炉外精炼- 合成渣洗
炉外精炼
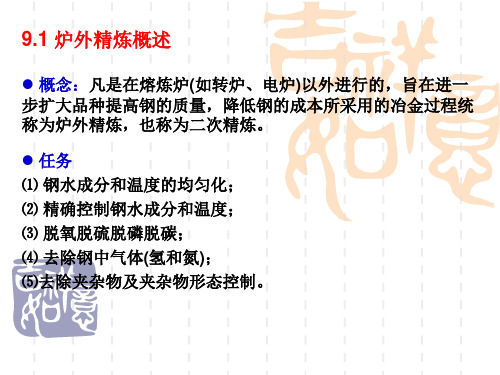
ASEA-SKF法的特点: 将炼钢过程分为两步:由初炼炉(如电炉、转炉)熔化钢铁料, 调整含碳量和温度;然后在钢包炉内,在电磁搅拌的条件 下,进行电弧加热、真空脱气、除渣和造新渣、脱硫、真 空脱氧和脱碳、调整成分与温度,最后吊出钢包进行浇注。
ASEA-SKF法的主要设备: ① 钢包由非磁性材料制成,有滑动水口,可直接用于浇注; ② 电磁感应搅拌器使钢水产生搅拌作用; ③ 真空炉顶及电气设备; ④ 电视—摄影及其他辅助设备如钢包移动装置,原料加入装 置和集尘装置等。
形式: ⑴ 底吹。是通过安装在钢包底部一定位置的透气砖(或 其他形式的喷口),将氩气吹入钢液。 ⑵ 顶吹。吹氩喷枪插入钢包内的钢液中,在接近包低 处将氩气吹入钢液。
最常见的有两种:CAS和CAS—OB。 ⑴ CAS 概念:采用强吹氩工艺将渣液面吹开后,将封闭的浸渍 钟罩内迅速形成氩气保护气氛,避免了钢水氧化的工艺 称为CAS法,又称SAB法。
9.1 炉外精炼概述
概念:凡是在熔炼炉(如转炉、电炉)以外进行的,旨在进一 步扩大品种提高钢的质量,降低钢的成本所采用的冶金过程统 称为炉外精炼,也称为二次精炼。
任务 ⑴ 钢水成分和温度的均匀化; ⑵ 精确控制钢水成分和温度; ⑶ 脱氧脱硫脱磷脱碳; ⑷ 去除钢中气体(氢和氮); ⑸去除夹杂物及夹杂物形态控制。
基本手段 (1) 渣洗;(合成渣渣洗) (2) 搅拌;(CAS钢包吹氩精炼) (3) 真空;(RH真空循环脱碳法) (4) 加热;(LF) (5) 喷吹。(WF喂丝法)
主要作用 ⑴ 提高质量扩大品种的主要手段; ⑵ 优化冶金生产流程,提高生产效率节能降耗降低成本 主要方法; ⑶ 炼钢—炉外精练—连铸—热装轧制工序衔接。
幻灯片 12
特点: ⑴ 除底部吹氩外,在钢包液面上加一沉入罩,罩内充有从钢 液中排出的或专门导人的氩气。 ⑵ 通过罩上方的加料口,可添加合成渣料和微调钢液成分用 的合金。 优点: ⑴ 均匀钢水成分和温度,且控制快速、准确,操作方便; ⑵ 提高合金收得率,且稳定; ⑶ 净化钢液,去除夹杂物,连铸坯质量提高; ⑷ 基建、设备投资少,操作费用低。
120t区域精炼工艺3-16详解

2018年10月12日
31
真空状态下,脱氢效果与以下因素有关: ☆初始含量:初始含量越低,达到最终含量的处理时间越短。 钢液中初始含量并不取决于大气中的氢分压,钢液中〔H〕 主要是空气中水蒸气和原材料中水分带入的。 ☆处理时间:处理时间越长,最终〔H〕含量越低,但是当 〔H〕含量降低到一定程度,随着处理时间的延长,最终 〔H〕含量变化不大。因为此时钢水静压力和传质速度是其 限制环节。 ☆真空度:真空度提高,气相中氢分压降低,有利于脱氢反 应。 ☆吹氩搅拌:通过吹氩搅拌,相应增加了气液反应界面;提 高了熔池内传质速度;氩气泡上浮时,溶解在钢中的〔H〕 会以原子的形式进入氩气泡,氩气泡相当于一个个微小的真 空室。 ☆表面活性元素:〔O〕、〔S〕等表面活性元素含量的降 低,有利于〔H〕原子通过气液界面。
2018年10月12日
3
4.喷吹 喷吹也称喷射,是将反应剂利用气流直接加入冶金 熔体中的一种炉外精炼方法。由于它简便、高效, 所以也经常作为一种精炼手段,组合到其他炉外精 炼方法中。 喷吹技术利用气体的搅拌作用增加了粉状精炼剂和 钢液的接触界面,显著改善冶金反应的动力学条件。 因此可以实现快速脱硫、脱磷、脱氧,提高合金收 得率,促使夹杂物变性等功能。 RH配备喷吹功能,可以进行深脱硫,生产超低硫钢。
2018年10月12日
4
5.喂线 喂线是通过喂线机将钙、铝、硅钙、钡系合金等制成的包芯 线或铝等金属线高速加入到钢液的方法。具有如下特点: ·合金收得率高; ·能解决特种合金的加入问题; ·避免合金加入时的吸氮; ·投资费用少,应用范围广,操作简便。 喂线技术可单独应用。也可应用到各种精炼方法中。目前各 种炉外精炼方法中都添加了喂线设施,并且以推广到中间包 喂线、结晶器喂线。 采用不同的包芯线、金属线,喂线技术可具有脱氧、脱硫、 夹杂物变性、防止水口堵塞等功能。
炉外精炼教程
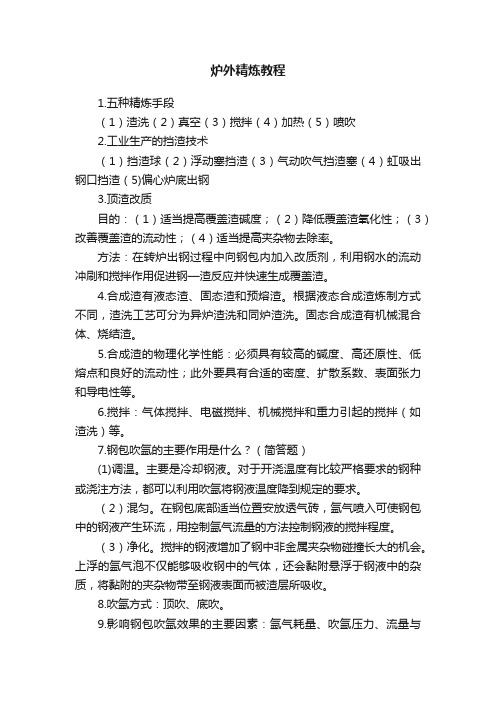
炉外精炼教程1.五种精炼手段(1)渣洗(2)真空(3)搅拌(4)加热(5)喷吹2.工业生产的挡渣技术(1)挡渣球(2)浮动塞挡渣(3)气动吹气挡渣塞(4)虹吸出钢口挡渣(5)偏心炉底出钢3.顶渣改质目的:(1)适当提高覆盖渣碱度;(2)降低覆盖渣氧化性;(3)改善覆盖渣的流动性;(4)适当提高夹杂物去除率。
方法:在转炉出钢过程中向钢包内加入改质剂,利用钢水的流动冲刷和搅拌作用促进钢—渣反应并快速生成覆盖渣。
4.合成渣有液态渣、固态渣和预熔渣。
根据液态合成渣炼制方式不同,渣洗工艺可分为异炉渣洗和同炉渣洗。
固态合成渣有机械混合体、烧结渣。
5.合成渣的物理化学性能:必须具有较高的碱度、高还原性、低熔点和良好的流动性;此外要具有合适的密度、扩散系数、表面张力和导电性等。
6.搅拌:气体搅拌、电磁搅拌、机械搅拌和重力引起的搅拌(如渣洗)等。
7.钢包吹氩的主要作用是什么?(简答题)(1)调温。
主要是冷却钢液。
对于开浇温度有比较严格要求的钢种或浇注方法,都可以利用吹氩将钢液温度降到规定的要求。
(2)混匀。
在钢包底部适当位置安放透气砖,氩气喷入可使钢包中的钢液产生环流,用控制氩气流量的方法控制钢液的搅拌程度。
(3)净化。
搅拌的钢液增加了钢中非金属夹杂物碰撞长大的机会。
上浮的氩气泡不仅能够吸收钢中的气体,还会黏附悬浮于钢液中的杂质,将黏附的夹杂物带至钢液表面而被渣层所吸收。
8.吹氩方式:顶吹、底吹。
9.影响钢包吹氩效果的主要因素:氩气耗量、吹氩压力、流量与吹氩时间及气泡大小等。
10.能量耗散速率(比搅拌功率):单位时间内,向1t钢液提供的搅拌能量作为描述搅拌特征和质量的指标。
11.常用的加热方法主要是电弧加热,化学加热(化学热法)、燃料燃烧加热、电阻加热等12.燃料燃烧加热存在哪些不足?(1)由于燃烧的火焰是氧化性的,而炉外精炼时总是希望钢液处在还原性气氛下,这样钢液加热时,必然会使钢液和覆盖在钢液面上的精炼渣的氧势提高,不利于脱硫、脱氧这样一些精炼反应的进行。
炉外精炼--合成渣洗

2.2.2.1 合成渣的乳化和上浮
合成渣有液态渣和固态渣,多数为液态渣。
合成渣洗的主要目的是降低钢中的氧,硫 和非金属夹杂物含量,它可以把[O]降至 0.002%、[S]降至0.005%甚至0.003%。
合成渣洗过程:在一个专门容器内(一般 使用电弧炉)熔炼合成渣(液态),炉渣温 度控制在1680~1750ºC,出钢前将熔炼好 的合成渣倒入钢包内并移至炉下,在出钢 过程中钢液流冲击包内的合成渣,充分搅 拌,钢液与合成渣充分接触,使钢液得到 渣洗。为了使钢渣充分搅拌接触,需大出 钢口、深坑出钢,即钢水有一定的冲击力, 钢流有一定的高度和速度,使钢水尽快出 净。混冲高度一般为3~4米,出钢时间要 短,如10t炉子35~55秒,20t炉子45~50 秒,合成渣用量一般为钢水量的5~6%, 进行渣洗的钢液出钢前应扒除炉渣,然后 再出钢。
2.1.1 挡渣技术
做好出钢时的挡渣操作,尽可能地减少 初炼炉的氧化渣进入钢包内是发挥精炼 渣精炼做用的前提。
2.1.1 挡渣技术
为消除或把带入钢包内的渣量降至最低, 目前用于工业生产的挡渣技术有: ( l )挡渣球。( 2 )浮动塞挡渣。( 3 )气动吹气挡渣塞。( 4 )虹吸出钢口 挡渣。( 5 )偏心炉底出钢
2.1.2 顶渣改质
钢包顶渣(覆盖渣)主要由转炉出钢过 程中流入钢包的渣和铁合金脱氧产物所 形成的渣层组成,渣的氧化性高,碱度 低。
钢包顶渣改质是当前普遍应用的一种钢 包顶渣调质工艺。
1.炉外精炼概述
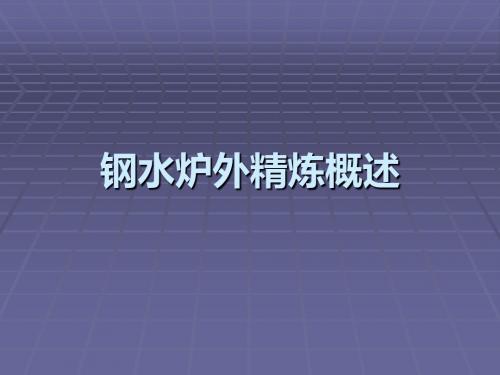
2 创造良好的冶炼反应的热力学和 动力学条件。
通过各种加热精炼手段补偿精炼过程中的温度 损失,使得需要在高温下的脱硫等反应得以顺利进 行。 炼钢过程中的各种冶金反应,多数是在高温下 进行的多相反应,通常化学反应本身进行较快,而 反应物传递到反应界面和生成物脱离反应界面较慢, 成为限制冶金反应速率的因素。通过搅拌、喷吹等 手段提高浓度梯度,增大反应界面,使各种冶金反 应得以顺利进行。
五 炉外精炼的手段
目前炉外精炼的手段有渣洗、真空、搅拌、喷吹和加热 五种。采用一种或几种不同手段的不同组合,就形成了某 一种精炼方法。 1 渣洗:获得洁净钢液并能适当进行脱氧、脱硫和去除 夹杂物的最简便的精炼手段。它是将事先配好的合成渣倒 入钢包内,借出钢时钢流的冲击作用,使钢液与合成渣混 合,从而完成脱氧、脱硫和去除夹杂等精炼任务。 2 真空:将钢液置于真空室内,由于真空作用使反应向 生成气相方向移动,达到脱气、脱氧、脱碳等目的。 3 搅拌:通过搅拌扩大反应界面,加速反应物质的传递 过程,提高反应速度。分为吹气搅拌和电磁搅拌。 4 加热:调节钢液温度的一项重要手段,使炼钢与连铸 更好地衔接。分为电弧加热法和化学加热法。 5 喷吹:用气体作载体将反应剂加入金属液内的一种手 段。喷吹的冶金功能取决于精炼剂的各类,它能完成不同 程度的脱硫、脱氧、合金化和控制夹杂物形态等精炼任务。
钢水炉外精炼概述
一 炉外精炼的产生原因
1 普通炼钢炉(转炉、电炉)冶炼出来 的钢液难以满足对钢的质量(如钢的纯净度 等)越来越高的要求。 2 为了提高生产率,缩短冶炼时间,把 炼钢的一部分任务移到炉外完成。 3 连铸技术的发展,对钢液的成分、温 度和气体的含量等也提出了严格的要求。
二 炉外精炼的概念
3 炉外精炼在炼钢生产中的重要地 位和作用
关于精炼过程中合成渣行为的探讨
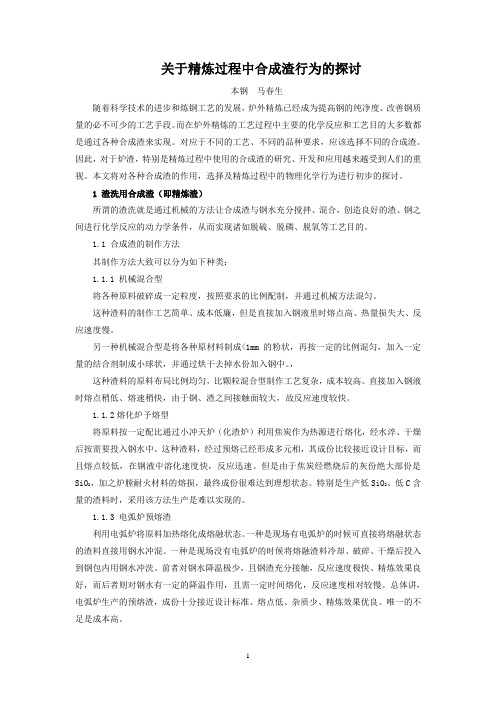
关于精炼过程中合成渣行为的探讨本钢马春生随着科学技术的进步和炼钢工艺的发展,炉外精炼已经成为提高钢的纯净度、改善钢质量的必不可少的工艺手段。
而在炉外精炼的工艺过程中主要的化学反应和工艺目的大多数都是通过各种合成渣来实现。
对应于不同的工艺、不同的品种要求,应该选择不同的合成渣。
因此,对于炉渣,特别是精炼过程中使用的合成渣的研究、开发和应用越来越受到人们的重视。
本文将对各种合成渣的作用,选择及精炼过程中的物理化学行为进行初步的探讨。
1 渣洗用合成渣(即精炼渣)所谓的渣洗就是通过机械的方法让合成渣与钢水充分搅拌、混合,创造良好的渣、钢之间进行化学反应的动力学条件,从而实现诸如脱硫、脱磷、脱氧等工艺目的。
1.1 合成渣的制作方法其制作方法大致可以分为如下种类:1.1.1 机械混合型将各种原料破碎成一定粒度,按照要求的比例配制,并通过机械方法混匀。
这种渣料的制作工艺简单、成本低廉,但是直接加入钢液里时熔点高、热量损失大、反应速度慢。
另一种机械混合型是将各种原材料制成<1mm的粉状,再按一定的比例混匀,加入一定量的结合剂制成小球状,并通过烘干去掉水份加入钢中。
,这种渣料的原料布局比例均匀,比颗粒混合型制作工艺复杂,成本较高。
直接加入钢液时熔点稍低、熔速稍快,由于钢、渣之间接触面较大,故反应速度较快。
1.1.2熔化炉予熔型将原料按一定配比通过小冲天炉(化渣炉)利用焦炭作为热源进行熔化,经水淬、干燥后按需要投入钢水中。
这种渣料,经过预熔已经形成多元相,其成份比较接近设计目标,而且熔点较低,在钢液中溶化速度快,反应迅速。
但是由于焦炭经燃烧后的灰份绝大部份是SiO2,加之炉膛耐火材料的熔损,最终成份很难达到理想状态。
特别是生产低SiO2、低C含量的渣料时,采用该方法生产是难以实现的。
1.1.3 电弧炉预熔渣利用电弧炉将原料加热熔化成熔融状态。
一种是现场有电弧炉的时候可直接将熔融状态的渣料直接用钢水冲混。
一种是现场没有电弧炉的时候将熔融渣料冷却、破碎、干燥后投入到钢包内用钢水冲洗。
炉外精炼各种方法

节流量50-80NL/min,同时测温、取样,加入 硅石2 kg/mm,调整炉渣碱度R=1 .2-1 .5。 • 测温、取样后VD加盖密封,抽真空。 • 真空泵启动期间,调整氩气流量保持30 - 40NL/min。
CAS工艺操作过程
RH钢液循环脱气法
• 主要冶炼高质量产品,如轴承钢、LF钢、硅钢、 不锈钢、齿轮钢等。
• 特点:①反应速度快,表观脱碳速度常数kC可达
到3.5min-1。处理周期短,生产效率高,常与转 炉配套使用。②反应效率高,钢水直接在真空室 内进行反应,可生产H≤0.5×10-6,N≤25×10-6, C≤10×10-6的超纯净钢。③可进行吹氧脱碳和二 次燃烧进行热补偿,减少处理温降;④可进行喷粉 脱硫,生产[S]≤5×10-6的超低硫钢。
VD工艺
• 真空保持时间:真空启动后,工作压力达到67 Pa时,保持时间≥15min。
• 真空保持期间调整氩气流量 70NL/min左右,并 通过观察孔观察钢水沸腾情况,及时调整,保持 均匀沸腾。
• 终脱氧后解除真空、开盖、测温,软吹15- 25min,氩气流量 70-100NL/min左右,控制 渣面微动为宜。
拌,进一步脱碳, 钢液温度达到1670-1750之间. • 6.加合金,微调成分,加铝吹氩搅拌几分 后,破真空浇铸.
AOD炉
AOD炉 主要是冶炼高质量的不锈 钢(C<20ppm,S,P<50ppm)使用更廉 价的原料(采用高碳铬代替低碳铬) 60%-70%的不锈钢产量 炉料:废钢,不锈钢返回料,高碳铬 铁,高碳镍铁 吹炼过程就是温度及氩氧比的控制 T=1680 O2:Ar=4:1(3:1)C下降为0.2% T=1700 O2:Ar=2;1 C下降为0.1% T=1730 O2:Ar=1;2 C下降为0.02% T=1750 O2:Ar=1:3 C下降为0.001%
钢的炉外精炼

但是基本上都是CaO-Al O 渣系,其中CaO含量大 都波动在45%-46%的范围,而Al O 的变动范围 较宽。
2 3 2 3
渣洗合成渣的选择
1)成分。为了取得最佳的精炼效果,要求合成 渣具备相应的物理化学性质,而炉渣成分是 炉渣物理化学性质的决定性因素。
2)熔点。在钢包内用合成渣精炼钢液时,一般 都应用液态渣,因此渣的熔点应当低于被渣 洗钢液的熔点。
●
●
●
●
〇
〇
〇
●
●
主要精炼装置的工艺目标
工艺
LF/VD AOD VOD ASEA-SKF VAD DH RH VD LF WF RH-OB/PB RH-KTB RH-MFB CaO粉 铝氧化 铝氧化 铝氧化 ● ● ● ● ● ● 〇 〇 电热 CaO CaO CaO主要辅助原料CaO升温方法
脱气 电热 吹氧 铝热 电热 电热 ● ● ● ● ● ● ● C 〇 ● ● 〇 〇 〇 P 〇
电磁搅拌——利用电磁感应的原理使钢液产生运动。要使钢
液能够产生电磁感应,靠近电磁感应搅拌线圈的部分钢包壳 应由奥氏体不锈钢制造。 五十年代以来,一些大吨位的电弧炉采用了电磁搅拌,以促 进诸如脱硫、脱氧等精炼反应的进行,保证熔池内温度及成 分的均匀。各种炉外精炼方法中,SKF采用了电磁搅拌,美 国的ISLD也采用了电磁搅拌。 电磁搅拌主要有以下作用: (1)均匀钢包温度和成分; (2)加速金属与熔渣之间的反应; (3)在搅拌处理过程中,Al、C、Mn含量可以调整到规定范围; (4)该工艺成本低,操作简单,处理时间短,热损失小; (5)电磁搅拌可以将非金属夹杂分离,提高钢液洁净度。
3)流动性。用作渣洗的合成渣,要求有较好的流动 性,这样增大渣钢接触界面。
- 1、下载文档前请自行甄别文档内容的完整性,平台不提供额外的编辑、内容补充、找答案等附加服务。
- 2、"仅部分预览"的文档,不可在线预览部分如存在完整性等问题,可反馈申请退款(可完整预览的文档不适用该条件!)。
- 3、如文档侵犯您的权益,请联系客服反馈,我们会尽快为您处理(人工客服工作时间:9:00-18:30)。
2.2.1.2 熔点 在钢包内用合成渣精炼钢液时,一般都应 用液态渣,因此合成渣的熔点应当低于 被渣洗钢液的熔点。 钢的熔点可按下式近似地计算。 Tf=1538-Σ ∆Tj[j%] 各种合成渣的熔点可根据合成渣的成分, 利用相应的相图来确定。
2.2.1.3 流动性 合成渣要求有较好的流动性,流动性是影 响渣在钢液中的乳化程度的重要因素之 一。在炼钢温度下(混冲时钢液温度一般 都大于1600℃,合成渣的温度可按要求 在炼渣炉中调整控制,一般也都在 1650℃以上),其粘度小于0.2Pa•s。
2 炉外精炼的理论与技术基础
2.1 顶渣控制
本节课内容
顶渣控制 渣洗的概念 合成渣的物理化学性能 渣洗的精炼作用 合成渣洗的优缺点(补充)Βιβλιοθήκη 2.1 顶渣控制
2.1.1 挡渣技术 在出钢过程后期,当炉内钢水降低至一 定深度时,出钢口上方的钢水内部会产 生漩涡,它能将表面的炉渣抽引至钢包 中。此外,在出钢临近结束时,也会有 炉渣随着钢水流进钢包内,这个过程被 称为出钢带渣或下渣。
2.1.1 挡渣技术
做好出钢时的挡渣操作,尽可能地减少 初炼炉的氧化渣进入钢包内是发挥精炼 渣精炼做用的前提。
2.1.1 挡渣技术
为消除或把带入钢包内的渣量降至最低, 目前用于工业生产的挡渣技术有: ( l )挡渣球。( 2 )浮动塞挡渣。( 3 )气动吹气挡渣塞。( 4 )虹吸出钢口 挡渣。( 5 )偏心炉底出钢
2.2.1.4 表面张力 表面张力也是影响渣洗效果的一个较为重要 的参数。当用CaO-Al2O3系合成渣洗一般钢 种时,其表面张力=700~1200 dyn/cm。 2.2.1.5 还原性 由渣洗完成的精炼任务决定了渣洗所用的熔 渣都是还原性的,渣中(FeO)含量都很低。 一般都低于0.3%。
2.2.2 渣洗的精炼作用
2.1.2 顶渣改质
钢包顶渣(覆盖渣)主要由转炉出钢过 程中流入钢包的渣和铁合金脱氧产物所 形成的渣层组成,渣的氧化性高,碱度 低。 钢包顶渣改质是当前普遍应用的一种钢 包顶渣调质工艺。
2.1.2 顶渣改质
顶渣改质的目的: 1 适当提高覆盖渣的碱度 2 降低覆盖渣的氧化性 3 改善覆盖渣的流动性 4 适当提高夹杂物去除率
2.2.1.2合成渣脱氧 在渣洗过程中,随着钢液温度的下降,脱 氧反应的平衡向脱氧方向移动,有可能 与钢中溶解的氧反应而进行沉淀脱氧。 还有一部分氧通过扩散进入渣中从而使 钢液脱氧。
扩散脱氧 当还原性合成渣与未脱氧(或脱氧不充分) 的钢液接触时,钢中溶解的氧能通过扩 散进入渣中,从而使钢液脱氧。 LO=钢液中的氧 /渣中氧
2.2.1.3 夹杂物的去除 渣洗过程中夹杂物的去除靠两方面的作用 一方面钢液内的夹杂物与乳化渣滴碰撞, 被渣滴吸附、同化而随渣滴上浮排除。 一方面促进了二次脱氧反应产物的排出, 从而使钢中的夹杂减少。
2.2.1.4 合成渣脱硫 在渣洗过程中,钢液中的S与合成渣中的 CaO作用生成CaS而去除。
2.2.1 合成渣的物理化学性能
2.2.1.1成分 为了取得最佳的精炼效果,要求合成渣具备相 应的物理化学性质,而炉渣的成分是炉渣物 理化学性质的决定性因素。合成渣主要有 CaO-Al2O3系,CaO-SiO2-Al2O3系,CaO-SiO2CaF2系等。其中CaO含量大都波动在45% ~ 60%的范围,MgO波动在6~10%, Al2O3波动 在12~16%。SiO2波动在16~20%。
2.1.2 顶渣改质
顶渣改质的方法:主要是在转炉出钢过 程中向钢包内加入改质剂(或称脱硫剂 、脱氧剂)。 顶渣改质剂的种类:通常采用CaO-CaF2 、CaO-Al2O3-Al、 CaO-CaC2-CaF2
2.2 渣洗
合成渣洗:由炼钢炉初炼的钢水再在钢 包内通过钢液对合成渣的冲洗进一步提 高钢水质量的一种炉外精炼方法。
常用的合成渣洗工艺流程是在专门的炼渣 炉中冶炼合成渣,按要求的成分、温度、 渣量先倒入钢包内,然后吊到电弧炉或 转炉出钢位置,靠出钢钢流的冲击使合 成渣乳化,渣和钢充分接触混合,然后 乳化的渣滴上浮至钢液面,完成钢液的 脱硫、脱氧、去除非金属夹杂、防止吸 气、减少钢水温度散失等精炼任务。
2.2.2.1 合成渣的乳化和上浮 倒入钢包内的合成渣在钢流的冲击下, 被分裂成细小的渣滴并弥散于钢液中, 粒径越小,与钢液接触的表面积越大, 渣洗作用越强。乳化的渣滴随钢流紊乱 搅动的同时不断碰撞合并长大上浮。
作业
P99 1、 2
碱度R
石灰-粘土渣:
R
(CaO MgO)% Al2O3 % SiO2 %
(CaO MgO)% 2SiO2 % R 石灰-氧化铝渣: Al2O3 %
(CaO 0.7 MgO)% 自熔性化合物: R 0.94SiO2 % 0.18 Al2O3 %
有效氧化钙:
(CaO)u (CaO) 1.4( MgO) 1.86( SiO2 ) 0.55( Al2O3 )
合成渣有液态渣和固态渣,多数为液态渣。 合成渣洗的主要目的是降低钢中的氧,硫 和非金属夹杂物含量,它可以把[O]降至 0.002%、[S]降至0.005%甚至0.003%。
合成渣洗过程:在一个专门容器内(一般 使用电弧炉)熔炼合成渣(液态),炉渣温 度控制在1680~1750ºC,出钢前将熔炼好 的合成渣倒入钢包内并移至炉下,在出钢 过程中钢液流冲击包内的合成渣,充分搅 拌,钢液与合成渣充分接触,使钢液得到 渣洗。为了使钢渣充分搅拌接触,需大出 钢口、深坑出钢,即钢水有一定的冲击力, 钢流有一定的高度和速度,使钢水尽快出 净。混冲高度一般为3~4米,出钢时间要 短,如10t炉子35~55秒,20t炉子45~50 秒,合成渣用量一般为钢水量的5~6%, 进行渣洗的钢液出钢前应扒除炉渣,然后 再出钢。
合成渣洗的优缺点
有利的方面: 脱硫操作比较简单; 不需要大型设备; 投资省。
不利的方面: 效果不稳定; 不能去除气体,而且当渣料不干燥时还可 能造成吸气,使[H]增加。 不能控制硫化物形态,要想控制硫化物形 态,渣洗后再注入钙线; 温降大 ; 耐火材料的侵蚀。 必须把合成渣加热到液态使用,这样就需 要增加一套专门熔化合成渣的设备,一般 使用电弧炉熔化。