悬架用减振器设计指南设计
减震器的设计(学术参考)

产品设计项目说明书一号宋体,居中汽车减震器的研究设计三号粗黑体,居中院(系)机械工程学院专业机械工程及自动化班级创新班学生姓名指导老师2015 年 01 月 05 日目录摘要 (3)第一章绪论 (4)1.1概述 (4)1.2 双筒液压减震器工作原理及优点 (5)1.3项目名称和要求 (6)1.4项目分析 (7)1.4.1双筒式减振器的外特性设计原则 (7)1.4.2减震器参数 (7)第二章参数的计算 (9)比亚迪S6主要参数 (9)2.1悬架静挠度的计算 (9)2.2相对阻尼系数 (10)2.3阻尼系数的确定 (11)2.4最大卸载力的计算 (12)2.5工作缸直径和减震器活塞行程的确定 (12)2.6减振器活塞行程的确定 (13)2.7 液压缸壁厚、缸盖、活塞杆和最小导向长度的计算 (14)2.7.1、液压缸的壁厚的计算 (14)2.7.2、液压缸的稳定性验算 (15)2.7.3、缸盖厚度的计算 (16)2.7.4、活塞杆的计算 (17)2.7.5、对杆强度进行 (17)2.7.6最小导向长度的确定 (18)2.8 活塞及阀系的尺寸计算 (18)第三章液压缸的结构设计 (19)3.1、缸体与缸盖的连接形式 (19)3.2、活塞杆与活塞的连接形式 (19)3.3、活塞杆导向部分的结构 (19)3.4、活塞及活塞杆处密封圈的选用 (19)3.5、液压缸的安装连接结构 (20)3.6、活塞环 (20)3.7、液压缸主要零件的材料和技术要求 (20)3.8弹簧片的选择 (20)3.9 密封元件和工作油液的确定 (21)3.9.1油封设计 (21)3.9.2密封元件 (21)3.9.3、油液的选取 (21)第四章使用说明 (23)4.1匹配技巧 (23)4.2故障维修与检测 (23)4.3漏油故障编辑 (25)总结 (26)参考文献 (27)附录 (28)摘要为改善汽车行驶平顺性,悬架中与弹性元件并联安装减振器,为衰减振动,汽车悬架系统中采用减振器多是液力减振器。
减震器设计

4.7减振器机构类型及主要参数的选择计算4.7.1分类悬架中用得最多的减振器是内部充有液体的液力式减振器。
汽车车身和车轮振动时,减振器内的液体在流经阻尼孔时的摩擦和液体的粘性摩擦形成了振动阻力,将振动能量转变为热能,并散发到周围空气中去,达到迅速衰减振动的目的。
如果能量的耗散仅仅是在压缩行程或者是在伸张行程进行,则把这种减振器称之为单向作用式减振器,反之称之为双向作用式减振器。
后者因减振作用比前者好而得到广泛应用。
根据结构形式不同,减振器分为摇臂式和筒式两种。
虽然摇臂式减振器能够在比较大的工作压力(10—20MPa)条件下工作,但由于它的工作特性受活塞磨损和工作温度变化的影响大而遭淘汰。
筒式减振器工作压力虽然仅为2.5~5MPa ,但是因为工作性能稳定而在现代汽车上得到广泛应用。
筒式减振器又分为单筒式、双筒式和充气筒式三种。
双筒充气液力减振器具有工作性能稳定、干摩擦阻力小、噪声低、总长度短等优点,在轿车上得到越来越多的应用。
设计减振器时应当满足的基本要求是,在使用期间保证汽车行驶平顺性的性能稳定。
4.7.2相对阻尼系数ψ减振器在卸荷阀打开前,减振器中的阻力F 与减振器振动速度v 之间有如下关系 v F δ= (4-51)式中,δ为减振器阻尼系数。
图4—37b 示出减振器的阻力-速度特性图。
该图具有如下特点:阻力-速度特性由四段近似直线线段组成,其中压缩行程和伸张行程的阻力-速度特性各占两段;各段特性线的斜率是减振器的阻尼系数v F /=δ,所以减振器有四个阻尼系数。
在没有特别指明时,减振器的阻尼系数是指卸荷阀开启前的阻尼系数而言。
通常压缩行程的阻尼系数Y Y Y v F /=δ与伸张行程的阻尼系数S S S v F /=δ不等。
图4—37 减振器的特性a) 阻力一位移特性 b)阻力一速度特性汽车悬架有阻尼以后,簧上质量的振动是周期衰减振动,用相对阻尼系数ψ的大小来评定振动衰减的快慢程度。
ψ的表达式为s cm 2δψ= (4-52)式中,c 为悬架系统垂直刚度;为簧上质量。
汽车悬架系统中橡胶减振元件的设计要求分析

Top Mount Bushing 1 图纸要求Bushing 2液压衬套的特性液压衬套的动态特性应用:减少上摆臂衬套的刚度减少车内噪声减小刚度,隔离控制臂500Hz的振动。
(以前为橡胶衬套,现在改用液压衬套)两个液室均为工作液室!!2. Applications of Hydro Bushings8. Technical product Development ExpertiseHydraulically Damping Subframe MountsThe dynamic characteristics of hydrobushing depend on their applications.front lower control arm系统的结构图:问题:发动机在2000~2300rpm (100Hz~115Hz 时,驾驶室内出现很大的Booming声,其中108Hz加动力吸振器和液压衬套以后,传动轴的振动减小。
吸振器和液压衬套以后,传动轴和地板的传递到驾驶室的振动由图可见,轴管的振动加速度和位置有关。
第一点的振动最大,要从这点想办法。
系统的结构。
支撑件的承载:300N。
传统的橡胶隔振器,可见系统的振动下降17~以后,将一个峰值削减成为两个峰值,可以下降新设计液压衬套的动态特性Strut mountSpring SeatJounce BumperShieldShock absorberSteering knuckleCoil springJounce bumperStrut mountBearing 2013-03-15AB CD EF G Houter path, which has a considerably higher level of rigidity.2013-03-15利用橡胶作为隔振的减振器上端支撑,由于兼顾其疲劳特性,其静刚度不可能很低。
此时,在减振器上端支撑中可以采用液压支撑元件。
悬架-减震器
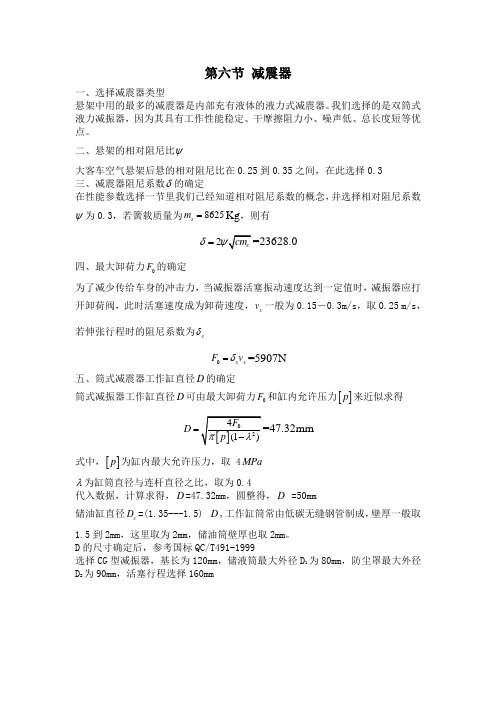
第六节 减震器
一、选择减震器类型
悬架中用的最多的减震器是内部充有液体的液力式减震器。
我们选择的是双筒式液力减振器,因为其具有工作性能稳定、干摩擦阻力小、噪声低、总长度短等优点。
二、悬架的相对阻尼比ψ
大客车空气悬架后悬的相对阻尼比在0.25到0.35之间,在此选择0.3
三、减震器阻尼系数δ的确定
在性能参数选择一节里我们已经知道相对阻尼系数的概念,并选择相对阻尼系数ψ为0.3,若簧载质量为8625s m =Kg ,则有
2δψ==23628.0
四、最大卸荷力0F 的确定
为了减少传给车身的冲击力,当减振器活塞振动速度达到一定值时,减振器应打开卸荷阀,此时活塞速度成为卸荷速度,x v 一般为0.15-0.3m/s ,取0.25 m/s ,
若伸张行程时的阻尼系数为s δ
0s x F v δ==5907N
五、筒式减震器工作缸直径D 的确定
筒式减振器工作缸直径D 可由最大卸荷力0F 和缸内允许压力[]p 来近似求得
D ==47.32mm 式中,[]p 为缸内最大允许压力,取 4MPa
λ为缸筒直径与连杆直径之比,取为0.4
代入数据,计算求得,D =47.32mm ,圆整得,D =50mm
储油缸直径c D =(1.35---1.5) D ,工作缸筒常由低碳无缝钢管制成,壁厚一般取
1.5到2mm ,这里取为2mm ,储油筒壁厚也取2mm 。
D 的尺寸确定后,参考国标QC/T491-1999
选择CG 型减振器,基长为120mm ,储液筒最大外径D 1为80mm ,防尘罩最大外径
D 2为90mm ,活塞行程选择160mm。
减振器选型设计计算书(原)
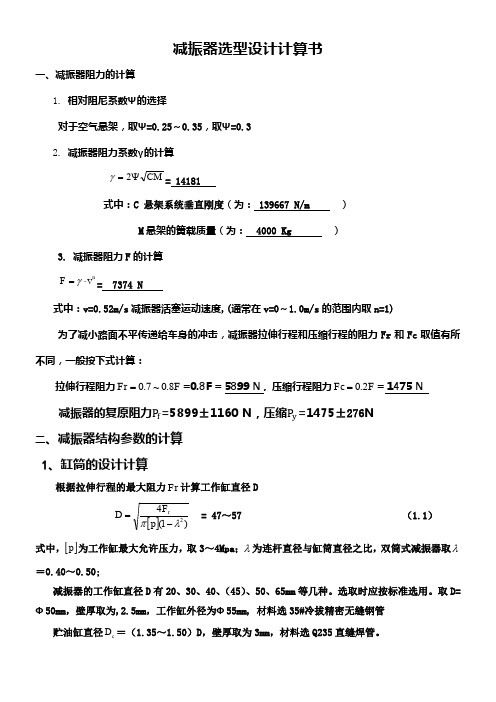
减振器选型设计计算书一、减振器阻力的计算1. 相对阻尼系数Ψ的选择对于空气悬架,取Ψ=0.25~0.35,取Ψ=0.32. 减振器阻力系数γ的计算 CM ψ=2γ= 14181式中:C 悬架系统垂直刚度(为: 139667 N/m )M 悬架的簧载质量(为: 4000 Kg )3. 减振器阻力F 的计算n v F ⋅=γ= 7374 N式中:v=0.52m/s 减振器活塞运动速度,(通常在v=0~1.0m/s 的范围内取n=1)为了减小路面不平传递给车身的冲击,减振器拉伸行程和压缩行程的阻力Fr 和Fc 取值有所不同,一般按下式计算:拉伸行程阻力F Fr 8.0~7.0==0.8F = 5899 N , 压缩行程阻力F Fc 2.0== 1475 N 减振器的复原阻力 =5899±1160 N ,压缩 =1475±276N二、减振器结构参数的计算1、缸筒的设计计算根据拉伸行程的最大阻力Fr 计算工作缸直径D [])1(42λπ-=p F D r = 47~57 (1.1) 式中,[]p 为工作缸最大允许压力,取3~4Mpa ;λ为连杆直径与缸筒直径之比,双筒式减振器取λ=0.40~0.50;减振器的工作缸直径D 有20、30、40、(45)、50、65mm 等几种。
选取时应按标准选用。
取D=Φ50mm ,壁厚取为,2.5mm ,工作缸外径为Φ55mm, 材料选35#冷拔精密无缝钢管 贮油缸直径c D =(1.35~1.50)D ,壁厚取为3mm ,材料选Q235直缝焊管。
c D =Φ70mm ,贮油缸外径取Φ76mm2、活塞杆的设计计算活塞杆直径g d 可按下式计算经验数据: g d =(0.4~0.5)D ,则g d =Φ20mm.材质为:冷拉45#圆钢,热处理:表面高频淬火,硬化层深0.7~1.2mm,硬度45~50HRC ,淬火后校直。
直线度为0.02mm,并去应力回火;表面处理:表面镀硬铬20um 以上,铬层硬度要求HV900以上。
汽车悬架减振系统优化设计1

第1章绪论1.1 选题的目的和意义随着我国经济的迅速发展,人民生活水平日渐提高,汽车已经成为人们的生活中必不可少的交通工具,并且对乘车的安全性和舒适性也有了更高的要求,本文对双筒液压减振器的优化就是为了满足这一目的。
车辆是一个由许多子系统组合而成的复杂系统,其总体性能与零部件的性能关系密切。
因此,零部件的研发,不但涉及零部件本身的分析计算与试验等,而且涉及许多与整车有关的参数,是一个较为复杂的研发过程。
减振器是车辆悬架系统中的重要部件,其性能的好坏对车辆的舒适性以及车辆及悬架系统的使用寿命等有较大影响。
1.2 减振器的发展历史世界上第一个有记载、比较简单的减振器是1897年由两个姓吉明的人发明的。
他们把橡胶块与叶片弹簧的端部相连,当悬架被完全压缩时,橡胶减振块就碰到连接在汽车大梁上的一个螺栓,产生止动。
这种减振器在很多现代汽车悬架上仍有使用,但其减振效果很小。
1898年,第一个实用的减振器由一法国人特鲁芬特研制成功并被安装到摩托赛车上。
该车的前叉悬置于弹簧上,同时与一个摩擦阻尼件相连,以防止摩托车的振颤。
减振器的结构发展主要经历了以下几种发展形式:加布里埃尔减振器,它是由固定在汽车大梁上的罩壳和装在其里面的涡旋形钢带组成,钢带通过一个弹簧保持其张力,钢带的外端与车桥轴端连接,以限制由振动引起的弹跳量。
平衡弹簧式减振器,这是加到叶片弹簧上的一种辅助螺旋弹簧。
由于每一个弹簧都有不同的谐振频率,它们趋向于抵消各自的振颤,但同时也增大了悬架的刚性,所以很快就停止了使用。
空气弹簧减振器,空气弹簧不仅兼有弹簧和吸振的作用,而且常常可省去金属弹簧。
第一个空气弹簧减振器是1909年由英国考温汽车工厂研制成功的。
它是一个圆柱形的空气筒,利用打气筒可以把空气经外壳上部的气阀注满空气筒,空气筒的下半部分容纳一个由橡胶和帘布制成的膜片。
因为它被空气所包围,所以其工作原理与充气轮胎相似,它的主要缺点是常常泄漏空气。
液压减振器,第一个实用的液压减振器是1908年由法国人霍迪立设计的。
悬架系统设计指南
5.1 主流独立悬架结构介绍 .................................................................................................................14 5.2 四轮定位 .........................................................................................................................................18 5.3 弹性元件设计 .................................................................................................................................23 5.3 导向机构设计 .................................................................................................................................35 5.4 减振器设计 .....................................................................................................................................42 5.5 悬架的抗制动点头、抗加速仰头性能计算 .................................................................................48 6 样机试验 ....................................................................................................................................................49
减震器支架设计
横梁的设计及校核1.由于悬架试验需要在两立柱上固定直线滑轨,而导轨的拆装十分困难,所以横梁必须在保留导轨的基础上设计,为此制定了三个方案:(1)横梁设计在导轨下方,不需跨过导轨,直接固定在立柱内平面上。
(2)横梁做成H型,跨过导轨和立柱,固定在立柱的两侧面上,如图3.6 (a)。
(3)横梁头部跨过导轨固定在立柱内平面上,如图3.6 (b)。
图3.6 (a)横梁设计方案一图3.6 (b)横梁设计方案二方案(1)设计简单,结构简单,加工制造比较方便,但由于需做悬架试验,导轨下方空间较少,如留出足够空间,必然对悬架试验造成一定影响,同时也浪费部分材料,所以此方案不可行,由图3.6(a)、(b)对比可知,方案(2)结构比较复杂,同时制造使用材料较多,且强度不能保证,从经济和安全上考虑决定最终选用第(3)个方案。
即,跨过导轨安装横梁,在不使用时可以拆掉,不影响悬架试验时滑轨的运动。
2.下面对横梁的强度进行校核已知横梁两端有螺栓固定在立柱表面,横梁的材料选用45钢,其许用弯曲应力是[σ]=200Mpa, 许用切应力[]τ=30Mpa ;横梁长度L=430mm,横梁中部截面为长方形,高h=50mm.宽b=30mm ,横梁中间部位受力,最大F=4448N 为减振器的最大拉压力。
根据已知条件作出受力图如图3.7:图 3.7 横梁受力分析根据其受力,计算横梁所受的剪切应力和弯矩:Q=F/2=2224N;Mmax=m N l Q .16.478215.022242=⨯=÷⨯可以画出其剪力图和弯矩图,如图3.8 (a )、(b )所示:图3.8 (a )剪力图图3.8 (b )弯矩图由图可知危险截面在中间位置由公式max 2423Q Rτ⨯=∏bh Q 23 )1( 计算梁的最大切应力max2423Q R τ⨯=∏[]Mpa Mp 30224.203.0.05.0222243=<=⨯⨯τ[]Mp Mp bh M WM 2003.3805.003.016.47866:)2(22max max max max =<=⨯⨯=⨯==σσσ计算最大弯曲正应力由公式故横梁的强度符合要求3.螺钉的校核横梁采用内六角圆柱头螺钉固定故校核螺钉所受的剪切力,螺钉选用GB 70—85 M12 ⨯60 材料为45钢,其许用切应力为[]Mp 30=τ。
减震器设计
设计这类减震器时,压缩、复原行程的阻尼力Fc、Fr应依据悬架系统所需的阻尼特性曲线确定。
因此,设计工作变为基于以上表达式的逆次求解。
因此,可以将设计研发重点分为两个方面,其一是确定D和d;其二为确定阀的参数以获得适宜的压力差△P。
设计阶段,可参阅现有的产品初步选定D和d,在设计过程中再作一定调整相比照拟容易一些。
然而节流阀的设计较为繁琐,因为它对油液特性、温度的变化等较为敏感,需要在初步设计根底上进展一定量的试验来确定。
1、设计参数分析假设由减震器上、下部的输入导致缸筒与连杆间的相对运动速度为V=X1-X2,那么通过节流阀的流量为Qc=V·Ar依据流体力学理论,油液流过小圆孔时所产生的压降△P为△P=〔Kiu+Kou+Kc〕þV2∕2 〔3〕式中K△为流体流过节流孔时的沿程损失系数;Kout、Kiu分别为节流孔出、入口的压力损失系数,紊流状态下Kout、Kin的影响很小,可忽略不计;þ为油液密度,Q为流速,与流量Qc和节流断面积A之间的关系为V=Qc∕A。
紊流状态下,沿程压力损失系数Kc与雷诺数N,水力半径R和流通管道长度L之间的关系为;0.316 LKc=———·—— (4)N0.25 4R式中N=4RV∕r,r为油液的运动粘度。
由此得到:0.0279L·þ Ar△Pc=——————〔——〕7∕4·r1∕4·V7∕4 (5) R5∕4 A或:0.0279L·þ△Pc= —————·r1∕4·Qc7∕4〔6〕R3∕4·A7∕4式〔6〕可用于初始设计阶段,主要是依据所选择油液的特性,在已经确定的D和d根底上初选节流阀的L和A,预算出△P,使其满足悬架系统阻尼特性曲线的要求;而式〔5〕可用于调整设计参数,与式〔1〕一起调整D和d的大致范围,以及节流阀的有关参数。
2、阀体参数的选择分析对双作用筒式减震器而言,提供阻尼力的大小取决于工作时相对速度V,当减震器工作在低速工作段时,阻尼力主要由单个阀的节流产生;当V值处在中高速段时,同时有两组(或以上)的阀起节流作用。
轿车悬架系设计指南华福林编写
轿车悬架系设计指南(华福林编写)1.概言一辆性能优良的轿车,几乎所有的整车性能,譬如:动力性、制动性、操纵稳固性、平顺性、舒适性、经济性、通过性及平安性,都与底盘设计的好坏息息相关。
所谓汽车底盘,一样指车身(含内外饰件)之外的所有零部件总成装配成的平台而言,而汽车设计业内人士那么还需将发动机、车架及它们相配套的零部件总成排除在外。
因此,汽车设计部门往往将《底盘》概念在两大系统之内,即:1.传动系统:含聚散器、变速器、分动器、传动轴、前后驱动桥(包括主减速器、差速器、半轴等)。
2.行路系统:含前轴(包括车轮及轮毂)系、转向系、制动系、悬架系等。
体会丰硕的驾驶员在对一辆新车试车后,除对其动力性、经济性评判外,该车的操纵稳固性、平顺性也是他们津津乐道的话题。
诸如车辆高速行驶下“发不发飘”、“摆不摆头”、“跑不跑偏”等等。
以下仅就个人近50年汽车设计的体会,围绕轿车悬架结构因素对性能阻碍的简明讨论,供缺乏悬架设计体会的设计师参考。
2.汽车的悬架系2-1 悬架系是汽车的重要部份。
它是将车身(含车架)与车桥(轴)弹性联结的部件,要紧功能是:2-1-1 减缓由于路面不平引发的振动和冲击,保证良好的平顺性。
2-1-2 衰减车身和车桥(或车轮)的振动。
2-1-3 传递车轮和车身(含车架)之间的各类力(垂直力、纵向力和横向力)和力矩(制动力矩和反作使劲矩)。
2-1-3 保证汽车行驶时的稳固性。
2-2 汽车悬架通常由弹性元件、导向机构和减震器组成。
2-2-1弹性元件(含各类弹簧)用来传递垂直力和减缓冲击;当汽车横向角刚度较小时,还需装横向稳固器(横向稳固杆)以减小车身的横向转动角(侧倾角)。
2-2-2导向机构用来操纵车轮相关于车身的运动特性,以保证必要的稳固性,同时传递除垂直力之外的力和力矩。
2-2-3减震器仅用来衰减车身和车桥(或车轮)的振动振幅,它并非能改变悬架的“硬软”程度。
2-3 悬架结构一样分为两大类:独立悬架和整体桥悬架(非独立悬架)。
- 1、下载文档前请自行甄别文档内容的完整性,平台不提供额外的编辑、内容补充、找答案等附加服务。
- 2、"仅部分预览"的文档,不可在线预览部分如存在完整性等问题,可反馈申请退款(可完整预览的文档不适用该条件!)。
- 3、如文档侵犯您的权益,请联系客服反馈,我们会尽快为您处理(人工客服工作时间:9:00-18:30)。
实用标准文档 文案大全 悬架用减振器设计指南 一、功用、结构: 1、功用 减振器是产生阻尼力的主要元件,其作用是迅速衰减汽车的振动,改善汽车的行驶平顺性,增强车轮和地面的附着力.另外,减振器能够降低车身部分的动载荷,延长汽车的使用寿命.目前在汽车上广泛使用的减振器主要是筒式液力减振器,其结构可分为双筒式,单筒充气式和双筒充气式三种. 导向机构的作用是传递力和力矩,同时兼起导向作用.在汽车的行驶过程当中,能够控制车轮的运动轨迹。
汽车悬架系统中弹性元件的作用是使车辆在行驶时由于不平路面产生的振动得到缓冲,减少车身的加速度从而减少有关零件的动负荷和动应力。如果只有弹性元件,则汽车在受到一次冲击后振动会持续下去。但汽车是在连续不平的路面上行驶的,由于连续不平产生的连续冲击必然使汽车振动加剧,甚至发生共振,反而使车身的动负荷增加。所以悬架中的阻尼必须与弹性元件特性相匹配。 2、产品结构定义 ①减振器总成一般由:防尘罩、油封、导向座、阀系、储油缸筒、工作缸筒、活塞杆构成。
②奇瑞现有的减振器总成形式: 实用标准文档
文案大全 二、设计目的及要求: 1、相关术语 *减振器 利用液体在流经阻尼孔时孔壁与油液间的摩擦和液体分子间的摩擦形成对振动的阻尼力,将振动能量转化为热能,进而达到衰减汽车振动,改善汽车行驶平顺性,提高汽车的操纵性和稳定性的一种装置。
*阻尼特性 减振器在规定的行程和试验频率下,作相对简谐运动,其阻力(F)与位移(S)的关系为阻尼特性。在多种速度下所构成的曲线(F-S)称示功图。
*速度特性 减振器在规定的行程和试验频率下,作相对简谐运动,其阻力(F)与速度(V)的关系为速度特性。在多种速度下所构成的曲线(F-V)称速度特性图。
*温度特性 减振器在规定速度下,并在多种温度的条件下,所测得的阻力(F)随温度(t)的变化关系为温度特性。其所构成的曲线(F-t)称温度特性图。
*耐久特性 减振器在规定的工况下,在规定的运转次数后,其特性的变化称为耐久特性。 *气体反弹力 对于充气减振器,活塞杆从最大极限长度位置下压到减振器行程中心时,气体作用于活塞杆上的力为气体反弹力。
*摩擦力 实用标准文档 文案大全 减振器以0.005m/s的速度运行时存在的阻力,定义为摩擦力。 *空程 由于减振器油里面有较大的汽泡导致的,在减振器运动中出现的阻尼力偏小或没有阻尼力的某段行程。
*减振器行程 减振器最大长度与最小长度之差称为减振器行程。
2、系统要求 ①在悬架压缩行程内,减振器阻尼应较小; ②在悬架伸张行程内,减振器阻尼应较大; ③当车桥(或车轮)与车架(或车身)的相对速度过大时,减振器阻尼力应保持在一定的限度之内;
三、设计注意事项: a、通过计算只能得到减振器的大致阻力范围。如何使减振器与弹性元件得到一个准确的最佳匹配值,则是一个很复杂的问题,要考虑到汽车使用条件、整车参数、悬架形式、各件之间的摩擦,减振器的速度特性等因素,在计算后,进行实验修正。 b、如果减振器示功试验时阻力相差15﹪,有经验的评分员已可在道路试验时感觉出来。一般人员也能分辨出阻力相差30﹪。由于目前一般整车中的减振器阻力是不能在行驶时调整的,所以减振器是不可能同时满足各种路况及载重要求的。例如满足汽车重载要求时,空载时就显得太硬;在沥青路面行驶时觉得合适,在坏路行驶时必然摇晃不停。因此选择减振器时只能采用折衷办法,满足一种主要的工况而略为“照顾”一下其它工况。例如:吉普车减振器阻力应选规则得比满载坏路行驶时的最佳值略小一些,在好路上行驶时只得让减振器显得硬一些。相反,小客车减振器阻力应选择得比好路高速行驶时最佳值略大一些,而在坏路行驶时只能让车身略有摇晃。 c、选择的阻力是示功试验时的阻力,而减振器在整车中的实际工作阻力要大于其5~10倍。 实用标准文档
文案大全 四、设计流程: 1、正向设计:
2、逆向设计:
五、计算和验证: 5.1、正向设计: 5.1.1、减振器阻尼力特性的确定 油液经过节流阀产生的阻尼力为节流阀两侧压力差与承压面积的乘积,压力实用标准文档 文案大全 P为:
QaCQPd2222 2/mmN 式中:-油液密度,3/mmkg; Q-通过阀的流量,smm/3;
a-节流孔面积,2mm;
dC-流量系数;
-节流孔形状和油液粘度有关的系数;
5.1.2、振器相对阻尼系数的确定 减振器装车后的基本参数,一般用相对阻尼系数表示,相对阻尼系数为:
KM2 式中:-相对阻尼系数; -减振器阻尼系数(阻尼特性的导数);
K-悬架刚度,mmN/;
M-簧上质量,kg;
当相对阻尼系数1时,产生非周期域运动,很大时虽然能在共振区很快衰减振动,但在非共振区内激振增大。当1时,产生周期运动,很小时振动衰减很慢,共振振幅过大。一般相对阻尼系数值在0.3~0.5范围内,对于无阻尼的弹性元件去上限,弹性元件和悬架导向机构中存在阻尼时取下限。 为迅速衰减汽车振动又不把大的路面冲击传递到车身上,一般把减振器拉伸和压缩阻力按8:2~6:4的比例分配。
选择减振器阻尼力系数时,应考虑悬架导向杆的杠杆比和减振器的安装角度的影响,下图所示 实用标准文档 文案大全 减震器阻尼力系数应为: 22cos2im mmsN/ 式中:i-杠杆比,ani -减振器轴线与垂直线的夹角; -簧上质量固有频率。 5.1.3、减振器主要尺寸的确定 选择减振器尺寸时主要考虑一下两点:在工作速度范围内油液压力适当,能够得到稳定的阻力值,容易保证油封的可靠性;减振器具有足够的散热面积,防止因温度过高引起阻力衰减或减振器早期失效。 作缸径的确定: 可根据减振器最大拉伸阻力和最大允许压力近似求出工作缸径。
2max14pFD mm 式中:D-作缸径,mm;
p-工作缸允许最大压力,一般为3~42/mmN; maxF-减振器最大拉伸阻力,N; -减振器杆直径与工作缸之比,双筒减振器为0.4~0.5,单筒减实用标准文档 文案大全 振器为0.3~0.35。 求出缸径后,参照JB1459标准,选择合适的标准工作缸径。
减振器储油缸直径DDc57.1~35.1,工作缸与储油缸壁厚一般取1.5~2.0mm。 5.1.4、减振器行程的选择
减振器总行程S由上行程S1,下行程S2两部分组成,即: S= S1+ S2 a、上行程:S1=L-Lmin L为汽车满载时减振器两吊耳处中心距。 S1应略大于悬架系统满载上行程(假设缓冲块脱落)。 b、下行程:S2=Lmax-L 由于减振器可承受一部分反跳拉力,所以S2只要略大于弹簧的静挠度。 S1、 S2选择不当必然使减振器工作不正常,因而产生拉脱压毁、撞坏或安装支架断裂等现象。
5.2、有参考车的设计(逆向设计) 5.2.1输入项: 基准车与开发车的车辆状态量: a、Design Load时的前轮Sprung Weigh(单侧轮)Wf b、Design Load时的后轮Sprung Weigh(单侧轮)Wr c、前轮端的Spring Rate(单侧轮)Kf d、后轮端的Spring Rate(单侧轮)Kr e、前S/ABS的Lever Ratio-- rf f、后S/ABS的Lever Ratio-- rr 5.2.2、检测基准车前后S/ABS的单件零件阻尼力特性: 按0.05、0.1、0.3、0.6、1.0m/s五组速度测减振器拉伸、压缩时的阻尼力特性。 5.2.3、计算出基准车以及新开发车的前后轮临界阻尼力系数Ccf、Ccr:
W:Design Load时的单侧轮的Sprung Weigh KWCc8.92实用标准文档 文案大全 K:轮端的Spring Rate 5.2.4、计算基准车前后轮端的阻尼力系数Cf、Cr:
5.2.5、计算HA车轮端的阻尼力系数比C/CC 由于设计思想为H13前后轮轮端的阻尼力特性和参考车HA车相同,因此,两车的C/CC一致,则得出H13车轮端阻尼力系数为:
5.2.6、计算新开发车的S/ABS单个零件的阻尼力特性: 单个减振器速度=轮端速度×r 综上得:
这样我们就得到一组阻尼力-速度特性值,可以大致做出阻力-速度特性曲线:
六、主要试验项目和方法: 6.1阻力特性试验 试验零件总数量:≥2支。 a、程序或标准: (1)、减振器要垂直放在试验台上; (2)、试验温度是20 ± 2 °C,试验前试件在恒温箱中保存至少6h以上; (3)、试验的开始位置在减振器行程的中点; (4)、试验行程100mm,试验行程中点与减震器的行程中点一致;
单个零件速度单个零件阻尼力=2rC1313CHCAAHCCCC
213/13HrCABSSH单个零件速度=单个零件的阻尼力车