数控铣床常用刀具的合理选用
数控刀具及其选用

一、选择刀具时应考虑的因素 (1)被加工工件的材料类别(黑色金属,有色金属或合金); (2)工件毛坯的成形方法(铸造,锻造,型材等); (3)切削加工工艺方法(车,铣,钻,扩,铰,镗,粗加工,半精加工,精加工等); (4)工件的结构与几何形状,精度,加工余量以及刀具能承受的切削用量等因素; (5)其他因数包括生产条件和生产类型。
数控刀具及选用
1.1 数控机床刀具的特点
数控机床刀具的特点是标准化、系列化、规格化、模块化和通用化。 为了达到高效、多能、快换、经济的目的,对数控机床使用的刀具有如下要求: (1)具有较高的强度、较好的刚度和抗振性能; (2)高精度、高可靠性和较强的适应性; (3)能够满足高切削速度和大进给量的要求; (4)刀具耐磨性及刀具的使用寿命长,刀具材料和切削参数与被加工件材料之间要适宜; (5)刀片与刀柄要通用化、规格化、系列化、标准化,相对主轴要有较高位置精度,转位、拆 装时要求重复定位精度高,安装调整方便。
1.5 常用数控刀具结构
一、整体式刀具结构 整体式刀具是指刀具切削部分和夹持部分为一体式结构的刀具。 制造工艺简单,刀具磨损后可以重新修磨。
二、机夹式刀具结构 机夹式刀具是指刀片在刀体上的定位形式。 机夹式刀具分为机夹可转位刀具和机夹不可转
位刀具。数控机床一般使用标准的机夹可转位刀具。 机夹可转位刀具一般由刀片、刀垫、刀体和刀
1.4 数控机床刀具分类
按照刀具材料可分为:高速钢刀具,硬质合金刀具,陶瓷刀具,立方氮化硼刀具和金刚石刀具。 按照刀具结构可分为:整体式,焊接式,机夹式(可转位和不转位),内冷式和减振式。 按照切削工艺分为:车削刀具,孔加工刀具(如钻头,丝锥和镗刀等),铣削刀具等。 按照数控工具系统的发展可分为:由整体式工具系统向模块式工具系统发展。有利于提高劳动 生产率,提高加工效率,提高产品质量。 标准化数控刀具已形成了三大系统,即车削刀具系统、钻削刀具系统和镗铣刀具系统。
加工中心刀具怎么选择合适的?

加工中心刀具怎么选择合适的?加工中心刀具怎么选择合适的?加工中心刀具主要分为铣削刀具和孔加工刀具两大类。
铣削刀具的选择主要是铣刀型别和铣刀尺寸的选择。
铣刀型别应与工件表面形状与尺寸相适应。
加工较大的平面应选择面铣刀;加工凹槽或者是较小的台阶及平面轮廓时应选择立铣刀;加工曲面应选择球头铣刀;加工模具型腔或凸模成形表面等多选用模具铣刀;加工封闭的键槽选择键槽铣刀;加工变斜角面应选用鼓形铣刀;加工各种直的或圆弧形的凹槽、斜角面、特殊孔等应选用成形铣刀。
当粗铣或铣不重要的加工平面时,可使用粗齿铣刀;当精铣时,可选用密齿铣刀,用小进给量达到低的表面粗糙度;当铣材料较硬的金属时,必须选用密齿铣刀,同时进给量要小,以防止振动。
铣刀尺寸也应与被加工工件的表面尺寸和形状相适应。
刀具直径的选用主要取决于装置的规格和工件的加工尺寸,另外还要考虑刀具所需功率应在机床功率范围之内。
粗铣时铣刀直径要小些,精铣时铣刀直径要尽量大些,最好能够包容整个加工宽度。
表面要求高时,还可以选择使用具有修光效果的刀片。
而孔加工刀具可分为钻孔刀具、镗孔刀具、扩孔刀具和铰孔刀具。
(1)钻孔刀具较多,主要有普通麻花钻、可转位浅孔钻以及扁钻。
用加工中心钻孔通常都会采用普通麻花钻,普通麻花钻主要由工作部分和柄部组成的。
刀具柄部分为直柄和锥柄两种。
直柄工具的刀柄主要是弹簧夹头刀柄,其具有自动定心、自动消除偏摆的优点,所以小规格的刀具最好选用该型别。
而工作部分包括切削部分和导向部分,所示,麻花钻的切削部分有2个主切削刃、2个副切削刃、1个横刃。
麻花钻的导向部位起导向、修光排屑和输送切削液作用。
麻花钻一般用于精度较低孔的粗加工,由于加工中心所用夹具没有钻套定心导向,钻头在高速旋转切削时容易会发生偏摆运动,而且钻头的横刃长,所以在钻孔时,要用中心钻打中心孔,用以引正钻头。
(2)镗削的主要特点是获得精确的孔的位置尺寸,得到高精度的圆度、圆柱度和表面粗糙度,所以,对精度较高的孔可用镗刀来保证。
数控铣常用刀具、夹具、量具
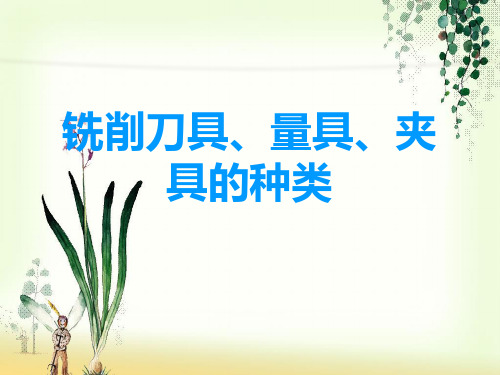
量具的分类
(1)钟表式百分表
量具的分类
(2)杠杆式百分
机床夹具的分类
机床夹具种类繁多,可按不同的方 式进行分类,常用的分类方法有以 下几种。
机床夹具的分类
1. 按用途分类: 1)通用夹具 2)专用夹具 3)组合夹具
机床夹具的分类
1)通用夹具:三爪、四爪卡盘,平口钳等,一般由专业厂 生产,常作为机床附件提供给用户。
(1)通用夹具
可在一定范围内用于加工不同工件的夹具。 如车床使用的三爪卡盘、四爪卡盘,铣床 使用的平口虎钳、万能分度头等。这类夹 具已经标准化,作为机床附件由专业厂生 产。其通用性强,不需调整或稍加调整就 可以用于不同工件的加工;生产率低,夹 紧工件操作复杂。这类夹具主要用于单件 小批量生产。
机床夹具的分类
a)
b)
c)
刀具的分类
6.铰刀 铰刀常用来对已有孔进行 最后精加工,也可对要求 精确的孔进行预加工。其 加工公差等级可达IT8~IT6 级,表面粗糙度Ra值达 1.6~0.2μm。铰刀可分为手 动铰刀和机机铰刀。
刀具的分类
7.镗刀 镗刀是对已有的孔进行再加工刀具。镗刀可在车床、镗床 或铣床上使用,可加工精度不同的孔,加工精度可达IT7~ IT6级,表面粗糙度Ra值达6.3~0.8μm。
刀具的分类
刀具的分类
4. 扩孔钻 扩孔钻专门用来扩大已有孔,它比麻花钻的齿数
多(Z>3),容屑槽较浅,无横刃,强度和刚度 均较高,导向性和切削性较好,加工质量和生产 效率比麻花钻高。
刀具的分类
5.锪钻 锪钻用于加工各种埋头螺钉沉孔、锥孔和凸台面 等。常见的锪钻有三种:圆柱形沉头锪钻、锥形 沉头锪钻及端面凸台锪钻。
2、千分尺 主要精密测量外径、内径、深度、 螺纹中径等。
数控机床、刀具和夹具的选择与使用

数控刀具的选择
▪ 刀具的选择是数控加工工艺设计中的重要内容之一。刀具选择 合理是否不仅影响数控机床的加工效率,而且还直接影响加工质量。 选择刀具通常要考虑机床的加工能力、工序内容和工件材料等等因 素。
模具制造工艺学
数控机床、刀具和夹具的选择与使用
▪ 数控机床的合理使用 ▪ 1 数控机床的选用原则
▪ 目前,我国生产的数控机床有高档、中档、及经济型3个档次, 经济性数控机床的性能现已有了质的提高,而价格却只有中档数控 的几分之一至十几分之一,应可能选用。
数控机床、刀具和夹具的选择与使用
▪ 数控机床的合理使用 ▪ 2 曲面加工与坐标轴数的选择
1.3 夹具的设计和使用
▪ 对数控机床夹具设计使用的具体要求
3 夹具的设计要方便加工零件的装卸,夹具要能迅速完成零件的 定位、夹紧和拆卸过程。为此,夹具的设计要力求结构简单,整体 性能好,不得有零碎的配件和繁杂的结构。为有效缩短辅助工作时 间,保证装夹的可靠,数控机床夹具常采用气动、液压和偏心夹紧 方式夹紧工件。
切屑缠绕都会影响加工的正常进行,因此,应合理选用断屑槽的形
状、尺寸与切削用量,保证断屑的可靠。
刀柄
▪ 刀柄是加工中心必备的辅助工具,用以将刀具与机床主轴连接 起来。由于加工中心有自动交换刀具的功能,所以刀柄必须满足机 床主轴自动松开和拉紧定位的要求,且能在机械手的夹持下与搬运 下,准确地安装各种切削刀具。
1.3 夹具的设计和使用
▪ 对数控机床夹具设计使用的具体要求
2 为适应数控加工高强度、大切削量的特点,数控夹具的结构应 具备足够的强度与刚度,以避免在振动与装夹力的作用下产生变形; 要避免工件在受强力切削时位置发生错动,数控夹具对工件的夹紧 力就要大一些,为防止过大的夹紧力与较大的切削力使工件产生变 形,夹具的定位点、支撑受力点、夹紧点的选择应慎重。
数控机床铣床的操作流程和技巧

数控机床铣床的操作流程和技巧数控机床铣床作为制造业中常见的加工设备,具备高效、精确、稳定等优点,广泛应用于各个领域。
然而,在操作数控机床铣床时,正确的操作流程和掌握一些技巧对于提高加工效率、保证产品质量至关重要。
本文将简要介绍数控机床铣床的操作流程以及一些常用的技巧。
一、数控机床铣床的操作流程1. 设计加工方案:在进行加工之前,首先需要根据所需加工的零件进行设计加工方案。
根据零件的形状、材料等特点确定铣削方式、切削参数等。
2. 编写加工程序:根据设计好的加工方案,通过相应的CAD/CAM软件编写加工程序。
加工程序中包括刀具路径、进给速度、切削深度等参数的设置。
3. 加载加工程序:将编写好的加工程序通过U盘或网络传输到数控机床的控制系统。
然后在机床控制面板中加载该程序。
4. 夹具与工件安装:根据加工方案和实际需要,选择合适的夹具并将工件固定在夹具上。
务必确保工件的稳定固定,以免加工中发生松动导致误差。
5. 刀具选择与安装:根据加工程序中所要求的切削方式和参数,选择合适的刀具。
然后使用正确的方法将刀具安装到主轴上,并紧固好。
6. 坐标系设置:在数控机床操作面板中进行坐标系设置。
包括零点坐标、工件坐标系、刀具补偿等设置。
坐标系设置的准确性直接关系到加工零件的尺寸精度。
7. 调试与确认:在正式加工之前,先进行刀具轨迹的调试与确认。
通过机床控制面板中的手动操作功能,逐个验证机床各轴运动是否正常,刀具路径是否正确。
8. 加工操作:确认调试无误后,可以开始进行加工操作。
通过启动机床控制系统中的自动运行程序,机床将按照设定的刀具路径和参数进行自动加工。
9. 监控与调整:在加工过程中,及时监控加工状态,观察切削情况、切削力、温度等参数的变化。
根据需要,及时调整切削参数,确保加工质量。
10. 加工完成与检验:加工完成后,将工件从夹具上取下,进行尺寸检测、表面质量检验等。
根据检验结果,判断加工是否合格,并进行必要的修正。
数控铣床刀具路径优化
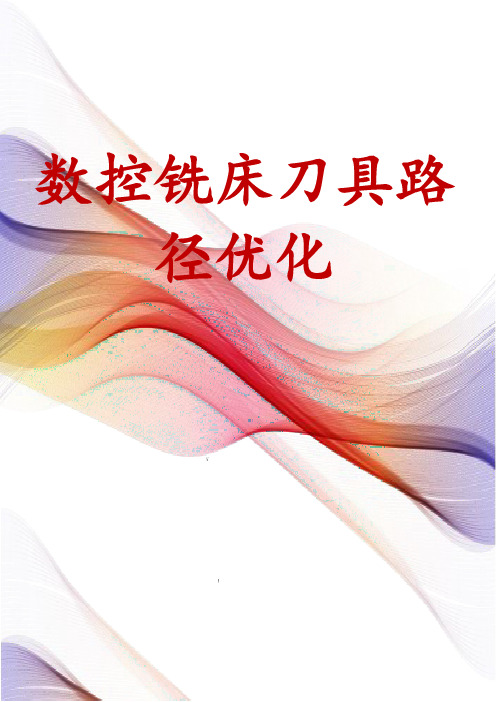
数控铣床刀具路径优化数控铣床刀具路径优化数控铣床刀具路径优化是一种优化加工过程的方法,通过合理规划和优化刀具路径,可以提高加工效率和加工质量。
本文将逐步介绍数控铣床刀具路径优化的步骤和方法。
第一步:了解零件加工要求和数控铣床的工作范围。
在进行刀具路径优化之前,需要明确零件的加工要求,包括精度要求、表面光洁度要求等。
同时,要了解数控铣床的加工范围和限制条件,包括工作台的行程、刀具长度等。
第二步:确定加工顺序和加工区域。
根据零件的形状和加工要求,确定加工顺序和加工区域。
通常情况下,需要先进行粗加工,再进行精加工。
在确定加工区域时,可以根据刀具的直径和长度,选择合适的工作区域,避免刀具碰撞和工件变形。
第三步:选择合适的刀具路径策略。
刀具路径策略包括切削路径和切削方向的选择。
在选择切削路径时,可以根据零件的形状和加工要求,选择合适的切削路径,如螺旋切削路径、直线切削路径等。
在选择切削方向时,可以根据切削力的方向和大小,选择合适的切削方向,以减小切削力和切削振动。
第四步:进行刀具半径补偿。
刀具半径补偿是根据刀具的实际半径,对刀具路径进行调整,以保证加工尺寸的准确性。
在进行刀具半径补偿时,需要根据实际加工情况,合理选择刀具半径补偿的方式,如刀尖补偿、刀具半径补偿等。
第五步:优化刀具路径。
在确定刀具路径后,可以通过优化刀具路径,进一步提高加工效率和加工质量。
刀具路径优化的方法主要包括减少刀具的回程距离、减少切削次数、减小切削力和切削振动等。
第六步:进行切削仿真和验证。
在完成刀具路径优化后,可以进行切削仿真和验证,以验证刀具路径的合理性和有效性。
通过切削仿真和验证,可以发现和解决潜在的问题,并对刀具路径进行进一步优化。
通过以上的步骤和方法,可以有效地进行数控铣床刀具路径优化,提高加工效率和加工质量。
同时,还可以减少刀具的磨损和损坏,提高刀具的使用寿命,降低加工成本。
数控铣床刀具路径优化是现代制造业中的一项重要技术,对于提高加工效率和提高产品质量具有重要意义。
数控刀具常用锥柄及拉钉标准简介

数控刀具常用工具锥柄标准简介随着数控金切机床的广泛使用,与之配套的数控刀具使用量也在不断增加。
由于我国多年来从不同国家引进了大量数控机床,而这些机床采用的工具锥柄标准不尽相同,这就给用户(尤其是刚接触数控金切机床的新用户)选用数控刀具带来一些困难和问题。
本文根据笔者手头收集到的一些相关标准作一简要介绍,希望有助于增加读者对数控刀具常用工具锥柄标准的了解和掌握。
目前,数控铣床和镗铣加工中心使用最多的仍是7∶24工具锥柄。
但在高速加工机床上,1∶10空心短锥柄的使用正日益增多。
对于车削中心和车铣中心,则以1∶10短锥柄使用较多(车削中心使用的CZG圆柱柄工具系统不属本文讨论范围)。
自动换刀机床常用的7∶24工具锥柄标准主要有:中国国家标准GB 10944-89《自动换刀机床用7∶24圆锥工具柄部40、45和50号圆锥柄》;国际标准ISO 7388/1:1983(40、45和50号工具锥柄)和ISO 7388/3:1986(30号工具锥柄);德国标准分DIN 69871-1:1995(30、40、45、50和60号工具锥柄)和DIN 69871-2(40、45、50、55和60号工具锥柄)两种;日本现行标准为JIS B 6339:1998(30、35、40、45、50、55和60号工具锥柄),用于代替日本工作机械工业会标准MAS-403:1975(40、45、50和60号工具锥柄);美国现行标准为AMSE B5.50-1994(30、40、45、50和60号工具锥柄),用于代替ANSI/AMSE B5.50-1985标准。
手动换刀用7∶24工具锥柄的常见标准有国家标准GB 3837.3-83和国际标准ISO 297-82,以及机械行业标准JB 3381.1-83。
1∶10空心工具锥柄目前已有国家标准GB 19449.1-2004《带有法兰接触面的空心圆锥接口第1部分:柄部—尺寸》。
它等同采用了国际标准ISO 12164-1:2001的内容。
刀具及切削参数选择
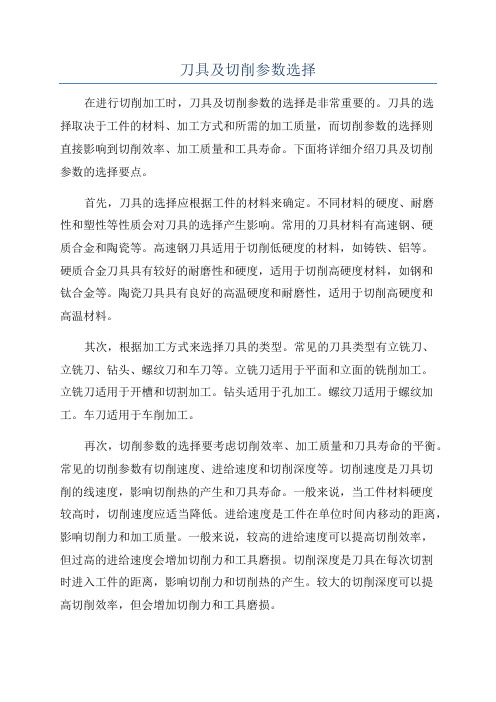
刀具及切削参数选择在进行切削加工时,刀具及切削参数的选择是非常重要的。
刀具的选择取决于工件的材料、加工方式和所需的加工质量,而切削参数的选择则直接影响到切削效率、加工质量和工具寿命。
下面将详细介绍刀具及切削参数的选择要点。
首先,刀具的选择应根据工件的材料来确定。
不同材料的硬度、耐磨性和塑性等性质会对刀具的选择产生影响。
常用的刀具材料有高速钢、硬质合金和陶瓷等。
高速钢刀具适用于切削低硬度的材料,如铸铁、铝等。
硬质合金刀具具有较好的耐磨性和硬度,适用于切削高硬度材料,如钢和钛合金等。
陶瓷刀具具有良好的高温硬度和耐磨性,适用于切削高硬度和高温材料。
其次,根据加工方式来选择刀具的类型。
常见的刀具类型有立铣刀、立铣刀、钻头、螺纹刀和车刀等。
立铣刀适用于平面和立面的铣削加工。
立铣刀适用于开槽和切割加工。
钻头适用于孔加工。
螺纹刀适用于螺纹加工。
车刀适用于车削加工。
再次,切削参数的选择要考虑切削效率、加工质量和刀具寿命的平衡。
常见的切削参数有切削速度、进给速度和切削深度等。
切削速度是刀具切削的线速度,影响切削热的产生和刀具寿命。
一般来说,当工件材料硬度较高时,切削速度应适当降低。
进给速度是工件在单位时间内移动的距离,影响切削力和加工质量。
一般来说,较高的进给速度可以提高切削效率,但过高的进给速度会增加切削力和工具磨损。
切削深度是刀具在每次切割时进入工件的距离,影响切削力和切削热的产生。
较大的切削深度可以提高切削效率,但会增加切削力和工具磨损。
此外,还应考虑冷却润滑剂的选择和使用。
合适的冷却润滑剂可以降低切削热的产生,减小工具磨损,提高加工质量。
综上所述,刀具及切削参数的选择需要考虑工件材料、加工方式和所需加工质量。
合理选择刀具类型和切削参数可以提高切削效率、加工质量和工具寿命。
在实际应用中,还需要根据具体情况进行调整和优化。
- 1、下载文档前请自行甄别文档内容的完整性,平台不提供额外的编辑、内容补充、找答案等附加服务。
- 2、"仅部分预览"的文档,不可在线预览部分如存在完整性等问题,可反馈申请退款(可完整预览的文档不适用该条件!)。
- 3、如文档侵犯您的权益,请联系客服反馈,我们会尽快为您处理(人工客服工作时间:9:00-18:30)。
数控铣床常用刀具的合理选用
数控铣床常用刀具的合理选用
一、前言
数控加工中刀具的选择和切削用量确定是在人机交互状态下完成,要求编程人员必须掌握刀具选
择和切削用量确定的基本原则,在编程时充分考虑数控加工特点,正确选择刀刃具及切削用量。
数控加工技术涉及的范围很广,就应用方面而言,其加工技术的特点
和难点仍在于如何高速、高效率地正确选用数控机床刀具编制出符合产品技术要求的数控加工工艺及程序。
数控加工可以大幅度缩短产品的制造周期,有效的解决机
械产品中复杂、精密、单件小批量、形状多变的零件加工。
二、数控铣床刀具选择
1.刀具的特点及种类
数控铣床加工刀具种类很多,为了适应数控机床高速、高效和自动化程度高的特点,所用刀具正朝着标准化、通用化和模块化的方向发展,主要分为铣削刀具和孔加工刀具两大类。
为了满足高效和特殊的铣削要求,
又发展了各种特殊用途的专用刀具。
1)刀柄结构形式
数控铣床刀具刀柄的结构形式分为模块式与整体式两种。
模块式刀具系统是一种较先进的刀具系统,其每把刀柄都可通过各种系列化的模块组装而成。
针对不同的加工零件和机床,采取不同的组装方案,可获得多种刀柄系列,从而提高刀柄的适应能力和利用率。
整体式刀柄装夹刀具的工作部分与机床上安装定位用的柄部是一体的。
这种刀柄对机床与零件的变换适应能力较差。
为适应零件与机床的变换,用户必须储备各种规格的刀柄,因此刀柄的利用率较低。
数控铣床刀柄与主轴孔的配合锥面采用7:24圆锥柄,并采用相应型式的拉钉,与机床主轴相结合。
锥柄具有不自锁,换刀方便等特点。
刀柄常用的规格有40号、45号和50号。
目前在我国应用较为广泛的有IS07388—1983.MAS403—1982.ANSI/ASME 135.50—1985等,选择时应考虑刀柄规格与机床主轴、机械手相适应。
JT:表示采用国际标准IS07388号加工中心机床用锥柄柄部(带机械手夹持槽);其后数字为相应的ISO锥度号。
BT:表示采用日本标准MAS403号加工中心机床用锥柄柄部(带机械手夹持槽);其后数字为相应的ISO锥度号。
对于高速切削一般采用HSK系列刀柄。
为提高加工效率,应尽可能选用高效率的刀具和刀柄。
选用强力铣夹头刀柄,夹持精度高,可以用来夹持直柄刀具,因卡簧自身夹紧变形小自锁性好,夹紧力大,可以用于强力铣削加工;还可以用于高精度铣铰孔加工,也可通过接杆夹持带孔类刀具。
选用弹簧卡头刀柄,卡簧弹性变形量为1mm,主要夹持小规格铣刀,
如钻头、铣刀、铰刀、丝锥等。
选用模块式工具系统由于其
定位精度高,装卸方便,连接刚性好,具有良好的抗振性,是目前用得较多的一种型式,它由刀柄、中间接杆以及工作头组成。
选用粗镗孔可选用双刃镗刀刀柄,既可提高加工效率,又有利于减少切削振动;对于批量大、加工复杂的典型工件,应尽可能选用复合刀具。
尽管复合刀具与刀柄价格较为昂贵,但在数控机床上采用复合刀具加工,可以使工序集中,把多道工序合并成一道工序、由一把刀具完成,有利于减少加工时间和换刀次数,显著提高生产效率。
2)数控铣床刀具的分类
数控铣床刀具的分类有多种方法,根据刀具结构可分为:
①整体式
②镶嵌式,采用焊接或机夹式连接,机夹式又可分为可转位和不可转位两种
③特殊型式,如复合式刀具,减震式刀具等。
根据制造刀具所用的材料可分为:
①高速钢刀具
②硬质合金刀具:硬质合金根据国际标准ISO分类,把所有牌号分成用颜色标识的六大类,分别以字母P、M、K、N、S、H表示。
P类用于加工长切屑的钢件;M类用于加工不锈钢件;K类用于加工短切屑的铸铁件;N
类用于加工短切屑的非铁材料;s类用于加工难加工材料H类用于加工硬材料。
镀层硬质合金刀具又分为:化学气相沉积CVD和物理气相沉积PVD 两种⑧金刚石刀具④陶瓷刀片材料如氮化硅陶瓷Si3N4,立方氮化硼CBN 从切削工艺上可分为:铣削类刀具(面铣刀、立铣刀、圆鼻刀、球头铣刀、锥度铣刀)孔加工类刀具(麻花钻、铰刀、镗刀、丝锥等)。
为了满足数控机床对刀具耐用、易调、稳定、可换等要求,机夹式可转位刀具得到广泛的应用,占整个数控刀具的40%-50%,金属切除量占总数的80%~90%。
2.数控加工刀具的选择
一刀具选择的总原则:安装调整方便、可靠性好、刚性好、耐用度和精度高。
在满足加工要求的前提下,尽量选择刀柄较短的刀具,以增强加工的刚性。
1)根据工件的表面尺寸选择刀具
选取刀具时,要使刀具的尺寸与被加工件的表面尺寸相适应用。
生产中,加工平面零件周边的轮廓,常采用立铣刀;铣削平面,应选硬质合金刀片铣刀。
加工凸台、凹槽时,选高速钢立铣刀;加工毛坯表面或孔粗加工时,可选用镶硬质合金刀片的玉米铣刀;对一些立体型面和变斜面轮廓外形的加工,选用盘形铣刀、圆鼻刀、平刀做粗加工,选用球头铣刀、环形铣刀、锥形铣刀做精加工。
2)根据工件的表面形状选择刀具
在进行模具加工时,由于球头刀具的端部切削速度为零,因此,为保证加工精度,切削行距一般采用顶端密距,故球头铣刀常用于曲面的精加
工。
而平头刀具在
表面加工质量和切削效率方面都优于球头刀,因此,只要在保证不过切的前提下,无论是曲面的粗加工还是精加工,都应优先选择平头刀。
另外,刀具的耐用度和精度与刀具价格关系极大,必须引起注意的是,在大多数情况下,选择好的刀具虽然增加了刀具成本,但由此带来的加工质量和加工效率的提高,则可以使整个加工成本大大降低。
3)合理安排刀具的排列顺序
在经济型数控机床的加工过程中,由于刀具的磨损、测量和更换多为人工手动进行,占用辅助时间较长,因此,必须合理安排刀具的排列顺序。
一般应遵循以下原则:
①工序集中一次装夹,同一把刀具能完成其进行的所有加工步骤;
②粗精加工的刀具应分开使用;
③先面后孔;
④先进行曲面精加工,后进行二维轮廓精加工;
⑤合理利用数控机床的自动换刀功能,以提高生产效率;
⑥尽量减少刀具数量。