压片机粘冲原因及解决办法
片剂产生松片,裂片,粘冲与吊冲,片重差异超限的原因及解决办法
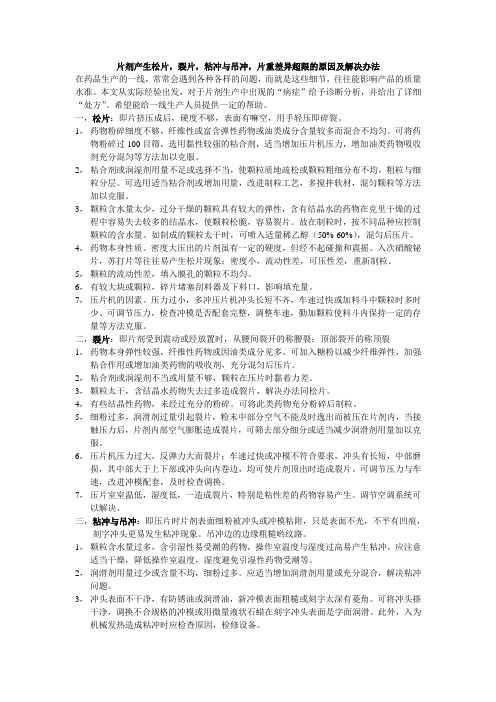
片剂产生松片,裂片,粘冲与吊冲,片重差异超限的原因及解决办法在药品生产的一线,常常会遇到各种各样的问题,而就是这些细节,往往能影响产品的质量水准。
本文从实际经验出发,对于片剂生产中出现的“病症”给予诊断分析,并给出了详细“处方”。
希望能给一线生产人员提供一定的帮助。
一,松片:即片挤压成后,硬度不够,表面有嘛空,用手轻压即碎裂。
1,药物粉碎细度不够,纤维性或富含弹性药物或油类成分含量较多而混合不均匀。
可将药物粉碎过100目筛,选用黏性较强的粘合剂,适当增加压片机压力,增加油类药物吸收剂充分混匀等方法加以克服。
2,粘合剂或润湿剂用量不足或选择不当,使颗粒质地疏松或颗粒粗细分布不均,粗粒与细粒分层。
可选用适当粘合剂或增加用量,改进制粒工艺,多搅拌软材,混匀颗粒等方法加以克服。
3,颗粒含水量太少,过分干燥的颗粒具有较大的弹性,含有结晶水的药物在克里干燥的过程中容易失去较多的结晶水,使颗粒松脆,容易裂片。
故在制粒时,按不同品种应控制颗粒的含水量。
如制成的颗粒太干时,可喷入适量稀乙醇(50%-60%),混匀后压片。
4,药物本身性质。
密度大压出的片剂虽有一定的硬度,但经不起碰撞和震摇。
入次硝酸铋片,苏打片等往往易产生松片现象;密度小,流动性差,可压性差,重新制粒。
5,颗粒的流动性差,填入膜孔的颗粒不均匀。
6,有较大块或颗粒,碎片堵塞刮料器及下料口,影响填充量。
7,压片机的因素。
压力过小,多冲压片机冲头长短不齐,车速过快或加料斗中颗粒时多时少。
可调节压力,检查冲模是否配套完整,调整车速,勤加颗粒使料斗内保持一定的存量等方法克服。
二,裂片:即片剂受到震动或经放置时,从腰间裂开的称腰裂:顶部裂开的称顶裂1,药物本身弹性较强,纤维性药物或因油类成分见多。
可加入糖粉以减少纤维弹性,加强粘合作用或增加油类药物的吸收剂,充分混匀后压片。
2,粘合剂或润湿剂不当或用量不够,颗粒在压片时黏着力差。
3,颗粒太干,含结晶水药物失去过多造成裂片,解决办法同松片。
压片机压片过程可能出现的问题及解决办法
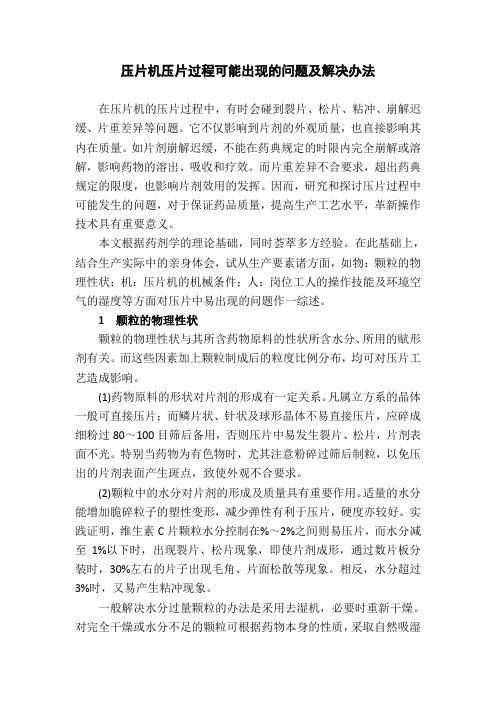
压片机压片过程可能出现的问题及解决办法在压片机的压片过程中,有时会碰到裂片、松片、粘冲、崩解迟缓、片重差异等问题。
它不仅影响到片剂的外观质量,也直接影响其内在质量。
如片剂崩解迟缓,不能在药典规定的时限内完全崩解或溶解,影响药物的溶出、吸收和疗效。
而片重差异不合要求,超出药典规定的限度,也影响片剂效用的发挥。
因而,研究和探讨压片过程中可能发生的问题,对于保证药品质量,提高生产工艺水平,革新操作技术具有重要意义。
本文根据药剂学的理论基础,同时荟萃多方经验。
在此基础上,结合生产实际中的亲身体会,试从生产要素诸方面,如物:颗粒的物理性状;机:压片机的机械条件;人:岗位工人的操作技能及环境空气的湿度等方面对压片中易出现的问题作一综述。
1颗粒的物理性状颗粒的物理性状与其所含药物原料的性状所含水分、所用的赋形剂有关。
而这些因素加上颗粒制成后的粒度比例分布,均可对压片工艺造成影响。
(1)药物原料的形状对片剂的形成有一定关系。
凡属立方系的晶体一般可直接压片;而鳞片状、针状及球形晶体不易直接压片,应碎成细粉过80~100目筛后备用,否则压片中易发生裂片、松片,片剂表面不光。
特别当药物为有色物时,尤其注意粉碎过筛后制粒,以免压出的片剂表面产生斑点,致使外观不合要求。
(2)颗粒中的水分对片剂的形成及质量具有重要作用。
适量的水分能增加脆碎粒子的塑性变形,减少弹性有利于压片,硬度亦较好。
实践证明,维生素C片颗粒水分控制在%~2%之间则易压片,而水分减至1%以下时,出现裂片、松片现象,即使片剂成形,通过数片板分装时,30%左右的片子出现毛角、片面松散等现象。
相反,水分超过3%时,又易产生粘冲现象。
一般解决水分过量颗粒的办法是采用去湿机,必要时重新干燥。
对完全干燥或水分不足的颗粒可根据药物本身的性质,采取自然吸湿或酌喷适宜浓度乙醇,静置或密闭吸湿5小时左右过筛后压片。
如含结晶水的药物颗粒,结晶水失去过多时出现的裂片、松片、崩解迟缓等情况则可采用此法解决。
压片出现粘冲的原因分析及处理方法
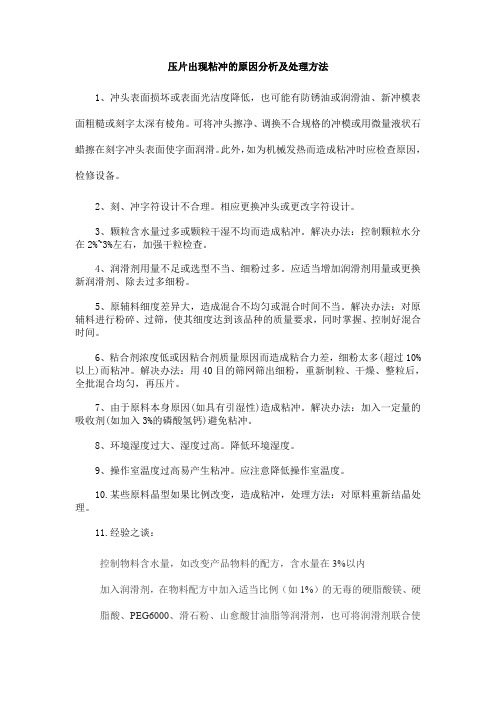
压片出现粘冲的原因分析及处理方法1、冲头表面损坏或表面光洁度降低,也可能有防锈油或润滑油、新冲模表面粗糙或刻字太深有棱角。
可将冲头擦净、调换不合规格的冲模或用微量液状石蜡擦在刻字冲头表面使字面润滑。
此外,如为机械发热而造成粘冲时应检查原因,检修设备。
2、刻、冲字符设计不合理。
相应更换冲头或更改字符设计。
3、颗粒含水量过多或颗粒干湿不均而造成粘冲。
解决办法:控制颗粒水分在2%~3%左右,加强干粒检查。
4、润滑剂用量不足或选型不当、细粉过多。
应适当增加润滑剂用量或更换新润滑剂、除去过多细粉。
5、原辅料细度差异大,造成混合不均匀或混合时间不当。
解决办法:对原辅料进行粉碎、过筛,使其细度达到该品种的质量要求,同时掌握、控制好混合时间。
6、粘合剂浓度低或因粘合剂质量原因而造成粘合力差,细粉太多(超过10%以上)而粘冲。
解决办法:用40目的筛网筛出细粉,重新制粒、干燥、整粒后,全批混合均匀,再压片。
7、由于原料本身原因(如具有引湿性)造成粘冲。
解决办法:加入一定量的吸收剂(如加入3%的磷酸氢钙)避免粘冲。
8、环境湿度过大、湿度过高。
降低环境湿度。
9、操作室温度过高易产生粘冲。
应注意降低操作室温度。
10.某些原料晶型如果比例改变,造成粘冲,处理方法:对原料重新结晶处理。
11.经验之谈:控制物料含水量,如改变产品物料的配方,含水量在3%以内加入润滑剂,在物料配方中加入适当比例(如1%)的无毒的硬脂酸镁、硬脂酸、PEG6000、滑石粉、山愈酸甘油脂等润滑剂,也可将润滑剂联合使用控制工作场所或车间的湿度,安装除温空调控制空气湿度调整压片机转速,速度越慢压片效果会越好也可在粉末成型设备上配置喷洒头,在压制过程中对压片机冲模表面喷洒硬脂酸镁辅助液冲头表面粗糙也会引起粘模粘冲问题,可更改冲模,或以抛光处理增加物料的颗粒密度,加入干法制粒、湿法制粒等工艺流程。
压片异常问题汇总
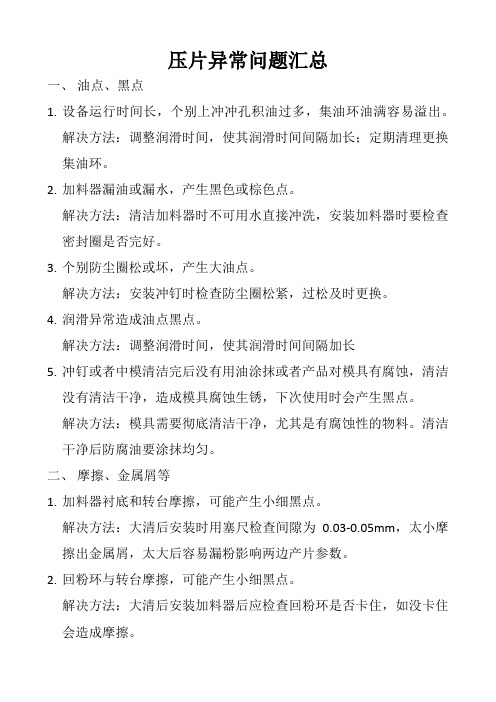
压片异常问题汇总一、油点、黑点1.设备运行时间长,个别上冲冲孔积油过多,集油环油满容易溢出。
解决方法:调整润滑时间,使其润滑时间间隔加长;定期清理更换集油环。
2.加料器漏油或漏水,产生黑色或棕色点。
解决方法:清洁加料器时不可用水直接冲洗,安装加料器时要检查密封圈是否完好。
3.个别防尘圈松或坏,产生大油点。
解决方法:安装冲钉时检查防尘圈松紧,过松及时更换。
4.润滑异常造成油点黑点。
解决方法:调整润滑时间,使其润滑时间间隔加长5.冲钉或者中模清洁完后没有用油涂抹或者产品对模具有腐蚀,清洁没有清洁干净,造成模具腐蚀生锈,下次使用时会产生黑点。
解决方法:模具需要彻底清洁干净,尤其是有腐蚀性的物料。
清洁干净后防腐油要涂抹均匀。
二、摩擦、金属屑等1.加料器衬底和转台摩擦,可能产生小细黑点。
解决方法:大清后安装时用塞尺检查间隙为0.03-0.05mm,太小摩擦出金属屑,太大后容易漏粉影响两边产片参数。
2.回粉环与转台摩擦,可能产生小细黑点。
解决方法:大清后安装加料器后应检查回粉环是否卡住,如没卡住会造成摩擦。
3.出料器与转台摩擦,产生小细金属黑点。
解决方法:安装完出料器后检查是否与转台摩擦。
4.筛片机进出口摩擦,产生小黑点但可以擦掉。
解决方法:安装完成后空机运行听是否有异响。
5.金检机灵敏度不合适,剔废异常。
解决方法:标注每台金检机宽度设置,每次生产前检查金检机灵敏度。
三、间隙调节1.出料器剔废挡板间隙太大,剔废时漏片,不合格片子流出;间隙太小摩擦出料口,剔废不灵敏,剔废不及时,造成不合格产品流出。
解决方法:调整合适的间隙,生产之前手动剔废调试查看间隙。
2.出片挡板间隙太大,出片时造成片子磕边;间隙太小,与转台摩擦,产生金属屑。
解决方法:生产前空机运行,检查间隙,进行调整。
3.压片过程中,上料时,提升机蝶阀开度较小,可能会造成颗粒筛分,导致两边加料器颗粒不均匀,两边产品硬度、厚度、崩解、含量有差异。
解决方法:开始加料时缓慢开启,料斗中物料满了之后,将蝶阀全部打开。
压片工艺粘冲产生的原因及解决方案

压片工艺粘冲产生的原因及解决方案在压片过程中粘冲分为粘冲和粘连两种方式,粘冲是指粉末颗粒粘附于冲头表面,粘连是指产品粘于冲头表面设计的字母、logo或图案的内部。
该文着重于表述粘冲的原因及解决办法。
当粘冲问题出现的时候,你会听到研发的同事说,我们在实验室阶段采用单冲压片机不粘冲,肯定是压片操作人员操作问题。
当问到压片机操作人员的时候,压片机操作人员会说如果颗粒做的好,我们压片过程中肯定不会出现粘冲问题。
而QA人员会建议检测压片设备是否存在冲模损坏或者冲模是否需要抛光,或者和设备供应商沟通。
但是具体粘冲是来源于压片机还是处方,冲头还是制粒或干燥,或者是操作人员问题,没有一个人可以确定。
一、粘冲的定义粘冲是压片过程中常见问题之一。
当粉末颗粒粘于冲头表面不能形成表面光滑的片时就是出现了粘冲。
下图就是由于粘冲引起的片不合格。
图一是产品粘于上冲表面。
粘连是粘冲的一种,是指颗粒粘于凸出或凹陷的字母和LOGO内部无论是粘冲还是粘连均会导致片不合格。
压片时处方已经配制完成,不能退库,也不能进行重加工,为了保证产品不浪费,压片过程中不得不进行目视监控并手动挑片,这样就会降低生产效率和产品收率。
粘冲可能会出现于压片过程中任何时间段。
经常会在设定压力的时候出现,可能会在压片过程中随机出现,也可能会有规律地出现。
对于一些产品,粘冲具有可预见性,压片机操作人员认为连续压片2个小时不出现粘冲的话就不会出现粘冲。
测定颗粒的水分或者产品的其他性质可以帮助我们预测产品是否粘冲。
尽管有时候混粉性质都符合标准仍然有可能出现粘冲的情况。
事实是,可能在粘冲之前你不知道你的产品到底怎样。
本文提供了一些粘冲的原因及解决方案。
粘冲原因可能和产品、设备、上游工艺或压片机操作有关,也可能是几个因素的综合。
二、粘冲的颗粒可以生产出合格的片当产品第一次压片时,操作人员首先调整片重(通常是通过调节下冲位置,从而改变填充体积,由于松密度不变,片重就得到调节)。
3-片重超差、粘冲和松片原因及解决方法

片重超差、粘冲和松片原因及解决方法一:片重超差的原因及处理如下:片重超差是指片重差异超过药典规定的限度。
1.颗粒粗细分布不匀,压片时颗粒流速不同,导致填充到中模孔内的颗粒粗细不均匀,如粗颗粒量多则片轻,细颗粒多则片重。
解决方法:应将颗粒混匀或筛去过多细粉,控制粒径分布范围。
2.如有细粉粘附冲头而造成吊冲时可使片重差异幅度较大。
此时下冲转动不灵活,应及时检查,拆下冲模,清理干净下冲与中模孔。
3.颗粒流动性不好,流入中模孔的颗粒量时多时少,引起片重差异过大而超限。
解决方法:应重新制粒或加入适宜的助流剂如微粉硅胶等,改善颗粒流动性。
4.颗粒分层。
解决颗粒分层,减小粒度差。
5.较小的药片选用较大颗粒的物料。
解决方法:选择适当大小的颗粒。
6.加料斗被堵塞,此种现象常发生于粘性或引湿性较强的药物。
应疏通加料斗、保持压片环境干燥,并适当加入助流剂解决。
7.物料内物料存储量差异大,控制在50%以内。
8.加料器不平衡或未安装到位,造成填料不均。
9.刮粉板不平或安装不良。
解决方法:调平。
10.带强迫加料器的,强迫加料器拨轮转速与转台转速不匹配。
解决方法:调一致。
11.冲头与中模孔吻合性不好,例如下冲外周与模孔壁之间漏下较多药粉,致使下冲发生“涩冲”现象,造成物料填充不足,对此应更换冲头、中模。
12.下冲长短不一,超差,造成充填量不均。
解决办法:修差,差±5μm以内。
13.下冲带阻尼的,阻尼螺钉调整的阻尼力不佳。
重新调整。
14.充填轨道磨损或充填机构不稳定。
解决方法:更换或稳固。
15.追求产量,转台转速过快,填充量不足。
特别是压大片时,要适当降低转速,以保证充填充足。
16.压片机震动过大,结构松动,装配不合理或重新装配;压片机设置压力过大,减小压力。
二:粘冲的原因及处理如下:粘冲是指压片时片剂表面细粉被冲头和冲模黏附,致使片面不光、不平有凹痕,刻字冲头更容易发生粘冲现象。
1.冲头表面损坏或表面光洁度降低,也可能有防锈油或润滑油、新冲模表面粗糙或刻字太深有棱角。
压片机的常见问题及解决方法
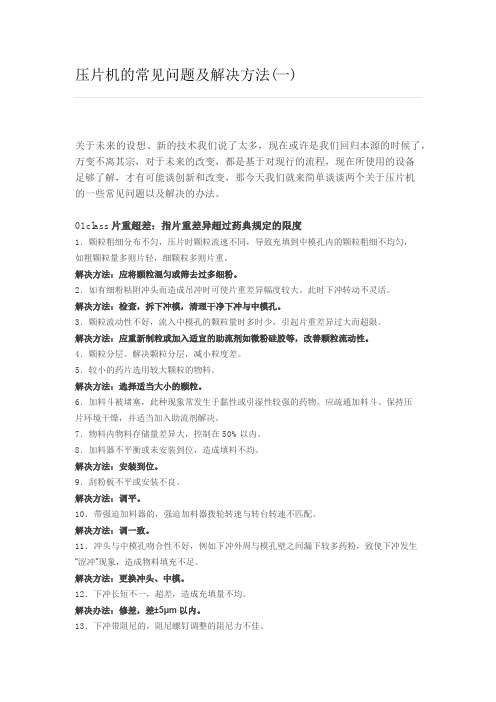
压片机的常见问题及解决方法(一)关于未来的设想、新的技术我们说了太多,现在或许是我们回归本源的时候了,万变不离其宗,对于未来的改变,都是基于对现行的流程,现在所使用的设备足够了解,才有可能谈创新和改变,那今天我们就来简单谈谈两个关于压片机的一些常见问题以及解决的办法。
01class片重超差:指片重差异超过药典规定的限度1.颗粒粗细分布不匀,压片时颗粒流速不同,导致充填到中模孔内的颗粒粗细不均匀,如粗颗粒量多则片轻,细颗粒多则片重。
解决方法:应将颗粒混匀或筛去过多细粉。
2.如有细粉粘附冲头而造成吊冲时可使片重差异幅度较大。
此时下冲转动不灵活。
解决方法:检查,拆下冲模,清理干净下冲与中模孔。
3.颗粒流动性不好,流入中模孔的颗粒量时多时少,引起片重差异过大而超限。
解决方法:应重新制粒或加入适宜的助流剂如微粉硅胶等,改善颗粒流动性。
4.颗粒分层。
解决颗粒分层,减小粒度差。
5.较小的药片选用较大颗粒的物料。
解决方法:选择适当大小的颗粒。
6.加料斗被堵塞,此种现象常发生于黏性或引湿性较强的药物。
应疏通加料斗、保持压片环境干燥,并适当加入助流剂解决。
7.物料内物料存储量差异大,控制在50%以内。
8.加料器不平衡或未安装到位,造成填料不均。
解决方法:安装到位。
9.刮粉板不平或安装不良。
解决方法:调平。
10.带强迫加料器的,强迫加料器拨轮转速与转台转速不匹配。
解决方法:调一致。
11.冲头与中模孔吻合性不好,例如下冲外周与模孔壁之间漏下较多药粉,致使下冲发生“涩冲”现象,造成物料填充不足。
解决方法:更换冲头、中模。
12.下冲长短不一,超差,造成充填量不均。
解决办法:修差,差±5μm以内。
13.下冲带阻尼的,阻尼螺钉调整的阻尼力不佳。
解决方法:重新调整。
14.充填轨道磨损或充填机构不稳定。
解决方法:更换或稳固。
15.追求产量,转台转速过快,填充量不足。
特别是压大片时,要适当降低转速,以保证充填充足。
16.压片机震动过大,结构松动,装配不合理或重新装配;压片机设置压力过大,减小压力。
压片黏冲的原因

压片黏冲的原因压片黏冲啊,这可真是个让人头疼的事儿呢!就像你满心欢喜地想要做一顿精致的饺子,结果面皮老是黏在案板上,那叫一个糟心。
咱得好好琢磨琢磨这压片黏冲的原因。
有时候啊,这冲模的表面就像那没擦干净的镜子,要是有一点点的油污或者是上次残留的物料没清理干净,那压片的时候可不就容易黏冲嘛。
这就好比你穿衣服,要是衣服上有胶水没擦干净,再穿新衣服的时候,新衣服就容易黏在上面。
冲模不干净,物料就像调皮的小娃娃,总爱黏在上面不下来,那压出的片子质量肯定好不了。
还有啊,这物料本身的性质也很关键。
有些物料就像那黏人的小猫咪,本身就比较黏糊。
比如说那些含有糖分或者是黏性成分比较多的物料,就容易在压片的时候黏在冲模上。
这就跟你手上沾了蜂蜜一样,走到哪儿都可能会黏住东西。
如果在制备物料的时候没有处理好,没有把它的黏性控制好,那压片的时候就等着和黏冲作斗争吧。
湿度这个因素也不能小瞧。
环境的湿度要是太大了,就像把物料放在了一个湿漉漉的澡堂子里。
物料吸了太多的水分,就会变得软塌塌的,然后就容易黏在冲模上。
这就好比你在潮湿的天气里晾衣服,衣服老是干不透,还黏糊糊的。
要是生产车间的湿度控制不好,那压片的时候就像走进了一个充满陷阱的迷宫,一不小心就被黏冲这个小怪兽给抓住了。
压力也和黏冲有关系呢。
压力不合适就像你走路的步伐不对一样。
如果压力太大,物料可能就会被挤得溢出冲模的边缘,然后就黏在冲模上了。
这就好像你往一个小盒子里塞太多东西,东西就会从盒子缝里挤出来,还会把盒子周围弄得脏兮兮的。
相反,要是压力太小,物料就不能很好地成型,也可能会造成黏冲,就像盖房子的时候,砖块没压实,摇摇欲坠的,也容易出问题。
再有啊,这润滑剂的使用也是个大学问。
润滑剂就像是冲模和物料之间的小滑滑梯。
要是润滑剂的量不够,就像滑滑梯没有润滑油了,物料在冲模里就不能顺利地滑动,那就容易黏住了。
要是润滑剂的种类选错了呢,就像你给汽车加错了油,发动机肯定运转不好,物料和冲模之间的配合也会出问题,黏冲就可能找上门来。
- 1、下载文档前请自行甄别文档内容的完整性,平台不提供额外的编辑、内容补充、找答案等附加服务。
- 2、"仅部分预览"的文档,不可在线预览部分如存在完整性等问题,可反馈申请退款(可完整预览的文档不适用该条件!)。
- 3、如文档侵犯您的权益,请联系客服反馈,我们会尽快为您处理(人工客服工作时间:9:00-18:30)。
浅谈压片机压片时造成粘冲的原因及解决办法压片是将颗粒状原料在压片机汇总加压成片剂的过程。
压出的片,一般要求含量准确,重量差异小;崩解时限或溶出度符合规定;硬度适当,色泽均匀,完整光洁;在规定的储藏期内不得变质,符合卫生学校检查要求等。
但在压片过程中,由于受到配料、制料、烘干等因素的影响,往往会出现粘冲等问题,从而影响产品质量,给生产厂家带来或多或少的经济损失,片剂表面不光、不平或有凹痕,检查冲头常有细粉粘着,这个现象叫粘冲。
关于粘冲问题的产生原因及解决办法,在一些相关的书籍中均有介是很好的经验总结,对各生产厂家提高片剂的产品质量起着积极的指导作用,作者通过多年来的实践经验,结合理论知识,对如何分析、解决粘冲问题作一探讨,以期达到相互学习的目的,从而确保生产过程中产品的质量。
1、颗粒机干燥不够,水分过多或颗粒干湿不均而造成粘冲。
解决办法:控制颗粒机水份在2%-3%左右,加强干粒检查。
未烘干,则不能从烘房中取出颗粒,因误判烘干而已取出的颗粒,应返工重烘,烘药时,药盘内盛装的颗粒机不易过多,而且升温不易太快,否则颗粒机内湿外干,如果有条件,可以烘一定时间后转盘,再烘。
2、原辅料细度差异大,造成混合不均匀或混合时间不当,解决办法:对原辅料进行粉碎、过筛、使其细度达到该品种的质量要求,同事掌握、控制好混合时间。
3、润滑剂选择不当或用量过少或混合不均,细粉过多。
解决办法:变换润滑剂,适当增加润滑剂用量或混合时间。
4、压片机冲头表面不干净,有防锈油或润滑油;新冲模表面粗糙或刻字冲头刻字太深有棱角。
解决办法:将冲头用溶媒擦净;调整不和规格的冲模或用微量液状石蜡搅在刻字冲头表面使字面润滑。
5、压片机压力不足或调压器未锁紧或换批后未调整压力而造成粘冲。
解决办法:适当增加压力,将调压器锁紧,换批后调整压力即可。
6、颗粒粗细悬殊,造成压片时颗粒流速不均,进粉不匀,使刮粉器受卡而粘冲。
解决办法:将干燥后的颗粒用14目的不锈钢筛网整粒即可。
7、粘合剂浓度低或因粘合剂质量原因而造成粘合力差,细粉太多(超过10%以上)而粘冲。
解决办法:用40目的筛网筛出细粉,重新制粒、干燥、整理后,全批混合均匀,再压片。
8、天气潮湿,冲头表面有微量水份附着或室内相对湿度太高,容易造成粘冲。
解决办法:前一班下半时,应关闭好门窗;擦去附着在冲头表面的水份;用除湿机除湿,使室内相对湿度低于60%。
9、冷机器刚开机时或压片机车速过快容易造成粘冲。
解决办法:先开一段时间(15min)空车或先用热颗粒上机压片,并调节好车速。
10、颗粒放置时间太久,未经密闭而受潮,使水份超标,造成压片时粘冲。
解决办法:及时压片或采取相应的防潮措施(如用胶带密闭颗粒)。
11、压片机冲头有卷边或破裂或凹度太深,容易造成粘冲。
解决办法:修正或换掉冲头。
12、由于原料本身的原因(如具有引潮性)造成粘冲。
解决办法:加入一定量的吸收剂(如加入3%的磷酸氢钙)避免粘冲。
综上所述,在压片过程中,影响产品质量的因素是很多方面的,除本文阐述的粘冲之外,还有裂片、松片、花斑、毛边、崩解度不合格、重量差异不合格等。
因此,在生产时,不论是生产管理还是质量监控都必须落到实处。
尤其是生产操作人员,必须持证上岗,严格按照产品的工艺鬼城岗位技术安全操作规则进行生产,做到及时发现问题,分析问题和解决问题,只有这样,产品的质量才能得到巩固和提高。