生产线不良或异常处理流程图
产线异常处理流程及技巧
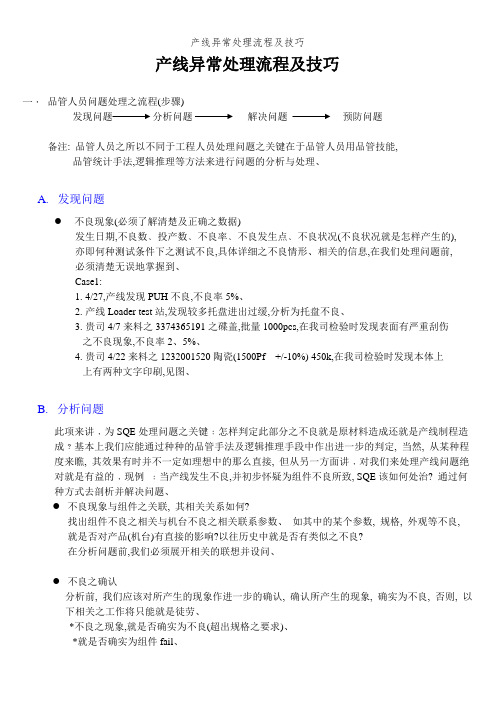
产线异常处理流程及技巧一.品管人员问题处理之流程(步骤)发现问题分析问题解决问题预防问题备注: 品管人员之所以不同于工程人员处理问题之关键在于品管人员用品管技能,品管统计手法,逻辑推理等方法来进行问题的分析与处理、A.发现问题●不良现象(必须了解清楚及正确之数据)发生日期,不良数﹑投产数﹑不良率﹑不良发生点﹑不良状况(不良状况就是怎样产生的),亦即何种测试条件下之测试不良,具体详细之不良情形、相关的信息,在我们处理问题前,必须清楚无误地掌握到、Case1:1.4/27,产线发现PUH不良,不良率5%、2.产线Loader test站,发现较多托盘进出过缓,分析为托盘不良、3.贵司4/7来料之3374365191之碟盖,批量1000pcs,在我司检验时发现表面有严重刮伤之不良现象,不良率2、5%、4.贵司4/22来料之1232001520陶瓷(1500Pf +/-10%) 450k,在我司检验时发现本体上上有两种文字印刷,见图、B.分析问题此项来讲﹐为SQE处理问题之关键﹕怎样判定此部分之不良就是原材料造成还就是产线制程造成﹖基本上我们应能通过种种的品管手法及逻辑推理手段中作出进一步的判定, 当然, 从某种程度来瞧, 其效果有时并不一定如理想中的那么直接, 但从另一方面讲﹐对我们来处理产线问题绝对就是有益的﹐现例﹕当产线发生不良,并初步怀疑为组件不良所致, SQE该如何处治? 通过何种方式去剖析并解决问题、●不良现象与组件之关联, 其相关关系如何?找出组件不良之相关与机台不良之相关联系参数、如其中的某个参数, 规格, 外观等不良,就是否对产品(机台)有直接的影响?以往历史中就是否有类似之不良?在分析问题前,我们必须展开相关的联想并设问、●不良之确认分析前, 我们应该对所产生的现象作进一步的确认, 确认所产生的现象, 确实为不良, 否则, 以下相关之工作将只能就是徒劳、*不良之现象,就是否确实为不良(超出规格之要求)、*就是否确实为组件fail、相关的不良之判定,需经验之积累、针对一些比较模糊的规格,希望尽量能量化来定义、如: 杂音的判定,焊锡性不良之判定等、●分析过程及方法: 前提:( 若初步分析为原材不良所致)组件不良确认:a.交叉实验法(尽可能多机种, 多状态, 多次实验作确认, 尽可能比较全面地得到第一信息、)*单体简单比较(单次)*多因子之间比较(机种, F/W, 线别, DISC,厂商,Date Code)*单体多次比较(PCBA, Mega)举例: ( PUH, MOTOR, CHIP-C等)b、借助我们现有之零件测试设备对零件参数作测试确认、这一点要求我们所有的SQE 人员在执行时日常的工作中应不断地提升我们对零件, 产品相关的认知, 不断提升 IQC检验之精准度, 可用性及实效性, 尽可能地从组件本身参数特性及与我们产品之相配性作检测, 如塑料件(尺寸, 实配治具等)、以厂商认可的测试判定方法来进行量化的判定、b.待不良确认后, 用罗辑, QC方法进一步展开原因之深入调查、品管人员在处理问题时,最重要的一点同时也就是最首要的工作就是进行相关数据的收集统计并分析,从而得出我们所需求的信息、*不良现象之集中性? 变羿性? 就是我们考究的重点、在此仅以材料羿常处理查德检表, 以供各位在日常工作中能灵活运用, 势必在处理相关问题时会得心应手、1.问题确认➢不良现象发生之日期, 时间?➢在哪一段时间这不良率DPPM就是多少?➢不良数就是否集中在哪一条件?➢不良数就是否集中在哪一个班?➢不良数就是否集中在哪一产品型号(版别)?➢不良品之DATE CODE 为何? 就是否有信集中之趋势?➢不良数就是否集中在哪一个基板位置?➢以前就是否有类似现象发生过?➢不良就是否集中在哪一个测试治具?➢仪嚣治具就是否有维修或不良?➢不良出现前后, 生产条件就是否有变更(5M: 人,机,材,法,量测)➢其她供货商之供料就是否有类似疵病?➢IQC 之SIP就是否有针对此项疵病作检验?➢IQC就是否有检验仪具与能力?以上经由收集相关资料来进一步判定不良现象之集中性及相关之 QC手法(查检表, 层别法), 对不良问题点作初步的判定并相关对策之实施、不良分析Case1:●手插5条线、●Function test ‘27项’不良、●初步分析为C221电容不良(Chip-C)d、利用前后制程的一致性来推断不良产生之原因、利用各前后制程之测试状况作相应之判定、相关以上不良问题而产生的一种重要的分析方法------实验法、各种实验的实施,能有效地辅助我们进行问题的分析与处理、C、解决问题内部➢满足产线正常生产为第一需求, 利上以上相关判定之信息, 换用其她DATE CODE, 厂商, 批次等料正常上线并追踪。
过程异常处理流程图

品质工程师根据品质数据判定是否可以结案
8
材料异常 NO
品质主管 由品质给出临时 方案并主导解决
异常信息传递
9 10 11 12 编制:吴烧威
效果验证
NO
O K
由责任部门给出长 期纠正措施
上报副总,组队 分析原因
依来料异常处 理流程处理
确定处理对策
NO 品质工程师以及巡检进行监督实施,并对效果确认
结案 审核:马文虎
工作内容
1、异常包括:1、巡检人员在首件检验不良、巡线过程发现工艺 纪律不符、产品抽检不良;2、生产人员在生产过程中发现的不 符合作业SOP或产品异常等; 2、生产过程中,生产班组长、员工以及品质巡检发现异常后应 立即向所属部门报告,经主管确认后发出《生产品质异常纠偏单 》; 2、IPQC将生产异常纠偏单交给品质工程师进行分析
步骤
IPQC
1
生产部
工作流程
过程异常处理流程图
工程\研发\QE
生产副总
SQE\IQC
开始
生产过程中发生异常 发出《生产品质异常纠偏单》 2
标识/隔 离
3
责任部门认定
4 NO
5
6
作业异常Βιβλιοθήκη 工艺/设计异常生产主管确认
工程主管确认
由责任主管给 出临时方案, 并现场指导
生产部按异常解决方案
7
处理异常,并记录损失
在确认异常后,由巡检立即对生产产品进行标识/隔离,必要的 需暂时停线
品质工程师对异常现象进行确认,并认定异常责任部门,涉及到 比较专业技能的内容需寻求品质主管或相关开发工程师进行分析
OCAP品质异常处理流程图-经典

分析造成异 常現象的 原
因
拟定临时对策
拟定永久对策
NG
供应 商改 善对 策
总经理
总经理核 准
作业指导
1、生产部门主导品质异常的提出; 2、品质部判定异常是否正确,NG继续生 产,OK进入第2段落; 3、异常标准: 1h内同种不良超10﹪;
1、品质部判定异常是否要停线,OK则停线进入第 3段落,NG由QE主导品质异常的处理; 2、停线标准: 见《LED生产车间质量问题停线制度》
段落
1 2 3
生产部
品质异常联 络单
停线并开出
品质部
判定是否
开异常单 NG
OK
OK
判定是否
停线
NG QE主导异常会议
异常原因分析 及确认
4
产线开始
5
试做或返工
不合格品
6
继续生产 7
8
生产制作流程
9
NG 确认对策 是否有效
OK
品质异常 联络单
结束
技术部
OCAP工作流程图
开发部
采购部
分析造成异 常現象的原
1、总经理负责改善对策的核准; 2、生产部按有效的改善对策继续生产, 停线通知废除;
1、生产部开始转入正常的《生产制作流 程》; 2、品质部负责《品质异常联络单》上传 、归档。
流程结束。
1、技术部负责对责任部门拟定临时改善 对策进行纠正,措施包含原材料、在制品 、成品等的处理方式; 2、如是原材料问题导致品质异常,采购 部负责落实供应商改善对策及改善效果追 踪; 3、技术部负责对责任部门拟定永久改善 对策进行预防,措施包含原材料、在制品 、成品等的处理方策是否有效,验证OK进入第7段落, NG则逐级返回第5段落重新拟定临时/永 久对策;
生产异常处理流程

生产异常处理流程生产异常处理流程————————————————————————————————作者:————————————————————————————————日期:1目的:为更加规范生产现场发生异常时,能及时准确地反映并能通过相关人员确认、分析、及时解决,确保生产顺利进行特制订此规定。
2范围:适用公司生产中心下辖所有生产线上发生的异常现象。
3权责:3.1生产管理人员:负责提出异常,并确认异常是否属实,协助相关人员处理异常;3.2工程部:负责生产线上异常分析,找出异常原因,提出改善对策。
3.3品质部:负责跟进改善结果及效果确认,对来料进行管控,并对此类异常制定纠正预防措施。
3.4总经办:负责生产过程中重大异常的方案决策、处理稽核。
3.5采购部:负责来料异常商务方面的异常处理。
3.6计划部:负责异常发生时的总体计划的协调和异常发生产生的工时和物料的核实,组织相关部门一起分析、处理异常。
4异常处理作业流程:4.1生产部按生产排期表提前到仓库领料并安排做首件并量产。
4.2生产部在生产中发现产品、物料与样品不符,生产出的成品达不到标准要求或来料无法使用等现象时,及时上报生产领班、品质部等相关人员确认。
4.3生产领班、品质部确认异常可接受,通知生产线继续生产,如确认异常不能接收则由生产领班或IPQC在异常发生的10分钟内开出《制程异常报告》,所有的《制程异常报告》由车间的IPQC拿到相关部门签字确认,最后由品质文员将单据发出,4.4经技术部分析,给出初步分析结果,结果分为工艺问题、设计问题、来料问题。
4.5由PE分析是来料问题、制程问题还是设计问题,并将分析的原因及解决方案记录在《制程异常报告》表上,并写给到工程部主管签名确认,如果需要返工或改变工艺则由工程部PE做出两块样品给到品质部确认,品质判定方案可行后,PE要在现场跟进生产部员工的作业方法、品质是否与样品一致。
PE必须要等到生产员工做出2件合格品后方可离开现场,整个过程品质部要跟踪监控确认。
制程异常处理流程图

备注:停线超过30分钟还无法确定及找到方案时,QE或PE职员下令拉长换线处理,并通知生产管理.
为了保障生产顺利,PE安排生产进行选别或加工时,生产无条件必须接受,生产可提出工时申请单进行工时索赔.
批准:生产作成来料异常处理流程产线来料异常发生
QE/PE 确定IQC 来
QE 影响程度确认QE 通知IQC 确认通知生产及计划
IQC 确认无库存
继续生产联络IQC 小大产线产品能选别生产暂时安排人继续生产OK OK OK 无法选别能让步接收吗NG
NG 停线处理
供应商联系及对策
QE/PE 指令暂时:选别
生产统计工时交要求供应商对:
产线不良返工
仓库不良返工纠正预防措施单对策回复检讨、结案
IQC 内部检讨与对IQC 确认有库存
仓库有没有不同质量是OK 的吗?继续生产OK OK 代仓库有没有不同批次
或不同日期的物料质量是OK 的吗?继续生产
OK OK NG
同一批物料也是质量是OK 的吗?领取仓库物料继
OK OK NG
NG QE/PE 指令暂时:加工IQC 统计不良数
据通知供应商QE 工作范围IQC 工作范围。
ocap品质异常处理流程图经典

81、生产部开始转入正常的《生产制作流程》;2、品质部负责《品质异常联络单》上传、归档。
OCAP工作流程图2341、品质部判定异常是否要停线,OK则停线进入第3段落,NG由QE主导品质异常的处理;2、停线标准:见《LED生产车间质量问题停线制度》1、品质部书面通知生产部停线;2、QE负责主导品质异常会议的召开 及组织品质异常的评审;1、QE进行品质异常原因分析并作进一步的确认,OK进入第5段落;2、如涉及生产工艺、产品结构、电路设计等问题则转技术部、开发部协助分析(物随单走);3、异常分析为原材料原因进入供应商改善第5段落,如是设计不良、生产作业问题则逐级返回技术部;段落总经理技术部作业指导生产部品质部1、技术部负责对责任部门拟定临时改善对策进行纠正,措施包含原材料、在制品、成品等的处理方式;2、如是原材料问题导致品质异常,采购部负责落实供应商改善对策及改善效果追踪;3、技术部负责对责任部门拟定永久改善对策进行预防,措施包含原材料、在制品、成品等的处理方式;1、总经理负责改善对策的核准;2、生产部按有效的改善对策继续生产,停线通知废除;流程结束。
579开发部611、生产部门主导品质异常的提出;2、品质部判定异常是否正确,NG继续生产,OK进入第2段落;3、异常标准:1h内同种不良超10﹪;1、品质部负责确认生产部或供应商的改善对策是否有效,验证OK进入第7段落,NG则逐级返回第5段落重新拟定临时/永久对策;采购部品质异常联络单总经理核准判定是否停线停线并开出拟定临时对策产线开始试做或返工不合格品拟定永久对策QE 主导异常会议确认对策是否有效NGOKOKNG生产制作流程NG供应商改善对策异常原因分析及确认分析造成异常現象的原因分析造成异常現象的原因OK结束继续生产NG品质异常联络单判定是否开异常单。
质量异常处理流程图

零(合)检检验记录(专检)质量记录台帐
产品标识卡
质量问题通知单
退修品通知单
质量问题通知单
紧急/例外放行申请单
退修品通知单
质量问题通知单
紧急/例外放行申请单
退修品通知单
质量问题通知单
紧急/例外放行申请单退修品通知单
质量问题通知单
紧急/例外放行申请单
十你想过普通的生活,就会遇到普通的挫折。你想过最好的生活,就一定会遇上最强的伤害。
质量异常处理基准
异常
发生时流程
1、停止生产2、隔离标识3、报告班长4、等待指示
1首次发现的不合格
2初物不合格
3关键工序的不合格
4性能项目的不合格
5不良品的连续发生
6其它不合格
责任者
操作工
上序操作工、班长
检查员
工艺员
车间主任
质量部长
技术部长
主管经理
处置对策
内容
异常定义:连续三件不合格以及控制图出现异常。
车间主任:组织追溯不合格品;向质量部报告。
不合格品处置;停产或再生产指示
对不合格进行评审,对工程进行确认,向质量部报告。
对不合格进行评审,对工程进行确认,明确处理方法。
对不合格进行评审。
再生产品质
确认
品质确认后作业开始。
追溯无误后恢复生产。
确认生产的产品无误。
对不合格进行功能性能试验。
记录
零(合)检检验记录(自检)
处置方式:停机、隔离、标识、向上序操作工、班长、检验员报告,等待作业。异常排除后再作业。
上序操作工:自检追溯确认,返工返修后再检验。
班长:互检、追溯、确认,向车间主任报告。处置不合格。
生产线不良或异常处理流程图

正式开出《校正 行为报告》
制订解决方案
生产、工 程、品检
监督生产线作业员按工艺文件作业情况; 用样机校正各测试位,并填写样机校位记录表; 检查各仪器设备运行情况; 每小时填写《工序质量日报表》。
《样机校 位报告》
生产、工 程、品检、 SMT
组长、领班、物料员、IPQC、工程人员、SMT 管 理人员要有问题意识,及时迅速发现异常或不 良,能预见不良或异常产生的影响和后果。 当单项不良低于 3%时,生产管理要及时将不良品 交修理维修,修理将修好的不良品要贴修理编 号,并从第一 QC 位下机。
1. 目的 及时、迅速处理,解决生产过程中阻碍生产顺利进行的各种问题,保证生产的正常运行。
2. 适用范围 生产线不良或异常包括物料、工艺、设备、产品功能、作业及其它方面使生产不能顺利 进行的各种因素。
3. 生产线不良或异常处理流程/职责和工作要求
流程
职责
工作要求
相关文件 /记录
开始 巡线 发现生产 不良或异常
为报告》
程、 品检、 组长、领班、物料员、IPQC、工程人员、SMT 管 《 不 合 格
SMT
理人员开出的《校正行为报告》单要如实反映问 品 控 制 程
题,不得夸大事实。
序》
作业问题应在《校正行为报告》单上描述纠正改
善措施。
设计、物料问题按《不合格品控制程序》执行。
工 程 、 生 修正工艺要求;
产 、 开 发 、 重新修订物料规格要求;
品检
修改设计存在的不完善因素。
流程
NO 评审 方案
YES
职责
工作要求
相关文件 /记录
工程、开 发 、 品 管 、 根据方案的要求进行评审,经技术和品质评估通 品检、生产 过可实施方案,未通过可继续进行分析确认。
- 1、下载文档前请自行甄别文档内容的完整性,平台不提供额外的编辑、内容补充、找答案等附加服务。
- 2、"仅部分预览"的文档,不可在线预览部分如存在完整性等问题,可反馈申请退款(可完整预览的文档不适用该条件!)。
- 3、如文档侵犯您的权益,请联系客服反馈,我们会尽快为您处理(人工客服工作时间:9:00-18:30)。
为报告》
程、 品检、 组长、领班、物料员、IPQC、工程人员、SMT 管 《 不 合 格
SMT
理人员开出的《校正行为报告》单要如实反映问 品 控 制 程
题为报告》单上描述纠正改
善措施。
设计、物料问题按《不合格品控制程序》执行。
工 程 、 生 修正工艺要求;
产 、 开 发 、 重新修订物料规格要求;
不良品或异常 现象确认
正式开出《校正 行为报告》
制订解决方案
生产、工 程、品检
监督生产线作业员按工艺文件作业情况; 用样机校正各测试位,并填写样机校位记录表; 检查各仪器设备运行情况; 每小时填写《工序质量日报表》。
《样机校 位报告》
生产、工 程、品检、 SMT
组长、领班、物料员、IPQC、工程人员、SMT 管 理人员要有问题意识,及时迅速发现异常或不 良,能预见不良或异常产生的影响和后果。 当单项不良低于 3%时,生产管理要及时将不良品 交修理维修,修理将修好的不良品要贴修理编 号,并从第一 QC 位下机。
工程人员根据问题判断类型(作业、物料、设计) 总不良高于 25%以上时,应勒令停线处理。 参照《不合格品控制程序》运行。
当单项不良超过 3%,在 15 分钟内未能解决时,
由生产线组长、领班、物料员、IPQC、工程人员、
SMT 管理人员根据不良或异常状况开出《校正行 《 校 正 行
生 产 、 工 为报告》;
品检
修改设计存在的不完善因素。
流程
NO 评审 方案
YES
职责
工作要求
相关文件 /记录
工程、开 发 、 品 管 、 根据方案的要求进行评审,经技术和品质评估通 品检、生产 过可实施方案,未通过可继续进行分析确认。
实施改善方案
工 程 、 开 依照方案内容验证实施情况,并将有关记录,实 《 纠 正 措
发 、 品 管 、 施中出现问题等信息提交责任部门。
施管理程
品检、生产 参照《纠正措施管理程序》
序》
问题改善后 的跟进
生 产 、 工 跟进改善后其状况变化,对同样的问题在解决方 《不合格
程、品检 案后再次出现,应上报上级部门。对标准的变更, 品 控 制 程
应参照《不合格品控制程序》执行。
序》文件
结束
1. 目的 及时、迅速处理,解决生产过程中阻碍生产顺利进行的各种问题,保证生产的正常运行。
2. 适用范围 生产线不良或异常包括物料、工艺、设备、产品功能、作业及其它方面使生产不能顺利 进行的各种因素。
3. 生产线不良或异常处理流程/职责和工作要求
流程
职责
工作要求
相关文件 /记录
开始 巡线 发现生产 不良或异常
编制:
审核:
批准: