乙烯裂解工艺流程
乙烯裂解工艺流程

每台裂解炉的TLE,均连接到一个共用汽包上的热虹吸系统。
产生的12.4MPa蒸汽,进入每个汽包的锅炉给水,用急冷油和对流段的烟道气预热。
蒸汽在TLE中产生,并在裂解炉对流段的盘管中过热到520度,过热器出口温度由锅炉给水注入量(注入到部分过热蒸汽中)来控制。
调节温度之后,蒸汽返回到对流段,以过热到需要的温度。
设计的裂解炉热效率约为95%(低热值)。
燃料燃烧系统设计是侧壁烧嘴或底部烧嘴,既可烷富氢燃料又可烧富甲烷燃料。
通常的燃料是氢气和甲烷的混合物,大约总热量的40%来自底部烧嘴,其余由侧壁烧嘴来平衡。
在急冷区,经常引起设备腐蚀,大部分是在与水接触的金届表面上产生的,其原因是水里溶解着硫化氢、氯化氢、碳酸气,较低分子量的环烷烃酸和脂肪酸或者苯酚等的腐蚀性物质和酸性物质。
腐蚀性物质和酸性物质,是在热裂解反应管上生成的.经过分析判明是甲酸(HC00H)、乙酸(CH3C00H)、苯酚(C6H50H)、丙烯酸(CHz=CHC00H)、丙酸和环烷酸,在冷凝稀释蒸汽中一般含量为百万分之几至百万分之几十。
硫化氢、碳酸气这些物质是在热裂解阶段生成的,无法防止,一班采用中和和注入防腐剂来防止腐蚀。
从各TLE出来的裂解物料汇人一条总管中,经泊急冷后送到汽油分馏塔。
在汽油分馏塔中,裂解气被进一步冷却,裂解燃料油从塔底抽出并送往汽提塔,汽油和较轻组分从塔顶获出。
从裂解气中回收的热量,经过一个急冷油循环系统用于产生稀释蒸汽。
汽油分馏塔采用在急冷塔中冷凝的汽油回流。
配备一个粘度控制系统.以维持循环急冷油的粘度在一个可接受的范围内。
汽油分馏塔底温反设计控制在185度,低于预期的粘度控制温度。
从乙烷裂解炉出来的物料,在一个独立的油急冷器中与一部分循环的急冷油接触,汇合后物流送往帖度控制罐。
昭顶馏分与来自其它裂解炉的全部物流混合.一起经油急冷,再到汽油分馏塔。
裂解燃料油汽提塔底物也送往粘度控制罐,底部抽出的重燃料油,用急冷水冷却并送往界区外。
乙烯裂解制取纯苯的工艺流程
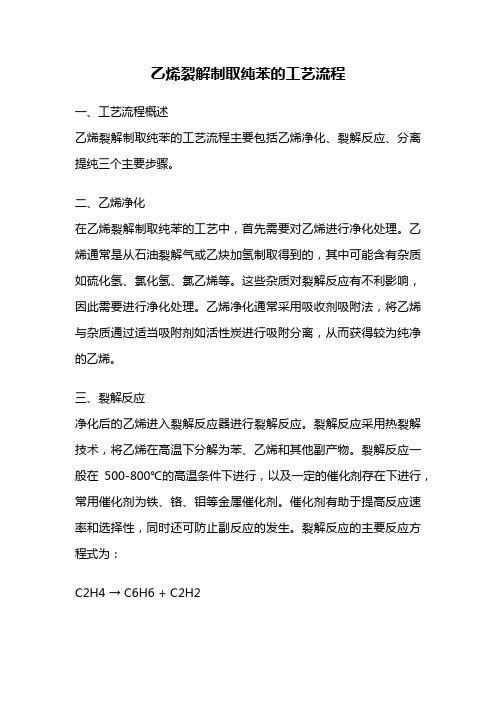
乙烯裂解制取纯苯的工艺流程一、工艺流程概述乙烯裂解制取纯苯的工艺流程主要包括乙烯净化、裂解反应、分离提纯三个主要步骤。
二、乙烯净化在乙烯裂解制取纯苯的工艺中,首先需要对乙烯进行净化处理。
乙烯通常是从石油裂解气或乙炔加氢制取得到的,其中可能含有杂质如硫化氢、氯化氢、氯乙烯等。
这些杂质对裂解反应有不利影响,因此需要进行净化处理。
乙烯净化通常采用吸收剂吸附法,将乙烯与杂质通过适当吸附剂如活性炭进行吸附分离,从而获得较为纯净的乙烯。
三、裂解反应净化后的乙烯进入裂解反应器进行裂解反应。
裂解反应采用热裂解技术,将乙烯在高温下分解为苯、乙烯和其他副产物。
裂解反应一般在500-800℃的高温条件下进行,以及一定的催化剂存在下进行,常用催化剂为铁、铬、钼等金属催化剂。
催化剂有助于提高反应速率和选择性,同时还可防止副反应的发生。
裂解反应的主要反应方程式为:C2H4 → C6H6 + C2H2四、分离提纯裂解反应产物中含有苯、乙烯和其他副产物,需要进行分离提纯以获得纯苯。
分离提纯通常采用精馏法,通过对产物进行多级精馏,将苯与其他组分分离。
在分馏塔中,底部收集到的是富含苯的液体,称为合成苯;而顶部收集到的是富含乙烯和其他副产物的气体,称为裂解气。
接下来可以对合成苯进行进一步处理和提纯,以获得所需的纯苯产品。
五、工艺优化及设备选择为了提高乙烯裂解制取纯苯的工艺效率和产品质量,可以采取一些工艺优化措施。
例如,通过调整裂解反应温度、催化剂种类和用量,可以提高苯的产率和选择性。
此外,还可以使用先进的分离设备如精馏塔、萃取塔和吸附塔等,以增加分离效率和产品纯度。
六、工艺原理乙烯裂解制取纯苯的工艺原理是基于乙烯分子的裂解反应特性。
乙烯分子在高温条件下经过热裂解反应,发生碳碳键的断裂,生成苯和乙烯等反应产物。
裂解反应是一个热力学控制的过程,因此高温条件有助于提高反应速率和产物选择性。
催化剂的存在可加速反应速率,并调控反应产物的生成。
乙烯生产工艺流程及设备认知 裂解工艺流程
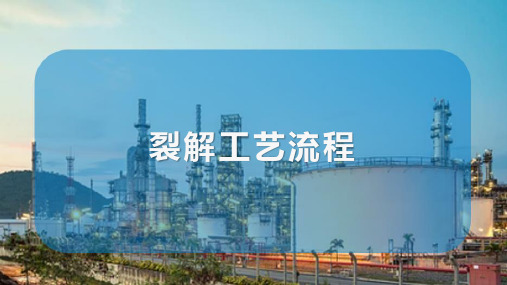
裂解工艺流程
管式炉裂解典型工艺流程图
BWF-锅炉给水:QW-急冷水;QO一急 冷油;FO-燃料油;CW-冷却水:MS-中
压蒸汽: 1一原料油泵;2一原料预热器;3一裂解 炉;4-急冷换热器:5-汽包;6-急冷器; 7一汽油分馏塔(油冷塔);8-燃料油汽 提塔;9一急冷油泵:10-燃料油泵:11水洗塔;12-油水分离器;13-急冷水泵; 14-裂解汽油回流泵;15-工艺水泵;16急冷水冷却器;17-工艺水汽提塔:18工艺水泵;19,20-稀释蒸汽发生器;21-
裂解工艺流程
目
CONTENTS
录
01 裂解工艺流程 02 烃类的裂解过程的特点
01
裂解工艺流程
裂解工艺流程
原料 水蒸气
798 ℃
450~550 ℃
249 ℃
109 ℃
裂解炉裂解
急冷换热器
油急冷器
精馏塔
C
C 裂解气 水冷塔 裂解汽油
蒸汽发生器
C 裂解燃料油
管式炉裂解流程框图
裂解工艺流程
原料加热及反应系统 急冷锅炉及高压水蒸气系统
小
结
1. 烃类的裂解 工艺流程
2. 烃类的裂解 过程的特点
裂解工艺流程
3. 油急冷及燃料油系统
从急冷换热器出来的裂解气, 进入急冷器。在急冷器内,裂解 气与急冷油直接接触冷却至 250℃以下,然后汇合送入油冷 塔。在油冷塔,裂解气进一步被 冷却,裂解燃料油从油冷塔底抽 出,被泵送到燃料油汽提塔。塔 底的燃料油通过燃料油泵送人燃 料油罐。
裂解工艺流程
4. 水急冷和稀释水蒸气系统
汽油汽提塔
裂解工艺流程
1.原料加热及反应系统
工艺流程—裂解炉生产乙烯

利用裂解炉生产乙烯热裂解特点:高温,吸热量大低烃分压,短停留时间,避开二次反响的发生反响产物是简单的混合物热裂解的供热方式如下所示:直接供热法:工艺简单,裂解气质量低,本钱过高。
其裂解工艺始终没有很大进展!工业上烃类裂解生产乙烯的主要过程为:原料热裂解裂解气预处理〔包括热量回收、净化、气体压缩等〕裂解气分别产品乙烯、丙烯及联产物等。
一、原料烃组成对裂解结果的影响影响裂解结果的因素:原料特性;裂解工艺条件;裂解反响器型式;裂解方法等。
族组成,% 大庆 145~ 成功 145~ 任丘 145~ 大港 145~350℃〔质量〕350℃350℃350℃原料特性是最重要的影响因素!(一) 原料烃的族组成、含氢量、芳烃指数、特性因数裂解产物分布的影响1. 族组成〔简称 PONA 值〕定义:是指原料烃分子中所含各族烃的质量百分比P —烷族烃 N —环烷族烃 O —烯族烃A —芳香族烃从表 1-7 作一比较,在管式裂解炉的裂解条件下,原料愈轻,乙烯收率愈高。
随着烃分子量增大,N+A 含量增加,乙烯收率下降,液态裂解产物收率渐渐增加。
表 1-7 组成不同的原料裂解产物收率裂解原料 乙烷 丙烷 石脑油 抽余油 轻柴油 重柴油 原料组成特性 PPP+NP+N P+N+A P+N+A 乙烯 84* 44.0 31.7 32.9 28.3 25.0丙烯1.4 15.6 13.0 15.5 13.5 12.4 主要产物收率,%〔质量〕 丁二烯 1.43.44.75.3 4.8 4.8 混合芳烃 0.4 2.8 13.7 11.0 10.9 11.2其它12.8 34.2 36.835.842.546.6*包括乙烷循环裂解原料的 PONA 值常常被用来推断其是否适宜作裂解原料的重要依据。
表 1-8 介绍我国几个产地的轻柴油馏分族组成。
表 1-8 我国常压轻柴油馏分族组成P 烷族烃正构62.641.021.6 53.223.030.2 65.430.025.4 44.4烷烃异构烷烃环烷族烃其中24.216.45.62.2 28.019.67.01.4 23.817.45.41.0 34.420.610.43.4 一环二环三环以上A 芳烃其中一环二环三环以13.27.05.30.9 18.813.55.00.3 10.87.23.40.2 21.213.27.30.7 上我国轻柴油作裂解原料是较抱负的。
乙烯生产方法选择—烃类热裂解制乙烯
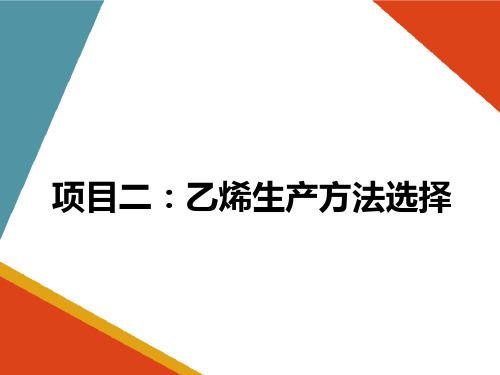
任务二 烃类热裂解制乙烯
1、原料加热及反应系统
由原料罐区来的石脑油等原料换热后,与DS (180℃, 0. 55MPa)按相应的油汽比混合进入裂解 炉对流段加热后进入辐射段。
物料在辐射段炉管内迅速升温进行裂解反应(以控 制辐射炉管出口温度COT的方式控制裂解深度, COT大约为800~900℃)。裂解气出口温度COT通 过调节每组炉管的烃进料量来控制,要求高于裂 解气的露点(裂解气中重组分的露点),若低于露点 温度,则裂解气中的较重组分有一部分会冷凝, 凝结的油雾黏附在急冷换热器管壁上形成流动缓 慢的油膜,既影响传热,又容易发生二次反应。
任务二 烃类热裂解制乙烯
4、水急冷和稀释水蒸气系统
油冷塔顶的裂解气,通过和水冷塔中的循环 急冷水进行直接接触进行冷却和部分冷凝, 温度冷却至28℃,水冷塔的塔顶裂解气被送 到裂解气压缩工段。
任务二 烃类热裂解制乙烯
4、水急冷和稀释水蒸气系统
急冷水和稀释水蒸气系统的生产目的是用水 将裂解气继续降温到40°C左右,将裂解气 中所含的稀释蒸汽冷凝下来,并将油洗时没 有冷凝下来的一部分轻质油也冷凝下来,同 时也可回收部分热量。稀释蒸汽发生器接收 工艺水,发生稀释蒸汽送往裂解炉管,作为 裂解炉进料的稀释蒸汽,降低原料裂解中烃 分压。
任务二 烃类热裂解制乙烯
二.世界乙烯原料情况
平均下来石脑油是最主要的,占了43%,排 第二名是乙烷占36%。但是具体到各国或地 区的情况却不同。欧洲、中国、日本一样主 要采用石脑油作原料。
任务二 烃类热裂解制乙烯
二.世界乙烯原料情况
典型的是西欧乙烯71%来自石脑油,来自轻 烃和LPG的各占11%仅7%来自乙烷。而美 国恰恰相反,主要使用乙烷作原料。它的乙 烯52%来自乙烷,22%来自轻烃5%来自石 脑油。
乙烯裂解流程
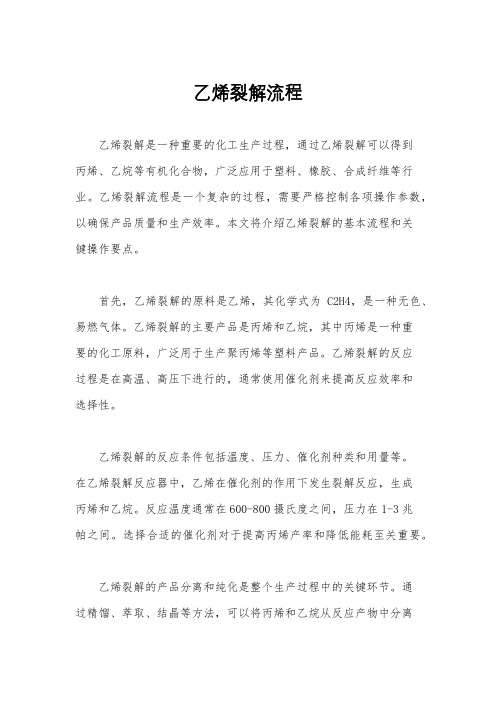
乙烯裂解流程乙烯裂解是一种重要的化工生产过程,通过乙烯裂解可以得到丙烯、乙烷等有机化合物,广泛应用于塑料、橡胶、合成纤维等行业。
乙烯裂解流程是一个复杂的过程,需要严格控制各项操作参数,以确保产品质量和生产效率。
本文将介绍乙烯裂解的基本流程和关键操作要点。
首先,乙烯裂解的原料是乙烯,其化学式为C2H4,是一种无色、易燃气体。
乙烯裂解的主要产品是丙烯和乙烷,其中丙烯是一种重要的化工原料,广泛用于生产聚丙烯等塑料产品。
乙烯裂解的反应过程是在高温、高压下进行的,通常使用催化剂来提高反应效率和选择性。
乙烯裂解的反应条件包括温度、压力、催化剂种类和用量等。
在乙烯裂解反应器中,乙烯在催化剂的作用下发生裂解反应,生成丙烯和乙烷。
反应温度通常在600-800摄氏度之间,压力在1-3兆帕之间。
选择合适的催化剂对于提高丙烯产率和降低能耗至关重要。
乙烯裂解的产品分离和纯化是整个生产过程中的关键环节。
通过精馏、萃取、结晶等方法,可以将丙烯和乙烷从反应产物中分离出来,并得到所需的纯品。
同时,对于未反应的乙烯和其他副产物也需要进行回收利用,以提高原料利用率和减少废物排放。
在乙烯裂解过程中,安全生产是首要任务。
高温、高压的反应条件下,需要严格控制设备的运行状态,确保设备的安全可靠。
同时,对于催化剂的选择和管理也需要特别注意,避免因催化剂失活导致生产事故。
总的来说,乙烯裂解是一项重要的化工生产过程,涉及到反应工程、分离工程、安全工程等多个方面的知识。
只有严格控制各项操作参数,合理设计生产工艺,才能保证乙烯裂解过程的稳定运行和高效生产。
希望本文对乙烯裂解流程有所帮助,谢谢阅读。
乙烯裂解工艺流程

乙烯裂解工艺流程
乙烯裂解是一种重要的石化工艺,用于将乙烷裂解成乙烯和丙烯。
以下是乙烯裂解的工艺流程。
首先,将乙烷和催化剂混合,在高温高压环境中进行裂解反应。
乙烷分子在催化剂的作用下发生断裂,生成乙烯和丙烯等烃类化合物。
这个反应是一个自发反应,需要消耗能量来维持反应温度和压力。
然后,将反应产物通过冷凝器进行冷却。
由于乙烯和丙烯的沸点较低,可以通过适当的降温使其冷凝成液体,便于进一步处理。
接下来,液态产物通过分离器进行分离。
乙烯和丙烯具有不同的沸点,可以通过调整分离器的温度和压力来实现二者的分离。
分离后的乙烯可以用于制造塑料、橡胶、纤维和化肥等产品。
此外,还会产生一些副产物,如乙烷和丙烷等未反应的烃类化合物。
这些副产物通常通过再循环回到裂解反应器中,以提高产物的利用率。
最后,还需要对废气进行处理。
乙烷裂解反应中会产生大量的废气,例如二氧化碳、氮气和未反应的乙烷等。
这些废气通常通过气体分离器进行分离和净化处理,减少对环境的污染。
在乙烯裂解的工艺流程中,温度、压力和催化剂的选择非常重要。
适当的反应温度和压力可以提高反应速率和产物选择性,
从而提高乙烯产率。
催化剂的选择会直接影响反应的效果和催化剂的寿命。
在实际工业生产中,还会有其他的辅助工艺,如能量回收和产品处理等,以提高工艺的经济性和环境友好性。
通过不断的技术创新和工艺改进,乙烯裂解工艺可以更加高效、可持续地产生乙烯和丙烯等重要石化产品,满足市场需求。
乙烯裂解装置工艺流程详细介绍ppt
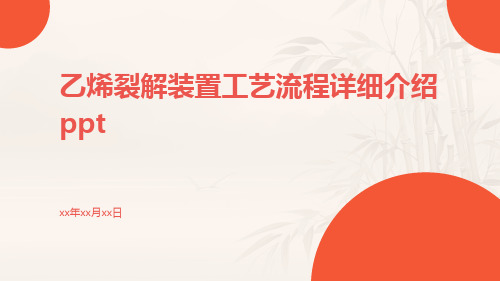
产品分离与处理
压缩和冷凝
将裂解气压缩并冷凝成液态,以便分离出各种产品。
产品分离
将液态混合物分离成各个组分,包括乙烯、丙烯、轻烃、燃料 油等。
产品精制
通过精馏等工艺,提纯各组分产品,以满足市场和用户需求。
燃料气系统与火炬系统
燃料气系统
将燃料气进行压缩、干燥和净化处理,作为燃料供应装置使用。
火炬系统
出。
裂解装置的应用
乙烯裂解装置是石化工业中的重要 生产设备之一,主要用于生产高附 加值的石化产品,如聚乙烯、环氧 乙烷、乙二醇等。
VS
此外,乙烯裂解装置也可以用于生 产燃料油和燃料气等产品。
02
乙烯裂解装置的工艺流程
原料预处理
原料选择
选择低硫、低氮、低重烃的轻质原油,以保证装置运行稳定和产品品质。
本文将详细介绍乙烯裂解装置的工 艺流程和技术特点。
裂解装置简介
裂解装置通常由进料、预热、裂解、冷却、 产品分离和排放等系统组成。
进料系统的作用是将原料送入装置中,预热 系统的作用是将原料预热到一定温度,裂解 系统的作用是在高温高压下将原料转化为乙 烯等产品,冷却系统的作用是将裂解产物迅 速冷却以防止二次反应,产品分离系统的作 用是将乙烯等产品分离出来并进行精制,排 放系统的作用是将裂解产生的废气和废液排
情况。
严格遵守工艺参数
02
操作过程中需严格遵守工艺参数,如温度、压力、流量等,以
确保装置正常运行。
操作人员资质
03
操作人员需具备相应的资质和经验,了解装置的操作规程和应
急处理措施。
安全风险与防范措施
高温高压风险
乙烯裂解装置运行过程中存在高温高压状态,可能引发烫伤、机械伤害等问题。应采取相 应的防护措施,如佩戴高温手套、穿防静电工作服等。
- 1、下载文档前请自行甄别文档内容的完整性,平台不提供额外的编辑、内容补充、找答案等附加服务。
- 2、"仅部分预览"的文档,不可在线预览部分如存在完整性等问题,可反馈申请退款(可完整预览的文档不适用该条件!)。
- 3、如文档侵犯您的权益,请联系客服反馈,我们会尽快为您处理(人工客服工作时间:9:00-18:30)。
每台裂解炉的TLE,均连接到一个共用汽包上的热虹吸系统。
产生的12.4MPa蒸汽,
进入每个汽包的锅炉给水,用急冷油和对流段的烟道气预热。
蒸汽在TLE中产生,并在裂解炉对流段的盘管中过热到520度,过热器出口温度由锅炉给水注入量(注入到部分过热蒸汽中)来控制。
调节温度之后,蒸汽返回到对流段,以过热到需要的温度。
设计的裂解炉热效率约为95%(低热值)。
燃料燃烧系统设计是侧壁烧嘴或底部烧嘴,既可烷富氢燃料又可烧富甲烷燃料。
通常的燃料是氢气和甲烷的混合物,大约总热量的40%来自底部烧嘴,其余由侧壁烧嘴来平衡。
在急冷区,经常引起设备腐蚀,大部分是在与水接触的金届表面上产生的,其原因是水里溶解着硫化氢、氯化氢、碳酸气,较低分子量的环烷烃酸和脂肪酸或者苯酚等的腐蚀性物质和酸性物质。
腐蚀性物质和酸性物质,是在热裂解反应管上生成的.经过分析判明是甲酸
(HC00H)、乙酸(CH3C00H)、苯酚(C6H50H)、丙烯酸(CHz=CHC00H)、丙酸
和环烷酸,在冷凝稀释蒸汽中一般含量为百万分之几至百万分之几十。
硫化
氢、碳酸气这些物质是在热裂解阶段生成的,无法防止,一班采用中和和注入
防腐剂来防止腐蚀。
从各TLE出来的裂解物料汇人一条总管中,经泊急冷后送到汽油分馏塔。
在汽油分馏塔中,裂解气被进一步冷却,裂解燃料油从塔底抽出并送往汽提塔,汽油和较轻组分从塔顶获出。
从裂解气中回收的热量,经过一个急冷油循环系统用于产生稀释蒸汽。
汽油分馏塔采用在急冷塔中冷凝的汽油回流。
配备一个粘度控制系统.以维持循环急冷油的粘度在一个可接受的范围内。
汽油分馏塔底温反设计控制在185度,低于预期的粘度控制温度。
从乙烷裂解炉出来的物料,在一个独立的油急冷器中与一部分循环的急冷油接触,汇合后物流送往帖度控制罐。
昭顶馏分与来自其它裂解炉的全部物流混合.一起经油急冷,再到汽油分馏塔。
裂解燃料油汽提塔底物也送往粘度控制罐,底部抽出的重燃料油,用急冷水冷却并送往界区外。
来自汽油分馏培的塔顶气体与急冷塔中再循环的水直接逆流接触,被冷却并部分冷凝。
来自急冷塔的循环热水向一些工艺单元提供低位热能,如c4原料蒸发器、裂解气加热器、脱乙烷塔再沸器、脱丙烷塔中间再沸器、丙烯精饵塔再沸器和甲烷汽提培再沸器。
急冷水经冷却水和预热裂解炉进料进一步冷却。
急冷塔顶部气体温度为40度、压力为0.04MPa(表),送往裂解气压缩机。
在急冷塔冷凝的汽油,从培底的循环急冷水和冷凝的
稀释蒸汽中分离出来,一部分冷凝的烃类作为回流返回汽油分馏塔,其余部分与来自压缩系统的烃冷凝物一起在汽油汽提塔中校稳定处理。
稳定后的烃类同脱丁烷塔底物料汇合,送往裂解汽油加氢装置。
在急冷系统中冷凝的稀释蒸汽在进入工艺水汽提塔之前先预热,在汽提塔中用直接蒸汽和再沸器中产生的蒸汽进行汽提,以脱除酸性气和易挥发的烃。
为了防止工艺水汽提塔产生泡沫,可加入消泡剂,如Ndc071—D5,其含量约为20x10-6。
干净的工艺水在稀释蒸汽发生器中被中压蒸汽和急冷油汽化,产生的蒸汽在作为裂解炉的稀释蒸汽再次使用以前,要用中压蒸汽过热。
工艺水汽提塔顶蒸汽在返回急冷塔之前,预热汽提塔的进料。
为了防止腐蚀,在工艺水汽提塔顶部和进料中,可分别加入3%(质)氨水使其含量最高为200x10-6 (最大),5%(质) NaOH使其含量为(50-100)x10-6,急冷水泵人口可加入5%(质)Na0H 0—1.5x10-6。