塑料模压成型技术_一_
塑料模压成型

第一节 塑料模压成型
二、热固性塑料模压成型工艺 (一)预处理 2.预热:干燥和预热作用
预热时间/min
流动性/mm
第一节 塑料模压成型
二、热固性塑料模压成型工艺 (一)预处理 2.预热——方法 (1)热板加热 (2)烘箱加热 (3)红外线加热 (4)高频电热
第一节 塑料模压成型
二、热固性塑料模压成型工艺 (二)成型过程 (1)加料 (2)闭模 (3)排气 (4)固化 (5)脱模
第一节 塑料模压成型
二、热固性塑料模压成型工艺 (三)模制工艺参数分析 1.模压压力
作用:加速流动 压密物料 克服低分子物挥发所产生的压力 保持制品的尺寸和形状 防止制品冷却变形
第一节 塑ห้องสมุดไป่ตู้模压成型
二、热固性塑料模压成型工艺 (三)模制工艺参数分析 1.模压压力
决定因素:物料种类 模具温度 预热温度 制品形状
模压时间与制品性能的关系 ① 欠熟:模压时间短、固化不完全 ② 过熟:固化时间过长,制品内压力大 ③ 完全熟化:固化完全
第九章
塑料模压成型
第一节 塑料模压成型
• 概述
第一节 塑料模压成型
一、模压成型原理 1.流动段:一定的温度下,物料塑化流动 2.胶凝段:物料逐渐反应支化或交联 3.硬化段:物料交联至失去流动性
第一节 塑料模压成型
二、热固性塑料模压成型工艺 (一)预处理 1.预压
第一节 塑料模压成型
二、热固性塑料模压成型工艺 (一)预处理 1.预压
分步加压法:先低压合模熔融再高压充模
第一节 塑料模压成型
二、热固性塑料模压成型工艺 (三)模制工艺参数分析 2.模压温度
流动性
tmax
温度
模压周期/min
模压成型工艺流程

模压成型工艺流程模压成型工艺流程模压成型是一种常见的塑料制品加工工艺,通过热塑性塑料在高温和高压的条件下,使其在模具中快速冷却固化,形成所需的产品形状。
模压成型通常适用于生产大批量的塑料产品,具有生产效率高、产品质量稳定等优点。
下面将详细介绍一下模压成型的工艺流程。
首先,模压成型的第一步是准备原材料。
通常情况下,模压成型使用的是热塑性塑料颗粒。
在生产之前,需要对原料进行检查和筛选,确保原料无异物、无杂质。
第二步是将选好的原料放入料斗中。
料斗是一个用于存放和输送塑料颗粒的设备,其底部连接着一个加热器。
原料通过料斗进入加热器,在加热器的作用下,原料被加热至熔点。
第三步是将熔化好的塑料料利用螺杆输送机送进模具中。
螺杆输送机是一个直径逐渐变小的圆柱形装置,螺杆在内壁上旋转,将熔化好的塑料颗粒从料斗中带到模具中。
在螺杆的作用下,塑料颗粒逐渐被推入到模具的加压区域。
第四步是施加高温高压。
当塑料颗粒填满模具加压区域后,需要施加高温高压。
通过加热元件给模具加热,使模具中的塑料保持在熔化状态。
同时,通过液压系统给模具施加高压,使塑料颗粒充分融合,并填满整个模具的空腔。
第五步是冷却固化。
在塑料充分融化并填满整个模具之后,需要将模具和塑料冷却至固化状态,使产品形成所需的形状。
通常情况下,可以通过给模具注入冷却水、冷风等方式进行快速冷却。
第六步是模具开启和取出成品。
当塑料完全冷却固化后,可以将模具开启,取出成品。
通常情况下,需要用工具将成品从模具中取出,并进行后续的检验和包装操作。
最后,整个模压成型的工艺流程就完成了。
需要注意的是,模压成型工艺中需要控制好加热温度、压力和冷却速度等参数,以保证产品质量的稳定和一致性。
总的来说,模压成型是一种常见的塑料制品加工工艺,通过一系列的步骤将熔化的塑料填充到模具中,并进行高温高压和冷却固化等操作,最终形成所需的产品。
模压成型工艺具有生产效率高、产品质量稳定等优点,被广泛应用于塑料制品的生产中。
第6章热固性塑料的主要成型加工技术
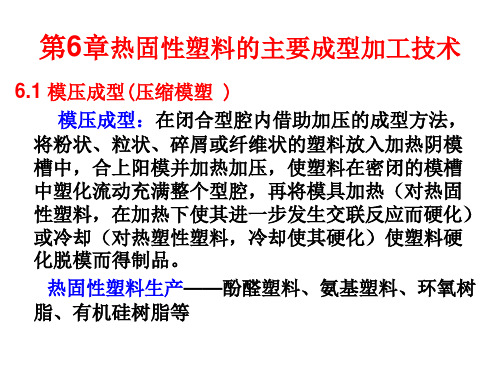
半溢式:有支承面与溢式相似,有装料室,用于小嵌件制品
无支承面与不溢式模具很相似,阴模向外倾斜3°, 阴模阳间有溢料槽
溢式模具
不溢式模具
图6-5 半溢式模具示意图 (a)有支承面 (b)无支承面
6.1.3 模压成型过程及操作
6.1.3.1 模压成型过程
成型物料的准备、成型和制品后处理三个阶段
模压成型原理
(2) 热固性与热塑性塑料注射成型不同点
热固性塑料在料筒内的塑化(料筒温度)
热固性塑料熔体在充模过程的流动(剪切
应力和充模速度)
热固性塑料在模腔内的固化(模具温度)
6.4.2 热固性塑料注射成型机
(1)注射装置
作用:将塑料均匀地塑化成熔融状态,将熔料注射到模腔内
基本形式:螺杆式和柱塞式,主要采用往复式单螺杆注射
机
螺杆——与热塑性塑料注射机区别大 (2) 螺杆驱动装置(低转速大扭矩油马达驱动螺杆旋转)
(3) 合模装置(由模板,拉杆,合模油缸等组成,合模力大)
(4) 控制系统
(5) 特殊注射机
双柱塞式注射机
图6-22 柱塞式聚酯料团注塑机 图6-21 多工位注塑机
6.4.3 热固性塑料注射成型工艺
图6-23 热固性塑料注塑成型工艺过程
C→E,交联,放Q→T物>T模, V↓
E点卸压, P↓常压
F点脱模
模压成型压力-温度-体积关系 ——:无支承面 ------:有支承面
6.1.4 模压成型工艺控制
6.1.4.1 模压压力Pm
指成型时压机对塑 料所施加的压力
pm
D2
4 Am
pg
Pm与塑料种类、模温、 制品形状有关
模压P对流动固化曲线的影响 a-50MPa b-20MPa c-10MPa
pc模压成型工艺

pc模压成型工艺
PC模压成型工艺是一种塑料加工方法,通过将粉状、粒状或纤维状的塑料放入模具中,在高温高压条件下使其成型并固化。
以下是PC模压成型的一些关键步骤和注意事项:
1. 材料准备:PC(聚碳酸酯)材料需先进行干燥处理,以降低其含水量至0.02%以下。
通常干燥条件为100-120℃,至少持续4小时以上。
2. 温度控制:炮筒温度应控制在270-320℃之间,避免超过340℃以防止PC分解。
熔体粘度随温度升高而下降,因此适当的温度对PC塑化是有利的。
3. 注射压力与速度:由于PC流动性差,需要使用较高的注射压力,同时要注意避免产生过大的内应力。
注射速度一般采用中速或慢速,对于薄壁、小浇口、深孔、长流程制品,推荐使用多级注射方式。
4. 保压压力与时间:保压压力的大小及保压时间的长短对PC制品的内应力有较大影响。
保压时间应根据制品的厚度、浇口大小和模温等因素来确定。
5. 模具设计:在设计胶口时,应考虑采用S形侧进胶或扇形进胶,以避免在高压充填中增加材料的剪切应力。
同时,模具设计应考虑充分的排气和顶出机制。
6. 模温控制:模具温度应控制在85-120℃,通常在80-100℃就可以。
对于形状复杂、较薄或有较高要求的制品,可以适当提高模温。
7. 固化过程:在模压过程中,模压料中的树脂将经历黏流、胶凝和固化三个阶段,树脂分子链将从线型变为不溶不熔的空间网状结构。
综上所述,PC模压成型工艺需要精确控制多个参数,包括材料的干燥、炮筒温度、注射压力与速度、保压压力与时间、模具设计以及模温控制等,以确保最终制品的质量。
塑料模压成型的工艺原理
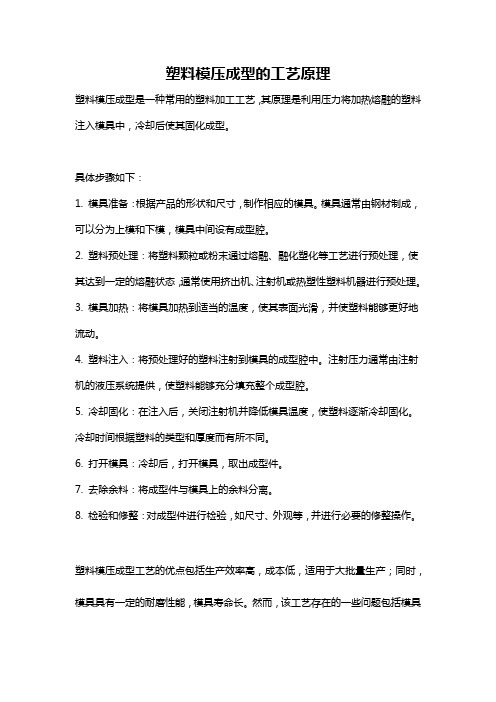
塑料模压成型的工艺原理
塑料模压成型是一种常用的塑料加工工艺,其原理是利用压力将加热熔融的塑料注入模具中,冷却后使其固化成型。
具体步骤如下:
1. 模具准备:根据产品的形状和尺寸,制作相应的模具。
模具通常由钢材制成,可以分为上模和下模,模具中间设有成型腔。
2. 塑料预处理:将塑料颗粒或粉末通过熔融、融化塑化等工艺进行预处理,使其达到一定的熔融状态,通常使用挤出机、注射机或热塑性塑料机器进行预处理。
3. 模具加热:将模具加热到适当的温度,使其表面光滑,并使塑料能够更好地流动。
4. 塑料注入:将预处理好的塑料注射到模具的成型腔中。
注射压力通常由注射机的液压系统提供,使塑料能够充分填充整个成型腔。
5. 冷却固化:在注入后,关闭注射机并降低模具温度,使塑料逐渐冷却固化。
冷却时间根据塑料的类型和厚度而有所不同。
6. 打开模具:冷却后,打开模具,取出成型件。
7. 去除余料:将成型件与模具上的余料分离。
8. 检验和修整:对成型件进行检验,如尺寸、外观等,并进行必要的修整操作。
塑料模压成型工艺的优点包括生产效率高,成本低,适用于大批量生产;同时,模具具有一定的耐磨性能,模具寿命长。
然而,该工艺存在的一些问题包括模具
制造成本高以及不适用于生产具有复杂结构的产品。
模压技术生产操作-成型工艺

模压技术生产操作-成型工艺简介本文档旨在介绍模压技术的生产操作中的成型工艺。
模压技术是一种常见的制造工艺,用于生产各种塑料制品。
成型工艺步骤下面是模压技术生产操作中的成型工艺步骤:1. 准备模具:选择合适的模具,确保其与要生产的产品设计相符。
2. 预热:将模具加热至适当温度,以保证塑料材料能够完全流动。
3. 准备材料:将所需塑料材料准备好,并按照要求对其进行预处理。
4. 放置材料:将预处理后的塑料材料放置在模具的预定位置。
5. 关闭模具:将模具紧密闭合,确保塑料材料受到充分压力。
6. 施加压力:通过推动模具上的压力机,施加适当压力,使塑料材料充分流动并填满模具腔体。
7. 冷却:保持模具处于所需的温度和压力条件下一段时间,使塑料材料冷却和固化。
8. 打开模具:当塑料材料完全冷却和固化后,打开模具,取出成型产品。
9. 检查和修整:对成型产品进行检查,确保其质量符合要求,如有需要,进行修整和加工。
10. 包装和存储:将成型产品进行包装,并妥善存储以待出售或使用。
注意事项在进行模压技术生产操作时,需要注意以下几点:- 操作人员应熟悉模压技术的原理和工艺要求。
- 确保模具与产品设计相符,避免产生不适配或无法实现的生产问题。
- 控制好模具的预热温度和保持时间,以保证塑料材料的流动性。
- 合理选择和处理塑料材料,确保其质量和适用性。
- 控制好施加压力的力度和时间,以保证产品的成型质量。
- 注意冷却时间和温度要求,以避免产生变形或缺陷。
- 在打开模具时要小心操作,防止损坏或意外受伤。
- 对成型产品进行严格检查,确保其符合质量要求。
以上是模压技术生产操作中的成型工艺的介绍,希望对您有所帮助。
压缩成型
(1)移动式 (2)半固定式 (3)固定式
16
压缩模分类及选用原则
2.按压缩模加料室的形式分类
(1)溢料(敞开)式压缩模
17
压缩模分类及选用原则
(2)不溢(封闭)式压缩模
18
压缩模分类及选用原则
(3)半溢式压缩模
19
三种结构模具的比较
溢式 配合: 无导柱定位 不溢式 较紧密单侧间隙0.07~0.08mm 半溢式 阴模上部略向外倾斜约3度,单侧间隙 0.025~0.075mm 加料室: 无 有 有,上壁做成15~20度锥度
(1)压缩成型压力
p成
D 2
4A
p表
压缩成型温度(℃) 压缩成型压力( MPa) 7~42 14~56 14~56 0.35~3.5 3.5~14 0.7~14 7~56
14
塑料种类 酚醛树脂(PF) 三聚氰胺甲醛(MF) 脲甲醛(UF) 聚酯塑料 邻苯二甲酸二丙烯酯(PDPO ) 环氧树脂eP) 有机硅塑料(OSMC)
加料量:
制品性能:
不准确,稍过量
外形简单质量不高
加料准确(称量法)
无明显毛边高度可较大
稍过量
料从非配合面溢出,有水平飞边,尺 寸 大外形 复杂、压缩率大的制品精 度较好
① 几乎所有热固性塑料。常见的有酚醛、脲醛、
环氧塑料、不饱和聚酯、氨基塑料、聚 酰亚胺、
有机硅等,也可用于热塑性的聚四氟乙烯和PVC唱
146~180 140~180 135~155 85~150 120~160 145~200 150~190
压缩成型设备
压缩成型的主要设备是 压力机。但根据传动方式不 同,压力机又可分为机械式 和液压式两种。机械式压力 机常用螺旋式压力机,但因 结构简单、技术性能不稳定, 故而被液压机所取代。
模压成型工艺的工艺流程是什么呢
模压成型工艺的工艺流程是什么呢模压成型工艺是一种常见的制造工艺,广泛应用于塑料制品、橡胶制品、复合材料等领域。
其基本原理是通过热压或冷压的方式,使原料在模具中发生形状、尺寸和性能的变化,从而得到所需的成品。
模压成型工艺包括准备工作、预热、模具充填、加压成型、冷却、脱模等多个环节。
首先,在进行模压成型前,需要准备好充分的原料和模具。
原料通常为颗粒状或片状的材料,根据产品的要求选择合适的原料。
模具则根据产品的设计图纸制作,包括上模、下模以及必要的辅助构件。
接下来是预热步骤,即将模具加热至适当温度。
预热的目的是为了提高原料的流动性,有利于充填模具空腔并保证产品的成型质量。
预热温度和时间根据原料的种类和厚度进行调控。
模具充填是模压成型的核心步骤之一。
在预热后的模具中,将预先称量好的原料粒料投入到模具腔内。
通过振动或压实等方式,保证原料充分填充模具空腔,并使得原料可以均匀一致地分布。
加压成型是将已经充填好的模具放入压力机中进行压制的过程。
通过施加恰当的压力,原料在高温高压下发生变形和流动,以适应模具的形状。
加压的时间和力度需要根据原料的性质和产品要求进行调整。
成型完成后,需要进行冷却阶段。
冷却的目的是使得产品在模具中保持形状和尺寸稳定,同时加快产品的硬化和固化过程。
通常采用自然冷却或水冷却的方式,不同原料和产品可能需要不同的冷却时间。
最后是脱模操作,即将成品从模具中取出。
脱模时需要小心操作,避免损坏产品表面或模具结构。
有些复杂的产品可能需要采用辅助工具或特殊的脱模方法,确保产品的完整性和质量。
总的来说,模压成型工艺是一种高效、可控的制造工艺,能够生产出形状复杂、精度高的制品。
通过合理设计工艺流程和选择适当的原料,可以满足各种产品的需求,并在工业生产中发挥重要作用。
1。
模压成型工艺—模压成型操作(塑料成型加工课件)
热固性塑料在一定的合模压力和模具温度下保 持一段时间,达到一定的交联程度。
在加热加压的状态下,物料快速发生化学交联 反应,交联程度快速提高,树脂分子链由线性结构 变成三维网路结构,物料固化,物理机械性能提高。 有时候,为了提高生产效率,在制品能够不变形脱 模时就暂时结束热压固化过程,然后再通过后处理 完成固化的后期过程。
首先,要检查模具是否有油污、碎屑或异物, 并清理干净,如果需要可适当喷涂脱模剂。然后, 向模具型腔加入物料,尽可能放在模具型腔的中间, 流动阻力大的部位应多放一些料。加料量直接影响 制品的密度和尺寸,加料量过多制品易产生飞边, 厚度尺寸不精确;加料量过少则预压,使树脂充满整个型腔。 在预压过程中应让模具缓慢合紧,使树脂有足 够的时间在模腔内流动,并且避免树脂因合模过快 被空气带出,使制品造成破坏。
模压成型
模压工艺操作
一、模压工艺流程
热固性塑料模压成型的工艺过程包括加料、预压、 排气、固化和脱模等。
二、操作过程
1.开机预热
先接通电源,然后启动模压机开关。将模具放 到加热板上,点击“主缸上”合模;通过控制面板 设置加热板温度,打开加热热开关启动加热,当温 度达到设置值后再恒温一段时间。
2.加料
4.排气
通过适当的卸压松模排除气体,该过程可和预 压配合进行。
热固性塑料在模压时发生化学交联反应,常伴 有水蒸汽和小分子挥发物放出,因此需要短暂的时 间打开模具,使水蒸汽、小分子挥发物和空气排除, 避免对制品造成缺陷影响。排气完成后,应在物料 还处于良好流动状态时迅速闭模,对物料加热加压。
5.固化
6.脱模
固化后让制品和模具分离。脱模速度不能过 快,否则制品容易变形,而速度过慢则会影响生 产效率。当制品脱模后,要认真清理模具,用铜 制工具取出模具上的杂志和附着物,为下一个制 品的生产做准备。
模压成型工艺流程
模压成型工艺流程
《模压成型工艺流程》
模压成型工艺是一种常见的塑料加工方法,其流程主要包括模具设计、原料预处理、模压成型、冷却固化和脱模等环节。
首先,在进行模压成型之前,需要设计相应的模具。
模具设计需考虑产品的形状、尺寸和结构,以及模具的开合方式和材料的选择等因素。
然后将设计好的模具进行加工制造。
随后,原料预处理是模压成型的重要环节之一。
首先是将塑料原料加热至熔融状态,然后将其注入模具腔体中。
在此过程中,需要考虑原料的温度控制、注塑速度和压力等参数。
接下来是模压成型阶段,即将熔融的塑料原料注入模具中,经过高压与高温的作用,使其填充模具腔体并成型。
在模具中保持一定的时间后,塑料原料冷却固化,形成所需的产品形状。
冷却固化完成后,即可进行脱模。
此时需要将冷却好的产品从模具中取出,通常需要采用脱模装置或其他辅助工具来辅助取出产品。
这一步骤需要注意操作方法和产品的保护,确保产品完好无损。
最后,经过脱模后的产品即为最终成型的产品,可以进行后续的加工处理,如去除刷边、组装等工序,以及进行质量检验和包装。
总的来说,模压成型工艺流程包括模具设计、原料预处理、模压成型、冷却固化和脱模等环节,每一步都需要严格控制和操作,以保证最终产品的质量和外观要求。
- 1、下载文档前请自行甄别文档内容的完整性,平台不提供额外的编辑、内容补充、找答案等附加服务。
- 2、"仅部分预览"的文档,不可在线预览部分如存在完整性等问题,可反馈申请退款(可完整预览的文档不适用该条件!)。
- 3、如文档侵犯您的权益,请联系客服反馈,我们会尽快为您处理(人工客服工作时间:9:00-18:30)。
4
橡塑技术与装备
2001 年第 27 卷
制新产品 或对新的聚合物材料和树脂基复合材料 的制品 采用传递成型更有利
的性能进行研究 以缩短试制周期 (5)特别适于成型不得翘曲的薄壁制品 壁厚小
至 0.6mm 的制品也可模压成型 但通常推荐壁厚
(3)由于一般模压料熔体的粘度很高 要使之完 全充模可能存在问题 为了保证熔体能完全充模 可能必须把模压料置于模腔内的一个最佳位置 有
热塑性塑料模压成型中的充模阶段与热固性 塑料的类似 但由于不发生化学反应 故在熔体充 满模腔后 要冷却模具使制品固化才能开模取出制
品 正因为热塑性塑料模压成型时模具需要交替地 加热和冷却 成型周期长 生产效率低 因此一般 不采用模压方法成型热塑性塑料制品 只有在成型 大型厚壁平板状制品和一些流动性很差的热塑性 塑料时才采用模压成型方法
模压成型中 除模具加热外 另一种热源是合 模过程中产生的摩擦热 这是因为合模会使塑料产 生流动 其局部流动速度会很高 从而转变成摩擦 热 对热固性塑料的模压成型 还有一种热量输入 发生在后固化阶段或称熟化阶段(一般为在 135 下进行 2h 然后在 65 下再进行 2h) 这是因为许 多热固性塑料制品脱模后在一升高的温度下放置 一段时间继续完善交联 可改善其电气性能和机械 性能 不进行后固化 热固性模压成型制品可能要 在很长时间(数月甚至数年)完成最后 5%~10%的交 联 尤其对酚醛模压料 后固化可适当缩短制品在 模腔内的固化时间 从而提高生产效率 1.4 模压成型的优缺点
文献标识码 A
文章编号 1009-797X(2001)02–0001-05
1 过程 原理及优缺点 模压成型(Compression Molding)又称压缩模塑
或压塑 它是最古老的聚合物加工技术之一 是生 产热固性塑料制品最常用的方法之一 也用于部分 热塑性塑料
模压成型中 把一定量通常被预热的塑料(可 以是粉状 粒状或片状等)置于被加热的模具型腔 内 然后合上模具 对塑料施加压力 使之熔融成 为粘流态而充满模腔 成型为制品 制品固化后 开模 取出制品 并清理模具 开始下一成型周期 见图 1
第2期
黄汉雄﹒塑料模压成型技术(一)
3
图 2 示出了典型的热固性塑料模压成型中模 板的位置随时间的变化情况 装料后合上模具 在 阳模尚未触及模压料前 应尽量采用高的合模速度 (见 AB 段) 以缩短成型周期和避免热固性模压料 过早固化 阳模触及模压料后 合模速度应降低(见 BC 段) 最后以较快的速度完全合模(见 CD 段) 合模时间由几秒至数十秒不等 热固性塑料模压成 型过程中 在合模加压后 将模具松开少许(见 EF 段)并停留一短时间(见 FG 段) 以排出模腔内的气 体 排气有利于缩短固化时间 提高制品性能
20 世纪 70 年代 模压成型领域重要的进展包 括闭环控制的模压机 螺杆喂料系统和无流道注射
2
ห้องสมุดไป่ตู้
橡塑技术与装备
2001 年第 27 卷
模压成型(RIC) 20 世纪 80 年代初期 汽车工业对 模压成型增强塑料汽车面板的产量有更高的需求 这导致了新的 快速 短行程的 SMC(片状模塑料) 用模压机的出现 这种模压机带有程序可控的力/ 速度控制(PFVC)系统和模板调平装置 80 年代末 期 SMC 和 GMT(玻璃纤维毡片增强热塑性塑料) 用模压机的微机控制至少与注塑或其他塑料加工 方法那样的先进 采用了远程诊断系统 快速合模 速度可达 1m/s
第2期
黄汉雄﹒塑料模压成型技术(一)
1
塑料模压成型技术(一)
黄汉雄
(华南理工大学 广州 510640)
摘要 模压成型是最古老的聚合物加工技术之一 简述了模压成型的发展历程及现状 分析了其成型过程的五个阶段及成
型原理 并与注塑和传递成型等方法相比 分析了模压成型的优缺点
关键词 塑料 模压成型
中图分类号 TQ320.66+1
图 1-2 典型的热固性塑料模压成型周期中模板的位置 示意图
A-周期始点 A B-高速合模 B C-慢速合模 C D-高速完全合 模 D E-加压 E F-开模 F G-排气 G H-合模 H I-固化
I J-开模 J-周期终点
1.3 模压成型的原理 模压成型热固性塑料(部分聚合)时 置于模具
型腔内的塑料被加热到一定温度后 其中的树脂熔 融成为粘流态 并在压力作用下粘裹着纤维一起流 动直至充满整个模腔而取得模腔所赋予的形状 此 即充模阶段 热量与压力的作用加速了热固性树脂 的聚合或称交联(一种不可逆的化学反应) 随着树 脂交联反应程度的增加 塑料熔体逐渐失去流动性 变成不熔的体型结构而成为致密的固体 此即固化 阶段 聚合过程所需的时间一般与温度有关 适当 提高温度可缩短固化时间 最后打开模具取出制品 (此时制品的温度仍很高) 可见 采用热固性塑料 模压成型制品的过程中 不但塑料的外观发生了变 化 而且结构和性能也发生了质的变化 但发生变 化的主要是树脂 所含增强材料基本保持不变 因 此 可以说热固性塑料的模压成型是利用树脂固化 反应中各阶段的特性来成型制品的
模压成型具有如下所述的优点 (1)由于没有浇注系统 故原料的损失小(通常 为制品质量的 2%~5%) (2)由于模腔内的塑料所受的压力较均匀 在压 力作用下所产生的流动距离较短 形变量较小 且 流动是多方向的 因此 制品的内应力很低 从而 制品的翘曲变形也很小 机械性能较稳定 此外 模压成型中不象在注塑模具浇口或流道处那样存 在很高的剪切应力区 故对含增强纤维的模压料 不会出现注塑中经常会发生的充模过程中纤维被 剪碎的现象 这样 模压料中可加入较多且较长的 增强纤维 模压成型制品中纤维的长度可以较长 从而制品可保持高的机械性能和电气性能 正因为 这样 模压成型技术的不少进展是直接或间接地涉 及到采用树脂基复合材料生产高强轻质的结构制 件 而注塑中仅能加入含量低且长度短(一般小于 3mm)的增强纤维 (3)由于模压料的流动距离短 故模腔的磨损很 小 模具的维护费用也就较低 (4)成型设备的造价较低 其模具结构较简单 制造费用通常比注塑模具或传递成型模具的低 故 适于多品种 小批量制品的生产 制品的成本也就 较低 也正因为这样 不少研究者采用模压成型试
20 世纪 90 年代 由于节能 环保和安全等的 要求 汽车工业等继续推动着模压成型技术的发 展 这主要表现在三个方面 首先 SMC 在汽车 工业中的使用量在增加 且推出了一些新的模压 料 尤其是 SMC(如低压 SMC 高模量 SMC 软 质 SMC 和易于加工的 SMC) BMC(团状模塑料) 以及 GMT 等 因为汽车工业是SMC BMC和 GMT 的最大用户 其次 模压成型机械进一步往高度自 动化 高速和高精度方向发展 第三 不断提高模 压成型制品的表观性能 可不采用模内涂覆即可生 产 A 级表面的汽车配件
图 1 模压成型的过程
清理模具 加料 合模 固化 开模 取出制品
1.1 模压成型的发展简述 许多世纪前 人们就已采用各种初始的模压成
作者简介 黄汉雄(1963-) 男 博士 教授 博士生导师 系主任 主要从事聚合物加工成型的机理与流变学研究以及聚合物成型设备-性 能研究 获国家霍英东教育基金会 第六届高等院校青年教师奖 等奖 励 在国际著名刊物及国内核心刊物上发表论文 50 余篇 获得中国发明 专利 1 项 编著出版 塑料吹塑技术 参与 机械工程手册 (二版) 等 4 本手册的编写工作
1653 年 帕斯卡(Pascal)发现了液压机工作的 基本原理 正是液压机的发明奠定了现代模压成型 方法的基础 不过 直至 1839 年 Goodyear 发现了 硫化橡胶的加工方法后 液压机才在商业模塑中得 到应用 从而揭开了现代模压成型技术的序幕
1907 年 Baekeland 开发成功第一种合成热固 性树脂 可模压成型的酚醛树脂 1910 年左右 酚醛树脂的出现刺激了模压机产量的提高 也导致 了早期半自动模压机的诞生 大约在 1915 年 Burroughs 研制成半自动模压机 这是模压成型技 术的一个重要进展
收稿日期 2000-12-22
型方法 几千年前 中国人已采用一种早期的模压 工艺造纸 中世纪 模压成型技术被用来压制各种 天然树脂 18 世纪 美国人采用动物的角或龟壳 模压成制品 19 世纪初期至中期 人们采用模压 方法压制橡胶零件 由杜仲胶压制刀柄及其他用 品 由虫胶塑料 木质纤维等压制照片框架等
总的来说 20 世纪的前 50 年 由于酚醛树脂 的出现并被大量采用 模压成型是加工塑料的主要 方法 至 20 世纪 40 年代 因热塑性塑料的出现并 可采用挤出和注射方法来成型 情况开始发生变 化 模压成型初期加工的塑料约占塑料总量的 70%(质量分数) 但至 50 年代 该比例降至 25%以 下 目前约为 3% 这种变化并不意味着模压成型 是一种没有发展前景的方法 只不过是模压成型生 产热塑性塑料制品时成本过高 20 世纪初期 95%(质量分数)的树脂为热固性的 至 40 年代中 期 该比例降至约 40% 而目前仅约为 3% 不过 模压成型仍是一种重要的塑料成型方法 尤其在成 型某些低成本 耐热等制品时 随着新的树脂基热 塑性和热固性模压料的出现 以及汽车工业等的发 展 模压成型正焕发出新的活力 1.2 模压成型的全过程
最小取 1.5mm 模压成型还可生产壁厚相差较大的 制品
为明确和方便起见 把模压成型的全过程划分 为以下五个阶段
(1)原材料准备 即制备模压料或预浸料坯 这一阶段可能包括 使树脂混合 使树脂与填料或纤维混合在一起或使
增强织物或纤维与树脂浸渍 原材料准备阶段通常 要控制模压料的流变性能 对增强塑料 还要控制 纤维与树脂之间的粘结
(2)预热 对某些热固性塑料 预热是在模具外采用高频 加热完成的 对 SMC 预热可在模压料置于模腔 内后但在合模与流动开始之前进行 热固性塑料经 预热后进行模压成型 可降低模压压力 缩短成型 周期 提高生产效率 改善模压料固化的均匀性 从而提高制品的性能 (3)熔体充模 这一阶段从塑料开始流动至模腔被完全充满 时为止 模压成型中物料流动的量是较少的 但对 制品的性能影响很大 流动控制着短纤维增强塑料 中增强纤维的取向 从而对制品的机械性能有着直 接的影响 即使对未增强的塑料 流动也对热传递 起着重要的作用 从而控制制品的固化 在某些模 压成型过程中 尤其是包含层压的过程中 初始的 模压料就已充满模腔 基本上没有流动 (4)模内固化 这是紧接熔体充模的一个阶段 即制品在模具 内固化 不过 对热固性模压料 有些固化在充模 过程中就开始发生了 而固化的最后阶段也可以在 制品脱模后的 后固化 加热过程中完成 通常模 内固化要把模压料由粘流态(可以流动以充满模腔) 转变成固态(足够硬以便从模具内取出) 这一阶段 要发生大量的热传导 因此重要的是要弄清热传递 与固化之间的相互作用 根据模压料类型 预热温 度以及制品厚度的不同 热固性塑料的固化时间由 数秒至数分钟不等 (5)制品脱模与冷却 这是模压成型的最后一个阶段 这一阶段对制 品是否发生变形以及残余应力的形成会有影响 产 生残余应力的一个原因是制品不同部位之间的热 膨胀存在差异 因此 即使制品在模压成型的温度 下是无应力的 在冷却至室温的过程中也会形成残 余应力 从而使制品变形 对粘弹性聚合物 在确 定这些应力将如何松弛方面 温度分布与冷却速率 是重要的参数 有时 为了保证制品有较高的尺寸 精度 制品脱模后被置于防缩器或冷压模内进行后 处理