两段式煤气发生炉工艺
两段式煤气发生炉操作规程
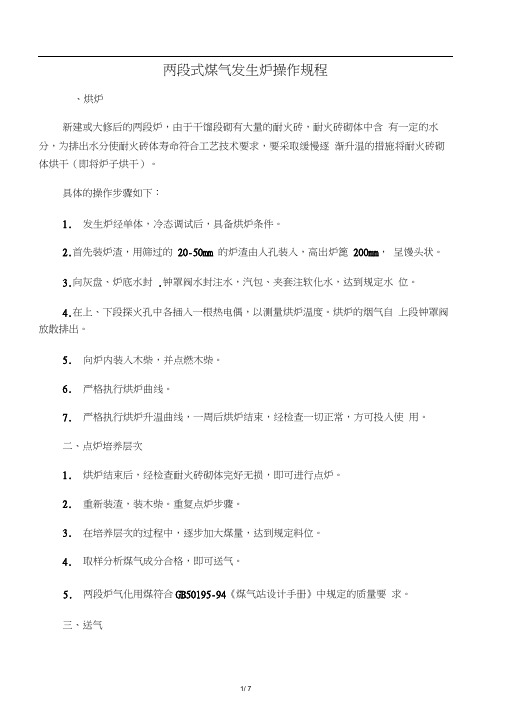
两段式煤气发生炉操作规程、烘炉新建或大修后的两段炉,由于干馏段砌有大量的耐火砖,耐火砖砌体中含有一定的水分,为排出水分使耐火砖体寿命符合工艺技术要求,要采取缓慢逐渐升温的措施将耐火砖砌体烘干(即将炉子烘干)。
具体的操作步骤如下:1.发生炉经单体,冷态调试后,具备烘炉条件。
2.首先装炉渣,用筛过的20-50mm 的炉渣由人孔装入,高出炉篦200mm,呈馒头状。
3.向灰盘、炉底水封.钟罩阀水封注水,汽包、夹套注软化水,达到规定水位。
4.在上、下段探火孔中各插入一根热电偶,以测量烘炉温度。
烘炉的烟气自上段钟罩阀放散排出。
5.向炉内装入木柴,并点燃木柴。
6.严格执行烘炉曲线。
7.严格执行烘炉升温曲线,一周后烘炉结束,经检查一切正常,方可投入使用。
二、点炉培养层次1.烘炉结束后,经检查耐火砖砌体完好无损,即可进行点炉。
2.重新装渣,装木柴。
重复点炉步骤。
3.在培养层次的过程中,逐步加大煤量,达到规定料位。
4.取样分析煤气成分合格,即可送气。
5.两段炉气化用煤符合GB50195-94《煤气站设计手册》中规定的质量要求。
三、送气1.接到站长送气通知,通知用户。
2.首先要对站内设备和管道进行气体置换,取样化验,煤气中的O2<0.4%时,启动煤气加压机,待运转正常后,送至用气单位。
3.有煤气贮气柜的要先将柜内气体置换好,在气柜顶部放散管处取样,在煤气质量合格,气柜达到规定容积后,再启动煤气加压机向用户供气。
4.调整外供煤气压力,达到规定工艺要求,通知用户点燃窑炉喷嘴。
四、炉况基本操作工艺参数1.每 1 小时插钎1 次,插相隔3孔,根据炉况调整饱和温度,加煤、出灰,并做好记录。
2.定期巡检各设备运转情况,保证水封高度,及时清理水封中的沉积物。
3.汽包、夹套及时补充软化水,确保不缺水;每班排污两次。
4.操作参数如下(供参考):⑴气化层厚度:火层:100—200mm中灰:150—300mm边灰:1000—1200mm⑵饱和温度:55 士。
两段式煤气发生炉工作原理
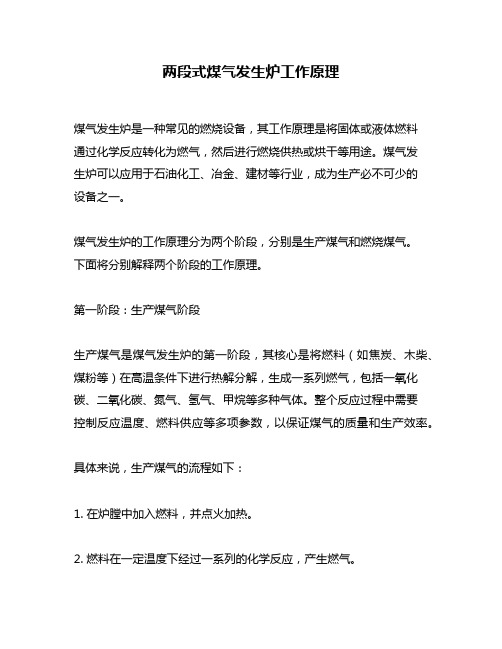
两段式煤气发生炉工作原理煤气发生炉是一种常见的燃烧设备,其工作原理是将固体或液体燃料通过化学反应转化为燃气,然后进行燃烧供热或烘干等用途。
煤气发生炉可以应用于石油化工、冶金、建材等行业,成为生产必不可少的设备之一。
煤气发生炉的工作原理分为两个阶段,分别是生产煤气和燃烧煤气。
下面将分别解释两个阶段的工作原理。
第一阶段:生产煤气阶段生产煤气是煤气发生炉的第一阶段,其核心是将燃料(如焦炭、木柴、煤粉等)在高温条件下进行热解分解,生成一系列燃气,包括一氧化碳、二氧化碳、氮气、氢气、甲烷等多种气体。
整个反应过程中需要控制反应温度、燃料供应等多项参数,以保证煤气的质量和生产效率。
具体来说,生产煤气的流程如下:1. 在炉膛中加入燃料,并点火加热。
2. 燃料在一定温度下经过一系列的化学反应,产生燃气。
3. 燃气经过水冷却,去除其中大部分的固态颗粒和小部分液态物质,得到煤气。
第二阶段:燃烧煤气阶段燃烧煤气是煤气发生炉的第二阶段,其核心是将生产的煤气送入燃烧室进行燃烧。
燃烧时需要保证煤气与空气的比例严格控制,以确保完全燃烧,并通过调节燃烧室的温度和风量来达到所需的供热或烘干效果。
具体来说,燃烧煤气的流程如下:1. 将生产的煤气送入燃烧室。
2. 在燃烧室中分别控制煤气和空气的供应量,保证其比例合适,实现完全燃烧。
3. 焚烧产生的高温烟气经过换热器进行热回收,以提高能源利用效率。
综上所述,煤气发生炉的工作原理分为生产煤气和燃烧煤气两个阶段。
其生产过程中需要控制多项参数,以保证煤气质量和生产效率。
燃烧过程中需要严格控制煤气和空气的供应量,保证完全燃烧,并通过热回收提高能源利用效率。
第一章 两段式煤气发生炉工艺流程及气化过程原理

1750
≤6500
400-600
98-196
煤气
工作压力 kPa
水封高度mm
≤4.0
550
1820
≤7500
400-600
98-196
煤气
≤4.0
550
工作原理: 煤气带着灰尘以一定的速度沿切线方向进入除尘器,在除尘器内以螺旋线的 形式作回转运动。悬浮的灰尘颗粒在离心力的作用下被抛向圆筒的内表面,在重 力作用下降落至排灰管。而煤气则从下部进入中央管,形成上升的螺旋气流,从 顶部离开除尘器。
4
2、底煤气的产生 原料煤在干馏段被底部煤气干馏后,形成热半焦进入气化段。热半焦的挥发 份一般为3~5%。热半焦因脱去煤中的活性组份,气化活性比烟煤有所降低,其 气化强度一般可达270~350Kg/㎡.h,二段式气化炉气化火层的温度一般为1000 ~1300℃之间。热半焦与蒸汽或空气混合气发生以下反应: C+O2=CO2+408840千焦/千摩尔 C+1/2O2=CO+123217千焦/千摩尔 CO2+C=2CO-162405千焦/千摩尔 C+ H2O =CO+ H2-118821千焦/千摩尔 C+ 2H2O =CO2+ 2H2-75237千焦/千摩尔
排渣方式
上段
煤气
出口
公称 直径
下段
mm
3.5 50-65 0.25 ≥0.20 0.294
2.97 7.5×2 DN350
400×400
5.0
6.5
6.5
50-65
50-65
50-65
0.25
0.25
0.25
≥0.20 0.294
双段煤气发生炉工艺流程
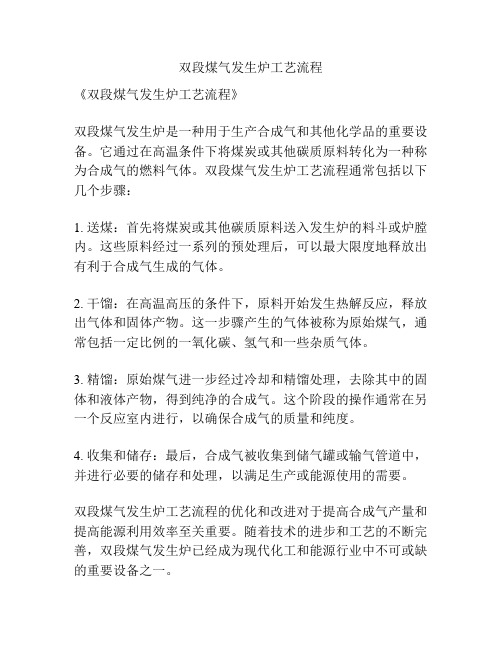
双段煤气发生炉工艺流程
《双段煤气发生炉工艺流程》
双段煤气发生炉是一种用于生产合成气和其他化学品的重要设备。
它通过在高温条件下将煤炭或其他碳质原料转化为一种称为合成气的燃料气体。
双段煤气发生炉工艺流程通常包括以下几个步骤:
1. 送煤:首先将煤炭或其他碳质原料送入发生炉的料斗或炉膛内。
这些原料经过一系列的预处理后,可以最大限度地释放出有利于合成气生成的气体。
2. 干馏:在高温高压的条件下,原料开始发生热解反应,释放出气体和固体产物。
这一步骤产生的气体被称为原始煤气,通常包括一定比例的一氧化碳、氢气和一些杂质气体。
3. 精馏:原始煤气进一步经过冷却和精馏处理,去除其中的固体和液体产物,得到纯净的合成气。
这个阶段的操作通常在另一个反应室内进行,以确保合成气的质量和纯度。
4. 收集和储存:最后,合成气被收集到储气罐或输气管道中,并进行必要的储存和处理,以满足生产或能源使用的需要。
双段煤气发生炉工艺流程的优化和改进对于提高合成气产量和提高能源利用效率至关重要。
随着技术的进步和工艺的不断完善,双段煤气发生炉已经成为现代化工和能源行业中不可或缺的重要设备之一。
两段式(冷站)煤气发生炉操作规程.doc

第一章煤气发生炉及净化设备一、工艺流程1.冷煤气站煤两段式煤气发生炉产生的煤气分为上段煤气和下段煤气。
上段煤气先进入一级电捕焦油器脱除重质焦油及灰尘,其工作温度80-150℃之间,再进入间冷器,在间冷器内煤气冷却至35-45℃左右。
下段煤气经旋风除尘器除尘,继而进入余热换热器,煤气温度降至200-230℃,再进入风冷器冷却,温度降至65-80℃,通过间冷器冷却至35-45℃。
被间冷器冷却后的上、下段煤气进入二级电捕焦油器脱油、除尘,通过煤气加压机输送到用户。
二、发生炉及净化设备主要结构及工作原理:两段式煤气发生炉由料仓、给煤机构、干馏段、气化段、出渣结构、汽包等六大部分组成。
分离好的20-60mm煤块,经过输煤系统储存于料仓,料仓中的煤经过给煤机构,根据需要均匀地加入干馏段与下部上升的制气进行热交换,温度逐渐上升。
煤中的机械水析出,以后是结晶水析出,随着煤块位置下降,煤块温度不断上升,煤块进行着复杂的热分解,析出不同馏分的挥发份,直到900℃以上基本结束。
残留的部分为固定碳及灰份,与外部鼓入的水蒸汽与空气组成的气化剂反应,生成H2、CO2、CO、CH4、N2等气化反应产物,同时放出大量的热,除了满足吸热反应外,均表现为气体的闲热带入上部,残留的灰份由出灰机排出。
气化段上升的热煤气,在干馏段充分热交换以后,由炉顶出口引出,称为上段煤气。
温度约80-120℃,约占煤气产量的40%。
气化段生成的煤气除了一部分作为载热气流上升进入干馏段外,另一部分从炉内中心管砖壁及中心收集管引出,称为下段煤气,温度约400-600℃,约占煤气产量的60%。
主要结构及工作原理:电捕焦油器又称静电除尘器,主要由筒体、电晕极、沉淀极、分气隔板、绝缘子箱组成,当含有焦油及固体颗粒的煤气经分气隔板均匀地进入电气滤清器,在高压电场直流电压为40-60kv的作用下,带负电的电晕极周围的气体被电离,产生大量的电子与正负离子,气体在流动的过程中,其中的焦油被电子与带正电的离子所吸引,形成了电子焦油粒子与带正电的焦油粒子,这些带电粒子在高压电场的作用下,各自向它们相对的极移动,即带负电的粒子向沉淀极移动,带正电的粒子向电晕极移动,在移动的过程中不断吸收其它粒子,使其变成更大的颗粒,最终到达沉淀极被吸附粘着于管壁,因自重沉到电捕焦底部,达到除焦油的目的。
两段式煤气发生炉工艺

二段式煤气发生炉煤气站工艺:合格原料煤由皮带机输送提升至主厂房储煤仓,再经双滚筒液压加煤机加入炉内,煤受到来自气化段煤气的加热干馏,干馏后半焦状态下的煤炭在气化段与气化剂(空气,蒸汽)发生反应,气化段生成的煤气分为两部分,一部分从两段炉下段煤气出口经旋风除尘器出炉,另一部分向上经中心管与干馏煤气混合从上段煤气出口出炉。
下段出口煤气经旋风除尘器降温除尘后进入强制风冷器,继续除尘降温,然后进入间冷器进一步降温。
上段出口煤气进入电捕焦油器除焦后,直接进入间冷器,与下段煤气混合,在混合中完成降温,混合后煤气进入电捕轻油器,捕除轻油,煤气经加压风机加压后送往水雾捕滴器脱水送往用户。
两段式煤气发生炉自上而下由干馏段和气化段组成,首先煤从炉顶煤仓经两段下煤阀进入炉体,煤在干馏段经过充分的干燥和长时间的低温干馏,逐渐形成半焦,进入气化段,炽热的半焦在气化段与炉底鼓入的气化剂充分反应,经过炉内还原层,氧化层而形成灰渣,由炉栅驱动从灰盆自动排出。
煤在低温干馏的过程中,以挥发分析出为主生成的煤气称为干馏煤气,组成两段炉的顶部煤气,约占总煤气量的 40% ,其热值较高( 6700KJ/nm3)温度较低(120°C ),并含有大量的焦油。
这种焦油为低温干馏产物,其流动性较好,可采用静电除尘器捕集起来,作为化工原料和燃料。
在气化段,炽热的半焦和气化及经过还原,氧化等一系列化学反应生成的煤气,称为气化煤气。
组成两段炉的底部煤气,约占总煤气量的 60% ,其热值相对较低( 6400KJ/nm3),温度较高( 450°C 左右 ) 因煤在干馏段低温干馏时间充足,进入气化段的煤已变成半焦,因此生成的气化煤气不含焦油,又因距炉栅灰层较近,所以含有少量飞灰。
底部煤气就可经旋风除尘器及风冷器等设备来处理,这样对于使用冷静化煤气的用户,便可不采用水洗法就能使用上冷静化煤气,从而避免了大量酚水无法处理的缺陷。
3.2m 两段式冷煤气站(厂房为钢结构)2.6m 两段式冷煤气站(厂房为混凝土结构)2.0m 两段式冷煤气站煤气站特点:(一)在整个冷煤气净化工艺中,本公司对底部煤气的处理采用旋风除尘器,强制风冷器来进行,改变了我国两段炉常用的双竖管、洗涤塔用水冷却工艺,即节约了生产用水,又消除了因使用传统工艺带来的酚水量太大弊端,从而彻底杜绝了国内传统的两段炉对环境的污染问题。
两段煤气发生炉工艺流程

两段煤气发生炉工艺流程
说起来,我在这行都摸爬滚打 20 多年啦!想当年我刚接触这玩意儿的时候,那叫一个懵圈,啥都不懂啊!
说到这儿,我想起个事儿。
有个同行小李,他有次加煤的时候居然睡着了,你说离谱不离谱?哈哈!
咱接着说,这煤气发生炉运行的时候,那声音“嗡嗡嗡”的,可带劲啦!然后呢,经过一系列的反应,煤气就产生啦。
不过这中间的反应过程,我记得好像是这样,不过也可能记错喽。
反正就是各种化学反应,什么氧化、还原啥的。
哇,有时候想想这些化学知识,头都大!
对了,还有个关键的点,就是控制温度和压力。
这要是控制不好,那可就全乱套啦!我刚入行的时候,就因为这个吃了不少亏。
我这又扯远啦!咱再回来说说后续的净化处理,这一步也很重要啊。
要是净化不好,那煤气质量可就不行喽。
朋友,你要是在操作过程中有啥问题,随时跟我交流哈。
说不定你能发现一些我都没注意到的点呢!
好啦,我能想到的暂时就这么多,剩下的就靠你自己在实践中摸索啦!。
两段式煤气发生炉操作规程
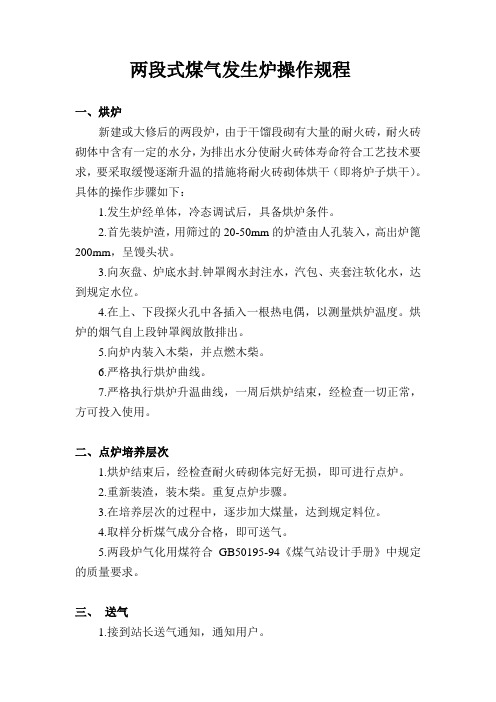
两段式煤气发生炉操作规程一、烘炉新建或大修后的两段炉,由于干馏段砌有大量的耐火砖,耐火砖砌体中含有一定的水分,为排出水分使耐火砖体寿命符合工艺技术要求,要采取缓慢逐渐升温的措施将耐火砖砌体烘干(即将炉子烘干)。
具体的操作步骤如下:1.发生炉经单体,冷态调试后,具备烘炉条件。
2.首先装炉渣,用筛过的20-50mm的炉渣由人孔装入,高出炉篦200mm,呈馒头状。
3.向灰盘、炉底水封.钟罩阀水封注水,汽包、夹套注软化水,达到规定水位。
4.在上、下段探火孔中各插入一根热电偶,以测量烘炉温度。
烘炉的烟气自上段钟罩阀放散排出。
5.向炉内装入木柴,并点燃木柴。
6.严格执行烘炉曲线。
7.严格执行烘炉升温曲线,一周后烘炉结束,经检查一切正常,方可投入使用。
二、点炉培养层次1.烘炉结束后,经检查耐火砖砌体完好无损,即可进行点炉。
2.重新装渣,装木柴。
重复点炉步骤。
3.在培养层次的过程中,逐步加大煤量,达到规定料位。
4.取样分析煤气成分合格,即可送气。
5.两段炉气化用煤符合GB50195-94《煤气站设计手册》中规定的质量要求。
三、送气1.接到站长送气通知,通知用户。
2.首先要对站内设备和管道进行气体置换,取样化验,煤气中的O2﹤0.4%时,启动煤气加压机,待运转正常后,送至用气单位。
3.有煤气贮气柜的要先将柜内气体置换好,在气柜顶部放散管处取样,在煤气质量合格,气柜达到规定容积后,再启动煤气加压机向用户供气。
4.调整外供煤气压力,达到规定工艺要求,通知用户点燃窑炉喷嘴。
四、炉况基本操作工艺参数1.每1小时插钎1次,插相隔3孔,根据炉况调整饱和温度,加煤、出灰,并做好记录。
2.定期巡检各设备运转情况,保证水封高度,及时清理水封中的沉积物。
3.汽包、夹套及时补充软化水,确保不缺水;每班排污两次。
4.操作参数如下(供参考):⑴气化层厚度:火层:100—200mm中灰:150—300mm边灰:1000—1200mm⑵饱和温度:55±5℃⑶炉底压力:3000—5000Pa⑷上段煤气压力:1500Pa上段煤气温度:90—120℃⑸下段煤气压力:3500Pa左右下段煤气压力温度:400—500℃五、煤气炉的并网和脱网煤气炉并网是指二台或多台煤气炉,共用一套输送管网,煤气炉同时或先后将合格煤气并入共用的管网中。
- 1、下载文档前请自行甄别文档内容的完整性,平台不提供额外的编辑、内容补充、找答案等附加服务。
- 2、"仅部分预览"的文档,不可在线预览部分如存在完整性等问题,可反馈申请退款(可完整预览的文档不适用该条件!)。
- 3、如文档侵犯您的权益,请联系客服反馈,我们会尽快为您处理(人工客服工作时间:9:00-18:30)。
二段式煤气发生炉煤气站工艺:
合格原料煤由皮带机输送提升至主厂房储煤仓,再经双滚筒液压加煤机加入炉内,煤受到来自气化段煤气的加热干馏,干馏后半焦状态下的煤炭在气化段与气化剂(空气,蒸汽)发生反应,气化段生成的煤气分为两部分,一部分从两段炉下段煤气出口经旋风除尘器出炉,另一部分向上经中心管与干馏煤气混合从上段煤气出口出炉。
下段出口煤气经旋风除尘器降温除尘后进入强制风冷器,继续除尘降温,然后进入间冷器进一步降温。
上段出口煤气进入电捕焦油器除焦后,直接进入间冷器,与下段煤气混合,在混合中完成降温,混合后煤气进入电捕轻油器,捕除轻油,煤气经加压风机加压后送往水雾捕滴器脱水送往用户。
两段式煤气发生炉自上而下由干馏段和气化段组成,首先煤从炉顶煤仓经两段下煤阀进入炉体,煤在干馏段经过充分的干燥和长时间的低温干馏,逐渐形成半焦,进入气化段,炽热的半焦在气化段与炉底鼓入的气化剂充分反应,经过炉内还原层,氧化层而形成灰渣,由炉栅驱动从灰盆自动排出。
煤在低温干馏的过程中,以挥发分析出为主生成的煤气称为干馏煤气,组成两段炉的顶部煤气,约占总煤气量的 40% ,其热值较高( 6700KJ/nm3)温度较低(120°C ),并含有大量的焦油。
这种焦油为低温干馏产物,其流动性较好,可采用静电除尘器捕集起来,作为化工原料和燃料。
在气化段,炽热的半焦和气化及经过还原,氧化等一系列化学反应生成的煤气,称为气化煤气。
组成两段炉的底部煤气,约占总煤气量的 60% ,其热值相对较低( 6400KJ/nm3),温度较高( 450°C 左右 ) 因煤在干馏段低温干馏时间充足,进入气化段的煤已变成半焦,因此生成的气化煤气不含焦油,又因距炉栅灰层较近,所以含有少量飞灰。
底部煤气就可经旋风除尘器及风冷器等设备来处理,这样对于使用冷静化煤气的用户,便可不采用水洗法就能使用上冷静化煤气,从而避免了大量酚水无法处理的缺陷。
3.2m 两段式冷煤气站(厂房为钢结构)
2.6m 两段式冷煤气站(厂房为混凝土结构)2.0m 两段式冷煤气站
煤气站特点:
(一)在整个冷煤气净化工艺中,本公司对底部煤气的处理采用旋风除尘器,强制风冷器来进行,改变了我国两段炉常用的双竖管、洗涤塔用水冷却工艺,即节约了生产用水,又消除了因使用传统工艺带来的酚水量太大弊端,从而彻底杜绝了国内传统的两段炉对环境的污染问题。
顶部煤气中的大量焦油采用 37 管电捕器捕集,因其流动性良好,可直接输送到焦油池储存。
混合煤气采用油洗冷却器冷却,此设备的特点是,煤气的冷却不与水直接接触,而是管板式间接冷却,再通过煤气自身冷凝下来的饱和水(含酚)循环使用洗涤煤气,使煤气站酚水减至最少量,此少量酚水为正增长,它的输送储存皆密闭进行。
在整个工艺中,对焦油的捕集采用二级电捕,以确保在冷煤气净化过程中焦油的含量在 40mg/m3以下。
顶部煤气用 37 管电捕焦,煤气在其中最大流速为 0.6m /s ,低于《发生炉煤气站设计规范》(GB50195-94 )中的 61管电捕青油器,
煤气在其中的最大流速为 0.65m /s 低于《发生炉煤气站设计规范》
( GB50195-94 )中的 0.8m /s 的要求。
本工艺自动化程度高,对于重要参数如上段煤气温度、气化剂温度、煤气站负荷实行自动调节,运行安全,便于操作,是一种比较先进的煤炭制气工艺。
(二)国内的两段炉是在单段炉的基础上又加一段干馏段,由于没有经过严格测验,其干馏段各参数及结构不尽合理,这样煤的干馏就不会充分,致使气化段煤气含有焦油,此部分焦油已经高温裂解,也已无法处理,只好采用水洗处理,洗涤水也含有大量沥青焦油,因而无法避免单段炉冷净化煤气工艺的环境污染缺陷。
本公司两段炉在几十年的试验基础上设计出来,并经工业性应用后多次改进定型的一种成熟粗放型,其显著特点如下:
o 底部煤气由 36 个耐火通道提取,并有 6 个底部煤气调节阀来调节整个炉膛面的燃烧平衡。
o底部煤气另设一路中心管提取,其作用为:
o与周边 36 个耐火通道共同组成干馏加热空间,形成内外两层环形圈辐射热源。
o与周边 36 个耐火通道共同组成炉膛断面燃烧平衡系统,避免了国内两段炉燃烧中心黑洞问题,能很方便的调节炉膛燃烧情况。
o采用高灰盆水封,高气化压力运行,发生炉气化程度高,产气量大。
o炉栅驱动除灰及下煤采用液压系统,通过 PLC 机实现自动控制。
o水夹套为压力容器,使用寿命非常长。
综上所述,由本公司生产的两段炉具有最优的干馏段与气化段比例及良好的干馏结构,其干馏段所产生的煤气只含焦油不含灰尘,气化煤气只含少许灰尘不含焦油,为彻底解决煤气站酚水污染及挥发酚对大气的污染问题奠定了坚实的基础。
(三)型号主要有:Φ2.0m Φ2.6m Φ3.0m Φ3.2m
热脱焦煤气站:两段炉有上下两个煤气出口,可输出不同热值的煤气,其气化效率和热效率均比单段式炉高。
炉体由原常压结构改为压力容器承压结构,去掉了煤气站外配的蒸汽锅炉增加了废热锅炉,充分利用煤气余热,自产0.25-0.3Mpa 的蒸汽,大大提高了系统蒸汽产量,满足了煤气站自身的需要。
煤炭经过炉体彻底干馏下段,煤气基本不含焦油,上段煤气含有少量轻质焦油,不易阻塞管道。
两段式煤气炉热值高,稳定性好,操作弹性大,自动化程度高,劳动强度低,无污染,节水显著,占地面积少,长期运行成本低等特点。
煤气发生炉的全部重量改为由地下基础承担,可采用简单的钢结构的厂房,降低工程造价、缩短了施工工期。
冷煤气站:在热炉基础上,增加净化设备,使煤气更加洁净,加压输送,增加了煤气的压力的稳定性。
1500m3煤气储气柜两段炉鼓风系统两段炉操作系统静电除焦系统结构图:
技术指标
工艺流程
两段式煤气发生炉冷站工艺流程图。