炼焦工序能耗
关于炼焦工序能耗标准的建议

炼焦生产物料平衡图
炼焦主要产品产率图(重量百分比%)
煤焦油 3.5% 焦炉煤气 17%
焦碳 焦炉煤气 煤焦油 粗轻苯 氨 化合水 其他
粗轻苯 1.1%
氨 0.3%
化合水 1.6%
其他 1%
焦碳 75%
4-2能量守恒
4-2.1炼焦热平衡
4.2.2焦炉炼焦热平衡表
收入 序 号 1 2 3 4 5 6 符 号 Q1 Q2 Q3 Q4 Q5 Q6 项目 加热煤气燃烧热 加热煤气显热 泄露荒煤气燃烧热 空气显热 干煤显热 配煤水分显热 数值 kJ/t % 1 2 3 4 5 6 7 8 9 10 Q ’1 Q ’2 Q ’3 Q ’4 Q ’5 Q ’6 Q ’7 Q ’8 Q ’9 Q’10 焦炭显热 煤焦油潜热和显热 粗苯潜热和显热 氨显热 净煤气显热 水气潜热和显热 废气显热 不完全燃烧热 炉体表面散热 误差 序号 符号 支出 项目 数值 kJ/t %
二.炼焦生产能耗计算必须遵守的原则
炼焦生产是十分典型的能源再加工过程 和热能的再回收利用过程,既生产重要的能 源产品(焦炭、炼焦煤气),又生产多种煤 化工产品(焦化苯类、煤焦油)等含热能较 高的重要化工资源。 ----必须遵照《物质守恒、能量守恒》的原则
2-1物质守恒—重量转化差
以2006年协会对部分会员单位的有关情 况统计看:
能源消耗总量包括以下各项: ①从投料到制成 产 品的整个生 产过 程,直接用于 该产 品的原料、燃料、 动 力和工 艺 用的 一 次能源 和二次能源; ②分摊在该产品的辅助生产系 统和附属生产系统消 耗的一次能源和二次能源; ③分摊在该产品的企业内部的亏损能源; ④次品和废品所消耗的一次能源和二次能源。 不包括下列各项: ①非工业生产用能源,如基本建设、生活用能源; ②各种余热、余气的回收利用及工业废渣的利用。
3能耗指标体系的分类计算

能耗指标体系的分类钢铁企业能耗指标主要有吨钢综合能耗、吨钢可比能耗、主要产品的工序能耗、主要产品的实物单耗(如炼铁焦比、炼焦煤耗等)以及产值能耗、增加值能耗等等。
能源分析评价指标中,包括企业内部能源加工转换指标和企业损失指标。
按钢铁企业能耗经济技术指标体系可分为:(1)企业级能源技术经济指标:如吨钢综合能耗、万元产值能耗、吨钢耗新水、吨钢电耗、损失率等。
(2)工序级能源技术经济指标:如炼钢工序能耗、炼铁工序能耗等。
(3)耗能设备级能源技术经济指标:加热炉燃耗、高炉焦比、制氧机电耗等。
按钢铁企业能效对标指南中能耗指标体系可分为:(1)综合性指标:如企业级能源消耗总量、工序级能源消耗总量、各类能源介质消耗总量、企业能源亏损量等指标。
(2)单耗性指标:如吨钢综合能耗、企业吨钢可比能耗、工序单位产品能耗。
(3)经济性指标:万元产值能耗、万元增加值能耗等。
2.能耗指标的范围及计算钢铁制造流程是由多个不同的生产工序组成的,前一道工序的产品为下一道工序的原料,这是钢铁工业的特点,由于其复杂性,因此,统计范围和指标定义必须规范,以便于对标,找出节能潜力,提升企业效益。
(1)吨钢综合能耗范围及计算综合能耗是规定的耗能体系在一段时间内实际消耗的各种能源实物量按规定的计算方法和单位分别折算为标准煤后的总和。
吨钢综合能耗(comprehensive energy consumption ):吨钢综合能耗是企业生产每吨粗钢所综合消耗的各种能源自耗总量;也就是每生产一吨钢,企业消耗的净能源量。
其计算公式为:吨钢综合能耗=企业钢产量企业自耗能源量(吨标准煤/吨钢,千克标准煤/吨;tce/t ,kgce/t )式中,企业自耗能源量即报告期内企业自耗的全部能源量。
统计上报按企业全部耗能量。
企业自耗能源量= 企业购入能源量 ± 库存能源增减量 - 外销能源量= 企业各部位耗能量之和 + 企业能源亏损量作为行业对标,吨钢综合能耗的统计范围可按照企业生产流程的主体生产工序(包括原料储存、焦化、烧结、球团、炼铁、炼钢、连铸、轧钢、自备电厂、制氧等动力厂)、厂内运输、燃料加工及输送、企业亏损等消耗能源总量,不包括矿石的采、选工序,也不包含炭素、耐火材料、机修、石灰、精制及铁合金等非钢生产工序的能源消耗量。
国内外高炉炼铁系统的能耗分析
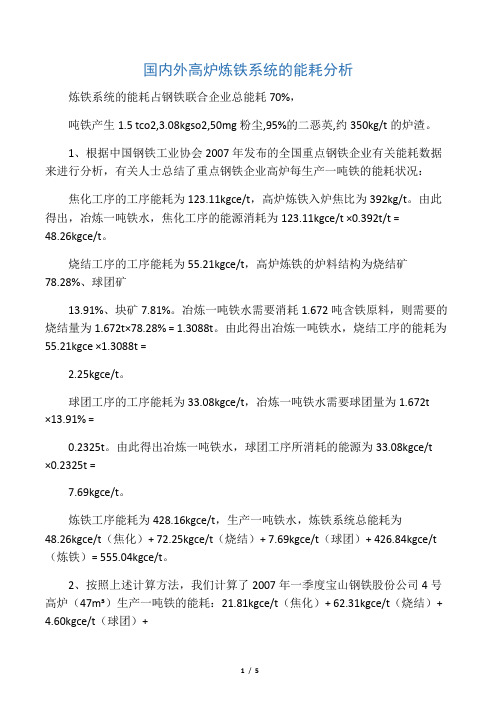
表12005年浦项制铁盒光阳厂炼铁有关能耗指标
项目工序能耗Kgce/t
烧结
66
57.4焦化
129.7
131.9炼铁
462.5
441.1入炉焦比Kgce/t炉料结构%
烧结比
76.4
70.9球团比
7.8
11.1块矿比
15.8
18.0xx
光阳494.7
492.1
表2全国重点钢铁企业能耗对比(单位Kgce/t)
高热值煤气回收利用率低是非高炉炼铁能耗高的“瓶颈”
2007年,我国重点钢铁企业的烧结、炼铁工序能耗与2006年相比进一步降低,炼铁生产部分工序能耗指标见表2。
2007年,全国重点钢铁企业高炉炼铁燃料比是529kg/t,浦项FINEX燃料比是740kg/t~750kg/t,澳大利亚Hismelt的煤耗在900kg/t(尚需1200℃风温和350kWh/t的电力)。这说明目前非高炉炼铁的能耗高于高炉冶炼生产工艺。
国内外高炉炼铁系统的能耗分析
炼铁系统的能耗占钢铁联合企业总能耗70%,
吨铁产生1.5 tco2,3.08kgso2,50mg粉尘,95%的二恶英,约350kg/t的炉渣。
1、根据中国钢铁工业协会2007年发布的全国重点钢铁企业有关能耗数据来进行分析,有关人士总结了重点钢铁企业高炉每生产一吨铁的能耗状况:
焦化行业清洁生产水平评价标准

焦化行业清洁生产水平评价标准
焦化行业清洁生产水平评价标准主要包括以下几个方面:
1. 资源能源利用指标:焦炭产量和主要原料煤的消耗量应满足相应的标准,例如吨焦耗洗精煤(干煤)应≤,全焦率应≥75%。
2. 炼焦工序能耗和热量消耗:炼焦工序的能耗应≤170kg标煤/t焦,而炼焦耗热量应满足特定的煤气加热值折算要求。
3. 水和电力消耗:吨焦耗新水应≤,吨焦耗电量应≤35KWh。
4. 煤气利用和水循环利用率:焦炉煤气利用率应≥95%,水循环利用率应≥85%。
5. 副产品综合利用:煤气不得直排或点火炬,煤焦油及苯类化工产品应进行有效回收。
6. 污染物产生指标:新建和改扩建焦化生产企业各种污染物产生指标不得超过炼焦行业清洁生产标准(HJ/T126-2003)中规定的二级标准。
废物回收利用指标也应达到相应的标准。
以上是焦化行业清洁生产水平评价标准的主要内容,具体标准可能会根据实际情况有所调整。
炼焦工序能效标杆水平

炼焦工序能效标杆水平
炼焦工序的能效标杆水平取决于多个因素,包括采用的技术、设备、操作方式等。
然而,以下是一些常见的炼焦工序能效标准:
1. 煤气利用率:衡量炼焦工序中煤气的利用效率。
通常用于发电或热能回收等用途。
高效的炼焦工序应该能够最大限度地利用煤气。
2. 焦炭收率:炼焦工序中产生的焦炭数量与原料煤数量的比例。
高效的工序应该能够最大限度地将原料转化为焦炭,以提高焦炭收率。
3. 能耗:炼焦工序中消耗的能源总量。
高效的工序应该能够尽量减少能源的消耗,例如优化供热系统、改善燃烧方式等。
4. 废水和废气处理:炼焦工序中产生的废水和废气的处理效率。
高效的工序应该能够有效处理废水和废气,以减少对环境的负面影响。
需要注意的是,能效标杆水平可能因地区和工艺的不同而有所差异。
因此,在具体应用中,应根据实际情况来确定具体的能效标杆水平。
工信部钢铁能耗标准
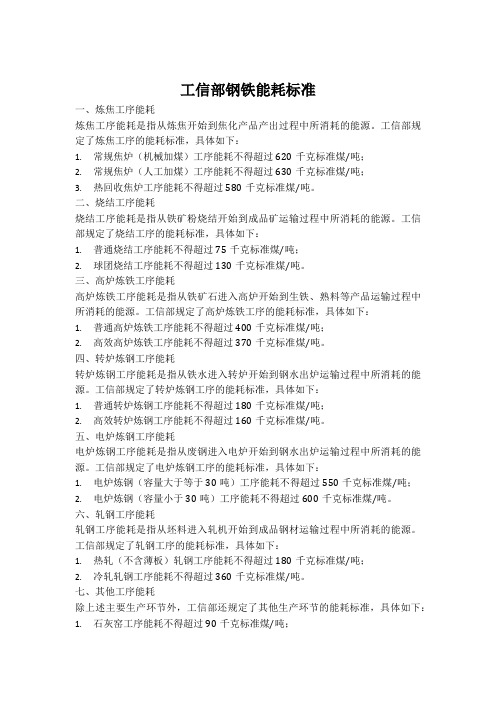
工信部钢铁能耗标准一、炼焦工序能耗炼焦工序能耗是指从炼焦开始到焦化产品产出过程中所消耗的能源。
工信部规定了炼焦工序的能耗标准,具体如下:1.常规焦炉(机械加煤)工序能耗不得超过620千克标准煤/吨;2.常规焦炉(人工加煤)工序能耗不得超过630千克标准煤/吨;3.热回收焦炉工序能耗不得超过580千克标准煤/吨。
二、烧结工序能耗烧结工序能耗是指从铁矿粉烧结开始到成品矿运输过程中所消耗的能源。
工信部规定了烧结工序的能耗标准,具体如下:1.普通烧结工序能耗不得超过75千克标准煤/吨;2.球团烧结工序能耗不得超过130千克标准煤/吨。
三、高炉炼铁工序能耗高炉炼铁工序能耗是指从铁矿石进入高炉开始到生铁、熟料等产品运输过程中所消耗的能源。
工信部规定了高炉炼铁工序的能耗标准,具体如下:1.普通高炉炼铁工序能耗不得超过400千克标准煤/吨;2.高效高炉炼铁工序能耗不得超过370千克标准煤/吨。
四、转炉炼钢工序能耗转炉炼钢工序能耗是指从铁水进入转炉开始到钢水出炉运输过程中所消耗的能源。
工信部规定了转炉炼钢工序的能耗标准,具体如下:1.普通转炉炼钢工序能耗不得超过180千克标准煤/吨;2.高效转炉炼钢工序能耗不得超过160千克标准煤/吨。
五、电炉炼钢工序能耗电炉炼钢工序能耗是指从废钢进入电炉开始到钢水出炉运输过程中所消耗的能源。
工信部规定了电炉炼钢工序的能耗标准,具体如下:1.电炉炼钢(容量大于等于30吨)工序能耗不得超过550千克标准煤/吨;2.电炉炼钢(容量小于30吨)工序能耗不得超过600千克标准煤/吨。
六、轧钢工序能耗轧钢工序能耗是指从坯料进入轧机开始到成品钢材运输过程中所消耗的能源。
工信部规定了轧钢工序的能耗标准,具体如下:1.热轧(不含薄板)轧钢工序能耗不得超过180千克标准煤/吨;2.冷轧轧钢工序能耗不得超过360千克标准煤/吨。
七、其他工序能耗除上述主要生产环节外,工信部还规定了其他生产环节的能耗标准,具体如下:1.石灰窑工序能耗不得超过90千克标准煤/吨;2.耐火材料及制品生产工序能耗不得超过450千克标准煤/吨;3.铁合金生产(包括硅系、锰系等)工序能耗不得超过580千克标准煤/吨。
单位产品能源消耗情况指标的计算方法

重(吨/立方米)
矿井其它产量指生产矿井回采和掘进产量以外的其它产量,主要包括井巷 维修出煤,已报废矿井复采后所出的煤,不合质量经处理后合格的回收煤,科 研试采出煤,出井无牌煤,水砂充填或水采矿井扫沉淀的煤泥,盘点发生的涨 (亏)吨煤,以及由生产费用开支不计能力的矿井产量。
2.非原煤生产用电量:
指煤矿企业附属的其他工业产品生产用电量。如选煤厂、机修厂、运输 队、建材厂、火药厂、化工厂、支架厂、钢铁厂、综合利用厂等用电量和由各 种专用基金支付的工程(如大修理、更新改造工程等)用电量,以及与上述有 关的线路和变压器的电损失。
3.非生产部门的用电量:
指煤矿企业的非生产部门用电量。如学校、托儿所、幼儿园、机关职工食 堂、住宅区浴室、消防队等用电量,以及与上述有关的线路和变压器的电损 失。
煤炭开采和洗选业
(06)
吨煤综合能耗:
吨煤综合能耗(吨标准煤/吨)=总能耗(吨标准煤)/原煤产量(吨)子
项:
总能耗=(原煤生产能耗+非原煤生产能耗)-(煤矸石、油页岩、煤泥、瓦 斯资源利用量)。
计算时,应折算成标准煤后计算。煤矸石、油页岩、煤泥、瓦斯资源利用 量按实测发热量数据计算标准煤量。
原煤生产能耗:
母项:
机制纸及纸板产量为合格品产量。
每吨机制纸浆耗电:
每吨机制纸浆耗电(千瓦时/吨)=100X企业生产用电量(万千瓦时)/机制 纸浆产量(吨)
子项:
母项:
原煤产量为矿井产量、露天产量、其他产量。矿井产量指回采产量、掘进
产量和矿井其它产量。露天矿产量指采煤阶段产量、剥离阶段产量和露天其它
产量。其他产量指基建工程煤、更改工程煤和不计能力小井(小露天)产量。
加强炼焦管理降低工序能耗

年同期 比下降 1. 9 egt 由原来 第三 名跃居 全 国 4 7 ck/ , 同类型企 业的前列 ( 见图 1 。 )
1 7 40 2 13 9 78
l
_ 1 l
20 年 04
i 圈
圈
; .
2 0 年 06
厂, 焦化厂的工 序能耗 指 标是衡 量企 业 能源综 合利
3 降低 工 序能 耗 的途径
3 1 完 善 能源 管理 机制 , . 推行 目标 管理 模式
厂部健全与 完 善能源 管理 网络 , 全厂 的能 源 对 实施统一管 理。每 月制定 能 源计划 、 目标及 管理 考
类能耗指标都 有显 著 降低 , 年工 序能 耗指 标与 去 今
维普资讯
处 于受 控 状 态 。
减少 人煤水分 的波 动 , 好雨 季到 来前 的原 料储 备 做
工作 , 免潮料 或 杂料 直接 进料 仓 。由于各 矿点 煤 避 的结焦性能不 同, 分 、 分 的差 异 , 灰 硫 因此按 品种 合 理堆放 , 按贯标要 求 , 牌 一致 。取煤采 用 “ 点煤 物 定 堆, 回转 取煤 ” 行均 匀化 作业 。根据 不 同矿点 、 进 煤
3 2 精 细化 管 理 , 绝能 源浪 费 . 杜
3 2 1 保证进厂煤 的质量 .. 进厂煤 的灰份 、 、 硫 水分是 直接影 响购人 能源质 量 的重要指标 , 要保证进 厂煤 的数 、 质量 做法是 : 在质量上 , 场严 格按 公 司进 厂原 料验 收 规定 煤
种, 充分 发挥 4 k 焦 炉实 验 的作 用 , 确 定最 佳 0 g小 来
配 比方 案 , 在保 证焦炭质量 的前 提下 , 配用低价 格 的
13焦煤 、 / 瘦煤替代其他高价格煤种 , 降低原料成本 。
- 1、下载文档前请自行甄别文档内容的完整性,平台不提供额外的编辑、内容补充、找答案等附加服务。
- 2、"仅部分预览"的文档,不可在线预览部分如存在完整性等问题,可反馈申请退款(可完整预览的文档不适用该条件!)。
- 3、如文档侵犯您的权益,请联系客服反馈,我们会尽快为您处理(人工客服工作时间:9:00-18:30)。
一、炼焦工序单位能耗
炼焦工序单位能耗是指生产1吨焦炭(干基)所耗用的能量。
其计算公式为:
炼焦工序单位能耗(千克标准煤/吨)=炼焦工序净耗能量(千克标准煤)/全部焦炭合格产出量(吨)计算说明:
1、子项炼焦工序净耗能量是指炼焦工艺生产系统的备煤车间(不包括洗煤)、厂内部原料煤的损耗、炼焦车间、回收车间(冷凝古风、氨回收、粗苯、脱硫脱氰、黄血盐)辅助生产系统的机修、化验、计量、环保等,以及直接为生产服务的附属生产系统的食堂、浴池、保健站、休息室、生产管理和调度指挥系统等所消耗的各种能源的实物量,扣除回收利用并外供的余热、二次能源、余热量,并折成标准煤。
即子项=原料煤折标准煤(千克)+动力折标准煤(千克)-焦化产品外供量折标准煤(千克)-余热回收外供量折标准煤(千克)-回收二次能源外供量折标准煤(千克)-利用余热外供量折标准煤(千克);
2、原料煤为装入焦炉的干洗精煤量;
3、焦化产品外供量是指供外厂(车间)的焦炭、焦炉煤气、煤焦油、粗苯等数量;
4、动力是指高炉煤气、水、电、蒸汽、压缩空气等;
5、余热回收外供量,如供应外工厂(车间)的蒸汽数量及熄焦工序外供的电量等。
二、焦炭主要能源实物消耗
焦炭主要能源实物消耗是指每生产1吨焦炭所消耗的某种能源实物量。
其计算公式为:
焦炭某种能源实物消耗(该能源计量单位/吨)=焦炭某种能源耗用量(该能源计量单位)/全部焦炭合格产出量(干基)(吨)计算说明:
1、应按所消耗的电力、水、煤气等能源品种分别计算。
2、某种能源耗用量是指全厂的耗用量,包括从配煤到煤气净化工序结束止,但不包括化工产品精制产品所用的物料消耗。
3、煤气消耗的单位也可用米3
/吨焦;蒸汽消耗单位也可用吨/吨焦。
4、在计算车间消耗指标时,除炼焦车间按焦炭量计算外,其他车间则按产品分别进行计算,即子项为生产该产品的水、电、煤气等能源实物消耗量,母项为该产品合格产出量。
三、焦炭单位产品综合能耗
1、统计范围
备煤(不包括洗煤)、炼焦和煤气净化工段的能耗和扣除自身回收利用和外供的能源量,不包括精制。
备煤工段包括贮煤、粉碎、配煤及系统除尘;炼焦工段包括炼焦、熄焦、筛运焦、装煤除尘、出焦除尘和筛运焦除尘;煤气净化工段内容包括冷凝鼓风、脱硫、脱氰、脱氨、脱苯、脱萘等工序和酚氰污水处理;干熄焦产出只计算蒸汽,不含发电。
2、计算方法
焦炭单位产品综合能耗应按以下公式计算:
EJT=(e
yl+e
jg-e
cp-e
yr)/p
JT
式中:
EJT ------焦炭单位产品综合能耗,单位为千克标准煤每吨(kgce/t);e
yl------原料煤量,单位为千克标准煤(kgce);ejg------加工能耗量,是指炼焦生产所用焦炉煤气、高炉煤气、水、电、蒸汽、压缩空气等能源,单位为千克标准煤(kgce);e
cp------焦化产品外供量,是指供外厂(车间)的焦炭、焦炉煤气、粗焦油、粗苯等的数量,单位为千克标准煤每吨(kgce/t);e
yr-----余热回收量,如干熄焦工序回收的蒸汽数量等,单位为千克标准煤每吨(kgce/t);p
JT------------焦炭产量,单位为吨(t)。
资源能源利用指标
指标一级二级三级
工序能耗,kg 标煤/t焦≤150≤170≤180
吨焦耗xx水量,m
3/txx≤2.5≤3.5
吨焦耗蒸汽量,t/t 焦≤0.20≤0.25≤0.40
吨焦耗电量,kW·h/t 焦≤30≤35≤40
炼焦耗热量(7%H
2O)kJ/kg 标煤
焦炉煤气≤2150≤2250≤2350
高炉煤气≤2450≤2550≤2650
焦炉煤气利用率,% 100≥95≥80
水循环利用率,%≥95≥85≥75。