对刀仪使用说明M70
M70绝对位置设置说明
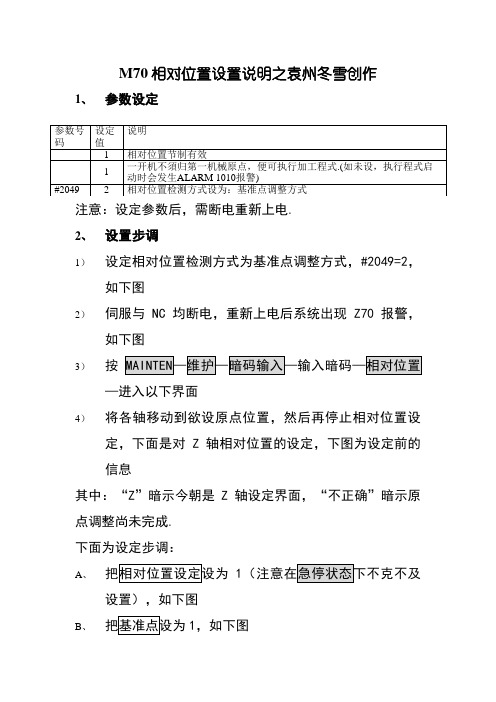
M70相对位置设置说明之袁州冬雪创作
1、参数设定
注意:设定参数后,需断电重新上电.
2、设置步调
1)设定相对位置检测方式为基准点调整方式,#2049=2,如下图
2)伺服与 NC 均断电,重新上电后系统出现 Z70报警,如下图
3)按
—进入以下界面
4)将各轴移动到欲设原点位置,然后再停止相对位置设定,下面是对Z轴相对位置的设定,下图为设定前的信息
其中:“Z”暗示今朝是Z轴设定界面,“不正确”暗示原点调整尚未完成.
下面为设定步调:
A、
1
设置),如下图
B、
1,如下图
C、设定原点值(可默许为1
5)此时Z
.
6).三轴设定完后Z70报警会消失.
7)完成上面步调后,相对位置设置即完成,NC再启动即可.。
对刀仪操作规范
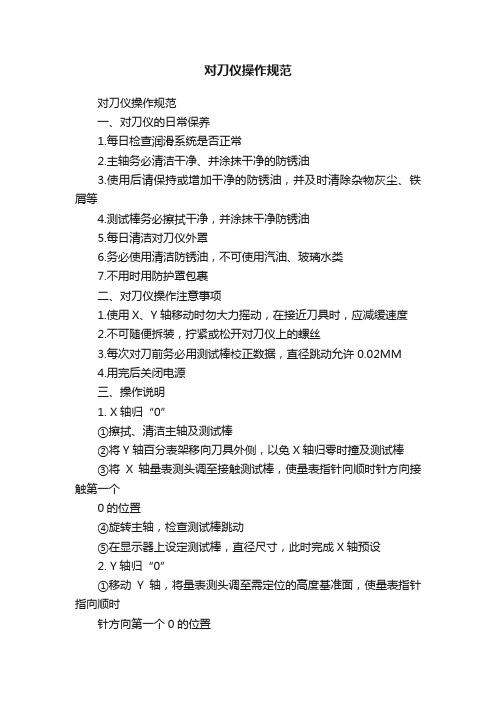
对刀仪操作规范
对刀仪操作规范
一、对刀仪的日常保养
1.每日检查润滑系统是否正常
2.主轴务必清洁干净、并涂抹干净的防锈油
3.使用后请保持或增加干净的防锈油,并及时清除杂物灰尘、铁屑等
4.测试棒务必擦拭干净,并涂抹干净防锈油
5.每日清洁对刀仪外罩
6.务必使用清洁防锈油,不可使用汽油、玻璃水类
7.不用时用防护罩包裹
二、对刀仪操作注意事项
1.使用X、Y轴移动时勿大力摇动,在接近刀具时,应减缓速度
2.不可随便拆装,拧紧或松开对刀仪上的螺丝
3.每次对刀前务必用测试棒校正数据,直径跳动允许0.02MM
4.用完后关闭电源
三、操作说明
1. X轴归“0”
①擦拭、清洁主轴及测试棒
②将Y轴百分表架移向刀具外侧,以免X轴归零时撞及测试棒
③将X轴量表测头调至接触测试棒,使量表指针向顺时针方向接触第一个
0的位置
④旋转主轴,检查测试棒跳动
⑤在显示器上设定测试棒,直径尺寸,此时完成X轴预设
2. Y轴归“0”
①移动Y轴,将量表测头调至需定位的高度基准面,使量表指针指向顺时
针方向第一个0的位置
②在显示器上设定Y轴值为0或任何预设值,此时完成Y轴高度预设。
三菱M70M80对刀仪调试

三菱M70/M80对刀仪安装调试一、操作对象基本信息机型:加工中心机对刀仪:近接式三菱M70/M80二、硬件安装及调试过程1.安装电气部分。
三、对刀仪软件安装及调试过程1.设置宏程式对应接口参数a.设置7011=36,7012=1,7013=9936(对落差宏);b.设置7021=66,7022=1,7023=9966(对补偿值宏);c.将参数#1121置1,#1122设置0,开通宏程式编辑使能;然后输入宏程式(O9936;O9966;O91113.设置共变量及对刀参数a. 轴参数#2040:X(**)Y(**)注:对刀仪的位置,跟据对刀仪实际安装位置而定。
b.共变量#520:-***.*** 注:Z轴对刀安全高度,Z轴以G01F2000的速度到达此位置后减速。
c.共变量#521:-***.*** 注:Z轴对刀距离,Z轴从对刀开始到对刀结束的行程,超过此行程对刀还未结束,就判断为刀具已损坏。
4.对刀仪使用及调试注意事项a.如果出现对刀时对刀仪过行程,机床将出警报"紧急停止",手轮移动Z轴向正方向以解除报警,并且重新设置共变量#520和#521的位置,直至对刀的安全开始行程和结束行程正确。
b.出现报警:Probe Fail 原因:A-两次对刀的数据差超过0.500mm;可能由于铁屑进入,应该重新对刀。
B-G31执行结束,但未读取到对刀仪信号,则应该检测共变量#521参数是否设置太小所至,应做适量调整。
5.对刀吹气对刀吹气开始为M48,对刀吹气结束为M49;相应的OUT点是Y3。
现在的宏动作是执行G31指令时开始吹气,G31执行结束后,对刀吹气结束。
四、对刀仪的使用1.落差值测量首先量测出工件与对刀仪之间的落差值。
将刀具碰触工件表面对刀点,将Z轴工件坐标清0,模式切换到MDI输入M36设定完成后按启动,机器会呼叫MACROO9936,并执行自动运行到对刀仪设定的位置点,执行量测动作,测出落差值。
对刀仪使用方法

对刀仪使用方法(总6页) -CAL-FENGHAI.-(YICAI)-Company One1-CAL-本页仅作为文档封面,使用请直接删除对刀仪使用方法随着加工中心的广泛使用,许多用户也开始使用刀具测量装置。
它不仅可以检测刀具的磨损情况,而且可实现自动补偿(通过修改刀补值实现),极大的提高了加工效率和精度。
另外,同时使用其刀具破损检测功能与刀具寿命管理功能,还可以实现自动寻找同组刀具的功能,节约了刀具检查和更换的时间。
但由于用户对测量原理不是很了解,使用时容易产生误区,有时补偿后的精度反而不如补偿前,这就使用户产生了迷惑,限制了测量装置的广泛使用。
本文以英国RENISH AW.html" target="_blank" class="keylink">雷尼绍(RENISHAW)公司TS27 R测头的安装调试为例,就如何更好的使用刀具测量装置做一详细介绍,供读者参考借鉴。
刀具测量的基本原理是利用系统的跳步功能(G31):在程序中指令“G31 Zx x x Fx x x”(与GO1的动作相同)。
但此时如果SKIP信号由“0”变为“1”时,Z轴将停止运动,再用宏程序控制坐标轴后退,然后再次碰触量块,反复测量并运算后得出刀具的实际长度和直径,最后修改系统宏变量从而达到修改刀补值的目的。
刀具测量装置的使用主要包括三个步骤:安装和接线;标定;测量。
1 安装和接线刀具侧量装置通常包括测头和信号转换装置(硬件)及相关的测量程序(软件包)。
测头(TS27R)安装在工作台上,并尽量远离加工区域,外部应加防护装置,使用前先将防护装置打开并将刀具用风吹干净(用M代码控制气动元件可实现自动),确保刀具表面无杂物,测量完成后关闭防护。
测头安装完成后,首先要调整测头接触面的平行度和直线度。
将一只百分表(或千分表DTI)吸在主轴头上,表头打在量块(圆形或方形)的上表面;用手轮控制X轴沿量块表面来回移动,观察表针变化,同时调整测头上的调节螺钉,使X向的直线度保证在0.010mm,调整好后紧固螺钉。
M70绝对位置设置说明
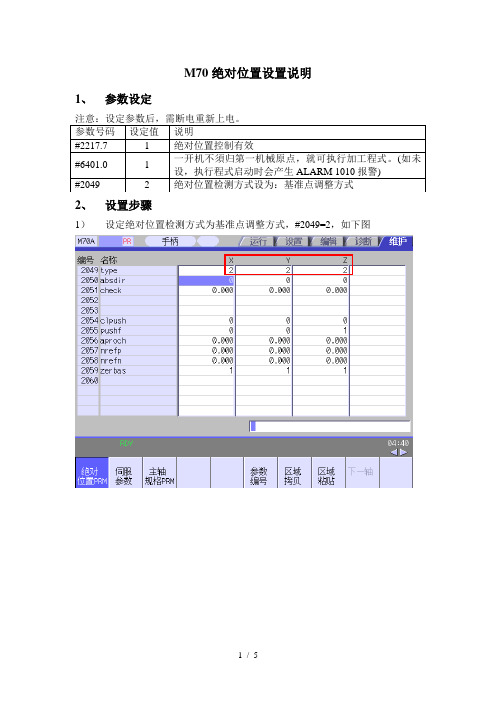
M70绝对位置设置说明
1、 参数设定
2、 设置步骤
1) 设定绝对位置检测方式为基准点调整方式,#2049=2,如下图
参数号码 设定值 说明
#2217.7 1 绝对位置控制有效
#6401.0 1 一开机不須归第一机械原点,就可执行加工程式。
(如未设,执行程式启动时会产生ALARM 1010报警)
#2049 2 绝对位置检测方式设为:基准点调整方式
2)伺服与NC 均断电,重新上电后系统出现Z70报警,如下图
3)按MAINTEN—维护—密码输入—输入密码—绝对位置—进入以下界面
4)将各轴移动到欲设原点位置,然后再进行绝对位置设定,下面是对Z轴绝对位置的设定,下图为设定前的信息
其中:“Z”表示目前是Z轴设定界面,“不正确”表示原点调整尚未完成。
下面为设定步骤:
A、把绝对位置设定设为1(注意在急停状态下不能设置),如下图
B、把基准点设为1,如下图
C、设定原点值(可默认为1)并移动轴,使其机械位置等于机械端的值,如
下图
5)此时Z
6)Z70报警会消失。
7)完成上面步骤后,绝对位置设置即完成,NC再启动即可。
M70绝对位置设置说明
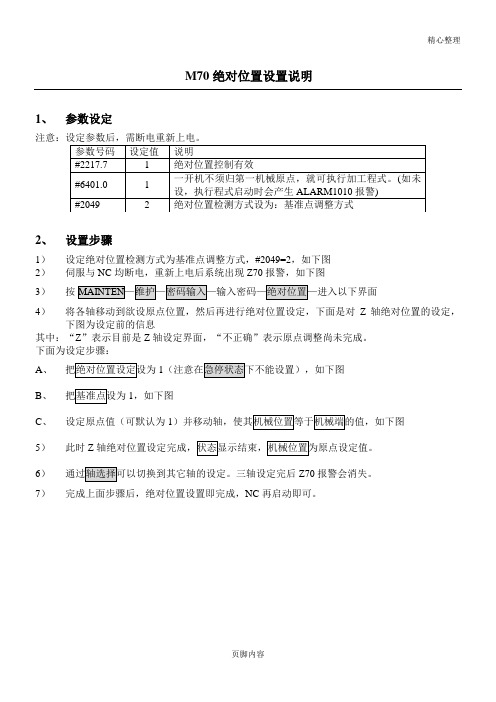
M70 绝对位置设置说明
精心整理
1、 参数设定
注意:设定参数后,需断电重新上电。
6) 通过轴选择可以切换到其它轴的设定。三轴设定完后 Z70 报警会消失。 7) 完成上面步骤后,绝对位置设置即完成,NC 再启动即可。 8)
页脚内容
参数号码 设定值 说明
#2217.7
1 绝对位置控制有效
#6401.0
1
一开机不须归第一机械原点,就可执行加工程式。(如未 设,执行程式启动时会产生 ALARM1010 报警)
#2049
2 绝对位置检测方式设为:基准绝对位置检测方式为基准点调整方式,#2049=2,如下图 2) 伺服与 NC 均断电,重新上电后系统出现 Z70 报警,如下图 3) 按 MAINTEN—维护—密码输入—输入密码—绝对位置—进入以下界面 4) 将各轴移动到欲设原点位置,然后再进行绝对位置设定,下面是对 Z 轴绝对位置的设定,
下图为设定前的信息 其中:“Z”表示目前是 Z 轴设定界面,“不正确”表示原点调整尚未完成。 下面为设定步骤: A、 把绝对位置设定设为 1(注意在急停状态下不能设置),如下图
B、 把基准点设为 1,如下图
C、 设定原点值(可默认为 1)并移动轴,使其机械位置等于机械端的值,如下图
5) 此时 Z 轴绝对位置设定完成,状态显示结束,机械位置为原点设定值。
M70绝对位置设置说明

M70绝对位置设置说明
1、参数设定
参数号码设定值说明
#1绝对位置控制有效
一开机不須归第一机械原点,就可执行加工程式。
(如未#1
设,执行程式启动时会产生ALARM 1010报警)
#20492绝对位置检测方式设为:基准点调整方式
注意:设定参数后,需断电重新上电。
2、设置步骤
1)设定绝对位置检测方式为基准点调整方式,#2049=2,如下图
2)伺服与 NC 均断电,重新上电后系统出现 Z70报警,如下图
3)按MAINTEN—维护—密码输入—输入密码—绝对位置—进入以下界面
4)将各轴移动到欲设原点位置,然后再进行绝对位置设定,下面是对Z轴绝对位置的设定,下图为设定前的信息
其中:“Z”表示目前是Z轴设定界面,“不正确”表示原点调整尚未完成。
下面为设定步骤:
A、把绝对位置设定设为1(注意在急停状态下不能设置),如下图
B、把基准点设为1,如下图
C、设定原点值(可默认为1)并移动轴,使其机械位置等于机械端的值,如
下图
5)此时Z轴绝对位置设定完成,状态显示结束,机械位置为原点设定值。
6)Z70报警会消失。
7)完成上面步骤后,绝对位置设置即完成,NC再启动即可。
对刀仪使用说明M70
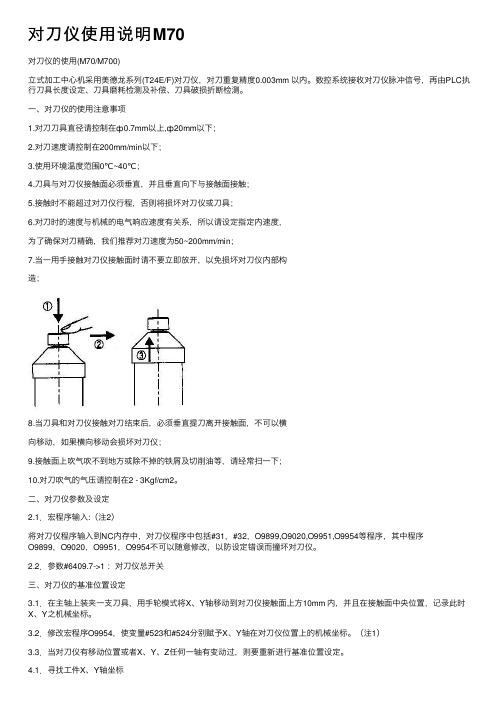
对⼑仪使⽤说明M70对⼑仪的使⽤(M70/M700)⽴式加⼯中⼼机采⽤美德龙系列(T24E/F)对⼑仪,对⼑重复精度0.003mm 以内。
数控系统接收对⼑仪脉冲信号,再由PLC执⾏⼑具长度设定、⼑具磨耗检测及补偿、⼑具破损折断检测。
⼀、对⼑仪的使⽤注意事项1.对⼑⼑具直径请控制在ф0.7mm以上,ф20mm以下;2.对⼑速度请控制在200mm/min以下;3.使⽤环境温度范围0℃~40℃;4.⼑具与对⼑仪接触⾯必须垂直,并且垂直向下与接触⾯接触;5.接触时不能超过对⼑仪⾏程,否则将损坏对⼑仪或⼑具;6.对⼑时的速度与机械的电⽓响应速度有关系,所以请设定指定内速度,为了确保对⼑精确,我们推荐对⼑速度为50~200mm/min;7.当⼀⽤⼿接触对⼑仪接触⾯时请不要⽴即放开,以免损坏对⼑仪内部构造;8.当⼑具和对⼑仪接触对⼑结束后,必须垂直提⼑离开接触⾯,不可以横向移动,如果横向移动会损坏对⼑仪;9.接触⾯上吹⽓吹不到地⽅或除不掉的铁屑及切削油等,请经常扫⼀下;10.对⼑吹⽓的⽓压请控制在2 - 3Kgf/cm2。
⼆、对⼑仪参数及设定2.1.宏程序输⼊:(注2)将对⼑仪程序输⼊到NC内存中,对⼑仪程序中包括#31,#32,O9899,O9020,O9951,O9954等程序,其中程序O9899,O9020,O9951,O9954不可以随意修改,以防设定错误⽽撞坏对⼑仪。
2.2.参数#6409.7->1 :对⼑仪总开关三、对⼑仪的基准位置设定3.1.在主轴上装夹⼀⽀⼑具,⽤⼿轮模式将X、Y轴移动到对⼑仪接触⾯上⽅10mm 内,并且在接触⾯中央位置,记录此时X、Y之机械坐标。
3.2.修改宏程序O9954,使变量#523和#524分别赋予X、Y轴在对⼑仪位置上的机械坐标。
(注1)3.3.当对⼑仪有移动位置或者X、Y、Z任何⼀轴有变动过,则要重新进⾏基准位置设定。
4.1.寻找⼯件X、Y轴坐标⼯件分中,将X、Y轴的相对坐标抄⼊⼯件坐标系统内,Z轴坐标由对⼑程序⾃动测量(通常,初始设0)。
- 1、下载文档前请自行甄别文档内容的完整性,平台不提供额外的编辑、内容补充、找答案等附加服务。
- 2、"仅部分预览"的文档,不可在线预览部分如存在完整性等问题,可反馈申请退款(可完整预览的文档不适用该条件!)。
- 3、如文档侵犯您的权益,请联系客服反馈,我们会尽快为您处理(人工客服工作时间:9:00-18:30)。
对刀仪的使用(M70/M700)
立式加工中心机采用美德龙系列(T24E/F)对刀仪,对刀重复精度0.003mm 以内。
数控系统接收对刀仪脉冲信号,再由PLC执行刀具长度设定、刀具磨耗检测及补偿、刀具破损折断检测。
一、对刀仪的使用注意事项
1.对刀刀具直径请控制在ф0.7mm以上,ф20mm以下;
2.对刀速度请控制在200mm/min以下;
3.使用环境温度范围0℃~40℃;
4.刀具与对刀仪接触面必须垂直,并且垂直向下与接触面接触;
5.接触时不能超过对刀仪行程,否则将损坏对刀仪或刀具;
6.对刀时的速度与机械的电气响应速度有关系,所以请设定指定内速度,
为了确保对刀精确,我们推荐对刀速度为50~200mm/min;
7.当一用手接触对刀仪接触面时请不要立即放开,以免损坏对刀仪内部构
造;
8.当刀具和对刀仪接触对刀结束后,必须垂直提刀离开接触面,不可以横
向移动,如果横向移动会损坏对刀仪;
9.接触面上吹气吹不到地方或除不掉的铁屑及切削油等,请经常扫一下;
10.对刀吹气的气压请控制在2 - 3Kgf/cm2。
二、对刀仪参数及设定
2.1.宏程序输入:(注2)
将对刀仪程序输入到NC内存中,对刀仪程序中包括#31,#32,O9899,O9020,O9951,O9954等程序,其中程序O9899,O9020,O9951,O9954不可以随意修改,以防设定错误而撞坏对刀仪。
2.2.参数#6409.7->1 :对刀仪总开关
三、对刀仪的基准位置设定
3.1.在主轴上装夹一支刀具,用手轮模式将X、Y轴移动到对刀仪接触面上方10mm 内,并且在接触面中央位置,记录此时X、Y之机械坐标。
3.2.修改宏程序O9954,使变量#523和#524分别赋予X、Y轴在对刀仪位置上的机械坐标。
(注1)
3.3.当对刀仪有移动位置或者X、Y、Z任何一轴有变动过,则要重新进行基准位置设定。
4.1.寻找工件X、Y轴坐标
工件分中,将X、Y轴的相对坐标抄入工件坐标系统内,Z轴坐标由对刀程序自动测量(通常,初始设0)。
4.2.量测工件表面与对刀仪基准面之高低差
(1).手动将Z 轴移至工件表面(刀尖碰触)后,执行程序#32,
O 32
G65 P9020 Wxx;
M30;
%
(2).程序中G65 P9020 Wxx (G54~G59,例W55 即G55)预备使用之工件坐标系统,要与X、Y轴抄入的坐标系统一致。
由工件表面位置与当前测量值计算出工件与对刀仪基准的高低差,补正至工件坐标系统。
若使用多个工件坐标系统,则重复执行步骤(1)。
4.3.自动刀长量测,写入到刀具补偿表中。
(1).执行刀长量测程序#31:
O 31
G65 P9954 ;
M30;
%
(2).使用自动刀长量测执行G65 P9954,将刀长量测值写入到刀具补偿表。
注意执行此程序后,测量值将写入与主轴刀号一致的刀补中。
4.4.验证使用量测工件表面零点方式
(1).手轮模式移动Z轴到工件表面位置后,先记录Z轴机械坐标再执行程序#32(G65P9020 Wxx)
(2).再执行下列程序
O0100
G90 Gxx;(与Wxx相同,G54~G59)
G01 G43 H* Z0 F3000;(*:第*号刀;有效范围:1-25)
M30;
%
(3).检视机械坐标应与第1步骤记录之坐标相同(误差约1~2μ)
(4).换另一把刀时,再执行#31程序,刀长测量值可覆盖相应的刀补。
注意所填到的刀补位置由当前所测量的刀,即主轴刀号*来决定补偿到第*号的刀补位置。
4.5 刀具破损警告
执行下列程序
O 31
G65 P9954 H*;(*:此次测量值与上次测量值相差之最大设定,单位mm) M30;
程序执行后,如果检测出此次测量值与上次测量值(刀补中可查)之差超过设定的限度,则程序暂停并报警“ BROKENTOOL”。
5-1.吹气管的交换
吹气连接螺丝材质比其它部位脆一点,是为了防止刀具或大块的铁屑在负载情况下碰到对刀仪先折断连接螺丝,起到保护对刀仪的其它部位。
1.将折断的连接螺丝(TS15)拧出,拧上新的连接螺丝(TS15),短螺纹部分拧到对刀仪气管支架上;
2.气管盖(TS32)和连接螺丝(TS15)连接后由螺母(M5)调节固定;
3.气管盖的顶部接触面约3.5mm,然后将螺母(M5)拧紧定位;
5-2.接触面的再次研磨
接触面的交换或研磨接触面
1.将3个紧定螺丝(M3)松1mm距离后拿出接触头,拿出时请垂直往上拿,不可以旋转拿出;
2.接触头的反面为基准研磨接触面,(以反面为基准研磨可以获得高的平行度);
3.安装接触面头时请顺次平均拧紧3个紧定螺丝(M3)。
注1:
使用对刀仪情况下,T码需放前面,如:T2M6;
修改宏程序须打开编辑锁,具体请参考《对刀仪安装简要说明》
在O9954副程式中设定之变数:
注意这些变量不可由其它程式所使用
#521 对刀仪 Z 测量点最低位置之机械座标,
即主轴加上刀套后能碰触到对刀仪的位
置。
#523 对刀仪 X机械座标
#524 对刀仪 Y 机械座标
O9954中修改的部分:
#523=0.(TOUCH X POS) (说明:X轴机械位置)
#524=0.(TOUCH Y POS) (说明:Y轴机械位置)
#521=0.(Z MIN) (说明:Z轴可到达的最低机械位置)#600=0.(MAX TOOL LENGTH) (说明:最大刀长,默认350.)
#601=0.(MIN TOOL LENGTH) (说明:最小刀长,默认0.)
如:以F6为例,修改后
#523= 12.123
#524= -9.432
#521= -350.
#600= 250.
#601= 0.
注2:刀库及对刀仪程式内部有使用的变量。