FMEA评分准则
FMEA几个参数值的评价准则

FMEA几个参数值的评价准则FMEA(Failure Mode and Effects Analysis)是一种用于系统性地识别和评估潜在故障模式及其潜在影响的方法。
它通过分析产品、过程或系统中的故障模式,确定其潜在影响,并制定相应的纠正措施,以防止这些故障发生或减轻其可能的影响。
在FMEA中,参数值的评价准则是评估故障模式和其潜在影响的重要依据。
下面是FMEA中常用的几个参数值的评价准则:1. 严重性(Severity):严重性评价准则用于评估故障模式的潜在影响有多严重,即故障对产品、过程或系统的功能和性能的影响程度。
严重性评价一般采用1到10的量表进行,其中1表示无影响,10表示严重影响。
评估时需要综合考虑故障对人员安全、环境保护、产品质量、顾客满意度等方面的影响。
2. 频率(Frequency):频率评价准则用于评估故障模式发生的可能性有多大,即故障的发生频率。
频率评价一般采用1到10的量表进行,其中1表示异常低的发生频率,10表示异常高的发生频率。
评估时需要综合考虑过去的经验数据、历史故障记录、设计可靠性分析等信息。
3. 检测性(Detectability):检测性评价准则用于评估故障模式是否容易被发现和检测到。
检测性评价一般也采用1到10的量表进行,其中1表示容易被发现,10表示很难被发现。
评估时需要综合考虑检测手段的可靠性、故障的可见性、测试方法的有效性等因素。
4. 优先度(Priority):优先度评价准则是根据严重性、频率和检测性综合评估故障模式影响的重要程度,以确定优先处理的顺序。
优先度评估通常通过将严重性、频率和检测性的数值相乘得到。
优先度越高的故障模式需要优先处理。
除了以上几个评价准则外,有些情况下还可以考虑其他参数,如影响程度、修复难度、预防性评估等。
选择哪些参数值作为评价准则应根据具体的情况而定。
在实施FMEA过程中,通过对故障模式进行评价,可以帮助团队识别潜在的高风险故障,并制定相应的改进措施。
FMEA评分标准

.推荐的PFMEA探测度评价准则 推荐的PFMEA探测度评价准则 PFMEA
准则 探测方法的推荐范围 不能探测或没有检查 只能通过间接或随机检查来实现控制 只通过目测检查来实现控制 只通过双重目测检查来实现控制 用制图的方法,如SPC(统计过程控 制)来实现控制。 控制基于零件离开工位后的计量测 量,或者零件离开工位后100%的止/通 测量 在后续工位上的误差探测,或在作业 准备时进行测量和首件检查(仅适用 X 于作业准备的原因) 在工位上的误差探测,或利用多层验 收在后续工序上进行误差探测:供应 X 、选择、安装、确认。不能接受有差 异的零件。 在工位上的误差探测(自动测量并自 X 动停机)。不能通过有差异的零件。 由于有关项目已通过过程/产品设计采 用了防错措施,有差异的零件不可能 X 产出。 A
9 有警告的危害
8 很高
7 高
6 中等
5 低
4 很低
3 轻微
2 很轻微 1 无
评定准则:后果的严重度 严重度 后果 (顾客的后果) (制造/装配后果) 这是一种非常严重的失效形式,它是在没有任 当潜在的失效模式在无警告的情况下影响 无警告的 或可能在无警告的情况下对(机 何失效预兆的情况下影响到行车安全或不符合 10 车辆安全运行和/或涉及不符合政府法规的 危害 器或总成)操作者造成危害 政府的法规,失效发生时无预警 情形时,严重度定级非常高 这是一种非常严重的失效形式,是在具有失效 当潜在的失效模式在有警告的情况下影响 有警告的 或可能在有警告的情况下对(机 预兆的前提下所发生的,影响到行车安全和/ 9 车辆安全运行和/或涉及不符合政府法规的 危害 器或总成)操作者造成危害 或不符合政府的法规。失效发生时有预警 情形时,严重度定级非常高 或100%的产品可能需要报废,或 车辆/系统不能运行(丧失基本功能) 8 很高 车辆/项目不能工作(丧失基本功能) 者车辆/项目需在返修部门返修1 个小时以上 或 产 品 需 要 进 行 分检 、一 部分 车辆/系统可运行,但性能下降,顾客非常不 车辆/项目可运行但性能水平下降。 (小于100%)需报废,或车辆/ 7 高 满意 顾客非常不满意。 项目在返修部门进行返修的时间 在0.5-1小时之间。 或一部分(小于100%)产品可能 车辆/项目可运行但舒适性/便利性项目不 车辆/系统可运行,但舒适性/方便性项目不 需要报废,不需分检或者车辆/ 6 中等 能运行。顾客不满意 能运行,顾客不满意。 项目需在返修部门返修少于0.5 小时 或100%的产品可能需要返工或者 车辆/系统可运行,但舒适性/方便性项目的 车辆/项目可运行但舒适性/便利性项目性 5 低 车辆/项目在线下返修,不需送 性能下降,顾客有些不满意。 能水平有所下降。 往返修部门处理 配合和外观/尖响和卡嗒响等到项目不符合要 或 产 品 可 能 需 要 分检 ,无 需报 配合和外观/尖响和卡嗒项目不舒服。多数 求。大多数顾客(75%以上)能感觉到有缺陷 4 很低 废,但部分产品(小不100%)需 (75%以上)顾客能发觉缺陷 返工。 。 或部分(小于100%)产品可能需 配合和外观/尖响和卡嗒响等项目不不符合要求 配合和外观/尖响和卡嗒项目不舒服。50% 3 轻微 要返工,无需报废,在生产线上 。50%的顾客能感觉到有缺陷。 的顾客能发觉缺陷。 其它工位返工。 配合和外观/尖响和卡嗒响等项目不符合要求。 或部分(小于100%)产品可能需 配合和外观/尖响和卡嗒项目不舒服。有辨 2 有辨识能力的顾客(25%以下)能感觉到有缺 很轻微 要返工,无报废,在生产线上其 识力顾客(25%以下)能发觉缺陷。 它工位返工。 陷。 无可辨别的后果。 1 无 无可辨别的影响 或对操作或操作者而言有轻微的 不方便或无影响。
FMEA问题等级评分标准
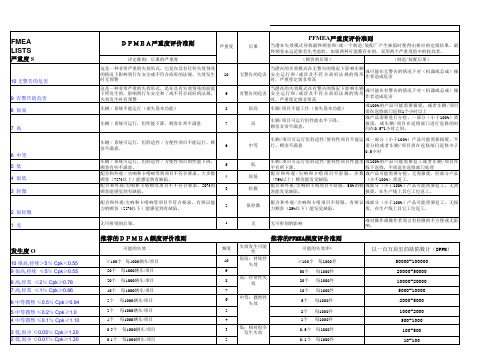
探测性
准则
探测方法的推荐范围
ABC
设计控制将不能和/或不可能找出潜在的起因/机理及后 续的失效模式,或根本没有设计控制
10
几乎不可能 绝对肯定不可能探测
不能探测或没有检查
X
设计控制只有很极少的机会能找出潜在的起因/机理及后 续的失效模式
9
很微小 控制方法可能探测不出来
只能通过间接或随机检查来实现控制
高
车辆/项目可运行但性能水平下降。 顾客非常不满意。
或产品需要进行分检、一部分(小于100%)需 报废,或车辆/项目在返修部门进行返修的时 间在0.5-1小时之间。
车辆/系统可运行,但舒适性/方便性项目不能运行,顾 客不满意。
6
中等
车辆/项目可运行但舒适性/便利性项目不能运 或一部分(小于100%)产品可能需要报废,不
车辆/项目可运行但舒适性/便利性项目性能水 或100%的产品可能需要返工或者车辆/项目在
平有所下降。
线下返修,不需送往返修部门处理
配合和外观/尖响和卡嗒项目不舒服。多数 或产品可能需要分检,无需报废,但部分产品
(75%以上)顾客能发觉缺陷
(小不100%)需返工。
配合和外观/尖响和卡嗒项目不舒服。50%的顾 或部分(小于100%)产品可能需要返工,无需
级低:失效不 太可能发生
≤0.01个 每1000件
1-10
可探测度 D
10 几乎不可能 9 很微小 8 微小 7 很小 6小 5 中等 4 中上 3高 2 很高 1 很高,肯定能检出
.推荐的DFMEA探测度评价准则
.推荐的PFMEA探测度评价准则
检查类别
准则:设计控制可能探测出来的可能性
探测度定 级
fmea打分规则
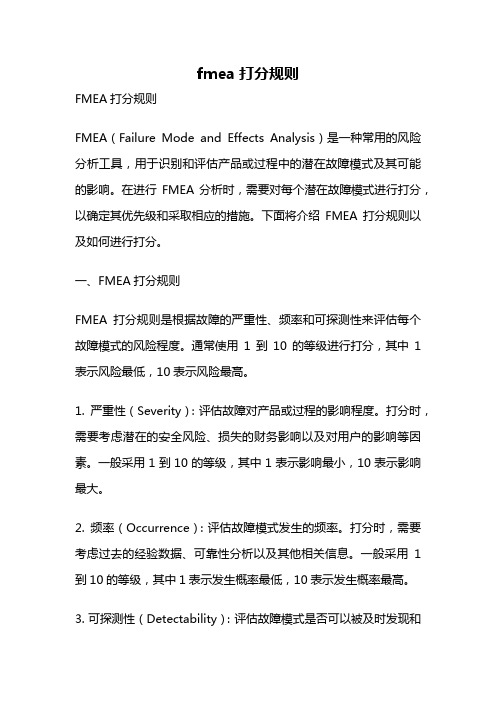
fmea打分规则FMEA打分规则FMEA(Failure Mode and Effects Analysis)是一种常用的风险分析工具,用于识别和评估产品或过程中的潜在故障模式及其可能的影响。
在进行FMEA分析时,需要对每个潜在故障模式进行打分,以确定其优先级和采取相应的措施。
下面将介绍FMEA打分规则以及如何进行打分。
一、FMEA打分规则FMEA打分规则是根据故障的严重性、频率和可探测性来评估每个故障模式的风险程度。
通常使用1到10的等级进行打分,其中1表示风险最低,10表示风险最高。
1. 严重性(Severity):评估故障对产品或过程的影响程度。
打分时,需要考虑潜在的安全风险、损失的财务影响以及对用户的影响等因素。
一般采用1到10的等级,其中1表示影响最小,10表示影响最大。
2. 频率(Occurrence):评估故障模式发生的频率。
打分时,需要考虑过去的经验数据、可靠性分析以及其他相关信息。
一般采用1到10的等级,其中1表示发生概率最低,10表示发生概率最高。
3. 可探测性(Detectability):评估故障模式是否可以被及时发现和探测。
打分时,需要考虑现有的检测手段、监测系统以及人工检查等因素。
一般采用1到10的等级,其中1表示可以容易地被探测到,10表示很难被探测到。
二、FMEA打分方法1. 计算风险优先数(Risk Priority Number,RPN):RPN是FMEA中用于确定优先级的指标,是通过将严重性、频率和可探测性的打分相乘得到的。
RPN=Severity × Occurrence × Detectability。
根据RPN的大小,可以确定优先处理的故障模式。
2. 制定打分规则:根据实际情况和需求,制定FMEA打分规则。
例如,可以定义RPN大于100的故障模式为高风险,需要立即采取措施;RPN在50到100之间的故障模式为中风险,需要进行改进;RPN小于50的故障模式为低风险,可以接受。
FMEA评价准则

探测度 10 9 8 7 6 5 4 3 2 1
用制图的方法,如SPC(统计过程控制)来实现控制 控制基于零件离开工位后的计量测量,或者零件离开工位后 100%的止/通测量 在后续工位上的误差探测,或在作业准备时进行测量和首件 检查(仅适用于作业准备的原因) 在工位上的误差探测பைடு நூலகம்或利用多层验收在后续工序上进行误 差探测:供应,选择,安装,确认.不能接受有差异的零件. 后继的误差探测(仪器测量),不能通过有差异的零件 由于有关项目已通过过程/产品设计采用了防错措施,有差异 的零件不可能产出.
控制有较多机会可探测 X 出 控制有较多机会可探测 X 出 控制几乎肯定能探测出 X 肯定能探测出
X
检验类别:A.防错B.量具C.人工检验 风险顺序数(RPN)是严重度(S)频度(O)和探测度(D)的乘积. 风险顺序数 (S)X(O)X(D)=RPN
探测性 几乎不可能 很微小 微小 很小 小 中等 中上 高 很高 很高
准则
不可能探测 控制方法可能探测不出 来 控制有很小的机会能探 测出来 控制有很小的机会能探 测出来 控制可能能探测出 控制可能能探测出
A
附表三:FMEA探测度评价准则 检查类别 B C X X X X X X X X X X
探测方法的推荐范围 不能探测或没有检查
附表一:FMEA严重度的评价准则 后果 无警告的严重危害 有警告的严重危害 很高 高 中等 低 很低 轻微 很轻微 无 评宣判准则:后果的严重度 这是一种非常严重的失效形式,它是在没有任何失效预兆的情况下影响到使用安全或不符合政府的法规 这是一种非常严重的失效形式,它是在具有失效预兆的情况下影响到使用安全或不符合政府的法规 项目不能运行(丧失基本功能) 项目可运行,但性能下降,顾客非常不满意 项目可运行,但性能下降,顾客不满意 项目可运行,但外观项目的性能下降,顾客有些不满意 配合项目不舒服,大多数顾客(75%)能感觉到有缺陷 配合项目不舒服,大多数顾客(50%)能感觉到有缺陷 配合项目不舒服,有辨识能力的顾客(25%以下)能感觉到有缺陷 无可辨别的后果 严重度 10 9 8 7 6 5 4 3 2 1
FMEA评价准则(CRI)

FMEA评价准则(CRI)
FMEA评价准则(CRI)
1. 简介
FMEA是一种风险评估工具,用于识别和评估潜在的系统故障和危险。
FMEA评价准则(CRI)是基于国际标准和最佳实践的指导,可用于指导FMEA的实施和评估过程。
2. FMEA评价准则的目的
FMEA评价准则的目的是提供一套规范和一致的方法来执行FMEA,并确保结果的可靠性和可比性。
它旨在确保FMEA评估的全面性、一致性和准确性,以帮助识别并减少系统故障和危险。
3. FMEA评价准则的关键要素
FMEA评价准则(CRI)包括以下关键要素:
3.1 范围定义
FMEA应准确定义评估的系统或过程的范围,以确保评估的全面性和可比性。
3.2 风险识别
在FMEA过程中,应识别可能的故障模式、原因、影响和控制措施,以帮助确定潜在的风险。
3.3 风险分析和评估
基于发现的风险,进行风险分析和评估,以确定风险等级和优先级。
这有助于确定哪些风险需要优先处理和控制。
3.4 控制措施和风险缓解
制定和实施适当的控制措施,以减轻和缓解风险,并监控其有效性。
3.5 FMEA报告和跟踪
撰写FMEA报告,包括评估结果、风险控制措施和风险缓解计划。
跟踪和监控这些计划的执行情况,并及时采取纠正措施。
4. 结论
FMEA评价准则(CRI)为实施和评估FMEA提供了一套指导,以确保评估结果的可靠性和可比性。
通过正确应用这些准则,组织
和团队可以更好地识别和控制潜在的系统故障和危险。
FMEA评定准则

FMEA评定准则FMEA(Failure Mode and Effects Analysis)是一种系统性的方法,用于评估和预防潜在问题或故障,并确定相应的改进措施。
FMEA评定准则是指在执行FMEA过程中应遵循的一系列原则和标准。
以下是一些常见的FMEA评定准则。
1.明确目标和范围:在进行FMEA评定之前,明确评定的目标和范围是非常重要的。
明确目标可以帮助确定关注的重点和特定的评估要素,范围则决定了所需的资源和时间。
2.组建适当的团队:成功的FMEA评定需要一个有效的团队来进行合作和协调。
团队成员应具备丰富的知识和经验,涵盖评定对象的各个方面,包括设计、生产、质量控制等。
3.确定评估对象:对于要进行评估的对象,需要明确其关键特征和性能指标,以及与其相关的人、设备、材料等因素。
4.识别可能的故障模式:通过分析历史数据、专家知识和类似产品的故障模式,识别与评估对象相关的可能故障模式。
这包括机械故障、人为错误、设计缺陷等。
5.评估潜在的效应和后果:对于每个故障模式,评估其潜在的效应和后果。
这包括安全问题、生产能力下降、产品质量问题等。
6.评估故障的严重程度:根据故障效应和后果的重要性,确定故障的严重程度。
这可以帮助团队确定优先处理的故障,并分配资源。
7.识别潜在的故障原因:对于每个故障模式,通过分析原因、原理、设计、制造等方面的因素,识别潜在的故障原因。
8.评估故障的发现和防止能力:评估故障在设计、生产和使用过程中的发现和防止能力。
这可以帮助团队确定适当的控制措施,防止故障的发生或降低其影响。
9.制定改进措施:根据评估结果,确定适当的改进措施。
这可能包括修改设计、更新工艺、改进维护计划等。
10.跟踪和监控改进措施:在实施改进措施后,应进行跟踪和监控,以确保其有效性。
这可以通过定期检查、性能测试和故障记录来完成。
总之,FMEA评定准则指导着FMEA评估的整个过程,确保评估的全面性和准确性。
通过遵循这些准则,企业可以有效地识别和预防潜在问题,提高产品和过程的质量,降低故障风险,并最大程度地满足客户需求。
FMEA严重度、频率、探测度评价准则

中等破坏
生产运行100%需要在其运行前进行生产线的工站上返工。
汽车可运行,但是外观或噪音等项目不合格,并且大多数(50%)顾客会发现这些缺陷。
3
生产运行的一部分需要在其运行前进行生产线的工站上返工。
汽车可运行,但是外观或噪音等项目不合格,并且大多数(<25%)有辨识能力的顾客会发现这些缺陷。
2
次要的破坏
8
10件/每千件
每100件中有一件
7
中等
2件/每千件
每500件中有一件
6
0.5件/每千件
每2000件中有一件
5
0.1件/每千件
每10,000件中有一件
4
低
0.01件/每千件
每100,000件中有一件
3
≤0.001件/每千件
每1,000,000件中有一件
2
很低
通过预防控制消除失效。
1
表格Cr3建议的过程FMEA探测度评价准则
对过程,作业或作业员带来轻微的不便。
没有影响
没有可识别的后果。
1
没有影响
没有可识别的影响。
表Cr2建议的过程FMEA频度评价准则
失效可能性
准则:起因发生可能性-过程FMEA(每项/每辆车出现的事故
等级
很高
≥100件/每千件
≥每10件中有1件
10
高
50件/每千件
每20件中有一件
9
20件/每千件
每50件中有一件
1
几乎肯定
次要功能丧失或降级
次要功能丧失(汽车可运行,但是舒适度/便利等功能失工然后可被接受。
次要功能降级(汽车可运行,但是舒适度/便利等性能层次降低)。
- 1、下载文档前请自行甄别文档内容的完整性,平台不提供额外的编辑、内容补充、找答案等附加服务。
- 2、"仅部分预览"的文档,不可在线预览部分如存在完整性等问题,可反馈申请退款(可完整预览的文档不适用该条件!)。
- 3、如文档侵犯您的权益,请联系客服反馈,我们会尽快为您处理(人工客服工作时间:9:00-18:30)。
后果
判定准则:后果的严重度
级别
无警告的 严重级别很高。潜在失效模式影响车辆安全运行和/或包含不符合政府 法规情形。失效发生时无预警。 严重危害 无警告的 严重级别很高。潜在失效模式影响车辆安全运行和/或包含不符合政府 严重危害 法规情形。失效发生时有预警。 很高 车辆/系统无法运行(丧失基本功能)
判定准则:后果的严重度 这级别导致当一个潜在失效模 式造成了在最终顾客和/或制 造/组装工厂的缺陷。应该随 时首先考虑到最终顾客。如果 放在两者都发生缺陷,则采用 较高一级的严重度 (制造/组装后果) 或,可能危及作业员(机器或 组装)而无警告。 或,可能危及作业员(机器或 组装)但有警告。 或,产品可能必须要100%丢 弃,或车辆/系统要在修理部 门花上多于一小时来加以修理 或,产品可能必须要经过筛 选,且一部分(少于100%)被 丢弃,或车辆/系统要在修理 部门花上半小时到一小时来加 以修理 或,可能有一部分(少于 100%)的产品不经筛选地被丢 弃,或车辆/系统要在修理部 门花上少于半小时来加以修理 或,100%的产品需要重新加 工,或车辆/系统要下生产线 修理,但不用到修理部门。 或,产品可能必须要筛选,没 有被丢弃,但一部分(少于 100%)需要重新加工。 或车辆/系统要在修理部门花 上半小时到一小时来加以修 理,而没有别丢弃。 或车辆/系统要在修理部门花 上半小时到一小时来加以修 理,而没有别丢弃。 或,轻微的对作业或作业员不 方便,或没有影响。
10 9 8 7 6 5
中上
设计控制有中上多的机会能找出潜在的起因/机理及后续的失效模式
4
多
设计控制有较多的机会能找出潜在的起因/机理及后续的失效模式
3
很多
设计控制有很多机会能找出潜在的起因/机理及后续的失效模式
2
几乎肯定
设计控制几乎肯定能找出潜在的起因/机理及后续的失效模式
1
后果
判定准则:后果的严重度 这级 别导致当一个潜在失效模式造成 了在最终顾客和/或制造/组装工 厂的缺陷。应该随时首先考虑到 最终顾客。如果放在两者都发生 缺陷,则采用较高一级的严重度 (顾客后果)
级别 10 9 8 7 6 5 4 3 2 1
探测度评价准则 探测度 评价准则:被设计控制探测的可能性 级别
绝对不肯 设计控制将不能和/或不可能找出潜在的起因/机理及后续的失效模式: 定 或根本没有设计控制 很极少 极少 很少 少 中等 设计控制只有很极少的机会能找出潜在的起因/机理及后续的失效模式 设计控制只有极少的机会能找出潜在的起因/机理及后续的失效模式 设计控制有很少的机会能找出潜在的起因/机理及后续的失效模式 设计控制有较少的机会能找出潜在的起因/机理及后续的失效模式 设计控制有中等机会能找出潜在的起因/机理及后续的失效模式
3
很轻微
装配和外观/尖响声和卡塔响声不符合要求,有辨识能力的顾客发现有 缺陷(少于25%)
2
无
没有可识别的影响
1
失效发生可能性 很高:持续发生的失效 高:反复发生的失效 中等:偶尔发生的失效 低:相对很少发生的相似失效 极低:失效不太可能发生
频度评价准则 可能的失效率 ≥100件/每千辆车 50件/每千辆车 20件/每千辆车 10件/每千辆车 5件/每千辆车 2件/每千辆车 1件/每千辆车 0.5件/每千辆车 0.1件/每千辆车 ≤0.010件/每千辆车
仅能以双重的目视检查来达到 控制 以图表方法(如SPC)来达到 × × 控制 × 在零件离开工位之后以计量值 量具来控制,或在零件离开工 位之后执行100%Go/No Go测定 在后续的作业中来探测错误, 或执行作业前准备和首件的测 定检查(仅适用发生于作业前 准备) 当场侦错,或以多重的接受准 则在后续作业中探测错误,如 库存、挑选、设置、验证。不 接受缺陷零件 当场探测(有自动停止功能的 自动化工具)。缺陷零件不能 通过
中上Leabharlann 现行控制方法有好 的机会去探测
× ×
高
现行控制方法有好 的机会去探测 现行控制方法几乎 确定可以探测
× ×
很高
× ×
几乎肯定
现行控制方法肯定 可以探测
×
该项目有过程/产品设计了防 错法,不会生产出缺陷零件
级别
10 9
8
7
6
5
4
3
2
1
级别
10 9 8 7 6 5
4
3
2
1
10 9
8
高
车辆/系统能运行,但性能下降。顾客很不满意。
7
中等
车辆/系统能运行,但舒适性/方便性方面性能失效。顾客不满意。
6
低
车辆/系统能运行,但舒适性/方便性方面性能下降。顾客有些不满意。 装配和外观/尖响声和卡塔响声不符合要求,多数顾客发现有缺陷(多 于75%)
5
很低
4
轻微
装配和外观/尖响声和卡塔响声不符合要求,50%的顾客发现有缺陷
探测度
评价准则
检查类型 A B C × × × ×
推荐的探测度分级方法
几乎不可能 确定绝对无法探测 很微小 微小 很小 小 中等 现行控制方法将不 可能探测 现行控制方法只有 很小的机会去探测 现行控制方法只有 很小的机会去探测 现行控制方法可能 可以探测 现行控制方法可能 可以探测
无法探测或没有检查 仅能以间接的或随机检查来达 到控制 仅能以目视检查来达到控制