燃油供给系统(英文版)
8.柴油供给系(双语)

2、分类Classification 按其所含重馏分的多少分为重柴油和轻柴油。
3、牌号Trademark : By solidifying point
根据凝点编定。如10号、0号、-10号、-20号等
§6.2
可燃混合气的形成与燃烧室
Combustible mixture forming and combustible chamber
fuel delivery fuel injection 油水分离器 pump advance Water/ fuel separator device
三、柴油Diesel
1、使用性能指标 Parameters of diesel performance
发火性Ignition property——指柴油的自燃能力;16烷值越高,发 火性越好。Spontaneous combustion 蒸发性 Evaporation ——指柴油的汽化能力;其指标由柴油的蒸馏 实验来确定。 粘度Viscosity——决定柴油的流动性;粘度越小,流动性越好。 凝点Solidifying point——指柴油冷却到开始失去流动性的温度。
放油螺塞 Drain plug
中心杆centre rod
四、两级柴油滤清器 Two-stage fuel filter
第二级细滤器 (航空毛毡及纺绸滤芯) Fine filter (Felt-tube element)
第一级粗滤器 (纸质滤芯) Coarse filter (paper element)
二、 组成Composition
燃油供给装臵Diesel supply devices:柴油箱、输油泵、柴油滤 清器、喷油泵、喷油器等。
空气供给装臵Air supply devices:空气滤清器、进气管道。
第2篇燃油供给系统(汽车英语)

课件重点难ຫໍສະໝຸດ 处理领读,找同学读,对重点单词进行归类举例讲解
课前提问
分组到黑板上默写单词,或对课件上的单词找学生回答
教学过程
首先进行课前提问,然后领读生词,讲解生词,进行课堂练习巩固提高。
课堂小结
通过以上教学学生基本能读或写出新单词的含义,能独立完成课堂练习
课外作业
1、单词抄写
2、课后练习。
重点词组彩色字体标注。
引导学生归纳知识要点。
一、领读单词;
二、结合课文讲解生词及课文
1、The electronic fuel injection system can be divided into three basic sub-systems.These are the air induction system, the fuel delivery system, and the electronic control system.
杭州技师学院授课教案首页
(学年第学期)
课程:汽车英语1授课教师:邢春霞序号:6
教学内容
Unit2 text3Electronic Fuel Injection System
授课时间
授课班级
教学要求
与目的
对课文中的生词要会读、能说出其中文含义并对重点单词进行英汉互译。
教学重点难点
重点讲解词汇:
课文分析
独立完成
审批意见
审批人/日期:
教学后记
教学环节
教师活动
教学内容安排
学生活动
【组织教学】
1min
课前准备工作
检查教室环境;检查学生考勤;填写教学日志
检查学生学习用具
准备上课用具
PT燃油供给系统

二、故障应急处理
③电路故障排除后,逆时针拧出燃油直通螺钉直至拧不动为止,恢复原有 供油状态。
摇臂
磁性滤清器
齿轮泵
滤清器
推杆
喷油器
脉冲膜片 减振器
两极调速器
电磁阀
节流轴
油箱
供油凸轮
一、基本组成及工作原理
(二)PT燃油系统工作原理
燃油从油箱流经燃油滤清器被齿轮式输油泵吸入后,以约980kPa的压力流出,
然后经过PT泵内部的稳压器、节流阀、切断阀后,大部分燃油经供油管分 别进入各缸的燃油通道,进入喷油器。
二、故障应急处理
二、故障应急处理
康明斯发动机运行途中突然熄火应如何判断处理? ①将PT泵前端燃油直通螺钉顺时针拧进,直到拧不动为止,此时燃 油不受截断阀门控制,油路处于一种直通状态。
二、故障应急处理
二、故障应急处理
ห้องสมุดไป่ตู้
②再次启动发动机,若发动机能迅速启动,则说明PT泵电磁阀断电后将 燃油关闭,使柴油机断油后熄火。
PT燃油供给系统
一、基本组成及工作原理 PT燃油系统为康明斯柴油发动机所专用,标识字母“PT” 是压力与时间(pressure-time) 的缩写。
一、基本组成及工作原理
(一)PT燃油系统组成
PT燃油系统由 PT燃油泵(简称PT泵)、浮子油箱、燃油滤清器、喷 油器、燃油分配歧管及回油歧管等组成。
燃油供给系统(英文版)

Supply Of Oil FuelsAccurate and complete analyses are difficult to obtain but specifications should confirm that certain parameters are not exceeded. Samples of the oil delivered should be kept for reference.Density of the oil must be given (usually measured at 15°C), since the consignment will be measured by weight. It will also be necessary to know this to adjust centrifuges to give purification.Viscosity is required, to calculate temperatures at which the fuel is treated and injected into the engine.Flash point for the fuel must not be below 60°C, although the actual value need not be stated. This minimum is for safety reasons.All residual fuels will contain contaminants, and to protect the engine some of these must be removed or reduced. Solid contaminants may consist of rust, sand, dust and refinery catalysts (catalytic fines), all of which are abrasives and will cause wear in fuel pumps, injectors, cylinder, liners, piston rings and exhaust valve seats. Liquid contaminants will be salt or fresh water, which may also contain other soluble substances; all of these are corrosive.Fuel to be used is first transferred from storage tanks to a settling tank in which it is heated to allow some water and sludge to settle out by gravity and be drained off. The fuel is then passed through the purification system and discharged to a daily tank.There are usually two daily tanks, used alternately, one in use while the other is being recharged. Settling and service tanks are lagged to conserve heat.A recommended standard of treatment for residual fuel to be used in a large engine requires two centrifuges of adequate capacity, operating in series. The first acts as a purifier to remove water, solubles, sludge etc while the second acts as a clarifier to remove solids. The purifier must be fitted with the correct disc or dam to match the oil density. The oil is heated before purification (max temp 98°C) and the rate of throughput is limited to assist efficientseparation. Both centrifuges must be cleaned frequently. Such systems can operate effectively on oils densities up to 0.99.From the service tank the treated oil is pumped through a pressurised fuel system to the engine. With the oil temperatures necessary for high viscosity fuel, and the possibility that a trace of water may still be present, it is necessary to maintain the engine pump suctions and circulating connections under pressure to inhibit boiling, gasification and cavitation.The oil first passes to the primary or supply pump which raises its pressure to about 4 bar; this pressure is maintained in the circulating returns. The circulating or booster pump draws oil from the primary discharge, raising its pressure to 10/12 bar and delivering it through the heater, viscosity regulator and fine filter to the main engine fuel pumps. The heater reduces the oil’s viscosity for efficient combustion. The temperature required will depend upon the oil quality, but to avoid fouling it should not exceed 150°C. The fine filter is of stainless steel mesh to filter out particles larger than 50 microns (0.05mm), or less for smaller engines. Filters must be changed over and cleaned regularly.In large two-stroke engines the fuel injectors will circulate fuel during the periods they are not actually injecting it to the cylinder. This ensures the system remains fully primed and at uniform temperature. The circulated oil is returned to a buffer or venting tank from which it passes either back to the low pressure part of the system before the circulating pump suction, or into the service tank. The fuel oil system is shown below.All pumps are in duplicate and have safe pressure relief valves fitted. All pipes carrying hot oil must be well lagged and fitted with trace heating if necessary. Fuel pipes must be clipped and supported to reduce stress from vibration.A tank containing diesel oil may be connected to the main heavy fuel system. This will allow flushing with light oil before stopping the engine for long periods of for maintenance.Various safety devices must be included in the system with alarms to detect loss in oil pressure, low tank level etc. Quick closing valves which can be operated from outside the machinery space must be fitted to all tanks and to the main engines. Fuel pumps must have remote switches by which they can be stopped in a emergency.There must be arrangements for venting and draining the system, cleaning strainers etc, but utmost care must be taken. Drain trays and save-alls, where fitted, must be kept clean; all joints must be kept tight with safeguards to prevent the possibility of hot oil spraying on to heated surfaces.Oil contained in tank with open drains should not normally exceed a temperature of 50°C or, if this is lower, may not exceed a temperature 20°C below the flash point of the oil.The ViscothermWhen burning heavy fuel oil in a diesel engine it is necessary to reduce the high viscosity of the fuel to a value at which correct atomisation can take place in the fuel injectors. This will allow intimate mixing of the fuel oil with heated air for ignition and efficient combustion. Viscosity of a fuel may be reduced by raising the temperature and it is passed through a heater to do this. Automatic control of the heater may be regulated either to maintain a constant temperature, or to measure and control the viscosity.It is possible that oils of varying properties are contained within a ship’s bunker tanks or even one tank, when its contents are from a number of different sources. Consequently, it is preferable that the actual viscosity of the fuel is controlled within those limits. In most casts this is regulated to have kinematic between 10 and 15 centistokes at 50°C (that is 50-70 seconds Redwood No. 1, at 100°F).The Viscotherm shown is an instrument which measures fuel oil viscosity at the heater discharge and regulates the heater temperature to control this. It consists of a small gear type pump rotated at a slow but constant speed (40 rpm) and is fitted within the fuel supply close to the heater discharge. The pump draws fuel from the system at a controlled rate and discharges it through a capillary tube. The form of flow within a capillary tube at corresponding speeds is such that the pressure difference between each end of the tube is directly proportional to the viscosity of the oil flowing through it.Pressures at the corresponding points are measured with Bourdon tubes and compared to read as viscosity. In addition these pressures are fed to a differential pressure transmitter which can automatically operate the heater control to maintain fuel viscosity within close limits.All parts of the instrument are of stainless steel. In the event of a failure of this control an oil bypass valve is included in the system and the temperature may then be controlled by hand or by a thermostat.Combustion of FuelThe general indications of good combustion are similar in any operating diesel engine; a clear exhaust, power produced and with balanced exhaust temperatures normal for the throttle setting. There should be no uneven running, knocking from cylinders or the fuel system.Viscosity, or resistance to flow, in a fuel oil is important when considering combustion. It must be low enough to ensure correct atomisation at the fuel injector. Since viscosity reduces as temperature is increased, it will be necessary to heat heavy fuel oil to reduce its viscosity to about 15 cSt at 50°C before atomisation for combustion.Atomisation is the splitting up of the fuel into very small droplets by the fuel injector forcing fuel at high pressure through small atomiser holes. The droplet size will depend upon the size of holes and the pressure difference between fuel pump discharge and that of the compressed air in the combustion chamber, and consequently the size of droplets may vary over the whole injection period. Atomised droplets have a high surface to mass ratio giving good heat transfer from the hot compressed air in the cylinder causing rapid evaporation andmixing.Penetration refers to the distance the oil droplets travel into the combustion space before mixing with the air and igniting. This will depend upon the droplet size (atomisation), velocity leaving the injector and the conditions within the combustion chamber. It is desirable that fuel should penetrate into the whole of the combustion space for good mixing, but droplets should not impinge on the internal surfaces before burning. The number of atomiser holes and their position will decide the spray pattern.Turbulence is the movement of compressed air and fuel within the combustion space before combustion occurs. This may have several causes. Swirl is imparted to the air during its entry at scavenge ports. It may be further agitated by the fuel spray pattern and the shape and movement of the piston crown. Turbulence will improve the mixing of fuel and air for effective and rapid combustion. It is particularly desirable for rapid combustion of heavy fuels in medium or higher speed engines.Compression Ignition is the term used to describe the combustion in diesel engines and they are often referred to as compression ignition engines. The combustion process may be considered as three consecutive phases. In phase one the atomised oil droplets emitted from the fuel valve nozzle into the combustion space at the start of injection will evaporate and mix with hot, compressed air and some chemical changes will also occur. The mixture will reach an ignitable condition and spontaneous combustion will commence. The time elapsed during this phase it termed the ignition delay or ignition lag.In phase two the ignition and start of combustion will set up a flame front which will accelerate through the chamber, enveloping and burning all the other droplets present, causing a very rapid generation of heat with a corresponding rise in pressure and temperature.During the ignition delay, the injector continued to inject fuel and, if this has built up a sufficient quantity, the rapid combustion and pressure rise will be quite violent, causing detonation, the shock loading creating a noise termed diesel knock.Following the rapid pressure rise in phase two, hot, turbulent conditions existing in the combustion chamber will ignite and burn the remainder of the measured fuel charge as it is injected. This is phase three; it is termed the controlled part of the combustion process as pressure is regulated by the rate at which fuel continues to be delivered. The cylinder pressure may start to reduce as the piston moves down after passing over top centre.Ignition quality of a fuel is the term used to denote the ignition delay, combustion characteristics and tendency to cause knock. It depends mainly upon the form of the hydrocarbon compounds in the fuel and no precise unit has been derived to measure this.The most usual measure of ignition quality of distillate fuels is the Cetane number. This is found by comparison of the ‘knock producing’ properties to those of mixtures containing an equivalent percentage of Cetane when burnt in a test engine. A high Centane number indicates a short ignition delay. Cetane numbers are not quoted in normal fuel specifications or analyses. Slow speed, two-stroke engines can operate efficiently of fuels down to Cetane number of about 24 but medium speed, four-stroke engines normally require a figure above 34; high speed engines need higher figures. Another measure which is similar to Cetane number but found from different parameters of the fuel, is termed its diesel index.For residual or blended fuels the ignition can be expressed as a CCAI value (calculated carbon aromacity index) or CII (calculated ignition index). The lower the CCAI value, the better the ignition quality. A limiting figure of 870 is suggested. These units take the viscosity into consideration.The ignition quality of a fuel is particularly important for each of starting an engine, or when operating at reduced power for long periods. It can be improved by increasing the compression ratio of the engine or by pre-heating the scavenge air. There will be design or operational limits to both of these.Variable Ignition Timing (VIT). If an engine operates for long periods at reduced power or speed, the residual heat in the main components of the combustion chamber will decrease, causing a lower air temperature after combustion. This will lead to an increase in the ignition delay of injected fuel, which will cause knocking or ‘rough running’ in the engine, with consequent damage from shock loads and poor combustion. This problem can be reduced by the use of variable ignition timing to advance the start of injection, allowing for the longer delay but maintaining ignition timing and the same peak pressure. In large, two-stroke engines, variable ignition timing is automatically superimposed on the normal fuel pump setting from the engine governor. Additional linkage from the governor will advance each pump setting over the range of lower speeds. Fuel pumps are designed to carry out necessary adjustment while the engine is running. This control can also be manually regulated to advance normal governor settings if it is known that fuel with low ignition quality is to be used.In medium speed engines, variable ignition timing is built in by shaping the profile of the pump plunger to give an earlier start of injection at lower fuel settings. Manual adjustment, advancing the timing for low ignition quality fuel, is fitted on some engines.Pilot Injection This is a system by which fuels with low ignition quality can be burnt smoothly and efficiently, even in medium or high speed engines. A small ‘pilot’ charge of finely atomised fuel is briefly injected very early during compression. This small charge is heated and vaporised, passing through its delay period and igniting just before the main charge of fuel is injected. Combustion of the pilot charge will cause high temperature and turbulence in the combustion space. This together with its flame front will cause the main charge of fuel to ignite and burn smoothly as it is injected. In this manner the violent pressure rise usual with these fuels is avoided. Combustion is efficient and the peak pressure is limited.Pilot injection can be implemented by two different methods. In the first case two separate injectors are fitted to each unit; both must be correctly timed. The pilot injector has fine nozzle holes to atomise the fuel at a moderate injection pressure and is timed to commence before the main valve. The main injector is situated in a position to give an effective fuel spray and it injects the main, measured charge at normal fuel injection pressure. This system with two valves is sometimes referred to as twin injection.The alternative method of pilot injection has one injector fitted to each unit. This injector is designed to inject the pilot charge with fine atomisation and must also inject the main fuel charge. To do this it requires variable nozzle holes and a two stage needle valve lift. Fuel pump drive for this system may require specially shaped cam profiles.Electronic Injection was a system introduced by MAN engines that electronically controlled fuel injection. The heart of the electronic injection system is a micro-processor to which the actual engine speed and crankshaft position are transmitted as output signals. When the desired speed is compared with the actual speed, the processor automatically retrieves the values of injection timing and pressure for any load under normal operating conditions. In the event of deviations from normal operating conditions additional signals are transmitted to the microprocessor either manually or by appropriate temperature and pressure sensors. The result is an engine operating at optimum injection pressure and timing at all times. Adjustments to the system during operation are possible.Corrections can be made for: adapting the injection system to varying conditions such as ballast voyages, bad weather; matching the engine to different fuels, ignition lag, cetane numbers, etc; readjusting for operation in the tropics or in winter; controlling the injection characteristics of individual cylinders, such as when running in; reducing the minimum slow running speed, such as when in canals.The most noticeable feature of a KEZ type engine with electronic injection, is the absence of a camshaft and individual fuel pumps. The fuel is delivered to high-pressure accumulator by normal fuel injection plunger pumps driven by gears and cams from the crankshaft. These pumps are located above the thrust bearing and, depending on the size and cylinder number of the engine, two or more of these pumps are used. To safeguard against failure of a pump or a pressure pipe, two independent fuel delivery pipes are placed between the high-pressure pumps and accumulator.The high-pressure accumulator generates a buffer volume to prevent the pressure in the injection valve from dropping below an acceptable limit when the fuel is withdrawn during injection into the cylinder. For the electronically controlled injections systems, metering of the fuel volume for one cylinder is not affected by limiting the delivery volume per stroke of the injection pump plunger as in conventional systems, but by limiting the duration of injection. This is initiated by an electronic controller, i.e. by a low voltage signal which controls the opening and closing action of an electro-hydraulic servo valve. The electrohydraulic valve is actuated by oil under pressure from two pumps and an air cushion-type accumulator.Sequential control ensures that according to the engine firing sequence, the correct engine cylinder is selected in the proper crank angel range and that the electronically controlled injection valve is actuated at the exact point of injection.For engine starting and reversing, the correct injection timing is linked with the electronically controlled starting air valve. Since electronically controlled starting valves have no time delay between the switching pulse and opening of the air valve, and since there are no flow losses, due to the elimination of the control air pipes, the starting air requirements are reduced in comparison with the former conventional air start system.The constant pressure maintained during fuel injection with the electronically controlled fuelinjection system, and the fact that the injection pressure can easily be matched to each load condition, lead to lower fuel consumption rates over the entire load range. It also means satisfactory operation at very slow speeds, which contributes favourably to the manoeuvrability of a vessel, a K3EZ 50/105C/CL engine on the test bed was operated at a dead slow speed of 30 rev/min, which had never been achieved before. The full load speed is 183 rev/min.Although this system never caught on in the early 1980’s with the advances in electronics it could easily returns in the near future.。
汽车实用英语项目二 发动机燃油供给系认识
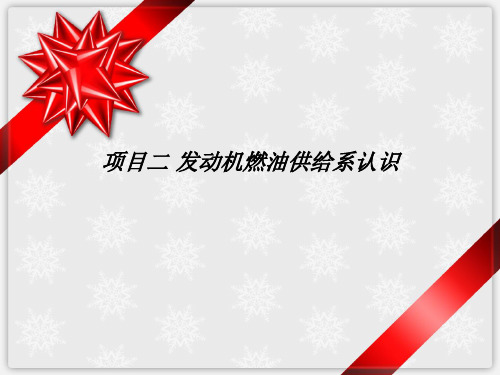
Components cognition
Components cognition
Components cognition
Proper Names
Proper Names
Text learning-example
• Project 2 Acquaintance with engine fuel system • Introduction • The fuel system has the job of supplying a combustible mixture of air and fuel to the engine. There are two different types of petrol fuel systems: systems with a carburetor and systems with electronic fuel injection (EFI). Carburetor fuel systems and EFI systems are designed to deliver the fuel mixture to the engine in a combustible form, but each system does it in a different way.[1] One basic difference is that carburetors atomize the fuel, and injectors spray the fuel. • Carburetor fuel system • The conventional carburetor fuel system consists of the fuel tank, fuel pump, fuel filter, carburetor, fuel lines, intake manifold and air cleaner (shown as Figure 2-1). As well as these, the exhaust system is sometimes considered to be a part of the fuel system.
燃料供给系统英文版
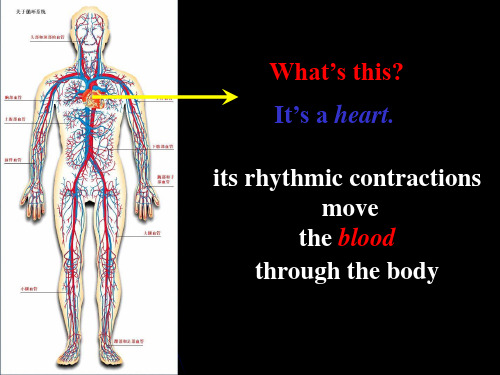
store vt.储存 The gasoline is stored in the gasoline tank. carry vt.运送 The fuel lines carry the gasoline from the tank to the carburetor. remove vt.消除 The gasoline filter removes impurities from the gasoline. draw vt.吸取
gasoline tank
air filter
gasoline filter
carburetor (mix)
gasoline pump cylinder fuel lines
intake manifold
The fuel system has anther job of expelling the exhaust gas out of the cylinder.
diesel engine
gasoline engine spark-ignition engine
The Four-stroke Spark-ignition Engine Cycle
compression intake power
exhaust
What is sucked into the cylinder?
分配油管 油压调节器 电控单元 氧传感器 喷油器
节气门位置传感器
3.ECU (electronic control unit)
4.oxygen ['ɔksidʒən] sensor ['sensə]
5.injector [in'dʒektə]
6.throttle['θrɔtl] position [pə'ziʃən] sensor
车辆工程外文翻译---内燃机的燃油供应系统
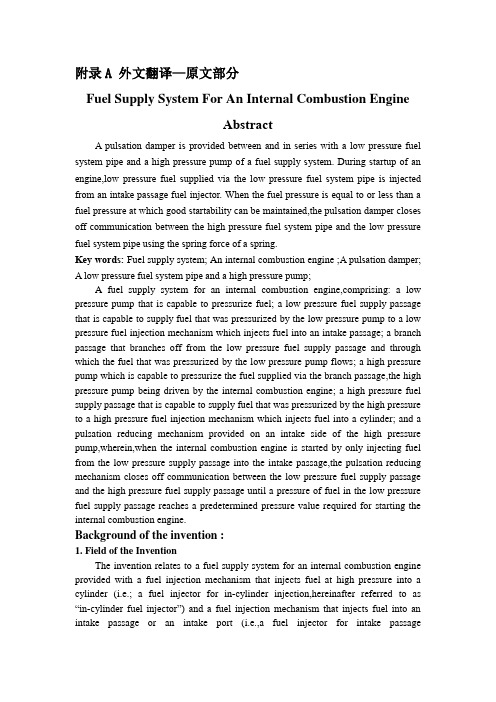
附录A 外文翻译—原文部分Fuel Supply System For An Internal Combustion EngineAbstractA pulsation damper is provided between and in series with a low pressure fuel system pipe and a high pressure pump of a fuel supply system. During startup of an engine,low pressure fuel supplied via the low pressure fuel system pipe is injected from an intake passage fuel injector. When the fuel pressure is equal to or less than a fuel pressure at which good startability can be maintained,the pulsation damper closes off communication between the high pressure fuel system pipe and the low pressure fuel system pipe using the spring force of a spring.Keywords: Fuel supply system; An internal combustion engine;A pulsation damper;A low pressure fuel system pipe and a high pressure pump;A fuel supply system for an internal combustion engine,comprising: a low pressure pump that is capable to pressurize fuel; a low pressure fuel supply passage that is capable to supply fuel that was pressurized by the low pressure pump to a low pressure fuel injection mechanism which injects fuel into an intake passage; a branch passage that branches off from the low pressure fuel supply passage and through which the fuel that was pressurized by the low pressure pump flows; a high pressure pump which is capable to pressurize the fuel supplied via the branch passage,the high pressure pump being driven by the internal combustion engine; a high pressure fuel supply passage that is capable to supply fuel that was pressurized by the high pressure to a high pressure fuel injection mechanism which injects fuel into a cylinder; and a pulsation reducing mechanism provided on an intake side of the high pressure pump,wherein,when the internal combustion engine is started by only injecting fuel from the low pressure supply passage into the intake passage,the pulsation reducing mechanism closes off communication between the low pressure fuel supply passage and the high pressure fuel supply passage until a pressure of fuel in the low pressure fuel supply passage reaches a predetermined pressure value required for starting the internal combustion engine.Background of the invention :1. Field of the InventionThe invention relates to a fuel supply system for an internal combustion engine provided with a fuel injection mechanism that injects fuel at high pressure into a cylinder (i.e.; a fuel injector for in-cylinder injection,hereinafter referred to as “in-cylinder fuel injector”) and a fuel injection mechanism that injects fuel into an intake passage or an intake port (i.e.,a fuel injector for intake passageinjection,hereinafter referred to as “intake passage fuel injector”). More particularly,the invention relates to a fuel supply system that can improve startability of an internal combustion engine.2. Description of the Related ArtA gasoline engine is known which is provided with a fast fuel injection valve for injecting fuel into a combustion chamber of the engine (i.e.,an in-cylinder fuel injector) and a second fuel injection valve for injecting fuel into an intake passage (i.e.,an intake passage fuel injector),and divides the injected fuel between the in-cylinder fuel injector and the intake passage fuel injector according to the engine speed and engine load. Also,a direct injection gasoline engine is also known which is provided with only a fuel injection valve for injecting fuel into the combustion chamber of the engine (i.e.,an in-cylinder fuel injector). In a high pressure fuel system that includes an in-cylinder fuel injector,fuel of which the pressure has been increased by a high pressure fuel pump is supplied to the in-cylinder fuel injector via a delivery pipe. The in-cylinder fuel injector then injects the high pressure fuel into the combustion chamber of each cylinder of the internal combustion engine.In addition,a diesel engine is also known which has a common rail type fuel injection system. In this common rail type fuel injection system,fuel which has been increased in pressure by a high pressure fuel pump is stored in a common rail. The high pressure fuel is then injected into the combustion chamber of each cylinder of the diesel engine from the common rail by opening and closing an electromagnetic valve.In order to increase the pressure of (i.e.,pressurize) the fuel in this kind of internal combustion engine,a high pressure fuel pump is provided which is driven by a cam provided on a driveshaft that is connected to a crankshaft of the internal combustion engine.Japanese Patent Application Publication No. JP-A-2005-139923 describes a high pressure fuel supply system for an internal combustion engine that can reduce vibrational noise when only a small amount of fuel is required by the internal combustion engine,such as during idling,while being able to deliver the necessary amount of fuel over the entire operating range of the internal combustion engine. This high pressure fuel supply system for an internal combustion engine has a two single plunger type high pressure fuel pumps each of which have a spill valve that spills fuel drawn into a pressurizing chamber that is divided by a cylinder and a plunger that moves back and forth in the cylinder,from that pressurizing chamber. When fuel is pressurized and delivered from the pressurizing chamber to the high pressure fuel system,the amount of fuel delivered is adjusted by controlling the spill valve open andclosed. One of these high pressure fuel pumps is a first high pressure fuel pump in which the lift amount of the plunger is small and the other high pressure fuel pump is a second high pressure fuel pump in which the lift amount of the plunger is large. In addition to these two high pressure fuel pumps,the high pressure fuel supply system for an internal combustion engine also includes control means. The control means controls the spill valve of each high pressure fuel pump according to the amount of fuel required by the internal combustion engine,such that fuel is pressurized and delivered using only the first high pressure fuel pump when the amount of required fuel is small,and fuel is pressurized and delivered using at least the second high pressure fuel pump when the amount of required fuel is large.According to this high pressure fuel supply system for an internal combustion engine,of the two high pressure fuel pumps,the first high pressure fuel pump has a plunger with a small lift amount so the rate of pressure increase is small and a large amount of water hammer is also self-suppressed. That is,with the high pressure fuel supply system,the vibrational noise produced when the required fuel quantity is small can be preferably reduced by controlling the spill valve of each of the high pressure fuel pumps so that only the first high pressure fuel pump is used when the amount of fuel required for the internal combustion engine is small such as during idling. On the other hand,the second high pressure fuel pump has a plunger with a large lift amount so pressurizing and delivering fuel using at least this second high pressure fuel pump also makes it possible to deliver the required fuel quantity when the amount of fuel required by the internal combustion engine increases to the point where it can no longer be delivered by the first high pressure fuel pump alone. That is,providing two high pressure fuel pumps having plungers with different lift amounts in this way enables the required amount of fuel to be delivered throughout the entire operating range of the internal combustion engine,while reducing vibrational noise when the amount of required fuel is small.In Japanese Patent Application Publication No. JP-A-2005-139923,the high pressure fuel supply system for a V-type 8 cylinder internal combustion engine having an in-cylinder fuel injector in each cylinder is provided with a high pressure fuel pump for each bank. Tip ends that branch off from a low pressure fuel passage which is connected to the fuel tank are connected to galleries of these high pressure fuel pumps. For each bank,a pulsation damper is provided midway between the branch portion of the low pressure fuel passage and the portion that connects with the gallery. This pulsation damper suppresses the pulsation in the fuel pressure in the low pressurefuel passage when the high pressure fuel pump is operating. At engine startup in this kind of a direct injection engine having only an in-cylinder fuel injector,fuel is unable to be delivered by the high pressure fuel pump until the engine turns over. Therefore,low pressure fuel is delivered by a feed pump to the fuel injection for in-cylinder injection. Therefore,the pulsation damper is designed to provide communication between the high pressure pipe system and the low pressure pipe system. For example,FIG. 6 is a sectional view of such a pulsation damper 215 ,FIG.7 is a sectional view taken along line VII-VII of FIG. 6 ,and FIG. 8 is a sectional view taken along line VIII-VIII of FIG. 7. As shown in FIGS. 6 to 8,grooves 223 A,223 B,223 C,and223 D are provided in an end face (i.e.,the upper surface in FIG. 8) that abuts against a contacting member 226 A of the pulsation damper 215 . Therefore,when the feed pressure is low,the spring 226 D presses the contacting member 226 A against the upper surface of the member that forms the inlet 222 and the outlet 224 . In this way,the structure is such that even if pressure is applied by the spring 226 D,the grooves 223 A,223 B,223 C,and223 D enable fuel delivered from the inlet 222 (i.e.,the feed pump side) to flow into the outlet 224 (i.e.,the high pressure fuel pump side) as shown by the dotted line in FIG. 8. On the other hand,as described above,an engine is known which includes,for each cylinder,an in-cylinder fuel injector that injects fuel into a combustion chamber of the engine and an intake passage fuel injector that injects fuel into an intake passage. In this engine,fuel is injected divided between the in-cylinder fuel injector and the intake passage fuel injector according to the engine speed and the load on the internal combustion engine. This engine is also providedwith the pulsation damper shown in FIGS. 6 to 8.However,in this kind of engine,the following problems occur when starting the engine by injecting fuel with an intake passage fuel injector. When fuel is delivered by a feed pump at engine startup,the volume of pipe that needs to be charged with fuel becomes significantly larger. That is,when the engine is started with fuel injected from the intake passage fuel injector,despite the fact that fuel can be delivered to the intake passage fuel injector with the feed pump by simply charging only the low pressure pipe with fuel,the pulsation damper is structured such that the high pressure pipe system and the low pressure pipe system are communicated or open to one another. Therefore,fuel is unable to be delivered to the intake passage fuel injector bythe feed pump unless both the low pressure pipe and the high pressure pipe are charged with fuel. As a result,it takes time for the feed pressure to rise,thereby adversely affecting startability (i.e.,increasing the start time).Summary of the inventionThis invention thus provides a fuel supply system for an internal combustion engine,which is capable of improving startability of an internal combustion engine that includes a fuel injection mechanism for injecting fuel at high pressure into a cylinder (i.e.,in-cylinder fuel injector) and a fuel injecting mechanism for injecting fuel into an intake passage or an intake port (i.e.,an intake passage fuel injector).A first aspect of the invention relates to a fuel supply system for an internal combustion engine which includes a low pressure fuel supply passage that supplies fuel that was pressurized by a low pressure pump to a low pressure fuel injection mechanism which injects fuel into an intake passage; a branch passage that branches off from the low pressure fuel supply passage and supplies fuel to a high pressure pump that is driven by the internal combustion engine; a high pressure fuel supply passage that supplies fuel that was pressurized by the high pressure pump to a high pressure fuel injection mechanism which injects fuel into a cylinder; and a pulsation reducing mechanism provided on the intake side of the high pressure pump. The pulsation reducing mechanism closes off communication between the low pressure fuel supply passage and the high pressure fuel supply passage when a pressure of fuel in the low pressure fuel supply passage is lower than a predetermined value.According to this first aspect,the high pressure pump which is driven by the internal combustion engine does not operate during startup of the internal combustion engine. In this case,the internal combustion engine is started by injecting fuel that has been pressurized by the low pressure pump from the low pressure fuel injection mechanism via the low pressure fuel supply passage. In this case,during startup of the internal combustion engine when the pressure of fuel in the low pressure fuel supply passage is low,the pulsation reducing mechanism closes off communication between the low pressure fuel supply passage and the high pressure fuel supply passage. Therefore,fuel can be delivered to the low pressure fuel injection mechanism simply by charging the low pressure fuel supply passage with fuel using the low pressure pump. Accordingly,there is no need to charge the high pressure fuel supply passage with fuel using the low pressure pump so the low pressure fuel supply passage and the branch passage that provides communication between the low pressure fuel supply passage and the high pressure pump can be charged with fuel quickly,and fuel can be quickly injected from the low pressure fuel injection mechanism. As a result,startability of an internal combustion engine provided with a fuel injectionmechanism that injects fuel at high pressure into the cylinder and a fuel injection mechanism that injects fuel into the intake passage or intake port can be improved.附录B 外文翻译—译文部分内燃机的燃油供应系统摘要在低压燃油供应系统管道和燃油供应系统的高压泵之间有一系列的有节奏的脉动衰减节气阀。
Lesson 8 Systems of Marine Diesel Engine

Lesson 8 Systems of Marine Diesel Engine船用柴油机系统Fuel oil systemThe fuel oil system for a diesel engine can be considered in two parts—the fuel supply and the fuel injection systems. 柴油机的燃油系统可分为燃油供应系统和燃油喷射系统两部分。
Fuel supply deals with the provision of fuel oil suitable for use by the injection system.燃油供应是指提供适合喷射系统使用的燃油。
A.Fuel oil supply for a two-stroke diesel engine二冲程柴油机的燃油供给A slow-speed two-stroke diesel is usually arranged to operate continuously on heavy fuel and have available a diesel oil supply for maneuvering conditions. 低速二冲程柴油机通常被设计为持续运行使用重油,同时,在机动操纵条件下也可使用柴油。
In the system shown in Fig. 8-1, the oil is stored in tanks in the double bottom from which it is pumped to a settling tank and heated. 在图8-1所示的系统中,燃油被储存在双层底舱中,从这里被泵泵送至沉淀柜并加热。
After passing through centrifuges then cleaned, heated oil is pumped to a daily service tank. 经过分油机离心分离后,干净的热油被泵送到日用油柜。
- 1、下载文档前请自行甄别文档内容的完整性,平台不提供额外的编辑、内容补充、找答案等附加服务。
- 2、"仅部分预览"的文档,不可在线预览部分如存在完整性等问题,可反馈申请退款(可完整预览的文档不适用该条件!)。
- 3、如文档侵犯您的权益,请联系客服反馈,我们会尽快为您处理(人工客服工作时间:9:00-18:30)。
Supply Of Oil FuelsAccurate and complete analyses are difficult to obtain but specifications should confirm that certain parameters are not exceeded. Samples of the oil delivered should be kept for reference.Density of the oil must be given (usually measured at 15°C), since the consignment will be measured by weight. It will also be necessary to know this to adjust centrifuges to give purification.Viscosity is required, to calculate temperatures at which the fuel is treated and injected into the engine.Flash point for the fuel must not be below 60°C, although the actual value need not be stated. This minimum is for safety reasons.All residual fuels will contain contaminants, and to protect the engine some of these must be removed or reduced. Solid contaminants may consist of rust, sand, dust and refinery catalysts (catalytic fines), all of which are abrasives and will cause wear in fuel pumps, injectors, cylinder, liners, piston rings and exhaust valve seats. Liquid contaminants will be salt or fresh water, which may also contain other soluble substances; all of these are corrosive.Fuel to be used is first transferred from storage tanks to a settling tank in which it is heated to allow some water and sludge to settle out by gravity and be drained off. The fuel is then passed through the purification system and discharged to a daily tank.There are usually two daily tanks, used alternately, one in use while the other is being recharged. Settling and service tanks are lagged to conserve heat.A recommended standard of treatment for residual fuel to be used in a large engine requires two centrifuges of adequate capacity, operating in series. The first acts as a purifier to remove water, solubles, sludge etc while the second acts as a clarifier to remove solids. The purifier must be fitted with the correct disc or dam to match the oil density. The oil is heated before purification (max temp 98°C) and the rate of throughput is limited to assist efficientseparation. Both centrifuges must be cleaned frequently. Such systems can operate effectively on oils densities up to 0.99.From the service tank the treated oil is pumped through a pressurised fuel system to the engine. With the oil temperatures necessary for high viscosity fuel, and the possibility that a trace of water may still be present, it is necessary to maintain the engine pump suctions and circulating connections under pressure to inhibit boiling, gasification and cavitation.The oil first passes to the primary or supply pump which raises its pressure to about 4 bar; this pressure is maintained in the circulating returns. The circulating or booster pump draws oil from the primary discharge, raising its pressure to 10/12 bar and delivering it through the heater, viscosity regulator and fine filter to the main engine fuel pumps. The heater reduces the oil’s viscosity for efficient combustion. The temperature required will depend upon the oil quality, but to avoid fouling it should not exceed 150°C. The fine filter is of stainless steel mesh to filter out particles larger than 50 microns (0.05mm), or less for smaller engines. Filters must be changed over and cleaned regularly.In large two-stroke engines the fuel injectors will circulate fuel during the periods they are not actually injecting it to the cylinder. This ensures the system remains fully primed and at uniform temperature. The circulated oil is returned to a buffer or venting tank from which it passes either back to the low pressure part of the system before the circulating pump suction, or into the service tank. The fuel oil system is shown below.All pumps are in duplicate and have safe pressure relief valves fitted. All pipes carrying hot oil must be well lagged and fitted with trace heating if necessary. Fuel pipes must be clipped and supported to reduce stress from vibration.A tank containing diesel oil may be connected to the main heavy fuel system. This will allow flushing with light oil before stopping the engine for long periods of for maintenance.Various safety devices must be included in the system with alarms to detect loss in oil pressure, low tank level etc. Quick closing valves which can be operated from outside the machinery space must be fitted to all tanks and to the main engines. Fuel pumps must have remote switches by which they can be stopped in a emergency.There must be arrangements for venting and draining the system, cleaning strainers etc, but utmost care must be taken. Drain trays and save-alls, where fitted, must be kept clean; all joints must be kept tight with safeguards to prevent the possibility of hot oil spraying on to heated surfaces.Oil contained in tank with open drains should not normally exceed a temperature of 50°C or, if this is lower, may not exceed a temperature 20°C below the flash point of the oil.The ViscothermWhen burning heavy fuel oil in a diesel engine it is necessary to reduce the high viscosity of the fuel to a value at which correct atomisation can take place in the fuel injectors. This will allow intimate mixing of the fuel oil with heated air for ignition and efficient combustion. Viscosity of a fuel may be reduced by raising the temperature and it is passed through a heater to do this. Automatic control of the heater may be regulated either to maintain a constant temperature, or to measure and control the viscosity.It is possible that oils of varying properties are contained within a ship’s bunker tanks or even one tank, when its contents are from a number of different sources. Consequently, it is preferable that the actual viscosity of the fuel is controlled within those limits. In most casts this is regulated to have kinematic between 10 and 15 centistokes at 50°C (that is 50-70 seconds Redwood No. 1, at 100°F).The Viscotherm shown is an instrument which measures fuel oil viscosity at the heater discharge and regulates the heater temperature to control this. It consists of a small gear type pump rotated at a slow but constant speed (40 rpm) and is fitted within the fuel supply close to the heater discharge. The pump draws fuel from the system at a controlled rate and discharges it through a capillary tube. The form of flow within a capillary tube at corresponding speeds is such that the pressure difference between each end of the tube is directly proportional to the viscosity of the oil flowing through it.Pressures at the corresponding points are measured with Bourdon tubes and compared to read as viscosity. In addition these pressures are fed to a differential pressure transmitter which can automatically operate the heater control to maintain fuel viscosity within close limits.All parts of the instrument are of stainless steel. In the event of a failure of this control an oil bypass valve is included in the system and the temperature may then be controlled by hand or by a thermostat.Combustion of FuelThe general indications of good combustion are similar in any operating diesel engine; a clear exhaust, power produced and with balanced exhaust temperatures normal for the throttle setting. There should be no uneven running, knocking from cylinders or the fuel system.Viscosity, or resistance to flow, in a fuel oil is important when considering combustion. It must be low enough to ensure correct atomisation at the fuel injector. Since viscosity reduces as temperature is increased, it will be necessary to heat heavy fuel oil to reduce its viscosity to about 15 cSt at 50°C before atomisation for combustion.Atomisation is the splitting up of the fuel into very small droplets by the fuel injector forcing fuel at high pressure through small atomiser holes. The droplet size will depend upon the size of holes and the pressure difference between fuel pump discharge and that of the compressed air in the combustion chamber, and consequently the size of droplets may vary over the whole injection period. Atomised droplets have a high surface to mass ratio giving good heat transfer from the hot compressed air in the cylinder causing rapid evaporation andmixing.Penetration refers to the distance the oil droplets travel into the combustion space before mixing with the air and igniting. This will depend upon the droplet size (atomisation), velocity leaving the injector and the conditions within the combustion chamber. It is desirable that fuel should penetrate into the whole of the combustion space for good mixing, but droplets should not impinge on the internal surfaces before burning. The number of atomiser holes and their position will decide the spray pattern.Turbulence is the movement of compressed air and fuel within the combustion space before combustion occurs. This may have several causes. Swirl is imparted to the air during its entry at scavenge ports. It may be further agitated by the fuel spray pattern and the shape and movement of the piston crown. Turbulence will improve the mixing of fuel and air for effective and rapid combustion. It is particularly desirable for rapid combustion of heavy fuels in medium or higher speed engines.Compression Ignition is the term used to describe the combustion in diesel engines and they are often referred to as compression ignition engines. The combustion process may be considered as three consecutive phases. In phase one the atomised oil droplets emitted from the fuel valve nozzle into the combustion space at the start of injection will evaporate and mix with hot, compressed air and some chemical changes will also occur. The mixture will reach an ignitable condition and spontaneous combustion will commence. The time elapsed during this phase it termed the ignition delay or ignition lag.In phase two the ignition and start of combustion will set up a flame front which will accelerate through the chamber, enveloping and burning all the other droplets present, causing a very rapid generation of heat with a corresponding rise in pressure and temperature.During the ignition delay, the injector continued to inject fuel and, if this has built up a sufficient quantity, the rapid combustion and pressure rise will be quite violent, causing detonation, the shock loading creating a noise termed diesel knock.Following the rapid pressure rise in phase two, hot, turbulent conditions existing in the combustion chamber will ignite and burn the remainder of the measured fuel charge as it is injected. This is phase three; it is termed the controlled part of the combustion process as pressure is regulated by the rate at which fuel continues to be delivered. The cylinder pressure may start to reduce as the piston moves down after passing over top centre.Ignition quality of a fuel is the term used to denote the ignition delay, combustion characteristics and tendency to cause knock. It depends mainly upon the form of the hydrocarbon compounds in the fuel and no precise unit has been derived to measure this.The most usual measure of ignition quality of distillate fuels is the Cetane number. This is found by comparison of the ‘knock producing’ properties to those of mixtures containing an equivalent percentage of Cetane when burnt in a test engine. A high Centane number indicates a short ignition delay. Cetane numbers are not quoted in normal fuel specifications or analyses. Slow speed, two-stroke engines can operate efficiently of fuels down to Cetane number of about 24 but medium speed, four-stroke engines normally require a figure above 34; high speed engines need higher figures. Another measure which is similar to Cetane number but found from different parameters of the fuel, is termed its diesel index.For residual or blended fuels the ignition can be expressed as a CCAI value (calculated carbon aromacity index) or CII (calculated ignition index). The lower the CCAI value, the better the ignition quality. A limiting figure of 870 is suggested. These units take the viscosity into consideration.The ignition quality of a fuel is particularly important for each of starting an engine, or when operating at reduced power for long periods. It can be improved by increasing the compression ratio of the engine or by pre-heating the scavenge air. There will be design or operational limits to both of these.Variable Ignition Timing (VIT). If an engine operates for long periods at reduced power or speed, the residual heat in the main components of the combustion chamber will decrease, causing a lower air temperature after combustion. This will lead to an increase in the ignition delay of injected fuel, which will cause knocking or ‘rough running’ in the engine, with consequent damage from shock loads and poor combustion. This problem can be reduced by the use of variable ignition timing to advance the start of injection, allowing for the longer delay but maintaining ignition timing and the same peak pressure. In large, two-stroke engines, variable ignition timing is automatically superimposed on the normal fuel pump setting from the engine governor. Additional linkage from the governor will advance each pump setting over the range of lower speeds. Fuel pumps are designed to carry out necessary adjustment while the engine is running. This control can also be manually regulated to advance normal governor settings if it is known that fuel with low ignition quality is to be used.In medium speed engines, variable ignition timing is built in by shaping the profile of the pump plunger to give an earlier start of injection at lower fuel settings. Manual adjustment, advancing the timing for low ignition quality fuel, is fitted on some engines.Pilot Injection This is a system by which fuels with low ignition quality can be burnt smoothly and efficiently, even in medium or high speed engines. A small ‘pilot’ charge of finely atomised fuel is briefly injected very early during compression. This small charge is heated and vaporised, passing through its delay period and igniting just before the main charge of fuel is injected. Combustion of the pilot charge will cause high temperature and turbulence in the combustion space. This together with its flame front will cause the main charge of fuel to ignite and burn smoothly as it is injected. In this manner the violent pressure rise usual with these fuels is avoided. Combustion is efficient and the peak pressure is limited.Pilot injection can be implemented by two different methods. In the first case two separate injectors are fitted to each unit; both must be correctly timed. The pilot injector has fine nozzle holes to atomise the fuel at a moderate injection pressure and is timed to commence before the main valve. The main injector is situated in a position to give an effective fuel spray and it injects the main, measured charge at normal fuel injection pressure. This system with two valves is sometimes referred to as twin injection.The alternative method of pilot injection has one injector fitted to each unit. This injector is designed to inject the pilot charge with fine atomisation and must also inject the main fuel charge. To do this it requires variable nozzle holes and a two stage needle valve lift. Fuel pump drive for this system may require specially shaped cam profiles.Electronic Injection was a system introduced by MAN engines that electronically controlled fuel injection. The heart of the electronic injection system is a micro-processor to which the actual engine speed and crankshaft position are transmitted as output signals. When the desired speed is compared with the actual speed, the processor automatically retrieves the values of injection timing and pressure for any load under normal operating conditions. In the event of deviations from normal operating conditions additional signals are transmitted to the microprocessor either manually or by appropriate temperature and pressure sensors. The result is an engine operating at optimum injection pressure and timing at all times. Adjustments to the system during operation are possible.Corrections can be made for: adapting the injection system to varying conditions such as ballast voyages, bad weather; matching the engine to different fuels, ignition lag, cetane numbers, etc; readjusting for operation in the tropics or in winter; controlling the injection characteristics of individual cylinders, such as when running in; reducing the minimum slow running speed, such as when in canals.The most noticeable feature of a KEZ type engine with electronic injection, is the absence of a camshaft and individual fuel pumps. The fuel is delivered to high-pressure accumulator by normal fuel injection plunger pumps driven by gears and cams from the crankshaft. These pumps are located above the thrust bearing and, depending on the size and cylinder number of the engine, two or more of these pumps are used. To safeguard against failure of a pump or a pressure pipe, two independent fuel delivery pipes are placed between the high-pressure pumps and accumulator.The high-pressure accumulator generates a buffer volume to prevent the pressure in the injection valve from dropping below an acceptable limit when the fuel is withdrawn during injection into the cylinder. For the electronically controlled injections systems, metering of the fuel volume for one cylinder is not affected by limiting the delivery volume per stroke of the injection pump plunger as in conventional systems, but by limiting the duration of injection. This is initiated by an electronic controller, i.e. by a low voltage signal which controls the opening and closing action of an electro-hydraulic servo valve. The electrohydraulic valve is actuated by oil under pressure from two pumps and an air cushion-type accumulator.Sequential control ensures that according to the engine firing sequence, the correct engine cylinder is selected in the proper crank angel range and that the electronically controlled injection valve is actuated at the exact point of injection.For engine starting and reversing, the correct injection timing is linked with the electronically controlled starting air valve. Since electronically controlled starting valves have no time delay between the switching pulse and opening of the air valve, and since there are no flow losses, due to the elimination of the control air pipes, the starting air requirements are reduced in comparison with the former conventional air start system.The constant pressure maintained during fuel injection with the electronically controlled fuelinjection system, and the fact that the injection pressure can easily be matched to each load condition, lead to lower fuel consumption rates over the entire load range. It also means satisfactory operation at very slow speeds, which contributes favourably to the manoeuvrability of a vessel, a K3EZ 50/105C/CL engine on the test bed was operated at a dead slow speed of 30 rev/min, which had never been achieved before. The full load speed is 183 rev/min.Although this system never caught on in the early 1980’s with the advances in electronics it could easily returns in the near future.。