日本的持续改善思想(KAIZEN)之父今井正明先生在康州举办研讨班,亚特·伯恩参加了这个研讨班,之后又邀请了日本新技能咨询公司的顾问团队,来到由他主管的雅各布制动器公司。
最新整理精益生产体系的结构与特征.doc

精益生产体系的结构与特征如果把精益生产体系看作是一幢大厦,那么大厦的基础就是计算机网络支持下的小组工作方式。
在此基础上的三根支柱就是:(1)准时生产(JIT),它是缩短生产周期,加快资金周转和降低成本,实现零库存的主要方法;(2)成组技术(GT),它是实现多品种、小批量、低成本、高柔性,按顾客定单组织生产的技术手段;(3)全面质量管理(TQC),它是保证产品质量、树立企业形象和达到无缺陷目标的主要措施,如图1所示。
一、精益生产体系的目标(一)精益生产的基本目标工业企业是以盈利为目的,从事商品生产的社会经济组织。
因此,最大限度地获取利润就成为企业的基本目标。
传统的大量生产方式是以标准化、大批量生产来降低成本,提高效率的,完全是依靠规模效益来实现企业利润目标的。
这种生产方式在经济高速增长、市场需求相对稳定的时期能取得良好的效果。
因为在这种情况下,实际上不需要太严密的生产计划和细致的管理,即使出现生产日程变动、工序间在制品储备不断增加、间接作业工时过大等问题,只要能保证产品质量,企业便可放手大量生产,确保企业利润就不成问题。
然而,在市场瞬息万变的今天,在实行多品种、小批量生产的情况下,这一生产方式显然是行不通的。
精益生产是采用灵活的生产组织形式,根据市场需求的变化,及时、快速地调整生产,依靠严密细致的管理,力图通过“彻底排除浪费”,防止过量生产来实现企业的利润目标的。
因此,精益生产的基本口的是要在一个企业里,同时获得极高的生产率、极佳的产品质量和很大的生产柔性。
为实现这一基本目的,精益生产必须能很好地实现以下三个子目标:零库存、高柔性(多品种)、无缺陷。
(二)精益生产的子目标[ ]1.零库存在传统生产系统中,在制品库存和成品库存被视为资产,期末库存与期初库存之差代表这一周期流动资产的增值,用以表示该部门效益的提高。
当由不确定的供应者供应原材料和外购件时,原材料和外购件的库存可视为缓冲器。
所以,原材料、外购件和成品的库存能作为供应昔不按期供货或顾客订购量增加的缓冲。
世界三大精益生产体系及应用比较
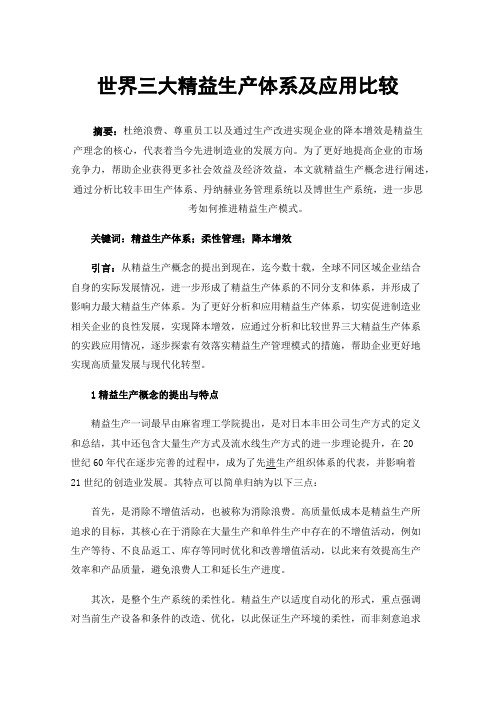
世界三大精益生产体系及应用比较摘要:杜绝浪费、尊重员工以及通过生产改进实现企业的降本增效是精益生产理念的核心,代表着当今先进制造业的发展方向。
为了更好地提高企业的市场竞争力,帮助企业获得更多社会效益及经济效益,本文就精益生产概念进行阐述,通过分析比较丰田生产体系、丹纳赫业务管理系统以及博世生产系统,进一步思考如何推进精益生产模式。
关键词:精益生产体系;柔性管理;降本增效引言:从精益生产概念的提出到现在,迄今数十载,全球不同区域企业结合自身的实际发展情况,进一步形成了精益生产体系的不同分支和体系,并形成了影响力最大精益生产体系。
为了更好分析和应用精益生产体系,切实促进制造业相关企业的良性发展,实现降本增效,应通过分析和比较世界三大精益生产体系的实践应用情况,逐步探索有效落实精益生产管理模式的措施,帮助企业更好地实现高质量发展与现代化转型。
1精益生产概念的提出与特点精益生产一词最早由麻省理工学院提出,是对日本丰田公司生产方式的定义和总结,其中还包含大量生产方式及流水线生产方式的进一步理论提升,在20世纪60年代在逐步完善的过程中,成为了先进生产组织体系的代表,并影响着21世纪的创造业发展。
其特点可以简单归纳为以下三点:首先,是消除不增值活动,也被称为消除浪费。
高质量低成本是精益生产所追求的目标,其核心在于消除在大量生产和单件生产中存在的不增值活动,例如生产等待、不良品返工、库存等同时优化和改善增值活动,以此来有效提高生产效率和产品质量,避免浪费人工和延长生产进度。
其次,是整个生产系统的柔性化。
精益生产以适度自动化的形式,重点强调对当前生产设备和条件的改造、优化,以此保证生产环境的柔性,而非刻意追求自动化和机械化的生产设备,以此来避免资金和技术浪费,提高生产计划的合理性与可行性[1]。
最后,是在员工管理上的人性化。
不同于传统的生产方式对员工的施压和约束,精益生产模式给予了员工更多的自主权利,而且在人事组织结构上有着扁平化的特点,不仅消除了上下级之间隔阂,而且提升了信息沟通效率,有助于构建团结一心的企业文化氛围。
精益理论框架课件
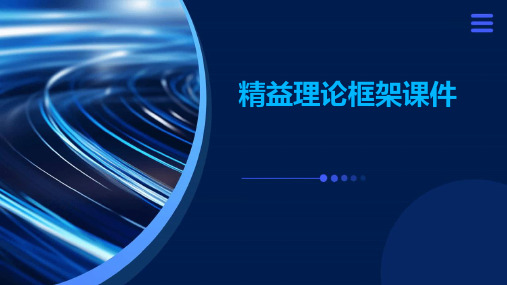
资源利用:传统管理往往存在资源闲置 和浪费,精益管理强调资源的有效利用 。
员工角色:传统管理中员工往往只是执 行者,精益管理鼓励员工参与改进和创 新。
02
CATALOGUE
精益理论框架的核心元素
价值流分析
01
02
03
定义
价值流分析是精益理论中 的一个重要工具,用于识 别、分析和优化生产过程 中的价值流动。
目的
通过消除浪费、提高效率 ,以最小的成本、最短的 时间为客户提供最大的价 值。
实施步骤
包括绘制价值流图,识别 增值活动和非增值活动, 制定改进措施等。
持续改进
定义
持续改进是精益理论中的一个核 心理念,强调在不断地寻求、实 施小的改进中,实现长期的、显
著的成果。
目的
通过持续改进,企业能够逐渐消除 浪费,提升效率,提高产品质量, 增强竞争力。
精益管理的基本理念和原则
基本理念
持续改进、尊重员工、客户至上。
原则
消除浪费、流程优化、拉动式生产、持续改进、全员参与。
精益管理与传统管理的比较
目标导向:传统管理重视计划和预算, 精益管理关注持续改进和适应变化。
以上内容仅为初步扩展,每个子标题下 可根据实际需求进一步丰富和完善内容 。
客户关系:传统管理可能更关注产品本 身而非客户需求,精益管理则强调满足 客户需求和建立长期关系。
04
CATALOGUE
精益理论框架的应用与拓展
精益理论框架在制造业的应用
生产流程优化
通过精益理论框架指导,制造业 企业可以消除生产浪费,提升生 产效率,实现流程的优化和再造
。
质量管理提升
精益理论框架强调质量是制造出 来的而非检验出来的,企业可以 通过持续改进生产过程中的质量 问题,提升整体质量管理水平。
精益生产及AOS专题汇报
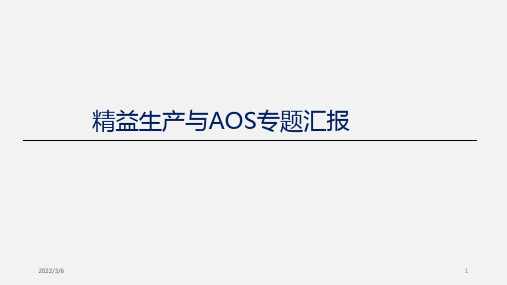
零浪费PICMDS 零转产工时浪费、零库存、 零浪费、零不良、零故障、零停滞、零灾害
JIT(准时化)
自动化
连续流 一个流 均衡化 拉动式 柔性化 标准化
出现问题自动停产 ANDON 人机分离 防止错误 就地品管
解决根本原因
精益思想:持续改进,消除生产中的一切浪费
现场5S、TPM、TQM、精益六西格玛、目视管理、看板、单元 生产、均衡生产、快速换模、IE、多能工、混合生产、标准化作
柔性化
成组技术、多品种小批量、多能工、快速响应市场需求
标准化
4 精益生产核心理念
自动化(Jidoka)
20世纪初,丰田集团创始人Sakichi Toyada –织布机 出现问题自动停产(停机) 人工智能、自动控制,将质量融入生产、人机分离、多工序操作(一人多机) ANDON、就地品管、防止错误 解决根本原因
出现问题自动停产 ANDON 人机分离 防止错误 就地品管
解决根本原因
精益思想:持续改进,消除生产中的一切浪费
现场5S、TPM、TQM、精益六西格玛、目视管理、看板、单元 生产、均衡生产、快速换模、IE、多能工、混合生产、标准化作
业、价值图分析、并行工程、持续改善
4 精益生产核心理念 JIT(Just in time)准时制
夯 实 基 础
战略类 运营类
管理与 支持类
战略管理
市场+研发+采购+生产制造+客户服务
人力资本管理 财务管理 资产管理 EHS
物流运输管理
品牌管理 审计与风险管理
IT与知识管理 变革与持续改进
企业文化
持 续 改 进
条件要素(精益思想+管理需求、意识、基础)
精益生产组织架构
精益生产组织架构与职责说明书1.职责,权限1.1 总则为确保公司精益生产工作顺利开展,保证阶段性项目能够如期完成,应对组织架构、项目小组人员以及其他小组人员的职责和权限做出明确规定。
1.2 精益生产组织架构·推进委员会:任主任,任副主任,各单位主管组成。
·精益办公室(项目小组):·各单位推进组:各单位主管,技术管理人员,车间班组长。
1。
3 精益办公室成员主要职责和权限1)参与实施并执行制度/宣传/考核/日常管理、培训/认证、项目管理;2)学习了解精益生产18个黄金法则和各种相关文件知识,熟悉掌握精益项目计划书和实施说明,并对其中涉及的各个项目制定详细的推进计划;3)对推进计划中必要实行的项目建立项目管理与奖惩机制,与推进委员会和各单位推进组成员积极沟通,指导推进组积极开展项目,并验收成果;4)对推进过程中发现的问题与精益项目指导老师进行沟通探讨,共同完善推进计划;4)积极听取和整合各单位推进组的反馈信息,允许对推进计划进行小范围修改;6)配合精益项目指导老师制定组织结构和各单位关键职能,人才教育培养和发展计划,绩效管理系统,基准分析持续改进和基准架构等关键项目指标;7)制定项目管理办法。
包括项目范围管理,项目进度管理,项目成本管理,项目人力资源管理,项目质量管理,项目沟通管理,项目知识管理,项目风险管理。
1。
4 各单位推进组主要职责及具体分工各单位推进组必须严格执行项目小组制定实施的各项项目管理办法,积极开展项目,对实施过程中碰到的问题及时反馈意见,加强沟通,共同探讨合适、合理的解决办法,并由项目小组最终制定解决方案.1。
4。
1 各单位主管1)作业详细排产. 基于生产计划,生产提前期、关键物料库存、生产中的交错/重叠/并行操作、产能等约束条件,制定各个生产单元的详细作业计划,同时设定作业计划的优先级等重要属性。
通过良好的作业顺序最大限度减少生产过程中的准备时间,优化车间性能;2)调度生产。
精益生产与AOS专题汇报
5 精益生产管理工具
TPM(Total Productive Maintenance)全员生产维护
全效率:设备寿命周期费用评价和设备综合效率 全系统:指生产维修系统的各个方法都要包括在内。即是PM、MP、CM、 BM等都要包含。 全员参与:指设备的计划、使用、维修等所有部门都要参加,尤其注重的是操作者的自主小组活动。
并行工程(Concurrent Engineering,CE)
并行工程是对产品及其相关过程(包括制造过程和支持过程)进行并行、集成化处理的系统方法和综 合技术。 产品开发人员从一开始就考虑到产品全生命周期(从概念形成到产品报废)内各阶段的因素(如功能、 制造、装配、作业调度、质量、成本、维护与用户需求等等),并强调协同工作,使后续环节中可能 出现的问题在设计的早期阶段就被发现,并得到解决,从而使产品在设计阶段便具有良好的可制造性、 可装配性、可维护性及回收再生等方面的特性,最大限度地减少设计反复,缩短设计、生产准备和制 造时间。
vertical v. to incline or bend from a vertical position; rely on for support adj. lacking excess flesh; containing little excess
精益: 精益求精,持续改善,小,少而精,集约,精细,细致,精确,精准,精致。
生产执行过程中
的异常问题
6
改进
异常快速处理 需求
改进 需求
改进实施 反馈
5 分析及改进
问题处理 反馈
精益生产(Lean Production, LP): 通过持续改进,消除生产中的一切浪费,以降低成本、缩短生产周期和改善
精益生产理念及体系简介
看板操作的六个使用规则
没有看板不能生产也不能搬运。 看板只能来自后工序。 前工序只能生产取走的部分。 前工序按收到看板的顺序进行生产。 看板必须和实物一起。 不把不良品交给后工序。
标准化作业
所谓作业标准化,就是对在作业系统调查分析的基 础上,将现行作业方法的每一操作程序和每一动作 进行分解,以科学技术、规章制度和实践经验为依 据,以安全、质量效益为目标,对作业过程进行改 善,从而形成一种优化作业程序,逐步达到安全、 准确、高效、省力的作业效果。
快速换模法这一概念指出,所有的转变(和启动)都 能够并且应该少于10分钟-----因此才有了单分钟这一 说法。所以又称单分钟快速换模法、10分钟内换模 法、快速作业转换,用来不断设备快速装换调整这 一难点的一种方法-将可能的换线时间缩到最短(即时 换线)。
SMED法的三个基本要点
区分“内变换操作”和“外变换操作”。 减少“内变换操作”。 缩短“内变换操作” 时间。
标准化有以下四大目的:技术储备、提高效率、防 止再发、教育训练。
Poka-Yoke概念
日本的质量管理专家、著名的丰田生产体系创 建人新江滋生(Shingeo Shingo)先生根据其 长期从事现场质量改进的丰富经验,首创了 Poka-Yoke(差错预防或防呆)的概念。
防呆法的意思简单地说就是如何去防止错误发 生的方法。
60年代起源于美国的PM(预防保全),经过 日本人的扩展及创新,于81年形成了全公司 的TPM(全面生产管理),并在日本取得巨大 成功。
TPM改善侧重于事前预防。
拉动系统和看板Kanban
看板管理方法是在同一道工序或者前后工序之间进行 物流或信息流的传递。
如图1所示,一旦主生产计划确定以后,就会向各个 生产车间下达生产指令,然后每一个生产车间又向前 面的各道工序下达生产指令,最后再向仓库管理部门、 采购部门下达相应的指令。这些生产指令的传递都是 通过看板来完成的。
精益生产简介PPT课件
原料
成品
BATCH SIZE 周期时间
Transport Time Operation 3
Operation Time Operation 7
Rework Operation 4
Setup Operation 10
传统功能重点
工作站 (局部化) 效率
原料
操作 1
操作 2
操作 3
操作 4
成品
效率 产出 / 天
机器模型原型生产当应用补充拉系统时必须使用一般拉系统补充拉系统补充拉系统应与一般拉系统同时使用以使lead时间的变动最小从而满足发货时间的要求补充拉系统逐个部件地将需求和流程分析应用于原料战略性wip仅当需要时成品如需要的适当存货规模并与过程能力和市场需求相平衡补充拉系统在过程中建立战略性分布的部件缓冲量buffer原料通过buffer存货将供应过程与消费过程分离部件补充是根据消费与净需求的关系将来需求帮助确定buffer规模而非真实的提供原料补充循环特定部件数的拉系统循环是生产过程中的一个连续路径其中产品需求促进产品补充拉拉系统中的典型循环消费推动的生产正确产品正确数量正确时间受约束的过程存货规模部件短缺情况的减少存货减少最好是达到最小化战略性buffer战略性buffer生产线周期时间顾客预期补充信号购买指令补充信号销售指令消费消费生产线生产销售商计算补充拉系统的因素为了正确计算拉系统的规模应知道每个战略性补充循环中的每次部件中的以下数据
40.0% 35.0% 30.0% 25.0% 20.0%
Ap Ma Jun Jul Au Se Oc No De Jan Fe Ma
ry
g pt t v c
br
Operating Income % (3 Mo. Rolling)
- 1、下载文档前请自行甄别文档内容的完整性,平台不提供额外的编辑、内容补充、找答案等附加服务。
- 2、"仅部分预览"的文档,不可在线预览部分如存在完整性等问题,可反馈申请退款(可完整预览的文档不适用该条件!)。
- 3、如文档侵犯您的权益,请联系客服反馈,我们会尽快为您处理(人工客服工作时间:9:00-18:30)。
精益模块 上述原则得以实现的保证
文件 BPS-手册 指导新规划的规划指南 成熟模型
项目 改进现行的生产系统 新规划 完善的评估
12
Introduction to BPS
House of orientation
目标: - 改进质量, 成本, 物流 - 行业最优
原则: - 客户至上 - 员工之上 - 过程导向 - 透明化
• 适应产量变化的柔性度低 交 付
• 适应产品变化的能力低 • 交付表现 92%
.....
要求
• 启动稳定
成
• 低投资
本
• 降低库存
• 0-英里 << 10 ppm
质 量
• 过程可控,维护需求小
• 具有适应产量和产品
品种变化的柔性度
交
付
• 交付表现100%
5
Introduction to BPS
价值贡献
CRV Common Rail Distributer
4
TPEX - Travel Pilot
ESP
ABS
DPF
10
CP1H Common Rail Pump
CP4
CP4 Common Rail Pump
12
DMV Diesel Magnet Valve
工厂
产品
10
Introduction to BPS
Meldung).
虽然大幅度的上下波动显示出过程的某种不稳定性,但是上升的趋势还是显而易见的。
8
Introduction to BPS 特征
降低
• 投资 • 质量成本 • 服务成本 • 班次奖金 • 加班工资 • 原料成本
C成本
Q质量
降低
• 报废 • 返工 • 测试 • ppm值 • 缺陷
D交付
降低
(Preview based on Wipl. 2004 ff)
∅平均库存水平(天)
100
88
87
84
80
80
65
60
60
58
60
57
55
52
49
40
47
45
43
40
20
2010年库存水平目标
0
2002
2003 V-Ist 2004 VS 2005
* GEZ based on NGU
100
78
80
56
Production System (BPS)
1
Introduction to BPS
传送系统的科学分析 团队合作
看板
及时生产 计划客户满意
TQM
七大工具
FPS MPS
科学人力研究 Aggressive
SE
Selling
系统供货
TPM
科学管理
Taylorismus REFA
Taylor, Ford
•交付时间 • Through put time •原材料,半成品(WIP), 成品 • 批次大小
提高
•OEE(设备利用率)
9
Introduction to BPS
PHEK(制造成本)-在试点项目里的降低情况
在现有的生 产线内部实
施
在现有的生产系 统内实施(比如
某个工厂)
1
ESP5.7
2
ABS5.3
持续改进
17
Introduction to BPS
小结:
Î Bosch生产系统(BPS)服务于全球范围内有关我们产品的质量, 交付和成本的改善,目标是在稳定的基础上增加收益。
Î 实施BPS的目标在于实现工作流程标准化、精益和快速,并满 足“最优”要求;使过程无误运行,从而减轻员工负担。
Î 所以我们使用已经证实的生产准则和我们已广泛长久实施的各 项工具.
开始丰田生产系 统
对‘持续改进’ 的英文翻译
„精益思想“ „改变世界的机器“ Womack, Jones
Womack, Jones
Shingeo Shingo
Ohno, Toyota Juran, Kamiya
1910
1940
1950
1960
1980
1992
1997 2002
历史
开始精益生产
西半球开始精益生产
2
Introduction to BPS
“精益生产”的概念是...
...通过持续改进,提高效率, 实现标准化.
…引导工作流程浪费最 小化的企业哲学
...以日本的经营方式为导向的 管理体系.
...以人为本...
Ohno*
...同时适用于内部及 外部组织结构
“只生产客户需要的!”
...员工相互着想,作 决定,相互合作,相 互支持
供应商
.. 多 (或少)都是 浪费,
是过程不稳定的 信号
客户
创建生产和物流的全局观 Î 博世生产系统
4
Introduction to BPS
现状
• 启动成本高 • 投资基础高
-投资 - 库存
Common Rail
成 本
• 0-英里 > 60 ppm • 质量保证费用高 • 内部缺陷成本高Biblioteka 质量EHB
60
47 40
! 38 20
10
0
VS 2006
UBG UBK UBI RB World
要实现库存水平为10天的目标,就有必要达到一个更高层次的BPS的实施.
7
Introduction to BPS
UBK不同事业部的交付表现
100
95
90
85
时间: 04/2004
GS DS CS AE EB CM 平均值 除了 AA
LIWAKS [in%]
80
Jan Apr May Jun Jul Aug Sep Oct Nov Dec Feb Mar Apr
01 03 03 03 03 03 03 03 03 03 04 04 04
月/年
注意: Jan 04 is not available because of shortened MGB (without LIWAKS
z 质量 z 交付 z 成本
C
MAE – 减少 > 30% 劳动生产率增高 » 10% p. a.
0-公里 < 30 ppm
新 10ppm
Q
缺陷成本 < 100 ppm
D
库存降低 < 10 天 交付表现100%
客户满意
6
Introduction to BPS
GEZ-Bosch 全球平均值* (GEZ= 库存水平)
...引入拉动式体系,即及时交付...
* Ohno: 丰田生产系统的创立者
...以客户为导向,以质量和降 低成本为导向.
3
Introduction to BPS
BPS的基本方法
我们只规划、生产、组装、运输 ...
z 正确的零件 z 正确的数量 z 在正确的时间 z (合格的质量) z (在正确的地点)
40
最佳实践 Toluca (TlP)
30
-26%
GEZ
20
关键数据的重大改进:
10
Î GEZ (库存周期天数) 从 31 天 (2002) 降至 23 天 (V-Ist 2004)
0 2002
0,8%
2003
V-Ist VS 2005 VS 2006 2004
Failure costs
Î 缺陷成本从 0,52% (2002) 降至 0,28% (V-Ist 0,6%
全员满意
交付
过程透明化 标准化
持续改进
14
Introduction to BPS
BPS准则—方针
完美质量
以过程为导向
过程透明化
柔性度
消除浪费
拉动式生产
标准化
和
持续改进
全员参与
BPS工具—保证
Wertstrom design
TPM
QTools
Poka Yoke
KaizenWorkshop
Quick
Changeover
2004)
0,4%
-46%
Î 0-km 从157 ppm (2002)降至3 ppm (V-Ist 2004)
0,2%
0,0% 200
2002
2003
V-Ist 2004
VS 2005
VS 2006
Î 构造成本从15,0% (2002) 降至13,5% (2004) 150
in PHEK fix/PHEK
实施
Î 必须使谁参与/深信BPS的可以成功实施?BPS是目标的一部分吗? Î 障碍是什么,如何清除? Î 如何测量实施所取得的进展,如何与参与人员进行沟通? Î 我如何能够并支持员工引入BPS?
16
Introduction to BPS
远景
Bosch生产系统 以价值为基础的管理模式 及时介入市场 以客户为焦点 ....... 持续改进 为基础 生产分析
Kanban
Lean Line Design
Ship to Line
5S
TOP
Flow Oriented Layout
Low-Cost Automation
Supplier Development
...
15
Introduction to BPS
BPS 是主管人员的任务,不能委派代理
远景
Î 根据BPS的介绍,我想要实现的是什么? Î 在我的职责范围,工厂里,BPS的远景是什么样的? Î 根据BPS远景,我所能实现的目标有哪些?